Adhesives and Dispensing
Labor shortages are driving new demand for automation.
Options for Screwfeeding
Light-curing, heat-resistant epoxy is used to attach magnets in electric motors. Photo courtesy DELO Industrial Adhesives
Faster curing times make one- and two-part adhesives more versatile.
Epoxies
What’s NEW With
Austin Weber // Senior Editor // webera@bnpmedia.com
Epoxies are the most widely used polymers for adhesives, sealants, coatings, encapsulants, potting materials and impregnating compounds. These versatile materials come in liquids, pastes, and semi-cured films and solids. They resist oil, moisture and many solvents, and they bond well to a variety of substrates.
Epoxy adhesives are versatile in both application and performance, with their most desirable properties being high bond strength to a wide variety of substrates, except untreated plastics and elastomers. Their versatility lies in the fact that they can be mixed with additional substances or fillers.
Epoxies typically have excellent tensile and shear strength, but poor peel strength. However, poor peel strength can be improved if the formulation is modified with a more resilient polymer or other filler.
“Today, most manufacturers are looking for epoxies that feature high performance, bond strength and fast cure time,” says Barry Siroka, business development manager at EpoxySet Inc. “The challenge is to get cure temperatures lower without causing any detriment to the physical properties of the adhesive.”
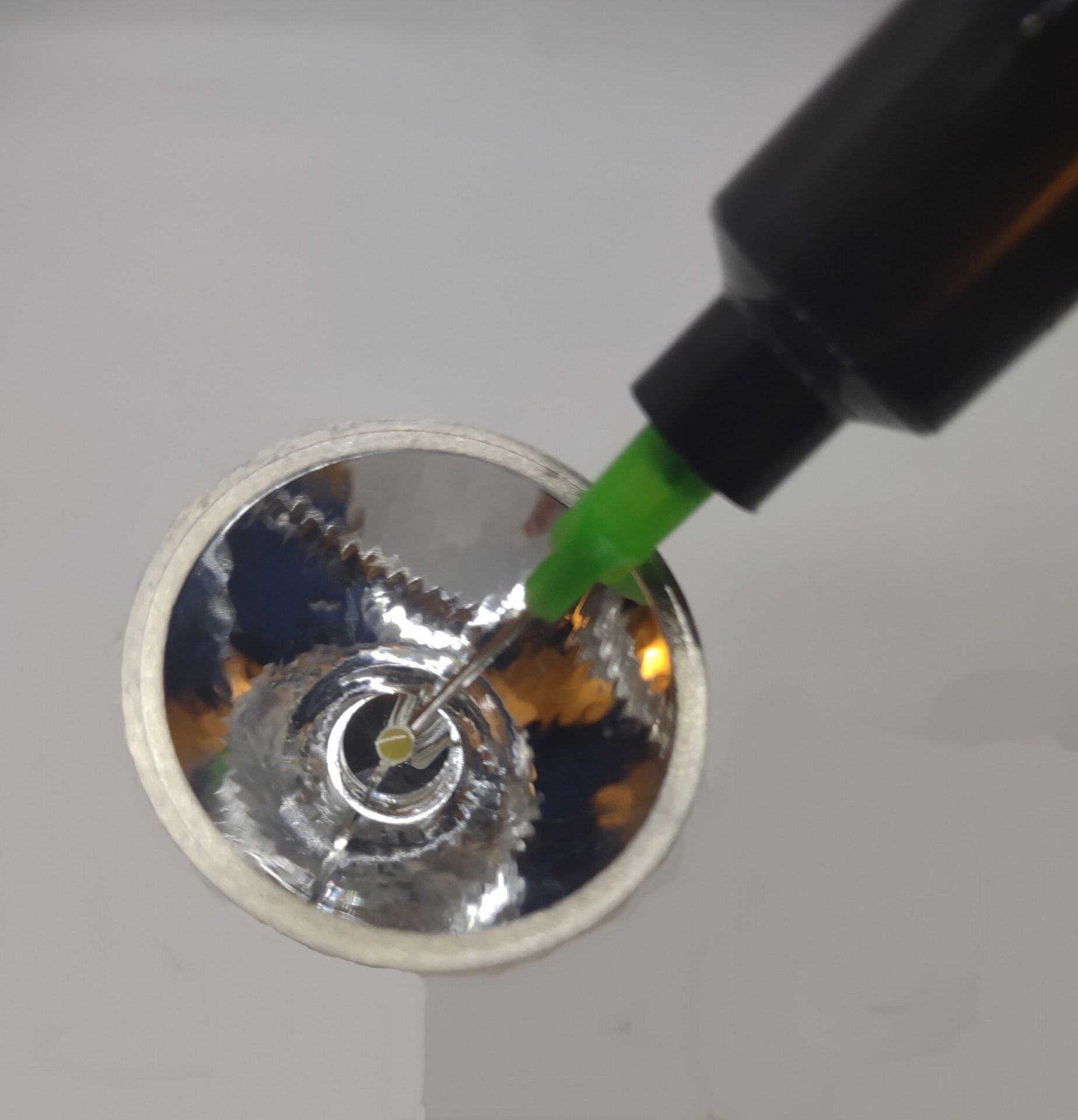
Epoxy is used to assemble a variety of optoelectronic devices. Photo courtesy EpoxySet Inc.
Better One or Better Two?
Engineers can choose between either one-component or two-component epoxies. The former can be used straight from the tube. No mixing, metering or degassing is required. However, these epoxies require heat for curing.
One-component adhesives have an initiator, which is activated by heat, mixed with resin. The epoxy then requires an oven or other heating mechanism to reach full cure. Typical cure times are 30 to 60 minutes at 350 to 400 F.
Handling strength can be achieved rapidly with induction cure. Curing time varies by product, but typically averages 6 seconds at 325 to 425 F. However, heat curing must follow induction curing for the epoxy to reach full cure. Ultraviolet light-curing epoxies are also available in one-component versions.
One-component epoxies are easier to use, because no mixing is involved. With metering and mixing eliminated, there is no risk of rejects due to incorrect hardener and resin ratios.
“One-part epoxies are convenient, because people like the idea of not having to mix them,” says Siroka. “But, they require higher temperatures for curing.
“Traditionally, most one-part products have to be cured over 212 F,” notes Siroka. “We have recently developed next-generation epoxies that can be either UV- or heat-cured at lower temperatures. Most of those adhesive can be cured anywhere between 80 to 120 F.”
Despite the advantages of one-component epoxies, two-part materials are commonly used for most assembly applications because they produce a stronger bond. These adhesives require the user to mix a resin and a hardener. Hardeners trigger the polymerization required for curing.
When the two are mixed, either mechanically or by hand, an exothermic reaction occurs as the molecules begin to cross-link. When a full cure is reached, the bond is essentially a hard piece of molded plastic.
Two-component epoxies can be cured at either room temperature or elevated temperature. They can achieve handling strength in 5 minutes to 8 hours, depending on the type of curing agent used. The most commonly used epoxies solidify in 2 to 3 hours at room temperature.
A catalyst can be added to speed the reaction between the resin and hardener.
However, all epoxies should be allowed to cure five to seven days at room temperature before testing.
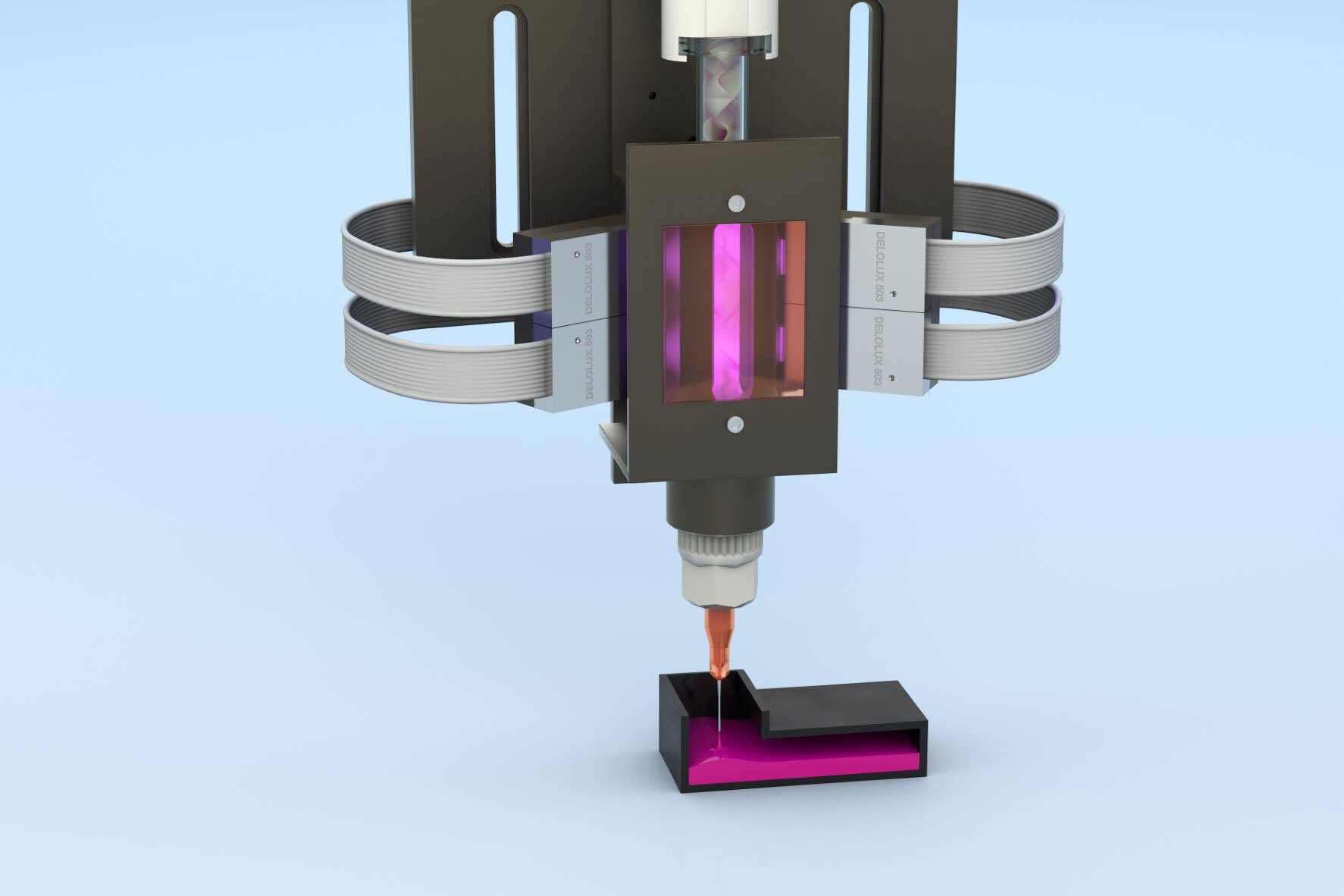
New “activation on the flow” technology combines the process steps of dispensing and preactivation by light, which reduces carbon emissions. Photo courtesy DELO Industrial Adhesives
Growing Demand
“Generally speaking, we see two fundamental reasons for increasing epoxy demand,” says Jürgen Bauer, head of product management, chemical formulations and new business at DELO Industrial Adhesives. “Phenomena such as miniaturization and multimaterial joints, as well as demand for more multifunctionality, have prompted the increased use of adhesives as a whole compared to other joining technologies.
“For epoxies specifically, increased thermal requirements in the automotive field, as well as more stringent [reliability] requirements for consumer electronics and semiconductors, [have driven] demand for epoxies,” explains Bauer.
“High-tech epoxies are not just a simple adhesive containing a resin and a hardener,” notes Bauer. “Rather, they are sophisticated formulations of 10 or so raw materials, each helping enable different properties that make them suitable for their specific applications. Examples include [fillers to improve] conductivity and additives for flowability or increased adhesion to specific substrates.
“[Today, we] see more and more epoxies with light fixation, which are proven to achieve high bonding accuracy while hastening production rates,” claims Bauer. “For example, they don’t require fixation devices to be assembled, disassembled and cleaned after each use as has often been the case before.
“Other trends include lower curing temperatures which, eventually, may reach room temperature,” says Bauer. “Sustainability has also become a pertinent theme in epoxies, with more products containing bio-based raw materials.
“[There has been] increased demand for features such as debonding on demand, introduced to improve reworkability, repairability and recycling,” explains Bauer. “In addition, temperature requirements are getting stricter, which results in the need for epoxies with higher temperature strength.”
Epoxies are typically used to bond metal, ceramic, glass and wood in structurally demanding applications. They’re used to assemble many types of products, including automotive hoods and doors, aerospace composites, batteries, electrical components, electronic devices, hardware, medical devices and sporting goods.
Today, epoxy adhesive is widely used to bond rare-earth magnets found in electric vehicle traction motors.
“We’re also seeing more demand for automotive electronics that are used in advanced driver assistance systems, such a cameras, lidar and other types of sensors,” adds Siroka.
“In addition epoxies are used for the active alignment of optical modules,” Siroka points out. “The components are used in a variety of photonics found in automotive, aerospace and defense applications. Adhesives are used to align parts and snap cure them to hold the alignment. It’s a growing market for us.”
New Products
Engineers have a variety of products available for epoxy applications, including many new types of high-strength adhesives that cure quickly.
One of DELO’s newest products is Dualbond HT2990, which it claims is the industry’s first high-temperature resistant structural adhesive with light fixation. It’s specifically designed for assembling electric motors.
“At room temperature, it can achieve a compression shear strength of up to 70-megapascals (MPa) on steel,” says Bauer. “In heat as extreme as 180 C, it still exhibits a tensile shear strength of 7 MPa on aluminum. This is equivalent to 70 kilograms per square centimeter of force, which is a very secure bond.”
EpoxySet recently unveiled Flashbond UV-3720, a UV-cured adhesive for active-alignment assembly applications.
“Originally formulated for camera modules, this epoxy is an excellent choice for optical devices, sensors and electronic modules where ensuring the alignment of the assembled parts is critical,” says Siroka.
UV-3720 is a dual-cure epoxy that can be cured with UV energy or heat. It cures in seconds under UV light, but it will cure to the same high properties when heated to 125 C and no UV energy. This makes the epoxy ideal for bonding shadowed areas and complicated configurations, eliminating the need for more than one adhesive.
The adhesive boasts a cure shrinkage of 0.015 percent. This rigid polymer has a glass transition temperature of 155 C, and a coefficient of thermal expansion of 30 parts per million per degree centigrade. It is perfect for holding alignments through a temperature range of -55 to 200 C.
“This halogen-free epoxy withstands 85/85 testing for 1,000 hours with an exceptionally low water absorption rate,” claims Siroka. “It produces excellent bond strength to polyphenylene sulfide, polyimides, polyester film, liquid crystal polymers and all elements in printed circuit boards.”
Master Bond Inc. recently developed Supreme 11AOHTLP, a two-component structural epoxy featuring thermal conductivity and electrical insulation. It meets NASA low outgassing specifications.
Inspection System
“This system is specifically designed for bonding larger parts, since it has a relatively long working life of 60 to 90 minutes (at room temperature for a 100-gram batch),” says James Brenner, marketing manager at Master Bond. “This makes it uniquely suited for demanding situations where more time for fixturing is needed. This toughened formulation is designed to withstand thermal cycling and offers a wide service temperature range from -112 to 400 F.”
Supreme 11AOHTLP cures at room temperature in two to three days, and faster with heat, in 2 to 3 hours at 200 F. It bonds well to a wide variety of substrates including metals, ceramics, glass, rubber and plastic.
The epoxy features a 1-to1 mix ratio by weight, with the mixed material being a thixotropic paste. To eliminate the need for manual measuring and mixing, it can be packaged in double barrel cartridges for gun kits. It’s also available in standard jars and cans, ranging from 0.5 pint to gallon containers.
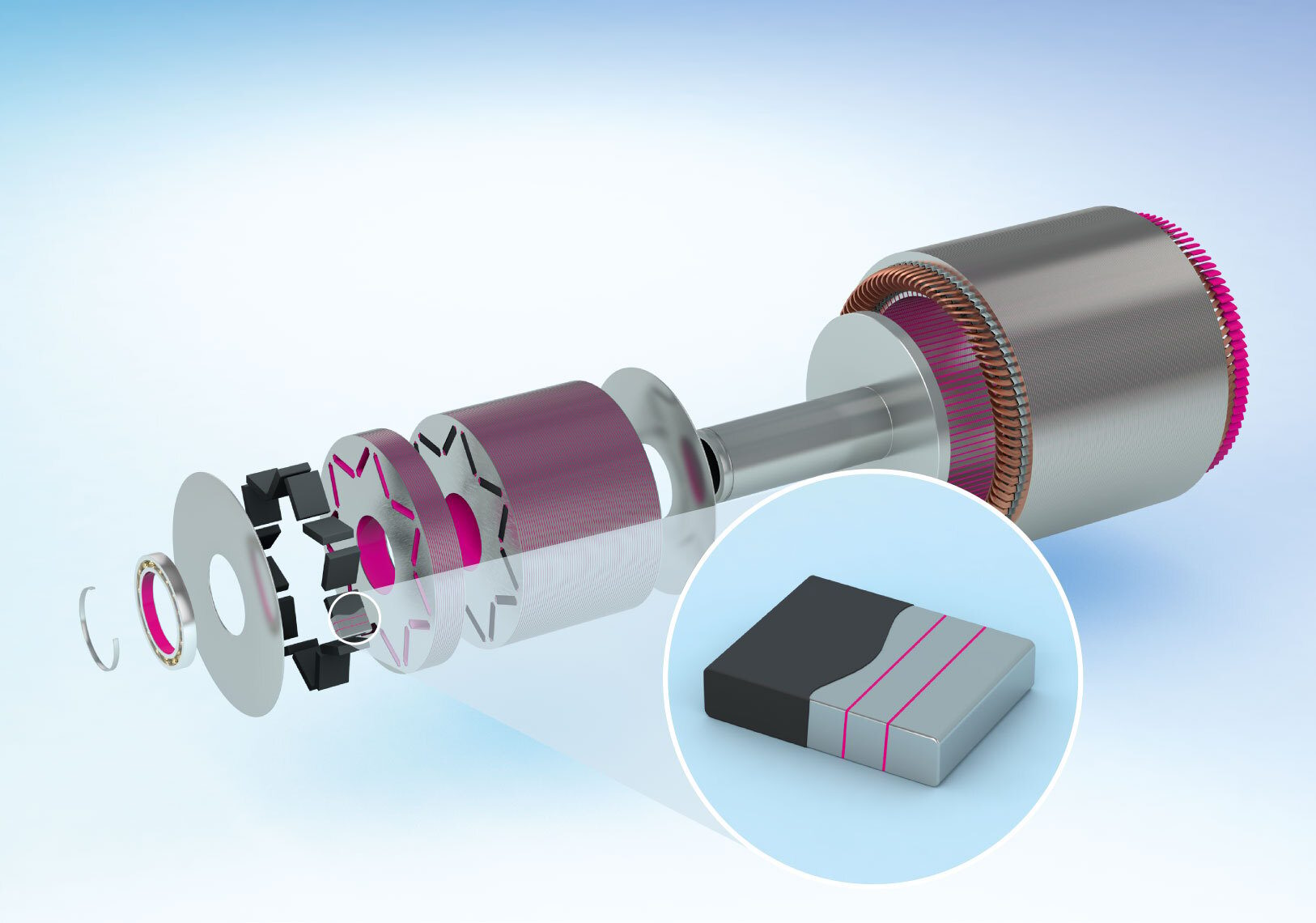