Canoo Beefs Up Manufacturing Footprint in Oklahoma
NEWS

Canoo plans to ramp up EV production next year at a new assembly plant in Oklahoma City. Illustration courtesy Canoo
OKLAHOMA CITY—Canoo plans to establish a second assembly plant here, joining a facility that’s set to open soon in Pryor, OK. It has acquired a 630,000-square-foot building that formerly house a Terex construction equipment factory.
After it has been retrofitted, the facility will produce Canoo's LDV and LV vehicles starting late next year. The small electric vans are designed for last-mile small package and grocery delivery applications. The vehicles will be built on a multi-purpose platform that integrates the motors, battery module and other components.
“The Oklahoma City facility has significant room for expansion and is a proven location for large-scale production, with an established transportation ecosystem, including rail," says Tony Aquila, chairman and CEO at Canoo. "We are working with our third-party manufacturing partners to achieve start of production on our own equipment this month. Following these initial builds, we will aggressively shift all our equipment into our new facility during the first half of 2023, with production ramp in the second half of the year."
In addition to Canoo's Oklahoma City vehicle manufacturing facility, the startup automaker recently announced that it plans to build a battery plant at its MegaMicro factory located on a 400-acre campus near Tulsa.
"We are accelerating our hiring plans in Pryor with the establishment of our battery module manufacturing facility, which will produce our proprietary batteries, energy management system and thermal control technology for our MPP platform," notes Tony Aquila.
“The location has been strategically selected due to its proximity to our battery cell partner Panasonic,” adds Aquila. “In addition, we will be the first EV company to produce our battery modules with hydro power from the Grand River Dam Authority. We will work closely with and hire within the surrounding communities to create an EV ecosystem in the region."
According to Aquila, the facility will mass-produce proprietary battery modules on high-capacity assembly lines with state-of-the-art automated machinery. Canoo has refined and validated its battery module manufacturing over recent months and is awaiting delivery of machinery at the new facility.
EV Motors Increasingly Integrate New Technologies
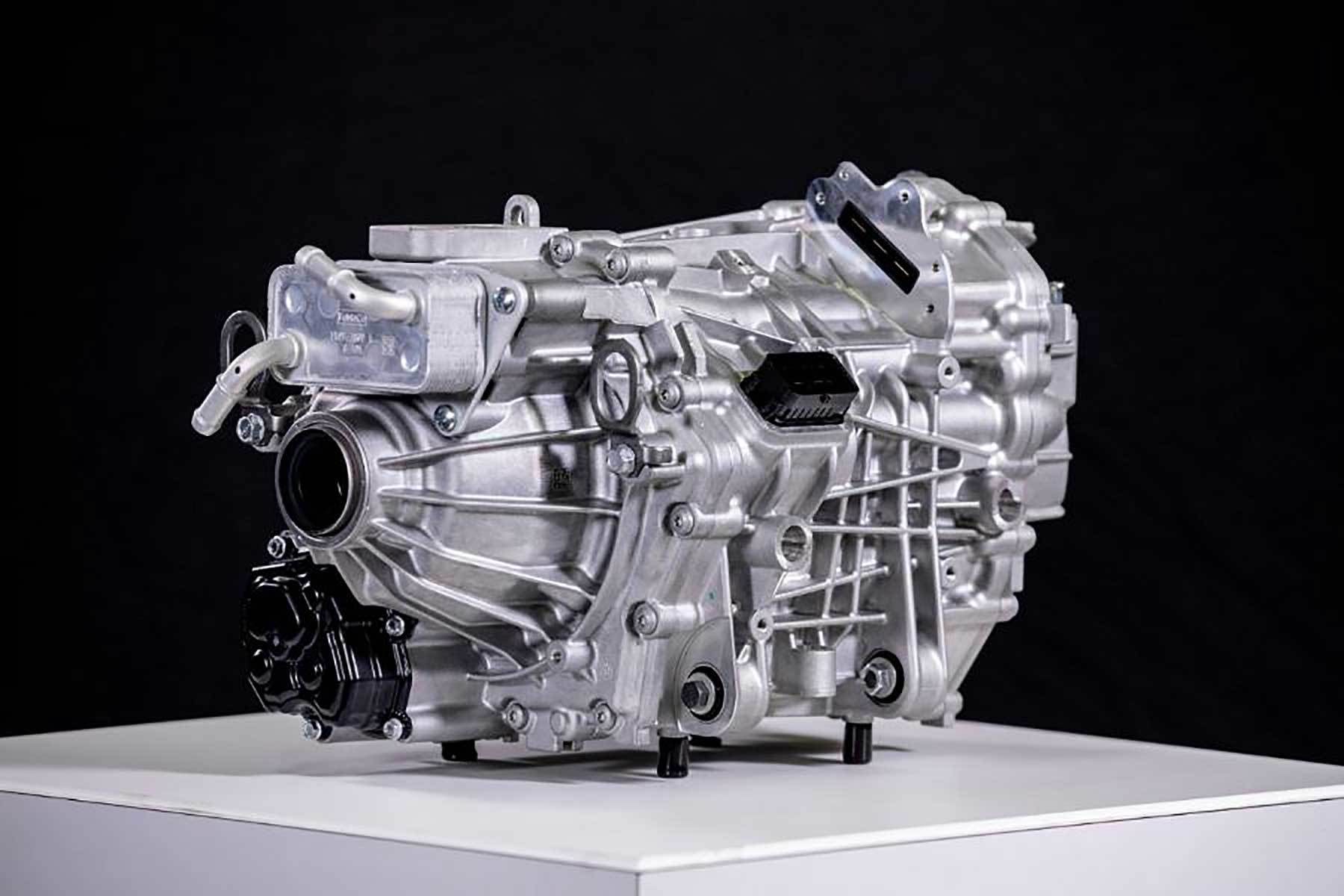
Automakers are exploring new types of electric traction motor technology. Photo courtesy Ford Motor Co.
BOSTON—More and more electric traction motors are being integrated with the inverter and transmission, while new technology concepts, such as axial flux and switched reluctance are being explored, according to a new report from Strategy Analytics Inc.
"As automakers adjust their businesses to become all-electric, they are increasingly looking into integrating their motors with other components to from e-axles to raise production efficiency and lower production cost, which enables them to use new flexible and modular vehicle platforms,” says Kevin Mak, principal analyst in the global automotive practice at Strategy Analytics.
“But, the increase in competition among automakers will also see further exploration of [new] concepts, such as axial flux motors by the likes of Mercedes and Renault, plus 800-volt motors and denser coil windings in the stator,” explains Mak. “Some are also limiting the use of costly rare-earth materials used in electric motor magnets through induction motors and externally-excited synchronous motors.
“[In addition], production of electric motors has swung in-house and back out to Tier One suppliers again, as the market becomes more commoditized,” adds Mak.
New Lithium-Ion Battery Uses Simplified Production Process
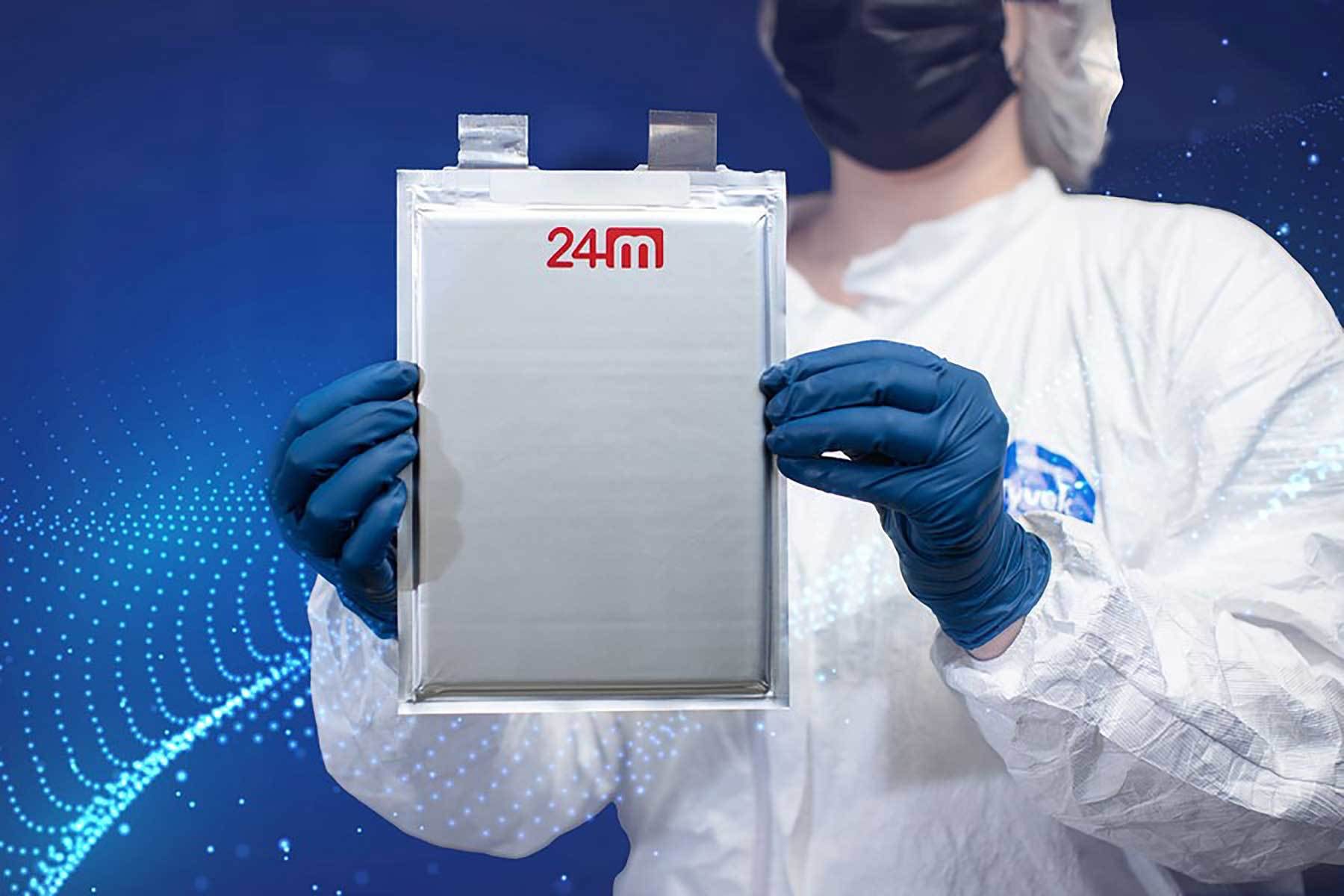
A new lithium-ion battery cell production process can reduce costs by up to 40 percent. Photo courtesy 24M Technologies Inc.
CAMBRIDGE, MA—When it comes to battery innovations, much attention gets paid to potential new chemistries and materials. However, the importance of production processes for reducing cost often gets overlooked.
Engineers at 24M Technologies Inc. recently designed a battery that reduces the cost of manufacturing lithium-ion cells. The simplified design requires fewer materials and fewer steps to produce each cell.
The start-up company claims the design, which it calls “SemiSolid” for its use of gooey electrodes, can reduce production costs by up to 40 percent. The approach also improves the battery’s energy density, safety and recyclability.
“The SemiSolid platform has been proven at the scale of hundreds of megawatts being produced for residential energy-storage systems,” says Naoki Ota, CEO of 24M Technologies. “Now, we want to prove it at the gigawatt scale.”
Establishing large-scale production lines is only the first phase of 24M’s plan. Another key draw of its battery design is that it can work with different combinations of lithium-ion chemistries. That means 24M’s partners can incorporate better-performing materials down the line without substantially changing manufacturing processes.
The kind of quick, large-scale production of next-generation batteries that 24M hopes to enable could have a dramatic impact on the cost and performance of electric cars.
“This is a platform technology,” says Ota. “We’re not just a low-cost and high-reliability operator. That’s what we are today, but we can also be competitive with next-generation chemistry. We can use any chemistry in the market without customers changing their supply chains. Other start-ups are trying to address that issue tomorrow, not today. Our tech can address the issue today and tomorrow.”
Traditional lithium-ion batteries use solid electrodes separated from the electrolyte by layers of inert plastics and metals, which hold the electrodes in place. Stripping away the inert materials of traditional batteries and embracing the gooey electrode mix gives 24M’s design a number of advantages.
It eliminates the energy-intensive process of drying and solidifying the electrodes in traditional lithium-ion production. The company says it also reduces the need for more than 80 percent of the inactive materials in traditional batteries, including expensive ones like aluminum and copper. In addition, the design requires no binder and features extra thick electrodes, improving the energy density of the batteries.
Ota believes the new technology will accelerate EV adoption, because battery costs still make up 30 percent to 40 percent of the price of EVs, according to the Institute for Energy Research.
“Lithium-ion batteries have made huge improvements over the years, but even Elon Musk says we need some breakthrough technology,” says Ota. “To make EVs more common, we need a production cost breakthrough. We can’t just rely on cost reduction through scaling, because we already make a lot of batteries today.”
Honda to Make EVs at Ohio Assembly Plants
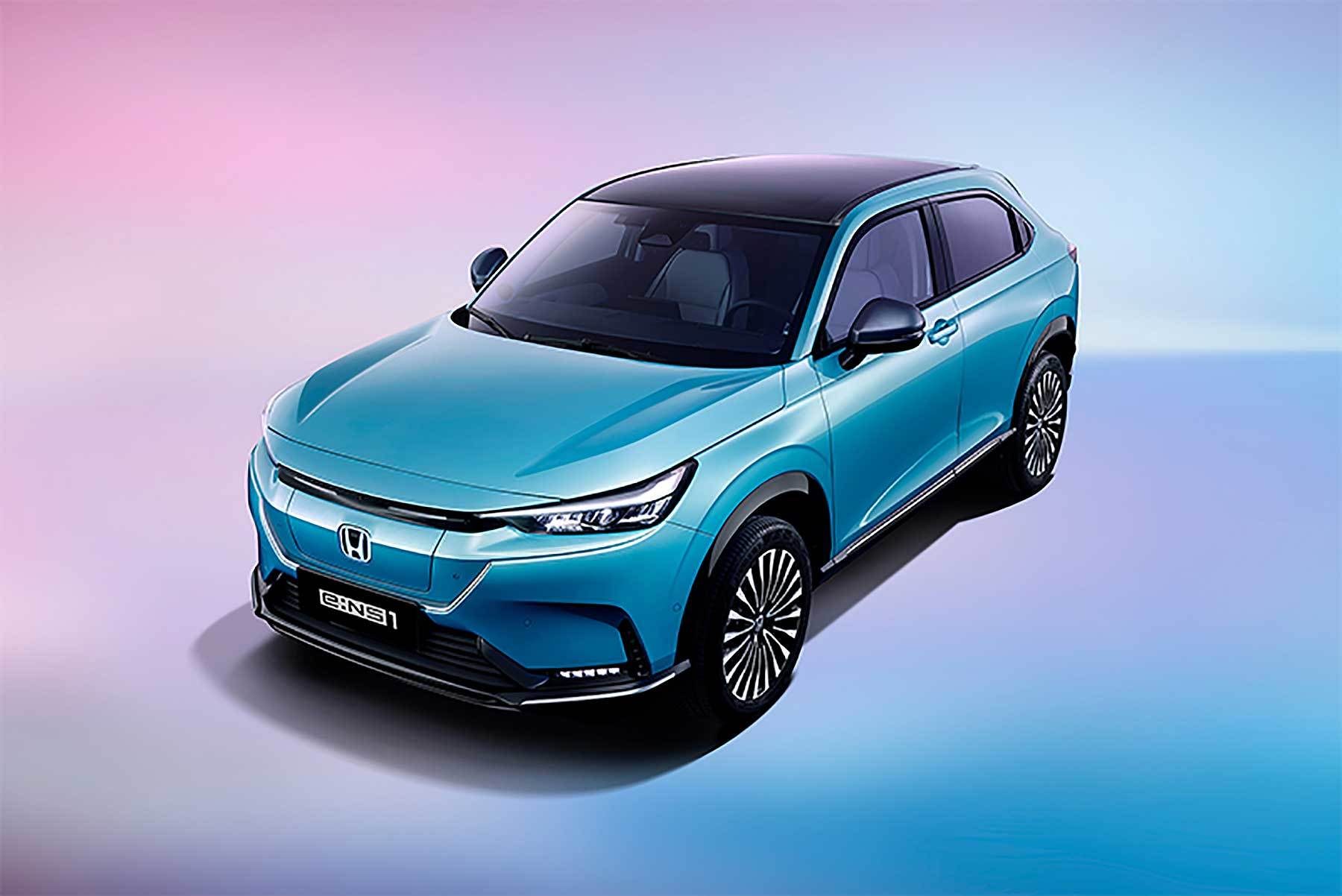
Honda plans to ramp up EV production at its Ohio factories. Photo courtesy Honda Motor Co.
MARYSVILLE, OH—Honda Motor Co. plans to invest $700 million to retool three plants in Ohio for EV production. The facilities are the Anna engine plant and vehicle assembly plants in East Liberty and Marysville.
Honda is also investing $3.5 billion in a joint-venture battery factory with LG Energy Solution. The latter facility will be located 40 miles southwest of Columbus in Jeffersonville, OH.
By 2040, Honda claims that 100 percent of its new vehicles in North America will be powered by batteries and fuel cells. The automaker’s three existing facilities in the Buckeye State, along with the new battery plant, will serve as an EV hub that will leverage the company's production, product development and purchasing operations located in central Ohio.
"This is a very challenging time for our entire industry, but also a very exciting time as Honda invests in full electric vehicle production," says Bob Nelson, executive vice president of American Honda Motor Co., “[We have] built hybrid-electric vehicles in Ohio for a number of years, and the experience and expertise of our associates in manufacturing, product development and purchasing will serve as an important foundation as we transition to the electrified future."
Honda produced and sold a record of more than 100,000 electrified vehicles in the U.S. last year, including the Accord Hybrid, CR-V Hybrid and Insight hybrid sedan.
Bosch Begins Assembling EV Motors in South Carolina
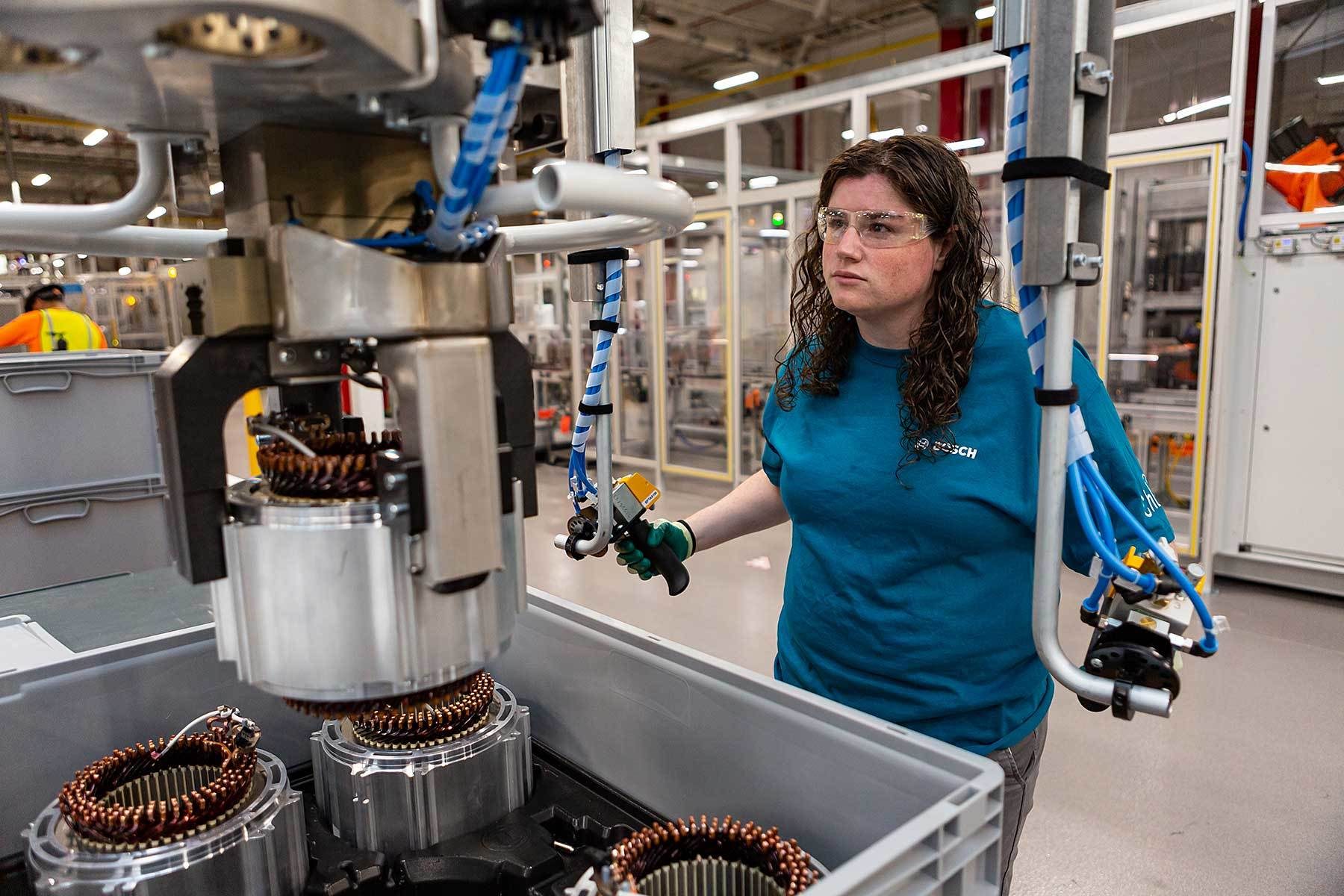
Bosch is assembling EV motors at a facility that previously produced diesel engine components. Photo courtesy Robert Bosch GmbH
CHARLESTON, SC—Robert Bosch GmbH has started to mass-produce electric vehicle motors at its factory here. The200,000-square-foot operation is housed in an existing building that previously produced diesel engine components. The new line produces subassemblies, such as rotors and stators, as well as finished motors.
“We have long been believers in the potential of electromobility, and we have been investing heavily to bring this technology to market at scale for our customers,” says Mike Mansuetti, president of Bosch North America. “We have grown our electrification business globally and here in the North American region.
“We’ve invested more than $6 billion in electromobility development, and in 2021, our global orders for electromobility surpassed $10 billion for the first time,” claims Mansuetti. “Local production helps to advance our customers’ regional electrification strategies, and further supports the market demand for electrification.”
The 48-year-old Charleston facility is one of Bosch’s largest manufacturing site in the United States, employing around 1,500 people. It covers more than 900,000 square feet of floor space located on 118 acres. The plant produces a variety of items, including high-pressure fuel injectors and pumps for internal combustion engines.
“The Charleston plant stands out with a long history of process competency, as well as its knowledge in the area of automation and robotics,” explains Mansuetti, who started out his Bosch career as a manufacturing engineer at the facility. “Production at the site features highly automated processes, and [we are using] artificial intelligence and Industry 4.0 methods to gain more efficiency.
“We are in the midst of major shifts in mobility, and the story of reinvention in Charleston is a model for how electrification production can evolve from within an existing facility,” says Mansuetti. “We are building on the long-standing expertise and commitment of the Charleston team with this new production.”
BMW Plans to Double Down on EV Production in USA
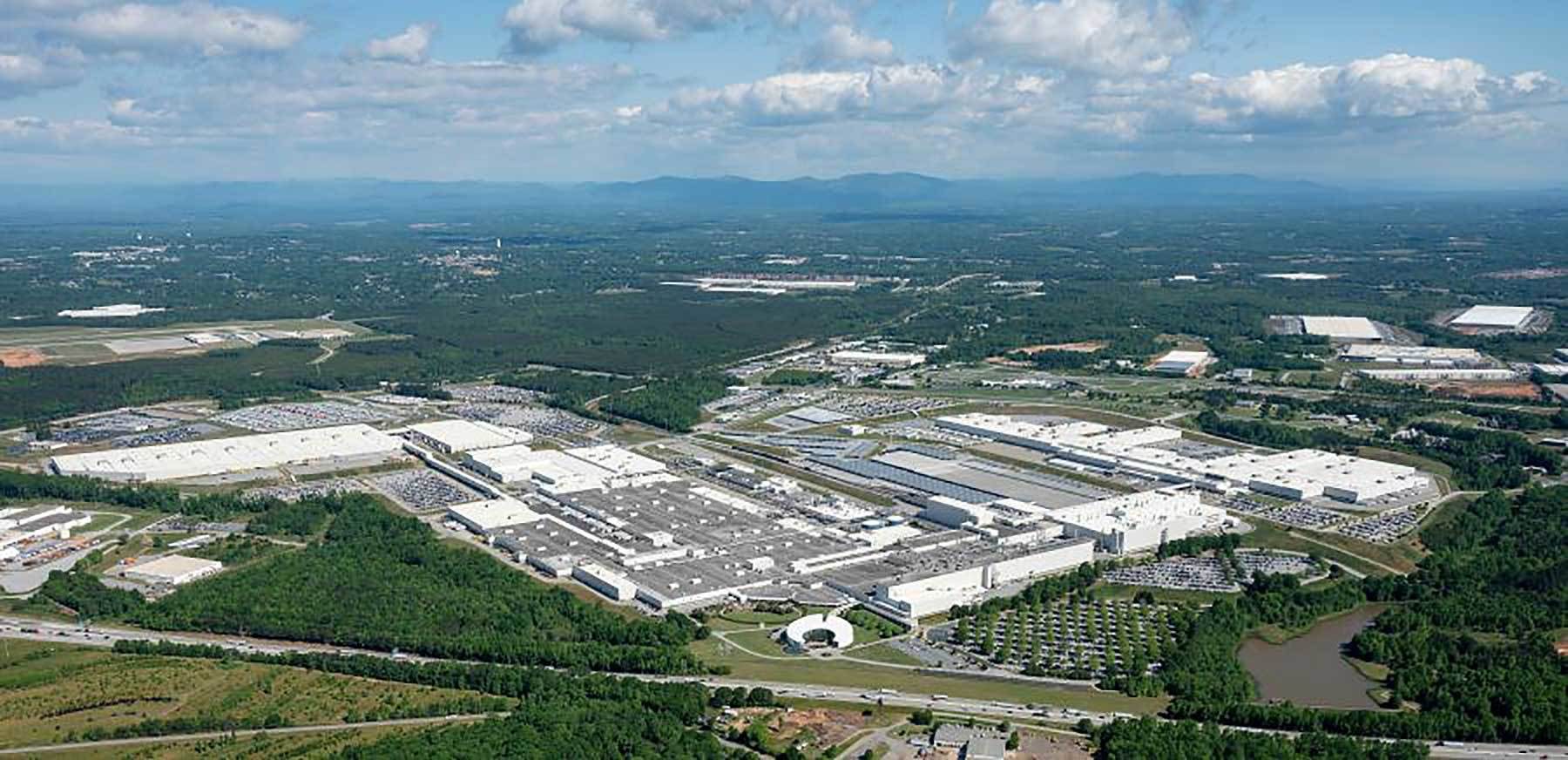
BMW will build at least six fully electric models at is flagship factory in Spartanburg, SC. Photo courtesy BMW Group
SPARTANBURG, SC—BMW Group plans to invest $1.7 billion in its U.S. operations, including $1 billion to prepare for the production of electric vehicles at its flagship factory here. The automaker will also spend $700 million to construct a new 1-million-square-foot battery assembly facility in nearby Woodruff, SC. By 2030, BMW will build at least six fully electric models in the United States.
“For decades, Plant Spartanburg has been a cornerstone of [our] global success,” says Oliver Zipse, chairman of the board of management at BMW Group. “It is the home of the BMW X models that are so popular all over the world. Going forward, it will also be a major driver for our electrification strategy.
“In addition, we can showcase [our] ‘local for local’ principle,” explains Zipse. “Our newly developed sixth-generation battery cells, which were specifically designed for next-generation electric vehicles, will be sourced in South Carolina, where X goes electric.”
As part of its local for local strategy, BMW plans to purchase battery cells for its EVs near where production takes place. The company is partnering with Envision AESC to build a new factory in South Carolina, which will mass-produce round lithium-ion battery cells.
According to Zipse, the new battery format will increase energy density by more than 20 percent, improve charging speed by up to 30 percent and enhance range by up to 30 percent. He also claims that CO2 emissions from cell production will be reduced by up to 60 percent through the partial use of secondary lithium, cobalt and nickel material, as well as renewable energy for production.
BMW’s Spartanburg plant currently produces lithium-ion battery modules for two plug-in hybrid electric vehicles: the X3 xDrive30e and the X5 xDrive45e. In 2021, nearly 70,000 electrified BMWs were built at the factory.
The 30-year-old assembly plant currently produces 11 models, including the BMW X3, X4, X5, X6 and X7 sport utility vehicles, four BMW M models and two plug-in hybrid electric models. Production of the all-new hybrid-electric XM will begin later this year. The plant is supported by more than 300 companies in the U.S., including more than 40 Tier One suppliers in South Carolina alone.
“This is a very important step for Plant Spartanburg as we continue our legacy of producing high-quality vehicles and build on the success of the last 30 years,” says Robert Engelhorn, president and CEO of BMW Manufacturing Co. “With this latest investment, we future-proof our operations and prepare the plant for electrification and new technologies, ensuring both the long-term success of our company and our position as an attractive and viable employer in the state of South Carolina.”
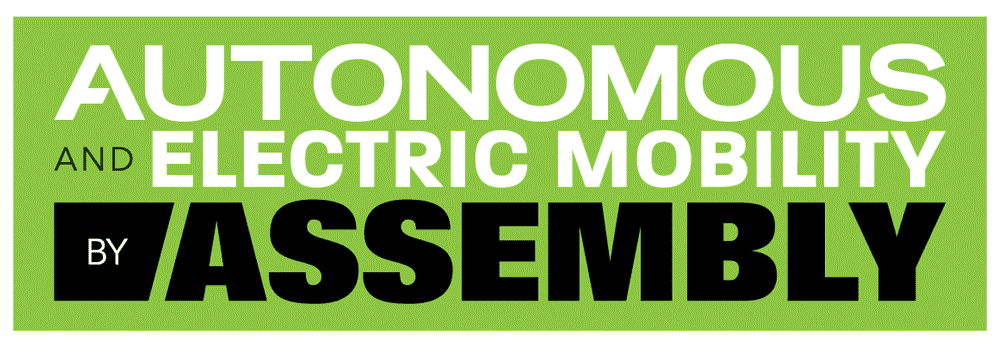