Infinitum Unveils Next-Generation EV Motor
NEWS
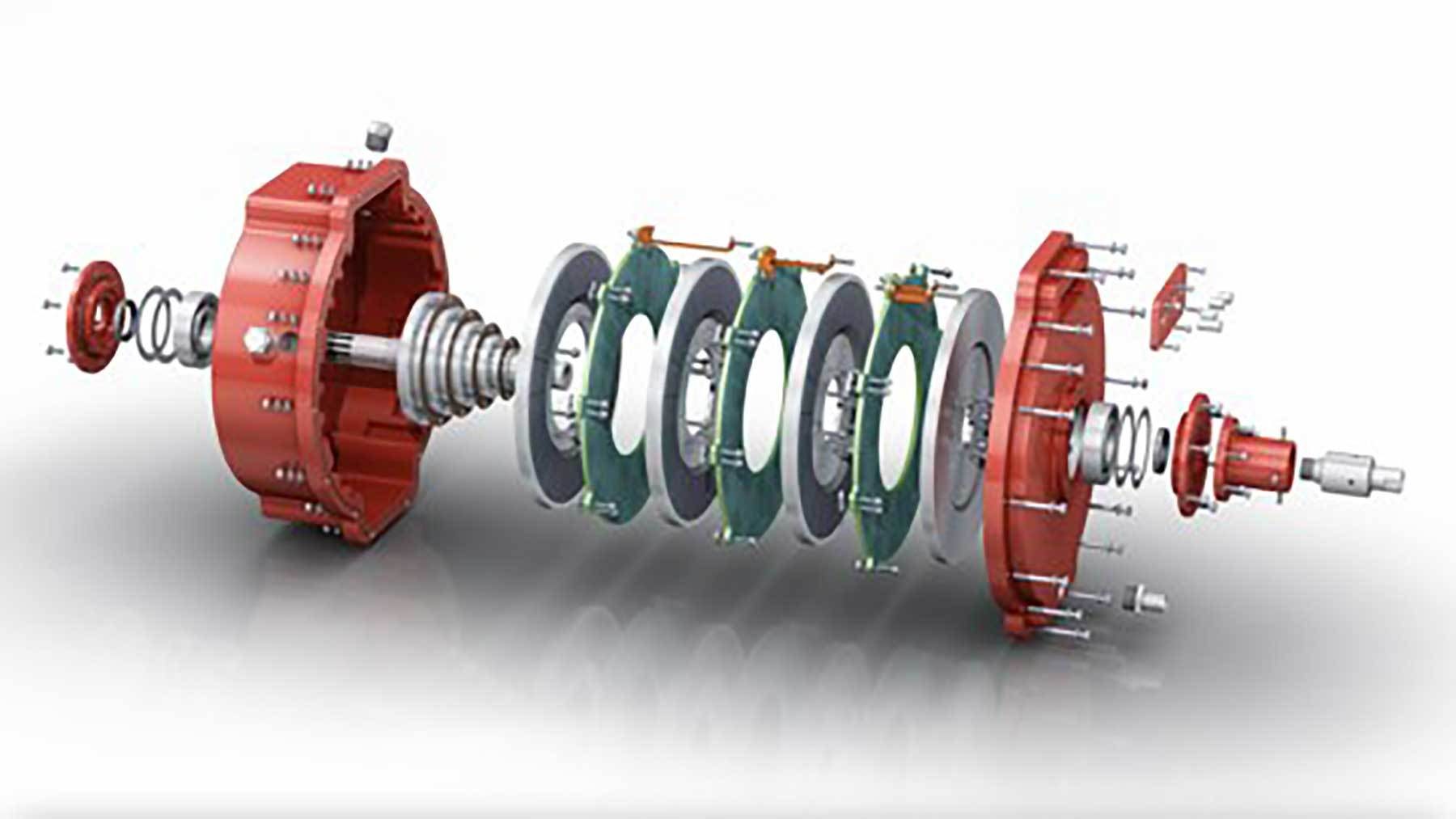
The Aircore Mobility traction motor features axial flux propulsion technology. Illustration courtesy Infinitum
LAS VEGAS—During the recent Consumer Electronics Show here, Infinitum unveiled the Aircore Mobility traction motor. It features axial flux propulsion technology. The motor is designed to power a variety of electric vehicles, including cars, trucks and tractors, plus aviation and marine applications.
The Aircore Mobility motor delivers high power and torque density. It operates efficiently over a wide range of speeds and load conditions to maximize vehicle range. The device replaces the heavy, copper-wound iron stator found in traditional motors with a lightweight, printed circuit board (PCB) stator that is 10 times more reliable.
Compared to conventional motors, Infinitum’s new product is 50 percent smaller and lighter, and uses 66 percent less copper. By replacing the iron core with a PCB stator, mechanical losses are reduced, efficiency is increased, and noise and vibration are significantly reduced. The Aircore Mobility motor is covered by 32 issued patents and 44 pending patents.
Leveraging its unique PCB stator design, the next-generation motor can achieve up to five times the current density of a conventional, liquid cooled motor using a liquid cooling technique that allows the coolant to be in direct contact with the stator, mitigating heat across a larger surface area, enabling high overload capability and extended life.
“Our aircore motor topology eliminates core losses and delivers a broader range of speeds and load conditions where the motor can operate at high efficiency levels,” says Paulo Guedes-Pinto, vice president of technology at Infinitum. “The motor offers a new avenue in extending range for Class 1-8 vehicles, aerospace, marine, construction and agricultural machines.”
According to Guedes-Pinto, the motor is designed with and will be manufactured with a sustainable, circular life cycle. It can be produced using fewer raw materials, while a modular design allows the housing, rotors and stators to be reused multiple times, giving parts a second and third life to serve future generations.
“The motor can also be manufactured almost anywhere locally without complex assembly equipment, and its smaller size means more product is shipped in equal space, which drastically reduces transportation-related emissions,” claims Guedes-Pinto.
“Infinitum’s motor design using PCB stators offers promising performance and efficiency benefits for mobility applications due to superior heat mitigation and high power density,” adds Sam Abuelsamid, principal analyst at Guidehouse Insights Inc. “With supply chain challenges, the motor’s materials, rapid assembly and scalable production should be attractive to OEMs seeking dramatically simpler manufacturing going forward.”
Battery Disassembly Process Improves EV Recycling Efforts
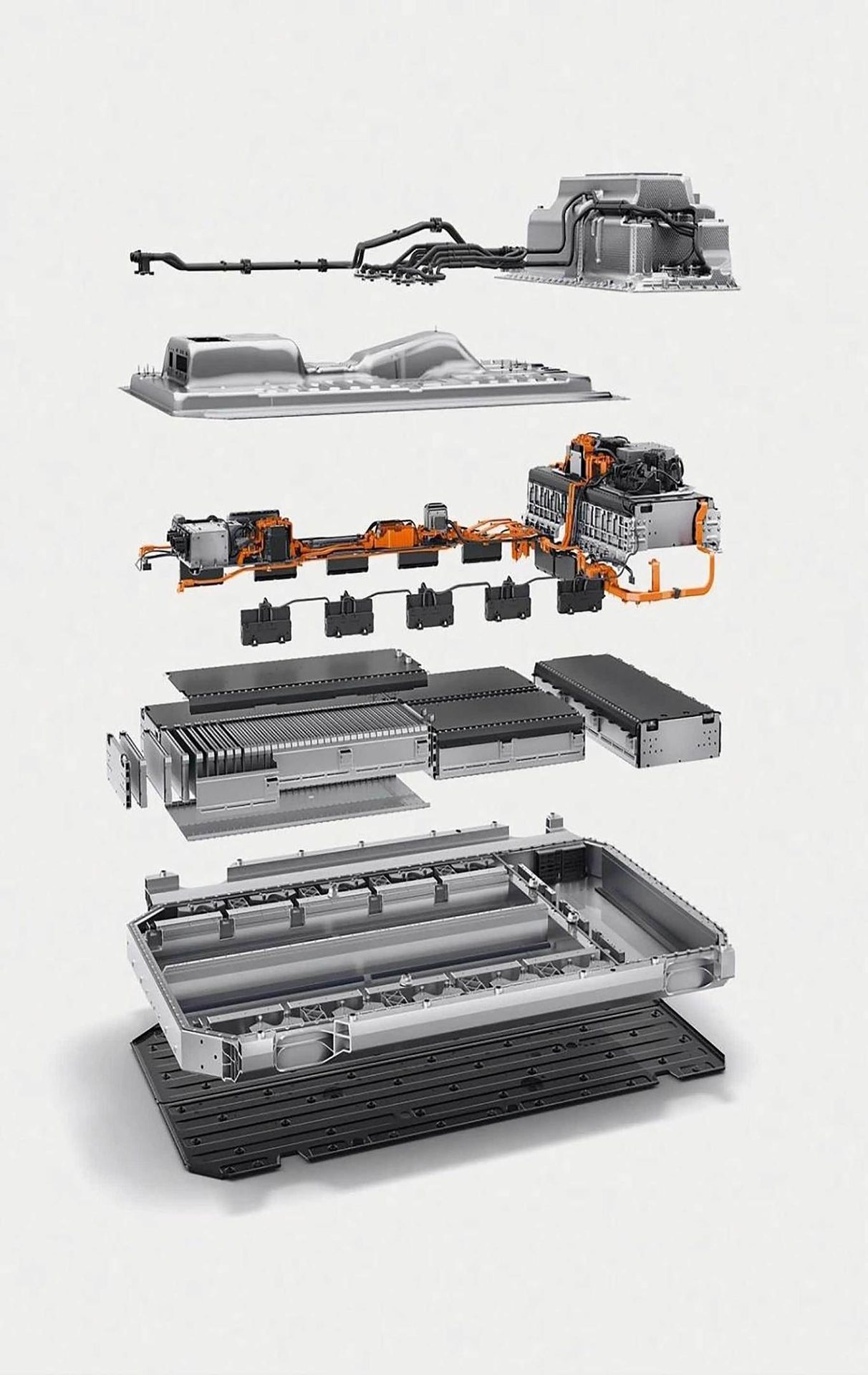
Engineers in Germany have developed a way to examine EV batteries for recycling. Illustration courtesy Fraunhofer Institute for Machine Tools and Forming Technology
CHEMNITZ, Germany—Engineers at the Fraunhofer Institute for Machine Tools and Forming Technology (IWU) here have developed a new way to recycle batteries and other car parts.
The EKODA project, which focuses on disassembly processes and technology, carefully examines each component during a complex testing procedure. Then, an evaluation system generates recommendations for how these components could be reused. This strategy optimizes the lifespan of the individual parts, making it possible to establish a sustainable circular economy in the mobility sector.
After a lithium-ion battery has been extracted from an old or damaged vehicle, a camera slowly moves over it, recording the battery type, model, serial number and power class (in kilowatts). The system compares this information with an internal database. Next, the battery cover is removed through a semiautomated process. Then comes more analysis.
A measuring system records the battery’s current charge level, the functionality of its control electronics and the condition of the individual battery cells. Evaluation software developed in-house then uses this data to create a detailed profile of the battery condition, which is analyzed and used to provide recommendations for reuse.
An intact battery that is only three or four years old, for example, could be transferred to a used car of the same type. If the energy storage system is older, it would be possible to use it in a smaller agricultural machine. Even if the battery has multiple defective cells, it may still be suitable for stationary use, such as electricity storage in a home photovoltaic system.
The battery system does not need to be thrown away. It gets a second chance that is tailored to its specific abilities. The same principle of examination and reuse can also be applied to other types of car parts, such as drivetrains.
“The decisive factor here is that the individual parts are disassembled carefully via a standardized and automated process, as we need to find possible ways of reusing the components right from the start,” explains Uwe Friess, Ph.D., head of the department for body construction, assembly and disassembly at Fraunhofer IWU.
The software, which is equipped with AI algorithms, is one of the core technologies of the EKODA project, which aims to bring about a circular economy through efficient, economically viable disassembly and processing.
“We want to move away from traditional recycling, instead looking at every component of a car as a valuable resource—regardless of the function they currently serve in the vehicle,” says Friess. “This is why we are working on a strategy for testing whether these individual components can be reused or repurposed in various contexts.”
Friess and his colleagues are also working on processes for automatically disassembling the individual components. By implementing this strategy systematically, they hope to enable reuse of all components as part of a circular economy.
Because this would reduce the need to manufacture new products, it would reduce both costs and CO2 emissions. Not only that, but it would also reduce or eliminate the need to prematurely scrap cars that may still be partially intact.
Stellantis to Assemble Electric Aircraft in Georgia
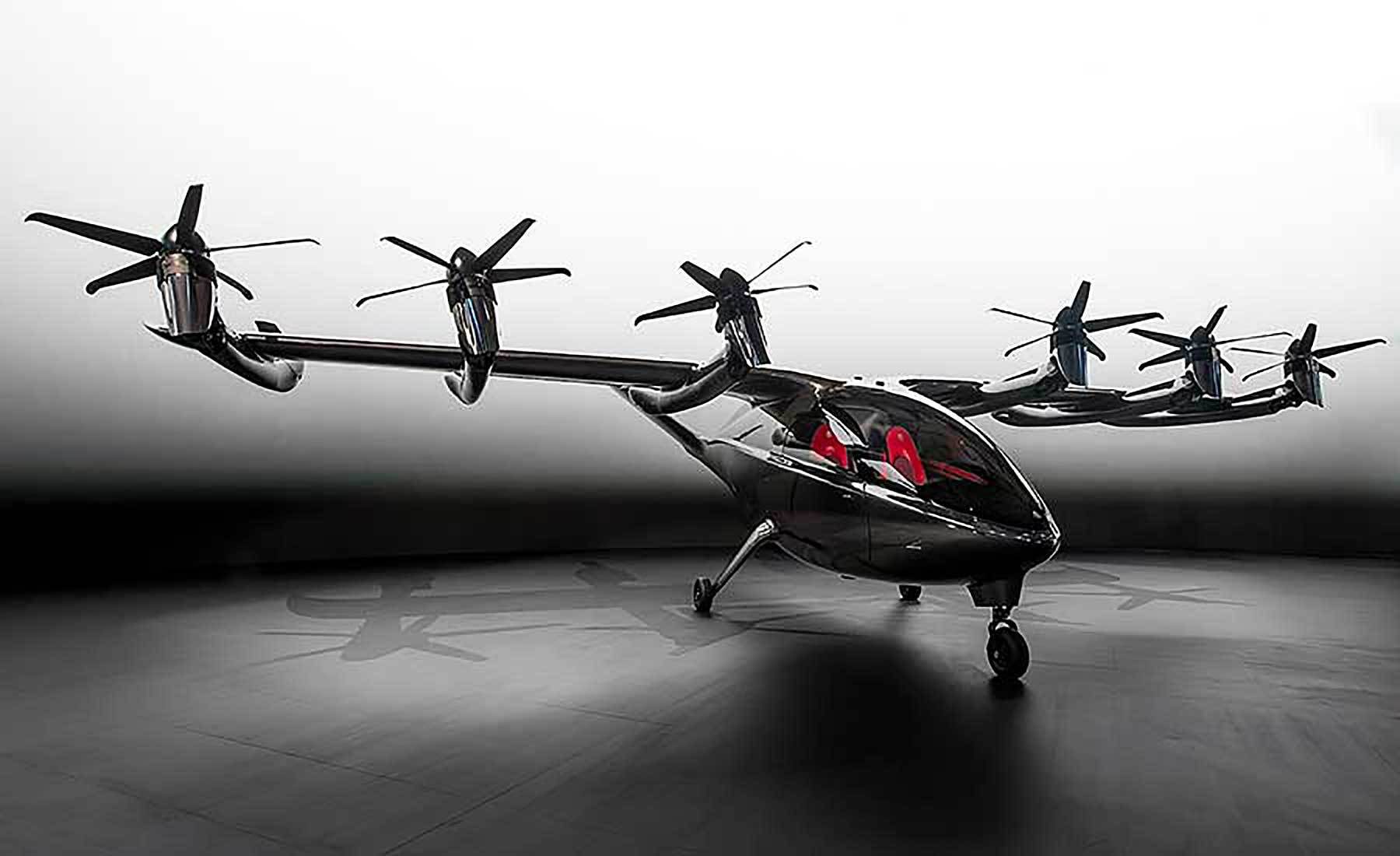
Stellantis will assemble Archer’s Midnight eVTOL at a factory in Georgia. Photo courtesy Archer Aviation Inc.
COVINGTON, GA—Stellantis NV has agreed to help Archer Aviation Inc. manufacture electric aircraft at the latter’s new assembly plant here.
Archer owns the factory, but Stellantis will help the aerospace start-up get the operation up and running. The factory will produce the Midnight, an electric vertical take-off and landing (eVTOL) aircraft designed to serve as an urban air taxi.
Production is planned to launch late next year, when Archer expects to certify the aircraft with the Federal Aviation Administration.
The goal is for Stellantis to be the exclusive contract manufacturer of Midnight. The agreement is a collaboration seeking to leverage both partners’ strengths. Archer brings its expertise in the development and certification of electric aircraft, while Stellantis offers experience in mass production in a highly regulated sector.
Unveiled in November, the Midnight is an aircraft that can carry a pilot and up to four passengers. It looks like a plane, but launches and lands more like a helicopter since it doesn’t require a runway. The battery-powered aircraft has a range of 100 miles and was designed for back-to-back short distance trips of around 20 miles with a charging time of 10 minutes in-between. It is capable of carrying more than 1,000 pounds and can travel at speeds up to 150 mph.
Audi Presents Plan for Future EV Production
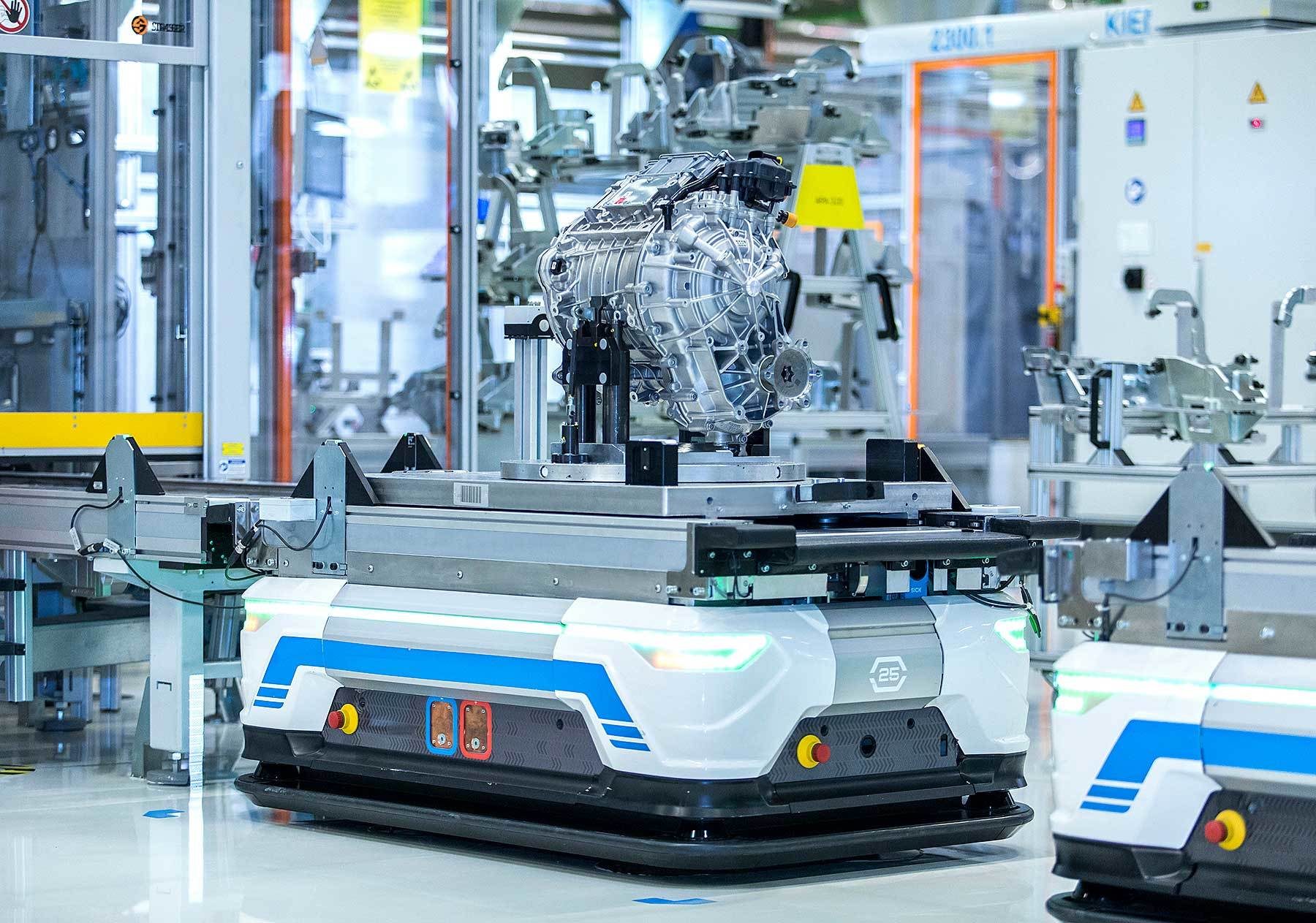
Audi’s factories will use state-of-the-art production equipment to assemble electric vehicles. Photo courtesy Audi AG
INGOLSTADT, Germany—Audi AG is preparing its assembly plants to produce EVs-only within 10 years. The goal is to make the automaker’s long-term manufacturing strategy flexible and resilient.
Audi calls its vision of the future the 360factory. The initiative places equal emphasis on “cost-effectiveness, sustainability, flexibility and attractiveness.”
By the end of the decade, Audi will be making electric-drive models at all of its production sites worldwide. It facilities in Böllinger Höfe and Brussels are already assembling EVs.
Starting next year, the Audi Q6 e-tron will be the first all-electric model to roll off the production line at Audi’s flagship plant in Ingolstadt. And, EV production will gradually ramp up in Neckarsulm, San José Chiapa and Győr.
By 2029, all of the automaker’s factories will be producing at least one EV. Depending on local conditions, production of all remaining ICE models will be gradually phased out by the beginning of the next decade.
“Step by step, we are bringing all our sites into the future,” says Gerd Walker, Audi board member for production and logistics. “We don’t want any standalone lighthouse projects or greenfield sites. Instead, we are investing in our existing plants so they end up being just as efficient and flexible as newly built production sites or greenfield [facilities].”
To ensure that future production will be economical, Audi wants to cut annual factory costs in half by 2033. To achieve this, it plans to reduce the complexity of its vehicles. For instance, Walker says vehicle development engineers will focus on streamlined production processes.
Audi also plans to continue to digitalize its factories. In the future, it will deploy cycle-independent modular assembly lines to simplify work with high product variability. According to Walker, virtual assembly planning will save material resources and make innovative, flexible collaboration possible across production locations.
In addition, Audi plans to make its manufacturing processes even more flexible. “We want to structure both product and production so we get the optimum benefit for our customers,” explains Walker. “To this end, the new Q6 e-tron, for example, will initially be made in Ingolstadt on the same line as the A4 and A5. The electric models will then gradually replace the combustion cars on the lines.”
Solar-Powered Car Assembly Is Underway in Finland

Production of Lightyear’s much anticipated solar-powered EV has started at a contract manufacturer in Finland. Photo courtesy Lightyear
UUSIKAUPUNKI, Finland—Production of Lightyear’s much anticipated solar-powered electric vehicle has started at Valmet Automotive’s state-of-the-art assembly plant here. The vehicle is equipped with solar panels that cover its hood, roof and tailgate. That unique feature will enable the EV to cover longer distances without having to stop and recharge.
The Dutch startup automaker claims that the Lightyear 0 is “the most aerodynamic car in the world,” with a drag coefficient of 0.175. Its vehicle has been carefully designed to minimize energy consumption and maximize solar yield.
The solar roof will capture sunlight continually whether the car is moving or stationary. Lightyear claims that feature will deliver enough energy to cover an average of more than 70 percent of annual mileage.
A conductive backsheet produced by Royal DSM is an integral element of the EV’s solar roof. It enables all the connections of the solar cells to be put on the back of the solar panel, which makes every available centimeter on the front of the module available for capturing sunlight.
“This start of production moment is both a beginning and an end: the end of the chapter we started back in 2016, and it’s the beginning of true solar mobility,” says Lex Hoefsloot, CEO of Lightyear. “It’s an achievement in the automotive industry like never before. And while we may be the first, my sincere hope and belief is that we won’t be the last.”
The car uses a 61.2-kilowatt-hour battery that weighs only 350 kilograms. Hoefsloot claims that it has the highest energy density of any electric vehicle available. “The low weight, compared to other electric car batteries, contributes to the light overall weight of Lightyear 0, standing at an industry low of 1,575 kilograms,” he points out. “This light weight is essential for making [the vehicle] as energy efficient as possible.”
Valmet Automotive, a leading contract manufacturer, has built new production facilities for the vehicle that includes a state-of-the-art assembly line.
Airbus and Renault to Develop EV Battery Technology
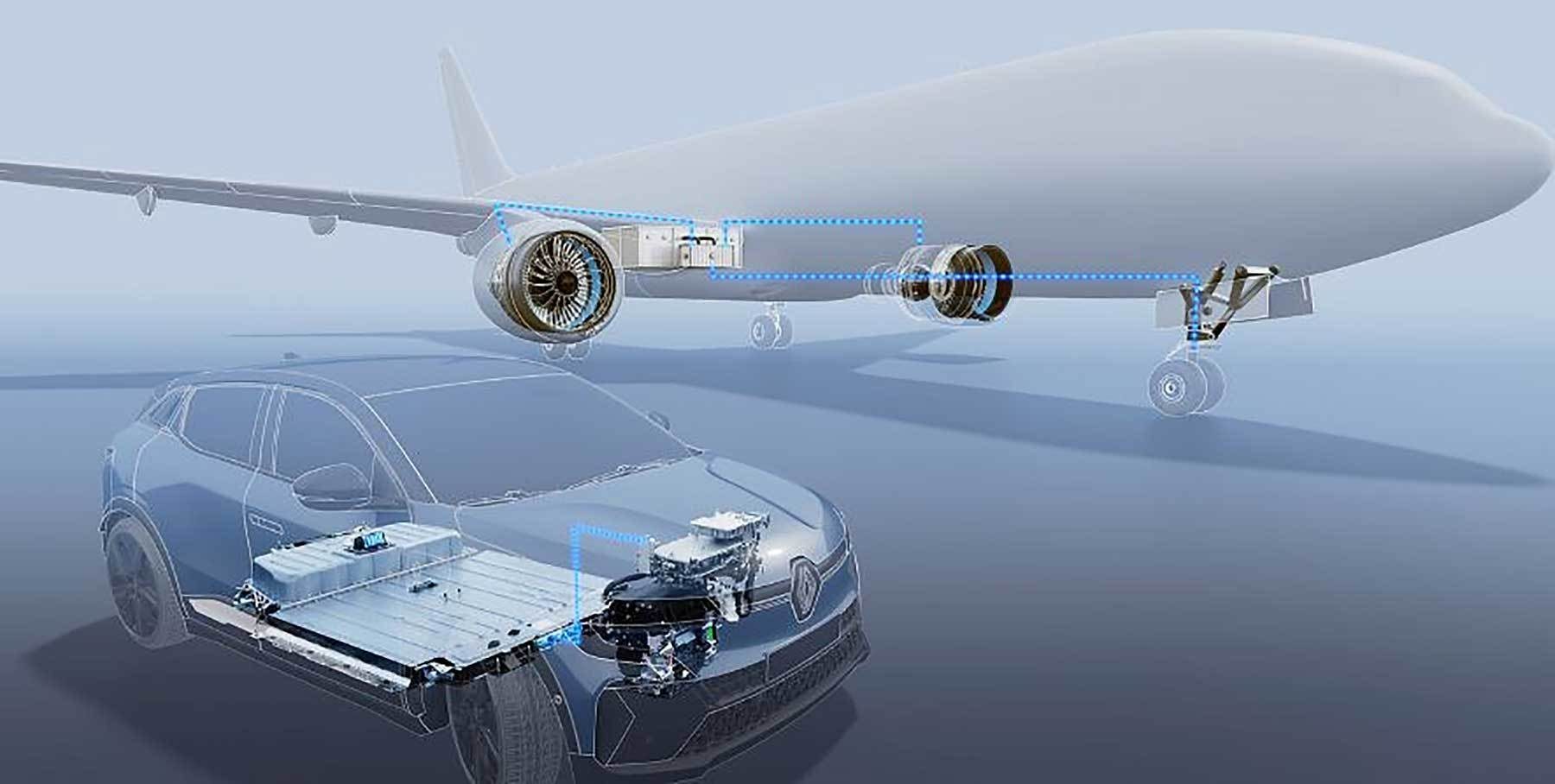
Airbus and Renault have formed a strategic partnership to develop EV battery technology. Illustration courtesy Airbus SE
TOULOUSE, France—Airbus SE and Renault Group have formed a strategic partnership to develop EV battery technology. Engineers from both companies will focus on energy management optimization, battery weight improvement and next-generation solid-state batteries. They’ll also study the lifecycle of future battery designs, from production to recyclability.
“For the first time, two European leaders from different industries are sharing engineering knowledge to shape the future of hybrid-electric aircraft,” says Gilles Le Borgne, executive vice president of engineering at Renault. “Aviation is an extremely demanding field in terms of both safety and energy consumption, and so is the car industry.
“Our 10 years of experience in the electric vehicle value chain gives us some of the strongest feedback from the field and expertise in the performance of battery management systems,” explains Le Borgne. “Driven by the same ambition to innovate and reduce the carbon footprint, our engineering teams are exchanging with those of Airbus to converge transversal technologies that will enable both hybrid aircraft to be operated and the vehicles of tomorrow to be developed.”
“This cross-industry partnership with Renault will help us mature the next generation of batteries as part of [our] electrification roadmap,” adds Sabine Klauke, chief technical officer at Airbus. “Reaching net zero carbon emissions by 2050 is a unique challenge that requires cooperation across sectors, starting today.
“Bringing together Renault’s experience in electric vehicles with our own track record in electric flight demonstrators will allow us to accelerate the development of the disruptive technologies required for future hybrid aircraft architectures in the 2030s and beyond,” claims Klauke. “It will also foster the emergence of common technical and regulatory standards in support of the clean mobility solutions needed to achieve our climate targets.”
FEBRUARY 2023 | ASSEMBLYMAG.com
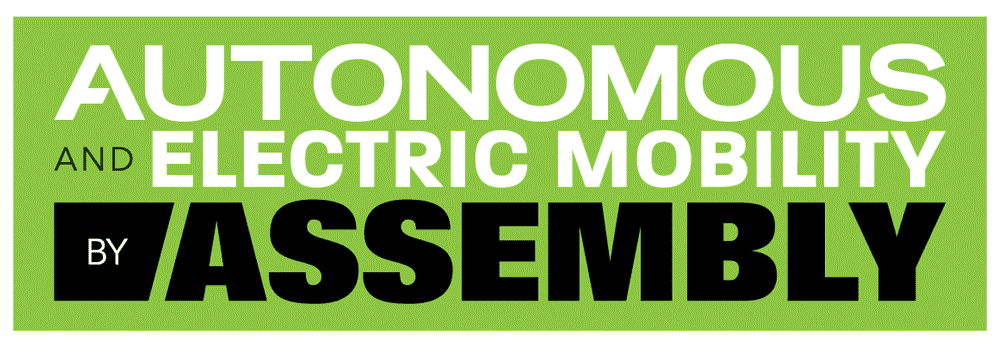