ASSEMBLY LINES
New Method Improves Human-Robot Interaction
CAMBRIDGE, MA—Engineers at the Massachusetts Institute of Technology (MIT) have developed a safety check technique that can prove with 100 percent accuracy that a robot’s trajectory will remain collision-free. Their method, which is so precise it can discriminate between trajectories that differ by only millimeters, provides proof in only a few seconds.
The engineers used a special algorithmic technique called sum-of-squares programming and adapted it to effectively solve the safety check problem. Using sum-of-squares programming enables their method to generalize to a wide range of complex motions.
“With this work, we have shown that you can solve some challenging problems with conceptually simple tools,” says Alexandre Amice, an electrical engineering and computer science graduate student at MIT. “Sum-of-squares programming is a powerful algorithmic idea, and while it doesn’t solve every problem, if you are careful in how you apply it, you can solve some pretty nontrivial problems.”
A new rapid safety check technique ensures that robots will avoid collisions while completing a task. Photo courtesy Massachusetts Institute of Technology
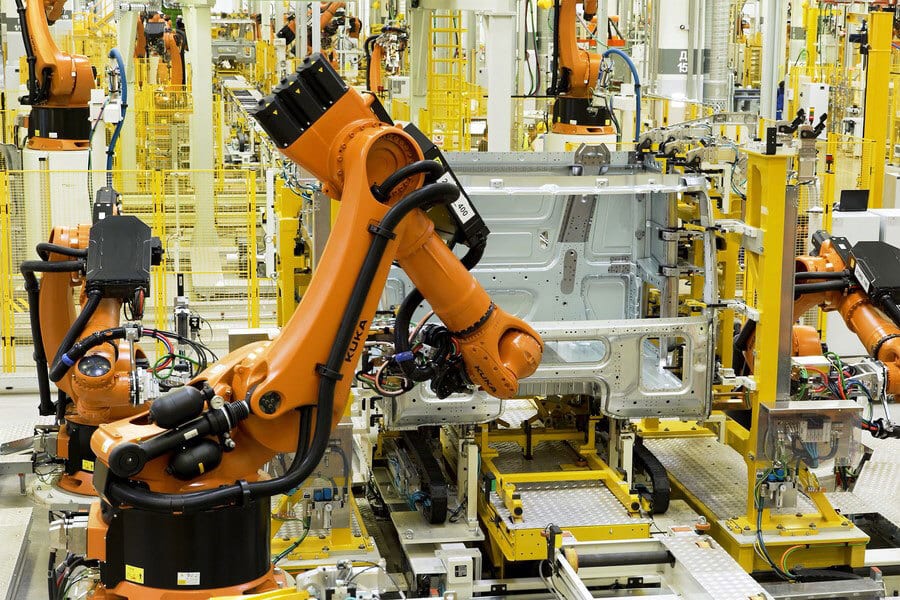
According to Amice, many existing methods that check whether a robot’s planned motion is collision-free do so by simulating the trajectory and checking every few seconds to see whether the robot hits anything. But, these static safety checks can’t tell if the robot will collide with something in the intermediate seconds.
Sometimes, these algorithms generate false positives, claiming a trajectory is safe when the robot would actually collide with something. Other methods that can avoid false positives are typically too slow for robots to use in the real world.
“Conceptually, one way to prove that a robot is not headed for a collision would be to hold up a piece of paper that separates the robot from any obstacles in the environment,” explains Amice. “Mathematically, this piece of paper is called a hyperplane.”
Many safety check algorithms work by generating this hyperplane at a single point in time. However, each time the robot moves, a new hyperplane needs to be recomputed to perform the safety check.
Instead, the new MIT technique generates a hyperplane function that moves with the robot, so it can prove that an entire trajectory is collision-free rather than working one hyperplane at a time.
“The key was figuring out how to apply sum-of-squares to our particular problem,” says Amice. “The biggest challenge was coming up with the initial formulation. If I don’t want my robot to run into anything, what does that mean mathematically, and can the computer give me an answer?”
While the approach is fast enough to be used as a final safety check in some real-world situations, it is still too slow to be implemented directly in a robot motion planning loop, where decisions need to be made in microseconds.
Amice and his colleagues plan to accelerate their process by ignoring situations that don’t require safety checks, like when a robot is far away from any objects it might collide with. They also want to experiment with specialized optimization solvers that could run faster.
Yamaha Smart Factory Features AGV Bypass System
IWATA, Japan—Yamaha Motor Co.’s flagship factory here is using state-of-the-art automated guided vehicles (AGVs) that address the challenges of assembling motorcycles in a high-mix, low-volume environment.
The AGVs can be linked together to form an assembly line or they can disconnect from the line and move to the next assembly process on their own. Called the AGV Bypass Method, the innovative production method replaces traditional conveyors.
The flexible assembly plant builds 35 motorcycle and scooter models with 1,525 variations that are shipped to 94 countries around the world. To enable more efficient production, the factory was recently renovated to increase the number of models that can be produced on one assembly line from 15 models in one category to 17 models across three categories.
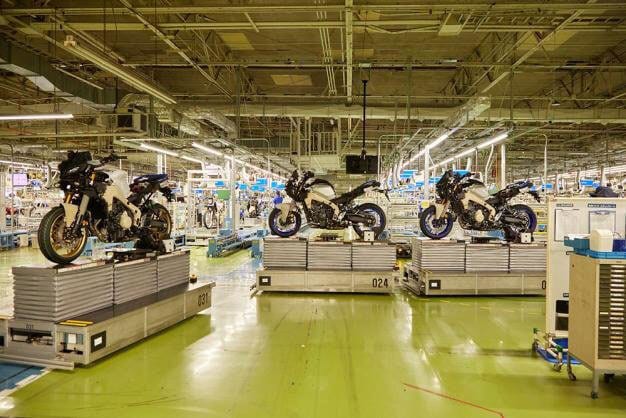
Automated guided vehicles can disconnect from the assembly line and move along a bypass route to the next production process. Photo courtesy Yamaha Motor Co.
Every day, approximately 9,000 different types of parts go into assembling various products at the factory, with some 600,000 parts being used every day.
“Because of fluctuating demand, the difficulty posed by efficiently producing various kinds of products in small lots has been a challenge for us for quite some time,” says a Yamaha engineer who worked on the project. “If we were always producing a set volume of the same thing every day, we could use simpler equipment and production setups.
“However, this creates an inefficient situation in which you have one line operating at full capacity day and night, while the adjacent line lies idle. For example, when we’re running several models on a line at the same time, the number of parts to fit and work time required for each process naturally differs.
“So, an AGV carrying a model that doesn’t require the next process on a line will branch off from it and automatically head over to where its next required process is and merge in. We decided to call this the ‘bypass method,’ because it works just like a bypass, allowing you to avoid a frequently packed road in order to get to your destination faster.”
The AGVs move through the factory not only carrying bikes being assembled, but also information about each product, process and operator. The unit sends assembly instructions to the tools and equipment at each destination, and optimizes the height of the lift to suit the height of the operator and the work process. In addition, the machines have the adaptability and versatility to respond to sudden production requests for just one unit.
IFR Names Top 5 Robot Trends
FRANKFURT—According to the International Federation of Robotics (IFR), the following five trends will drive increased demand for robots in 2024:
• Artificial intelligence and machine learning. The emergence of generative AI is opening up new applications for robots. Suppliers are developing generative AI-driven interfaces that enable users to program robots more intuitively by using natural language instead of code. Predictive AI is being used to analyze robot performance data to identify the future state of equipment. Machine learning algorithms can also analyze data from multiple robots performing the same process for optimization.
Illustration courtesy International Federation of Robotics
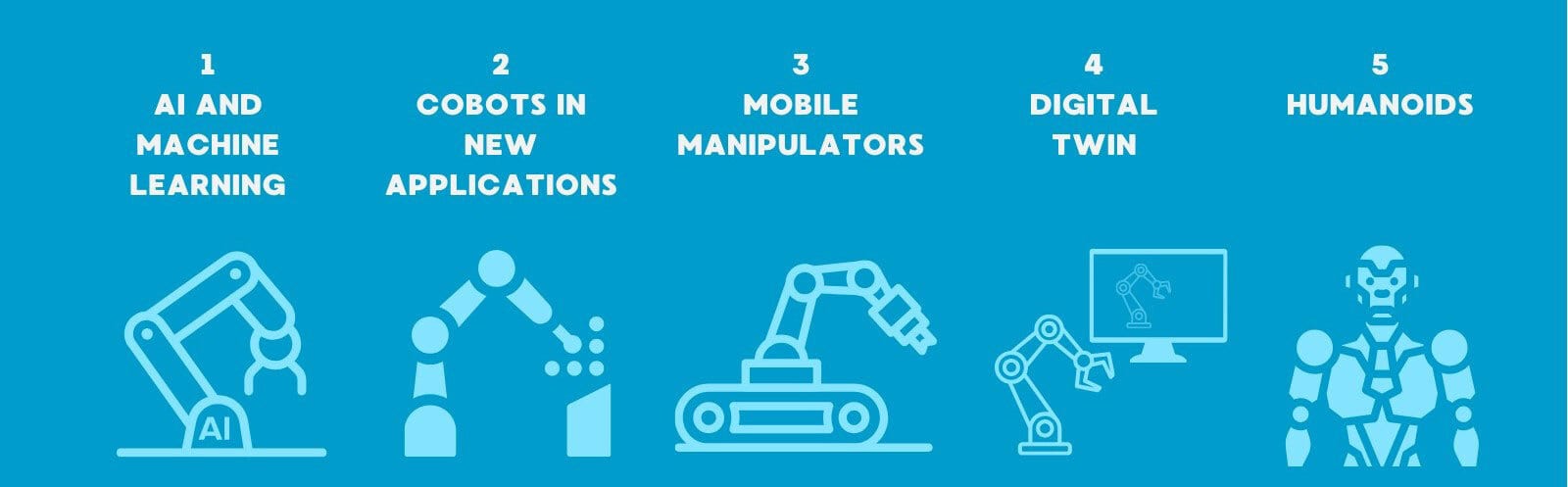
• Collaborative robots. Human-robot collaboration continues to be a major trend in robotics. Rapid advances in sensors, vision technologies and smart grippers allow robots to respond in real-time to changes in their environment and thus work safely alongside human workers. The range of collaborative applications offered by robot manufacturers continues to expand. Cobots will complement, not replace, investments in traditional industrial robots that operate at much faster speeds and will therefore remain important for improving productivity in response to tight product margins.
• Mobile manipulators. Mobile manipulators (MoMas) that combine collaborative robot arms and autonomous mobile robots are automating material handling tasks in industries such as aerospace, automotive and logistics. They combine the mobility of robotic platforms with the dexterity of manipulator arms. This enables them to navigate complex environments and manipulate objects. Equipped with sensors and cameras, these robots perform inspections and carry out maintenance tasks on machinery and equipment. One of the significant advantages of mobile manipulators is their ability to collaborate and support human workers.
• Digital twins. Digital twin technology is increasingly used as a tool to optimize the performance of a physical system by creating a virtual replica. Since robots are more and more digitally integrated in factories, digital twins can use their real-world operational data to run simulations and predict likely outcomes. Because the twin exists purely as a computer model, it can be stress-tested and modified with no safety implications while saving costs. All experimentation can be checked before the physical world itself is touched. Digital twins bridge the gap between digital and physical worlds.
• Humanoid robots. The robotics industry is witnessing significant advancements in humanoids designed to perform a wide range of tasks in various environments. The human-like design with two arms and two legs allows these machines to be used flexibly in work environments that were actually created for humans. Therefore, they can be easily integrated into existing manufacturing or warehouse processes and infrastructure. However, humanoid costs are a key factor and success will depend on their return on investment competing with well-established robotic technology such as mobile manipulators.
“The five mutually reinforcing automation trends in 2024 show that robotics is a multidisciplinary field where technologies are converging to create intelligent solutions for a wide range of tasks,” says Marina Bill, president of IFR. “These advances continue to shape the merging industrial and service robotics sectors and the future of work.”
AI Drives New Frontiers in Robotics
AUBURN HLLS, MI—Artificial intelligence technology will enable robots to expand into new segments and applications not previously served by automation.
“[This year] will see a growing focus on the critical role of AI,” says Marc Segura, president of ABB Robotics. “From mobile robots and cobots, to enabling new robotic applications in new sectors and creating new opportunities for people to learn and develop, these frontiers for AI are redefining the future of industrial robotics.”
Segura believes there are three key trends to watch:
• AI will drive new levels of autonomy in robotic applications. Accelerating progress in AI is redefining what is possible with industrial robotics. AI is enhancing everything from robots’ ability to grip, pick and place, as well as their ability to map and navigate through dynamic environments. From mobile robots to cobots and beyond, AI is giving robots unprecedented levels of speed, accuracy and payload carrying ability, enabling them to take on more tasks.
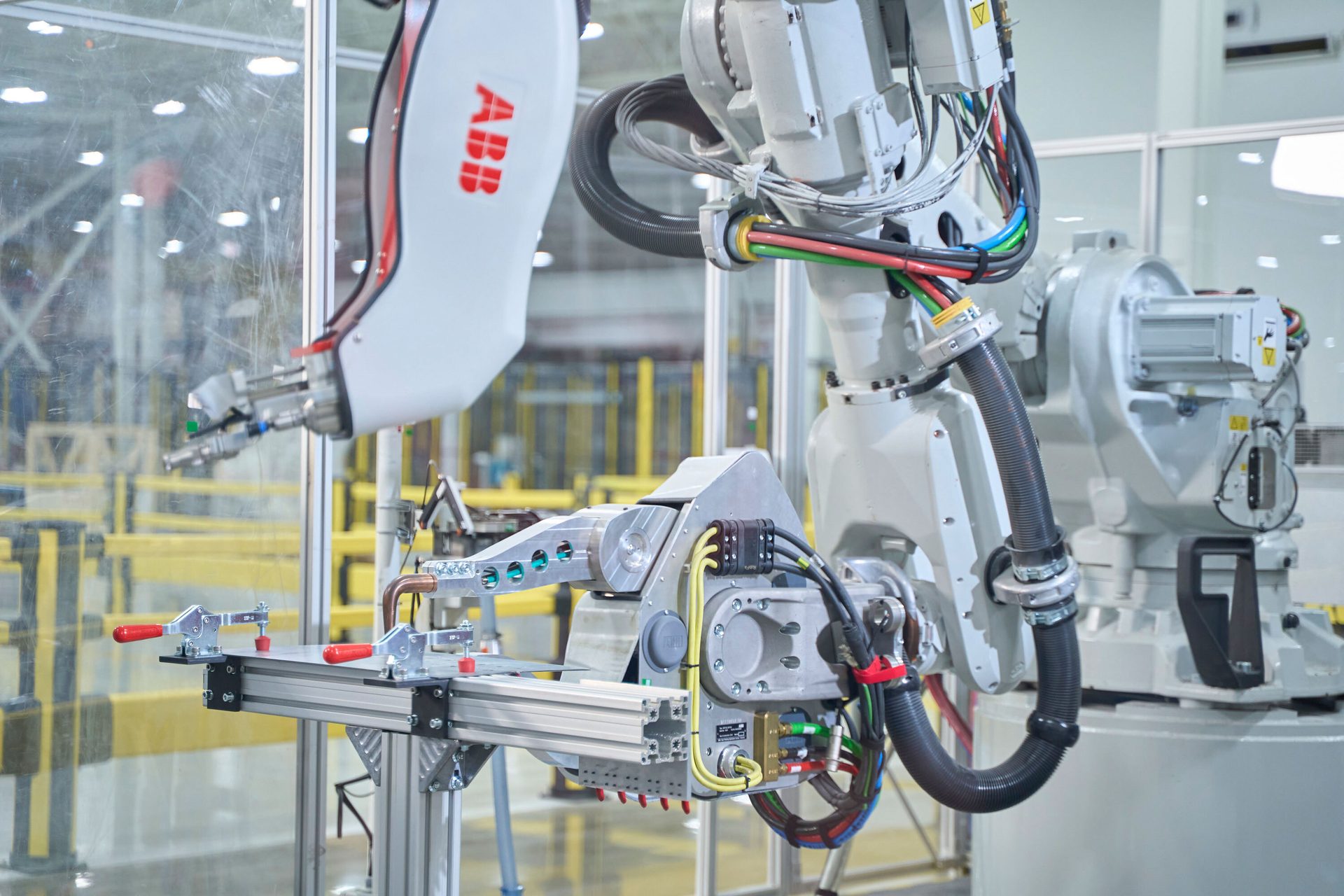
Artificial intelligence technology will enable robots to expand into new segments and applications not previously served by automation. Photo courtesy ABB Robotics
“AI-enabled mobile robots can transform sectors like discrete manufacturing, logistics and laboratories,” explains Segura. “Robots equipped with [our] new Visual Simultaneous Localization and Mapping (Visual SLAM) technology, for example, have advanced mapping and navigation skills, granting new levels of autonomy, while greatly reducing the infrastructure needed by previous generations of guided robots.
“This paves the way for a shift from linear production lines to dynamic networks, creating significant efficiencies and taking on more dull, dirty and dangerous tasks, to enable workers to take up more rewarding jobs,” Segura points out.
• AI will see robots enter new sectors. The potential offered by AI-enabled robotics is influencing sectors far beyond manufacturing. These technologies are expected to bring substantial efficiency improvements to more dynamic environments, such as healthcare and life sciences, as well as retail. Another example is the construction industry, where AI-powered robotics can make a material contribution to boosting productivity, enhancing safety and sustainable construction practices while spurring growth.
“The construction industry is a great example of a sector where AI-powered robots will prove transformative, delivering real value by addressing many of the issues facing the industry today, including worker shortages, safety issues and stagnant productivity,” says Segura. “Abilities such as enhanced recognition and decision-making offered by AI, coupled with advances in collaborative robots, enable safe deployment alongside workers.
“These advances also enable robots to perform key tasks such as bricklaying, modular assembly and 3D printing with greater precision and speed, all while contributing to more sustainable construction by lowering emissions, such as concrete mixing on site, to reducing the need to transport materials across far distances with on-site assembly,” notes Segura.
• AI will offer new opportunities for education and working with robots. The advances being made in AI and robotics are significant for training and education, closing the automation skills gap and making robots more accessible to more people and businesses.
With AI making programming easier, through lead-through and even natural language, education can shift more toward how robots can assist humans more effectively, rather than just teaching programming skills. This transition will make robots more approachable and bring them to a wider audience, leading to new job prospects while helping alleviate labor and skill shortages.
“A shortage of people with the skills needed to program and support robots has long been a hurdle to the uptake of robotic automation, especially in small-to-medium-sized manufacturing companies,” says Segura. “We will see this increasingly being overcome as advances in generative AI lower the barriers to automation and expand the focus of education beyond programming.
“Developments in natural language programming powered by AI, in which workers can verbally instruct a robot in its task, will create a new dynamic in human-robot interactions,” claims Segura.