FOCUS ON AEM
Two-wheeled electric vehicles feature super-quick acceleration and quiet performance. Photo courtesy BMW Motorrad
Battery-powered motorcycles and scooters offer big benefits, but pose unique assembly challenges.
Zooms Ahead
Electric scooters are one of the hottest segments of the electric vehicle market. Their popularity is due to low price, ease of use and a small form factor that’s ideal for urban environments.
According to a 2023 report from the International Energy Agency, battery-powered two- and three-wheelers accounted for nearly 30 percent of global vehicle sales in 2023, with China, India and Southeast Asia leading the way.
In large European and North American cities, where traffic congestion, parking and air quality are pressing issues, the benefits of micromobility are hard to ignore. That’s why traditional motorcycle manufacturers such as BMW, Honda, and Yamaha have developed electric versions of their machines.
Even old-school Harley-Davidson is active in the sector, with its spinoff LiveWire brand. And, a host of start-up companies, ranging from Arc to Zapp, are producing two-wheeled electric vehicles that boast super-quick acceleration and quiet performance.
“Electric scooters have become quite cost competitive,” says Pedro Pacheco, an analyst at research firm Gartner. “You can charge them at home; in some cases, remove the battery and charge it inside. They also eliminate both air and noise pollution.”
In some markets, electric scooters are cheaper than gas-powered alternatives. For instance, in China, government support, infrastructure readiness and sheer population density have enabled mass-scale deployment of electric two-wheelers.
“[However], what’s missing in the motorcycle world is basically a Tesla—one player that brings super-innovative technology and builds a strong competitive advantage over the rest of the market,” says Pacheco. “No bike maker has managed to do that yet.”
Nathan Eddy // Contributing Writer
AEM PRODUCTS
Battery limitations have also slowed progress. While scooters can function with smaller, swappable batteries, full-size motorcycles require more power and greater range. Many current models still fall short of the 200-mile threshold that gas-powered bikes routinely exceed. Charging infrastructure tailored to two-wheelers is also underdeveloped, particularly in the U.S. and parts of Europe.
But, innovation is progressing, largely due to developments in the automotive industry.
“Bikes will keep adopting technology that comes from passenger cars,” says Pacheco. “Battery innovations and motor efficiency will trickle down into motorcycles and scooters over time.”
Examples of cross-sector spillover include regenerative braking, advanced thermal management systems and AI-powered energy optimization systems.
While e-scooters have firmly established themselves as a practical mode of transportation in urban settings, electric motorcycles are still in a transition phase.
“There’s definitely a future for electric motorcycles,” claims Pacheco. “But, it’s going to take time—and it’s not going to look like the electric car market.”
Here’s how a handful of two-wheel OEMs are approaching the market, and some of the unique production challenges they face.
Automatically feed and install metal or plastic clips with verifiable precision. Auto-feed direct to insert point technology for rapid clip insertion. Machine builder packages for collaborative and industrial robots. Engineered part interface tooling mirrors part tower and is ruggedly built for repeatable clip insertion. Videos and more on Visumatic's website.
Visumatic Industrial Products
859-255-7907
sales@visumatic.com
www.visumatic.com
Automotive Trim Panel Clip Insertion Gear
BMW Produces the Ultimate E-Scooter
BMW AG has been producing motorcycles for 100 years. And, its Motorrad division has been making electric vehicles for more than 10 years, with a focus on products that address urban mobility needs. The company currently markets CE 02 and CE 04 e-scooters.
Both products are engineered in Germany. The CE 04 is assembled at the flagship BMW Motorrad plant in Berlin, while the eParkourer CE 02 is built under contract in India by the TVS Motor Co. The high-voltage battery and the electric traction motor are manufactured in-house at the Berlin plant.
The housing for the battery is manufactured at the plant’s welding shop and is made of aluminum.
The cell modules are supplied by the BMW Group production network and are inserted into the housing at the Spandau plant. Then, the control unit for the battery is added and the case is sealed. After thoroughly testing the battery, it is transported to the general assembly line.
The CE 04 features a separately excited synchronous motor that operates at 148 volts and delivers 31 kilowatts of power.
The BalTec ELECTRIC EA30 is a roller forming machine with 3-axis servo technology. With its three-inline servo motors, the EA30 can control with precision the stroke and rotation of the roller head assembly and articulation of the roller wheels. Each axis is individually programmable, offering superior forming capability and flexibility.
BalTec Corporation
724-873-5757
Articulating Roller Forming with 3-Axis Servo Technology
“Instead of a fuel tank, a modern energy storage system is used, which supplies the electric motor with the necessary energy, regulated through power electronics,” says Christian Ott, C-Series product manager. “For those who need to charge on the go, an integrated onboard charger allows the battery to be charged up to 80 percent at public stations in just under an hour.
“Thanks to the simple operation without a clutch and gearbox, the technology fades into the background, making it pure fun, even for inexperienced motorcyclists,” explains Ott. “Even maneuvering and parking becomes child’s play with the electric reverse assist at the push of a button.”
Power and torque are transmitted to the rear wheel of the CE 04 via a belt drive. The result is powerful acceleration, taking just 2.5 seconds to go from 0 to 31 miles per hour.
“The complexity of the components can be rated lower than that of a comparable vehicle with a combustion engine,” explains Ott. “The biggest challenge is to design the drive components—especially regarding weight and range—and to integrate them aesthetically into the vehicle package.”
The CE 04 is produced on a dedicated assembly line. The first step is to attach the battery and traction motor to the frame, then connect the wiring harness. Next, various chassis parts are attached, followed by the body fairings, which are finished at the company’s in-house paint shop.
The last step on the assembly line is an overall inspection and quality check. After that, the electric scooter enters the media filling station, where brake fluid is added. Finally, the e-scooters take a test drive on a dyno where all functions are carefully checked and calibrated.
Automation is used for welding and engine assembly applications. But, most of the final assembly line involves manual processes.
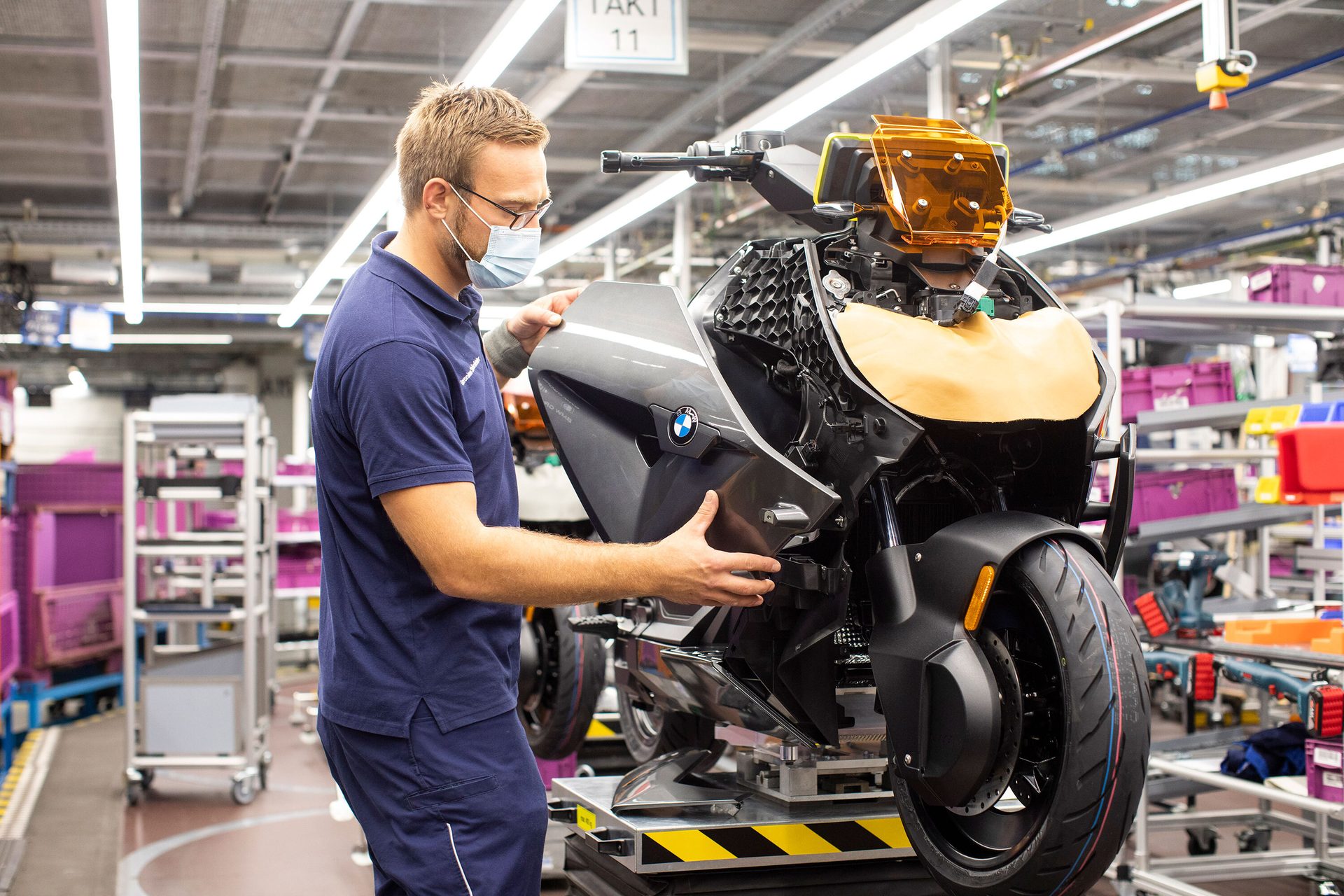
BMW’s state-of-the-art factory in Berlin mass-produces electric scooters. Photo courtesy BMW Motorrad
Lightning Focuses on Fast Past
Lightning Motorcycle Corp., founded in 2006, carved out an early reputation in the competitive world of racing. The company built the world’s first lithium-ion battery-powered sport bike, then proved its mettle by competing against—and beating—gas-powered rivals.
After setting speed records on the Bonneville salt flats and claiming victory at the Pikes Peak hill climb in 2013 by defeating the Ducati factory team by more than 10 seconds, Lightning pivoted from racing to production.
However, delivering the world’s fastest electric motorcycles isn’t just about speed for the company. It’s about precision, performance and complete control of the process from concept to final bolt.
“The first customer bike was a street-legal, road-going version of the bike that set the land speed record, won Le Mans and won Pikes Peak,” says Richard Hatfield, CEO of Lightning Motorcycle. “It featured over 240-hp at the rear wheel and 220-ft-lbs of torque at the motor shaft.”
The LS-218, named for its 218 mph top speed at Bonneville, was the company’s first commercial product. The custom machine blurred the lines between track weapon and luxury object. Each bike is made by hand in Hollister, CA.
“We’re making the majority of our components in-house,” says Hatfield. “[However], we buy battery cells, and we have a company that does windings and lamination for our motors.” It also purchases printed circuit boards (PCBs) from suppliers.
Lightning’s battery expertise is the product of years of experimentation and hands-on engineering. For instance, its battery management system and vehicle control unit are in-house designs.
“We have used a variety of different cells in the past—some from Korea, some made in the U.S. and some from Japan,” explains Hatfield. “The batteries today have a lot of trade-offs: cycle life, power per mile, range per mile, internal resistance and how much heat they generate under high-power discharge.”
That complexity has led Hatfield and his colleagues to develop a deep understanding of energy storage systems through rigorous testing and practical deployment.
“We’ve done a lot of battery testing,” claims Hatfield. “We’ve built a lot of different battery packs.”
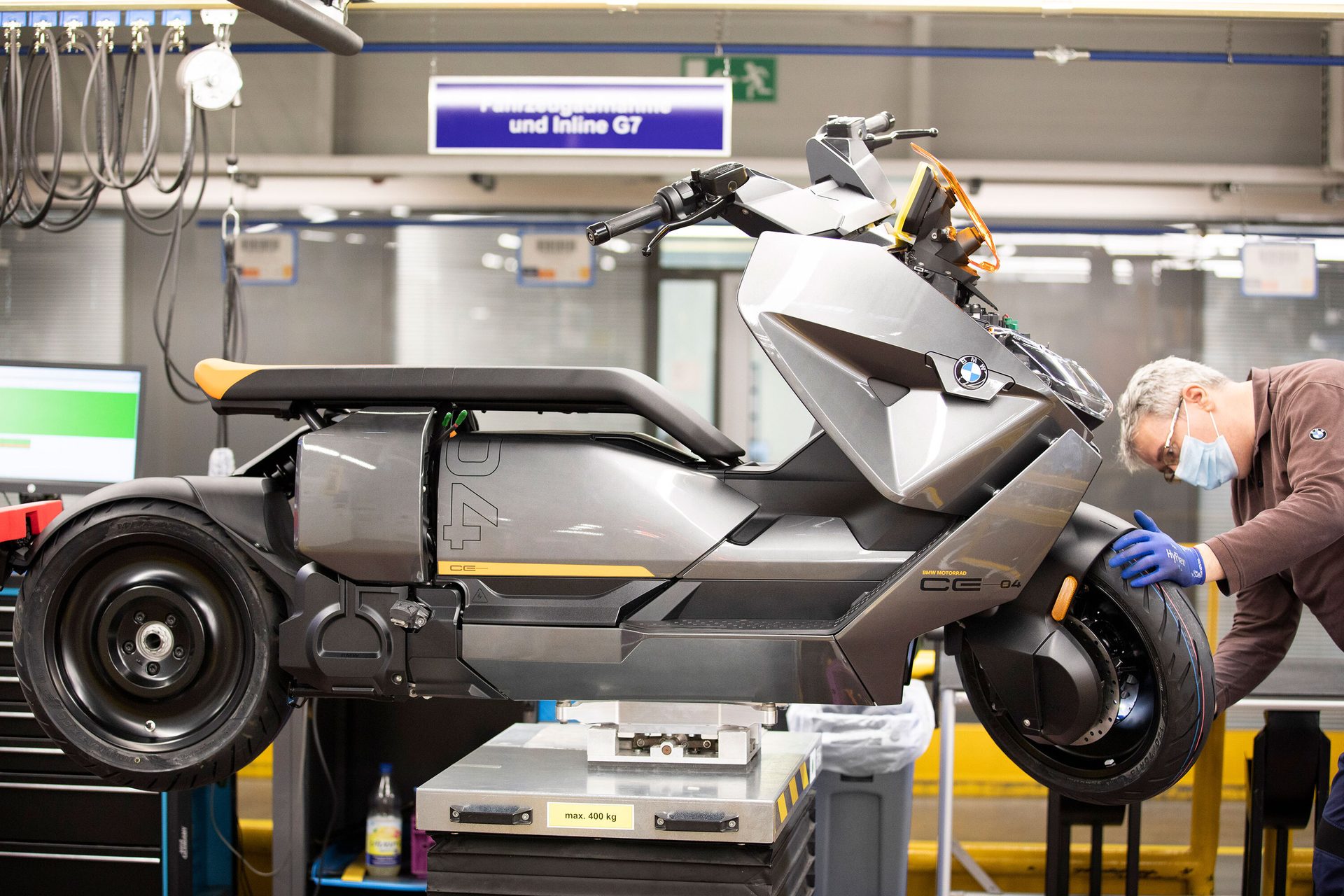
In some markets, electric scooters are cheaper than gas-powered alternatives. Photo courtesy BMW Motorrad
And, Lightning has experience beyond just motorcycles, because it has taken on engineering projects to support its core mission.
“We’ve done a whole series of projects for other companies to generate the capital to fund our electric motorcycle work,” says Hatfield said. “Everything from electric buses and trucks to off-grid systems, electric airplanes, boats and battery backup systems.”
That diverse experience has given Lightning a broad perspective on battery performance and optimization. “We’ve learned a lot about batteries and what the trade-offs are,” Hatfield points out.
Lightning’s approach to vertical integration is atypical in the modern motorcycle world, especially in the electric space where many start-ups rely heavily on off-the-shelf systems. The company designs PCBs and manufactures components like battery packs itself, often tailoring each bike to a customer’s intended use.
“If a customer is predominantly going to be riding the bike on long trips, then we’ll look at something that’s more biased toward longer range, higher energy,” notes Hatfield. “We can really tailor the bike specifically for that customer.”
Much of Lightning’s R&D happens in Hollister, and Hatfield envisions this site remaining the center for design and engineering as production expands internationally. However, the company is also actively exploring partnerships in India, which is home to one of the world’s largest motorcycle markets and a mature supply chain.
“India is a huge motorcycle producer,” says Hatfield. “There’s a well-developed joint-venture process there. BMW, Honda and KTM all build bikes there.”
Lightning’s design team works closely with engineers on iterative improvements, rapidly moving from prototype to production within the same facility. The company’s in-house capabilities include low-volume parts machining.
Lightning isn’t shy about comparing itself to Tesla. While not yet a household name, the company shares Tesla’s commitment to design control and vertically integrated manufacturing.
“We tend to think of the Strike kind of in Tesla terms, as the Model 3,” explains Hatfield.
Introduced in 2018, the Strike was envisioned as a more affordable follow-up to the record-setting LS-218.
“It was a bike that was built to deliver good value,” says Hatfield. That value, he argues, isn’t just in the performance specs—it’s revealed in how the bike is built.
For the company’s existing products, including its upcoming adventure bike and a new high-performance model to succeed the LS-218, Lightning maintains full control over critical components, ensuring tight tolerances and high quality assembly.
However, while in-house manufacturing has allowed the company to maintain quality and push innovation, it also limits production scale. Though he won’t disclose exact sales figures, Hatfield admits that volumes remain small.
“We are not building high volume,” explains Hatfield. “We’re building great bikes, but with a great deal of labor.”
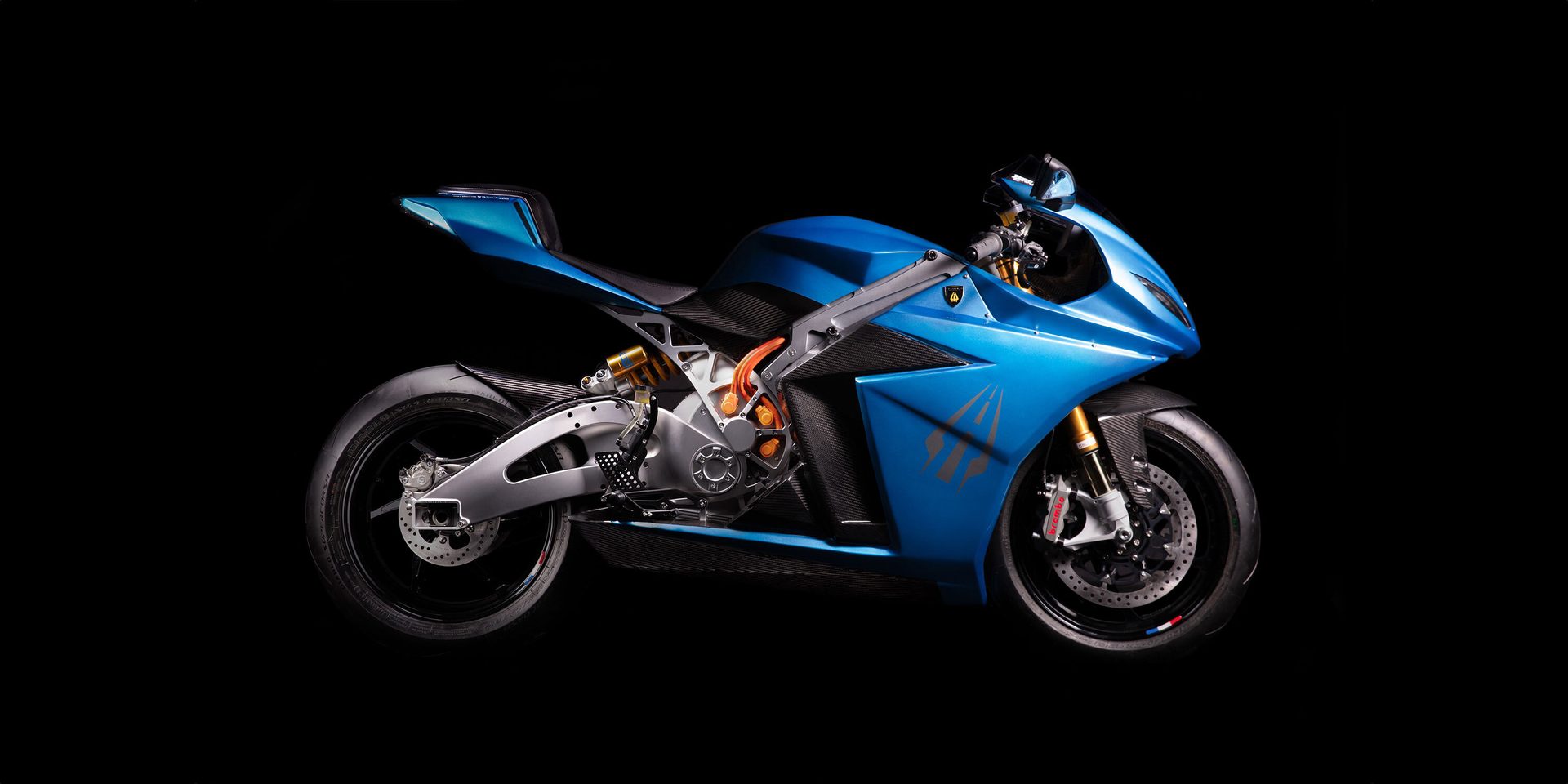
This hand-made electric motorcycle is built for speed. Photo courtesy Lightning Motorcycle Corp
Recent geopolitical tensions have complicated Lightning’s strategy in China, prompting a stronger pivot toward India, which offers a mature ecosystem for two-wheel manufacturing. Hatfield is enthusiastic about tapping into that country’s production capacity and engineering talent, envisioning a future where his company can deliver not only ultra-premium electric superbikes, but also mass-market offerings that compete globally with 250 cc to 400 cc gas bikes.
“We’re looking for the right partner to build in scale, then going down market where we can build more affordable bikes that compete in the world markets,” says Hatfield. “The partners we’re talking with are building millions of vehicles a year. They’re heavily leveraging automation and robotics. I think it’s natural to work with their engineering groups, take the technology we’ve developed and adapt it to leverage their processes."
Lightning’s variable configurations also allow for different use cases—from long-distance road trips to record-setting sprints.
“We’ve done a lot of battery testing,” Hatfield points out. “If someone wants to go out and set records on one-mile or two-mile runs, we bias toward higher discharge and lighter weight.”
In the near term, Lightning remains focused on developing technology that can hold its own against the best gas-powered sport bikes in the world.
Long-term, Hatfield envisions a broader lineup, with more price points and styles for different kinds of riders. But, he remains steadfast that performance will always be a part of the brand’s DNA.
“We are building electric motorcycles that are absolutely no compromise and that can compete against the best ICE motorcycles in rider experience and performance, and all of the metrics that really matter,” claims Hatfield.
Zapp Takes a Modular Approach
Zapp Electric Vehicles Ltd., a British company based in London, recently started to produce its i300 model. The electric scooter for urban applications is designed to offer motorcycle-level performance within a step-through format.
Assembly takes place at the company’s new facility in the Bangkok Free Trade Zone. Production began in December 2024.
The i300 is road-certified in multiple markets and does not require a motorcycle license in some regions. The 19-hp e-scooter can accelerate from 0 to 30 mph in approximately 2.35 seconds. Its electronically limited top speed is 60 mph. In Eco mode, the estimated travel range is approximately 37 miles per charge.
“We’ve just made our first run of production,” says David MacIntyre, chief operating officer at Zapp. “The assembly facility allows us to build over 20,000 units per year. Our investment is in the hundreds of thousands of dollars, as opposed to hundreds of millions.”
Initial deliveries will begin in Thailand, with plans to expand across other Asian markets and into Europe later in 2025. The facility in Bangkok covers less than 12,000 square feet and follows a modular, scalable, manual production process.
“We call it our reference manufacturing site, and it’s a model that can be replicated in other markets around the world,” claims MacIntyre.
The i300 features an exoskeleton chassis that provides a lower center of gravity and fewer total components. It uses a mid-mounted, air-cooled interior permanent magnet (IPM) electric motor, which is compact and designed for high efficiency.
The power system includes two removable lithium-ion battery packs. Each battery weighs around 13 pounds and is located beneath the rider’s feet to contribute to mass centralization. The i300 can operate with either one or both batteries installed.
The batteries are designed to be charged off the bike using a standard wall outlet. This modular charging capability offers users flexibility for daily urban commuting without relying on dedicated charging infrastructure.
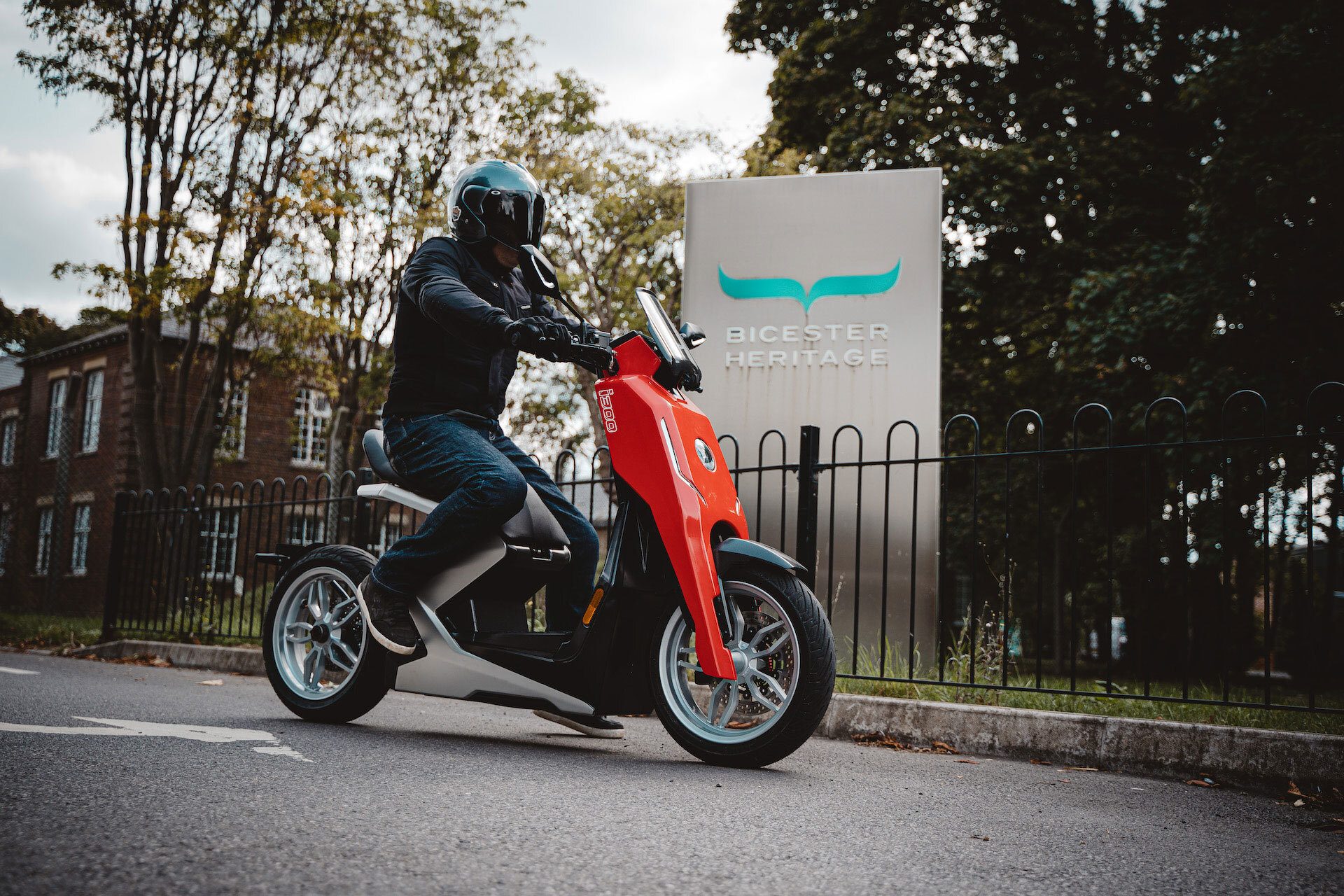
This electric scooter offers motorcycle-level performance. Photo courtesy Zapp Electric Vehicles Ltd
“The IPM motor is the most efficient device that we could find on the market to suit our needs,” says MacIntyre. “It can deliver up to 95 percent efficiency.”
The motor’s compact size and light weight align with Zapp’s overall design philosophy of maintaining a low center of gravity and lightweight construction. To complement the motor, engineers designed a battery system that focuses on volumetric energy density.
“You can leave one battery in the bike while you’re charging the other one,” notes MacIntyre. “You just take out the battery and charge it like a laptop.”
Zapp’s modular production model allows it to build small, scalable factories without heavy automation or conveyor systems. The i300 was designed with a “low component architecture” that reduces the total number of primary parts to under 150.
The visual design of the i300 was shaped not only by performance goals, but also by an emphasis on aesthetics and weight efficiency. It incorporates both visual distinctiveness and functional engineering. One prominent example is the mono swing arm, a single-sided rear suspension component with structural cutouts that reduce mass. Weight distribution was also a primary consideration.
“All the weight is pushed as low as possible, which is why the batteries are below your feet,” explains MacIntyre “It’s why the motor is mid-mounted as opposed to, say, hub-mounted. The placement strategy is designed to improve stability and handling by centralizing the mass lower in the frame”
Zapp’s modular production process uses five subassembly stations followed by a final assembly line. “This gives us a takt time of 20 minutes, so we can produce three jobs per hour,” says MacIntyre.
Based on this configuration, the company estimates an output of approximately 7,000 units per year on a single shift, with a maximum capacity of more than 21,000 units annually across three shifts.
“One of the benefits of being in Thailand is that there is a very well-established supply chain for premium motorcycles,” MacIntyre points out. Many hardware components are locally sourced. But, motors come from England, inverters from Italy and lithium-ion batteries from China.
Zapp eventually plans to replicate its microfactory model in other regions, particularly where demand for electric two-wheelers is growing. For instance, the company is currently evaluating opportunities in Europe, India and Latin America.
According to MacIntyre, e-mobility tends to be particularly well-suited to two-wheeled vehicles due to their lighter weight and lower range requirements compared to cars. “Electric mobility makes much more sense on two wheels than it does on four,” he points out. “Because you need to carry less battery, you don’t need as much range.”
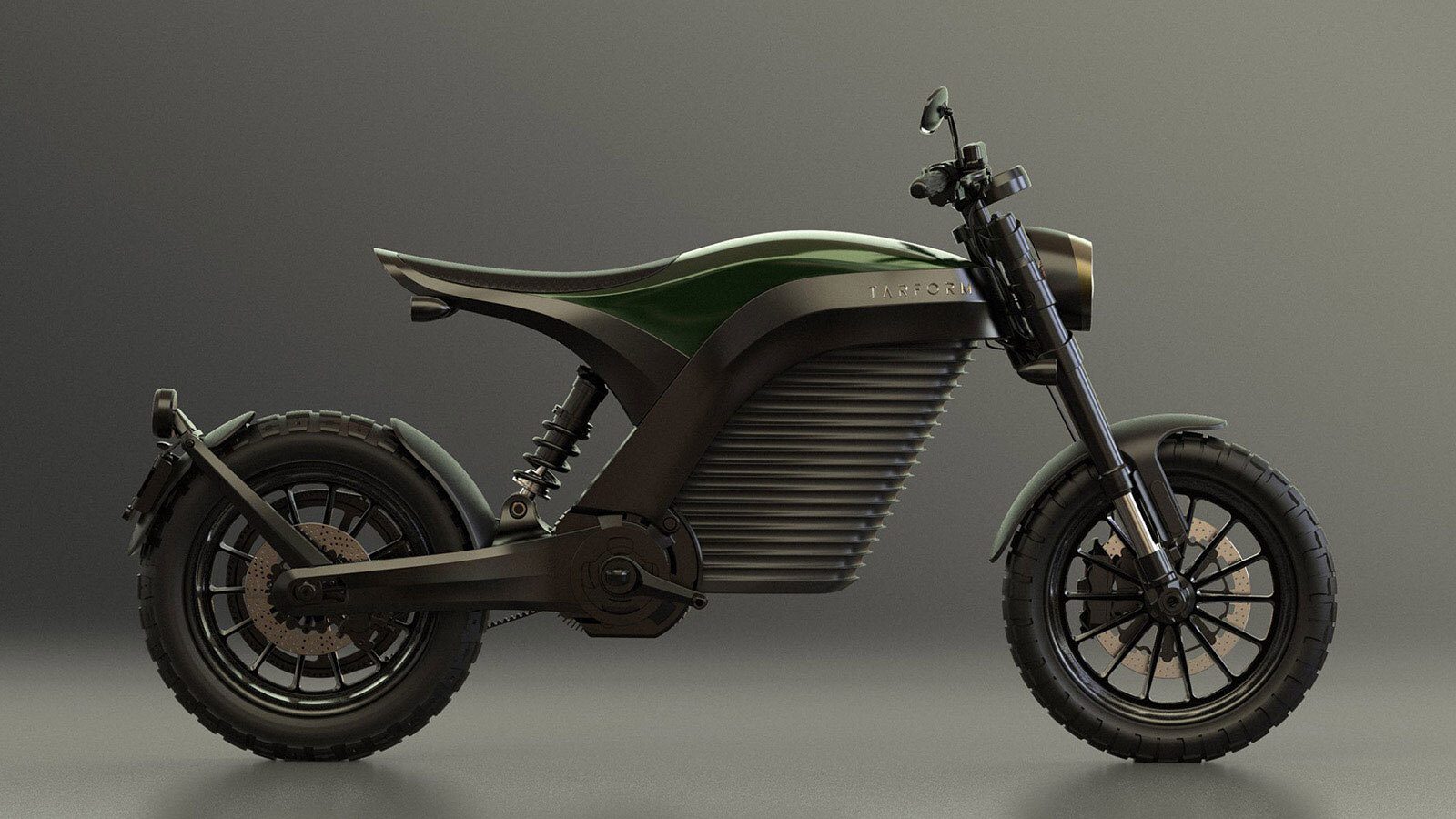
This luxury bike features a blend of modern electric power train components and classic motorcycle aesthetics. Photo courtesy Tarform Inc.
Tarform Targets Classic Design Aesthetics
What began as sketches on a napkin a decade ago has grown into an electric motorcycle start-up called Tarform Inc. The company evolved from founder and CEO Taras Kravtchouk’s ambition to blend classic motorcycle aesthetics with the future of electric mobility.
Kravtchouk, whose background is in product design and technology, used to spend his weekdays immersed in screen-based work at his design studio, while his weekends were dedicated to restoring Nortons, Triumphs and other vintage British motorcycles.
By 2017, Kravtchouk began to see a shift in local interest in electric motorcycles. Despite growing conversations around EVs, he felt the available electric bikes lacked the appeal and personality of traditional motorcycles. “No one’s really made anything that is desirable,” claims Kravtchouk.
This observation sparked the idea to build an electric motorcycle that retained the iconic spirit of a vintage café racer while incorporating future-facing design language. Working out of a garage in Brooklyn, Kravtchouk and two collaborators began figuring out what was required to make the concept a reality.
From mechanical engineering to electrical systems, they taught themselves how to build a bike from scratch.
“It took us about a year and a half to build the first two prototypes,” says Kravtchouk. “They were kind of like a vision statement—they were barely running and cobbled together with 3D-printed parts.”
Instead of building everything in-house, the entrepreneurs began reaching out to technology partners, asking if they’d be interested in showcasing their innovations through the prototype bikes. That approach led to a formal launch at New Lab, a Brooklyn, NY-based hardware accelerator located in the old Navy Yard. The prototypes generated interest, leading to early press coverage and an initial round of funding.
That early validation helped transform Tarform from an exploratory design project into a venture-backed start-up aiming to produce electric motorcycles at scale. The company currently has around 30 vehicles on the road, with production time now ranging from one to two weeks per unit.
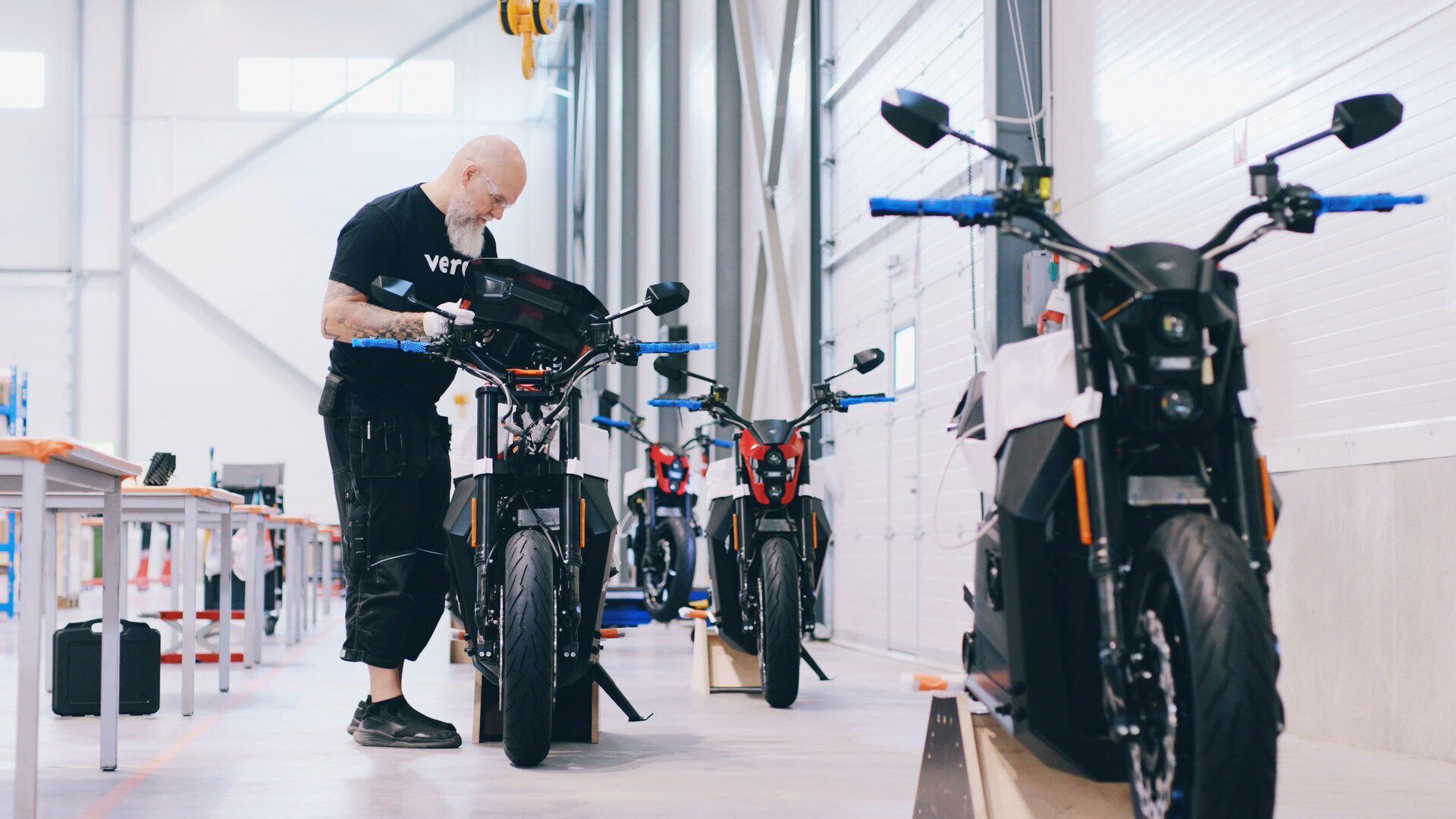
Despite its modest size, Verge’s assembly line features advanced production processes. Photo courtesy Verge Motorcycles
The Luna is a $44,000 luxury model that features a blend of modern electric power train components and classic motorcycle aesthetics. The company’s second model, the Vera, is currently in development and will target a broader market with a lower price point of around $16,000.
Building an electric motorcycle from scratch involved a steep learning curve for Kravtchouk, who began with knowledge of internal combustion engines, but little experience with electric drivetrains. “Most guys who like motorcycles try to avoid electrical stuff because, to a lot of them, it’s just wizardry,” he points out.
Kravtchouk’s early research involved watching YouTube tutorials and home-build videos to better understand electric vehicle architecture. He identified three core components: battery, motor and inverter. Additional features, such as Bluetooth connectivity and vehicle control units, were layered on later.
Designing the Luna began with aesthetics, bucking the traditional approach of starting with internal components. Kravtchouk prioritized visual appeal to bridge the gap between classic motorcycles and futuristic design.
After finalizing the exterior, Kravtchouk collaborated with a French company to develop a 10-kilowatt-hour battery pack that balanced range and performance. A redesigned trellis frame and new battery system followed, resulting in a preproduction model with improved handling, acceleration and range.
“The only thing I think we kept from the first prototype was the motor,” says Kravtchouk. “The development process emphasized performance characteristics like weight distribution and handling.
“A lot of thought and attention went into weight distribution, handling and trying to find a perfect blend between a bike you can take on the highway and something nimble in the city,” explains Kravtchouk.
Sustainability was also a major focus. That’s why the Luna incorporates hand-shaped aluminum tanks, in addition to carbon fiber and bio-based materials.
“How we reduce our waste throughout the whole manufacturing cycle was a major consideration,” claims Kravtchouk. His environmental goals extend beyond producing zero-emission vehicles; they aim to improve the entire lifecycle of the motorcycles.
Tarform produces vehicles in batches of five to 10 at a time, adjusting designs based on customer feedback to refine the power train, improve reliability and reduce overall weight.
Design work begins with 3D modeling software before moving into Fusion 360 or SolidWorks for detailed mechanical design and system integration. Once designs are finalized, parts are either printed in-house for prototyping or sent out to a global network of suppliers across Canada, China, India, Mexico and Sweden.
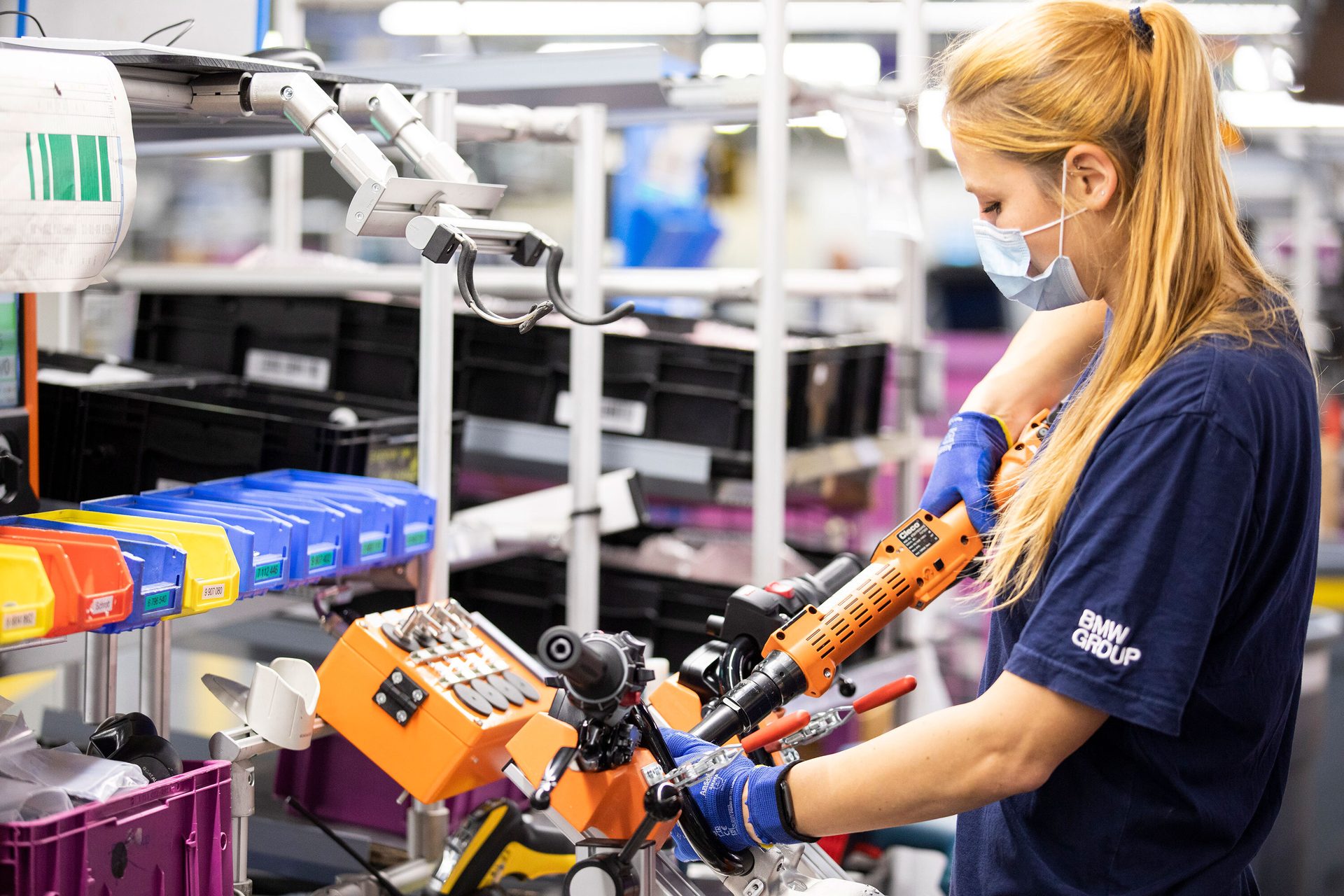
Traditional motorcycle manufacturers, such as BMW, have developed electric versions of their machines. Photo courtesy BMW Motorrad
“We don’t manufacture parts ourselves,” says Kravtchouk. “There are hundreds, all requiring different manufacturing methods. It’s basically like a giant Lego set.”
As production scaled, Tarform hired a production engineer with experience at Aston Martin and McLaren. “He helped us create a blueprint for quality control, inventory management and standard operating procedures,” explains Kravtchouk. “Initially, it felt like wasted time, but we quickly saw the value of proper documentation and workflow tracking.”
By adopting lean manufacturing principles, Tarform was able to streamline its shop for efficiency, create workflows and minimize waste.
Each motorcycle is assembled according to a 120-step build sequence starting with the frame, battery, motor and controller, followed by electrical components and accessories. Once fully assembled, the bike undergoes rigorous testing. Each vehicle is personally test-ridden for several hours by Kravtchouk himself around the Brooklyn Navy Yard for several hours.
As Tarform transitions from its custom-made Luna motorcycle to the more mass-market Vera, the company is rethinking how it approaches production. The lessons learned from building the Luna are shaping the strategic direction of the Vera.
“We learned so much from Luna,” recalls Kravtchouk. “How do we reduce parts? How do we reuse parts we’ve already developed? How do we make things lighter, more efficient and streamline our assembly process?”
The Vera’s design process prioritized simplification and scalability. The focus has shifted toward keeping key components and design elements that define the brand’s visual identity, while eliminating unnecessary complexity to make production more efficient.
The first batch of Vera motorcycles will follow a low-volume production pattern, before scaling up. Between 20 and 50 units will be built in Brooklyn using the company’s refined in-house assembly process, which includes subassemblies, structured build sequences and end-of-line testing. However, to scale up further, Tarform plans to transition to a contract manufacturing model.
“The idea is to outsource to a contract manufacturer somewhere in the United States,” says Kravtchouk. He’s currently evaluating potential partners and locations to establish this next phase of production.
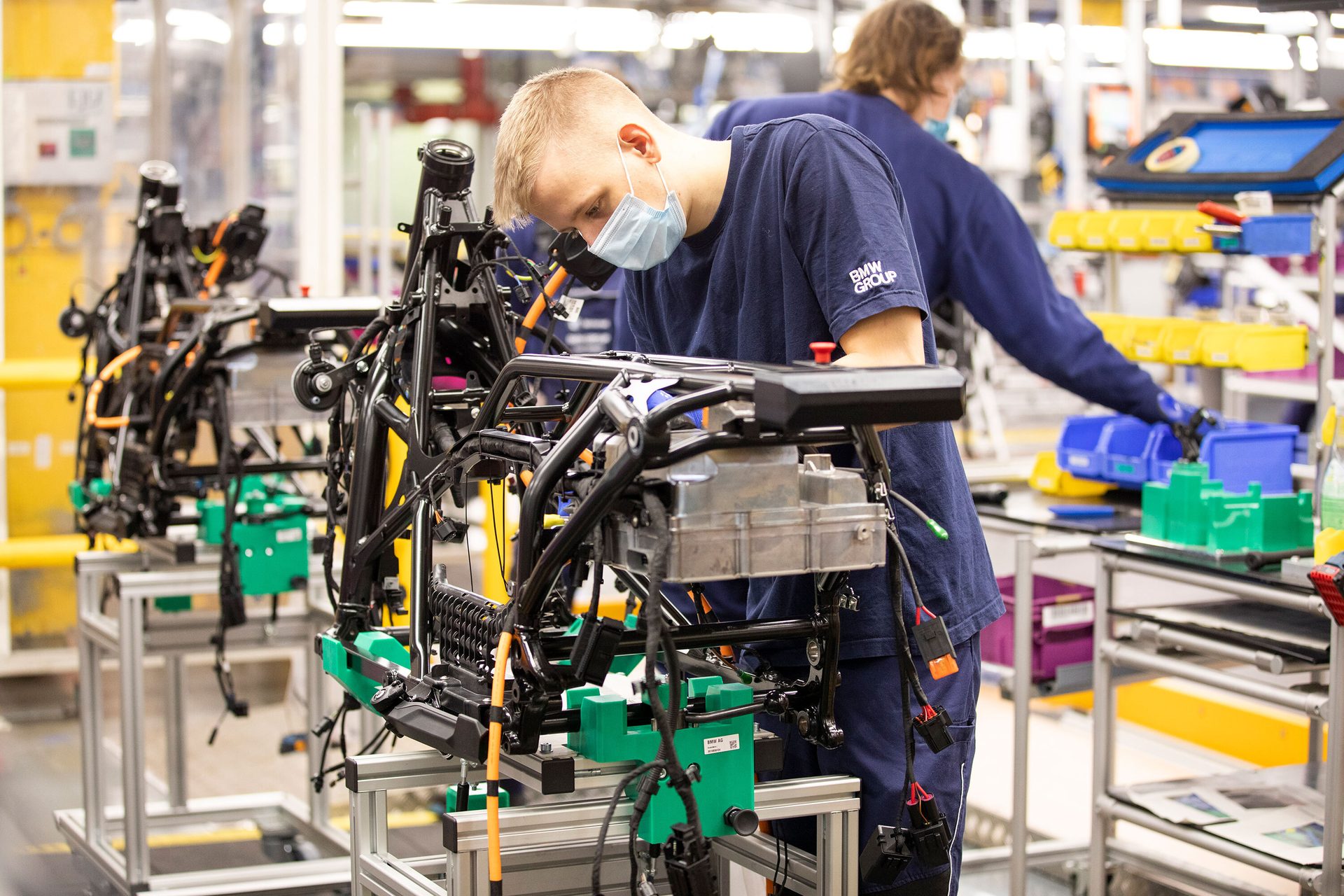
Until production volumes ramp up, electric scooter and motorcycle manufacturers are relying on manual production methods. Photo courtesy BMW Motorrad
On the Verge of Success
Verge Motorcycles is building its electric future in Estonia, with a manufacturing strategy rooted in autonomy, scalability and precision engineering. Led by CEO Tuomo Lehtimäki, the company produces two models of electric motorcycles—the TS Pro and the TS Ultra—designed to combine high-tech functionality with a European supply chain and a flexible factory model.
The TS Pro model has been in limited production for two years and is currently only available in Europe. However, deliveries to the U.S. are expected to begin by the end of this year. The TS Ultra is already available for reservation, but will enter production in 2026.
Future improvements to the bikes will focus on battery performance and charging speed. “We will have faster charging bikes that go longer distances,” says Lehtimäki. He believes adding battery safety and range are critical to making gas-powered motorcycles obsolete.
The start-up company evolved from a desire to reimagine personal mobility for a new generation of riders seeking powerful, sustainable and low-maintenance alternatives to traditional motorcycles.
Verge’s factory, located outside Tallinn, spans 43,000 square feet and operates with a compact, but carefully integrated layout. The facility was designed to remain flexible, with all equipment intentionally unbolted from the floor.
This portability is central to Verge’s broader manufacturing strategy: treat the factory itself as a flexible product that can be copied and easily deployed in new markets.
“We can have all the same tools and same layout in any empty building,” says Lehtimäki. “If we need a factory in South America, we can buy all the same things we have here. We copy this factory and start locally.”
The Estonian facility currently handles motor assembly, battery pack production and final bike assembly under one roof. Despite its modest size, Verge’s assembly line supports advanced production processes.
“We have 200 suppliers and build the motors in-house, from coil winding to assembly,” explains Lehtimäk. Verge also produces its own frames using a robotic welding cell.
Rather than chasing the lowest price globally, the company has focused on building relationships with reliable suppliers in Estonia, Finland, Germany, Italy and Sweden.
Last year, Verge built 100 vehicles, which is a pace deliberately aimed at ensuring quality and refining processes. “We don’t want to accelerate too quickly,” says Lehtimäki.
The company’s modular, transportable factory model not only provides agility in uncertain global markets, but also aligns with Verge’s values of transparency and local engagement. “We are ready to just copy and paste a similar assembly plant to any country,” claims Lehtimäki.
With an in-house supply chain, a flexible factory model and ambitious expansion plans, Verge is positioning itself as a long-term player in the premium electric motorcycle market. As production scales, its modular approach to manufacturing may allow it to reach new markets without sacrificing its identity or values.
“We are making good business decisions,” claims Lehtimäki. “And, we are doing it our way.”
ASSEMBLY ONLINE
For more information on motorcycle manufacturing, visit www.assemblymag.com to read these articles:
MAY 2025 | ASSEMBLYMAG.com
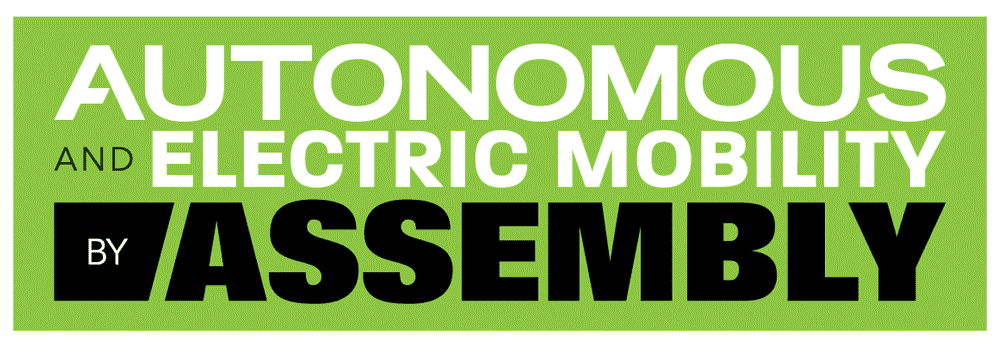