
FACTORY OF THE FUTURE
Jon Donner // General Manager
Fabrica Group, Nano Dimension // Waltham, MA
For the first time, additive manufacturing can rival the tolerances that can be achieved via micro molding.
Micro Additive
Manufacturing
Fabrica 2.0 builds additively in 1.5 micron layers and can produce parts with a 1-micron resolution. Photo courtesy Nano Dimension

Working at the vanguard of micro additive manufacturing (AM) for so many years, I have had time reflect about the role this technology will play in the future of precision manufacturing.
AM has been a disruptive technology ever since it came onto the scene nearly 30 years ago. First, it disrupted the prototyping stage of product development. Then, it disrupted manufacturing itself. AM is now a production technology that in many situations is a cost-effective and speedy alternative to legacy manufacturing processes. At the same time, it is stimulating development of geometrically complex and innovative parts, and it has become an enabler of mass customization.
Until recently, however, AM has struggled to find a foothold with precision or micro manufacturing. This was due to an inherent lack of precision in industrial AM processes that could only be overcome by prohibitively expensive and extremely slow platforms. Given the industrywide drive towards miniaturization of parts, the need for a viable, cost-effective and fast micro-AM process was obvious. This was the impetus behind the development of our Fabrica 2.0 precision micro AM technology.
Through this technology, manufacturers can now reimagine how they produce precision micro parts and components. Fabrica 2.0 has changed the economics of manufacturing in numerous industry sectors worldwide.
BENEFITS OF MICRO AM
Two materials are used in micro AM. Precision N-800 is like ABS, combining strength and flexibility. Precision N-900 is a reinforced composite material. Photo courtesy Nano Dimension
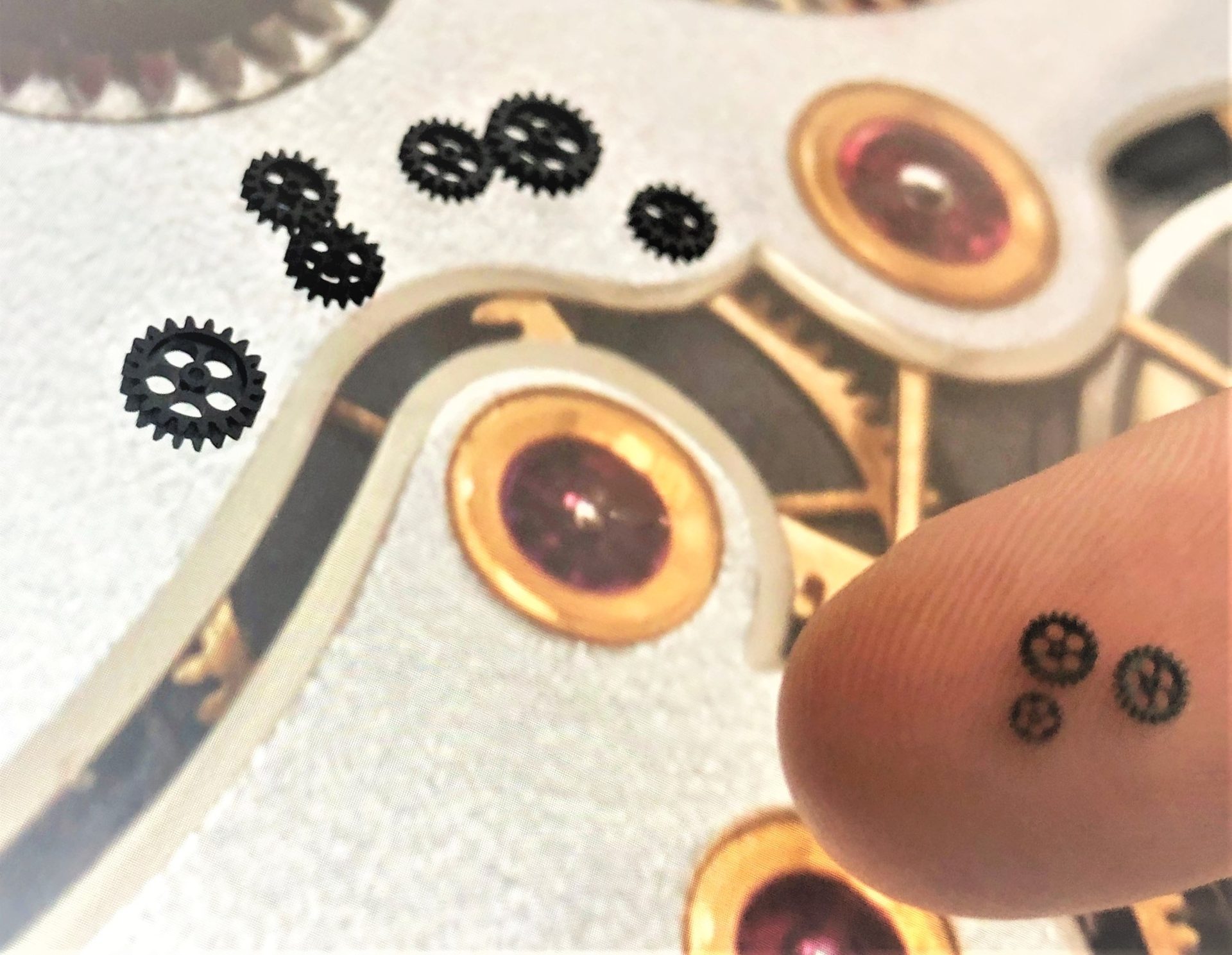
For the first time, AM can rival the tolerances that can be achieved via micro molding. This level of precision in AM brings additional benefits, all of which combine to reduce prototyping and product development time for micro parts or micro molds. Fabrica 2.0 builds additively in 1.5 micron layers and can produce parts with a 1-micron resolution. As a result, the path to creating innovative miniature parts quickly and cost-effectively is open to all industry sectors.
There is a limit to the ability to create complicated parts using traditional micro tooling. With increased complexity comes increased cost, but not when using Fabrica 2.0 micro AM technology. Without the need for a physical tool, design engineers can think out of the box and attain design goals that were previously unimaginable. Because AM is relatively agnostic to part complexity, engineers can design and manufacture unique geometries. As such, Fabrica 2.0 can be true stimulator of innovation, allowing engineers to design parts and features that were previously impossible to produce.
AM also has no set up costs. The time needed to acquire the tooling for traditional manufacturing processes can delay time to market. It also makes such processes uneconomic for small- or medium-sized production runs. With AM technologies, small- and medium-sized runs are cost-effective. Indeed, it’s the sweet spot for the technology.
Success with Fabrica 2.0 is measured in microns and hours. Micron-level detail can be achieved without the need to fabricate tools. This means that you can have intricate and geometrically complex prototypes in a matter of hours.
Finally, AM allows for mass customization and personalization. And, manufacturers can use the same platform for prototyping, small batches and mass production.
HOW IT WORKS
MultiVu used micro AM to make this tiny part for a digital camera. Photo courtesy Nano Dimension
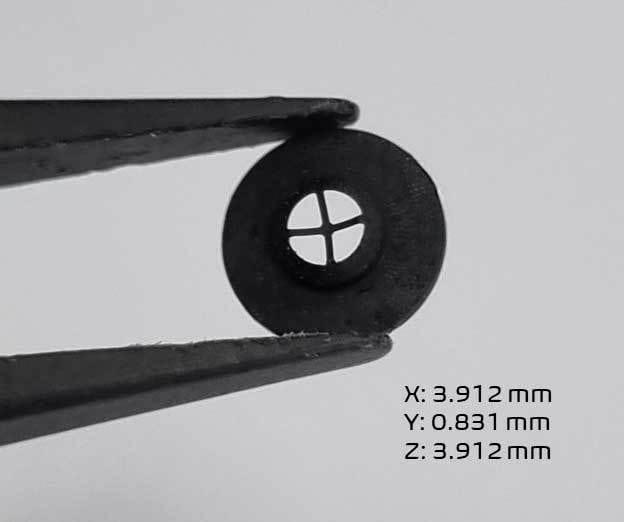
The Fabrica 2.0 combines the Digital Light Processor (DLP) engine with the use of adaptive optics. In conjunction with an array of sensors, this allows for a closed feedback loop, which enables the attainment of micron-level accuracy while remaining cost-effective as a manufacturing technology. Adaptive optics have been used in other areas of technology, but this is the first time that they have been applied to AM.
In terms of software, Fabrica 2.0 has a multi-resolution strategy, meaning that areas where fine details are required are printed relatively slowly, but areas where the details aren’t so exacting, the part is printed at speeds 10 to 100 times faster. The technology also uses an algorithm family that focuses on file preparation, optimizing parameters, such as print angle, build plate and supports.
Much work has been done on materials development, as well. Two key materials we use are Precision N-800 and Precision N-900. N-800 is like ABS, combining strength and flexibility. It is ideal for structural applications across various industries, such as electronics, optics, automotive and aerospace. N-900 is a reinforced composite material. It can be used to make parts that are nearly 100 percent ceramic at a resolution of 1 micron. It resists high temperatures and can be used for outdoor applications. It also offers high wear resistance for longevity for enhanced performance in mechanical assemblies.
MICRO AM DELIVERS PERFECT FIT FOR CAMERA COMPANY
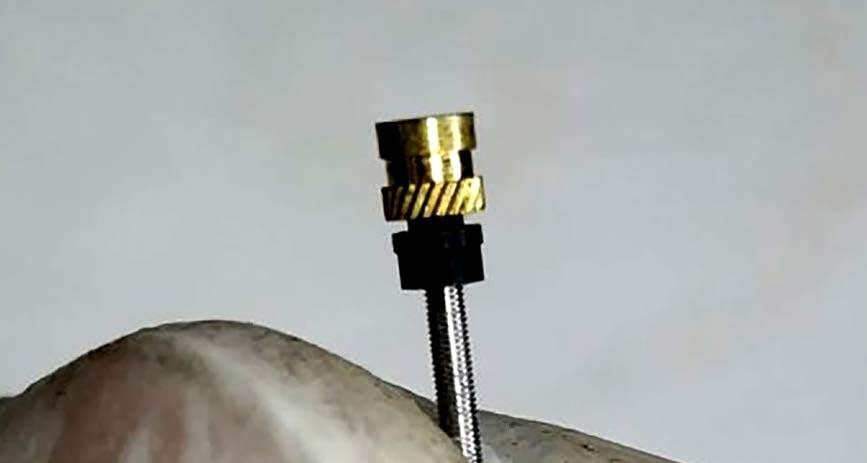
Medical device startup AntiShock used micro AM to make small parts for this electro-optical sensing device. Photo courtesy Nano Dimension
MultiVu is a unique Israeli start-up that is developing next-generation 3D imaging cameras. MultiVu’s technology is based on three elements: a proprietary lens design, a unique optical filter, and deep-learning algorithms. The company’s first product is a compact, single-sensor camera that can be used in mobile phones, medical devices, automotive applications and security applications. MultiVu customizes the camera for each application.
When the company was working on its first fully functional prototype, the R&D team had to find a way to manufacture a variety of small parts. One of those parts was a plastic element that is assembled between lenses. The part must fit perfectly with the lenses to enable full functionality of the camera.
One option was to make the part using conventional AM technologies. But, they could meet the technical requirements of the part. This was also the case for CNC machining. A third option was to produce the part using a small mold. However, the costs would have been very high, since several molds would be needed to make the different designs to be tested. Molding would be more relevant when the time came for mass production.
Micro AM technology from Nano Dimension solved the problem. Engineers at MultiVu were initially skeptical about the process. They questioned the ability of any 3D printer to produce such a small part, in the right material, with the right mechanical properties, and with the required precision and geometry.
After examining the CAD file of the part, Avi Cohen, vice president of the Nano Dimension’s Fabrica Group, accepted the challenge. It took several attempts and a small adjustment in the design, but a first part was produced in just a few days. Intrigued and amazed at how fast the first part was delivered, the MultiVu team assembled the part with the other elements of the camera. The first tests showed there was an 85 percent fit of the part to the lenses.
With digital manufacturing, additional adjustments in the design were simple. It took an additional three iterations to get the final part and to conduct another lab test, but the result was a perfect fit.
In this case, the biggest advantage of micro AM was that no other manufacturing technology could produce the part. This enabled MultiVu to pass an important hurdle in the development phase of its prototype.
The second advantage was that micro AM could make such a small part for less than $50, in a functional material, with the required details, accuracy and geometry, and in a very short time frame.
Finally, micro AM allows MultiVu’s to stay flexible when developing future products. Each camera prototype will be assembled from different parts, and no other manufacturing technology could support such a development process.
For more information on micro AM, visit www.nano-di.com.
ASSEMBLY ONLINE
For more information on additive manufacturing, visit www.assemblymag.com to read these articles:
Additive Manufacturing: The Quest for Automation
Five Things: Additive Manufacturing
Additive Manufacturing Helps Boom Supersonic Produce Complex Parts
FACTORY OF THE FUTURE NOVEMBER 2022
