New Report Touts Benefits of 48-Volt Electrical Systems
NEWS
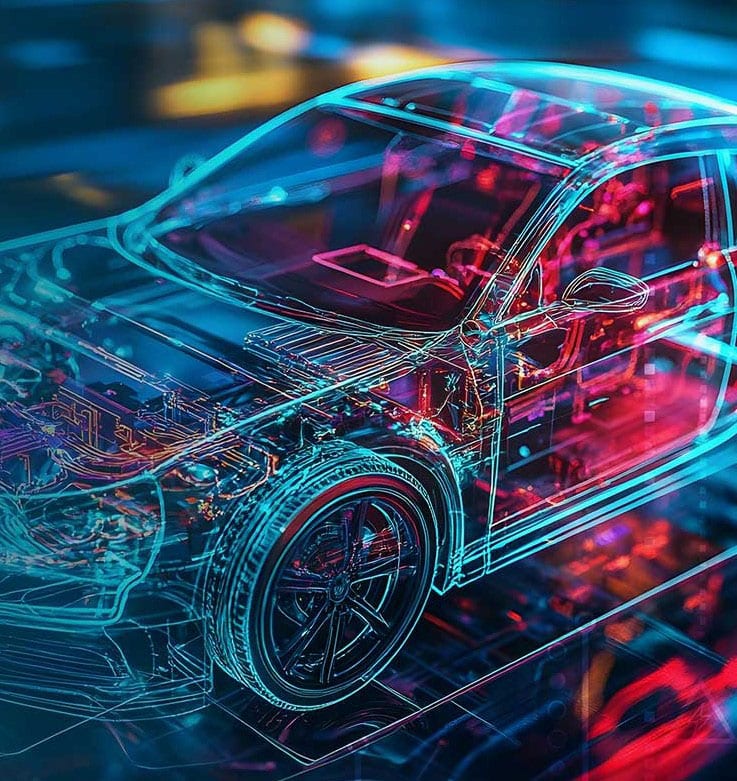
Higher powered electrical systems will require heightened connector performance and reliability. Illustration courtesy Molex LLC
LISLE, IL—Automotive engineers have been intrigued by the benefits of 48-volt electrical systems for more than a decade. However, despite numerous advantages, the auto industry has been slow to adopt the technology.
A new report from Molex LLC, a leading supplier of connectors, adapters and cable accessories, examines the challenges of transitioning from traditional 12- to 48-volt architectures.
According to “Rewiring the Road: Harnessing the Power of 48V,” the higher powered technology can improve vehicle performance, efficiency, functionality and comfort. But, to unlock these benefits, significant hurdles need to be cleared, including requirements for upfront investments in components, system integration and compatibility with current electrical systems.
“48V technology holds great promise, but the path forward requires industry-wide collaboration to overcome technical obstacles and establish industry standards,” says Scott Whicker, senior vice president and president of transportation innovative solutions at Molex. “We are working with partners across the automotive ecosystem to accelerate 48V adoption.
“Together, we can optimize system integration, reduce development costs, and speed time to market for power system components and connectivity [systems], ensuring reliable and efficient power delivery,” explains Whicker. He claims that 48-volt systems are adaptable with both traditional internal combustion engine vehicles and fully electric models.
By quadrupling system voltage, the delivery of higher currents also increases power efficiencies in the critical sensors, actuators and control units needed for advanced driver assistance systems, while paving the way for fully autonomous driving.
However, the higher voltage levels in 48-volt systems can lead to increased electromagnetic interference (EMI), making it more challenging to shield against EMI than lower voltage systems. Equally important are wiring and harness designs, as higher current and voltage requirements introduce challenges related to weight, space and cost.
Higher powered electrical systems will require heightened connector performance and reliability, as well as advanced materials with superior electrical and thermal properties. Design innovations, such as zonal architectures, will be critical for improving power distribution, lowering wiring complexity and boosting system reliability.
Structural Battery Could Pave the Way for Lightweight EVs
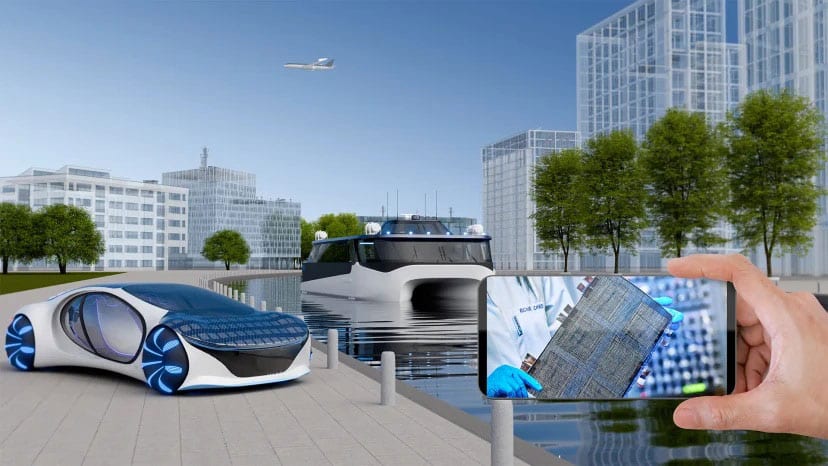
Structural batteries could increase the driving range of electric vehicles. Illustration courtesy Chalmers University of Technology
GOTHENBURG, Sweden—Engineers at the Chalmers University of Technology here have developed a massless energy storage device that functions as both a battery and a load-bearing structure. The structural battery could increase the driving range of electric cars and enable lightweight airplanes, ships and trucks, in addition to a variety consumer electronic devices.
Structural batteries are materials that, in addition to storing energy, can carry loads. In this way, the battery material can become part of the actual construction material of a product, which means that much lower weight can be achieved.
The Chalmers battery is made out of carbon-fiber composite that is as stiff as aluminum and energy-dense enough to be used commercially. It has an energy density of 30 watt-hours per kilogram.
"Investing in light and energy-efficient vehicles is a matter of course if we are to economize on energy and think about future generations,” explains Leif Asp, Ph.D., a materials science professor who is leading the R&D project. “We have made calculations on electric cars that show that they could drive for up to 70 percent longer than today if they had competitive structural batteries.”
Asp says there is still a lot of engineering work to be done before the batteries can be mass produced. However, a Swedish start-up company called Sinonus AB is in the process of developing the technology.
Honda Outlines Key Production Processes Behind New Line of EVs
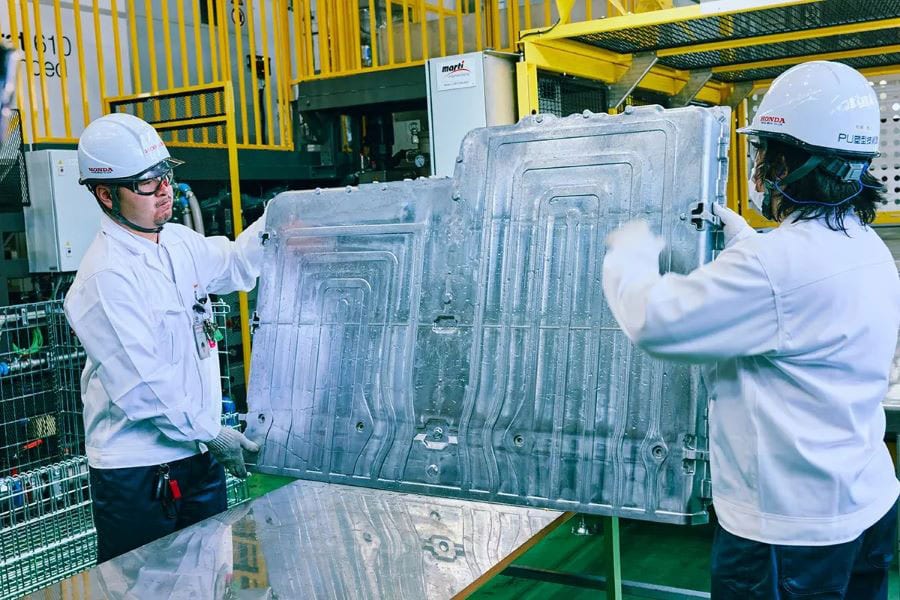
Megacasting involves molding large cast parts such as one-piece battery enclosures that eliminate seams. Photo courtesy Honda Motor Co.
TOKYO—Honda 0 Series is the automaker’s new approach to electric vehicle development, which is focusing on the theme of “thin, light and wise.” The goal of the R&D project is to minimize battery size while providing sufficient cruising range and a nimble driving experience that transcends the existing image of EVs.
Honda engineers are focusing their efforts on four core production technologies, including megacasting and friction stir welding.
Megacasting involves molding large cast parts such as one-piece battery enclosures that eliminate seams. A new battery case, which traditionally consists of more than 60 parts, has been reduced to only five parts, making it possible to produce a high-quality, thin and light enclosure.
3D Friction Stir Welding (FSW) is being applied to two processes in the manufacturing of battery cases. The first is the process of joining parts made by megacasting to form the case enclosure, and the second is the process of joining the water jacket cover, which is necessary to provide the battery with cooling. The technology uses only the frictional heat between the rotating rod-shaped tool and the joint to soften and join the aluminum parts.
“We believe that FSW is an important way to increase the flexibility and productivity of our products,” says Atsushi Yoshida, a Honda engineer working on the project. “As there is less damage to the base material from heat than with conventional welding, joints can easily be maintained at a high quality, making the entire battery case thinner and lighter while ensuring joint strength and airtightness.
“With battery case manufacturing, we focused on shortening the processes,” explains Yoshida. “By setting the joining conditions according to characteristics such as strength that vary by material, and optimizing tool movements and other factors according to the shape of the joints, we were able to stabilize the quality of the joints while minimizing the amount of preprocessing required.”
Honda is also experimenting with a flex-cell production system where all assembly tasks are performed by one person in a fixed location. The revolutionary production system avoids stoppages of the entire line by arranging multiple identical facilities in parallel, stabilizes production volume, improves production efficiency by eliminating waiting time for product transfer, and realizes more efficient capital investment.
“Furthermore, it can accommodate future changes and evolution of production lines,” says Rikki Ito, a body production engineer at Honda. “Since each process has to be connected in order to build a flex-cell production system, communication among [operators] was the most difficult aspect of the project. We were able to realize this system by building good human relationships….”
When joining body parts, it is often difficult to join ultra-high tensile strength steel plates and decorative exterior plates (thin soft steel plates) using conventional spot welding, due to spatter and loss of strength which occurs because of the difference in thickness and materials.
To address this problem, Honda engineers have developed constant DC chopping (CDC) welding technology that uses inverter-controlled current. “Conventional spot welding could not be used with light and strong materials, leading to an increase in the weight of body components, while CDC welding technology has improved material efficiency and weight reduction,” explains Xihao Tan, a Honda engineer who specializes in metal joining processes.
“At first, welding machine manufacturers said this technology was impossible, because of its very short time control of approximately 10 microseconds,” says Tan. “But, ‘if it doesn’t exist, we make it’ is Honda’s way. We did not give up, but worked out how to make it real.”
Cat Eyes Inspire Vision System for Autonomous Vehicles
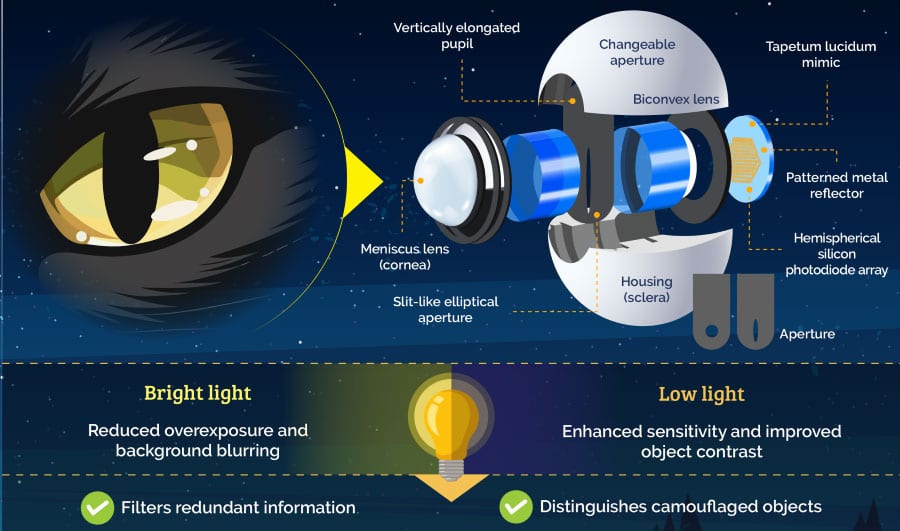
An advanced vision system based on cat eyes can enhance accuracy in challenging environments. Illustration courtesy Gwangju Institute of Science and Technology
GWANGJU, South Korea—Cats have an uncanny ability to see and detect objects in various lighting conditions, including both bright light and darkness. Their eyes feature a unique shape and reflective surface that reduces glare in bright environments and boosts sensitivity in low-light scenarios.
That distinctive feline trait inspired engineers at the Gwangju Institute of Science and Technology (GIST) to develop a vision system that enhances accuracy in challenging environments. The breakthrough could lead to smarter, more efficient autonomous systems.
Cat eyes are uniquely adapted. During the day, vertical slit-shaped pupils help them focus and reduce glare. At night, their pupils widen to let in more light, and a reflective layer called the tapetum lucidum boosts night vision, giving feline eyes a familiar glow.
Potential applications for the GIST vision system include autonomous vehicles and humanoid robots, which often struggle to "see" well in different environments, such as bright sunlight, low light or when objects blend into complex backgrounds.
“Robotic cameras often struggle to spot objects in busy or camouflaged backgrounds, especially when lighting conditions change,” says Young Min Song, Ph.D., a professor of electrical engineering and computer science at GIST who worked on the project. “Our design solves this by letting robots blur out unnecessary details and focus on important objects.”
The system includes a slit-like aperture that, like a cat’s vertical pupil, helps filter unnecessary light and focus on key objects. It also uses a special reflective layer similar to the one found in cat eyes that improves visibility in low-light conditions.
“The advanced vision system promises to elevate the precision of drones, security robots and self-driving vehicles, enabling them to adeptly navigate intricate environments and execute tasks with unparalleled accuracy,” explains Song. “From search-and-rescue operations to industrial monitoring, these cutting-edge robotic eyes stand ready to complement or even replace human efforts in a variety of critical scenarios.”
New EV Battery Enclosure Lowers Carbon Emissions
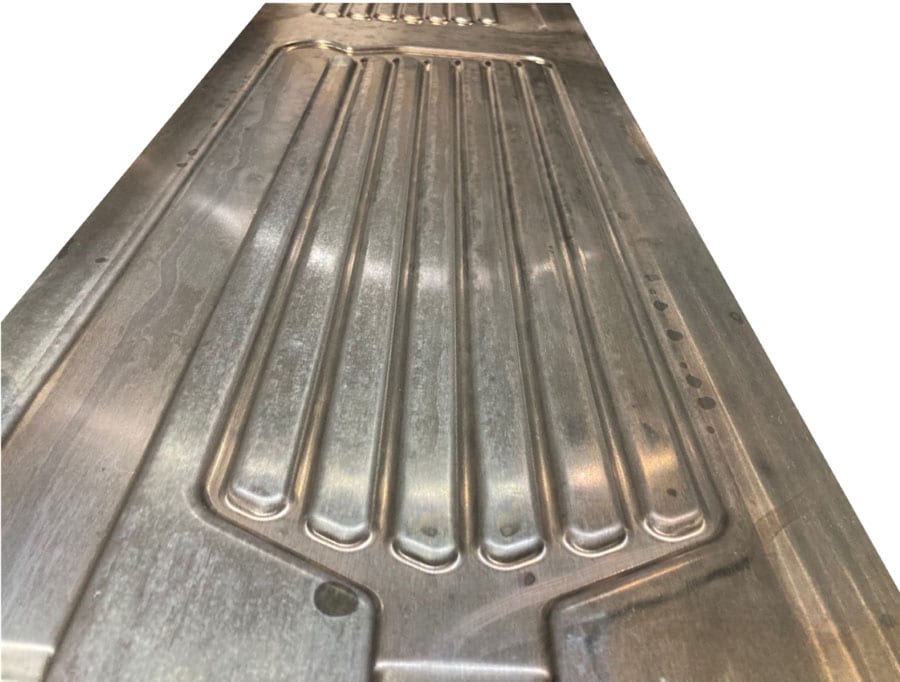
A European research project called COOLBat is developing next-generation battery enclosures for electric vehicles. Photo courtesy Fraunhofer Institute for Machine Tools and Forming Technology
CHEMNITZ, Germany—A European research project called COOLBat is developing next-generation battery enclosures for electric vehicles. The goal of the initiative is to improve charging power and range, while lowering environmental impact.
Engineers at the Fraunhofer Institute for Machine Tools and Forming Technology (IWU) are examining new ways to make battery enclosures lighter and cut carbon dioxide emissions by 15 percent. They aim to achieve this by combining individual systems, packing more functions into a smaller installation space, and using new heat-conductive materials and bio-based flame retardant coatings.
“Integrating new lightweight construction methods and more functions in a smaller installation space with fewer interfaces makes it possible to reduce weight while also cutting carbon emissions,” says Rico Schmerler, an engineer in the battery systems department at Fraunhofer IWU who is working on the project. “Reducing mass lets us increase energy density, and thus range, even as the number of battery cells stays the same. By making the enclosure lid out of a fiber composite material, we were able to reduce the mass by more than 60 percent compared to the reference out of steel.”
Another option for reducing weight is combining individual systems in the enclosure that previously performed thermal and mechanical functions separately. For example, cooling channels cast at the Fraunhofer Institute for Manufacturing Technology and Advanced Materials are incorporated directly into load-bearing structures such as cross beams.
The cooling unit function is combined with underride protection in a single component, the base plate. Aluminum foam inside the base plate absorbs the energy from stone impacts and accidents. Combined with a phase-change material, a kind of wax that can be used to store and later release a wealth of thermal and cooling energy, the aluminum foam also lowers the amount of energy needed to cool EV batteries.
According to Schmerler, this configuration protects battery cells from mechanical loads and overheating at once. A fluid flows through the channels, cooling the cells not only from below but also from the sides. This reduces the electricity needed to cool the cells and eliminates the need for cooling elements elsewhere in the vehicle.
“We’re focusing on functionally integrated structures,” explains Schmerler. “Tasks that used to be handled by different modules inside the battery are being integrated into a single component—the base assembly, in this case—to shrink the installation space and streamline interfaces. These base plates will provide protection from overheating and avert damage to the battery core in case of an accident.”
Schmerler and his colleagues are using batteries from a Mercedes-Benz EQS sport utility vehicle for their R&D project.
Mercedes-Benz Begins Assembling Electric Truck
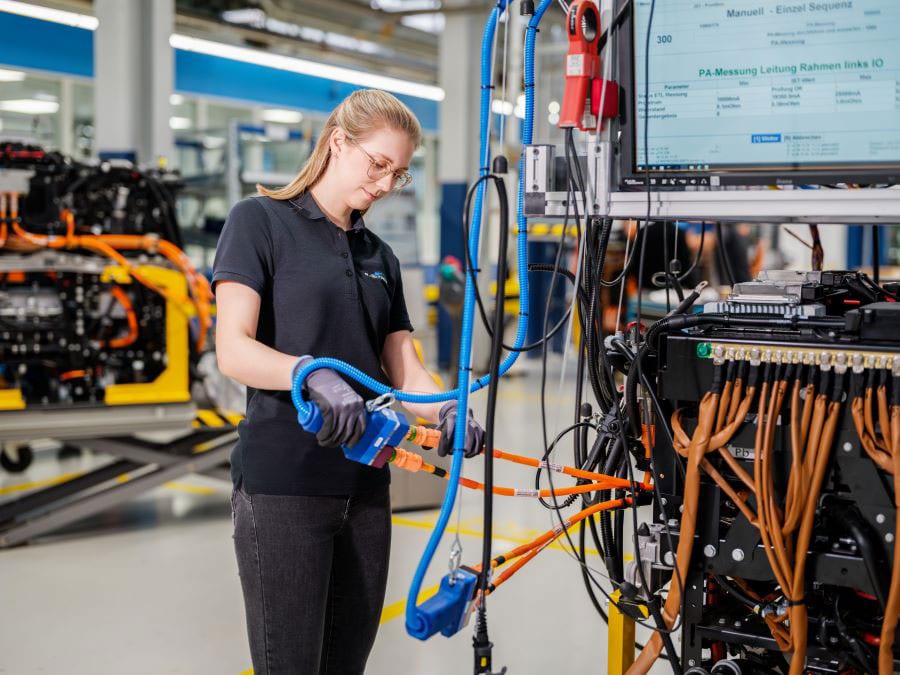
The “front box” is a complex module that contains several control units, high-voltage components and an electric air compressor. Photo courtesy Mercedes-Benz Trucks
MANNHEIM, Germany—Mercedes-Benz Trucks has begun assembling a key component of its new eActros 600 long-haul truck at its factory here. The “front box” is a complex module that contains several control units, high-voltage components and an electric air compressor. It’s located in the space previously occupied by an internal combustion engine.
In contrast to a traditional diesel engine, the front box doesn’t have a specific drive function, but contains a large number of components that are essential for the truck to operate. In total, there are more than 1,000 individual parts.
Packaging this high number of components in a very confined space was a challenge to engineers. They developed a “layered structure” in which the individual components are built up from bottom to top.
“The front box is an assembly-intensive unit for battery-powered vehicles,” says Andreas Moch, plant manager at Mercedes-Benz Mannheim. “After a successful prototype phase, we are now pleased to be able to move into series production.
“Our plant is the competence center for battery technology and high-voltage systems at Daimler Truck,” explains Moch. “With the start of production of the front box, we are already reaching the second milestone this year, after we opened our Battery Technology Center in the summer. We [have transformed the factory] and are making an important contribution to shaping the emission-free mobility of the future.”
Over a one-year period, extensive renovation work was carried out in a building that is more than 100 years old. Among other things, the floor surface, ventilation and lighting system was improved, while the support structure was rebuilt. A state-of-the-art assembly line with a logistics zone was then installed. “It offers a high degree of flexibility for different quantities, product variants and subsequent generations,” says Moch.
The front box assembly line consists of four consecutive production sections. Each contains various assembly stations, with the corresponding material zones and subassembly stations located to the side.
After each workstation, the front box passes through a quality gate, where the correct execution of the assembly process is verified before the next level is built. Once all quality gates have been successfully passed and the assembly quality has been confirmed in an end-of-line inspection, the front box is shipped to Mercedes-Benz’s final assembly line in Wörth.
All operators have been trained in a new high-voltage training center. According to Moch, the facility provides “a practical learning environment in which participants can gain comprehensive knowledge of the latest high-voltage and battery technologies. Innovative teaching methods are used for this purpose, such as virtual reality glasses and augmented reality technology.”
Other Mercedes-Benz factories involved in making electric drive components for the eActros 600 include the Gaggenau plant, which is producing shafts, gears and housing parts, and the Kassel plant, which is assembling axles and transmissions.
The eActros 600 features a 600-kilowatt hour battery and an in-house developed power train that enables it to achieve a range of 500 kilometers without intermediate charging.
DECEMBER 2024 | ASSEMBLYMAG.com
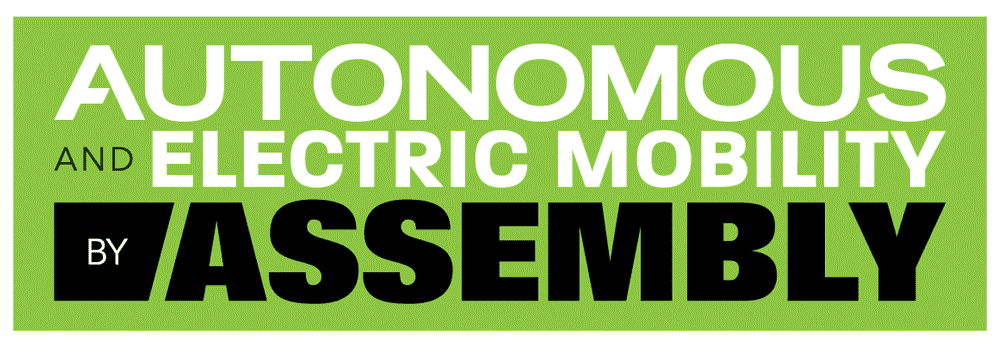