APRIL 2023
A special section to ASSEMBLY
Cobots Install Cable Ties
xxx
For a real-world application, engineers will need to develop a specialized end-effector for installing cable ties. Photo courtesy Tecnológico de Monterrey
Ciro A. Rodriguez, Ph.D. // Professor Of Mechanical Engineering // Tecnológico De Monterrey // Monterrey, Mexico
By some estimates, 90 percent of wire harness assembly tasks are done manually. As a result, harness assemblers are at risk of occupational health problems due to repetitiveness and awkward postures. Improving these processes is therefore critical for both productivity and ergonomics.
Collaborative robots have the potential to radically increase productivity, improve ergonomics and lower costs. Conceivably, cobots could be used to route wires, insert wires, tape wires or install cable ties.
To date, however, few studies have looked at applying cobots in the harness assembly process. One study, for example, demonstrated that a cobot could effectively automate the process of spot-taping wires on a harness board. Another study showed that cobots could successfully assemble electrical connectors.
On the other hand, harness assembly does pose challenges for automation. In a laboratory study, the harness never changes, so the cobot only needs to be programmed once. In a high-mix harness shop, the cobot would have to be reprogrammed constantly, which would eat into productivity gains. The parts themselves represent another challenge. Robots typically have difficulty handling flexible objects, such as wire and cable, that move in unpredictable ways. As a result, most attempts at automation focus on tasks, such as taping, in which the harness is fixed in place.
Our study examines the possibility of using a vision-guided cobot to install cable ties on a wire harness. The work was done in collaboration with a small Mexican manufacturer that specializes in the production of electrical, automotive and industrial wire harnesses. In an interview, the company’s production manager identified cable tie placement as the process that generates the most ergonomic problems for her workforce. We wondered if a cobot could alleviate that burden. The addition of machine vision to the application could, in theory, solve the problem of having to reprogram the cobot to work on different harnesses.
Ergonomic Assessment Methods
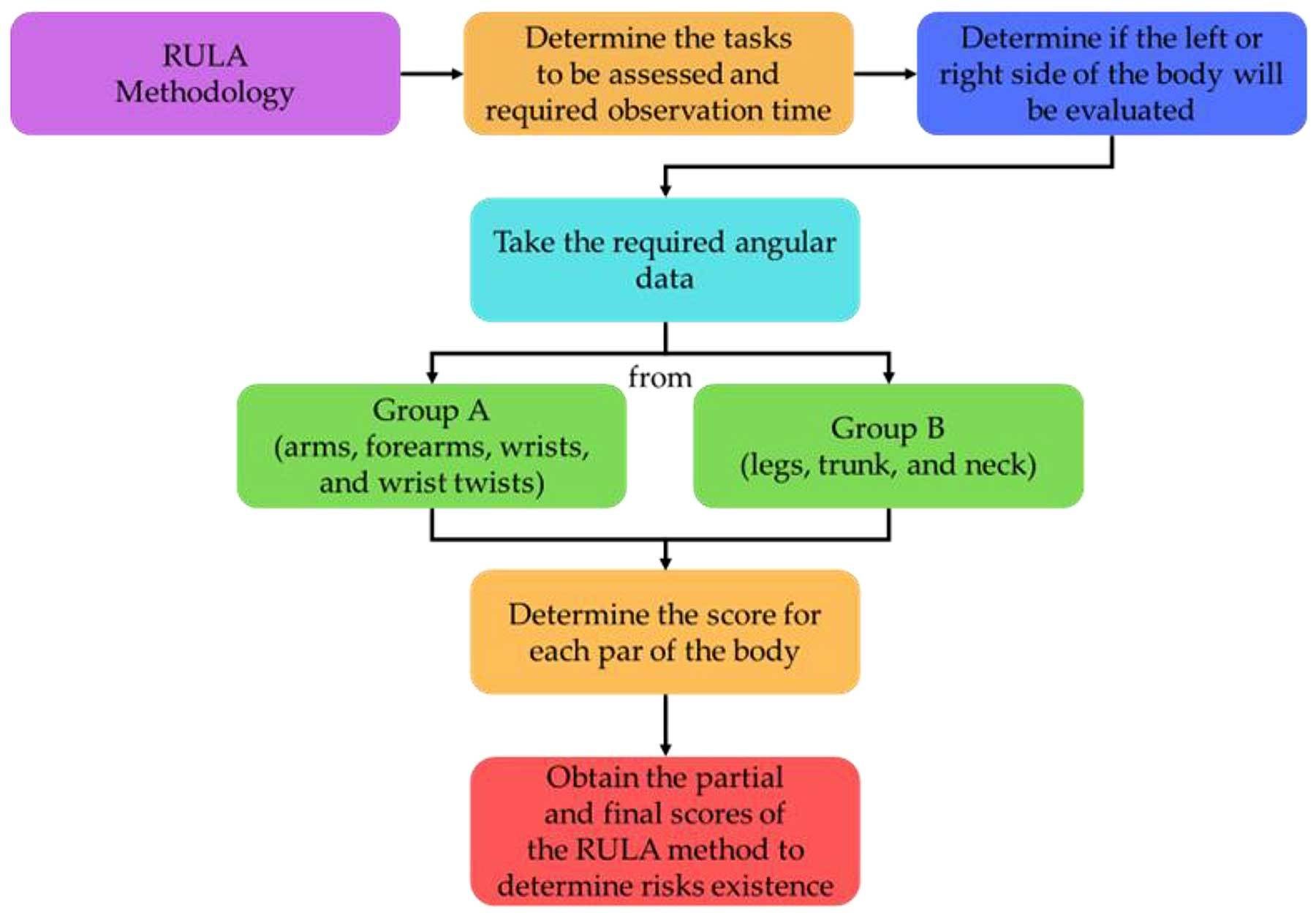
RULA helps identify the risk factors associated with high postural loads. Illustration courtesy Tecnológico de Monterrey
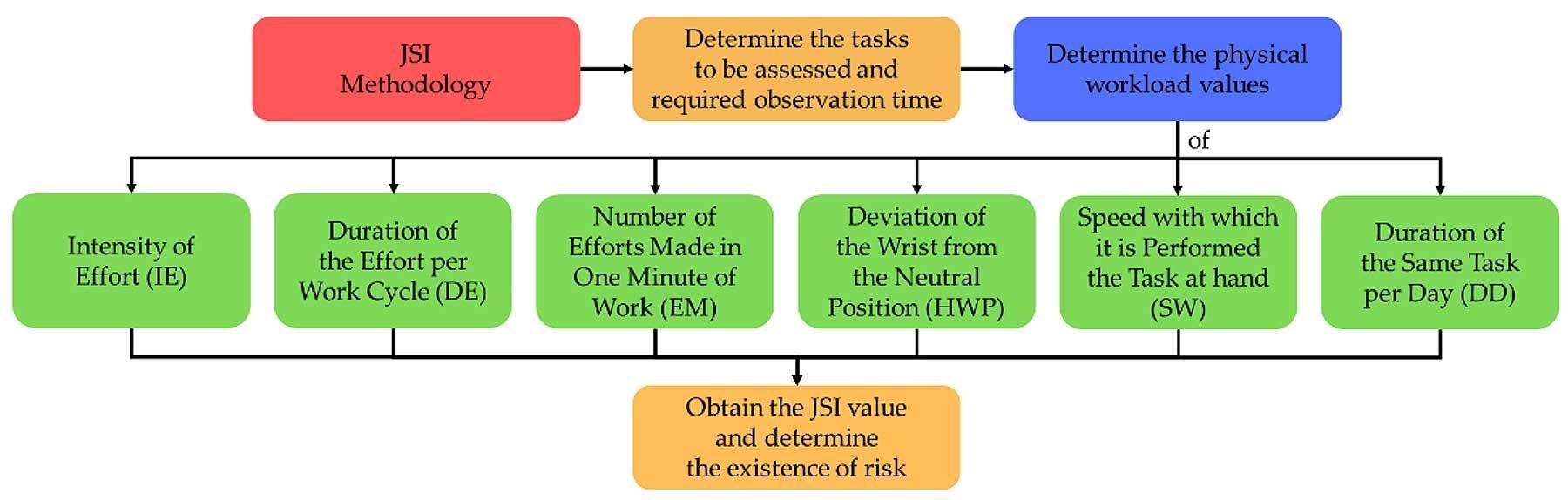
The JSI complements RULA, considering additional factors such as time and speed. It can predict whether workers will develop injuries due to repetitive motion of their upper limbs. Illustration courtesy Tecnológico de Monterrey
Our study uses two methodologies to evaluate the ergonomics of a harness assembly task: the Rapid Upper Limb Assessment (RULA) and Job Strain Index (JSI). RULA is a robust ergonomics evaluation method. It measures all upper body limb angles and considers other factors, such as muscular activity and applied forces. The JSI complements RULA, considering additional factors such as time and speed. Moreover, the JSI can predict whether workers will develop injuries due to repetitive motion of their upper limbs.
RULA helps identify the risk factors associated with high postural loads. It also recognizes ergonomic problems due to excessive postural load on the upper limbs of a worker. RULA provides a score that determines if the work postures are acceptable or require changes, or even a complete redesign of the task.
RULA only evaluates individual postures and not a sequence of postures in a job routine, so it’s necessary to determine which postures should be considered. First, it has to be specified which postures will be evaluated. These are selected by looking at those tasks with a more significant postural load based on their duration, frequency and deviation from the neutral position.
Postural load measurements are completed by calculating the angles of different body parts with their determined reference. The tool RULER from the Ergonautas Research Group of the Polytechnic University of Valencia conducts these angle evaluations using photographs.
To calculate the RULA score, the body is divided into two groups: Group A consists of arms, forearms, wrists and wrist twists. Group B consists of legs, trunk, and neck. A RULA score is assigned to each body part using scoring tables. Then, general values are calculated for each group using the scores of each body part.
The musculoskeletal injury risk is determined with levels from 1 to 4. The final scores of each group are adapted according to muscular activity and the forces applied in the task. With these scores, the final values are calculated. “1” is an acceptable posture, and “4” shows that a change is urgently required.
In a complementary way, the JSI evaluates whether a worker could develop repetitive motion injuries in his upper extremities due to work activities. The JSI measures six physical workload variables: the intensity of effort (IE), the duration of the effort per work cycle (DE), the number of efforts made in one minute of work (EM), the deviation of the wrist from the neutral position (HWP), the speed with which the task is performed the task (SW), and the duration of the task per day (DD).
The final JSI score is calculated by multiplying the variables: IE x DE x EM x HWP x SW x DD.
If the JSI is less than or equal to 3, it indicates that the task is probably safe. A JSI greater than or equal to 7 indicates that the task is likely dangerous. Scores higher than 5 are associated with musculoskeletal disorders of the upper extremities.
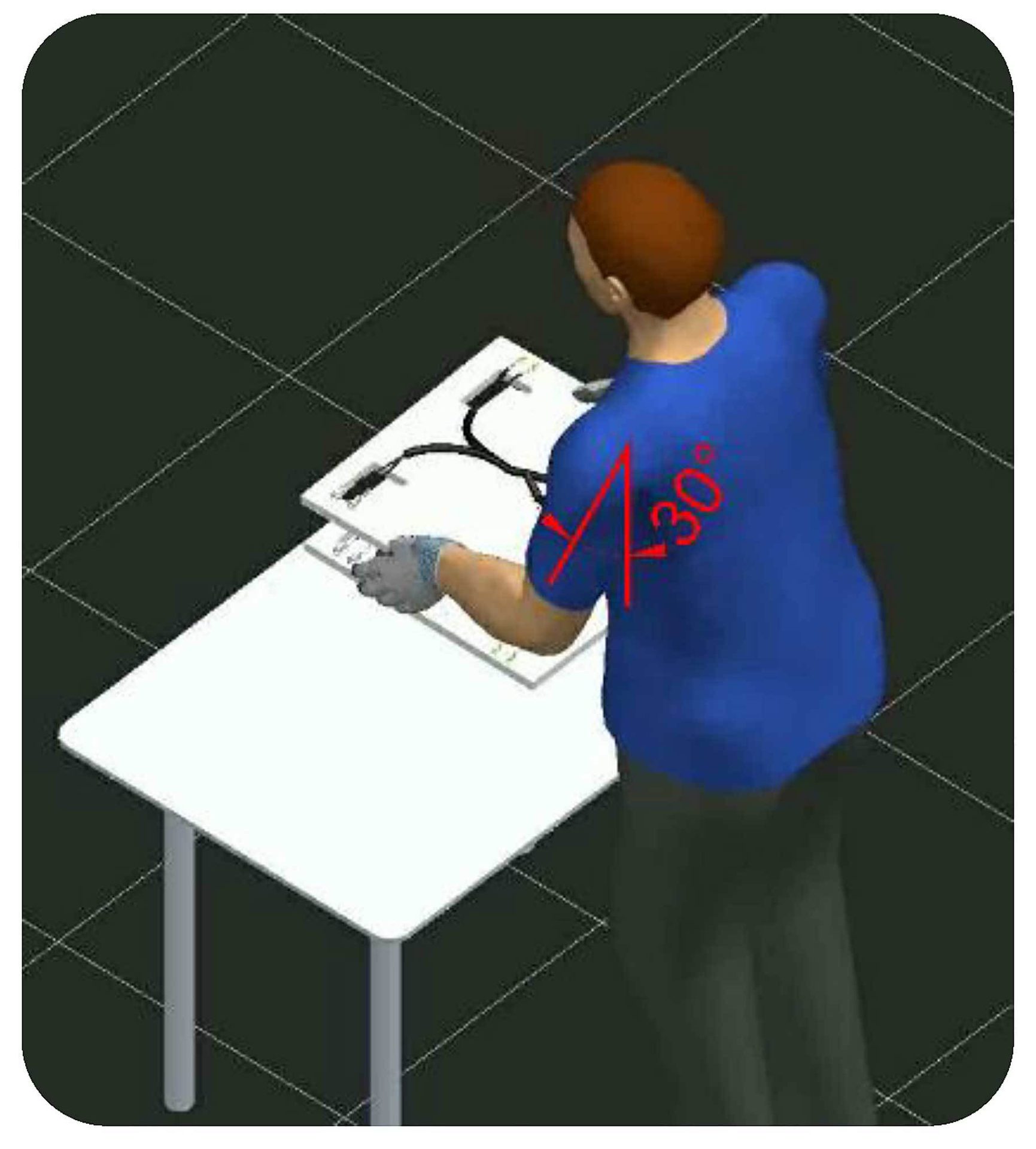
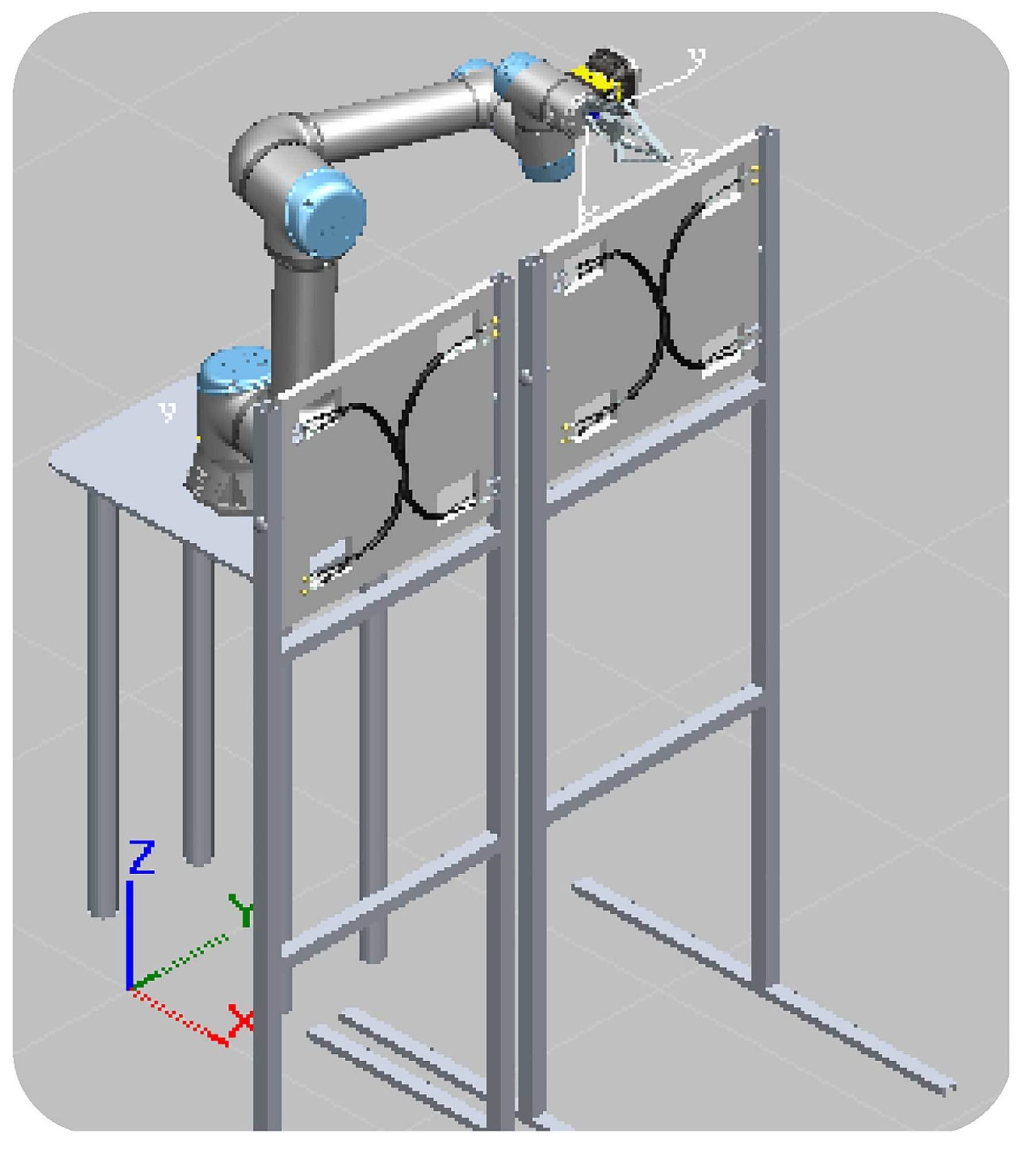
Among other variables, RULA measures the angle of arm positions during an assembly task. Photo courtesy Tecnológico de Monterrey
The researchers designed a workstation with a cobot at the back of the assembly board. This arrangement eliminates the risk of collision between the worker and the cobot. It also allows completion of two boards simultaneously. Photo courtesy Tecnológico de Monterrey
We used the following equipment in our study:
- Universal Robots UR5 six-axis cobot.
- On Robot RG2 two-finger gripper.
- Cognex IS7905M machine vision camera.
The RULA and JSI scores for installing cable ties indicate that the task is ergonomically risky.
After measuring the angles of various body parts during installation, the values of Groups A and B were calculated. The value for Group A was 5 and the value for Group B was 8, for a final RULA score of 7.
For the JSI, we obtained the following values: IE = 1, DE = 2, EM = 3, HWP = 2, SW = 1, and DD = 1. The JSI is therefore 1 x 2 x 3 x 2 x 1 x 1 = 12.
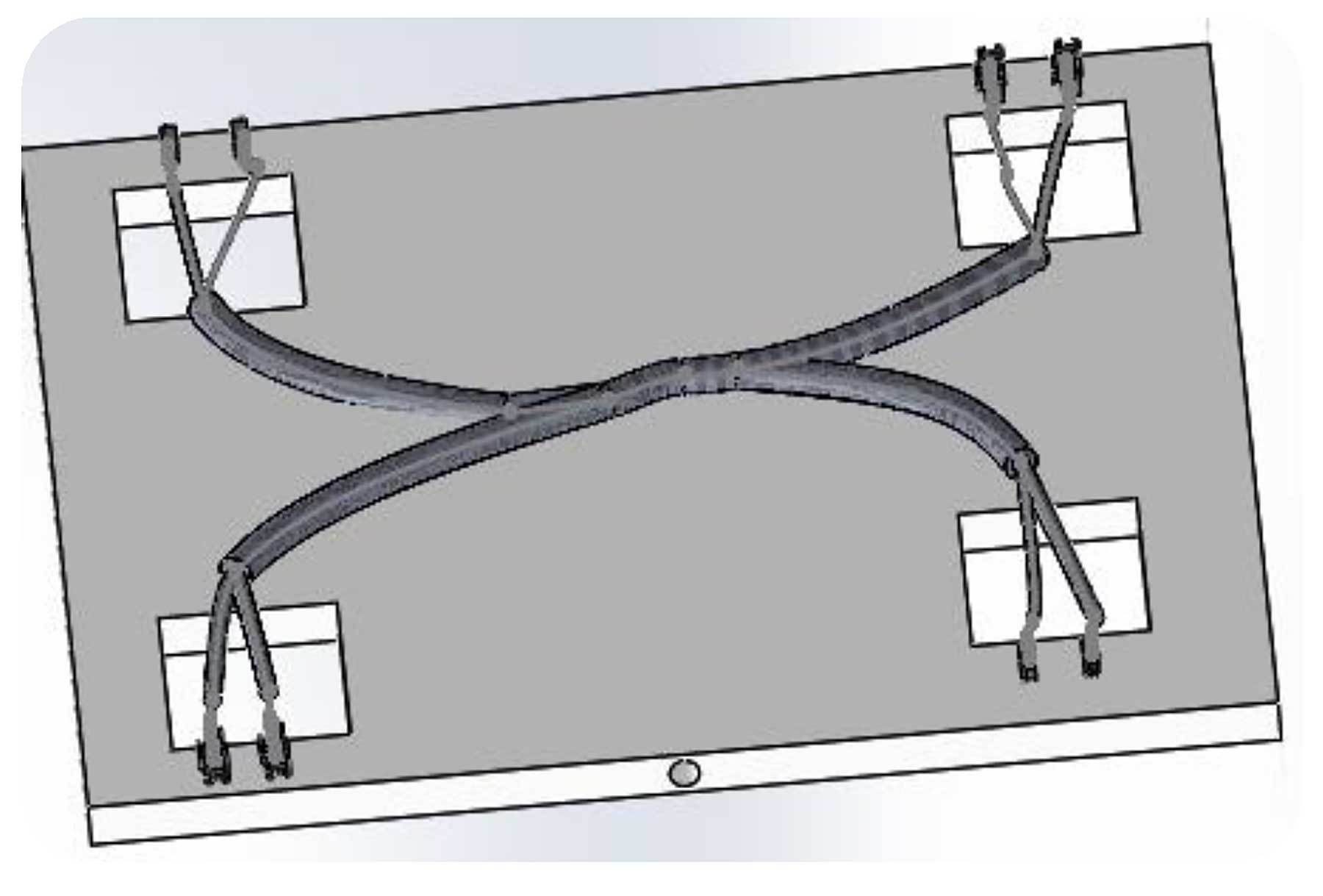
The researchers’ experimental wire harness required four cable ties to be installed in opposite corners. Photo courtesy Tecnológico de Monterrey
Next, we designed a workstation with a cobot at the back of the assembly board. For our design, we needed to make some holes in the assembly boards so the cobot could install the ties from behind. This arrangement eliminates the risk of collision between the worker and the cobot, since they do not work side by side. It also allows completion of two boards simultaneously. While the assembler is working on Board 1, the cobot can be working on Board 2, and vice-versa.
Our experimental process worked as follows: First, the assembler places the harness onto the assembly board. Next, the camera photographs the board to identify the number and positions of the holes and sends this data to the cobot. Then, the cobot will install a cable tie one by one at each hole position. Meanwhile, the worker places the other wire harness into the second assembly board. Lastly, the cobot installs the cable ties in the second board before going to a waiting position to repeat the task.
The interaction between the cobot and the worker is sequential, because they perform their assembly tasks independently and in sequence. They work on the same wire harnesses, but at different moments.
Case Study
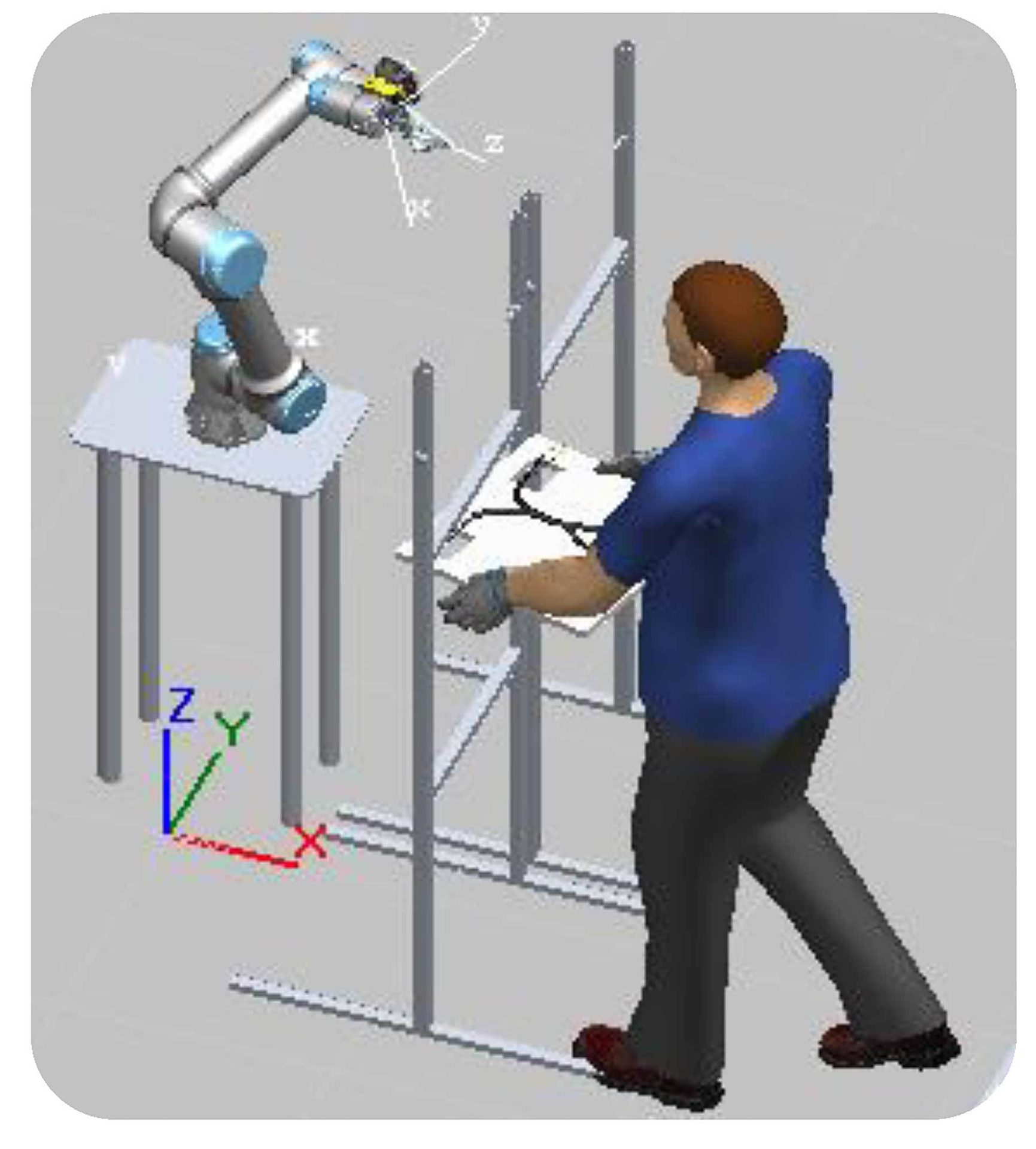
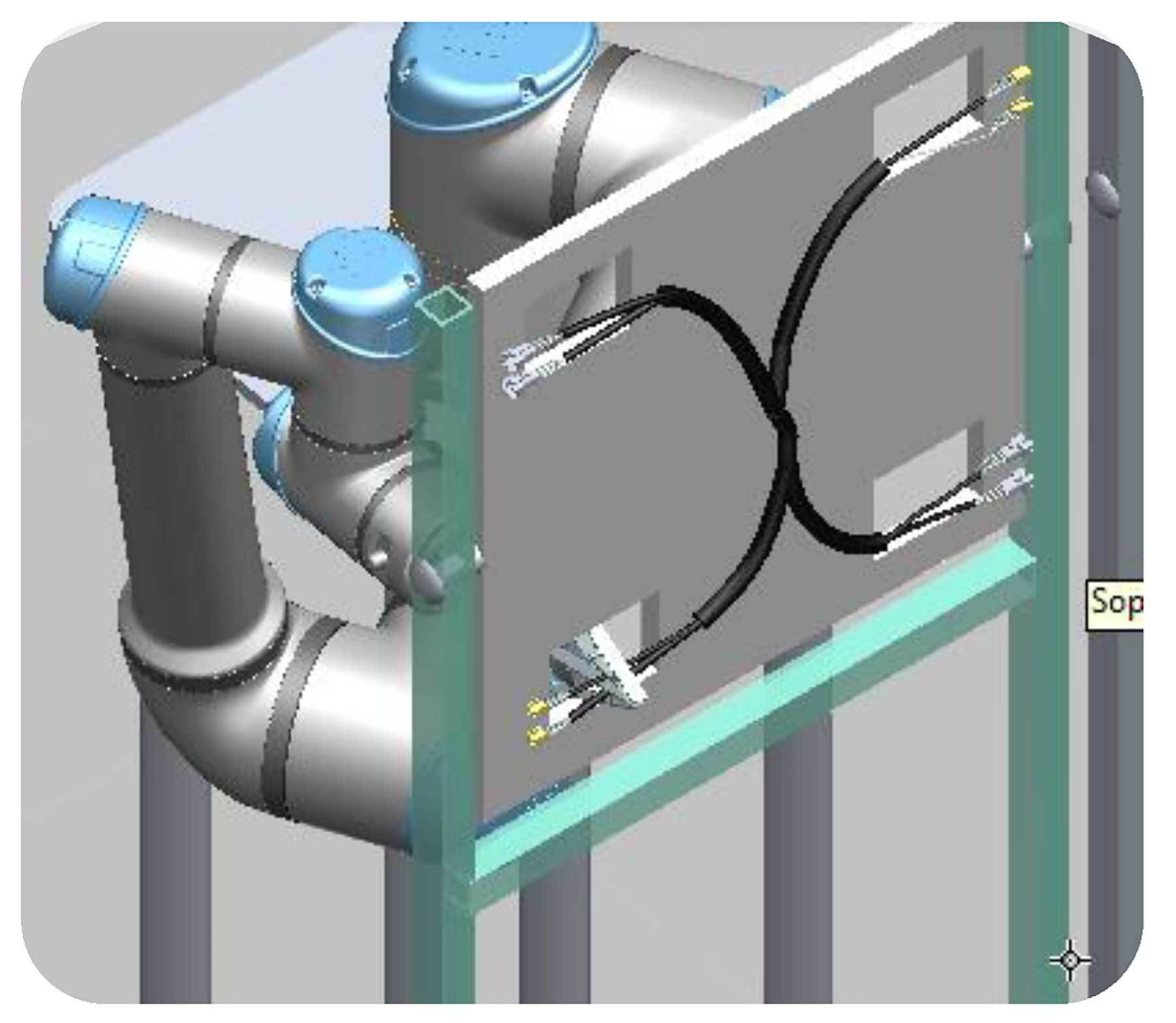
An assembler loads a harness assembly board onto the workstation. Photo courtesy Tecnológico de Monterrey
A cobot installs a cable tie onto a harness. Photo courtesy Tecnológico de Monterrey
Our project is a functional prototype of a human-robot collaborative workstation for cable tie installation. For real-world operation, a specialized end-effector for cable tie installation would need to be developed.
To program our system, the first step was to teach the camera to identify the holes in the harness board. The camera software can only transmit the position of each hole one by one, rather than as a group. As a result, it was necessary to use Modbus communication to send the number of holes found by the camera to the cobot.
The cobot program for installing the cable ties was designed in Polyscope, Universal’s programming software. The program works for two different harness assembly boards.
Finally, we did an ergonomic analysis of the new cable tie installation process using RULA and JSI. After measuring the angles of various body parts, the values of Groups A and B were calculated according to RULA. The value for Group A was 3, and the value for Group B was 4, resulting in a final score of 4. This score is significantly lower than the original manual operation.
Similarly, the JSI for the automated station was 4.5, which is lower than the risk level for the manual operation.
Our project clearly shows that cable tie installation task could be automated, improving ergonomics.
Our biggest technical problem was related to programming the vision system. The camera could not work on the Z axis of the workspace of the workbench; this was from the Cartesian coordinate system perspective of the cobot. This is why the calibration process had to be carried out in the X-Y plane of the cobot. To correct this issue, it was necessary to generate two planes in the cobot program code and transform the coordinates that are in the X-Y plane to the Y-Z plane.
Issues to explore in the future include:
- Design a specialized end-effector for cable tie installation and its integration with the cobot arm. There are three possible approaches to this task. One would be to adapt an existing hand tool for the cobot. Another would be to adapt an existing gripper for the task. A third option would be to design a robotic installation tool from scratch.
- Establish a safety protocol for assemblers that will allow them to work securely with the cobot during cable tie installation.
- Compare automated cabled tie installation with manual installation in terms of quality and cycle time.
Editor’s note: The following also contributed to this article: Gabriel E. Navas-Reascos, David Romero and Federico Guedea of Tecnológico de Monterrey, and Johan Stahre, Ph.D., professor of production systems at Chalmers University of Technology, Göteborg, Sweden.
This article is a summary of a much longer research paper. To read the complete paper, click here
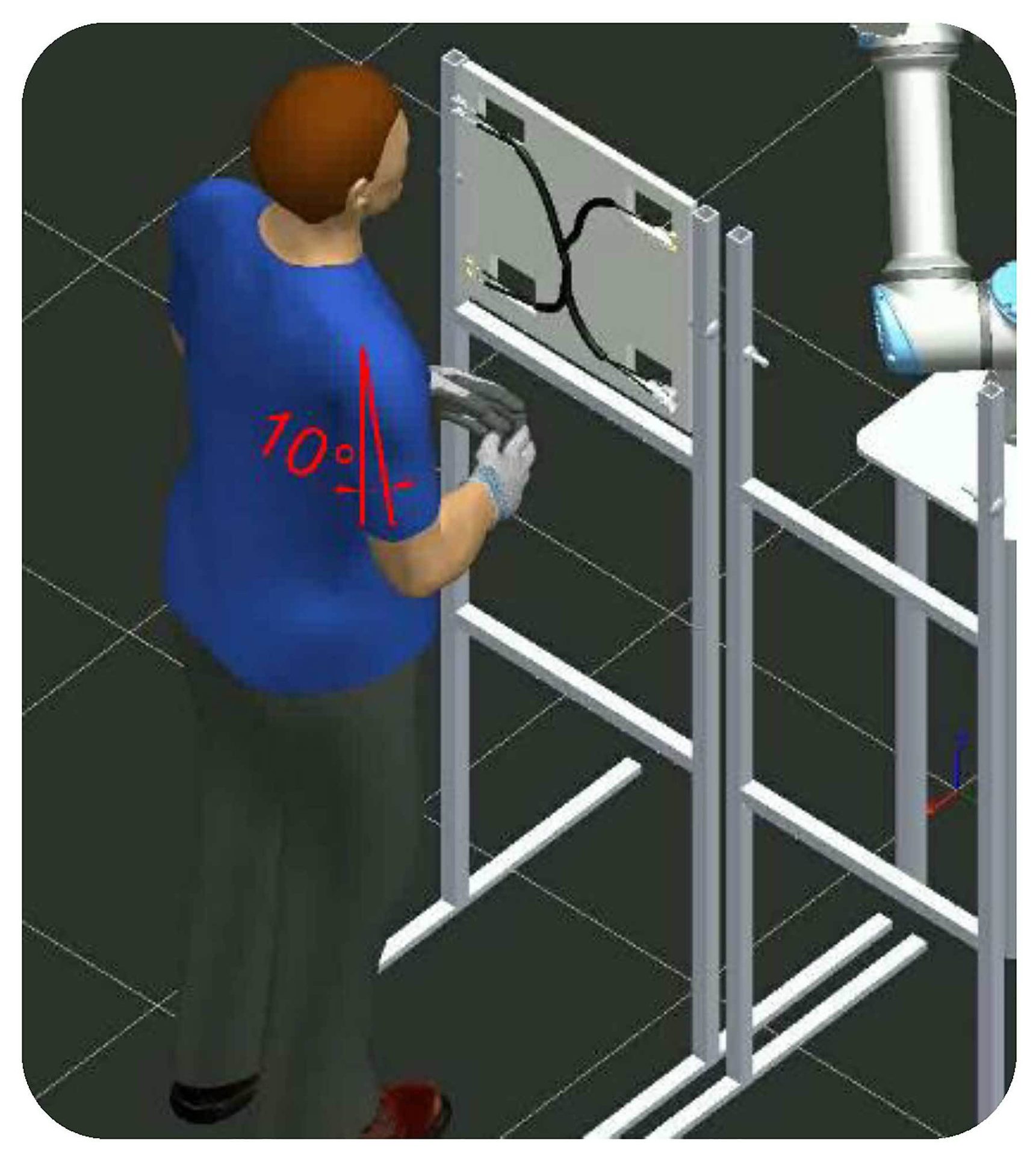
RULA and JSI scores show that the human-robot collaborative process is more ergonomic than a purely manual one. Photo courtesy Tecnológico de Monterrey
ASSEMBLY ONLINE
For more information on automation for harness assembly, visit www.assemblymag.com to read these articles: