CONTACT
Austin
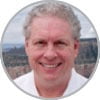
Flexible automation can help automakers solve production challenges.
Navigating EV Assembly Challenges to Improve Speed to Market
Mark Ziencina // Business Development Manager, Battery and EV // Bosch Rexroth Corp.
As automakers strive to expand production to meet surging EV demand, they need state-of-the-art automation. Illustration courtesy Bosch Rexroth Corp.
Flexible automation can help automakers solve production challenges.
Mark Ziencina
Business Development Manager, Battery and EV
Bosch Rexroth Corp.
Navigating EV Assembly Challenges to Improve Speed to Market
Whether building new production lines or converting existing internal combustion engine assembly plants to produce electric vehicles, automakers need a broad array of flexible, open and proven automation technologies. New technology and flexible systems can help improve speed to market by enabling manufacturers to quickly ramp up to meet surging demand.
Legacy and startup automakers need automation to boost quality and productivity. Along with many common assembly workflows, they face new challenges associated with scaling up battery pack, motor and e-axle production.
EV Welding Challenges
Electric vehicles have replaced engines, gas tanks and transmissions with electric motors, regenerative braking technology and advanced battery packs. Assembling these new components presents unique challenges. However, at the same time, there are assembly processes common to both EV and ICE assembly lines.
Like traditional vehicle assembly, EVs contain body parts that are welded using high-speed six-axis robots. Extremely precise control of weld quality is vital to the long-term performance of a vehicle. Automakers are using more aluminum, high-strength steel, and other next-generation materials to help reduce weight and improve run time per battery charge.
To address these complex assembly processes, a new generation of intelligent welding controllers is now available. They provide greater control than was previously achievable. Some improved capabilities include expanding the number of available heat blocks available so engineers can customize welding to specific throughput and material characteristics.
For example, the PRC7000 adaptive resistance welding controller can store up to 10,000 welding programs that can be easily configured via a drag-and-drop interface to incorporate more sophisticated welding sequences. It also features a dual-processor architecture for process control and communication, enabling fast welding data transfer rates to higher-level machine and plant management systems without impacting weld quality.
In addition, welding control suppliers are augmenting their platforms with new welding analytics tools. Weld spot analytics technology provides analysis and process, automatically compiling data generated by the controller into easy-to-read formats with real-time dashboards.
These advances in welding control platforms help support novel EV body designs under development, such as structural batteries. With this body design, the battery pack itself is welded with a front casting and a rear casting, simplifying the frame design, reducing the number of parts needed and potentially further reducing weight.
Industry 4.0 Fastening Tools
Assembling an EV involves numerous manual assembly steps. Many are virtually identical to existing ICE processes. Operators install headlights, windshields, retractable sunroofs, center consoles, seats, and door and window controls. These processes require quality, precision and repeatable efficiency to ensure high-value, well-assembled EVs are delivered to the market.
One way operators can achieve quality and productivity is through intelligent tightening tools and guidance systems that provide the efficiency and process control that’s critical in manual assembly tasks.
Suppliers of assembly tools are providing greater accuracy, energy efficiency and durability in their devices, offering precise, repeatable performance for high-volume assembly lines. For example, the Nexo cordless Wi-Fi nutrunner integrates the device controller directly into the tool for easier, lower-cost integration into existing lines. This design enables high-quality measurement of torque and angle for every fastener, ensuring correct assembly while providing full traceability.
Wider use of these Industry 4.0 tools can help manufacturers increase throughput and operate with greater flexibility as different vehicle models move down the line. These tools also generate valuable data that engineers can use to improve training, adjust workflows and apply lean manufacturing principles.
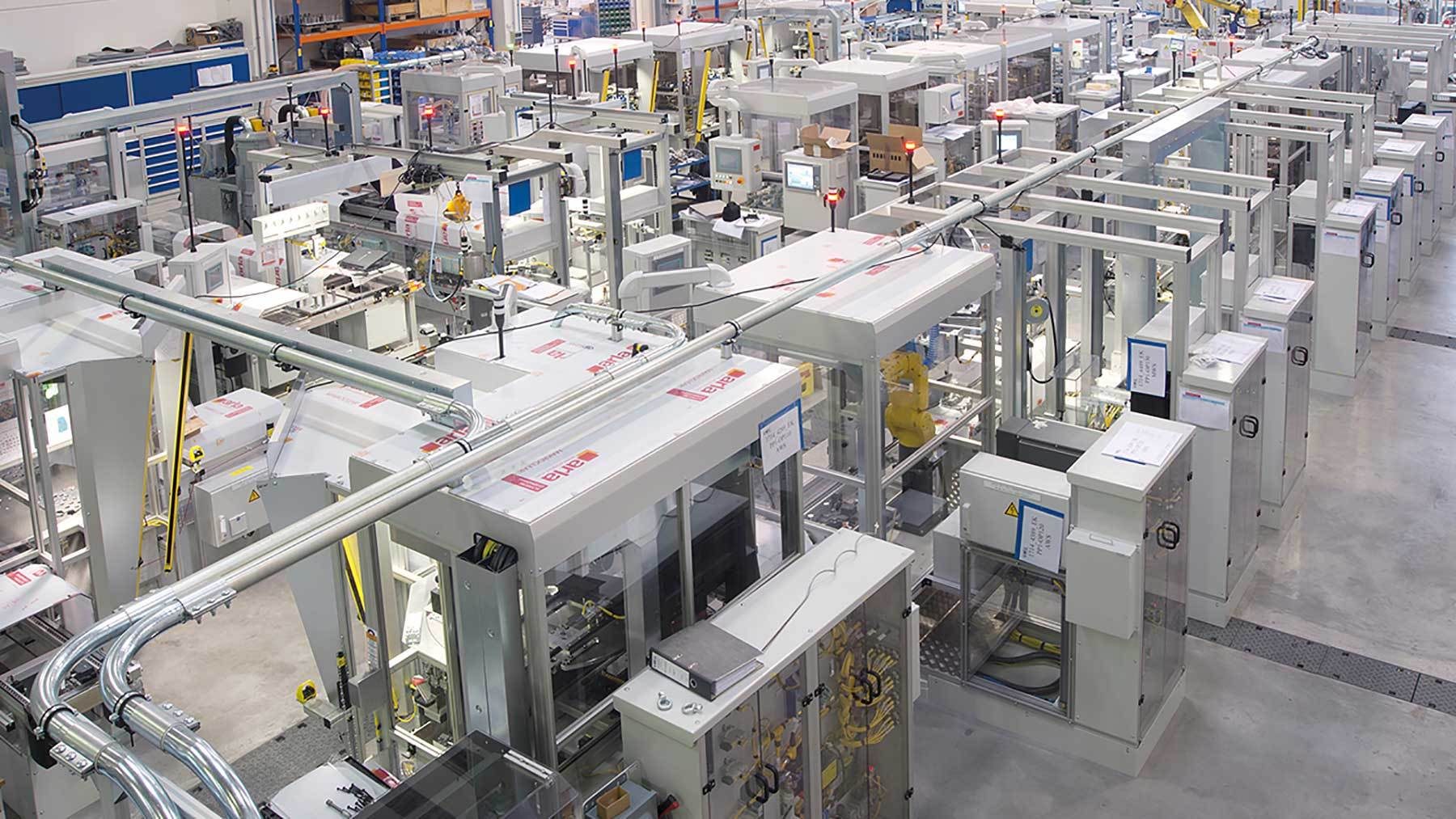
Broad automation portfolios can help streamline EV assembly by ensuring full integration of disparate technologies.Photo courtesy Bosch Rexroth Corp.
Smart Intralogistics
Using new intralogistics technology, mobile robots can help save time in delivering parts to manual workstations and production cells. Autonomous mobile robots (AMRs) are faster and easier to implement than more static delivery systems and don’t require delivery personnel with powered industrial trucks to move material to production lines.
AMRs combine speed and efficiency and can be used to move pallets or shelves so that fully filled flow racks can be delivered to manual workstations. Tasks can be triggered manually via a wireless button, tablet or PLC, or through a connection to an upstream ERP, MES or WMS via API.
Reactive collision avoidance and lidar-based navigation technology enables mobile robots to be more adaptable in rapidly changing environments without the need for special tracks or other fixed navigation aids.
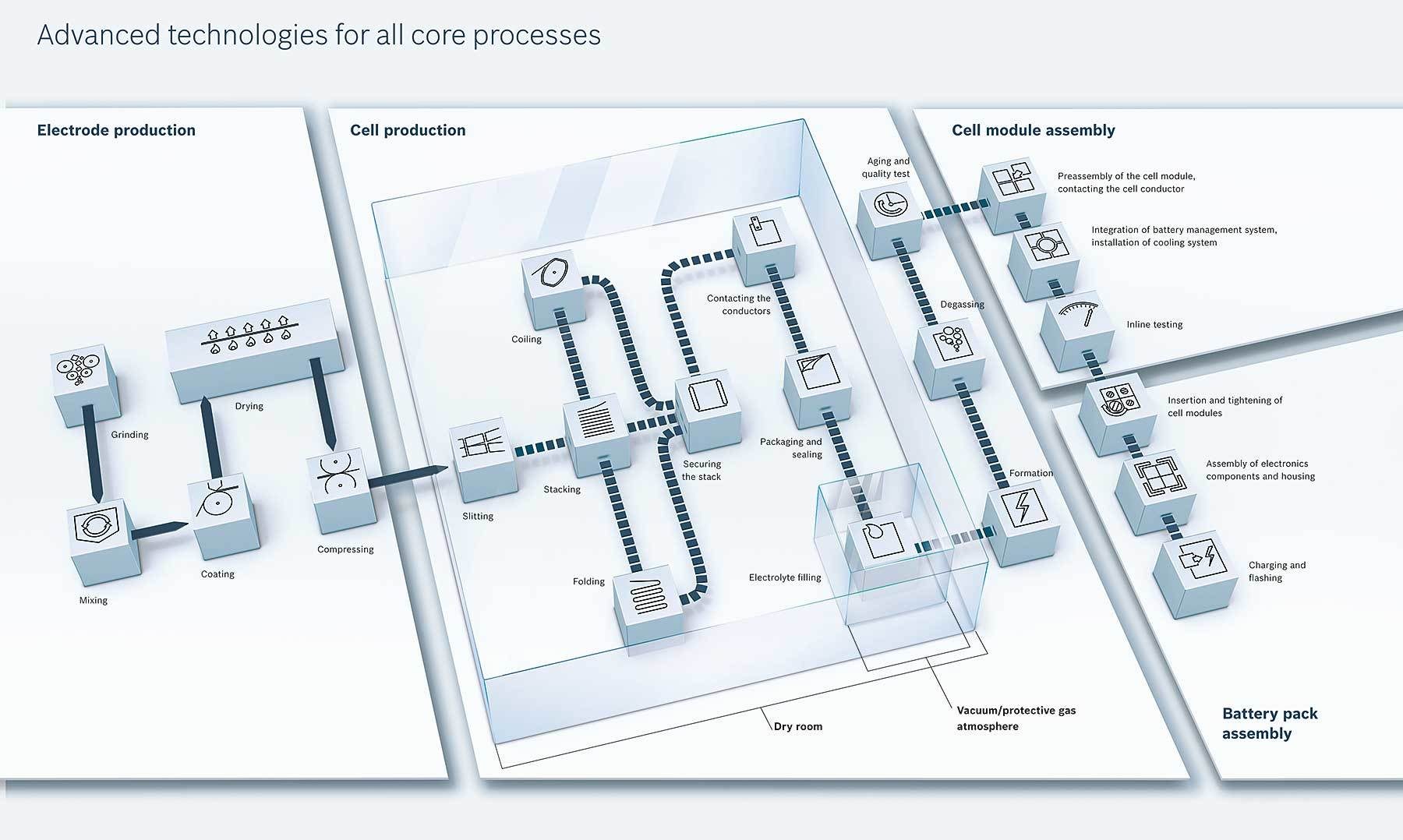
Electric vehicle battery fabrication is a complex, multistep process that requires advanced control platforms, mechatronics and material handling systems.Illustration courtesy Bosch Rexroth Corp.
Controls and Mechatronics
There are four major steps in battery pack manufacturing: electrode production, cell assembly, module assembly and pack construction, including end-of-line battery testing. Each stage uses an array of automation to go from raw materials to completed packs. Production requires high throughput rates combined with extremely tight assembly tolerances and quality control systems.
In electrode production, raw materials move through multiple automated processing steps. Maximizing control over these processes requires technologies that ensure cells are created with desired electrochemical properties, life cycle and energy density.
Advanced automation platforms feature controllers, drive hardware and software that’s designed precisely for these high-throughput production processes. For example, multiple material layers are coated and combined under tight pressure in the calendaring process to fabricate the battery electrode.
Powerful, Linux-based controllers with 64-bit multicore CPUs provide advanced closed-loop sag and loop control to eliminate breakage and minimize waste. They also support high-speed multi-axis synchronization for web speed and position alignment.
New systems like the ctrlX AUTOMATION platform also feature modular software toolkits that use the latest app technology so engineers can easily upgrade production tools or add features such as real-time video inspection by simply adding apps to the controller. This results in reduced engineering time, fewer components and higher productivity.
In cell production, individual cylindrical or pouch batteries are combined into cells. Many manufacturers are working to optimize the stacking process and improve the throughput of the entire line. High-speed mechatronic handling systems, either delta robots or linear robots, are essential tools in this process. A key challenge is engineering and integrating these mechatronics systems quickly to help EV manufacturers launch new assembly lines as rapidly as possible.
Mechatronic system providers are also offering “plug-and-produce” Cartesian robots for both assembly and handling functionality. They utilize state-of-the-art online tools to support quick and intuitive configuration, modeling and quoting, enabling engineers to order complete systems that come with pre-installed software for easier commissioning and faster production starts.
Similar plug-and-produce mechatronics tools can be used for more complex cell module processing steps where electrolyte chemicals need to be dispensed into each cell; the cell caps are placed and welded on; positive and negative poles are added; and then all the cells in the module are wired together.
Modular mechatronic systems for pressing and dispensing are becoming more widely used, offering precise operation and high throughput rates.
Rather than ordering multiple components that require integration and programming, engineers should consider working with a supplier whose complete mechatronics tools combine presized linear axes with servo drive and control technology to create production tools with common interfaces and operating software.
Drag-and-drop motion functions also make it easy to parameterize and program, regardless of whether the systems are used for pressing, welding or dispensing. These mechatronic kits often include pre-installed software that automatically parameterizes the servo drive, saving valuable setup time.
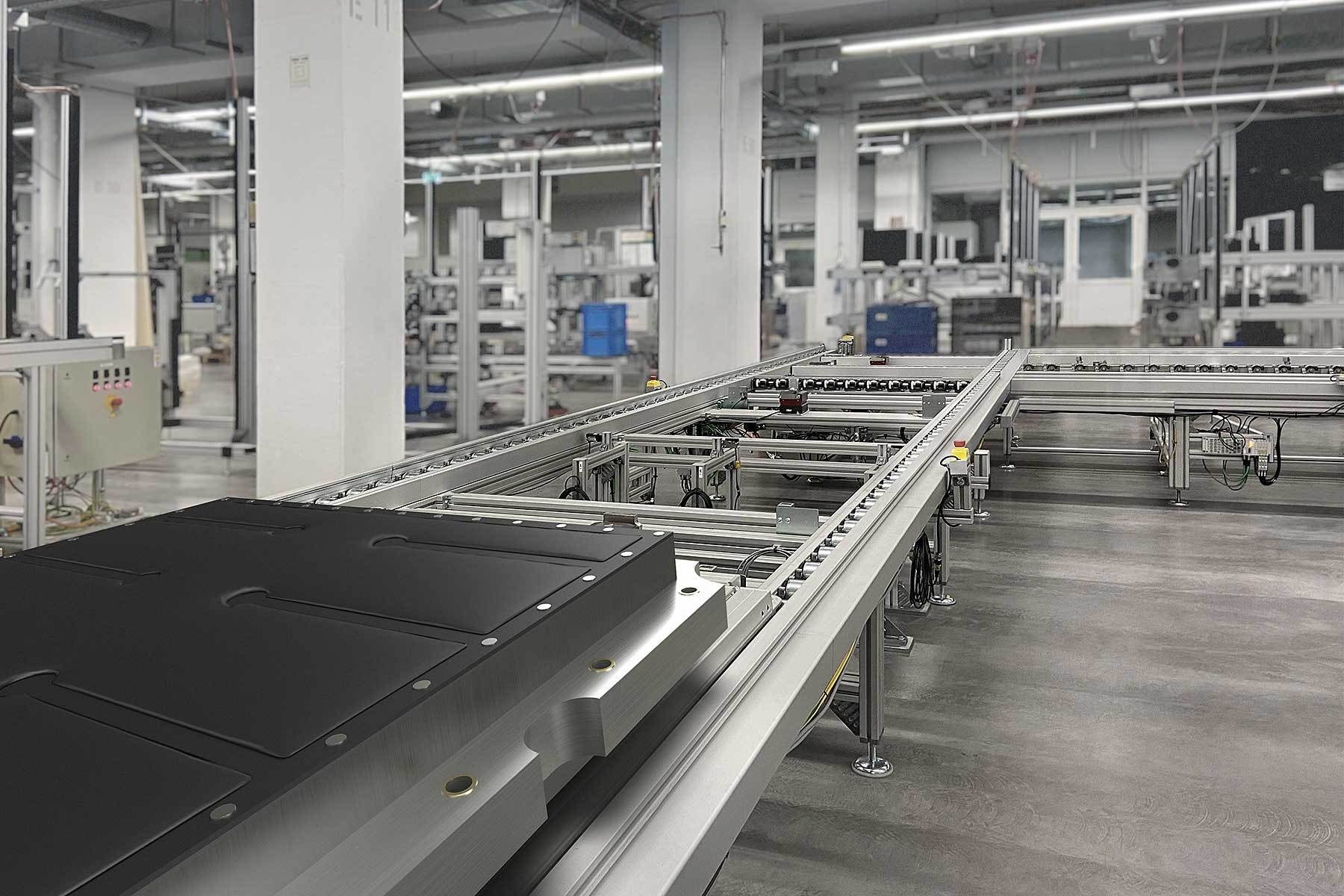
Weight and component size increases with each step of the battery assembly process. Photo courtesy Bosch Rexroth Corp.
Modular Movement
Going from raw materials to a tested and installed battery pack presents a major automation transport challenge. With each assembly step, weight and component size increases, so a range of material transport conveyors and other systems is necessary.
Rather than going with a single conveyor and then trying to customize it for different load and speed requirements, there are advantages to selecting conveyor systems with a range of speed and load capabilities. And, there are additional design and engineering advantages if they can all be sourced from one supplier with a broad offering to cover custom applications as required.
Flexible plastic chain conveyors can rapidly move cell assemblies horizontally, vertically and around obstacles or be integrated with other process flows. These also support workpiece pallets to convey cell components where positioning or higher stopping precision is specified.
Further down the line, where more rapid movement and the ability to move workpiece pallets independently of each other may be needed, engineers should consider high-speed linear motor-based systems. For example, Bosch Rexroth’s Flexible Transport System supports pallet-based transport and allows for individual carrier control for more complex movement at faster throughput rates.
In addition, for successful EV assembly operations, it’s important to design conveyor systems early in the development process, not as a final step once all the production machines and cells have been defined. This helps ensure productive material handling and movement through every process step. It can also prevent the need to build in non-value-added transport time, while also allowing for easier modifications later as production requirements scale up.
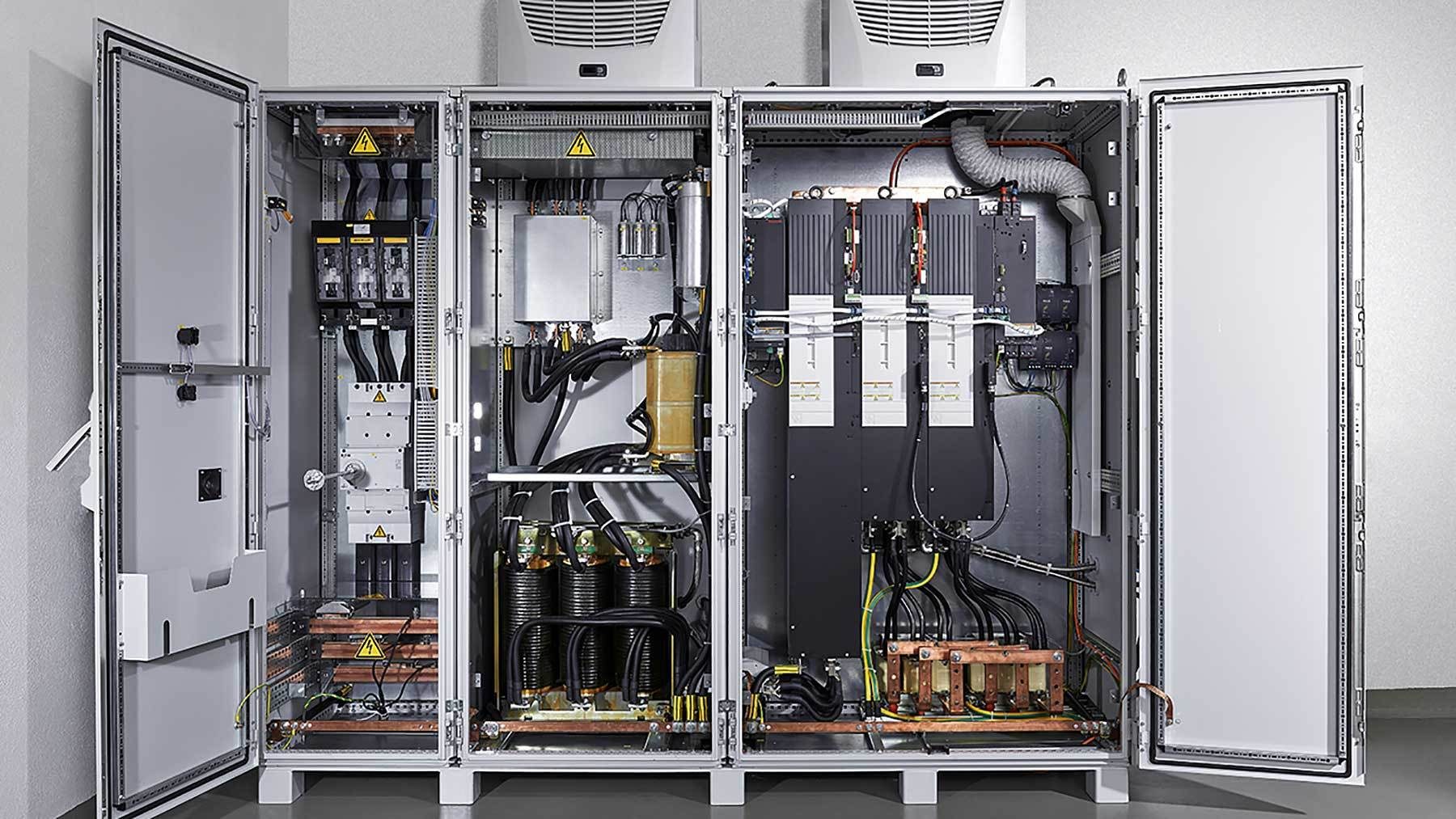
Battery and e-axle testing demands scalable DC power systems. Photo courtesy Bosch Rexroth Corp.
End-of-Line Testing
Another essential step in EV battery pack manufacturing is end-of-line testing. The performance of each pack must be tested and documented.
A plant producing 50 cars per hour needs to test a new battery pack every 72 seconds, so testing systems must be extremely reliable and highly automated to match assembly line production rates.
To meet this need, manufacturers of power converter technology are launching complete testing platforms that provide very precise and accurate control during testing of the battery pack output.
For example, the IndraDrive ML family of power converters uses a software-controlled system that provides constant voltage, current and power according to the required test cycling. It features a scalable DC-DC drive design with the industry’s smallest footprint, helping conserve valuable space in the control cabinet and, ultimately, production floor space.
Automation Insight
Because automakers are under increasing pressure to expand EV production, they run risks by simply throwing technology at their throughput challenges, rather than considering how well their technology and component choices work together. All assembly technology should be engineered and harmonized to maximize throughput without sacrificing the quality of the end product or profitable, productive manufacturing.
It’s also important to consider an effective concurrent engineering approach to save weeks of time and effort. This combines system design, programming, component acquisition and integration in tight, overlapping time frames to deploy automation technology more rapidly.
There are advantages to working with suppliers that feature multi-technology portfolios and proven experience in automotive and battery manufacturing applications. Rather than just one piece of technology, they can provide complete systems and help automakers expand EV production and accelerate speed to market.
FEBRUARY 2023 | ASSEMBLYMAG.com
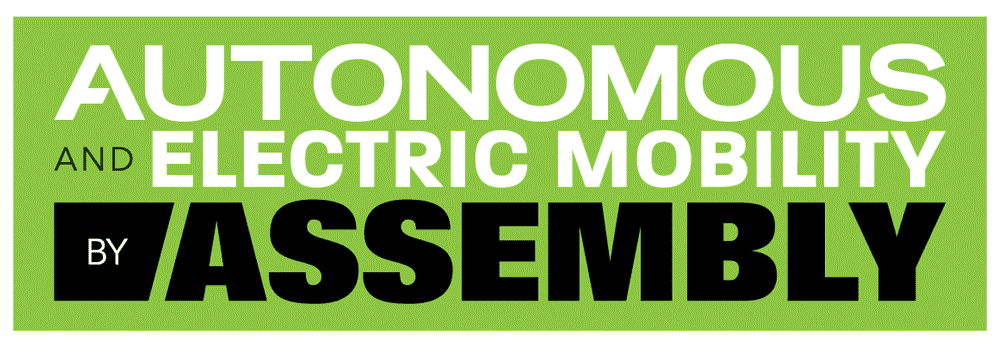