CONTACT
Austin
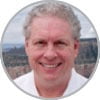
Electric vehicle factories must reduce downtime and speed up time to market.
Maximizing EV Productivity With Industry 4.0
Cliff Rice // Global Industry Consultant, Electric Vehicle and Battery Manufacturing // Rockwell Automation
Today, automakers are under constant pressure to reduce downtime, boost productivity and get to market as quickly as possible. Illustration courtesy Rockwell Automation
Electric vehicle factories must reduce downtime and speed up time to market.
Maximizing EV Productivity With Industry 4.0
Electric vehicle manufacturers are deploying Industry 4.0 technology to improve visibility into production processes and enable assemblers to make better, faster decisions. An integrated automation strategy that uses digital twins, predictive maintenance and other cutting-edge tools can enable smart production.
The EV industry is rapidly evolving alongside increasing demand for environmentally friendly automobiles. According to projections, EV sales in the U.S. could reach 40 percent of total car sales by 2030.
To compete in this crowded and fast-growing market, automakers must produce high-quality vehicles with minimal delay. However, the shift from traditional internal combustion engine (ICE) to EV manufacturing presents significant challenges for engineers that will impact productivity, downtime and time to market.
Smart features and downloadable updates make EVs more like consumer electronic products such as cell phones. As a result, manufacturers have to adopt a smarter, more connected production approach.
Even legacy automakers may find hidden challenges as they transition to EVs. For example, ICE components differ greatly from EV components such as battery modules, battery packs, electric motors and drivetrains.
The same production and procurement strategies that were effective in ICE manufacturing may not be the best fit for facilities that make EVs. These changes take time, human resources and money to implement properly, which can be a challenge when companies are fighting time to be first to market with a new product.
The challenge for battery manufacturers is even more intimidating. Battery costs are falling and demand for EVs is rising, meaning a significant demand for batteries is imminent. Battery manufacturers must be able to quickly and easily scale production up and down as demand fluctuates in the short term, while being prepared to ramp up quickly in the future to meet increased demand.
Cliff Rice // Global Industry Consultant for Electric Vehicle and Battery Manufacturing, Rockwell Automation
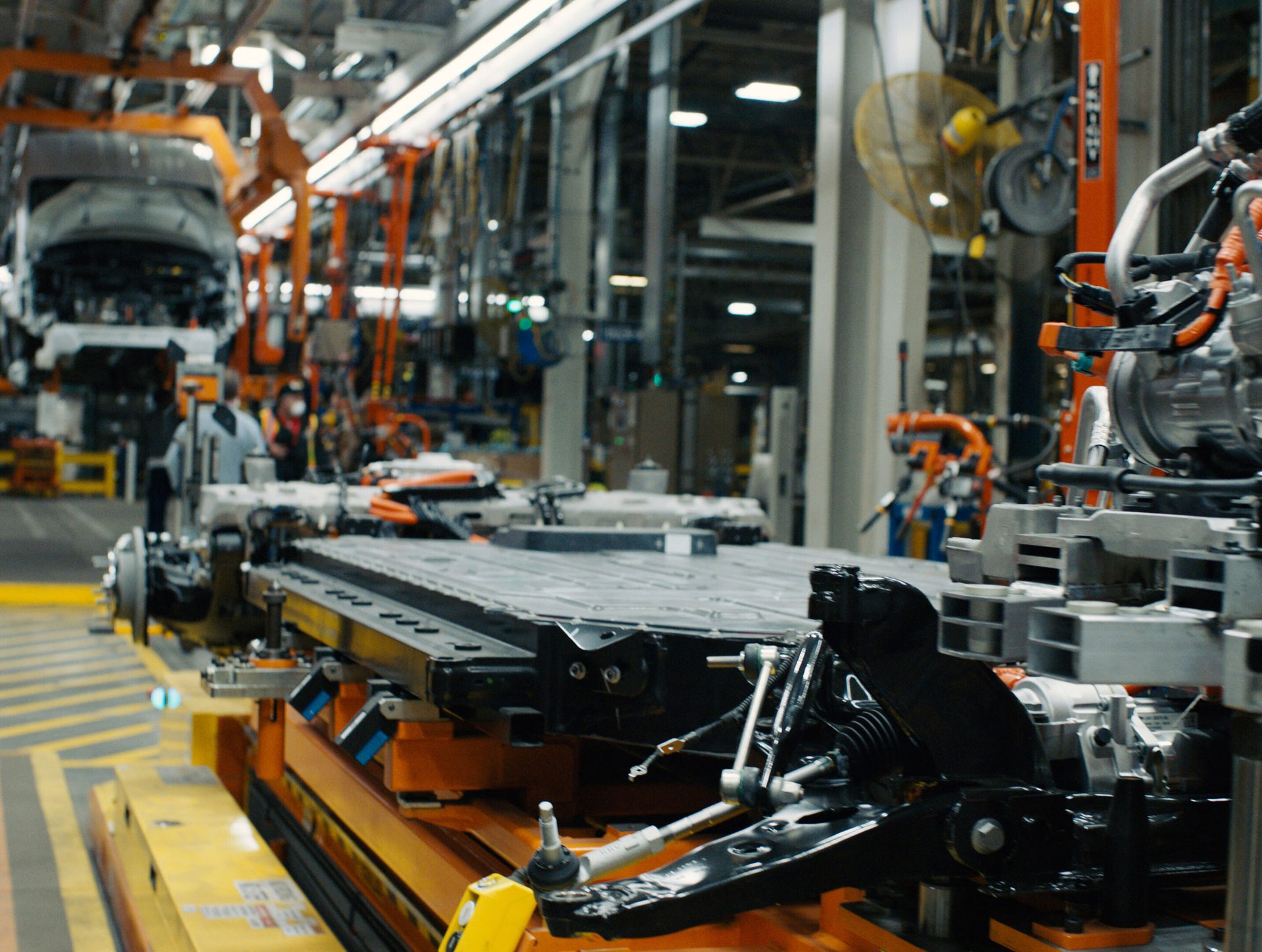
The same production and procurement strategies that were effective in ICE manufacturing may not be the best fit for facilities that make EVs. Photo courtesy Ford Motor Co.
Maximizing Productivity
To maximize productivity, EV manufacturers should deploy Industry 4.0 technology. This strategy seamlessly connects data across an entire organization. It improves visibility into production processes and enables workers to make better and faster decisions.
For example, smart machines can help teams create more efficient process workflows and more quickly identify the cause of production delays and errors, leading to faster resolution and remediation. Advanced analytics that monitor asset data over time can help companies predict where problems may occur, so maintenance teams can prevent delays from occurring before they even happen.
An integrated automation architecture, which uses control and information systems that share a common network, control platform, data structure and design environment, also facilitates smart production.
It provides access to the right information at the right time to make important operational decisions due to the single network feature and shared data structure, which connects plant systems across the enterprise. Common design environments make it easier to integrate new equipment into factories, allowing for more efficient installations, operations and maintenance.
To keep up with growing demand and evolving vehicle technologies, EV production operations must be as nimble as they are productive. By creating smart, flexible and scalable operations, manufacturers can reduce downtime and get more products to market faster.
Digital Technology
The latest digital technologies can help maintain and even improve productivity during this transition period. Examples include digital twins, independent cart technology and predictive maintenance.
Digital twins are virtual replicas of physical vehicles, components and manufacturing processes that enable real-time monitoring and analysis. Engineers can make adjustments, simulate scenarios and troubleshoot issues without disrupting the actual assembly line. This not only enhances the quality of EVs, but also minimizes downtime and improves efficiency.
For example, a digital twin allows the testing of new products and configurations before real-world implementation to identify and eliminate downtime risks. Augmented reality knowledge-capture tools also allow the sharing of step-by-step instructions to help cut training time and increase operator effectiveness, further reducing downtime.
Independent cart technology (ICT) allows manufacturers to move components around an assembly plant faster and more precisely than traditional conveyors. This technology can significantly expedite production processes, especially in critical areas like battery cell and pack production, where high-speed conveyance can be a challenge. ICT offers the potential for higher line speeds and reduced downtime, enabling manufacturers to bring EVs to market more quickly.
Independent cart technology allows for the movement of small components, such as battery modules and electric motors, or even full-size car bodies, around a plant faster and more precisely than traditional mechanical systems or human labor. With fewer moving parts, these systems can reduce maintenance needs and improve uptime by enabling changeovers to take place with the push of a button.
Predictive maintenance integrates advanced sensors, data analytics and machine learning technology. It enables manufacturers to continually monitor the condition of motors, drives and other critical components on their assembly lines. This proactive approach allows for the early detection of potential issues or wear and tear, which reduces downtime and prevents costly breakdowns. As a result, EV production lines can maintain a consistent workflow, minimizing disruptions and ensuring that vehicles are produced at a steady rate.
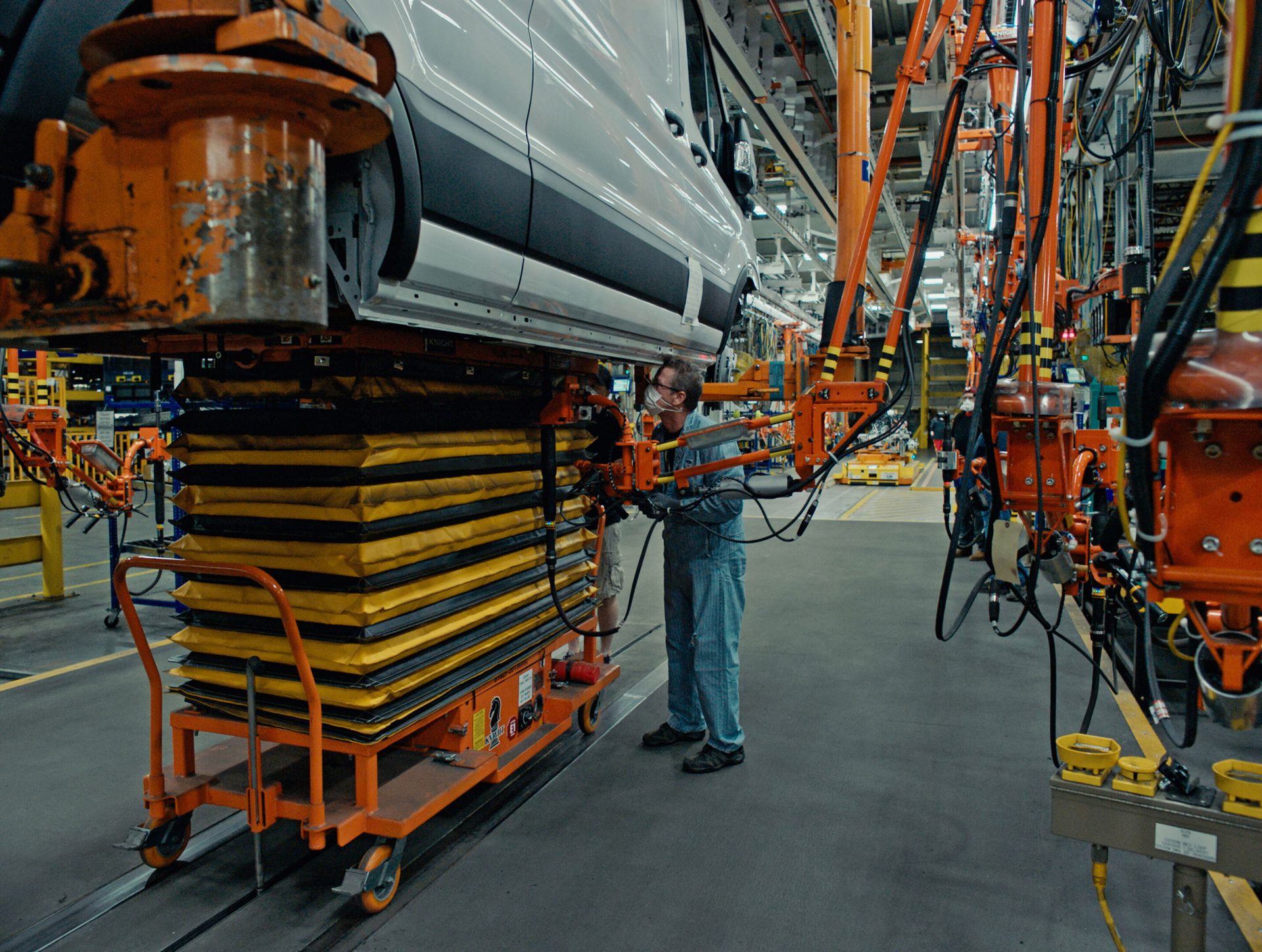
Electric vehicle manufacturers are deploying Industry 4.0 technology to enable assemblers to make better, faster decisions. Photo courtesy Ford Motor Co.
Data Collection and Analysis
Industry 4.0 technology has revolutionized the manufacturing landscape by enabling engineers and assemblers to improve productivity. The integration of the Internet of Things (IoT) and sensor technology allows real-time data collection from machinery and equipment on the factory floor. This data provides engineers with a wealth of information, such as performance metrics and operational status, which enables them to monitor and analyze processes in real-time. With this instant access to critical data, engineers and assemblers can quickly identify issues, anticipate maintenance needs and optimize production, leading to more informed decision-making.
Advanced data analytics and machine learning algorithms process the vast amounts of data generated by Industry 4.0 technology. Engineers can leverage predictive analytics to forecast potential equipment failures and quality issues, allowing them to take proactive measures and prevent costly downtime or defects. These technologies can also help in demand forecasting, resource allocation and production planning, allowing for better decision-making in terms of resource optimization and production scheduling.
Collaborative platforms and cloud-based solutions facilitate communication and data sharing among engineering teams, regardless of their geographical locations. This interconnectedness fosters collaboration and knowledge exchange, enhancing the collective decision-making capabilities of engineers and assemblers. With improved access to expertise and information, manufacturing professionals can make better and faster decisions, ultimately resulting in more efficient and competitive production processes.
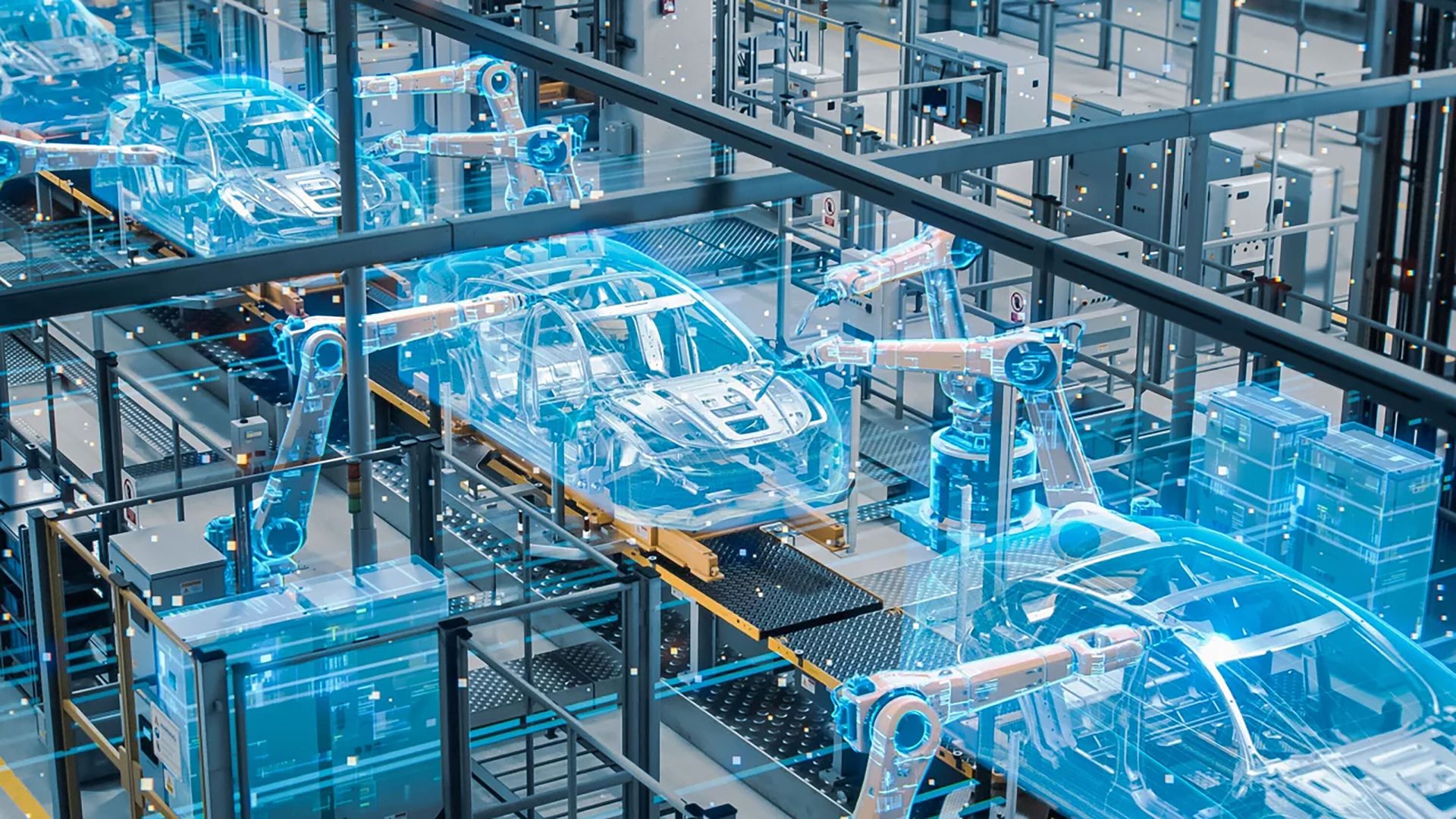
An integrated automation strategy that uses digital twins and other cutting-edge tools can enable smart production. Illustration courtesy Rockwell Automation
MES and MOM
Manufacturing execution system (MES) and manufacturing operations management (MOM) applications can address specific manufacturing challenges that lead to downtime. For example, a quality application can track, identify and alert when a machine’s or operator’s processes do not adhere to quality standards.
These digital solutions provide plant managers with the ability to optimize production schedules, monitor production metrics and identify inefficiencies or bottlenecks in real time. MES and MOM applications are essential to EV manufacturers looking to optimize operations and remain competitive in a rapidly changing industry.
In addition, MOM applications can help manufacturers implement best practices and standardize processes across multiple production lines and facilities. This ensures that products are consistently manufactured to the same high-quality standards, regardless of location. MOM software can also improve collaboration and communication between departments, such as engineering and production, to streamline workflows and reduce errors.
Overall, MES and MOM applications are essential tools for engineers looking to optimize their operations and remain competitive. As manufacturing processes become more complex and interconnected, these software applications will only become more critical in ensuring efficient and effective EV production.
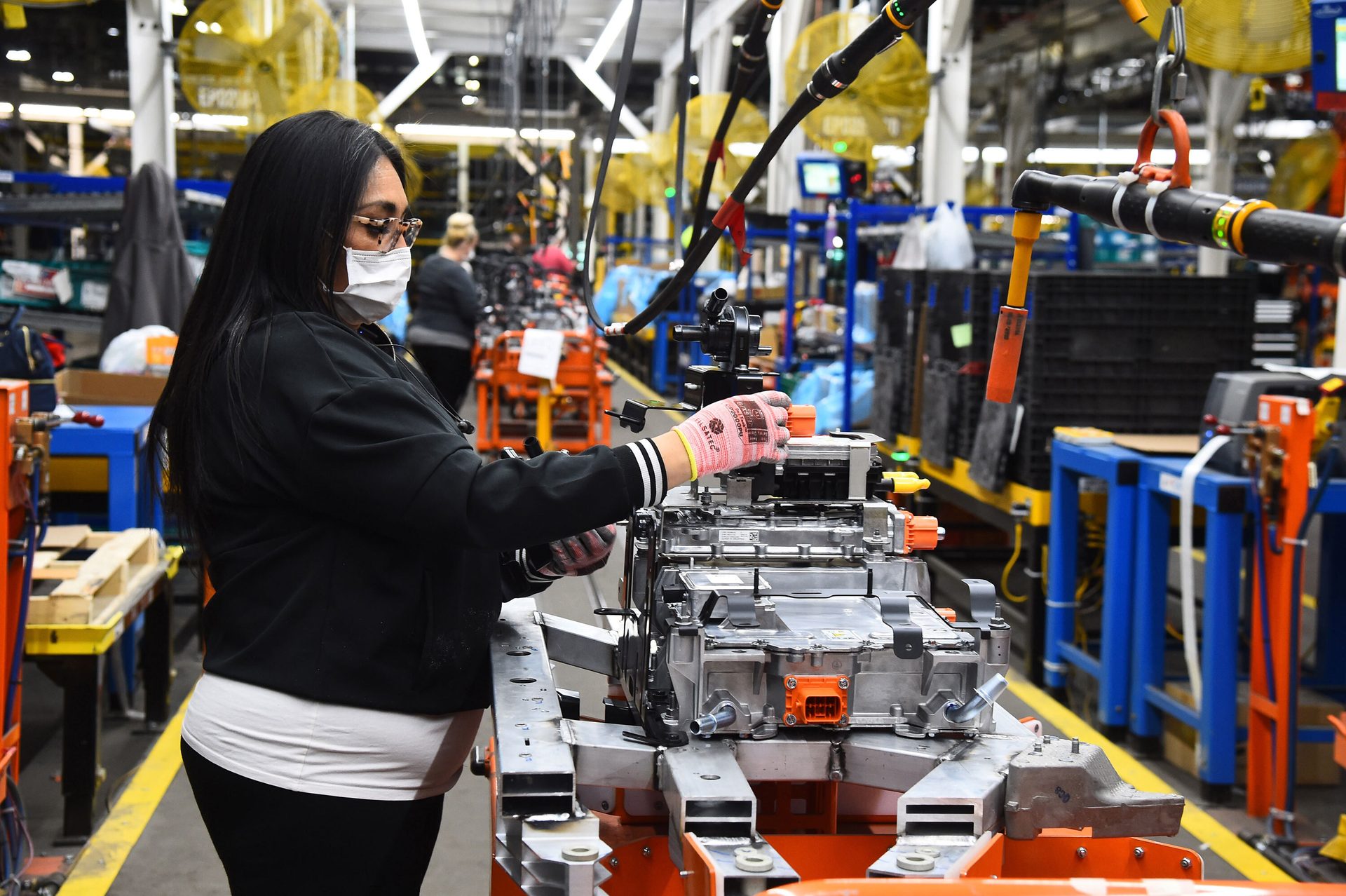
Electric vehicle manufacturers must be able to quickly and easily scale production up and down as demand fluctuates. Photo courtesy Ford Motor Co.
Speeding up Time to Market
To gain a competitive edge in the EV market, it is critical for manufacturers to use smart tools and strategies to optimize plant processes. Manufacturers can use scalable infrastructure to converge networks, connect plant and business systems and give workers access to the information they need to make better decisions.
Modular and scalable MES applications help automakers understand and manage production without investing in an enterprise-wide MES solution, which can be too costly for EV startups. Manufacturers can start at the machine or work-area level with a single MES application module and eventually add other applications or scale up to a full MES.
Today, automakers are under constant pressure to reduce downtime, boost productivity and get to market as quickly as possible. With the right production strategy, they can stay ahead of the competition, meet industry pressures and satisfy customer demand.
Maximizing productivity and reducing downtime are key components of an EV production strategy that speeds time to market. This can be achieved by implementing Industry 4.0 technology. By focusing on maximizing productivity, reducing downtime and speeding up time to market, companies can stay ahead of the curve and position themselves for success in this fast-growing and increasingly competitive industry.
DECEMBER 2023 | ASSEMBLYMAG.com
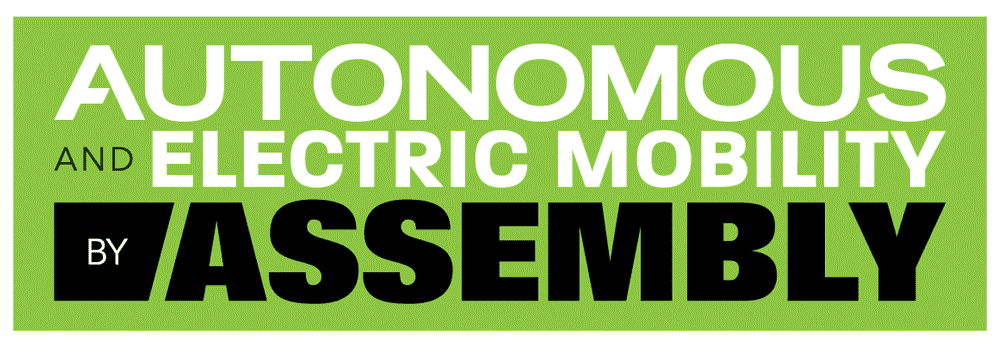