ASSEMBLY LINES
Manufacturers Harness Extended Reality Technology
WASHINGTON—Manufacturers in a variety of industries are using extended reality technology for applications ranging from quality assurance to workforce development. Extended reality (XR) is an umbrella term that refers to augmented reality, virtual reality and mixed reality. With the aid of wearable devices, XR combines the physical world with the digital world, giving users an immersive experience.
According to a recent study conducted by the XR Association, 81 percent of manufacturers believe that immersive technology is important. In addition, more than one-third of respondents claim that XR technology can help address workforce skill gaps by significantly reducing barriers to skill acquisition, improving new hire training and helping with employee recruitment.
Manufacturers are using extended reality technology for everything from quality assurance to workforce development. Illustration courtesy XR Association
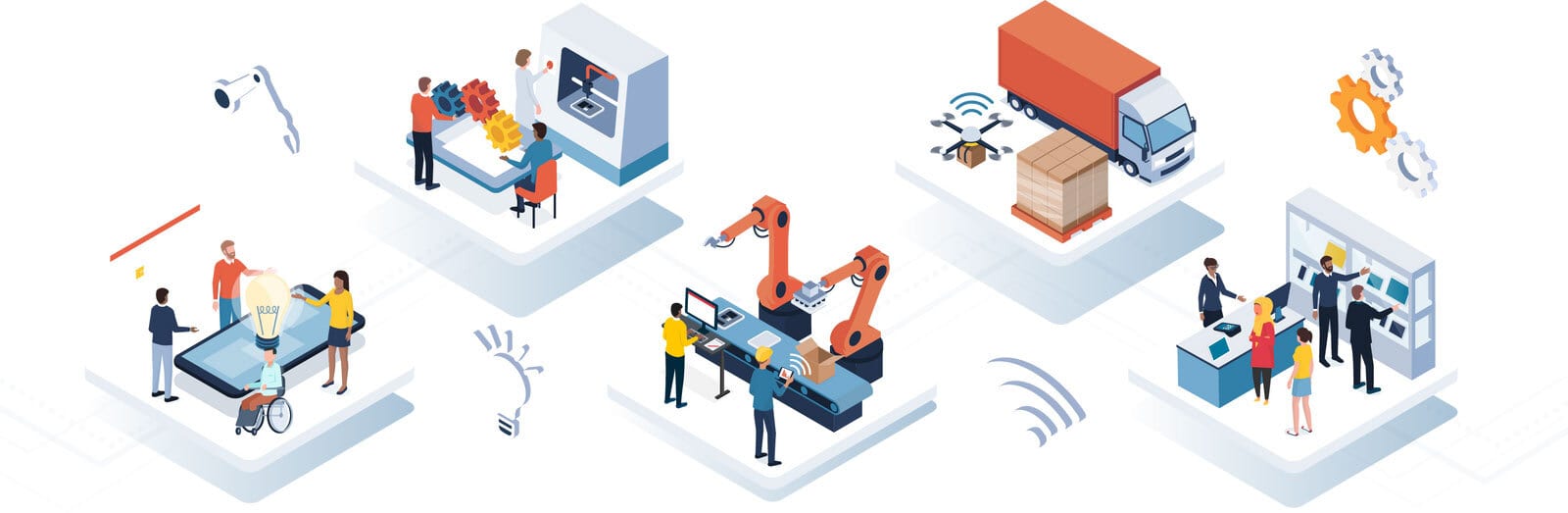
“Our intention with this survey was to take a comprehensive look into an industry that is exploring the use of immersive technology to address some of the same challenges we’re seeing across other fields, including skills and employee shortages,” says Stephanie Montgomery, vice president of research and development at the XR Association. “This isn’t a phenomenon isolated to the manufacturing industry, but a piece of the larger puzzle seeking to drive efficiencies in workflows.”
Montgomery claims that XR technology can be used to improve employee training, recruitment and retention at a fraction of the cost of traditional methods. She says manufacturers can also apply the technology to improve quality control, design and prototype products, encourage remote collaboration, and improve customer engagement and sales.
Dance Moves Help Humanoids Work Better With Humans
SAN DIEGO—Engineers at the University of California San Diego have trained a humanoid robot to effortlessly learn and perform a variety of expressive movements, including simple dance routines and gestures like waving, high-fiving and hugging.
The enhanced expressiveness and agility of the machine may pave the way for improving human-robot interaction on assembly lines, enabling humanoids to safely operate alongside operators.
“Through expressive and more human-like body motions, we aim to build trust and showcase the potential for robots to co-exist in harmony with humans,” says Xiaolong Wang, Ph.D., a professor of electrical and computer engineering at UC San Diego. “We are working to help reshape public perceptions of robots as friendly and collaborative rather than terrifying like The Terminator.”
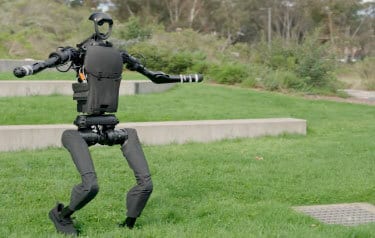
Engineers have trained a humanoid robot to perform a variety of expressive movements, including simple dance routines. Photo courtesy University of California San Diego
Wang and his colleagues used an extensive collection of motion capture data and dance videos. They trained the robot’s upper and lower body separately. This approach allowed the machine’s upper body to replicate various reference motions, such as dancing and high-fiving, while its legs focused on a steady stepping motion to maintain balance and traverse different terrains.
“The main goal here is to show the ability of the robot to do different things while it’s walking from place to place without falling,” explains Wang. “By extending the capabilities of the upper body, we can expand the range of motions and gestures the robot can perform.”
Despite the separate training of the upper and lower body, the robot operates under a unified policy that governs its entire structure. This ensures that it can perform complex upper body gestures while walking steadily on surfaces like gravel, dirt, wood chips, grass and inclined concrete paths.
Currently, the robot’s movements are directed by a human operator using a game controller, which dictates its speed, direction and specific motions. A future version may be equipped with a camera to enable the robot to autonomously perform tasks and navigate terrains.
AI Use in Manufacturing Is Growing
ARLINGTON, VA—American manufacturers are eager to adopt artificial intelligence technology in their factories. In fact, the Manufacturers Alliance Foundation claims that many companies are already using AI today, with a significant focus on strategic business initiatives.
Some 93 percent of manufacturers recently surveyed have added new AI initiatives within the last 12 months, while another 6 percent are preparing to launch such initiatives.
Manufacturers expect AI to improve productivity, throughput and quality. And in time, provide significant topline benefits.
Manufacturers expect investments in artificial intelligence technology to improve productivity, throughput and quality. Photo courtesy Siemens
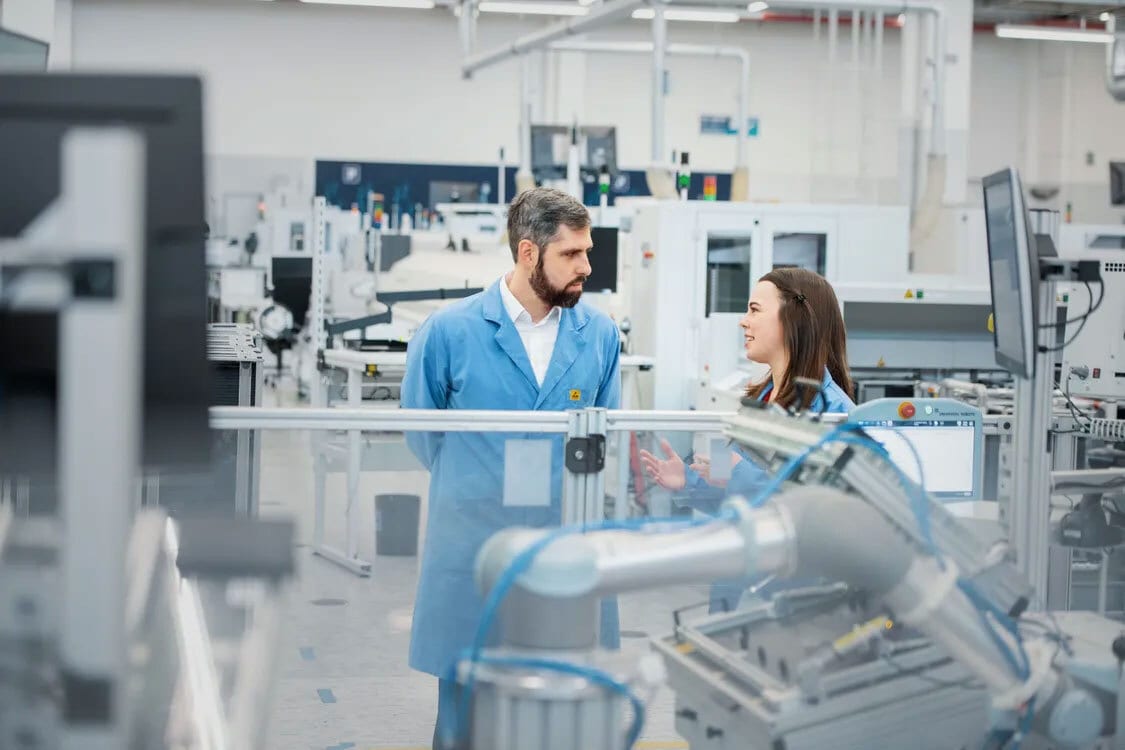
Manufacturers have been adding AI to the value stream in departments such as design and engineering; production and maintenance; quality; supply chain management; and warehousing and inventory.
“AI implementation is a natural evolution of manufacturing,” says Stephen Gold, president of the Manufacturers Alliance Foundation. “Adding language-based models to already tried and tested machine learning and industrial AI allows [applications] to accelerate at an advanced pace. [Manufacturers] are at the crux of transforming fiction into a key component of technology that improves operations and business functionality.”
According to Gold, finding new use cases of generative AI creates more opportunities for manufacturers to embrace long-term change. He also says that despite the learning curve, companies are discovering that AI helps solve existing problems more efficiently.
More than one half (55 percent) percent of respondents are prioritizing AI initiatives to strategic business objectives, while an additional 24 percent are focused on potential cost savings. At the same time, revenue growth is the top-ranking ROI expectation, followed by improved uptime and product quality.
New Aluminum Alloy Is Ideal for Additive Manufacturing
WEST LAFAYETTE, IN—Engineers at Purdue University have developed a high-strength aluminum alloy that is ideal for additive manufacturing applications because of its plastic deformability. The innovation has practical applications in a variety of industries, including aerospace and automotive manufacturing.
“Most commercially available high-strength aluminum alloys cannot be used in additive manufacturing,” claims Xinghang Zhang, Ph.D., a professor of material engineering at Purdue University. “They are highly susceptible to hot cracking, which creates defects that could lead to the deterioration of a metal alloy.”
A traditional method to alleviate hot cracking during additive manufacturing is the introduction of particles that strengthen aluminum alloys by impeding the movements of dislocations.
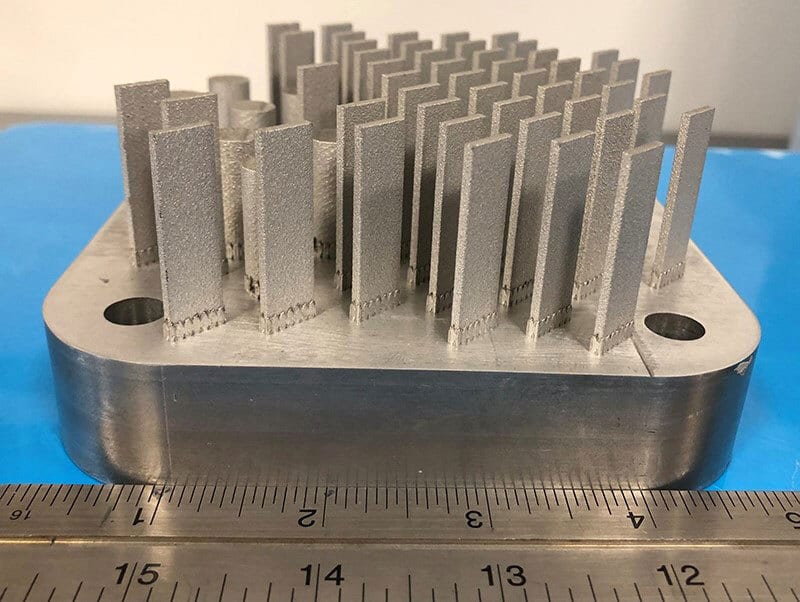
A patent-pending method creates ultra high-strength aluminum alloys that also demonstrate high plastic deformability. Photo courtesy Purdue University
“But, the highest strength these alloys achieve is in the range of 300 to 500 megapascals, which is much lower than what steels can achieve, typically 600 to 1,000 megapascals,” says Zhang. “There has been limited success in producing high-strength aluminum alloys that also display beneficial large plastic deformability.”
Zhang and his colleagues have produced new aluminum alloys by using several transition metals including cobalt, iron, nickel and titanium. These materials have traditionally been avoided in the manufacture of aluminum alloys.
“These intermetallics have crystal structures with low symmetry and are known to be brittle at room temperature,” explains Zhang. “But, our method forms the transitional metal elements into colonies of nanoscale, intermetallic lamellae that aggregate into fine rosettes. The nanolaminated rosettes can largely suppress the brittle nature of intermetallics.
“Our work shows that the proper introduction of heterogenous microstructures and nanoscale medium-entropy intermetallics offers an alternative solution to design ultra-strong, deformable aluminum alloys via additive manufacturing,” says Zhang. “These alloys improve upon traditional ones that are either ultra strong or highly deformable, but not both.
“The heterogeneous microstructures contain hard nanoscale intermetallics and a coarse-grain aluminum matrix, which induces significant back stress that can improve the work hardening ability of metallic materials,” Zhang point out. “Additive manufacturing using a laser can enable rapid melting and quenching, and thus introduce nanoscale intermetallics and their nanolaminates.”