
FACTORY OF THE FUTURE
Johannes Winter // Chief Strategy Officer // National Academy Of Science And Engineering // Munich, Germany
Manufacturers have made significant progress in digital transformation, but more work remains to be done.
Towards the Next Decade
of Industry 4.0
Photo courtesy EvilWata, Creatas Video+ / Getty Images Plus
Jon Sprovieri // Chief Editor
Highly automated smart factories are no longer a pie in the sky concept.
Smart Factories:
Here and Now
Photo courtesy Traitov, iStock / Getty Images Plus

Ten years ago, in Germany, researchers from computer science, engineering, economics and other disciplines, as well as representatives from industry and the service sector, presented a concept for the future of industrial value creation and customer-specific mass production that resonated globally. That concept became known as Industry 4.0.
Since then, manufacturers have made significant progress in digital transformation.
But, more work remains to be done. There are three areas in particular where more progress is needed: sovereignty and resilience of value networks, open-source technology, and the strategic combination of digitalization and sustainability.
SOVEREIGNTY
DataSpace Industrie 4.0 is an initiative for a sovereign European industrial data ecosystem. Photo courtesy National Academy of Science and Engineering
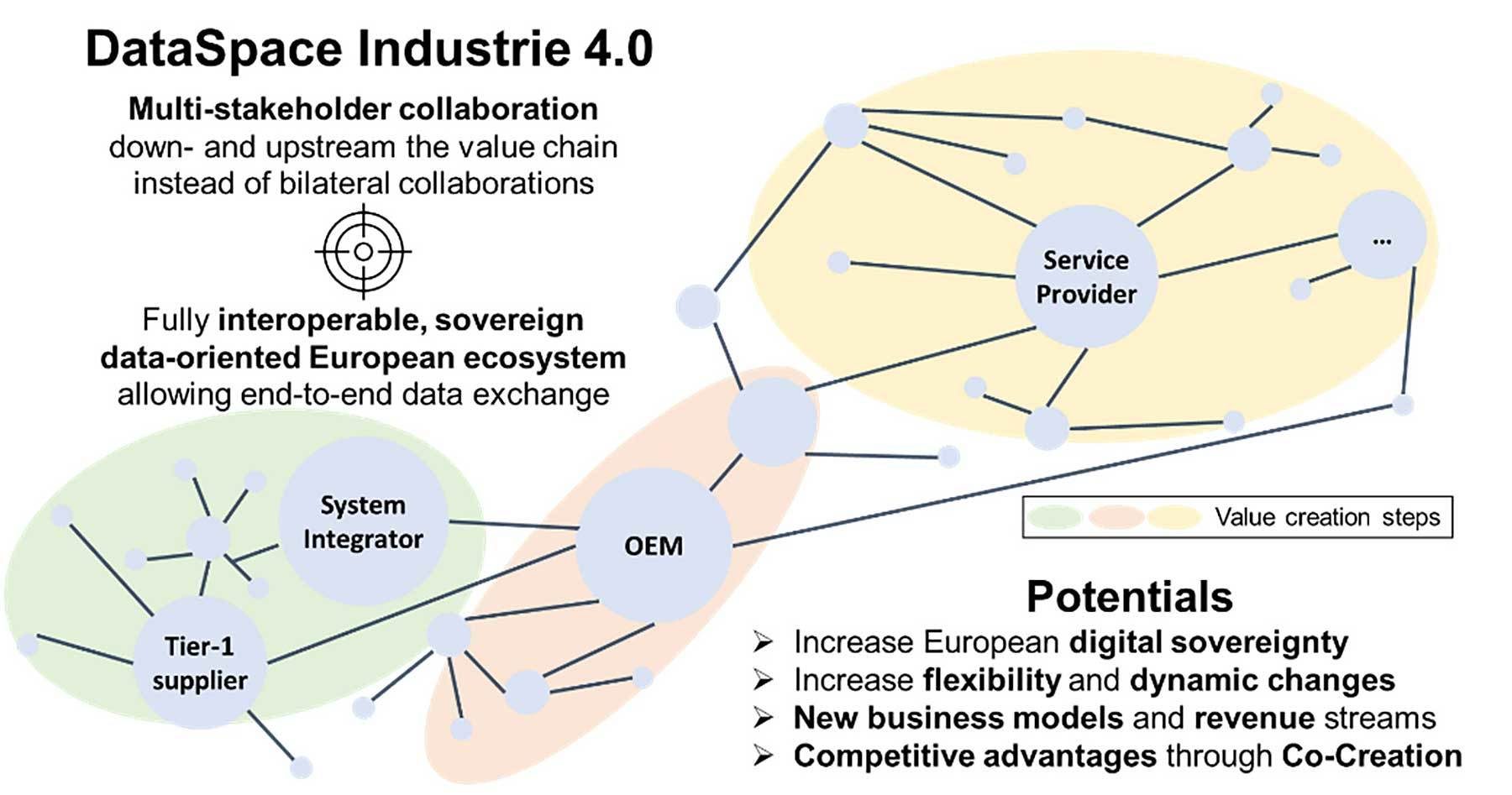
Globalization has increased interdependencies in global value chains. For example, Germany, like most countries, is highly dependent on raw materials, predominantly from the Far East.
The digitalization of industry has created new dependencies, predominantly from the U.S., where most of the technology companies delivering services for industry, such as Microsoft, Amazon and Oracle, are located. Under the presidency of Donald J. Trump, the U.S. gradually turned away from Europe as its primary geostrategic and economic partner. Even though it might have been a temporary phenomenon, it highlighted the importance of technological sovereignty for the EU and Germany in terms of economic policy. This has been recognized by policymakers, who now emphasize the importance of economic sovereignty in general and Industry 4.0 in particular. Whereas technological sovereignty demands government action to ensure independence on a macroeconomic level, on a microeconomic level, individual companies need to operationalize this strategic directive by becoming more resilient.
The resilience of value networks requires specific attention. As in the U.S., the COVID-19 pandemic unveiled the dependency of German industry on global value chains. The Russian invasion in Ukraine has led to shortages of semiconductors and cable harnesses, and it has caused oil and electricity price explosions. German industrial companies have not been resilient in the face of these crises. To increase the resilience of its value networks, German industry must become more robust and agile. Three measures can help: adoption of value creation networks; safe and secure data integration; and reliance on Industry 4.0 technologies.
The paradigm of single sourcing coupled with just-in-time delivery caused a production standstill during the COVID-19 pandemic. German industry still depends on global value chains. Indeed, 43 percent of Germany’s net exports are only generated because it is embedded in global value chains. This dependency must be reduced.
A short-term cure is to rethink the just-in-time paradigm and maintain larger inventories. In addition, manufacturers need to diversify their supply base. In the event of a catastrophe—for example, in the event of economic lock-down measures in one production country—manufacturers can quickly switch production to other countries. This will mitigate supply-side risk, but it will lead to higher costs.
A medium-term approach is a local-for-local strategy: locating production and the upstream value chain in the sales market. By synchronizing supply- and demand-oriented risks in sales markets, only the respective regional clusters are affected in the event of a disaster. This mitigates the risk of supply chain disruptions. At the same time, resources are duplicated to a much greater extent, causing efficiency losses. This may provide more resilience, but it will be unable to counter increasing uncertainty and pressure for change in the market environment.
Smart farming services as an example of the potential for synergy between digital transformation and sustainability initiatives. Photo courtesy National Academy of Science and Engineering
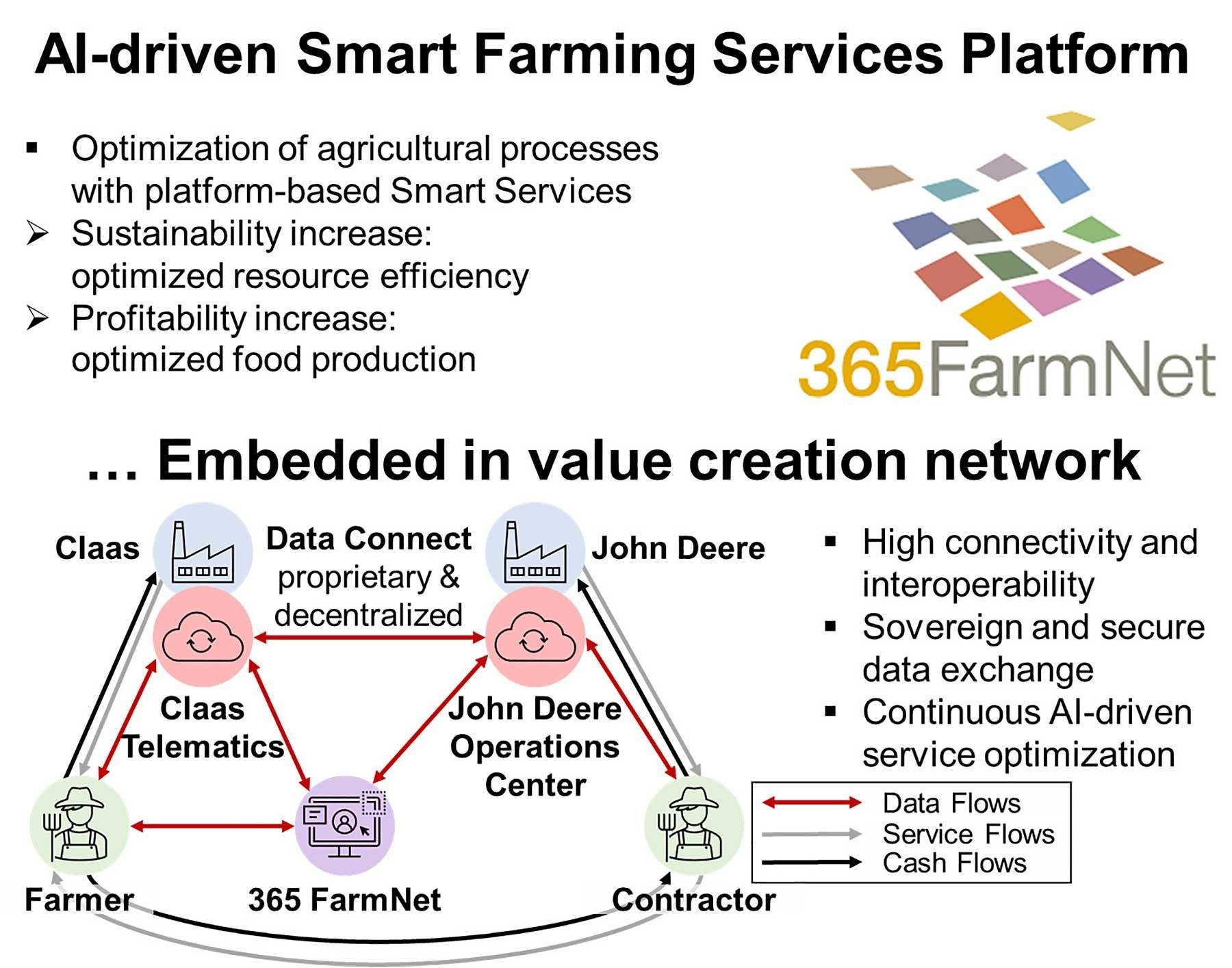
In the long run, the monolithic and highly optimized value chains of the present could be gradually replaced by resilient and adaptive value creation networks—multiple sourcing based on regional local-for-local strategies; the creation of redundancies to allow for flexible reaction to crises; and a diversification and continuous evaluation of the supplier base as part of risk and sustainability management.
Based on the paradigm of co-creation, value creation networks require data infrastructure that allows companies to collaborate seamlessly to develop and strengthen resilient business models that, on a macroeconomic level, promise to increase digital sovereignty. The German Platform Industry 4.0 drives such an attempt with its European Data Space Industry 4.0, building a data infrastructure for companies from German industry and the information and communications technology (ICT) sector.
These data spaces increase digital sovereignty as well as data sovereignty, enabling the secure, decentralized and self-determined exchange, collection, analysis and sharing of data. They form the basis for new, highly scalable, data-driven, and platform-based business models—one of the focus points in the next decade of Industry 4.0.
Next to the establishment of value creation networks, data integration is a prerequisite for a resilient Industry 4.0. Our analysis indicates that this is currently not achieved in practice. Small- and medium-sized enterprises, in particular, face problems with data management. They require support and an innovative data ecosystem. Data integration requires platforms where standardized data exchange can be enabled. Real-time monitoring of procurement, logistics, production and sales processes allows for optimization of processes. This data could also be integrated into data exchange platforms and could train self-learning AI models for an industrywide optimization of production.
Industrywide implementation of Industry 4.0 technologies is key. Software-based risk management is required for resilient and adaptive value creation. Big data analytics and AI are the basic technologies for reaching the paradigm of the smart factory. Digital twins require industrywide penetration. Only if industry applies these technologies can it future-proof for the next decade of Industry 4.0.
INTEROPERABILITY
Globalization has increased interdependencies in global value chains. Photo courtesy Continental AG
Achieving the goal of AI-driven smart factories and platform-based business models will requires the establishment of an innovative ecosystem where companies and customers interact seamlessly. To reduce transaction costs, interoperability will be key. In the first 10 years of Industry 4.0, significant initiatives were started. The GAIA-X project aims at developing a safe and interconnected data infrastructure for a European digital ecosystem, with industry sitting at its heart establishing guidelines and a standard architecture framework contributing to cross-sector interoperability. Industry-specific interoperability has also been improved by the launch of RAMI 4.0 as an international industry-specific standardization and reference architecture for Industry 4.0; the coordination of the standardization of Industry 4.0 by the Standardization Council Industry 4.0; the establishment of OPC UA as a standard for interoperable interfaces for AI-driven production; and the launch of the administration asset shell.
For the next decade of Industry 4.0, open-source software (OSS) will play a pivotal role in implementing new platform-based business models. Already at the beginning of the 2020s, OSS contributes €65 billion to €95 billion to the EU’s GDP, and it promises significant growth opportunities in the future, especially for Industry 4.0. OSS could even be applied to enhance interoperability, as demonstrated by BaSyx-middleware.
Currently, economywide motivations for participating in OSS mainly lie in the need to find technical solutions, avoid vendor lock-in—a factor that is also relevant for technological sovereignty—and build knowledge in high-quality coding. At the same time, as OSS builds on voluntary contributors, its cost–benefit ratio is a highly promising driver for value creation. For every euro invested, a €12 value creation is achieved. This is a significant lever, especially for SMEs in the industry, given the cost pressures they are facing.
A short-term cure is to supply chain disruptions is to rethink the just-in-time paradigm and maintain larger inventories. Photo courtesy MTU Aero Engines
However, to exploit this lever across the breadth of the manufacturing sector, further advancements for OSS from a technological, regulatory and innovation perspective are required. Within companies, OSS must be integrated as an elementary step in value creation. This begins with the development and the communication of an open-source strategy developed by an interdisciplinary team creating acceptance and support in the workforce. It should be embedded in a top-level vision and strategy, which could imply the application of open-source to create standards, to boost business model strategies, or to gain competencies in core technologies.
Establishment of an Open-Source Program Office (OSPO) should boost implementation. As the central business unit responsible for open source processes, the OSPO would be responsible for quality management, checking license compatibilities and OSS integrity with intellectual property, and qualifying employees to develop OSS. Senior management needs to ensure the establishment of an open-source mindset in the workforce and create communities for open-source development.
Additionally, OSS must be crosschecked continuously. It is recommended that OSS should only be developed for non-IP-relevant products, processes or code. It should not be attached to the primary value proposition of a company. If the latter did occur, a company would cannibalize its market position. This indicates the need for continuous adaptation of and reflection on business models.
In industrial policy, open-source has played an important role. However, European governments have taken a more laissez-faire approach, and today, the EU is on the back foot when it comes to capabilities in this area. As a result, the public sector should establish OSPOs, publicly fund R&D projects related to open-source more intensively, support entrepreneurial activities around OSS, and build a European ecosystem around OSS.
SUSTAINABILITY
To become more resilient, many manufacturers are adopting a local-for-local strategy: locating production and the upstream value chain in the sales market. Photo courtesy Haier Home Appliances
The need for sustainable manufacturing is more important than ever in view of global socioeconomic inequality and the climate crisis. German industry is the second biggest producer of greenhouse gas (GHG) emissions beyond the energy sector. Thus, the German government has set ambitious goals to reduce the ecological footprint of the industrial sector. GHG neutrality should be achieved by 2045.
Industry 4.0 can play a key role in meeting this goal. The smart factory promises to reduce emissions and increase energy efficiency by optimizing resource consumption. However, rebound effects, such as overproduction and overconsumption caused by a more efficient smart factory, could increase the ecological footprint of German industry. The same holds for AI. According to a recent analysis, AI contributes positively to 139 of 169 indicators of the United Nations’ Sustainable Development Goals (UN SDGs), but it adversely affects 59 of those indicators.
To exploit the positive effects of ICT while mitigating its negative effects on sustainability, a strategic combination of digitalization and sustainability is required to create win-win scenarios for the economy, ecology and society. “Digitainability,” a strategic perspective on Industry 4.0 based on circular economies and sustainable business models, should be the goal.
A sustainability strategy for Industry 4.0 would consist of five stages: status and stakeholder assessment, sustainability target setting, impact check, adoption of technological strategy, and implementation and continuation.
Data integration is a prerequisite for a resilient Industry 4.0. Photo courtesy Claas Tractor
In the first stage, status and stakeholder assessment, manufacturers would evaluate the current value chain, conduct stakeholder analyses, and assess the impact of ICT on a company’s sustainability. This will identify the critical areas that require attention in sustainability management.
Step 2, sustainability target setting, includes operationalizing a company’s sustainability vision in measurable dimensions. These dimensions include economic, ecological and social sustainability.
Step 3, impact check, assesses where action is needed in the creation and design of products, services or processes in the company, and how measures need to be designed so that they contribute to these sustainability targets. The UN SDGs are a good reference point in this regard.
Step 4, adoption, is the merging of the sustainability strategy with the digitalization strategy. Here, companies apply ICT only in those areas where they are creating benefits. They need to assess how their products, processes or services can be optimized, and how new sustainable business models based on AI and other ICT could be developed.
In step 5, implementation and continuation, it is important to create a “digitainability” mindset within an industrial company. This includes employee-related measures regarding the use of digital technologies in the company and the permanent integration of the company’s individual sustainability goals into the company organization.
Strategically merging sustainability and Industry 4.0 offers potential for companies to create new and resilient value creation networks or to even design sustainable platform-based business models that promise to increase and solidify revenue streams.
If companies become that innovative, it will create market opportunities for German and European industry to position itself as a market leader regarding sustainable services and products. Given a sufficient level of interoperability, such an ecosystem would promise to strengthen the sovereignty of German and European industry.
ASSEMBLY ONLINE
For more information on Industry 4.0, visit www.assemblymag.com to read these articles:
Cybersecurity for the Factory of the Future
Measuring the Value of Digital Transformation
FACTORY OF THE FUTURE NOVEMBER 2022
