By Austin Weber, Senior Editor // webera@bnpmedia.com
New Manufacturing Process Produces Cheaper Cathodes for Lithium-Ion Batteries
AV/EV tech trends
A new hydrothermal synthesis method makes a cobalt-free cathode material with more uniform, round, tightly packed particles (right) than is common in today’s cathodes (left), maintaining more stability throughout the battery charging cycle. Illustration courtesy Oak Ridge National Laboratory
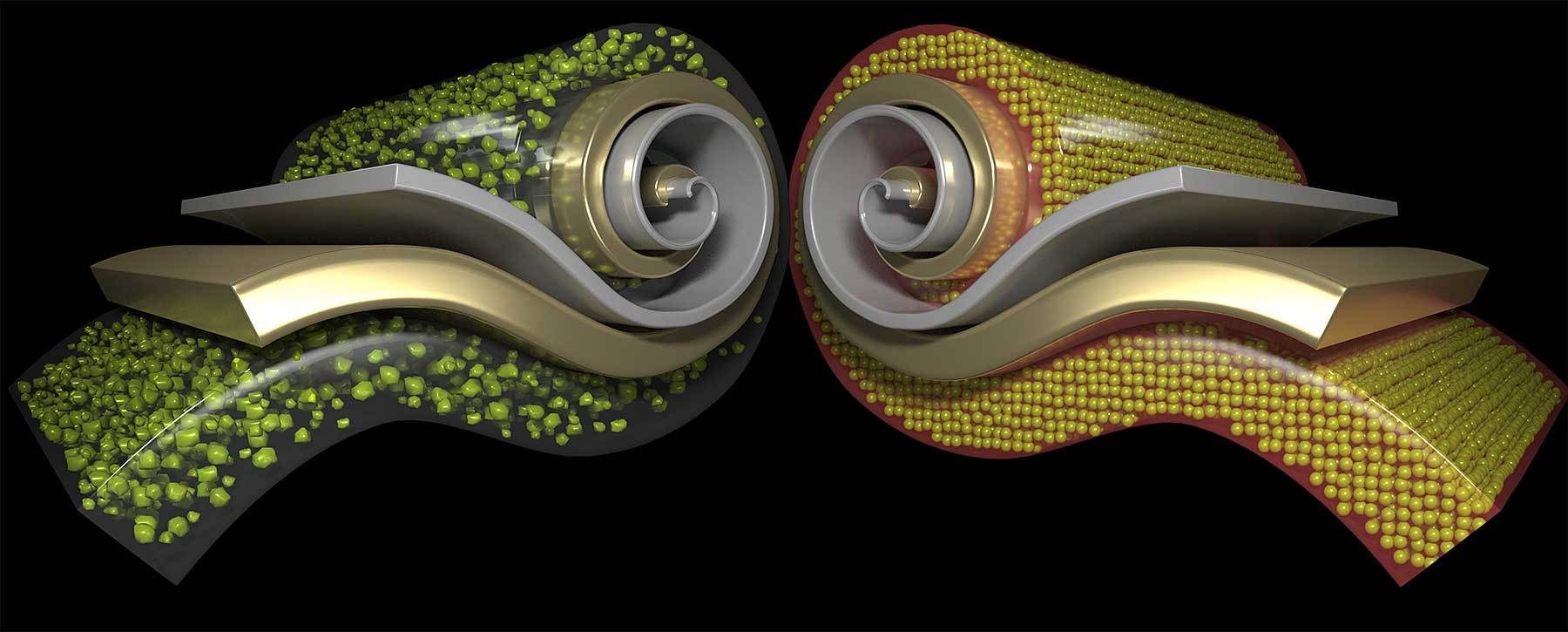
Oak Ridge National Laboratory (ORNL) engineers have developed a new process to produce better, cheaper cathodes for use in lithium-ion batteries. It enables a way to make more affordable batteries from a faster, less wasteful process that uses less toxic material.
Traditional processing presents numerous challenges. One big obstacle is a reliance on cobalt, a rare metal mined and refined abroad.
The balance of other metals common in cathodes can also make the manufacturing process longer and more hazardous. For example, high nickel concentration has led to the widespread use of a chemical mixing method for cathode production that requires large quantities of ammonia for corrosive reactions. Using this toxic chemical increases costs, heightens health and environmental concerns, and wastes large amounts of water to reduce acidity.
Instead of continuously stirring cathode materials with chemicals in a reactor, the new ORNL method uses a hydrothermal synthesis approach. It crystalizes the cathode using metals dissolved in ethanol. The ethanol is safer to store and handle than ammonia, and afterward it can be distilled and reused.
“This novel process offers the key advantage of moving the cathode industry to cleaner and more cost-competitive production, while putting less burden on our environment,” says Ilias Belharouak, Ph.D., ORNL’s principal investigator for the project.
The hydrothermal synthesis method is also much faster. The time required to make particles and prepare for the next cathode batch drops from as many as a few days to 12 hours.
“In addition, the material produced has more uniform, round, tightly packed particles that are ideal for a cathode,” explains Rachid Essehli, ORNL lead researcher. “Because its properties are similar to those of today’s cobalt-based cathodes, the new material can be seamlessly integrated into existing battery manufacturing processes. This cathode material can give more energy and decrease the cost of electric car batteries.”
High-Speed EV Motor Features Improved Power Density
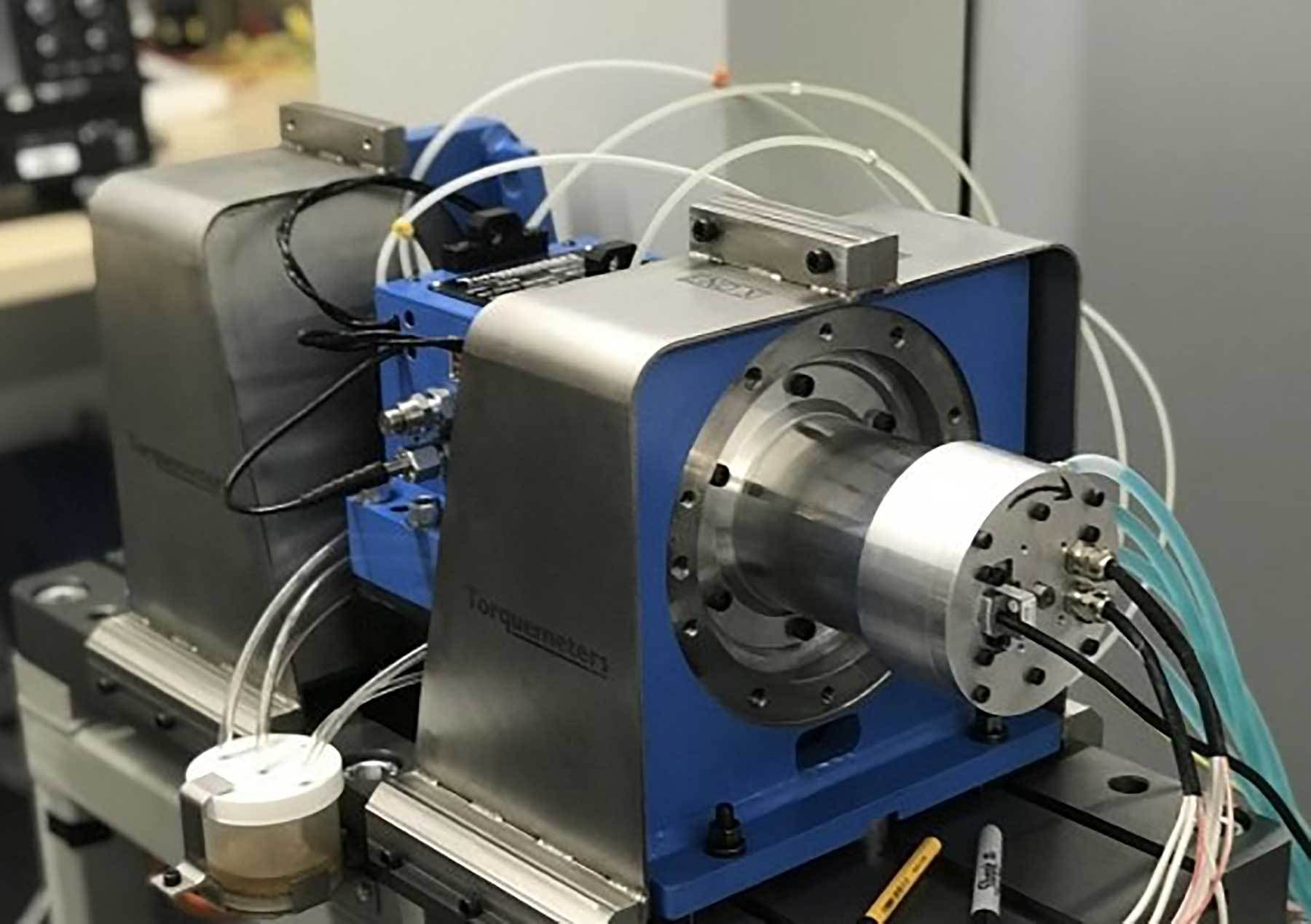
This high-speed magnetically driven motor significantly reduces the use of rare-earth materials such as neodymium. Photo courtesy University of New South Wales
Engineers at the University of New South Wales (UNSW Sydney) have developed a magnetically driven motor that significantly reduces the use of rare-earth materials such as neodymium. The high-speed device has the potential to increase the range of electric vehicles.
The design of the prototype interior permanent magnet synchronous motor (IPMSM), inspired by the shape of the longest railroad bridge in South Korea, has achieved speeds of 100,000 revolutions per minute. The maximum power and speed achieved by the motor have exceeded the existing high-speed record of laminated IPMSMs, making it the world’s fastest IPMSM ever built with commercialized lamination materials.
The motor is able to produce a very high power density, which is beneficial for EVs in reducing overall weight and increasing range for any given charge.
An IPMSM has magnets embedded within its rotors to create strong torque for an extended speed range. However, existing designs suffer from low mechanical strength due to thin iron bridges in their rotors, which limits their maximum speed.
The UNSW device features a new rotor topology that significantly improves robustness, while also reducing the amount of rare-earth materials per unit of power production. It is based on the engineering properties of the Gyopo rail bridge, a double-tied arch structure, as well as a compound-curve-based mechanical stress distribution technique.
“One of the trends for electric vehicles is for them to have motors which rotate at higher speeds,” says Guoyu Chu, Ph.D., an electrical engineering specialist at UNSW. “Every EV manufacturer is trying to develop high-speed motors. The reason is that the nature of the law of physics then allows you to shrink the size of that machine. And, with a smaller machine, it weighs less and consumes less energy; therefore, that gives the vehicle a longer range.
“With this research project we have tried to achieve the absolute maximum speed, with a peak power density that is around 7 kilowatts per kilogram,” explains Chu. “For an EV motor, we would actually reduce the speed somewhat, but that also increases its power.
“We can scale and optimize to provide power and speed in a given range,” claims Chu. “For example, a 200-kilowatt motor with a maximum speed of around 18,000 rpm [would] perfectly suit EV applications.”
According to Chu, the new motor also offers a significant cost advantage over existing technology and uses less rare-earth materials.
“Most high-speed motors use a sleeve to strengthen the rotors and that sleeve is usually made of high-cost material, such as titanium or carbon fiber,” says Chu. “The sleeve itself is very expensive and also needs to be precisely fitted. That increases the manufacturing cost of the motor.
“Our rotors have very good mechanical robustness, so we don’t need that sleeve, which reduces the manufacturing cost,” Chu points out. “And, we only use around 30 percent of rare earth materials, which includes a big reduction in the material cost, thus making our high-performance motors more environmentally friendly and affordable.”
Big Breakthrough Paves the Way for Lithium-Sulfur Batteries
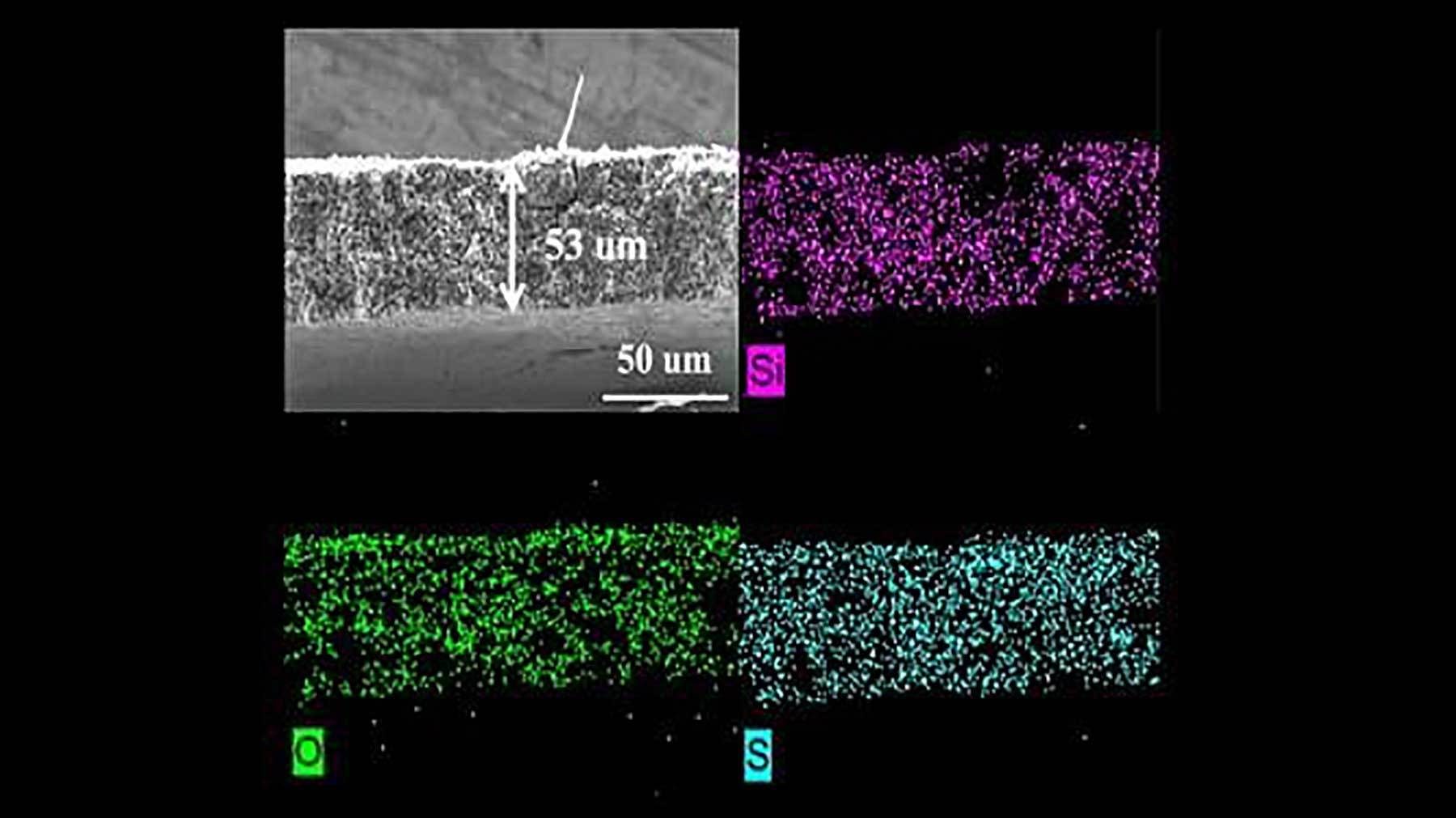
This image shows microstructure and elemental mapping (silicon, oxygen and sulfur) of a porous sulfur-containing interlayer after 500 charge-discharge cycles in a lithium-sulfur battery cell. Illustration courtesy Argonne National Laboratory
Sulfur is extremely abundant, cost effective and can hold more energy than traditional ion-based batteries. A recent R&D project at Argonne National Laboratory discovered a new way to make sulfur-based batteries. Engineers created a layer within the battery that adds energy storage capacity while nearly eliminating a traditional problem with sulfur batteries that caused corrosion.
“These results demonstrate that a redox-active interlayer could have a huge impact on lithium-sulfur (Li-S) battery development,” says Wenqian Xu, a beamline scientist at Argonne. “We’re one step closer to seeing this technology in our everyday lives.”
The promising battery design pairs a sulfur-containing positive electrode (cathode) with a lithium metal negative electrode (anode). In between those components is the electrolyte.
Early Li-S batteries did not perform well because sulfur species (polysulfides) dissolved into the electrolyte, causing its corrosion. This polysulfide shuttling effect negatively impacts battery life and lowers the number of times a battery can be recharged.
To prevent this polysulfide shuttling, previous efforts tried placing a redox-inactive interlayer between the cathode and anode. The term “redox-inactive” means the material does not undergo reactions like those in an electrode.
But, this protective interlayer is heavy and dense, reducing energy storage capacity per unit of weight for the battery. It also does not adequately reduce shuttling. This has proved a major barrier to the commercialization of Li-S batteries.
To address this issue, the ORNL team developed and tested a porous sulfur-containing interlayer. Tests in the laboratory showed initial capacity about three times higher in Li-S cells with this active, as opposed to inactive, interlayer. More impressively, the cells with the active interlayer maintained high capacity over 700 charge-discharge cycles.
“Previous experiments with cells having the redox-inactive layer only suppressed the shuttling, but in doing so, they sacrificed the energy for a given cell weight because the layer added extra weight,” says Guiliang Xu, Ph.D., an Argonne chemist. “By contrast, our redox-active layer adds to energy storage capacity and suppresses the shuttle effect.”
Future research efforts will evaluate the growth potential of the redox-active interlayer technology. “We want to try to make it much thinner, much lighter,” says Xu.
FEBRUARY 2023 | ASSEMBLYMAG.com
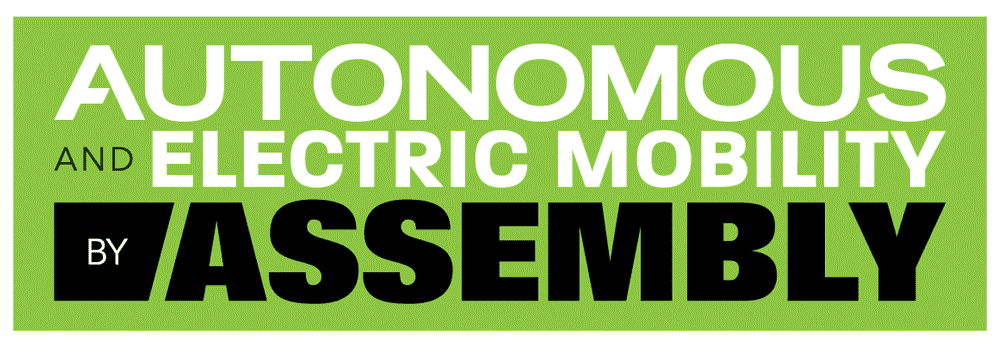