Automated Assembly
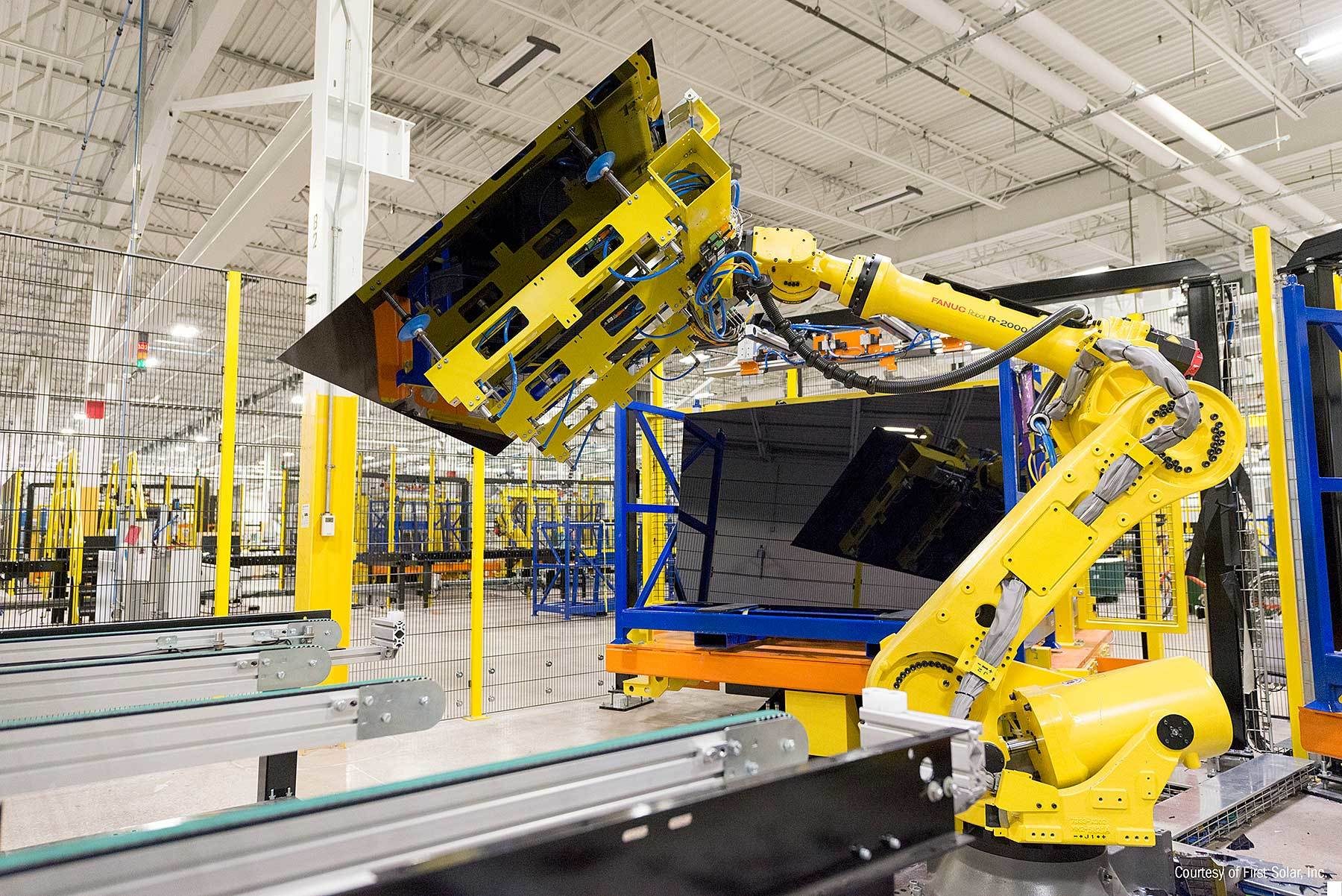
According to ASSEMBLY’s annual Capital Equipment Spending Survey, 25 percent of U.S. factories make more than 1 million products annually. The only way to meet that kind of volume is with automation. Automated assembly systems can be synchronous or asynchronous. Each has advantages and limitations. Synchronous systems come in several configurations: rotary, carousel, inline and continuous motion. All four types are driven by a central camshaft that rotates at a constant speed. Each assembly station is associated with one or more cams on the shaft. As the cams rotate, they trigger the stations to perform their tasks. In an asynchronous system, conveyors transfer parts on pallets from one station to the next. Assembly operations and pallet transfers are triggered by sensors or switches, and the system is governed by one or more computers or PLCs. Flexibility is the main advantage of these systems. Because asynchronous systems are typically modular, stations can be added or subtracted relatively easily. Whichever system you choose, the information in this section will help.
To find all suppliers of Automated Assembly, click one of the sections below.
Automated Assembly Machines & Systems
Parts Feeders & Controls & Positioning Equipment
Conveyors & Handling Systems
Photo courtesy First Solar Inc.