SAE Provides Blueprint for EV Charging Standard
NEWS
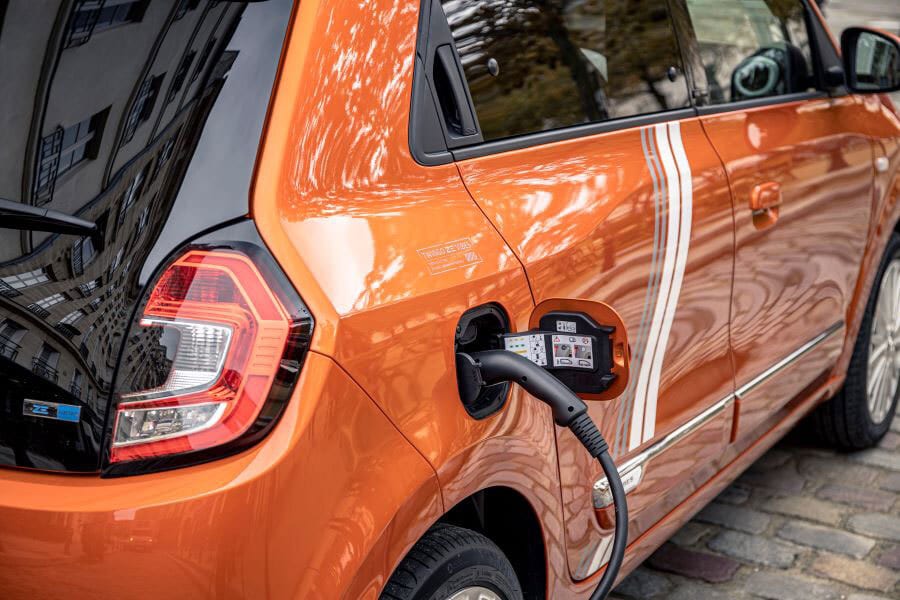
A new standard will dramatically increase access to electric vehicle charging throughout North America. Photo courtesy Edmunds
WARRENDALE, PA—SAE International has unveiled a blueprint of a new standard that will dramatically increase access to electric vehicle charging throughout North America. The SAE J3400 North American Charging Standard (NACS) Electric Vehicle Coupler Technical Information Report (TIR) will help to ensure that any supplier or manufacturer will be able to use, manufacture or deploy the J3400 connector for EVs and charging stations.
Earlier this year, SAE announced that it would standardize the Tesla-developed NACS connector, which promises to play a key role in building an interoperable national charging network that will work for EV drivers with multiple kinds of charging connectors.
“Open and interoperable standards are crucial to ensuring that every EV can charge at any station,” says Gabe Klein, executive director of the Joint Office of Energy and Transportation, which helps coordinate expertise between the U.S. Department of Energy and the U.S. Department of Transportation. “We appreciate the commitment and knowledge of SAE and its experts from the automotive, EV charging, academic, and government sectors to make the charging experience easier and more accessible for Americans nationwide.”
“SAE J3400 provides a blueprint for cost-effective mass electrification of transportation in North America,” adds Rodney McGee, Ph.D., P.E., chairman of the SAE J3400 NACS Task Force. “It facilitates broad interoperability for EV charging solutions by providing a unified, compact connector for both AC and DC charging.
“It is compatible with bring-your-own-cord solutions that make J3400 an optimal approach for AC power transfer for street charging, parking garages, parking lots, and multi-unit or mixed-use buildings,” claims McGhee, who also serves as a research engineer at the Transportation Electrification Center at the University of Delaware.
According to McGhee, this standardized approach means that the same utility power feeds for DC fast charging can be utilized for single-phase AC charging, eliminating the need for separate circuit panels and additional step-down transformers at charging sites, resulting in lower infrastructure costs and higher efficiencies.
U.S. Electric Vehicle Battery Manufacturing Is on Track to Meet Demand
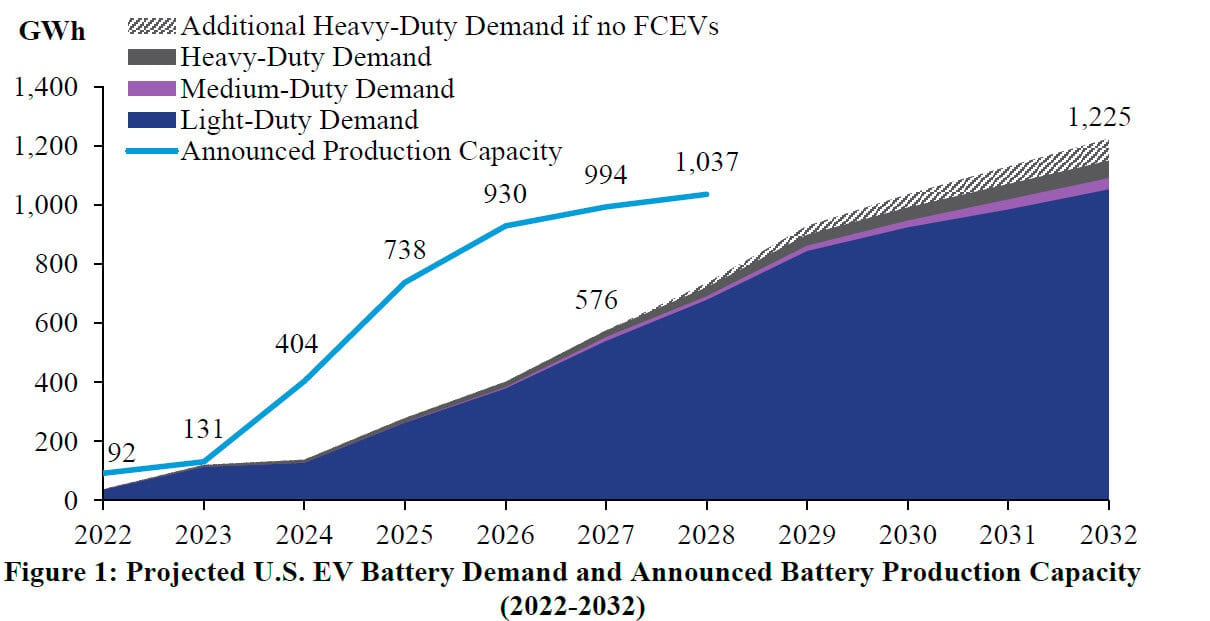
The United States has enough planned battery production capacity to supply all the electric vehicles expected to be sold in 2030. Illustration courtesy Environmental Defense Fund
WASHINGTON—A recent analysis claims that the United States has enough planned battery production capacity to supply all the electric vehicles expected to be sold in 2030.
Researchers at the Environmental Defense Fund (EDF) determined that more than 1,000 gigawatt hours per year of U.S. EV battery production capacity has already been announced to come online by 2028. That’s the equivalent of what is needed to power 10 million electric cars.
All of the announced electric vehicle battery manufacturing captured in EDF’s latest analysis is domestic, which underscores that the U.S. is poised to supply its own battery needs. States with the most announced battery production capacity include Michigan (140 gigawatt hours per year), Georgia (136 gigawatt hours), Tennessee (128 gigawatt hours), Kentucky (119 gigawatt hours) and Indiana (97 gigawatt hours).
“This analysis adds to the large body of evidence already supporting the unambiguous feasibility of protective EPA vehicle emission standards for both light-and-medium-duty and heavy-duty vehicles,” says Ellen Robo, EDF’s Manager of Transportation and Clean Air Policy.
EDF’s analysis evaluates battery demand that could result if manufacturers choose to sell battery electric vehicles to meet both EPA’s Multi-Pollutant Emission Standards for Light and Medium-Duty Vehicles and EPA’s Phase 3 Greenhouse Gas Emissions Standards for Heavy-Duty vehicles.
More than 40 battery manufacturing facilities have been announced already, with an average production capacity of 23 gigawatt hours per year. What’s more, the average time between announcement and expected start of production for the battery facilities in this analysis is 2.7 years.
That means additional facilities that would come online after 2026 have not yet been announced. It also means manufacturers can respond to additional demand for batteries in a relatively short timeframe.
Roughly 90 percent of electric vehicle battery demand is expected to come from passenger vehicles, although demand for electric buses and trucks is also growing. Heavy-duty, commercial vehicle manufacturers have begun announcing battery production facilities, and significant sharing of batteries and components is possible across light and heavy-duty electric vehicles.
Electric vehicles reached 12 percent of all vehicles produced for sale in the U.S. in 2023, an increase of 70 percent over the year before.
Hyundai Unveils New EV Drive System
SEOUL—Engineers at Hyundai Motor Co. and Kia Corp. have developed a paradigm-shifting drive system called the Uni Wheel. The Universal Wheel Drive System dramatically improves available space inside an electric vehicle. It enables a flat-floor configuration by moving an EV’s reduction gear inside the wheel hub, locating a compact individual motor close to each wheel, reducing the length of the drive shafts.
Uni Wheel uses a special planetary gear configuration consisting of a sun gear in the center, four pinion gears on each side and a ring gear surrounding the arrangement. Power generated by the motor is transmitted to the sun gear, which in turn engages the pinion gears to rotate the ring gear. This is connected to the wheel to drive the vehicle.
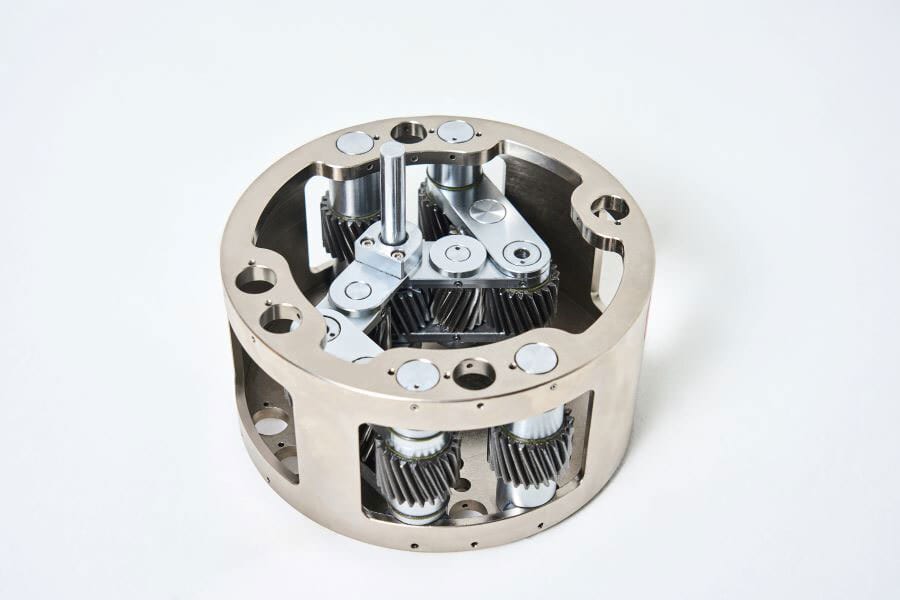
The Uni Wheel uses a special planetary gear configuration consisting of a sun gear in the center, four pinion gears on each side and a ring gear surrounding the arrangement. Photo courtesy Hyundai Motor Co.
Uni Wheel’s pinion gears are connected to each other to form two linkages, and this multi-link mechanism enables Uni Wheel’s multi-axis movement to allow a wide range of suspension articulation.
A conventional drive system using a regular CV joint suffers from a decrease in efficiency and durability as the angle of drive shaft deflection increases when travelling over bumpy, undulating surfaces. Uni Wheel can transmit power with almost no change to efficiency regardless of wheel movement, ensuring high durability and ride comfort.
When combined with electronic air suspension that can adjust ride height according to the driving situation, this can be increased to stabilize the vehicle on rough roads, or decreased for high-speed driving to improve power and stability.
By moving the reduction gear to the wheel hub, Uni Wheel’s high reduction ratio delivers a significant torque output and allows for a more compact electric motor. With independent control of up to four efficient electric drive units, Uni Wheel also allows for unprecedented levels of torque vectoring to boost dynamic ability, and deliver high levels of steering and driving stability.
“We are pleased to showcase innovative ideas that could become game changers in the future mobility market,” says Jongsool Park, Senior Fellow at the Institute of Advanced Technology Development of Hyundai Motor Group. “We will perfect the technology so that customers can experience mobility in a completely different and new way.”
Volvo Invests in State-of-the-Art Robots to Assemble EVs
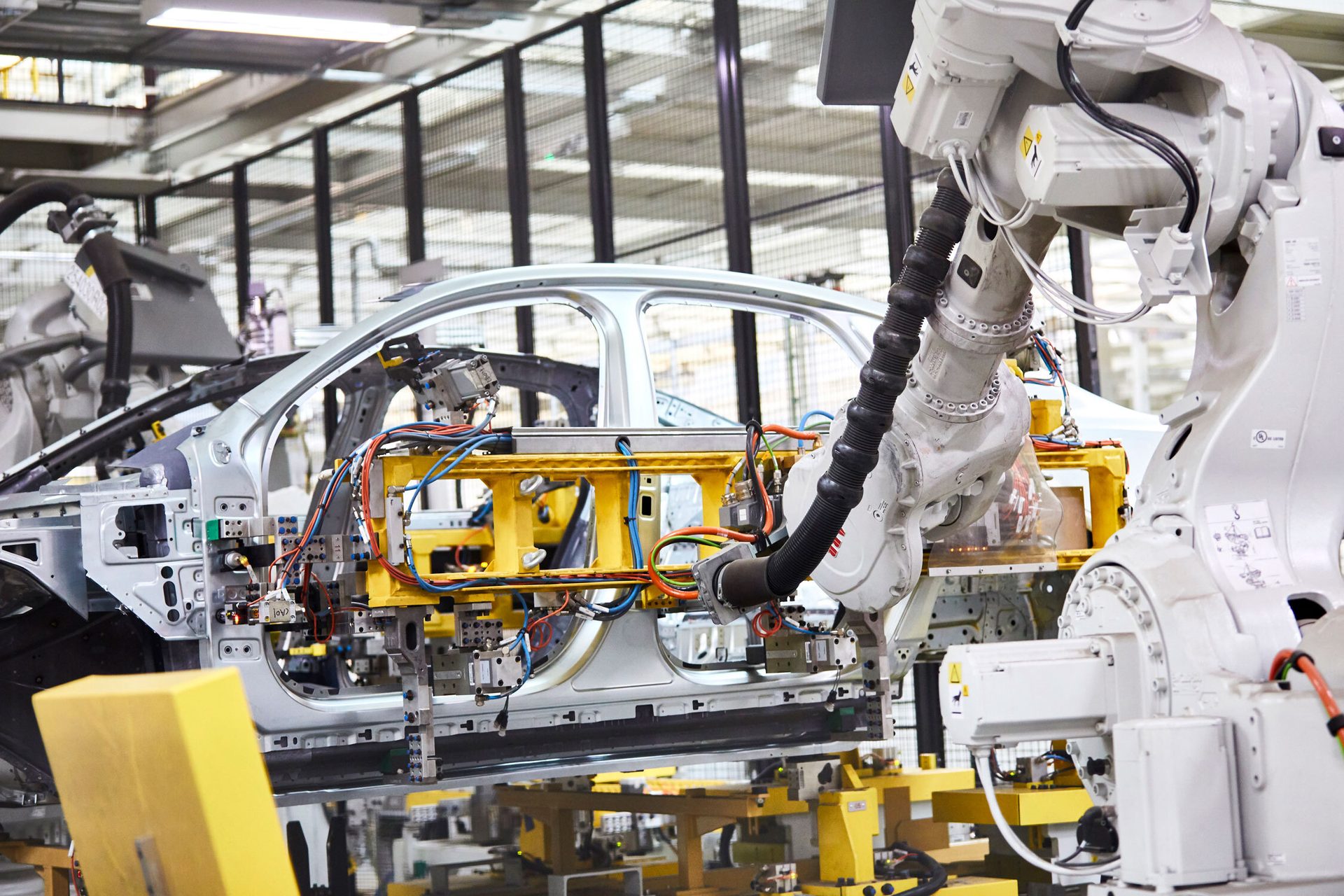
Volvo is acquiring more than 1,300 robots to assemble its next generation of electric vehicles. Photo courtesy ABB Robotics
ZURICH—Volvo Cars is acquiring more than 1,300 robots from ABB to assemble its next generation of electric vehicles. The machines will be installed at the automaker’s factories in Torslanda, Sweden, and Daqing, China.
The robots will be used for variety of applications, such as adhesive dispensing, flow drilling, riveting, spot welding and ultrasonic welding.
“The automotive industry’s historic transformation, driven by increasing consumer demand for electric vehicles and a desire to operate more sustainably, is creating new opportunities as well as challenges for global manufacturers,” says Marc Segura, president of ABB Robotics. “This latest commitment from Volvo Cars demonstrates our shared focus of delivering more sustainable manufacturing.
"Through our new, energy-efficient large robot family and OmniCore controllers, we will help to deliver energy savings of up to 20 percent at sites around the world,” claims Segura.
During the deployment, Segura says ABB will ensure production remains uninterrupted through the use of its RobotStudi planning and programing software platform to visualize and optimize operations before the robots are installed.
Hexagon and JSOL Form Partnership to Accelerate EV Power Train Design
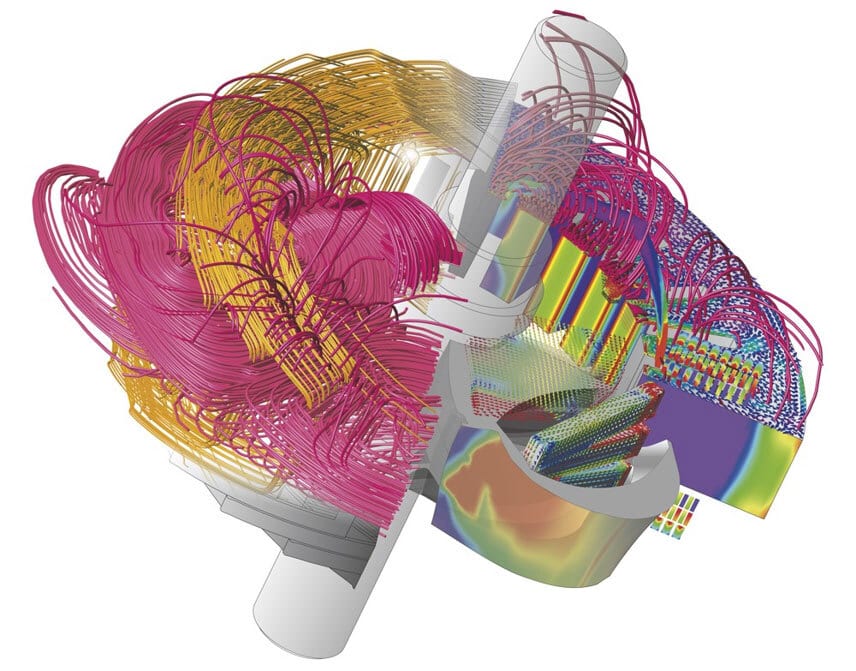
Simulation software enables engineers to reliably predict durability, efficiency, thermal management, and noise and vibration at the component, subsystem and system level. Illustration courtesy Hexagon AB
STOCKHOLM—Hexagon AB and JSOL Corp. have formed a strategic partnership to accelerate EV power train design with virtual prototyping and multi-physics simulation. It will enable engineers to reliably predict durability, efficiency, thermal management, and noise and vibration at the component, subsystem and system level.
The partnership will enable customers to combine Hexagon's extensive engineering simulation software suite with JSOL’s electromagnetic field analysis software to solve a full spectrum of system design problems in the virtual world more quickly, thoroughly and cost effectively than physical prototyping allows.
"As the move toward electrification accelerates, new challenges need to be addressed to improve vehicle performance characteristics, from the component to system level,” says Mahesh Kailasam, general manager of design and engineering at Hexagon’s Manufacturing Intelligence division. “For example, improvements to noise, vibration and harshness (NVH) performance now require simulation solutions to provide answers at much higher frequency ranges.
“Our partnership with JSOL solidifies our commitment to serve our existing and new customers in this rapidly evolving [field],” explains Kailasam. “To stay ahead in the market, electromagnetic power trains need to be very efficient and light, using new designs, materials and manufacturing techniques.”
America’s First Public EV Charging Road Opens in Detroit
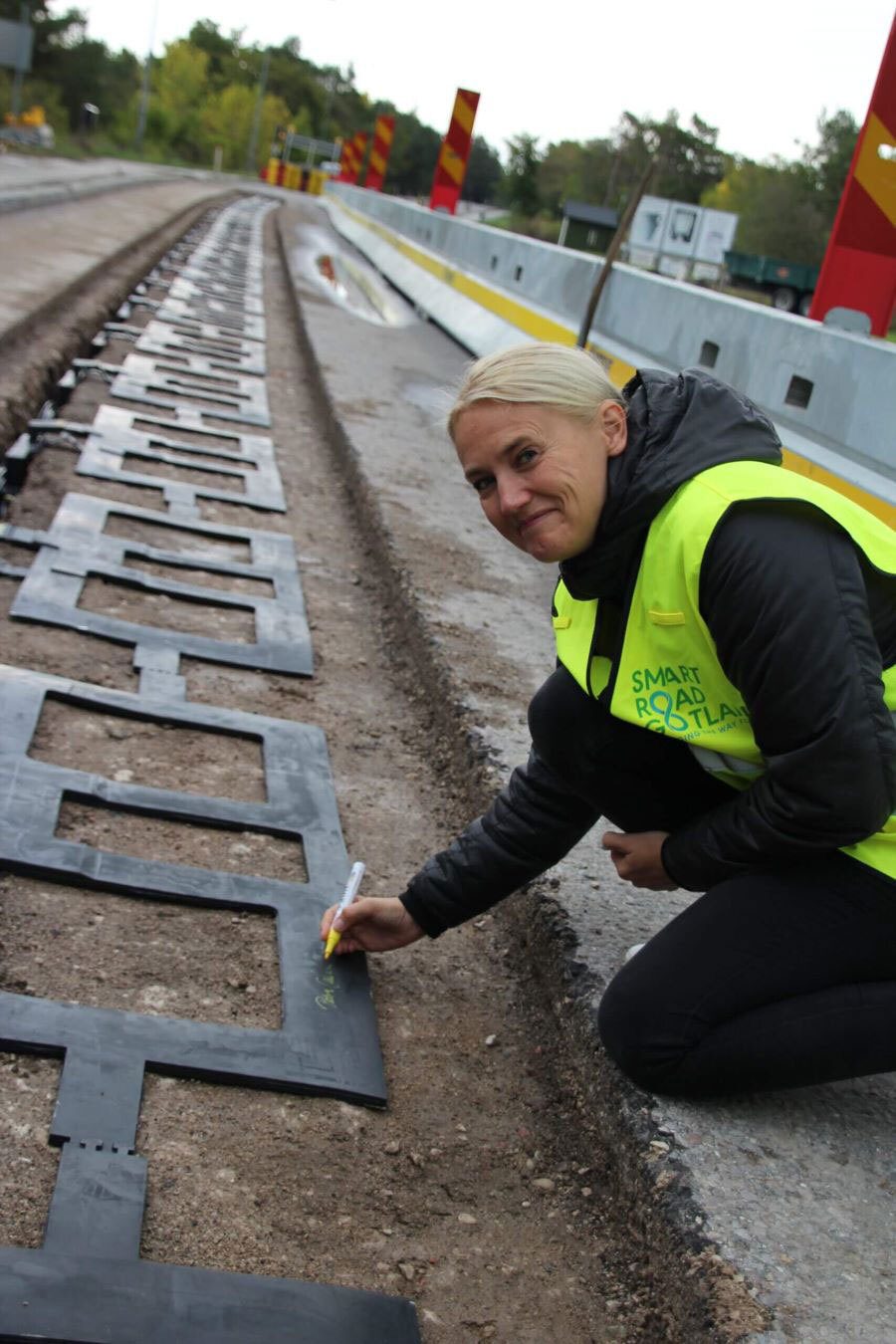
The nation’s first wireless-charging public roadway recently opened in Detroit. Photo courtesy Electreon Wireless Ltd.
DETROIT—The nation’s first wireless-charging public roadway recently opened at the Michigan Central innovation district here. It uses inductive-charging coils embedded in the pavement.
The 0.25-mile stretch of road will be used to test and perfect the technology developed by Electreon Wireless Ltd. It runs alongside the Newlab at Michigan Central Building, which is home to more than 60 tech and mobility startups.
Electreon's wireless charging technology is based on inductive coupling between copper coils installed below the road surface and receivers installed on EVs. When a vehicle with a receiver nears the in-road charging segments, the road transfers electricity wirelessly through a magnetic field. This electricity is then transferred as energy to the vehicle's battery.
The electric road is safe for drivers, pedestrians and wildlife. Each coil in the road is activated only when a vehicle with an approved receiver passes over the coil. This ensures that energy transfer is controlled and provided only to vehicles that require it.
"We’re excited to spearhead the development and deployment of America's first wireless charging road," says Stefan Tongur, vice president of business development at Electreon. "Alongside Michigan's automotive expertise, we'll demonstrate how wireless charging unlocks widespread EV adoption, addressing limited range, grid limitations, and battery size and costs. This project paves the way for a zero-emission mobility future, where EVs are the norm, not the exception."
“For more than a century, Detroit has been known around the world as the leader in transportation innovation,” adds Detroit Mayor Mike Duggan. “We are the birthplace of the auto industry, and the home of the first mile of concrete road and the first three-way traffic signal.”
february 2024 | ASSEMBLYMAG.com
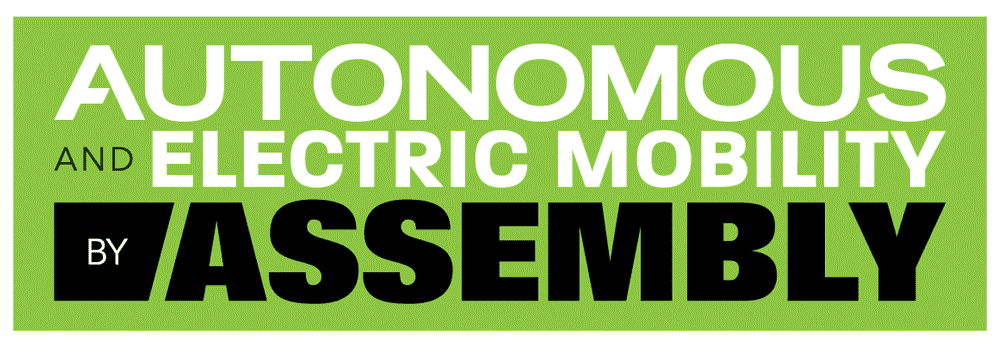