
FACTORY OF THE FUTURE
Seog-Chan Oh, Ph.D. // Staff Researcher // Manufacturing Systems Research Lab // General Motors Co. // Warren, Mi
Automakers don’t need conveyors to transport vehicles on assembly lines—the vehicles can move themselves.
Conveyor-Less Micro Factories
for Urban Car Production
GM already uses automated guided vehicles to transport large subassemblies on the line. Photo courtesy General Motors Co.

The current paradigm of car manufacturing, which provides a variety of models, colors and options, is called mass customization. However, mass customization is now transforming into mass individualization. In mass individualization, products are uniquely catered to consumers’ desires. For example, some car buyers may want to replace ordinary car seats with luxury brands, such as Louis Vuitton, to differentiate themselves.
The advent of autonomous electric vehicles (AEVs) could accelerate this trend. An AEV does not require a driver to operate the vehicle. As a result, it creates space and time for the driver and passengers to do activities other than driving. The car can be an office for those who are busy with work or a rest area for those who need a break. If the vehicle becomes an extension of the home or office, it is no longer an option, but a necessity, to customize its interior just like an office or a house.
However, it will be difficult to mass produce personalized vehicles with a manufacturing process and value chain designed for high-volume, low-mix production.
The automobile manufacturing value chain consists of a press shop, body shop, paint shop and assembly. The assembly process is different from other processes in terms of automation. The level of automation in press shops, body shops and paint shops is usually very high. Many are nearly 100 percent automated. However, final assembly is difficult to automate due to the complexity of the tasks and diversity of the parts.
A sensor skid, temporarily attached under an EV, can guide the vehicle through the assembly process based on local sensing and communication with a high-level fleet management system. Photo courtesy General Motors Co.
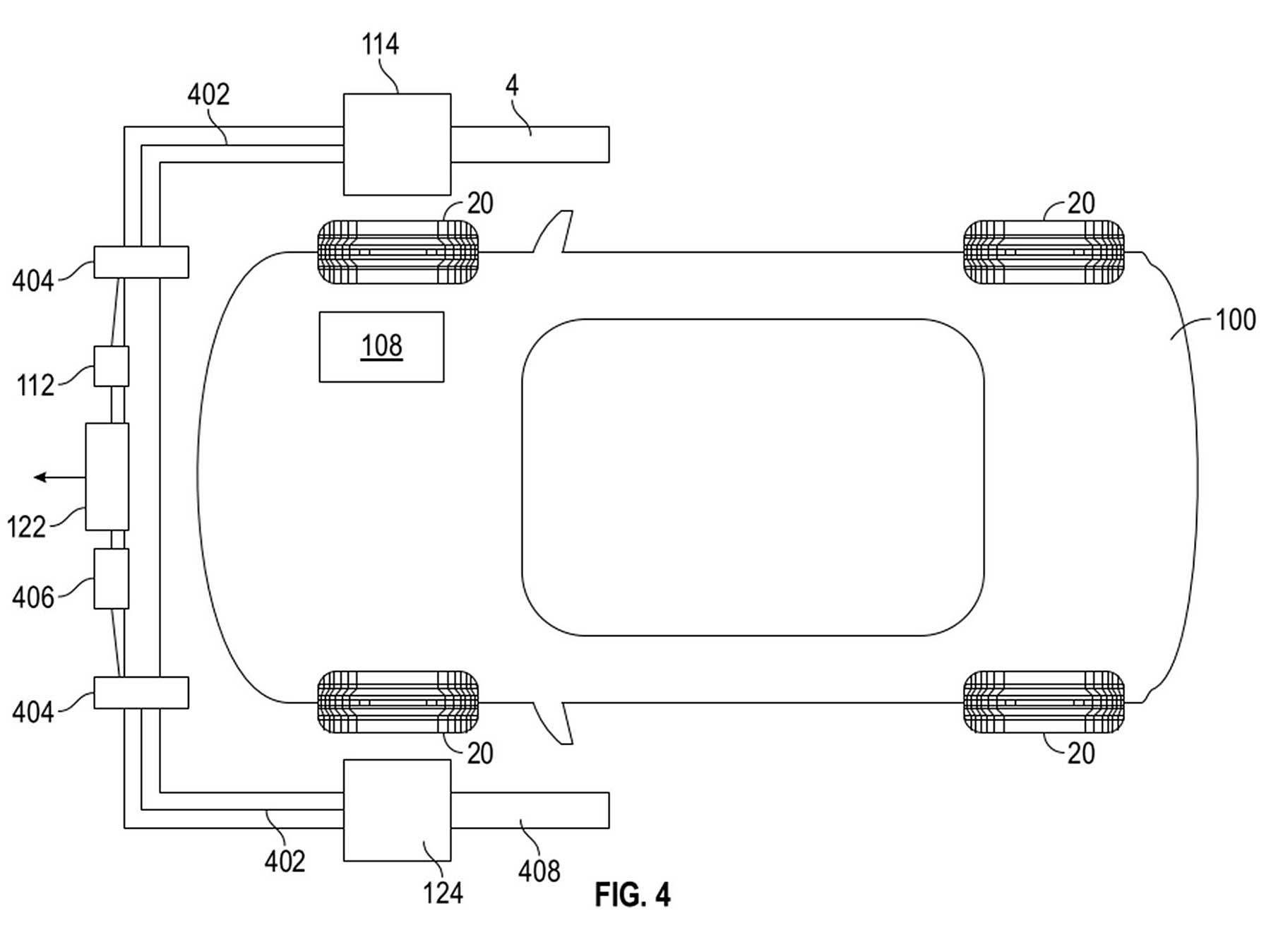
An ergonomic positioning device could be actuated by one or more wheels of the vehicle without a need for external power. It would consist of two rollers, a belt and a passive motion device. When a wheel of the vehicle is interlocked between the two rollers, the wheel can drive the belt, actuating a passive motion device, which moves the vehicle up or down. Photo courtesy General Motors Co.
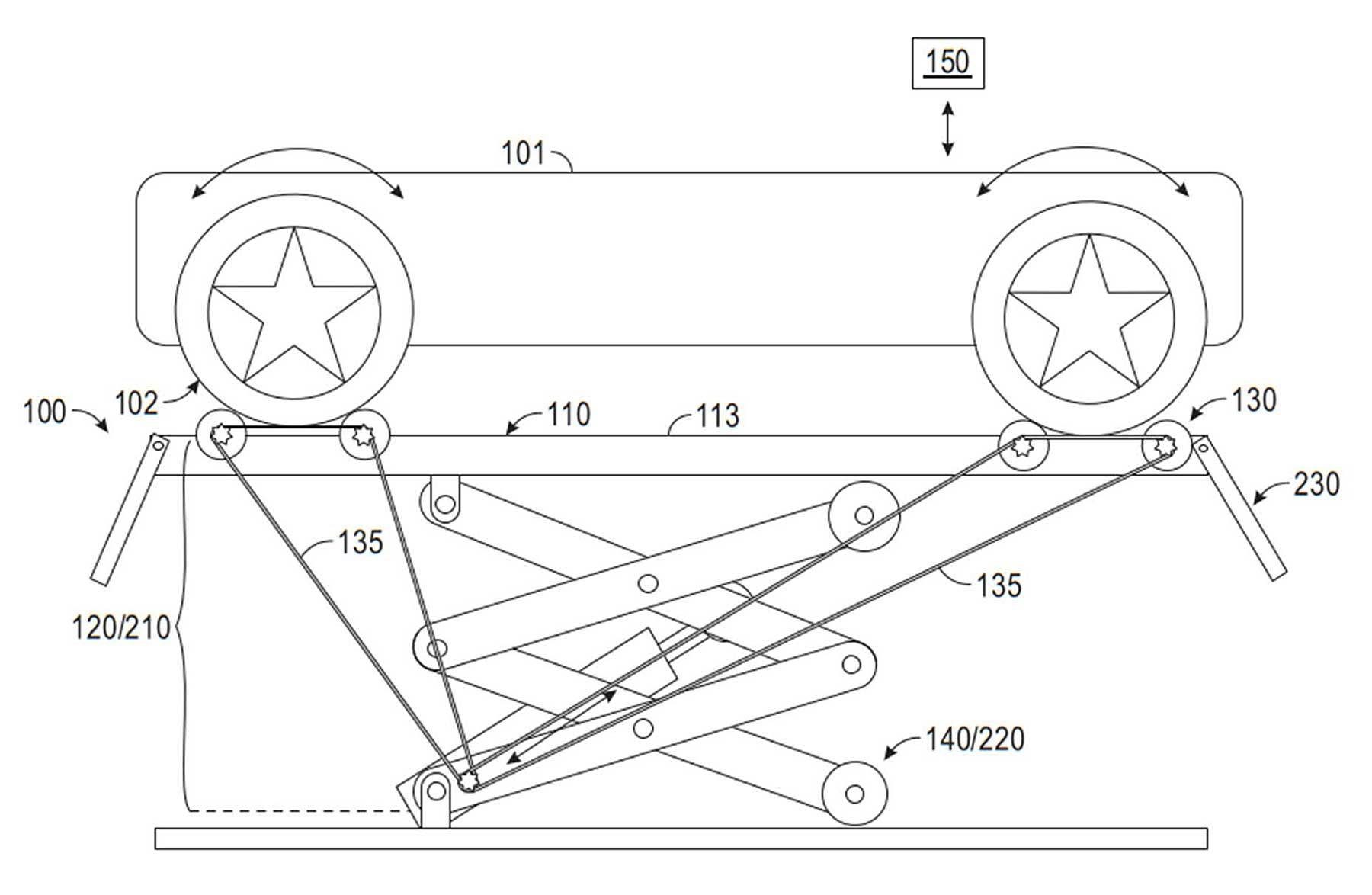
Using an autonomous mobile robot to transport vehicles on the assembly line—or using the vehicle itself—gives OEMs more flexibility in factory layout. Photo courtesy General Motors Co.
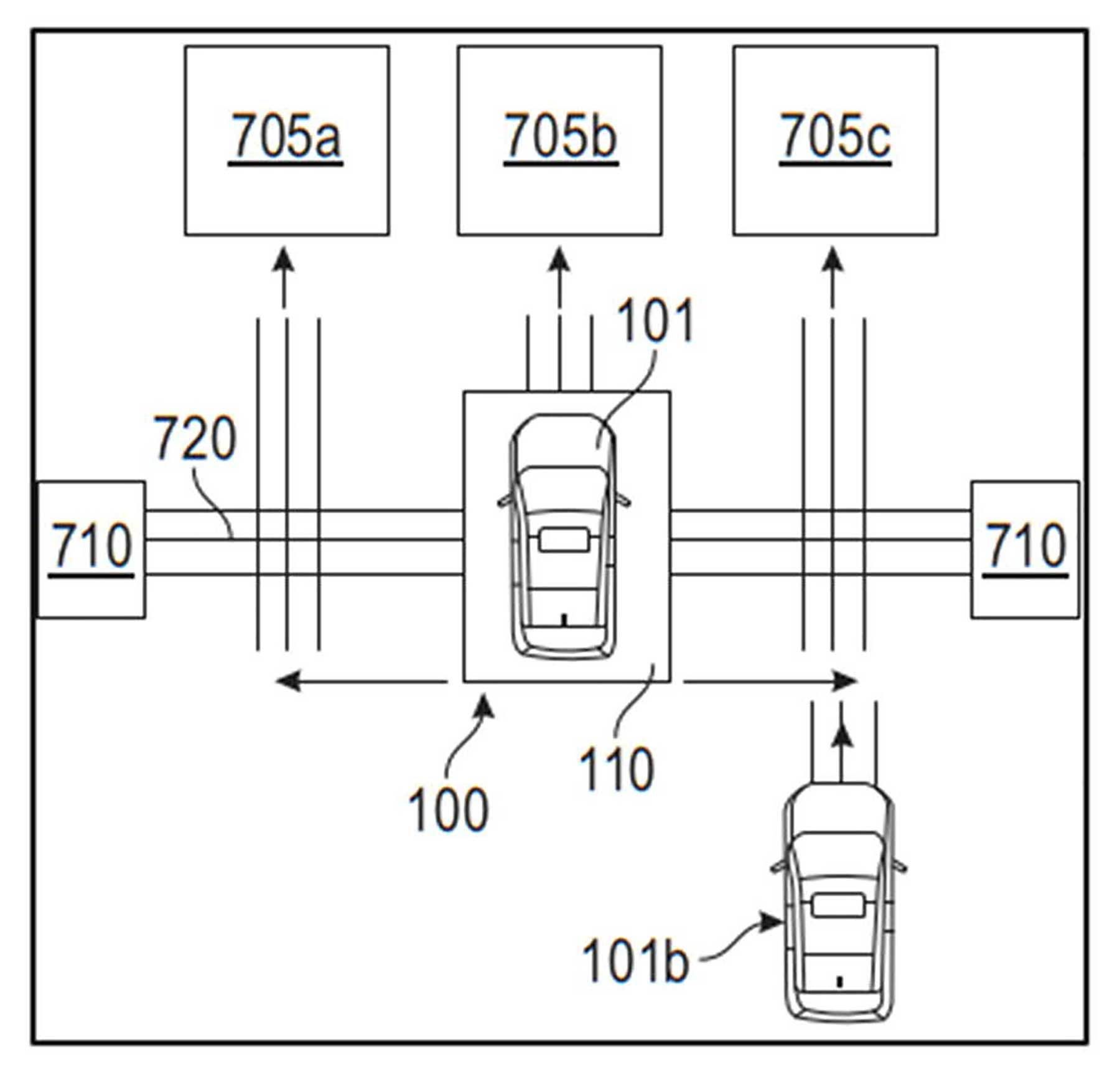
One way to achieve mass individualization while maintaining various automation levels is to decouple final assembly from the value chain. The press shop, body shop and paint shop would continue as mass production centers in central locations, while final assembly would be carried out in separate micro factories located in urban areas. The assembly process does not need to be physically located with the other manufacturing processes. Instead, it can be moved to an urban area where the labor supply is elastic. Low-volume, high-mix production can be realized with this model.
However, one obstacle to establishing an assembly plant in a city is the limitation on building size. It can be difficult to secure a large empty space to install conveyor lines. Such lines are essential for traditional automotive assembly plants designed for low-mix, high-volume production. But, in urban assembly plants, such lines will become inflexible and expensive monuments. For mass individualization, urban assembly plants must adopt asynchronous production systems. They must be designed for maximum flexibility and minimal capital investment.
A conveyor-less design solves that problem. Better still, it’s a perfect fit for EV assembly, because the number of components required for EVs is much less compared with gas-powered vehicles.
CURRENT EXAMPLES
GM uses autonomous forklifts to store and retrieve parts at its factory in Grand Rapids, MI. Photo courtesy General Motors Co.
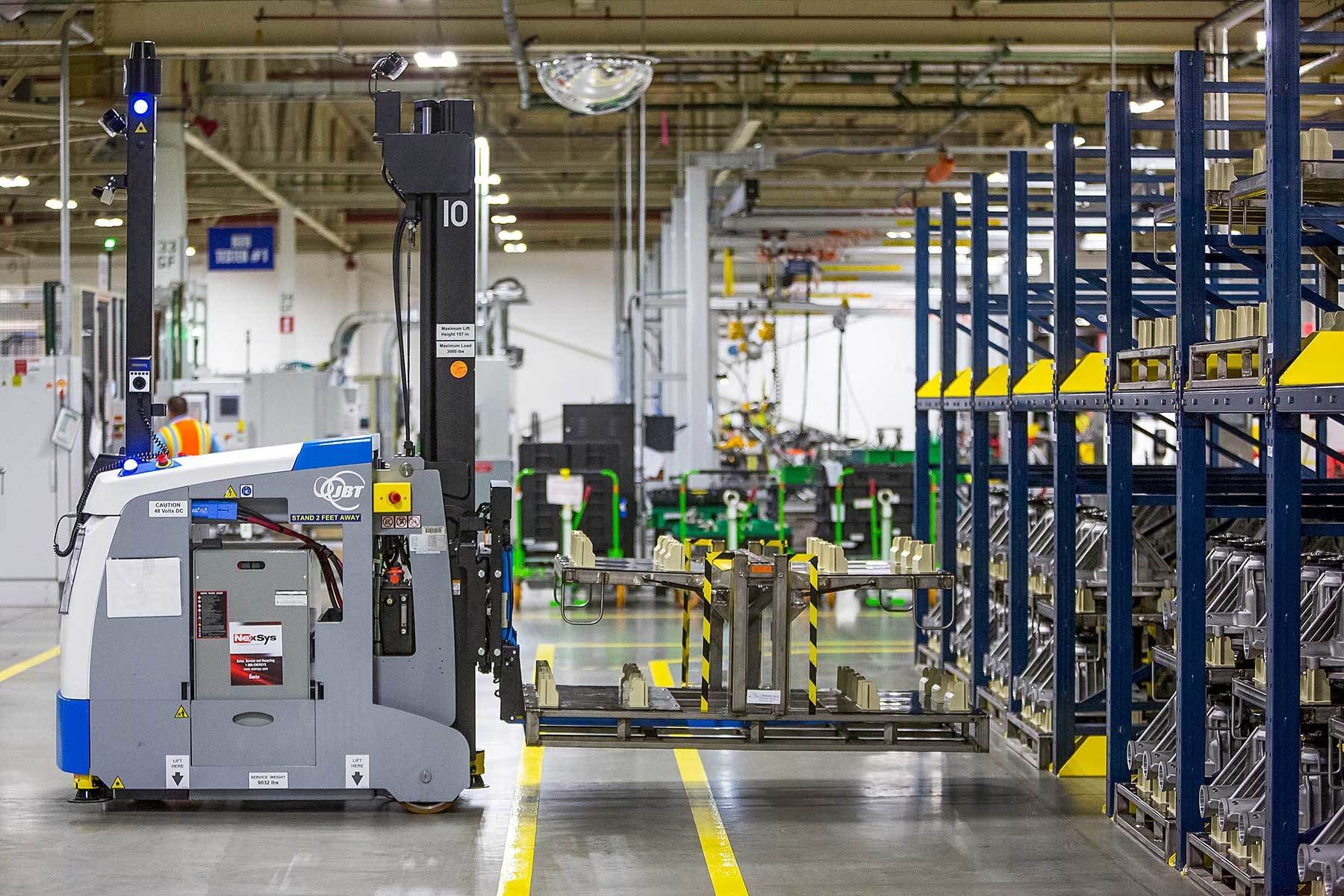
Automotive assembly plants have been built in urban areas since the industry’s birth. However, a notable change in recent years is the urbanization of EV production. Several examples come to mind.
The first is the micro factory that Arrival, the U.K. EV startup, built in Rock Hill, SC, in 2021. Arrival aims to make electric buses and vans as inexpensive as possible. Aluminum is used instead of steel for the frame. Body panels are made from proprietary composite materials. Without the need for hundreds of acres of land and specially purposed buildings, the micro factory was built in an existing empty warehouse space in about six months. The factory does not have expensive metal-stamping presses, welding or paint shops, and fixed conveyor lines. Instead, a flat skateboard chassis is assembled from extruded aluminum parts. Body panels are bonded with aerospace-grade adhesives. And, finishing is performed by dying the composite material or wrapping the vehicle. AGVs transport components instead of conveyor lines.
Another example is e.GO Mobile’s EV assembly plant in Aachen, Germany. Founded in 2015, e.GO started at RWTH Aachen University in Aachen. This plant maximizes the advantages of urban infrastructure without violating the environmental standards of the residential area. For instance, emission-related adjustments and noise insulation measures have been adopted to mitigate the impact of the factory on local residents. Inbound and outbound logistics are set up in such a way as to divert the traffic from adjacent residential areas.
A third example is Volkswagen’s assembly plant in Dresden, Germany. The factory was built in 2001 with a glass structure that allows people to see inside. Initially, more than 17,000 citizens signed a petition against the factory construction because of expected exhaust emissions and inbound and outbound trucks. However, the factory eventually got the green light after VW adopted the innovative idea of using the public tram infrastructure, called CarGoTram, to deliver materials and products. The plant now produces 72 e-Golfs per day in two shifts.
One more urban car factory that is expected to attract the attention of the industry is the Singapore Hyundai Mobility Global Innovation Center. Scheduled to open in the second half of 2022, the smart factory is said to have been designed to connect people, nature and technology.
VEHICLE AS A CONVEYOR
E.GO Mobile’s assembly plant in Aachen, Germany maximizes the advantages of urban infrastructure without violating the environmental standards of the residential area. Photo courtesy e.GO Mobile
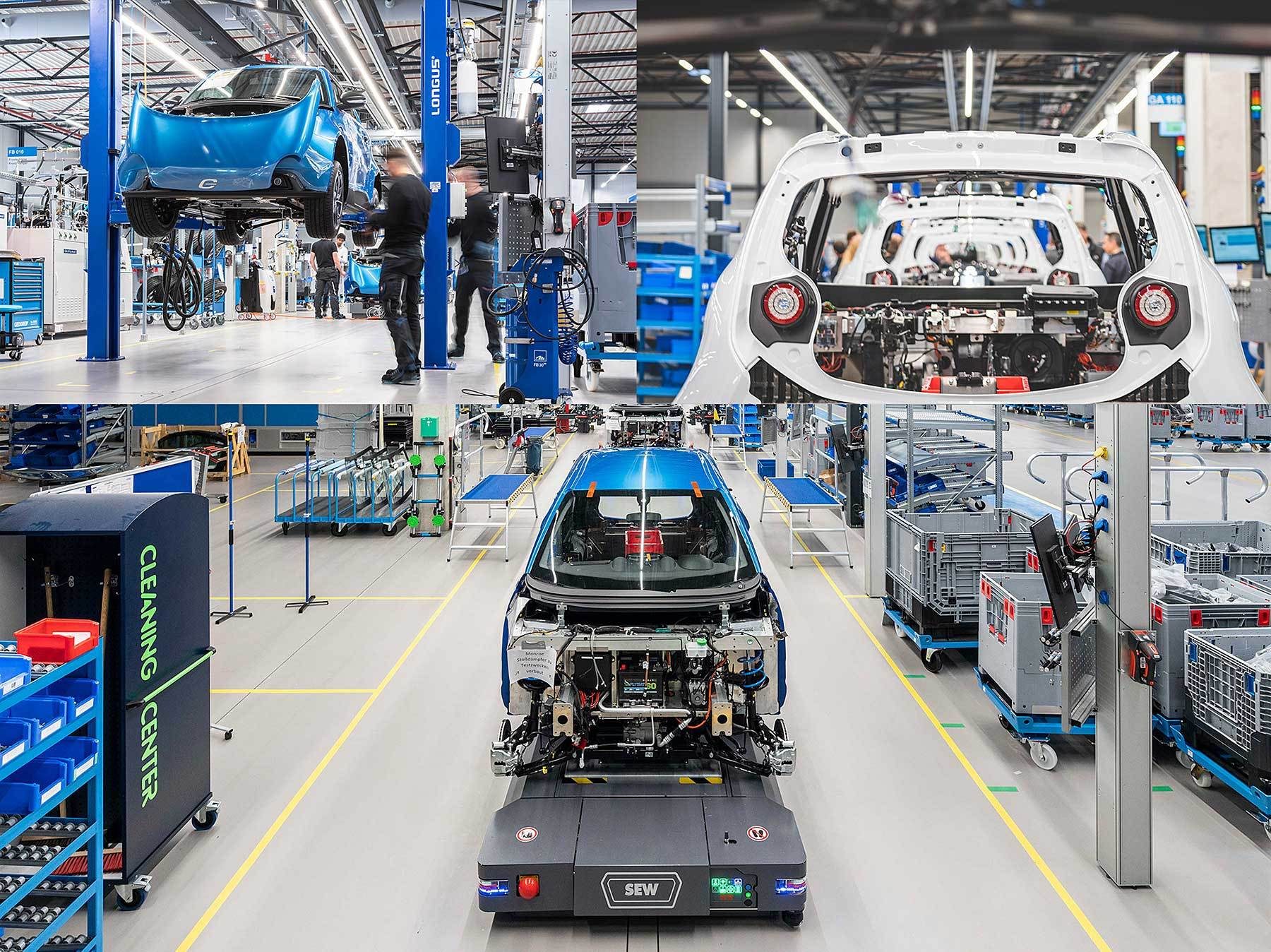
An urban automotive assembly plant should be designed for maximum flexibility, minimal capital investment and asynchronous production. That points away conveyors and favors autonomous transport technologies. Two options are available: autonomous mobile robots (AMR) and VaaC.
AMRs are vehicles that are equipped with on-board sensors to autonomously move vehicles or materials along predefined paths without the need for magnetic tapes on the floor.
In VaaC, the EV guides itself through the assembly process. A sensor skid, temporarily attached under the EV, guides the EV based on local sensing and communication with a high-level fleet management system. The skid is designed to be easily removed at the end of the assembly. The skid body has a set of pins that temporarily engage with locating holes in the underbody. The skid is equipped with numerous sensors that detect objects around the EV.
As an alternative to the sensor skid, a safety-sensor guidance system can be used. The guidance system is mounted to the chassis and temporarily takes control of the vehicle’s control system. In essence, the EV becomes an autonomous vehicle. The guidance system includes a sensor, a transceiver and an emergency stop device. The sensor detects intrusion into a predetermined zone. The range is dictated by standards for safety-rated sensing and stopping distances. The guidance system also includes a path projector, which projects a visible beam forward from the vehicle. In some cases, the guidance system might have multiple sensors at one or more corners of the chassis. Each sensor can be configured to sense in a three-dimensional volume, so that the volumes overlap to create a buffer zone around the chassis.
Another technology that will enable conveyor-less assembly systems is vehicle-powered positioning devices. In a typical car plant, special equipment is used to lift or tilt vehicles to optimize working positions for assemblers. However, such equipment requires a significant amount of electrical power and is not easily reconfigured. Instead, it would be desirable to use a vehicle-powered device to position the vehicle. Such a device would not require an external power supply, and it would also save space.
The positioning device would be actuated by one or more wheels of the vehicle without a need for external power. It would consist of two rollers, a belt and a passive motion device. Instead of a belt, the device may include other mechanisms, such as a chain, drive shaft or hydraulics. When a wheel of the vehicle is positioned and interlocked between the two rollers, the movement of the wheel drives the belt, actuating the passive motion device, which lifts the vehicle up or down.
In the near future, we can imagine a scenario in which the car factory, per se, ceases to exist and is combined with car dealerships. Using the VaaC concept and a skateboard-type car design platform, a micro factory could be built in the warehouse of a car dealership. Then, vehicle components—the skateboard, the body components, the seats, glass, console, etc.—are shipped from suppliers directly to the dealer. The dealer assembles vehicles and delivers them to customers through an order-to-delivery system. We can call this a point-of-sale factory, which is one possible practical scenario of using our proposed technology.
ASSEMBLY ONLINE
For more information on automotive assembly plants, visit www.assemblymag.com to read these articles:
Automation Helps Lotus Zoom Ahead
Aptera to Use AGVs to Assemble Solar Cars
FACTORY OF THE FUTURE NOVEMBER 2022
