Automated Assembly
Labor shortages are driving new demand for automation.
Options for Screwfeeding
Since the company automated the machine tending process, employees can concentrate on more demanding tasks such as technical drawings or quality inspection. Photo courtesy OnRobot
A safe, flexible gripper enables the cobot to handle a wide variety of parts.
Cobot Automates Machine Tending
Colleen Soine // Global Marketing & Event Manager // OnRobot // Odense, Denmark
When employees of Donk Industries enter the factory hall in the morning, their newest colleague has already completed a slew of parts during the night shift.
He’s not the least bit social. He doesn’t wish them a good morning. They gave him a job to do at the end of the previous day, and he carried it out—precisely and without complaint. He doesn’t even expect to get paid for his services.
Their colleague, of course, isn’t human. It’s a six-axis collaborative robot from Universal Robots equipped with an RG6 gripper from OnRobot. Donk has been using the machine to automatically load and unload one of eight CNC machines around the clock.
Employing some 100 people, Donk has been making aluminum parts and assemblies in Lopik, the Netherlands, since 1932. The foundry, powder coating plant, machining department, assembly line and product development are all located under one roof. Handling all these processes at one location is a logistical advantage both for Donk and its customers. The arrangement enables Donk to respond optimally to customer requests.
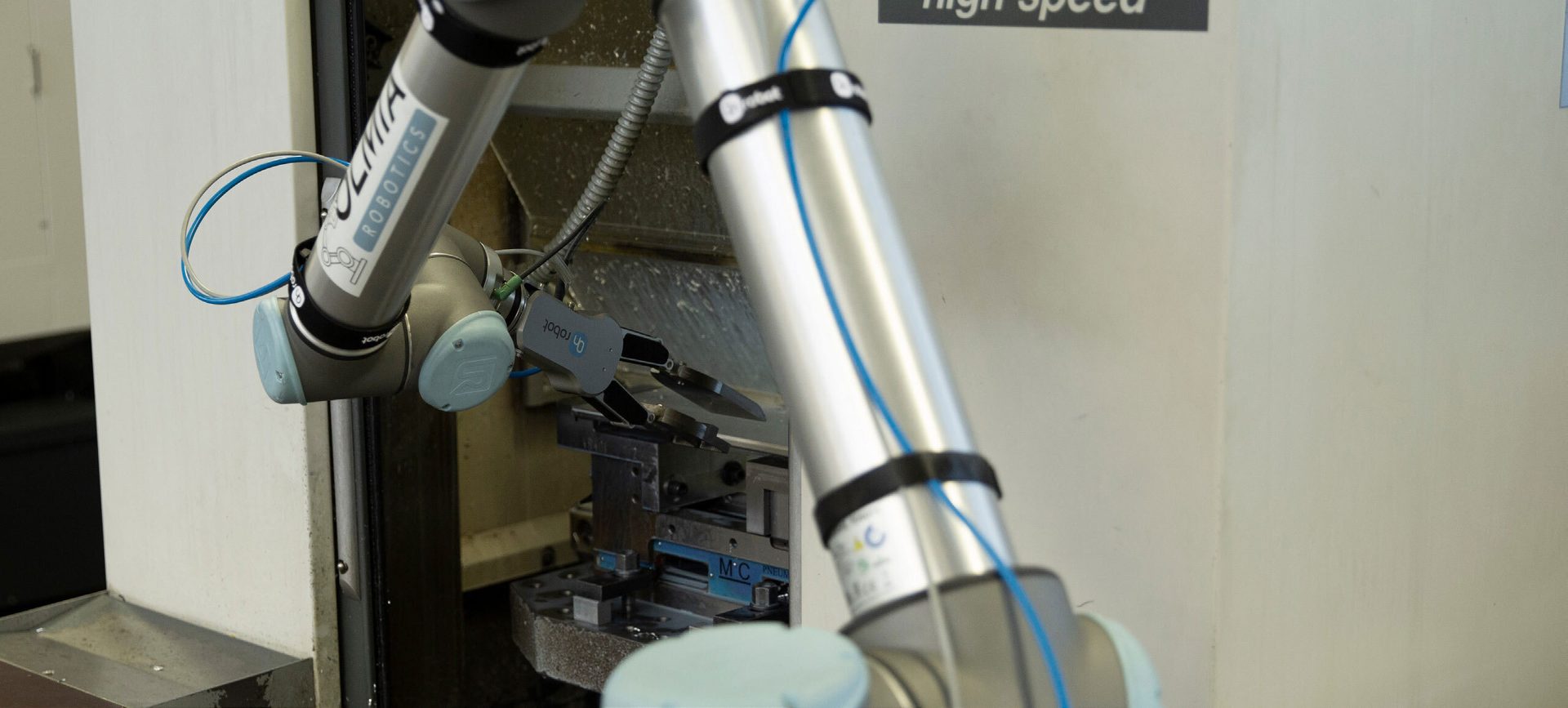
The gripper is equipped with a force and torque sensor to give the robot some “feel” as it loads and unloads parts. Photo courtesy OnRobot
Skilled Worker Shortage
But this service also comes with it challenges: As a job shop, Donk must cope with high-mix, low-volume production. At the same time, the company must keep its inventories low and supply customers on time. “To stand up to competitive pressure and meet the requirements of a small-run manufacturer, we need qualified personnel,” says Jaap Zentveld, assistant production manager at Donk.
In recent years, however, the company has been confronted with a shortage of skilled workers. It has been particularly difficult to find personnel to operate the CNC machines, a monotonous, time-consuming, and not very demanding task. Long cycle times meant personnel spent a lot of time waiting on the machine.
“Employees who actually have other areas of responsibility were tied to the CNC machine,” explains Zentveld. “This also had consequences for the quality and delivery reliability of the products.”
Zentveld wanted to automate machine tending so he could deploy his employees more effectively, increase productivity, and maintain the company’s high quality standards. A collaborative robot was high on his list.
“We were already automating many other parts of the production process with industrial robots,” says Zentveld. “However, we have to be flexible, given our product variety and the small quantities involved. We had to be able to convert our production lines quickly. In addition, many of the parts we make require special handling.
“Collaborative robots meet these requirements in particular: They can be flexibly converted for new tasks and are easy to program. In contrast to conventional industrial robots, the combination of cobot and corresponding end-of-arm tooling can be used directly next to people and work directly with them.”
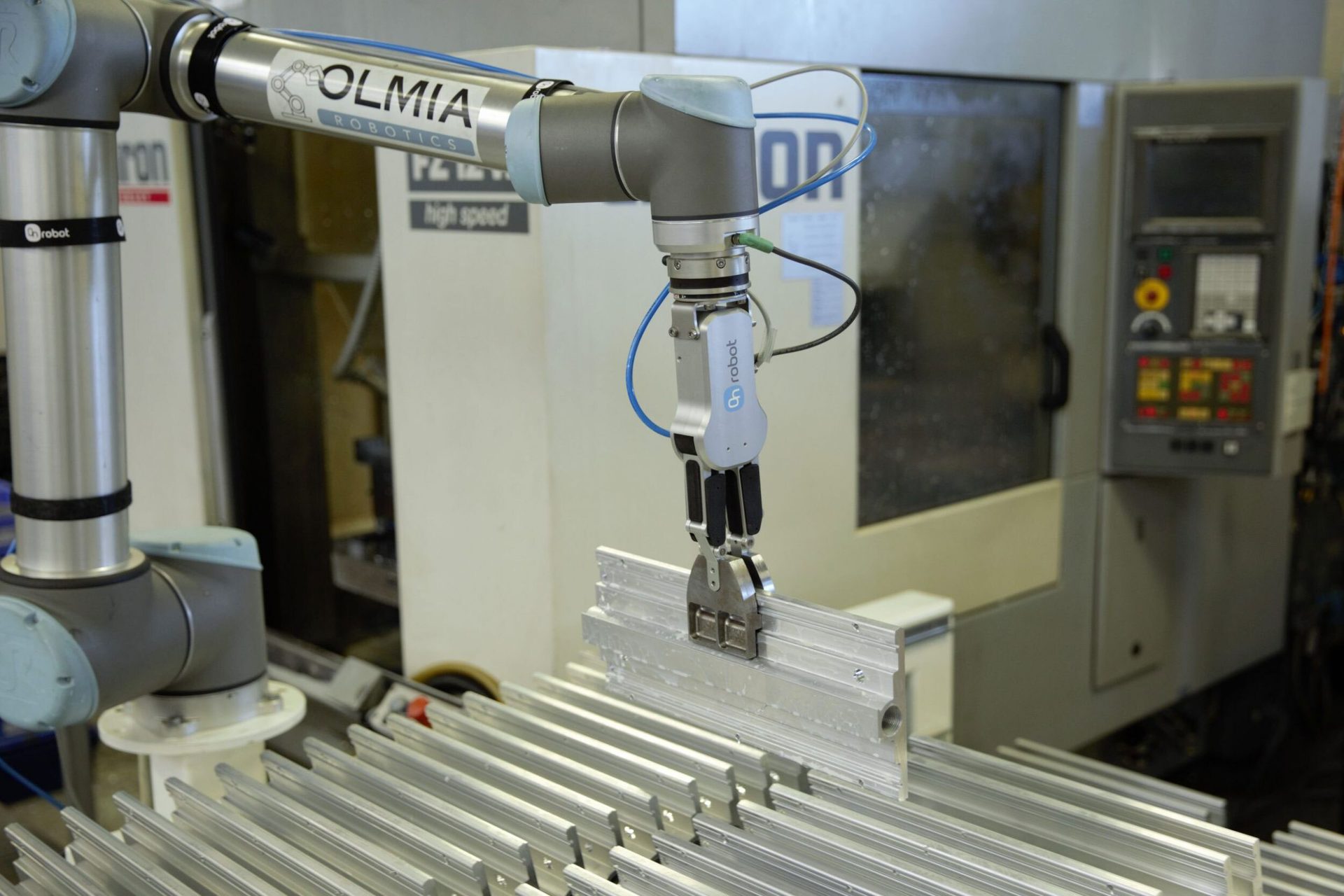
The gripper removes a part from a loading station and reinserts it there after the milling process. Photo courtesy OnRobot
Machine Tending With a Cobot
The robot loads and unloads one of eight CNC machines at Donk’s factory. The RG6 gripper, equipped with an OnRobot HEX sensor, is mounted at the end of the cobot arm. This force and torque sensor provides sensitivity so that the gripper can pick parts precisely and perform efficiently.
The RG6 gripper is a flexible collaborative gripper with a built in quick-change bracket. The bracket makes it easier to change the gripper’s orientation, without changing its range of motions and positions. The control cable is supported through the bracket. There’s no need to connect and disconnect an external cable when it’s time to change tools.
It can carry a payload up to 6 kilograms. Gripping stroke can be adjusted from 0 to 160 millimeters. Gripping force can be adjusted from 3 to 40 newtons. The gripper comes with a single mounting bracket and works on robots by Universal Robots, KUKA, Kawasaki, FANUC, Techman, Doosan, NACHI, Hanwha and Yaskawa.
A custom loading station, the Robobooster4000, was developed by local systems integrator Olmia Robotics to enable smooth loading and unloading of the machine. The gripper removes a component from this station and inserts it into the machine. After the milling process, it takes the finished product out and places it in a magazine. The cycle is repeated until all components have passed through the process.
Inspection System
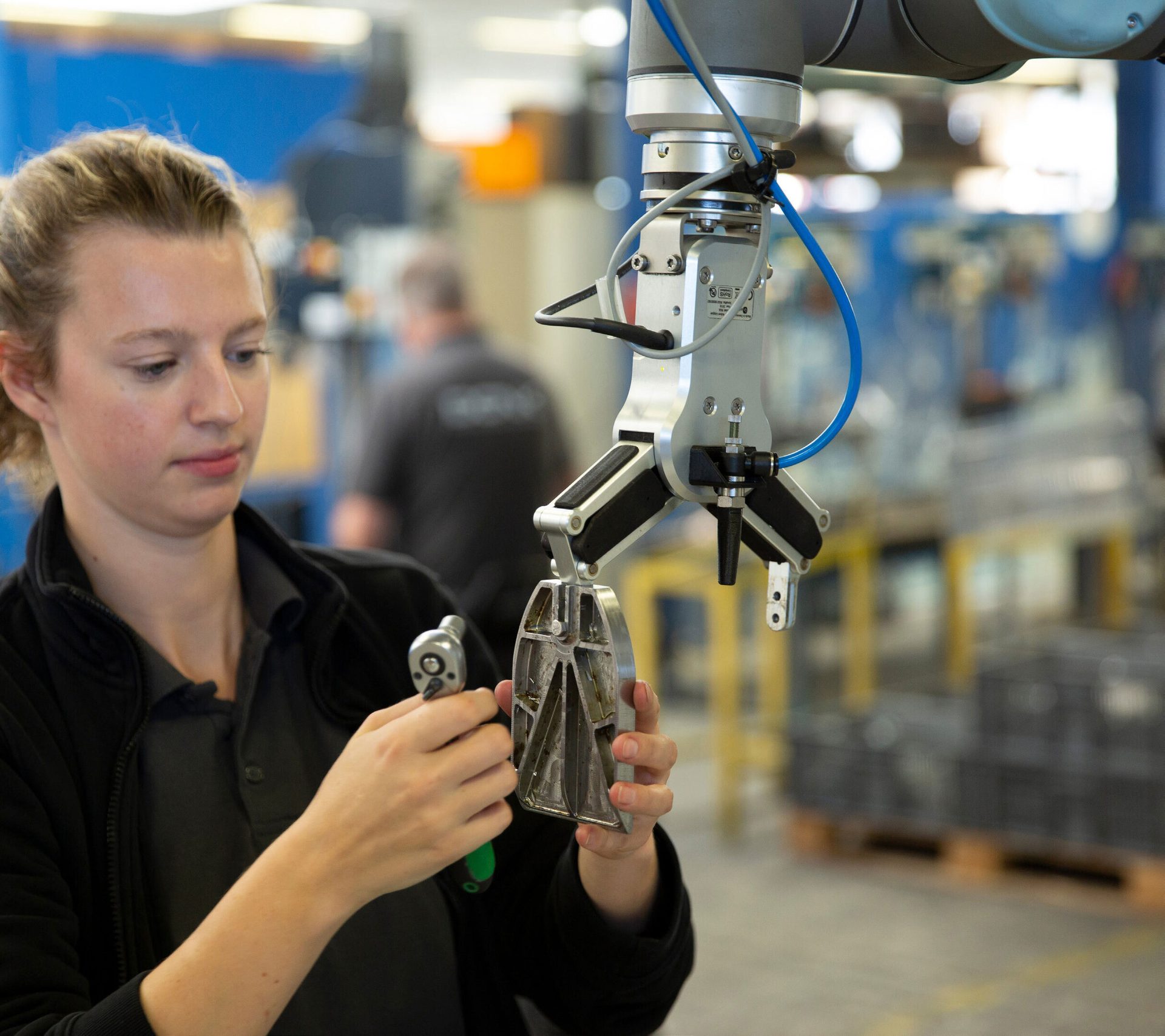
To handle individual parts, Donk has developed special fingers that employees can mount to the gripper in just a few minutes. Photo courtesy OnRobot
Thanks to its individually adjustable fingertips, the gripper can handle objects of different shapes and sizes. Olmia helped adapt the robotic system to Donk’s products.
“With Donk Industries’ specific requirements in mind, we recommended an OnRobot gripper,” says Peter van Olm, founder of Olmia Robotics and a distributor of OnRobot. “Because it is so flexible, we were able to adapt it individually to the application.”
The fingertips of the RG6 can be replaced within minutes. All the employees have to do is loosen a few screws, attach the new fingertips, and retighten the screws. This enables them to quickly adjust the gripper to handle different parts. If new parts are added, the employees develop suitable fingertips together with Olmia Robotics. This flexibility is reflected in time savings and better delivery reliability.
The cobot system has doubled the productivity of the CNC machine within a short time, while the failure rate has been halved. Even without human intervention, the application runs smoothly and can be used overnight. The constant operation of the machine has even more advantages: “Production is now much smoother—you can tell this from the product quality, which is much more consistent than before,” comments Zentveld.
The employees also reacted positively to the helping hand on the CNC machine.
“For us, the cobot is a great support, because we were able to give up some repetitive tasks. Now, we have more time to do more demanding things, such as quality control and technical drawings,” says Josine de Groot, an employee at Donk.
Donk has not cut any jobs by automating the machine tending process. In fact, valuable working time now flows into activities that previously could only be performed inadequately. Thus, the application has helped counteract the shortage of skilled workers.
In the future Donk Industries wants to focus even more on automation. “The entire project has shown us that automation is a real enrichment for our company and our employees,” says Zentveld. “In addition, we can now produce much more efficiently.”
Zentveld and his team are planning to automate additional CNC machines with cobots to relieve the strain on employees.
For more information on collaborative robots, visit https://www.universal-robots.com.
For more information about grippers for cobots, visit https://onrobot.com/us.
ASSEMBLY ONLINE
For more information on collaborative robots and grippers, visit www.assemblymag.com to read these articles: