AL System™ Heightens Crane Capabilities
With new Ultra Low Headroom End Trucks and AL System™ Workstation Cranes, Engineered Material Handling (EMH) solved the problem of low ceilings and high machinery in tight spaces. With most workstation cranes, bridges hang below the runway. Consequently, the distance between the support steel and hoist trolley takes up about 30 inches. With new EMH Low Profile End Trucks, you can now raise the bridge within 3 inches of the overhead obstruction, which positions the pin on the trolley about a foot to 13 inches from the height obstruction. Low dropped ceilings no longer present a problem because the bottom of the bridge easily clears the top of most test machinery.
Handling Concepts, located in Akron, Ohio, was one of the first EMH distributors to sell this AL System modification. Using lightweight aluminum track profiles, AL System Cranes already accommodate many applications with capacities up to 2,200 pounds. With anodized aluminum extrusions and enclosed rails to maximize strength, AL-System Cranes with Ultra Low Headroom End Trucks are durable and aesthetic, blending in well with modern test rooms. With a stainless-steel component option, they are ideal for clean rooms. Designers can also specify single or double girder configurations and motorized versions.
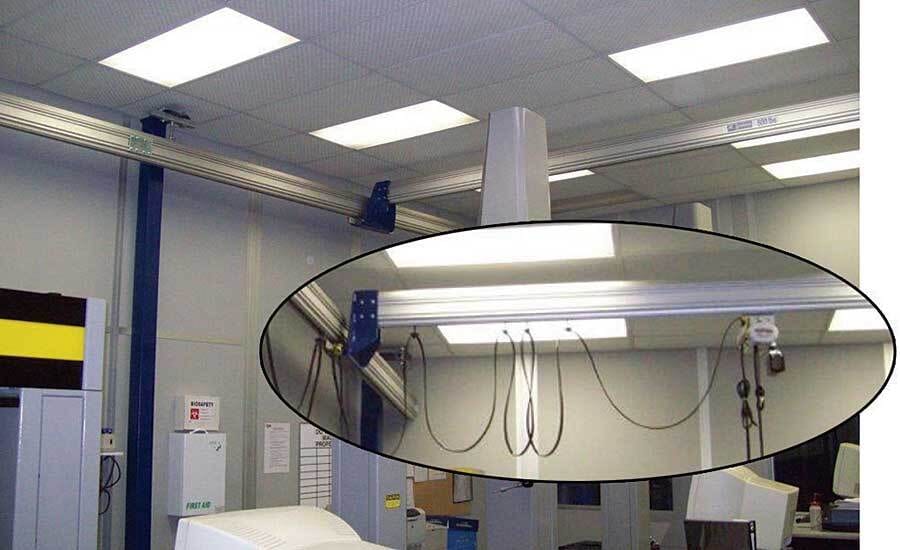
Delivering Performance in Every Machine
The Arthur G Russell Company (AGR) develops state-of-the-art automated assembly equipment for the medical device, consumer, pharmaceutical, electronics, automotive, as well as other industries.
With the addition of their AGR machine, global medical device company, Cooper Surgical, went to just one shift, increased production six-fold, and realized a cost savings of over $400,000 a year.
“This machine replaced an older machine we inherited in an acquisition. That machine was producing 60 brushes per minute compared to the AG Russell machine producing 360 brushes per minute, running flawlessly since 2011.”
—Kevin Hicks, Value System Manager, Cooper Surgical
AGR provides remote support, preventative maintenance, and critical spare parts assessments to keep your lines running smoothly. Our onsite training, Proof of Principle projects, and i4.0 support ensure adaptability and efficiency. From small to large-scale productions, AGR crafts flexible automation systems that evolve with your evolving needs.
Visit AGR at The Assembly Show South in Booth# 1342. Not able to attend? See how we deliver the performance you need in every machine at www.arthurgrussell.com.
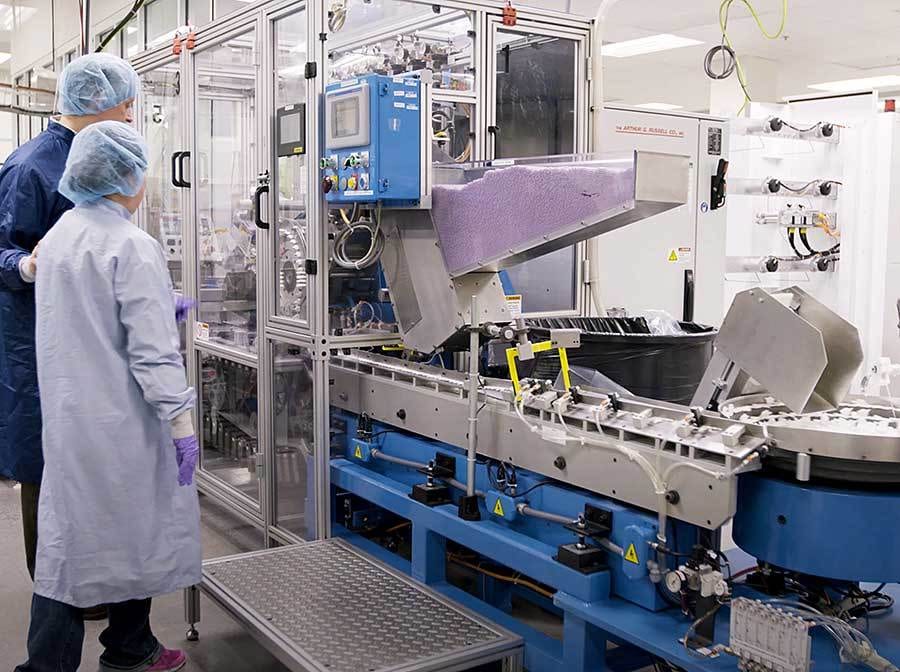
Wire Harness Benches Increase Production.
Tolerances have to be consistently tight when you’re assembling wire harnesses for a jet fighter – 1/8 of an inch over 32 feet to be exact. Workbenches that can’t accommodate such tolerances would be, well, intolerable.
That’s the problem that a jet manufacturer faced when they determined that they needed to upgrade their facility. They were using pieces of plywood on A-frames for the assembly. This not only affected tolerance levels but also led to stress, strain and fatigue.
The jet fighter manufacturer found a company that could deliver what they were looking for in Proline. A leader in ergonomic workbenches. A company renowned not just for its rugged, technologically advanced workbenches, but also for its ability to “think on the fly” and produce, application-specific solutions, Proline met all of the jet manufacturer’s specs.
Thanks to the range of easy vertical movement provided by the Pro-Line benches, along with tilt, all sections of the wire harness are always within easy reach. Since this initial installation, this jet plane manufacturer is currently in the process of expanding its operation with additional Pro-Line workbenches. Clearly they are more than satisfied that they have harnessed such precise, ergonomically sound and productivity-enhancing workbench solutions.
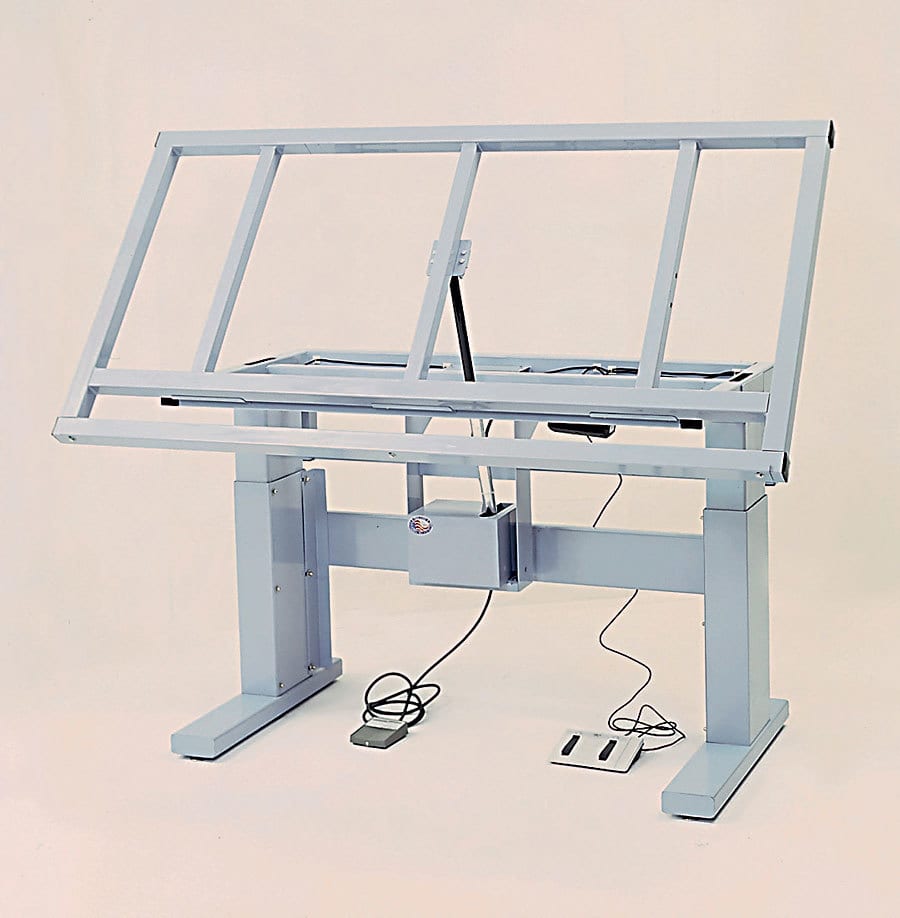
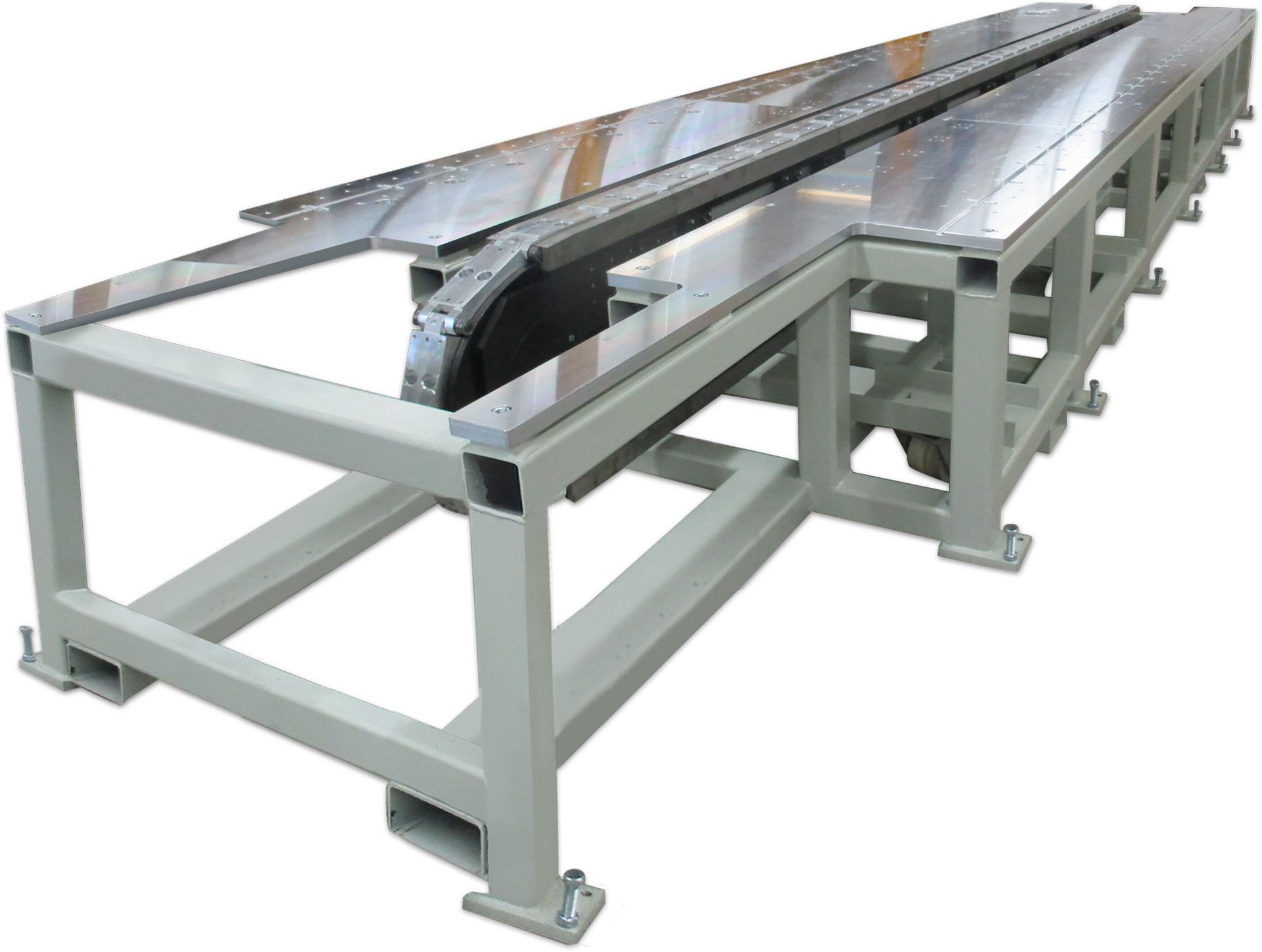
New Custom Designed Precision Link Conveyor
Motion Index Drives designed and manufactured this NEW custom Precision Link Conveyor for our customer in Automotive manufacturing to accommodate their application requirements. The customer needed to have the precision conveyor index at 9 inch increments because the tooling was at a 9 inch center distance. When none of our standard conveyors could meet their needs, Motion Index Drives designed a 9 inch precision conveyor that would fit their application.
Other requirements included the precision link conveyor to be housed in a tubular structure base that could be moved on heavy duty castor wheels for easy transport around their shop. This also allowed for aluminum jig plates to be mounted along the sides of the conveyor to mount the customer tooling. The plates were machined with tapped, dowel holes and keyways per customer design to match tooling requirements.
Promess Inc.
810-229-9334
promess@promessinc.com
Save Money with a Promess EMAP
Challenge:
Promess encountered a challenge when a leading pump manufacturer approached them with a pressing issue. The manufacturer utilized a hydraulic press for bearing insertion into a housing. However, the press consistently reached full pressure during each cycle, posing a significant problem. The lack of a detection mechanism meant they couldn't pinpoint when this occurred or determine the optimal force for individual parts. Moreover, these failures drastically reduced pump lifespan by approximately ninety-five percent. Consequently, pumps passed internal tests but failed prematurely in the field, resulting in a troubling return rate of 10%-20%.
Strategy:
To address this challenge, Promess deployed the Electro-Mechanical Assembly Press (EMAP) equipped with a Promess motion controller. This system allowed for precise control over the bearing insertion process. It enabled the insertion to commence and reach a designated point before applying pressure relative to that position. Throughout this operation, comprehensive process data, including a force versus distance curve, was meticulously recorded. All data was then archived in a database, along with crucial cycle information such as timestamps, serial numbers, and tolerances. This ensured thorough traceability, maintaining a complete record for every part.
Results:
Following the implementation of the Promess EMAP solution, the pump failure issue was completely eradicated. This achievement translated to substantial savings for the company, with an estimated $1,000,000 reduction in warranty costs within the initial year alone.
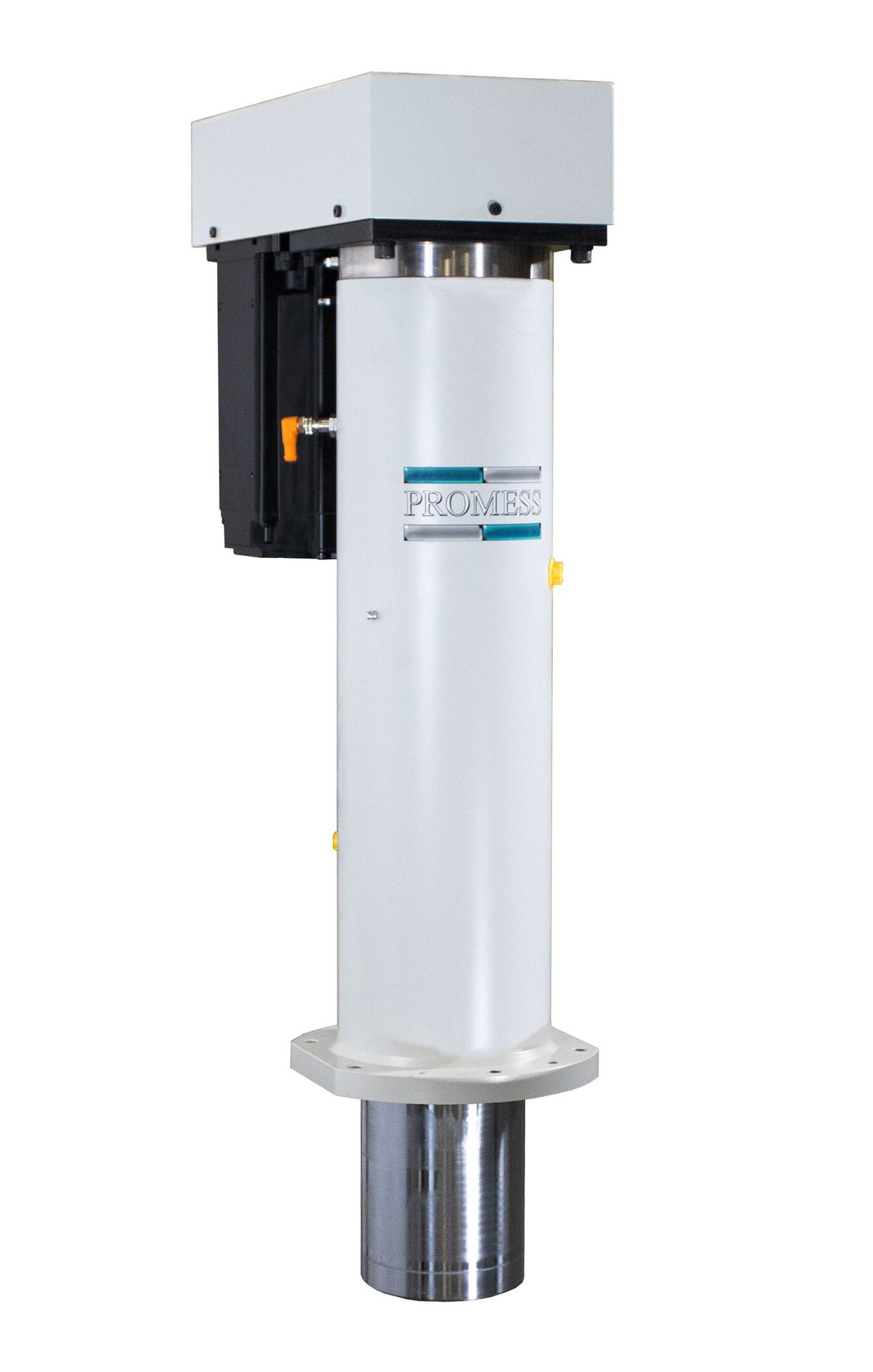
Precision and Controllability - BalTec ELECTRIC
Precise Riveting and Controllability is exactly what the BalTec ELECTRIC (servo-driven riveting machine) was designed to do. Customer provided a challenging application involving a small diameter aluminum rivet that needed to be formed to retain a plate with a hermetically sealed joint, but still allow the plate to rotate. Existing processes were not repeatable and could not maintain all the critical finish criteria of an acceptable assembly. The customer’s new product design was doomed to be scrapped until they reached out to BalTec. Through collaborative testing and BalTec’s 60+ years of forming experience, a solution was found using the BalTec ELECTRIC. BalTec ELECTRIC provided the control and precision needed for repeatable results as well as a user-friendly interface to easily adjust input factors for completing Design Of Experiments (DOE).
The expertise of BalTec Group with its headquarters in Pfäffikon, Switzerland, is in the manufacturing of joining technology machinery, with a special focus on radial riveting technology, but also orbital riveting, and roller forming. Today we are the global leader in riveting technology, encompassing seven companies with sales partners on every continent. Joining is our business - worldwide. Please reach out to us for help with your application!
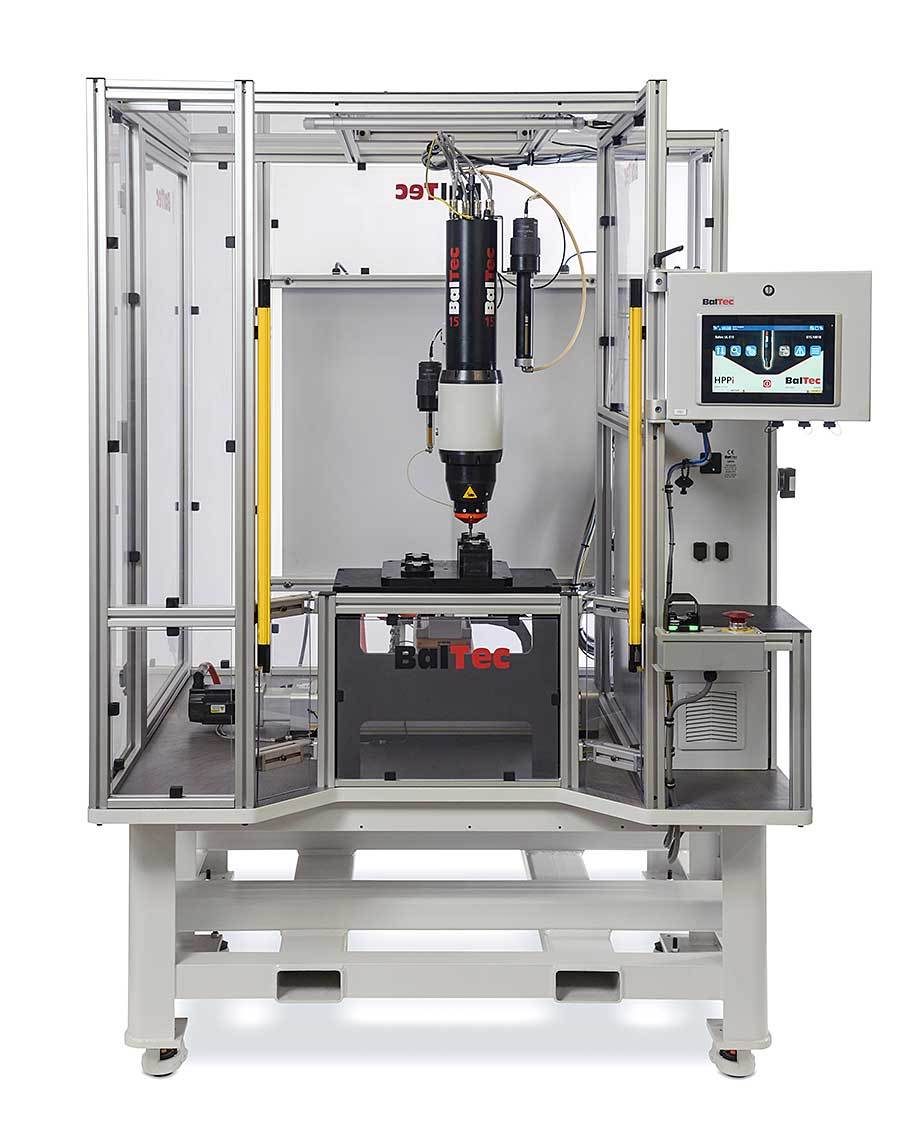
Your customers want their product fast
To meet the heavy demands of one of their most significant customers, the General Motors EV Plant in Detroit, Android Industries turned to Rhino Tool House to get the right tool solutions quickly—in other words, fast.
In record time, Rhino tapped into their partner network to find a unique fix for Android, helping them solve their immediate need while improving their operations for the future.
The Rhino solution included three state-of-the-art mobile assembly carts equipped with advanced worker guidance software, high-precision DC assembly tools, and intelligent torque wrenches. After integrating the carts into Android's MES system, they produced the parts quickly and shipped them to GM with full certification.
Android was able to deliver for GM on time while establishing a new efficiency and quality standard for their future manufacturing.
Don’t let frustrating delays and limited solutions hold you back. Call Rhino Tool House today and get more from your manufacturing
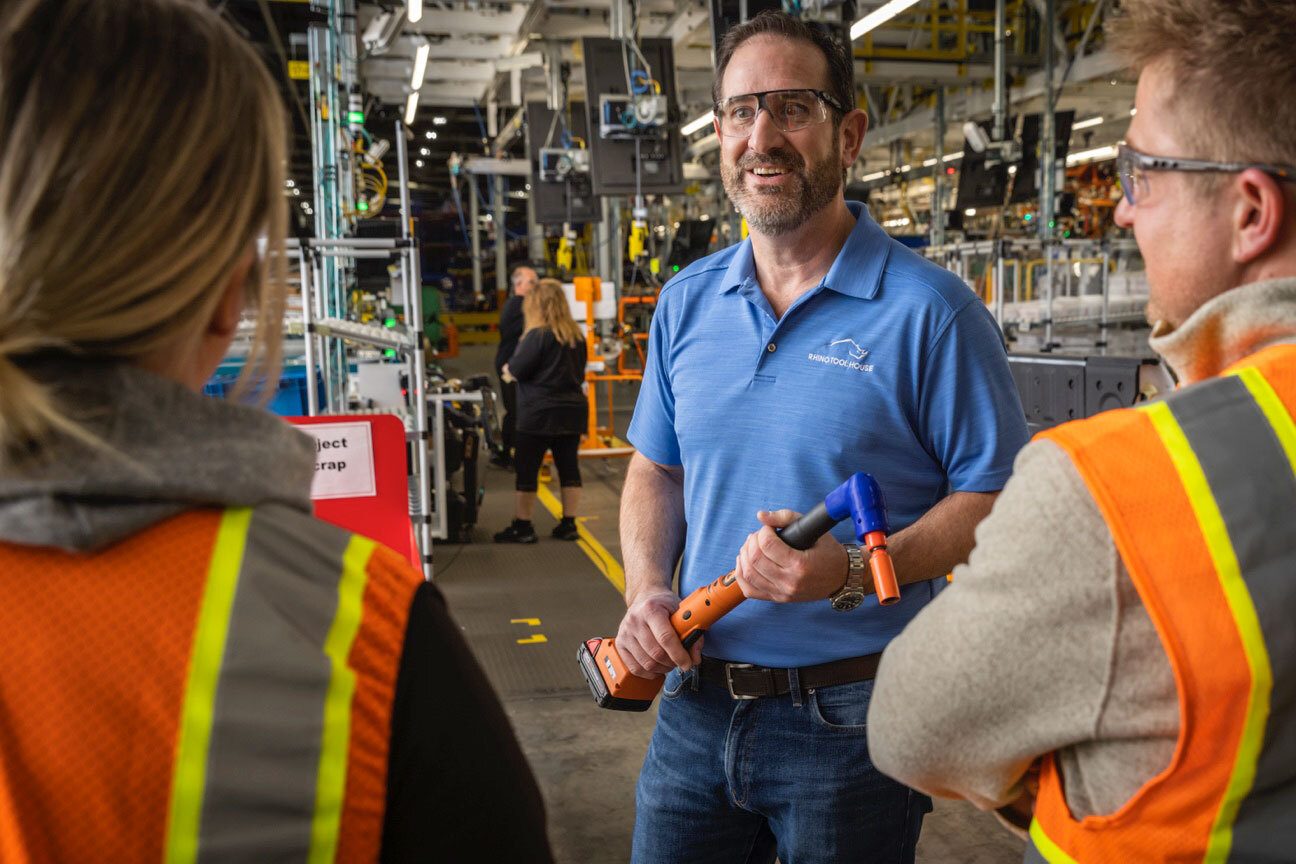
Integrated Collaboration Increases Lab Productivity
In cooperation with ABB and Mettler Toledo International, Zimmer Group helps to complete automated workflows in laboratories with components from its intelligent handling systems technology.
ABB and Mettler Toledo International recently partnered on a major project to advance automation within a variety of standard laboratory processes in several industries. ABB’s collaborative robots will integrate with LabX, Mettler Toledo’s laboratory instrument management software, to increase lab productivity, reduce system complexity and fulfill data quality and safety and regulatory requirements. The process will relieve scientists and lab technicians of mundane, repetitive tasks resulting in the elimination of common errors while optimizing productivity and providing more time for lab professionals to pursue higher-value activities.
For ABB’s collaborative robots, Zimmer Group provided their MATCH end-of-arm platform along with two grippers - the GEH6000IL and the HRC-03. Both grippers can be programmed with IO-link technology. The GEH6000IL gripper can grip at different widths with varying force. The HRC-03 2-jaw parallel collaborative gripper offers direct assembly to the robot flange guaranteeing easy installation with a self-locking mechanism.
This partnership will implement valuable automation processes while unlocking resources in the pharmaceuticals, chemicals, food and beverage, semiconductors and battery industries.
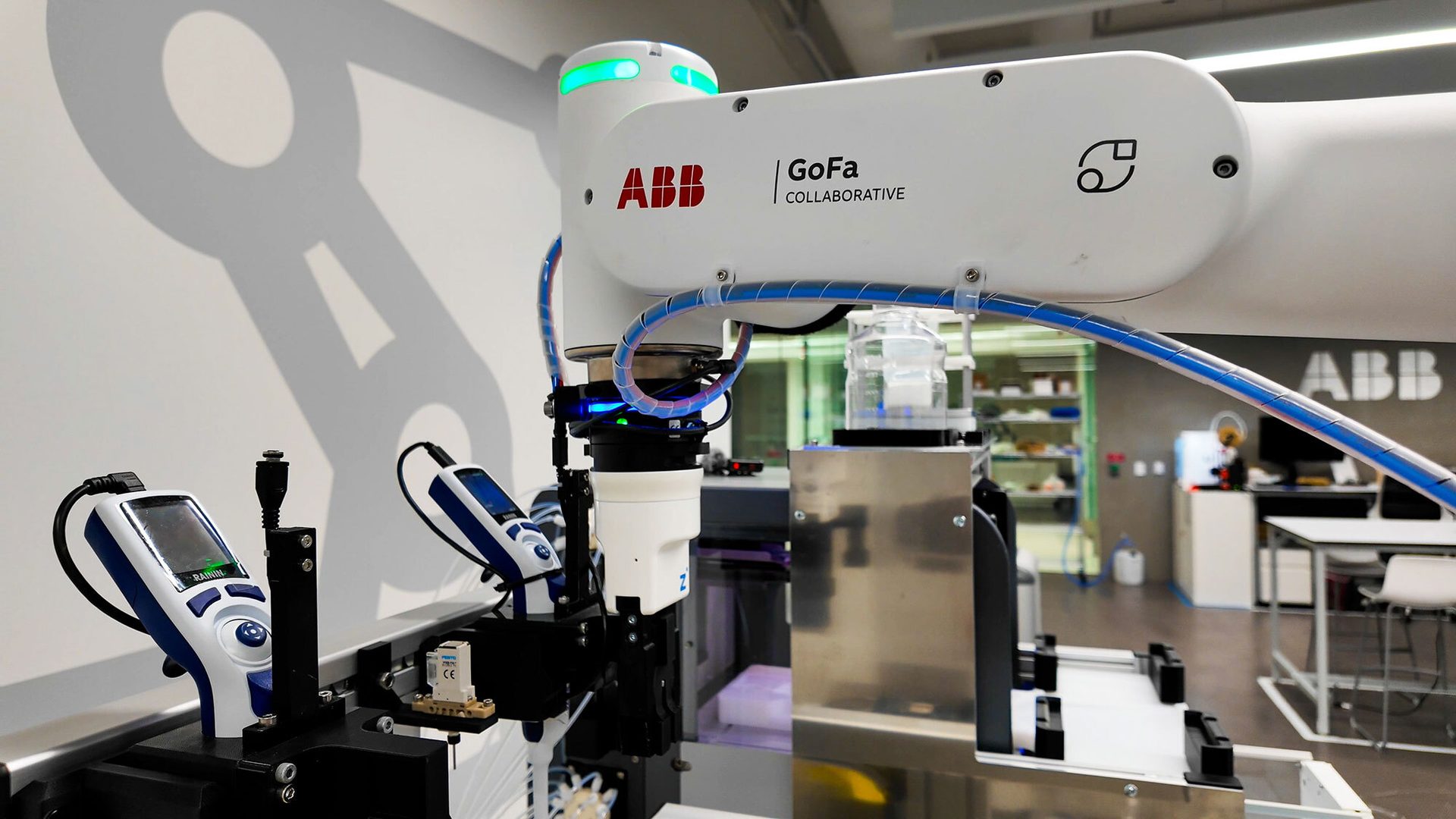
WEISS North America, Inc.
888-WEISSNA (888-934-7762)
info.us@weiss-world.com
Multipurpose Flexibility from WEISS
A consumer goods manufacturer recently decided to standardize on multipurpose assembly chassis with a flexible tool plate. Twenty chassis will be purchased as this customer standardizes and updates their assembly cells. Together with the customer’s in-house build team, WEISS provided custom-designed chassis with two tool plate variations.
Each chassis features a two-station TC120 indexer, a welded base, aluminum base plate, and aluminum tool plate with clear anodized finish, leveling plates with casters, aluminum side panels and lockable, hinged door, an aluminum indexer mount plate and extruded aluminum guarding with hinges and latches from Industrial Profile Systems, a wholly owned subsidiary of WEISS North America.
Initially contacted to provide the 2-station TC120 rotary indexers while the customer sourced other suppliers for the chassis, guarding, hardware, and other components of the design, WEISS proposed a single-source solution designed around proven and reliable WEISS automation components and value-added services. This provided the customer a simplified vendor sourcing/vetting process, proven platforms and components, faster time to completion, reduced lead time and overall cost savings due to economies of scale.
To learn more about WEISS, please visit www.weiss-world.com or call one of our automation pros today at 888-934-7762.
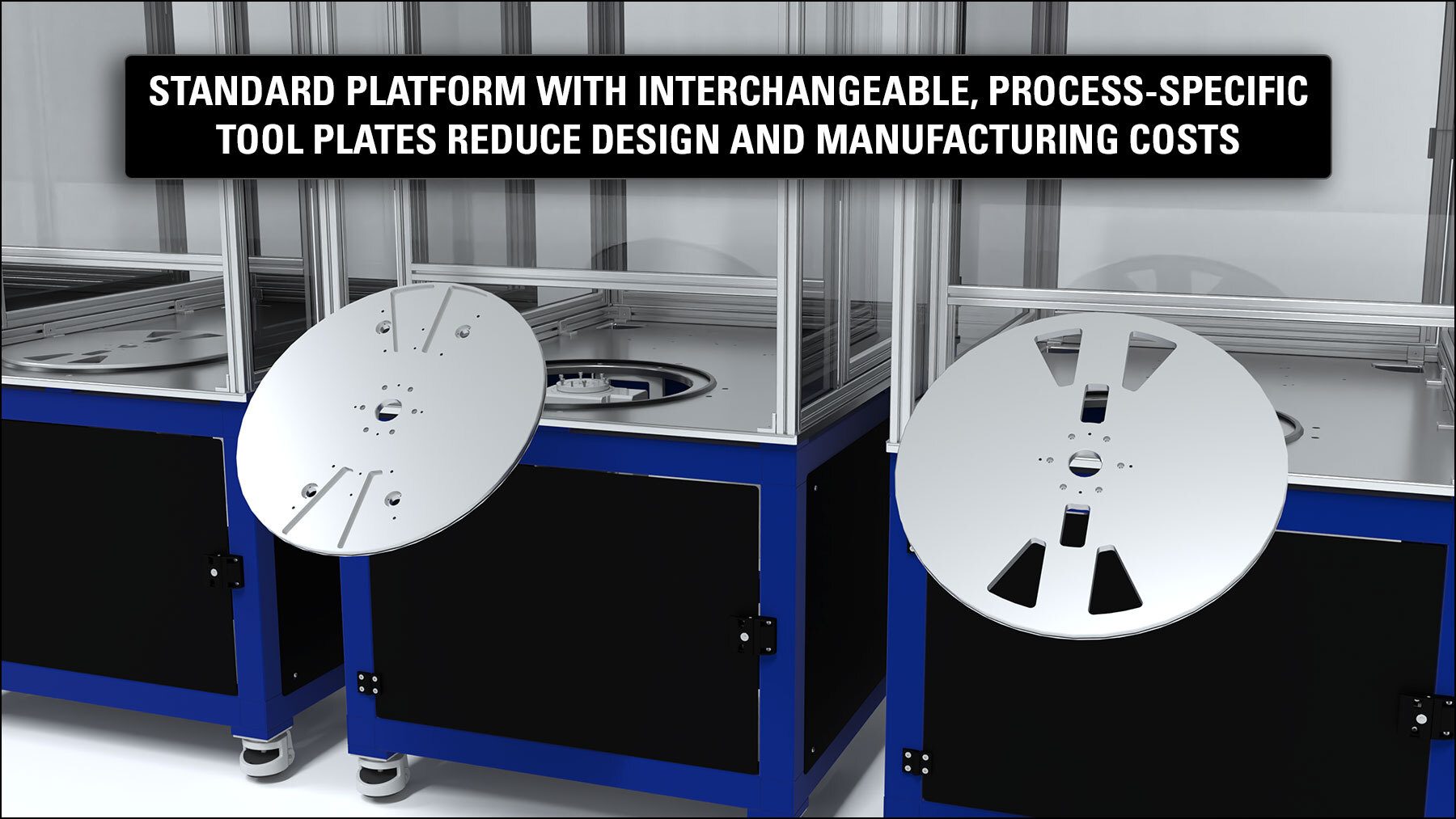
Afag Automation Americas Inc.
883 Seven Oaks Blvd, Suite 800, Smyrna, TN 37167
615 730 7515
nashville@afag.com
Are you ready to unlock your manufacturing potential?
Afag is now part of Emerson. The combination of the world class Afag feeding and handling solutions and the Emerson factory automation portfolio offers you even greater capabilities to revolutionize your automation processes. Call us today and hear about our Floor to Cloud approach to optimize your manufacturing process, improve operating equipment effectiveness, and meet your sustainability goals.
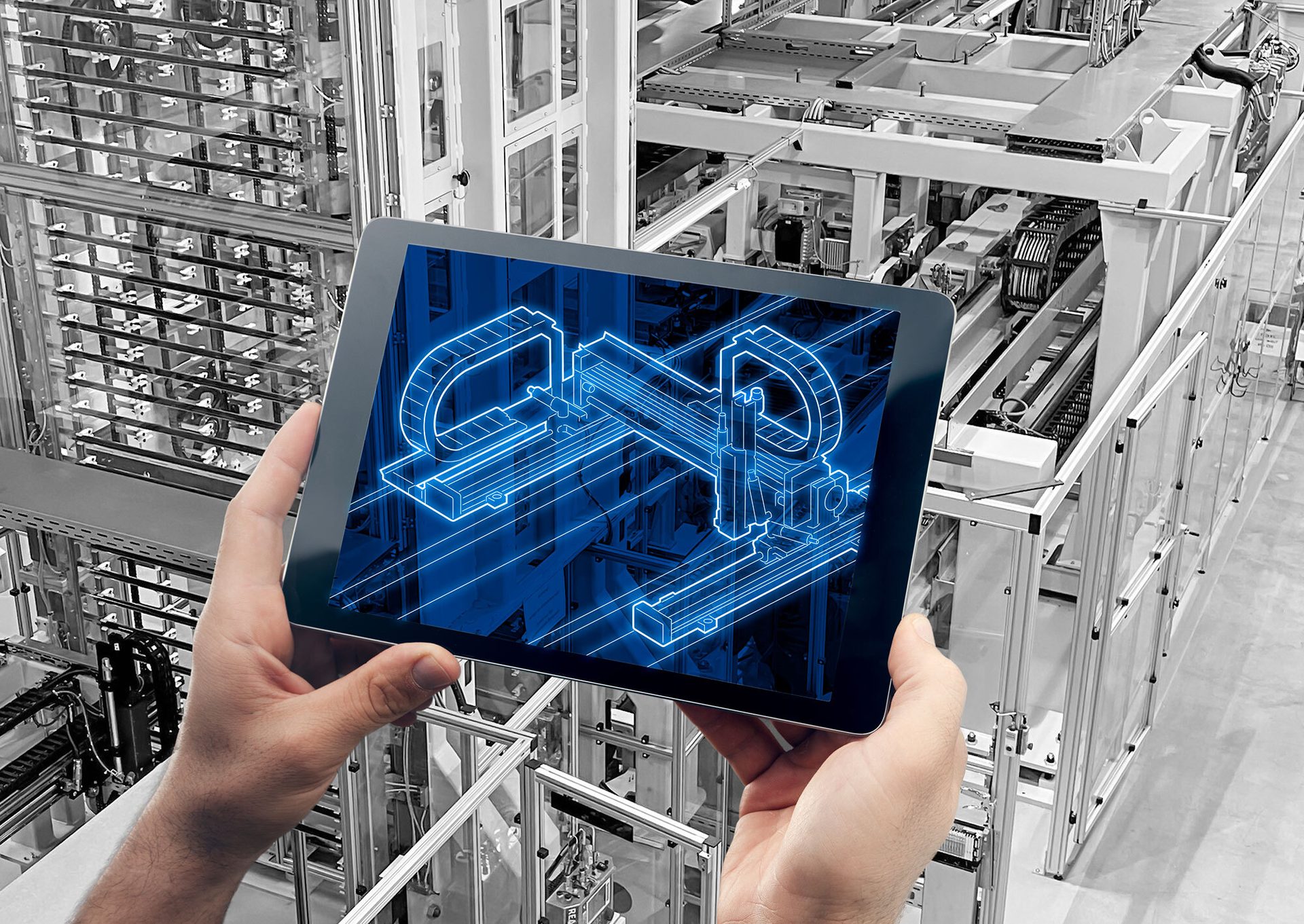
MVG Multi-zone Gripper for Palletizing
A customer came to COVAL with a challenge. They were looking to automate their packaging process that was currently being done by hand, to palletize a variety of sizes of corrugated boxes. The customer wanted to move all the boxes with the same gripper to avoid having to do a tool changeover, and also maintain individual control of each box while picking several boxes at once.
After extensive configuration testing in COVAL’s in-house test lab, COVAL was able to offer a solution that met all of the customer’s needs. A custom sized MVG gripper was designed with multiple independent gripping zones to reduce leakage around the many box sizes, with a suction cup interface designed for handling cardboard. Paired with a COVAL vacuum pump sized to provide the necessary vacuum flow rate, the MVG gripper was easily integrated on multiple packaging lines. The customer was very pleased with the end result, as it allowed them to increase their productivity and profitability, while also reducing the risk of injury to their employees.
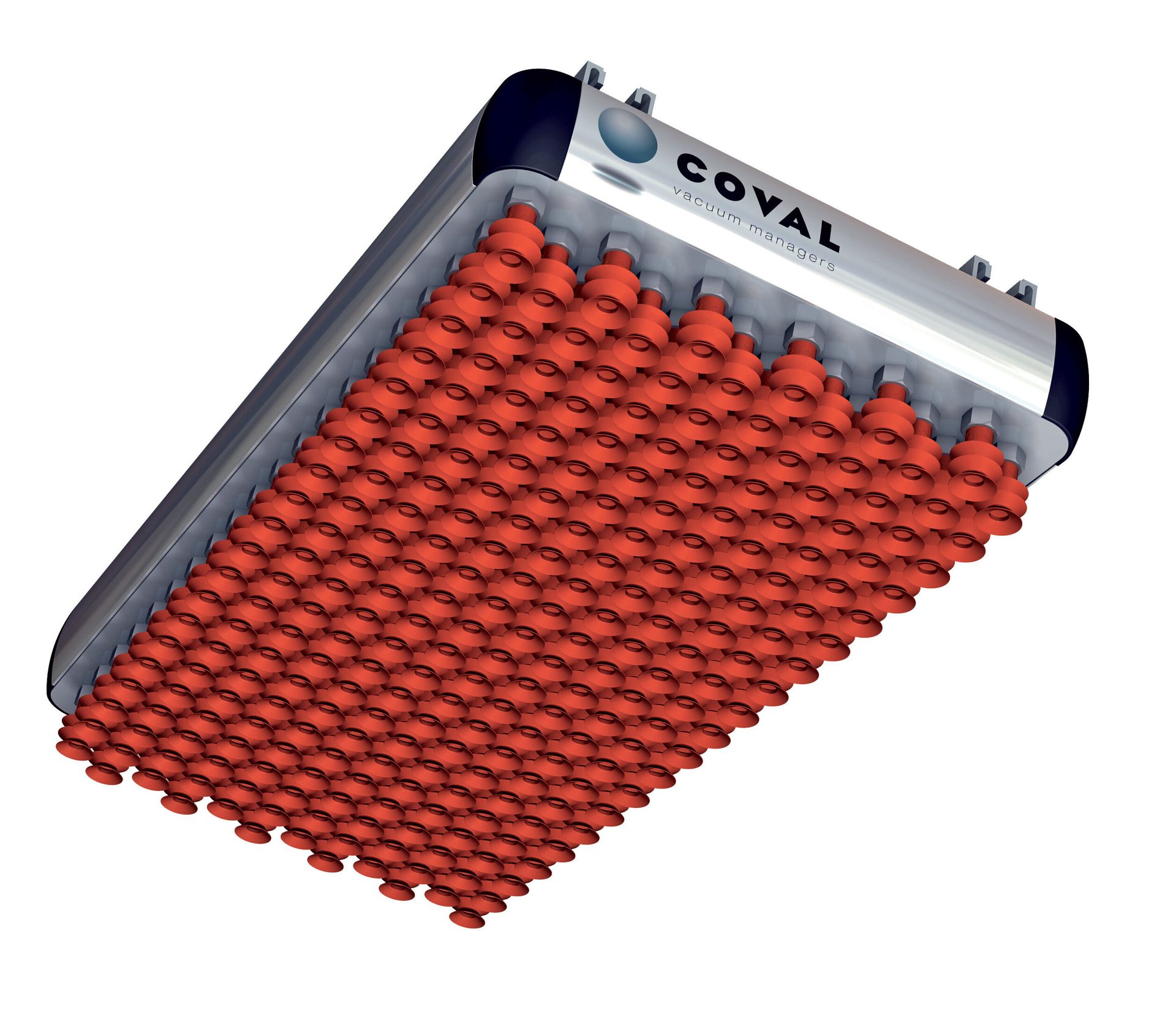
MC Fastening Solutions: Exclusive North American Distributor of DDK Fastening/Servo Press Products
SHELBY TOWNSHIP, MICH.--MC Fastening Solutions, a division of MC Machinery Systems, is now the exclusive North American distributor of Dai-lchi Dentsu, Ltd. (DDK) fastening/servo press products, including AC nutrunners, DC hand tools, electric servo presses and micro screwdrivers.
Located near Detroit in Shelby Township, Mich., MC Fastening Solutions supplies advanced and reliable servo press and nutrunner fastening systems and machines to industries including automotive, aerospace, defense, medical, appliance, energy and semiconductor.
“Our team has a combined 50-plus years of experience in assembly and fastening systems, taking projects from proposal to production, ensuring seamless integration and optimal performance,” said MC Fastening Solutions Product Manager Keith Lowery.
MC Fastening Solutions’ core products include:
• DSP3000 Series Digital Electric Servo Presses
• AFC3000 Series Fixtured AC Electric Nutrunners
• AFC3000 Series Micro Nutrunners / Screwdrivers
• HFC3000II Handheld DC Electric Nutrunners
MC Fastening Solutions will be exhibiting at the Assembly South Show May 1 and May 2 in Nashville, Tenn. in Booth 506.
MC Machinery Systems, a subsidiary of the Mitsubishi Corp., is a premier supplier and servicer of machine tool equipment, including Mitsubishi lasers, electrical discharge machines (EDMs), automation systems, milling machines and press brakes. Headquartered in Elk Grove Village, Ill., MC Machinery has a comprehensive regionalized service network and seven North American technology centers.
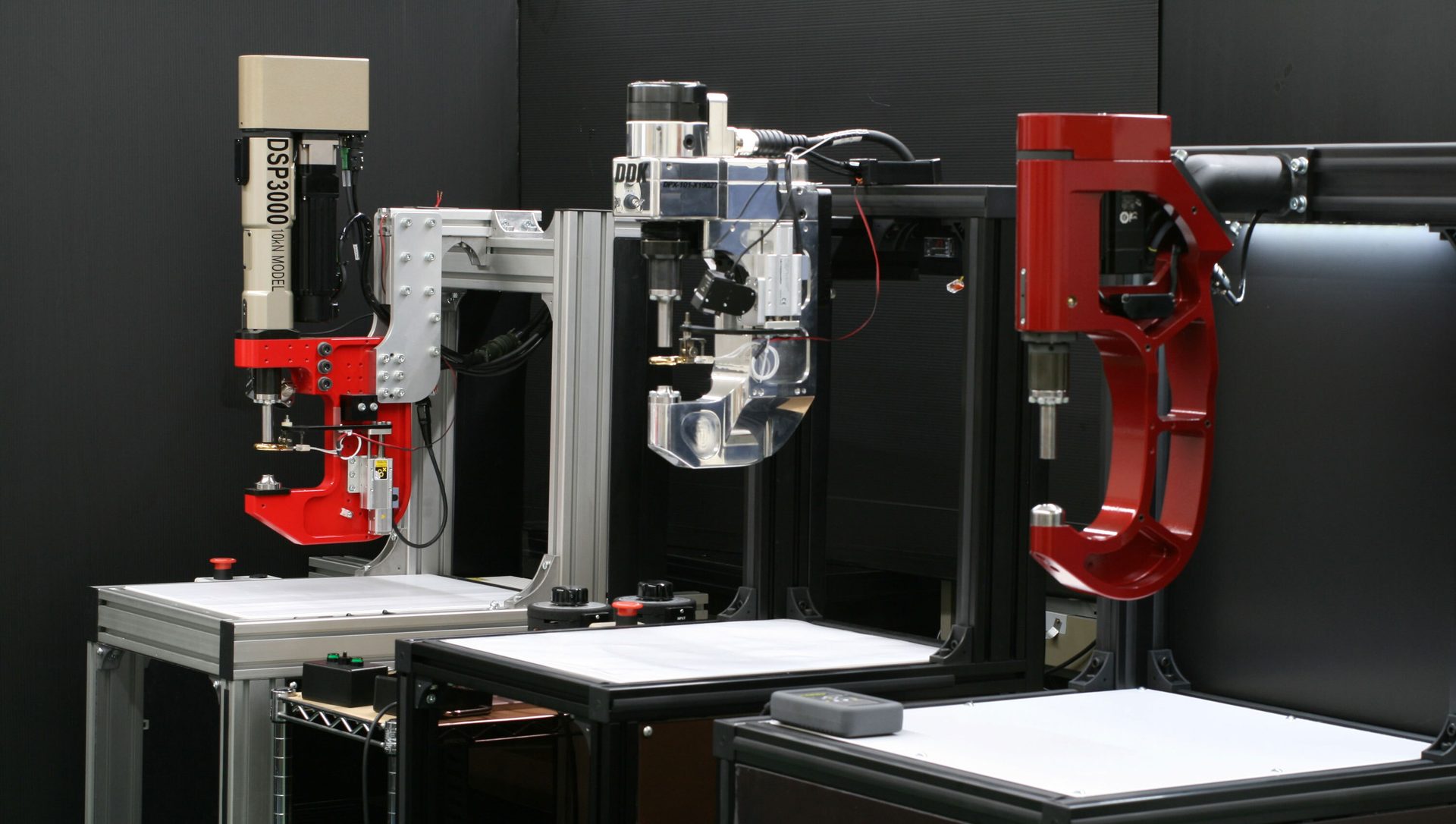
MC Fastening Solutions is a scalable supplier of fastening and pressing applications, including single-tool systems and advanced pressing cells.
Boulware Equipment, LLC
3134 Pinkie ln
Newton, NC 28658
704-651-6061
BRAD BOULWARE
PALLET TRASH, REPURPOSED FOR PROFIT
In 2017 Boulware Equipment commissioned the 1st of 2 Shredding systems at an assembly plant (pictured) in Eastern North Carolina. When the plant increased its capacity in 2018, they returned to Boulware Equipment for a 2nd Wood Grinding System. Now in 2021 both systems run simultaneously & Boulware Equipment is responsible for over 100 + Tons of Wood Scrap a week from this single location. This customer and many others choose Boulware Equipment for their wood scrap recycling solution because of how the scrap is handled & repurposed once it leaves your plant. Boulware Equipment provides turn-key equipment design, installation & startup. Our network of 100s of wood fiber buyers across the USA allow us proudly to say we NEVER take wood scrap to the landfill.
Our company supplies woodchip trailers and logistics for the wood fiber recycling at no charge to our customer. We reduce costs, lower your carbon footprint, and repurpose your wood trash in a responsible way, and guarantee no landfill. Repurposing wood trash is our mission.
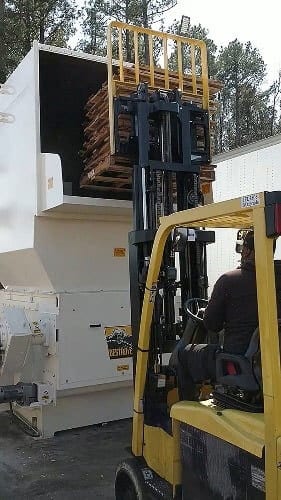