Robotics
Austin Weber // Senior Editor // webera@bnpmedia.com
Improved technology has empowered end users and made robots less intimidating.
New Software Makes Robots Easier to Deploy
New software tools make robot programming a less daunting task. Photo courtesy Ready Robotics Corp.
Traditionally, many small- and medium-sized manufacturers avoided robots, because they were intimidating. Companies lacked the necessary programming knowledge and technical expertise. And, they simply weren’t willing to make investments in personnel that bigger manufacturers could afford.
However, that attitude has changed dramatically in recent years, partially due to the rise of open-source operating systems. That’s good news for many companies, because programming can be time-consuming and very expensive.
Robot programming can be a daunting task. Depending on the complexity of a project, such as the number of robots being programmed, the number of tasks, and whether users are starting from scratch or making modifications, the entire process can take anywhere from weeks to months of engineering time to accomplish.
In fact, according to some experts, programming accounts for 75 percent of the average cost of a robotic cell over its life cycle. A shortage of programmers capable of quickly readjusting cells across multiple robot brands and languages also limits automation deployment and growth in a variety of industries.
“Third-party programming software is designed to be agnostic to robotics hardware, meaning it can be used on most, if not all, industrial robots [marketed] by major brands,” says Lian Jye Su, robotics research director at technology intelligence firm ABI Research Inc. “Traditional robot software tends to very low level and requires high technical skills.
“Third-party software allows end users to program and simulate the behavior and movement of an industrial robot on a very user-friendly interface,” explains Su.
“Every robot manufacturer does things their own way,” adds George Konidaris, Ph.D., an associate professor of computer science at Brown University and director of the Intelligent Robot Lab. “If you want to control a robot from any specific manufacturer, you must learn the programming language it supports.
“Those languages are complex, cumbersome, low-level and not in any way mutually intelligible, so many integrators end up specializing in one brand of robot,” claims Konidaris. “That’s bad, because not only are the languages hard to use, but once they’re specialized, [companies are stuck with it].
The growing popularity of UR’s collaborative machines has helped spur new software developments. Photo courtesy Universal Robots USA Inc.
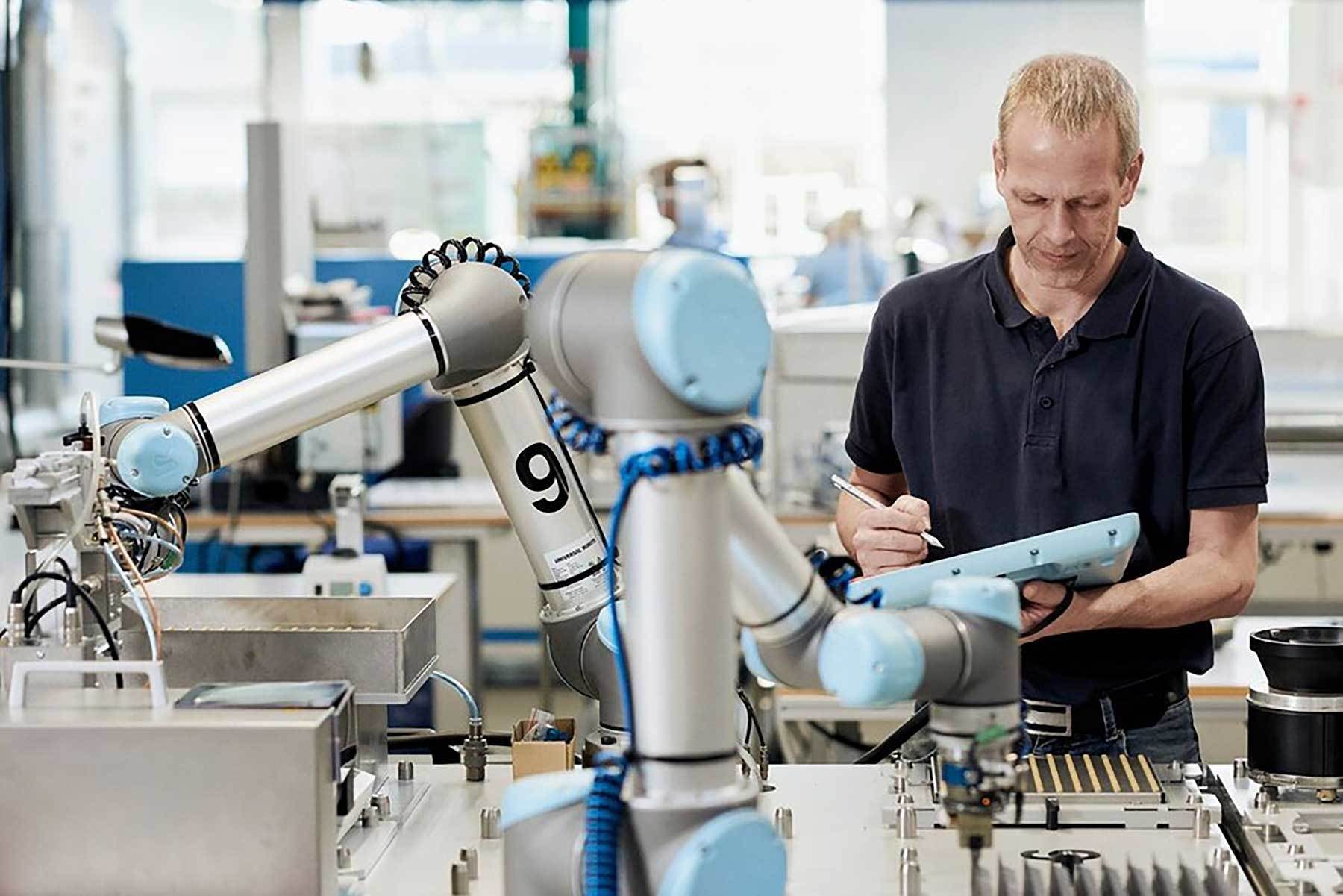
“With open, third-party software, a systems integrator can learn a single software package—which typically operates at a much higher level of abstraction—capable of controlling robots from any manufacturer,” explains Konidaris, who also serves as chief roboticist at Realtime Robotics Inc., a start-up company that has developed motion planning software that can be used with a variety of robot brands. “Now, they can pick the right robot for the job at hand.
“A useful analogy is thinking about desktop computer printer brands,” says Konidaris. “Imagine if, in order to print a document, you had to use a special-purpose, low-level programming language, and each manufacturer had a different one. If you wanted to print on an HP printer, you had to use one language, and if you wanted to use a Canon or Lexmark printer, you’d need to learn a new one.
“That would be terrible,” Konidaris points out. “And, it would make desktop printers expensive to install and impractical for lots of people. Instead, what people do is install a printer driver, and your computer gives you an intuitive and uniform interface to all the printers. That's the 'win' that third-party software delivers for industrial robots.”
End Users Drive Change
New programming software is designed to be agnostic to robotics hardware. Photo courtesy Realtime Robotics Corp.
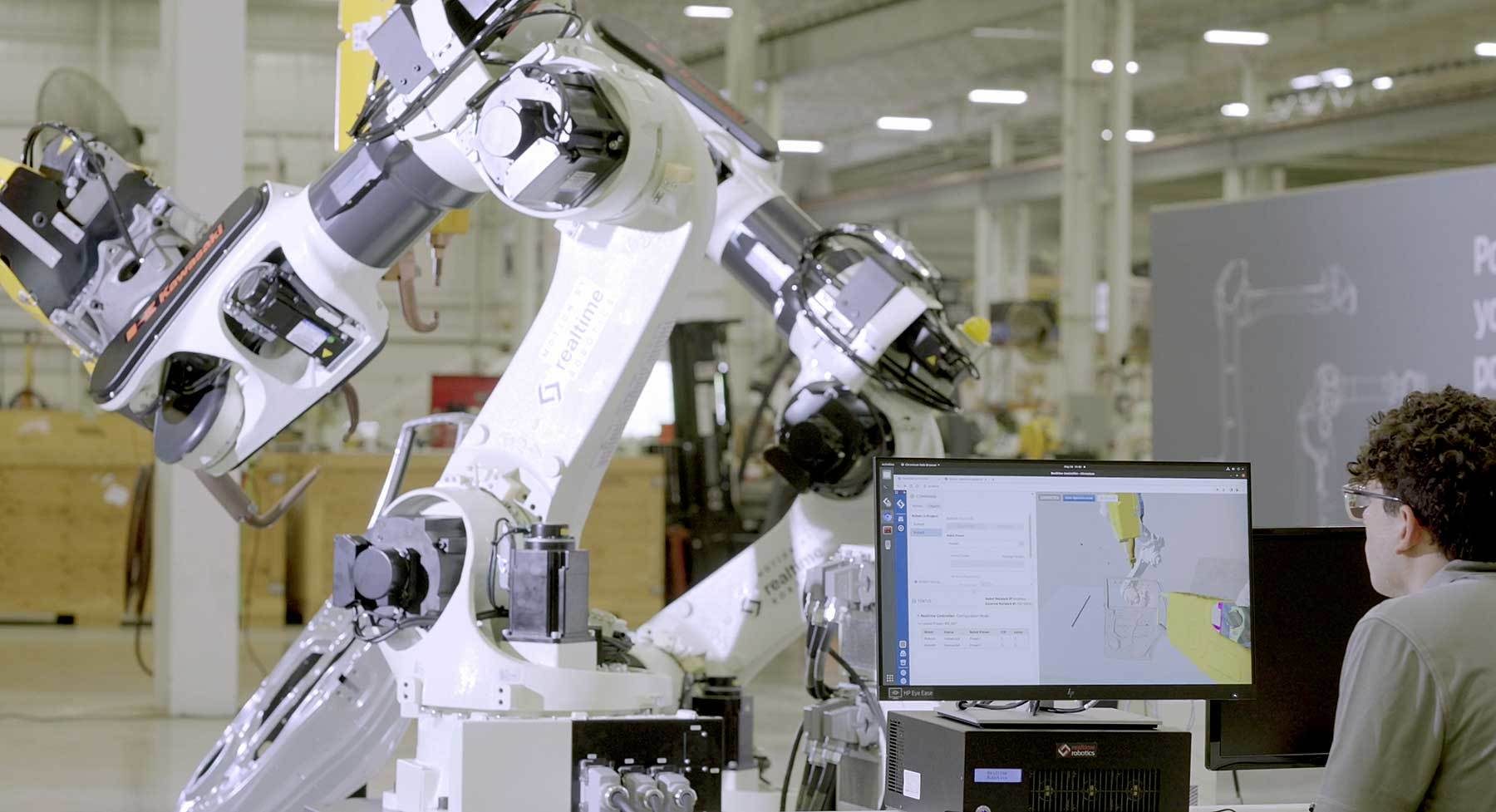
Although robots have been around for more than 50 years, vendor-agnostic software has only become available recently.
“It is mainly due to a shift in consumer behavior,” says Su. “Consumers are demanding more products and more customization. A higher number of product variations generally translates into a high-mix, low-volume manufacturing process. This leads to manufacturers needing to cope with a broader range of robotic [options] from different brands.
“Since the configuration of robotics solutions across other brands can be extremely expensive and take a long time, manufacturers prefer to use [alternative] software to address this pain point, allowing for the rise of third-party software,” explains Su.
“In the past, many companies were stymied by the complexity of traditional programming,” adds Benjamin Gibbs, CEO of Ready Robotics Corp., which has developed an open, cross-brand operating system for industrial automation called Forge/OS. With support for ABB, Epson, Fanuc, Kawasaki, Stäubli, Universal Robots (UR) and Yaskawa robots, it offers a single programming interface for hundreds of machines and peripherals.
“Today, open systems make it more cost-effective to use robots in high-mix production environments,” claims Gibbs. “Several developments have helped push this idea forward. One is the advent of Industry 4.0 technology, which has forced robot vendors to open up their platforms.
“Another was the debut of the robot operating system (ROS), an open-source system that was developed 15 years ago,” notes Gibbs. “However, ROS typically works better with automated guided vehicles and autonomous mobile robots rather than robot arms.
“In addition, the growing popularity of UR’s collaborative machines has helped spur new developments,” claims Gibbs. “It has led to a big increase in easier-to-use programming techniques.”
“Companies like UR have opened up their application programming interface (API) to allow third-party companies to develop directly onto their software,” adds Tyler Bouchard, CEO of Flexxbotics, which markets a cloud-based manufacturing management software platform that’s used by companies such as Abiomed, Boeing, Northrop Grumman, Sub-Zero and Toyota.
“They have created a robot company that sits on a platform,” says Bouchard. “The platform has accelerated innovation within robotics, giving manufacturers access to more application-based solutions.”
New Frontiers
Today, engineers are looking for tools to make robot programming easier and faster. Illustration courtesy TM Robotics (Americas) Inc.
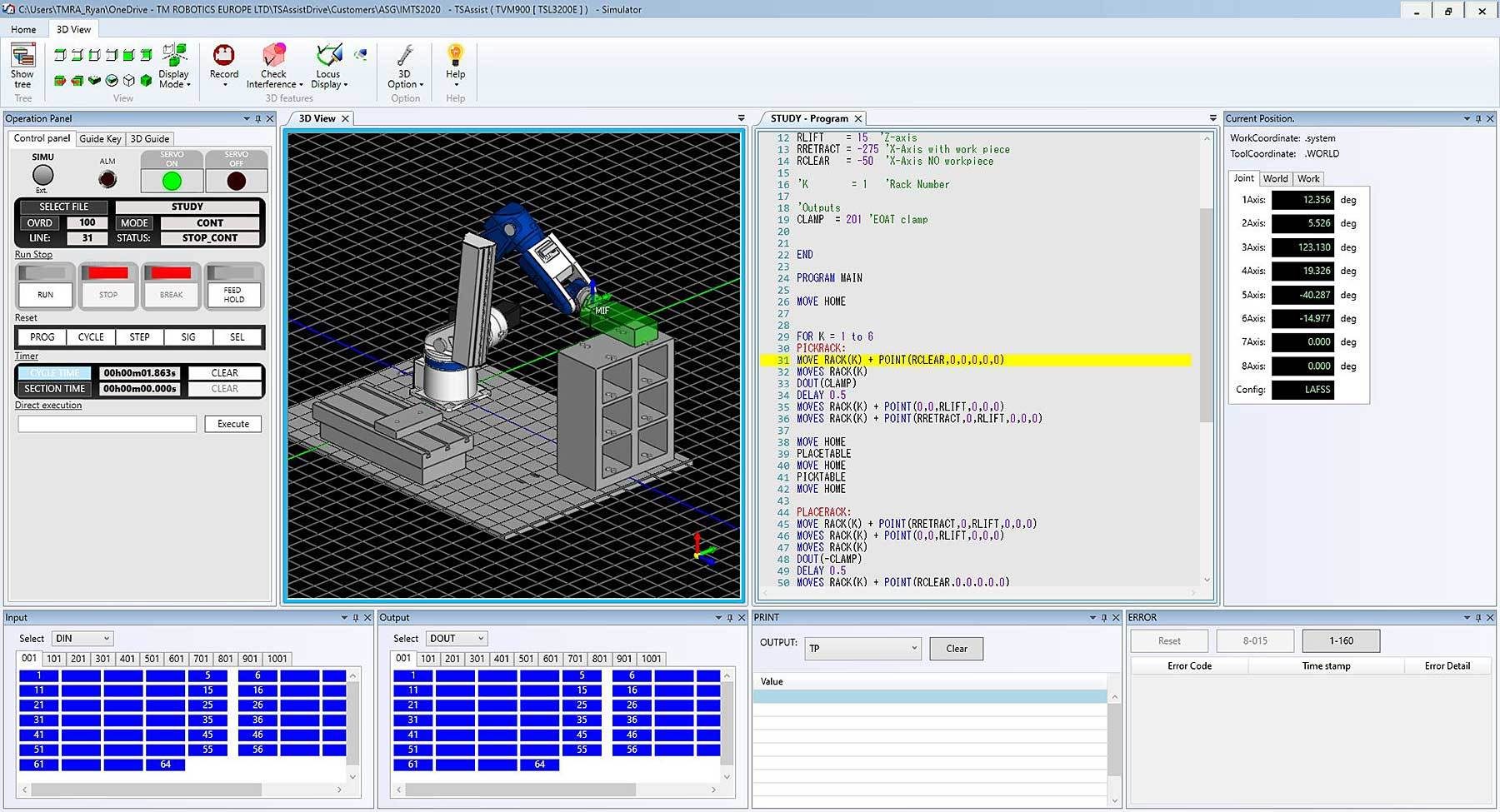
According to Realtime Robotics’ Konidaris, two other factors have contributed to the rise of third-party software. “One is increasing pressure to automate, coming from both the realization that the industry is nowhere near reaching its potential, and from price pressure,” he points out.
“The second reason is that new technology that has been brewing with robotics researchers for decades is finally reaching a level of maturity where it can be usefully applied in practice,” says Konidaris. “Third-party software will be a game-changer.”
The software generally has the following features that make it easy to use:
Intuitive robot programming and control.
Simple connection between the robot and controller.
Robotic movements in 3D simulation.
Digital twins that enable direct execution and monitoring.
Direct configuration with accessories, such as camera interfaces.
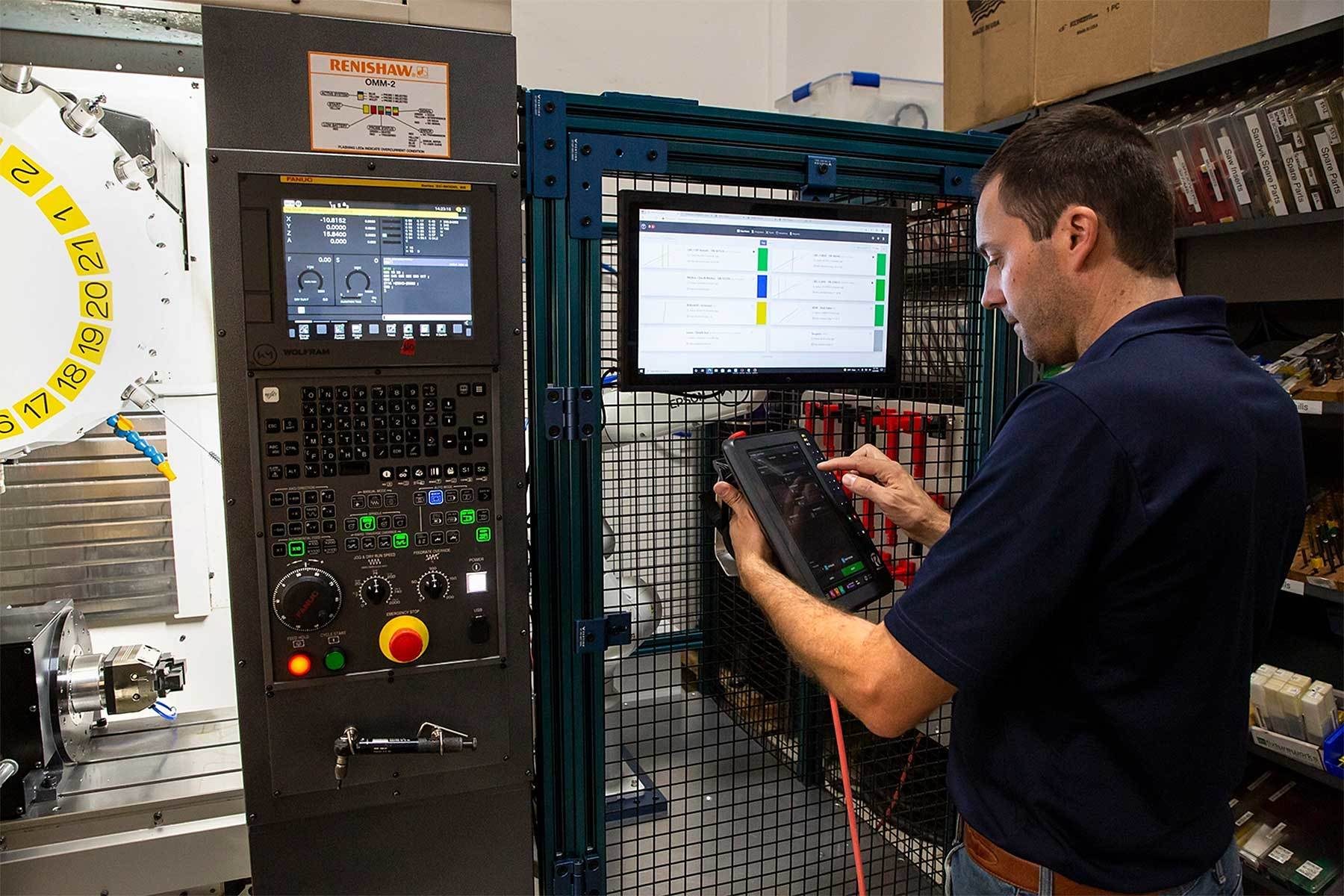
Manufacturing has been held back for decades by software silos between robot vendors. Photo courtesy Ready Robotics Corp.
“[Engineers today] are looking for tools to make programming easier,” says Ryan Guthrie, executive vice president of TM Robotics (Americas) Inc., the American and European distributor of Shibaura (formerly Toshiba) Machine robots. “There is less and less interest in having to script out code. Customers want precanned, packaged, plug-in, drag-and-drop tools.
“They don’t want to think about code at all,” notes Guthrie. “They want to be able to modify robot programs without having to even look at or understand the code.
“Most third-party apps that we have come across were developed to address specific needs,” adds Guthrie. “When a robot leaves the factory, we do not know if it is going to be packing chocolates, welding an auto body, gluing together battery cells for an electric vehicle, assembling electrical components or being used in a laboratory that is developing a cure for a disease.”
Robot manufacturers need to develop generic software that works for all these cases, and as such, they can’t possibly know what types of details or functions might be needed for specific applications.
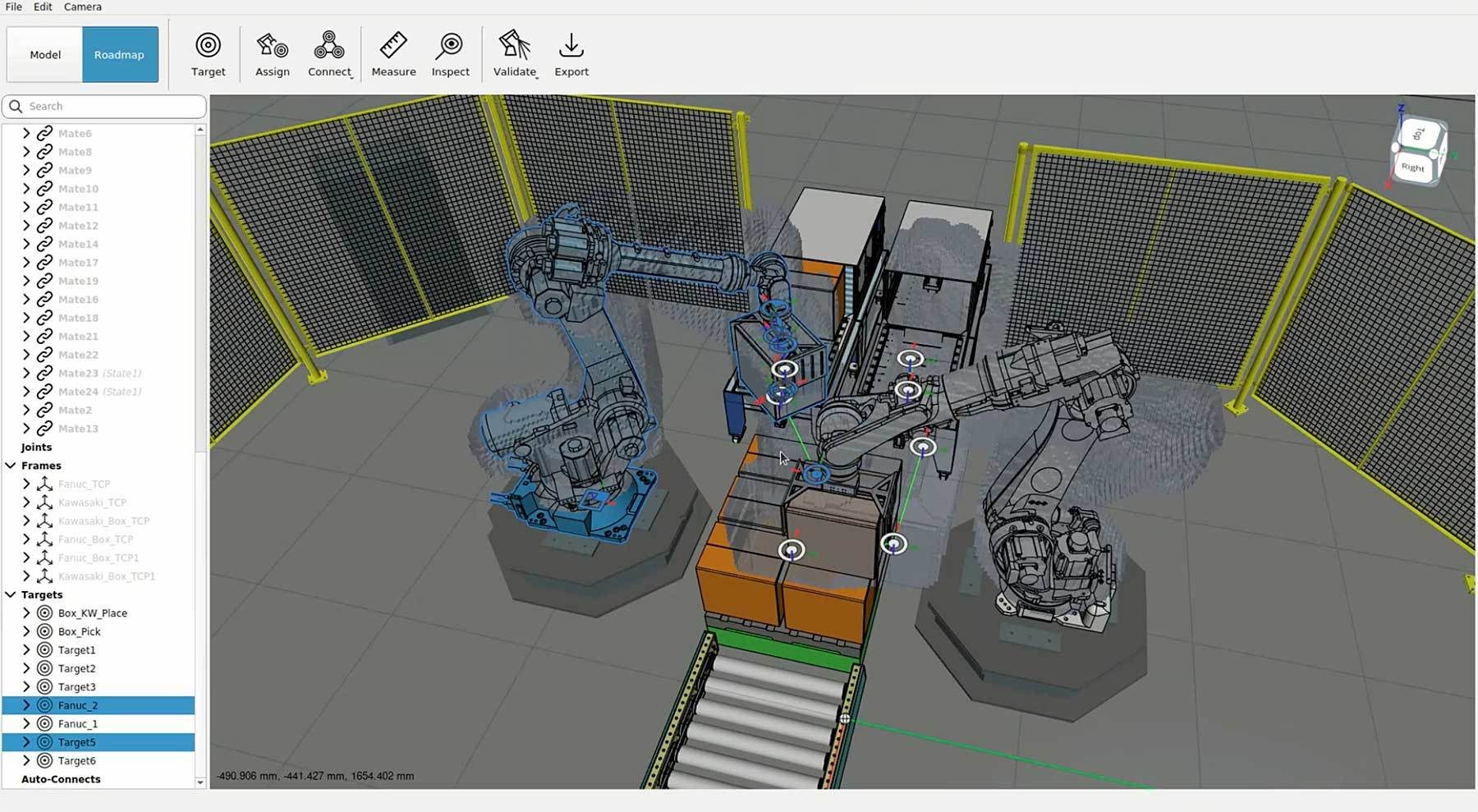
New software simplifies programming and speeds up deployment time. Illustration courtesy Realtime Robotics Corp.
However, third-party apps can be used to take the flexibility of the robot and really dial it in and tune it to the niche production task a specific end user may have in mind.
Guthrie says the push to make programming easier is not a new concept. “The idea of canned libraries and drag-and-drop code is something that has always been there,” he points out. “What is changing is processing power and the overall general knowledge of integrators.
“Things that are happing in the consumer space, which moves at a much faster development pace, are driving changes in the industrial [sector],” explains Guthrie, who has been programming robots for 15 years. “Software is becoming much more intuitive, with icon-driven menus and simplified interfaces. Most of the heavy lifting is now done with script that runs in the background without the user even knowing it is happening.”
In the future, artificial intelligence and data analytics technology will play an important role in programming software.
“AI is really changing the way programming is approached,” claims Guthrie. “As more and more data is fed into the logarithms that run AI, smarter [programs] will be developed.
“Just as vision systems have really changed how robots ‘see’ over the last decade, AI is going to change how robots ‘think,’” predicts Guthrie. “[However], we are still a long way out from machines that can think, react and grow on their own.”
“The future of programming is less ‘dealing with every low-level detail by hand because the robot is so stupid,’ and more ‘describing your industrial process and letting the robot figure it out,’” adds Realtime Robotics’ Konidaris.
“We are going to see a major leap in what can be cost-effectively and reliably automated when we raise the level of abstraction at which we have to think about robot programming,” says Konidaris. “What we’re doing right now is like trying to decide where to go for lunch by reasoning one footstep at a time, instead of picking a target restaurant. Someday very soon, all that low-level spatial reasoning will be the robot’s job.”
New Products
In the future, artificial intelligence and data analytics technology will play an important role in robot programming software. Photo courtesy Universal Robots USA Inc.
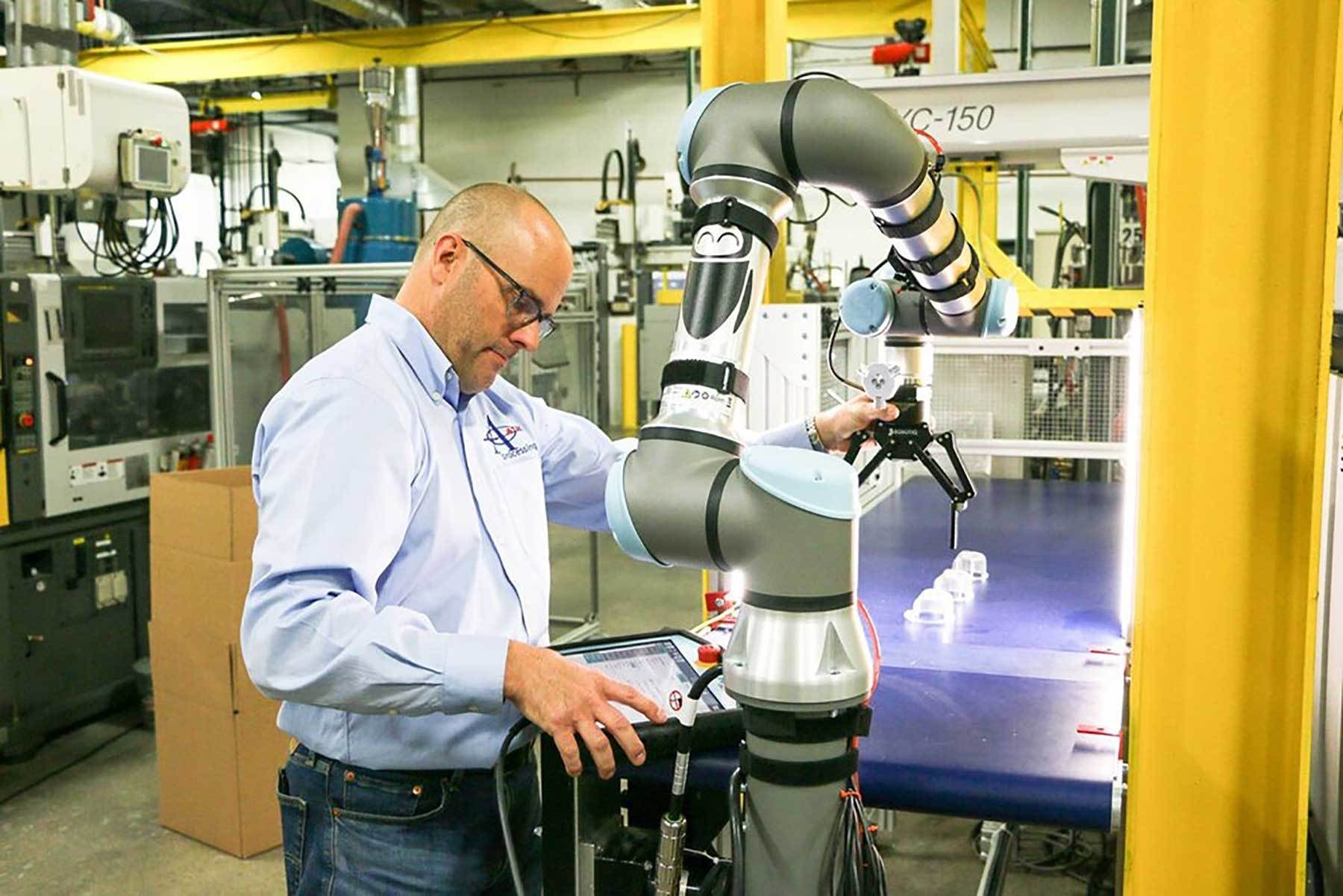
Manufacturing engineers can choose a variety of innovative software products that make it easier than ever to use robots for assembly applications.
For instance, Ready Robotics recently released Version 5.3 of Forge/OS. It unites all the hardware in a robotic workcell under a single user-friendly programming platform. In doing so, the operating system makes automation accessible to any manufacturer and any operator, with no experience necessary.
Forge/OS provides a hardware-agnostic software layer that controls robots and related automation hardware from leading brands through a common set of APIs. Using those APIs, Ready Robotics has built a suite of low-code apps designed to make it simple for non-engineers to program and manage robotic cells.
“Manufacturing has been held back for decades by software silos between robot vendors,” claims Gibbs. “We’ve broken down those barriers with a standard interface that simplifies deployment for enterprises and dramatically increases the market opportunity for the automation industry.
“For factory workers, that interface is a no-code tablet which allows them to upskill to become a robot programmer within weeks,” explains Gibbs. “For software developers, it’s a standard API that unlocks data streams from over 3 million compatible robots deployed today.”
Flexxbotics just launched FlexxConnect UR, a continuous improvement platform that empowers discrete manufacturers to easily manage their collaborative robots and maximize performance.
It provides instant access to contexualized data and intelligence, enabling engineers to fully optimize and continuously improve cobot performance. The platform also gives simple, step-by-step instructions that enable a quick transfer of ownership of cobot workcells to operators, upskilling the existing workforce.
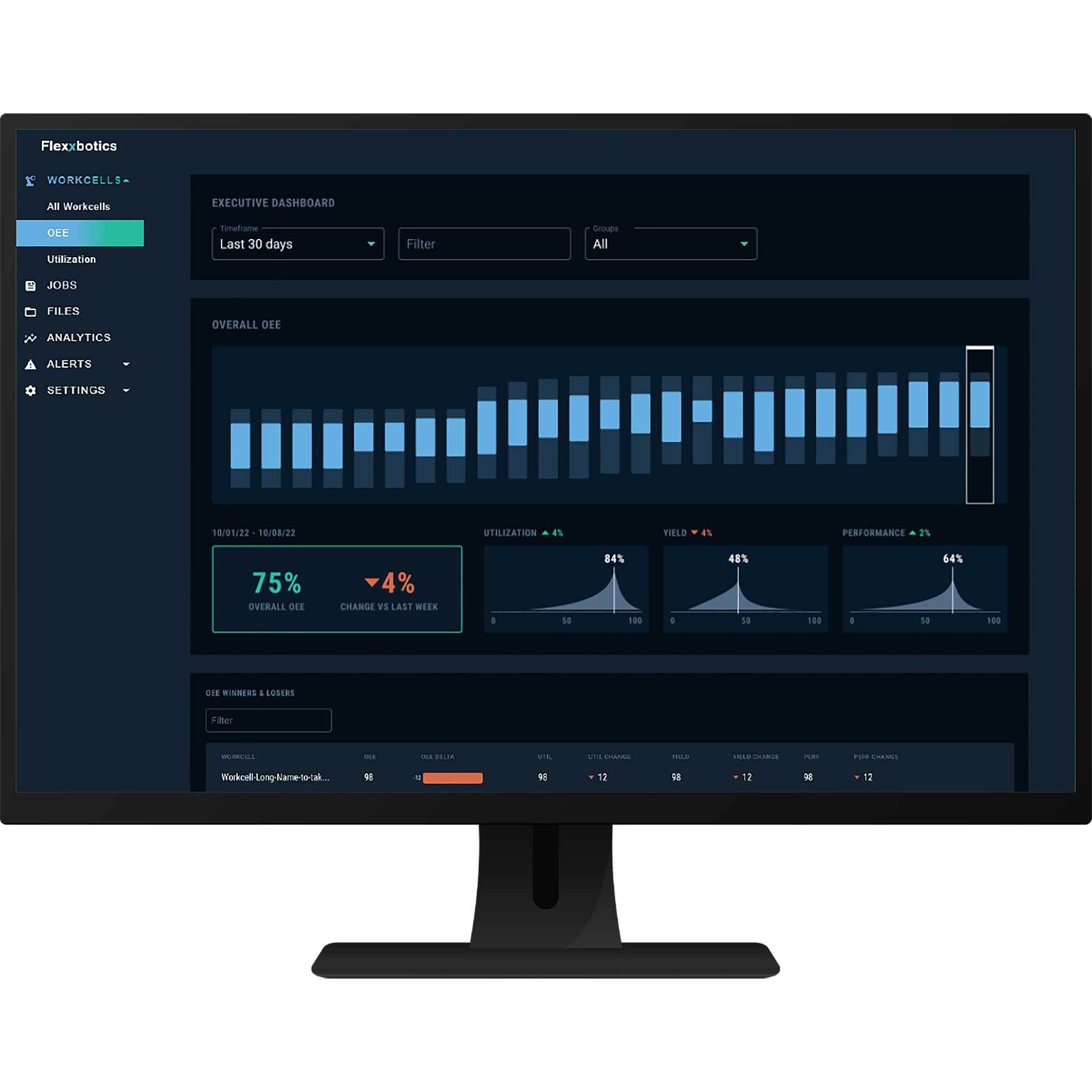
This continuous improvement platform enables manufacturers to easily manage their robots and maximize performance. Illustration courtesy Flexxbotics
“FlexxConnect enables the instantaneous transfer of both job intelligence and robot data digitally between the workcell and back office business systems,” says Bouchard. “The platform is revolutionizing the way jobs are being built, dispatched and executed. [It saves] manufacturers time, reduces changeover tasks and empowers the entire workforce to do more with less.
“Digital transformation can be a daunting task,” Bouchard points out. “We break it into pragmatic, digestible steps so manufacturers can trial different approaches to maximize their business outcomes.
“A robot’s life cycle can be split into three distinct buckets: design, deploy and operate,” explains Bouchard. “FlexxConnect focuses heavily on the operating portion, which is the longest aspect of a robot’s life cycle.”
Earlier this year, Realtime Robotics unveiled RapidPlan software, which simplifies programming and speeds up deployment time. It choreographs all robot movements and removes the need for brand-specific robot programming.
Cell modeling, task planning, programming and operations are all handled within the same workflow tool. The motions in simulation and as-built reality match, dramatically speeding up the design and deployment processes.
“Optimizing the efficiency of your factory operations should not be held back by technical barriers,” says Konidaris. “We specifically designed RapidPlan to deliver an accurate simulation of robot task planning, making it easy to program models and use them directly on the factory floor, but did so in a way that streamlined the process and made the technology easy-to-use for all.
“Our software functions as the basic physical intelligence that robots should have, but don’t,” explains Konidaris. “It allows robots to autonomously generate their own motion, rather than having to specify each and every movement by hand, at the individual joint level. The programmer simply tells the robot where its business-end needs to be and our software handles the rest. Each robot generates its own highly performant motion that never collides with the environment or any other robot.
“This unlocks immense value, because suddenly building a 12-robot workcell is just a matter of specifying goals for 12 robots,” claims Konidaris. “Existing technology is more like choreographing a 12-dancer ballet in a small, dark room. Our [system] makes development faster and easier.”
Editor’s note: This is the last of a three-part series about design for AM. Parts 1 and 2 explored the advantages additive manufacturing over traditional manufacturing processes, and the pitfalls to avoid to achieve the most successful outcomes.
ASSEMBLY ONLINE
For more information on additive manufacturing, visit www.assemblymag.com to read these articles: