ROBOTICS REVIEW
CONTACT
Austin
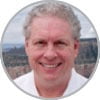
Lightweight battery-powered aircraft are ready for take-off.
AI-Enhanced Robots Improve Aircraft Production
Austin Weber // Senior Editor // webera@bnpmedia.com
A workcell equipped with xCognition improved the accuracy and consistency of a six-axis robot when performing a set of drilling tests on an aluminum plate. Photo courtesy Xaba Inc.
ROBOTICS REVIEW PRODUCTS
Traditionally, airplane manufacturing has been difficult to automate, due to factors such as tight tolerances and stringent quality demands. However, a new breed of robots enhanced with artificial intelligence technology promises to change that scenario.
A Canadian startup company called Xaba Inc. has been working with Lockheed Martin Corp. to apply AI-enhanced robotics at its factory in Marietta, GA, that assembles military planes such as the C-130 transport and the P-3 Orion surveillance aircraft.
Xaba uses AI to control industrial robots and enable intelligent systems that are more accurate than traditional options and can easily be applied to existing manufacturing operations. Its technology transforms robots into fully intelligent, self-directed systems that can automatically optimize, adjust or change to incorporate various production constraints.
“Our system lowers the barriers to adopting new manufacturing technologies, materials and approaches,” says Massimiliano Moruzzi, CEO of Xaba. “For the first time, robots used in manufacturing will be able to consider all elements of execution in the process, which will ultimately reduce reliance on human supervision.
“The aerospace industry has always had a conservative mindset,” explains Moruzzi, an aerospace engineer who formerly worked at Boeing on the 787 Dreamliner project. “A combination of critical tolerances, tight spaces and dissimilar materials typically makes it difficult to apply automation in this sector.
ZiMo enables easy and mobile positioning at various locations without the need for complex integration into existing systems. An intuitive setup allows for operation without programming knowledge and its flexible configuration with quick adaptation enables profitable automation solutions, even for small-batch sizes. ZiMo offers versatility and flexibility - thanks to its compact size and adaptable setup.
Zimmer Group US, Inc.
828-855-9722
info.us@zimmer-group.com
www.zimmer-group.com
Mobile Robotic Cell Provides Flexible Automation Solution
“An incredible amount of variables and layers of regulations also add to the complexity,” Moruzzi points out. “In general, the key performance indicators required to produce an airplane are much higher than for many other products, such as dishwashers or refrigerators.”
New Opportunities
Growing demand for automation in the aerospace sector today is driven by changing market conditions that require more variation and new products. Cost is another issue, in addition to waste reduction, skilled labor shortages and an increasing need for assembly line flexibility.
Startups such as Archer Aviation, Boom Supersonic and SpaceX are putting additional pressure on traditional aerospace manufacturers to automate their factories.
“Next-generation automation will be required to grow and maintain market share in the future,” claims Moruzzi. “Aerospace manufacturers want autonomous cells for drilling, riveting and fiber layup applications. They need equipment that is flexible, intelligent and scalable.
Any investment in automation must guarantee quality and consistency.
COVAL’s MVG series vacuum grippers correspond perfectly to the expectations of integrators and users, thanks to their high degree of modularity. They provide the optimal handling solution for products of varied sizes, shapes, and weights. One MVG gripper can carry out single or multiple grips of diverse products, and create independent gripping zones, guaranteeing optimization of vacuum management.
COVAL Vacuum Technology, Inc.
(919) 233-4855
contact-us@coval.com
www.coval.com
MVG by COVAL: The Modular Optimal Handling Solution
“In military applications today, there’s a big push toward cost reduction, while commercial aircraft manufacturers are focusing heavily on sustainability and material reduction initiatives,” says Moruzzi. “Unlike many other industries that have successfully adopted robotics, aerospace still depends on many manual production tasks that are labor and time intensive.
“Accurate drilling historically requires expensive (both in hardware and real estate) static machine tools,” explains Moruzzi. “Otherwise, the task is manually performed by skilled operators.
“Using industrial robots and collaborative robots instead of the options currently embraced by aerospace companies is appealing,” says Moruzzi, “because they are much more flexible, adaptable and less costly than CNC machine tools.
“However, commercial industrial robotic systems have struggled to perform critical aircraft manufacturing operations such as drilling, laser welding, light machining and precise assembly,” notes Moruzzi. “The reason for this is the lack of robotics intelligence required to deliver accuracy and repeatability, and to work in path programming mode rather than point-to-point.”
To address these challenges, Xaba has developed two control systems that use proprietary, state-of-the-art AI technology to provide consistency, robustness, persistently high execution quality and autonomy. The platforms eliminate the need for constant human supervision and reprogramming, while reducing waste.
xCognition captures and models the physics of industrial robots (elastic, dynamic, mechanical, tooling), and enables any robotic system to execute tasks such as adhesive dispensing, drilling, riveting and welding with maximum accuracy, repeatability and minimum programming.
xTrude is an additive manufacturing program for Fused Deposition Modeling (FDM) applications. It enables companies to print large functional parts while dramatically reducing failures such as delamination, collapse and distortion.
Lockheed Martin’s factory in Marietta, GA, assembles military planes such as the C-130 transport. Photo courtesy Lockheed Martin Corp.
“The systems allow engineers to evaluate, adopt and deploy intelligent automation in a much shorter time with a substantially higher throughput and increased sustainability,” claims Moruzzi. “xCognition uses a proprietary language model combined with deep learning path processing that provides automatic extraction of the robotics trajectory for a particular task.
“The system is constantly learning, so no programming is required,” explains Moruzzi. “A production task that may take weeks to program and teach only takes minutes with our system. Engineers don’t have to spend time transferring knowledge to the robotic system.
“xCognition uses an AI-powered interface to capture an operator’s intent with little to no training required, or it can be driven by sensor input such as a vision system,” says Moruzzi. “It then automatically generates machine programs in the required language for a robotics workcell.
“It also uses AI to learn precisely how and where a robot needs to move, automatically generating its control programs and self-correcting the machine when it gets off course, dramatically increasing precision and consistency,” notes Moruzzi.
This collaborative robot uses AI-enabled technology to dramatically improve absolute positioning and trajectory accuracy during a welding application. Photo courtesy Xaba Inc.
Pilot Program
Xaba recently worked with Lockheed Martin engineers to test a drilling application using a six-axis machine from ABB Robotics.
“Lockheed Martin was using a vision-based robotic drilling application, but it was taking a long time for the machine to reach the tolerances that they wanted,” says Moruzzi. “Our system acts as a ‘synthetic brain’ that sits on top of the robot and enables it to control the physics of the machine.
“The goal of the project was to test how the [AI-enhanced system] could empower a commercial robot with greater intelligence and understanding of its body, and the task it is about to execute, while ensuring required quality and tolerances are achieved,” explains Moruzzi.
The pilot test at Lockheed Martin Marietta consisted of two phases:
• Assessing the robot’s performance in maintaining accurate and consistent trajectory positioning with and without xCognition.
• Performing a set of drilling tests on an aluminum test plate with specified positional tolerances.
According to Moruzzi, xCognition improved accuracy and consistency of the robot by a factor of 10 times. “This test shows how industrial robots augmented with [AI technology] can perform crucial manufacturing operations that until now have been exclusively done by more expensive and less flexible CNC machines,” he points out.
“The accuracy performance of a robotic system limits the type of process it can perform based on the cost efficiency of the accuracy hardware,” adds Matthew Galla, a mechanical engineer at Lockheed Martin Aeronautics Co. who worked on the project. “The test with the xCognition controller allows us to rethink how we can accelerate innovation in manufacturing.”
“AI-driven control systems open a new world of application opportunities for industrial robots and cobots,” claims Moruzzi. “Unlike analytical AI used for predictive modeling, industrial AI focuses on the physical world. It can model and drive a vehicle, a complex machining center and more complex industrial applications.
“xCognition integrates seamlessly with every commercial robot brand to make them more consistent, robust and autonomous, significantly increasing applications and throughput,” says Moruzzi.
“A company with Ford’s scale can really influence the supply chain and business practices across our entire industry,” adds Sue Slaughter, purchasing director at Ford Motor Co. “It is so important that we not only think about how [we] can use our purchasing power to fuel our business needs, but also to advance sustainability.”
Because the automotive supply chain is extremely complex, the Guiding Principles contain expectations about business ethics, working conditions, human rights, health and safety, environmental leadership and supply chain due diligence for suppliers at all tiers. All suppliers are expected to uphold these standards and enforce them throughout their supply chain.
The Guiding Principles are based on fundamental elements of social, environmental and governance responsibility that are consistent with applicable laws and international standards created by organizations such as the United Nations.
Topics covered under the revised guidelines include the following:
Business ethics, including counterfeit parts and data protection.
Environmental issues, such as air quality, carbon neutrality, chemical management, circularity and water management.
Health and safety issues, such as personal protective equipment and workspace.
Human rights and working conditions, such as benefits, wages and working hours.
Responsible supply chain management, such as ethical sourcing of raw materials.
The BMW Group has implemented several projects in its packaging logistics unit to help the environment and conserve resources. The goal of the initiative is to work closely with suppliers to reduce carbon emissions and adhere to the principles of a circular economy.
BMW’s European assembly plants are using more recycled material in their packaging. For newly awarded contracts, the proportion of recycled material in reusable packaging for logistics purposes will almost double this year from around 20 percent to over 35 percent.
Using alternative sustainable materials, reducing single-use packaging, introducing lightweight packaging in certain areas and reducing transport volumes will also help cut carbon emissions.
BMW is monitoring the impact of individual measures via a CO2 calculator for packaging. The automaker’s overall aim is to reduce CO2 emissions in the supply chain by 20 percent per vehicle compared to 2019.
“Our re:think, re:duce, re:use, re:cycle approach is being implemented consistently in packaging logistics,” says Michael Nikolaides, head of production network and logistics at BMW Group. “We’re using innovative strategies to consistently reduce the volume of resources we use, thus reducing our carbon footprint.
“We are also doing our part to get the BMW iFACTORY up and running, with a particular focus on the ‘green’ side of things…with an emphasis on flexibility and efficiency, sustainability and digitalization,” explains Nikolaides. “It provides an answer to the challenges involved in the transformation to e-mobility and [leverages] the latest technologies to create a production process that uses minimal resources.”
According to Nikolaides, BMW is using more recycled material, such as expanded polypropylene (EPP) packaging. “Our newly developed EPP packaging already contains 25 percent recycled material,” he points out. “EPP is used in special containers, as its shape can be adapted to the components being packaged, allowing them to be transported safely.
“Around 360,000 of these containers are needed each year,” claims Nikolaides. “Using 25 percent recycled material allows us to save almost 280 tons of CO2 annually. There are plans to increase this proportion of recycled material even further, with the first pilot schemes with 100 percent recycled material currently underway. If these tests are successful, this configuration will become standard for new contracts from 2024.
“An additional 680 tons of carbon emissions savings can be made every year by using covers and so-called small load carriers with 50 percent recycled contents,” says Nikolaides. “As things stand, these measures are focused within the European markets due to the current waste management situation and available recycling infrastructure. But, we are working toward expanding to our locations in China, Mexico and the United States.”
BMW also plans to use folding large load carriers in place of traditional pallet cages made of steel. The plastic alternatives will be made from over 90 percent recycled material. They work in a similar way to the collapsible shopping crates that most people are familiar with.
When they’re empty, the carriers can be folded up, making them easier to transport. Nikolaides claims that using 15,000 of these new containers will reduce CO2 by around 3,000 tons per year.
“When it comes to packaging, the sky’s the limit,” says Nikolaides. “We’re launching pilot projects using bio-based materials to replace oil-based substances such as polyethylene and polypropylene.
“We are also investigating whether and in what ways we can use materials from recycled household appliances in our packaging,” explains Nikolaides. “In the long term, our aim is to use alternatives to raw materials across the board.”