By Austin Weber, Senior Editor // webera@bnpmedia.com
Charging Lithium-Ion Cells at Different Rates Boosts Battery Packs
AV/EV tech trends
Engineers at Stanford University have developed a new way to make lithium-ion battery packs last longer and suffer less deterioration from fast charging. Photo courtesy General Motors
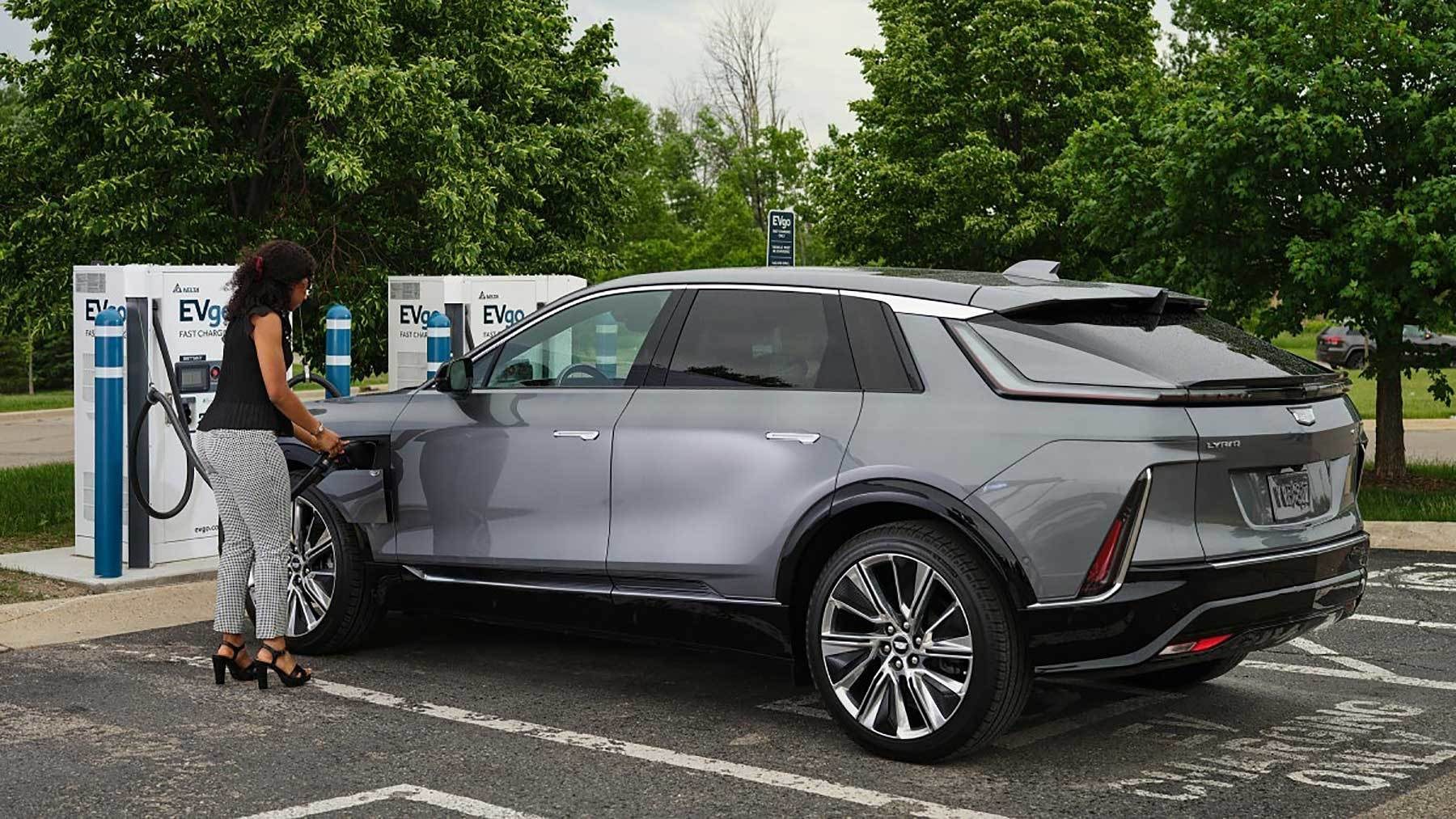
Engineers at Stanford University have developed a new way to make lithium-ion battery packs last longer and suffer less deterioration from fast charging. It could enable electric vehicle batteries to handle more charge cycles and last longer.
The key is to actively manage the amount of electrical current flowing to each cell in a pack, rather than delivering charges uniformly. Initial simulations suggest batteries managed with the new technology could handle at least 20 percent more charge-discharge cycles, even with frequent fast charging, which puts extra strain on the battery.
Most previous efforts to prolong EV battery life have focused on improving the design, materials and manufacturing of single cells. It has been based on the premise that, like links in a chain, a battery pack is only as good as its weakest cell.
However, while weak links are inevitable due to manufacturing imperfections and because some cells degrade faster than others as they’re exposed to stresses like heat, they don’t need to bring down the whole pack. The key is to tailor charging rates to the unique capacity of each cell to stave off failure.
“If not properly tackled, cell-to-cell heterogeneities can compromise the longevity, health and safety of a battery pack and induce an early battery pack malfunction,” says Simona Onori, Ph.D., an assistant professor of energy science engineering at Stanford University. “Our approach equalizes the energy in each cell in the pack, bringing all cells to the final targeted state of charge in a balanced manner and improving the longevity of the pack.”
The typical warranty for EV batteries is eight years or 100,000 miles. Though battery packs routinely outlast their warranty, Onori believes consumer confidence in EVs could be bolstered if expensive battery pack replacements became rare. A battery that can still hold a charge after thousands of recharges could also spur the electrification of long-haul trucks.
Onori and her colleagues have focused their R&D efforts on single lithium-ion cells, which typically don’t lose charge capacity as quickly as full battery packs do. As a first step, they crafted a high-fidelity computer model of battery behavior that accurately represented the physical and chemical changes that take place inside a battery during its operational life. Some of these changes unfold in a matter of seconds or minutes, while other take months or years.
“To the best of our knowledge, no previous study has used the kind of high-fidelity, multi-timescale battery model we created,” claims Onori, who serves as director of the Stanford Energy Control Lab.
Simulations with the model suggest that a modern battery pack can be optimized and controlled by embracing differences among its constituent cells. Onori believes the model could be used to develop battery management systems that can be easily deployed in existing vehicle designs.
“Lithium-ion batteries have already changed the world in so many ways,” says Onori. “It’s important that we get as much as we possibly can out of this transformative technology and its successors to come.”
New Headlight Design Incorporates Lidar and Radar Sensors
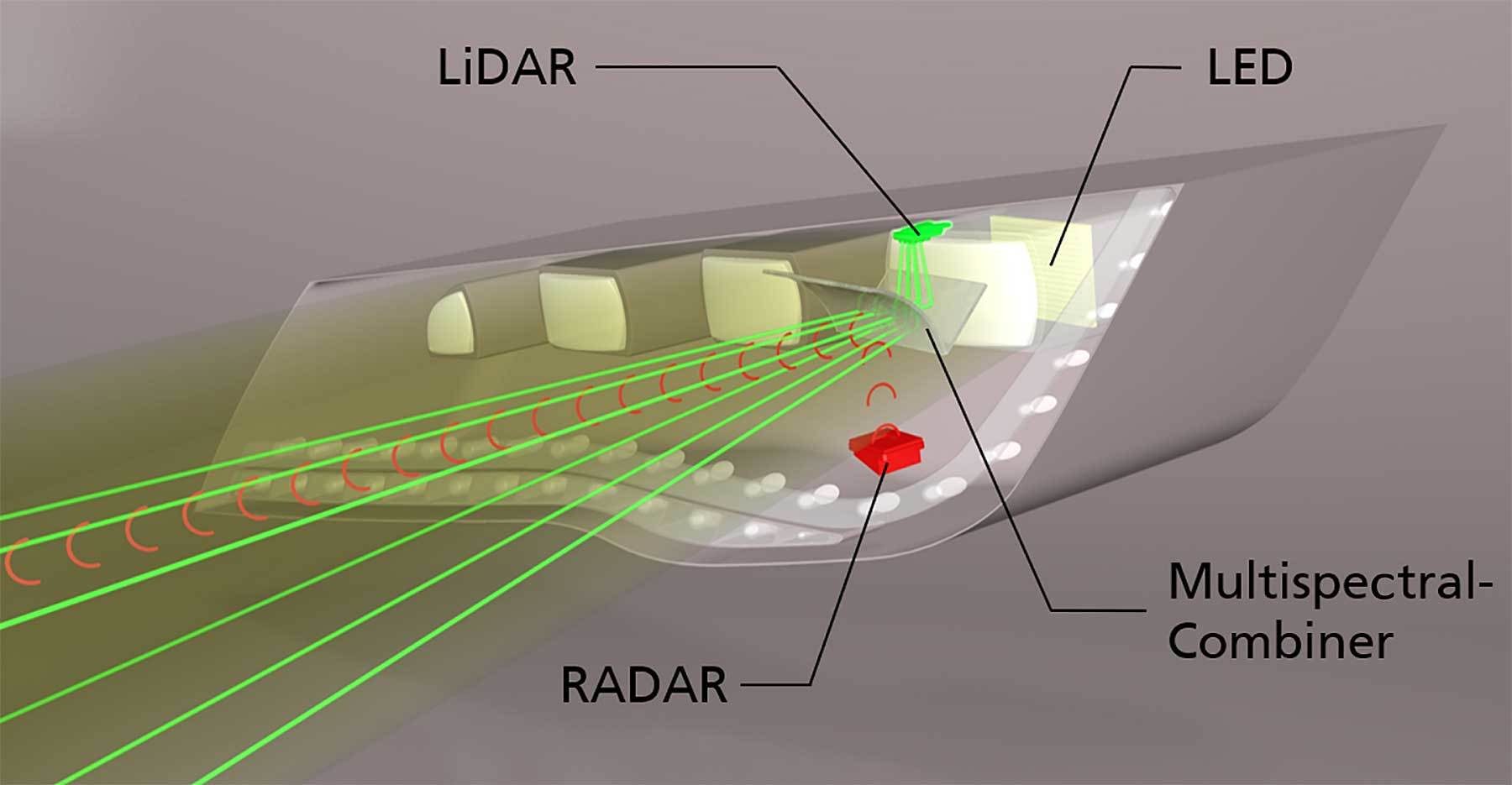
Future headlights may be equipped with multispectral combiners for coaxially merging optical light, lidar (red) and radar (green) beams. Illustration courtesy Fraunhofer FHR
Humans use their eyes and ears to monitor a variety of traffic situations and potential hazards. For self-driving vehicles to do the same thing, they need multiple sensors. As the number of sensors they contain increases, however, packaging becomes a big challenge for engineers.
A team of engineers at the Fraunhofer Institute for High Frequency Physics and Radar Techniques (FHR) are tackling the challenge. The Smart Headlight project aims to create a method of installing sensors that is both space-saving and as subtle as possible, without compromising function or performance.
The goal is to develop a sensor-integrated headlight for driver assistance systems that makes it possible to combine a range of sensor elements with adaptive light systems. This will improve sensors’ ability to identify objects on the road, which could improve current electronic brake assist or distance control systems and future fully autonomous systems.
“We’re integrating radar and lidar sensors into headlights that are already there anyway,” says Tim Freialdenhoven, an engineer at Fraunhofer FHR working on the R&D project. “What’s more, they’re the parts that ensure the best possible transmission for optical sensors and light sources, and are able to keep things clean.
The first stage in creating headlight sensors involves designing a lidar system that is suitable for integration into automotive technology. Among other things, the light beamed onto the road by the headlight cannot be impeded by the two additional sensors, even though the LEDs that are responsible for the light are located far back in the headlight.
Freialdenhoven and his colleagues are positioning the lidar sensors at the top and the radar sensors at the bottom of the headlight casing. At the same time, the beams from both sensor systems need to follow the same path as the LED light—something that is made more difficult by the fact that all the beams involved have different wavelengths.
The visible light from the headlight measures in the region of 400 to 750 nanometers, while infrared lidar beams range from 860 to 1,550 nanometers, close to the visible range. Radar beams, on the other hand, have a wavelength of 4 millimeters.
“These three wavelengths need to be merged coaxially,” explains Freialdenhoven. “This is where a multispectral combiner comes in. Guiding the beams coaxially in this way is crucial for preventing parallax errors, which are complicated to untangle.”
Arranging the sensors next to one another would take up significantly more space than a coaxial configuration, so the Fraunhofer engineers are getting around this using bicombiners. To combine LED light and lidar, this technology uses a dichroic mirror with a special coating that guides the two beam bundles along a single axis by means of wavelength-selective reflection.
The same effect happens in the second combiner, where the LED light, lidar and radar are combined. Because radar sensors are already in widespread use in the automotive industry, Freialdenhoven says bicombiner designs have to allow manufacturers to continue using existing sensors without the need for modifications.
Smaller light modules, more compact lidar sensors and integrated radar sensors will make it possible to create multi-sensor concepts. As a result, future autonomous vehicles may be able to not only detect a person, but also analyze their speed, how far away they are and the angle at which they are positioned in relation to the vehicle.
Magnetic Field Helps Thick Battery Electrodes Tackle EV Challenges
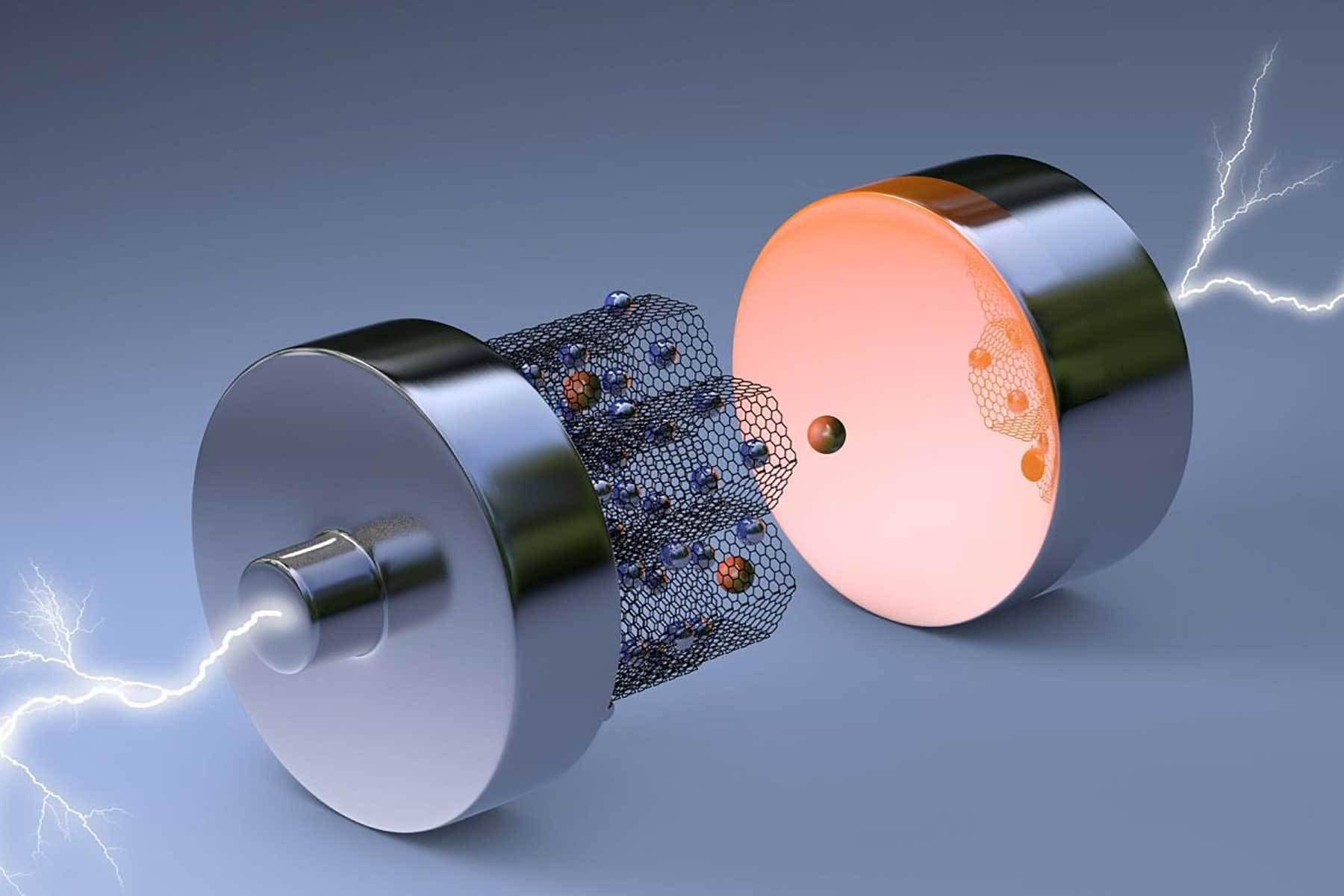
A new type of electrode for lithium-ion batteries could unleash greater power and faster charging. Illustration courtesy University of Texas
Two of the biggest challenges facing electric vehicles are limited range and slow recharging. Engineers at the University of Texas have developed a new type of electrode for lithium-ion batteries that could unleash greater power and faster charging.
They created thicker electrodes using magnets to create a unique alignment that sidesteps common problems. The result is an electrode that could potentially facilitate twice the range on a single charge for an EV, compared with a battery using an existing commercial electrode.
“Two-dimensional materials are commonly believed as a promising candidate for high-rate energy storage applications, because it only needs to be several nanometers thick for rapid charge transport,” says Guihua Yu, Ph.D., a mechanical engineering professor at the University of Texas. “However, for thick-electrode-design-based next-generation, high-energy batteries, the restacking of nanosheets as building blocks can cause significant bottlenecks in charge transport, leading to difficulty in achieving both high energy and fast charging.”
Thin, two-dimensional materials are used as the building blocks of the electrode, stacking them to create thickness and then using a magnetic field to manipulate their orientations. Yu and his colleagues used commercially available magnets during the fabrication process to arrange the materials in a vertical alignment, creating a fast lane for ions to travel through the electrode.
Typically, thicker electrodes force the ions to travel longer distances to move through the battery, which leads to slower charging time. The horizontal alignment of the layers of material that make up the electrode force the ions to snake back and forth.
According to Yu, the new electrode shows superior electrochemical performance, partially due to the high mechanical strength, high electrical conductivity and facilitated lithium-ion transport.
In addition to comparing their new electrode with a commercial electrode, the engineers fabricated a horizontally arranged electrode using the same materials for experimental control purposes. They were able to recharge the vertical thick electrode to 50 percent energy level in 30 minutes, compared to 2.5 hours with the horizontal electrode.
The long-term goal of the R&D project is to apply the vertically organized layers to different types of electrodes using other materials. Yu believes this could enable fast-charging, high-energy batteries in future EVs.
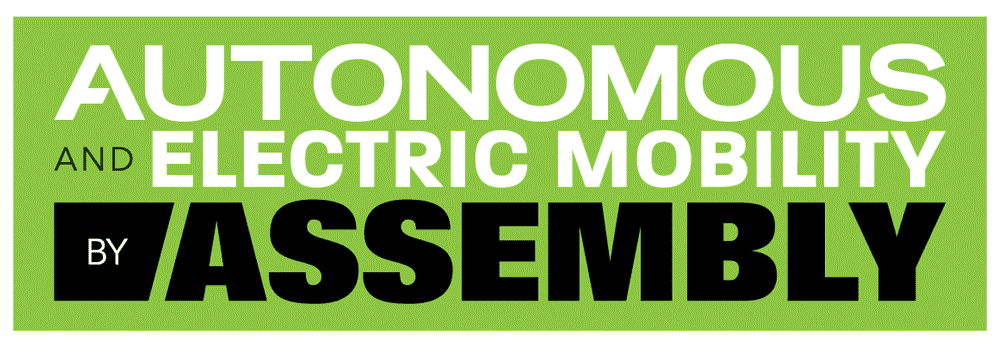