
FACTORY OF THE FUTURE
Sangchul Han, Ph.D. // Professor Of Robotics // Korea Institute Of Industrial Technology // Ansan, Korea
Researchers have developed a single end-of-arm tool that can simultaneously hold a part in place and install it at the same time.
Screwdriving Gripper Mimics
Two-Handed Assembly
Photo courtesy EvilWata, Creatas Video+ / Getty Images Plus

To automate an assembly task that requires two hands, engineers have two options: one robot equipped with a tool changer or two robots. Now, there may soon a third option. We have developed a single end-of-arm tool that can simultaneously hold a part, such as a dowel or a long screw, in place and install it at the same time.
Furniture assembly is a good example of an application that could benefit from such an end-effector. Consider the process of assembling a typical chair from IKEA. Many steps involve holding one part, such as a leg, while inserting another part, such as a peg or a screw. It would be considerably inefficient to automate each assembly step using multiple robots.
Standard two- or three-finger grippers lack the degrees of freedom or the control to perform all three tasks—picking up a screw, holding in place, and driving it.
Several studies have looked at using an anthropomorphic gripper for such tasks. Because they have a joint configuration similar to that of the human hand, these grippers have a high degree of freedom and versatility. One study showed that such a gripper could be used to turn a hex key—as long as the tool was already engaged with the fastener. The gripper could not perform the entire screwdriving process.
We devised a robotic screwdriving gripper that mimics two-handed assembly by a person.
DESIGN OF THE ROBOTIC SCREWDRIVING END-EFFECTOR
Researchers have developed a robot end-effector that can pick up a screw, hold it in place, and drive it. Photo courtesy Korea Institute of Industrial Technology
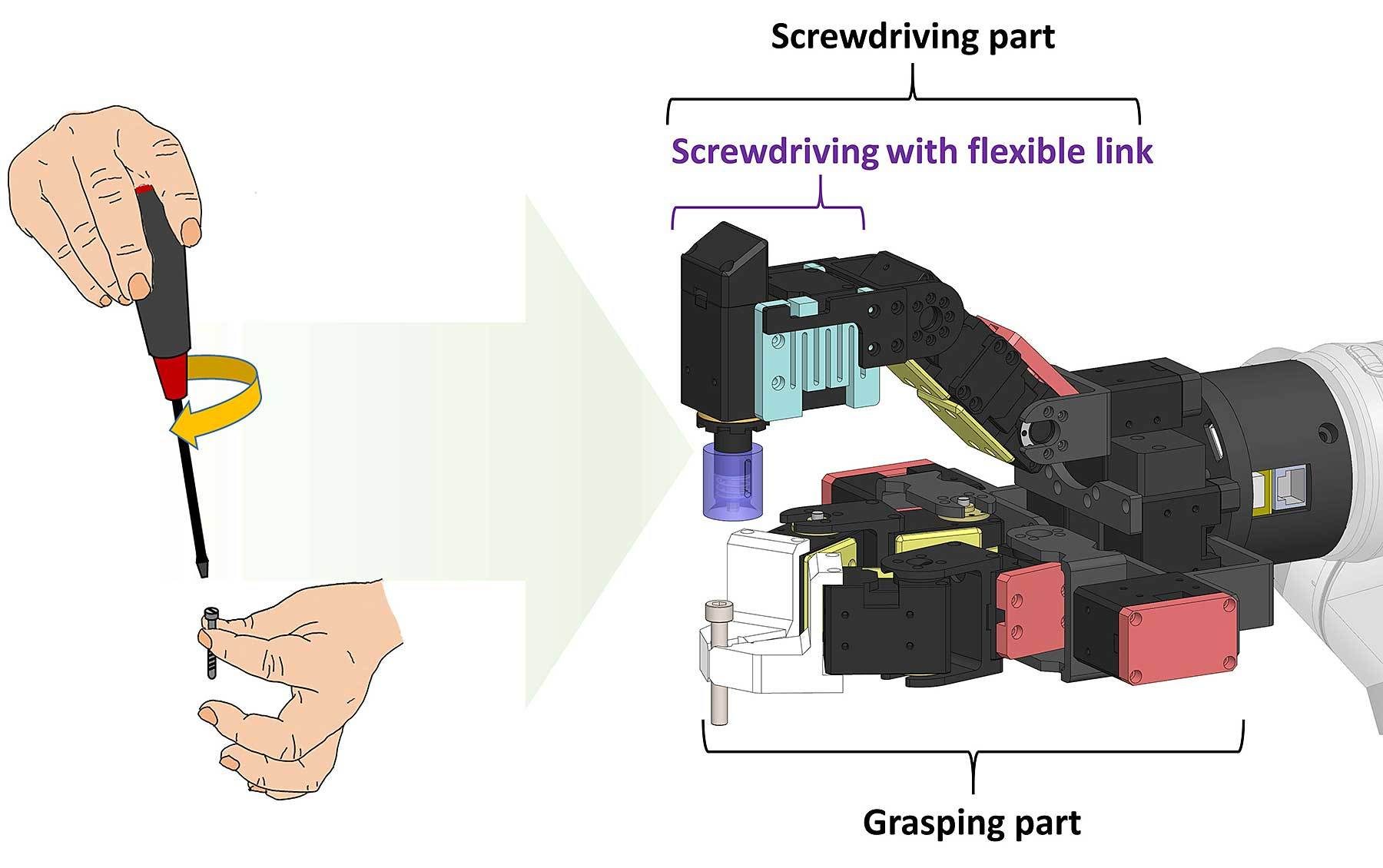
To manipulate small objects, people use a pinch grasp. For large objects or objects requiring large force, they use a power grasp. Hand manipulation is essential for pinching. In contrast, a power grasp rotates or changes direction using the wrists or arms, because the degrees of freedom of the fingers are constrained. To drive a screw, a person pinches the screw with two or three fingers to align it with the driver and the hole. Then, with the other hand, he uses a power grasp to drive the screw with a tool.
Our screwdriving gripper performs both these functions simultaneously. A single end-effector is divided into two parts: one for grasping the screw and another for driving it.
The grasping part can grip objects such as screws and dowels. It comprises two fingers and a joint configuration of roll-yaw-pitch-pitch. The yaw joint plays the role of pronation and supination of the human wrist. The roll joint provides both pinching and lifting motions. The fingertips have a V-shaped groove for handling small cylindrical objects, such as screws. The groove helps align the screw in the vertical direction without additional manipulation. It also prevents the screw from slipping.
To drive a screw, a person grasps a tool and rotates it using his wrist or arm. At the same time, he presses down onto the fastener with enough force that tool won’t separate from the screw head. The screwdriving part of our end-effector performs this role using a finger, a screwdriving motor, and a flexible link.
For a robot to install a screw, the driver and fastener must be aligned, and the tool needs to apply constant downward force. By itself, the robot controller cannot maintain the distance between the screw head and driver. That’s bad, because an error can damage the assembly or the gripper. The screwdriving part of our end-effector is designed to apply consistent contact force without a force sensor, using a flexible link structure.
The screwdriving part of the end-effector is designed to apply consistent contact force without a force sensor, using a flexible link structure. Photo courtesy Korea Institute of Industrial Technology
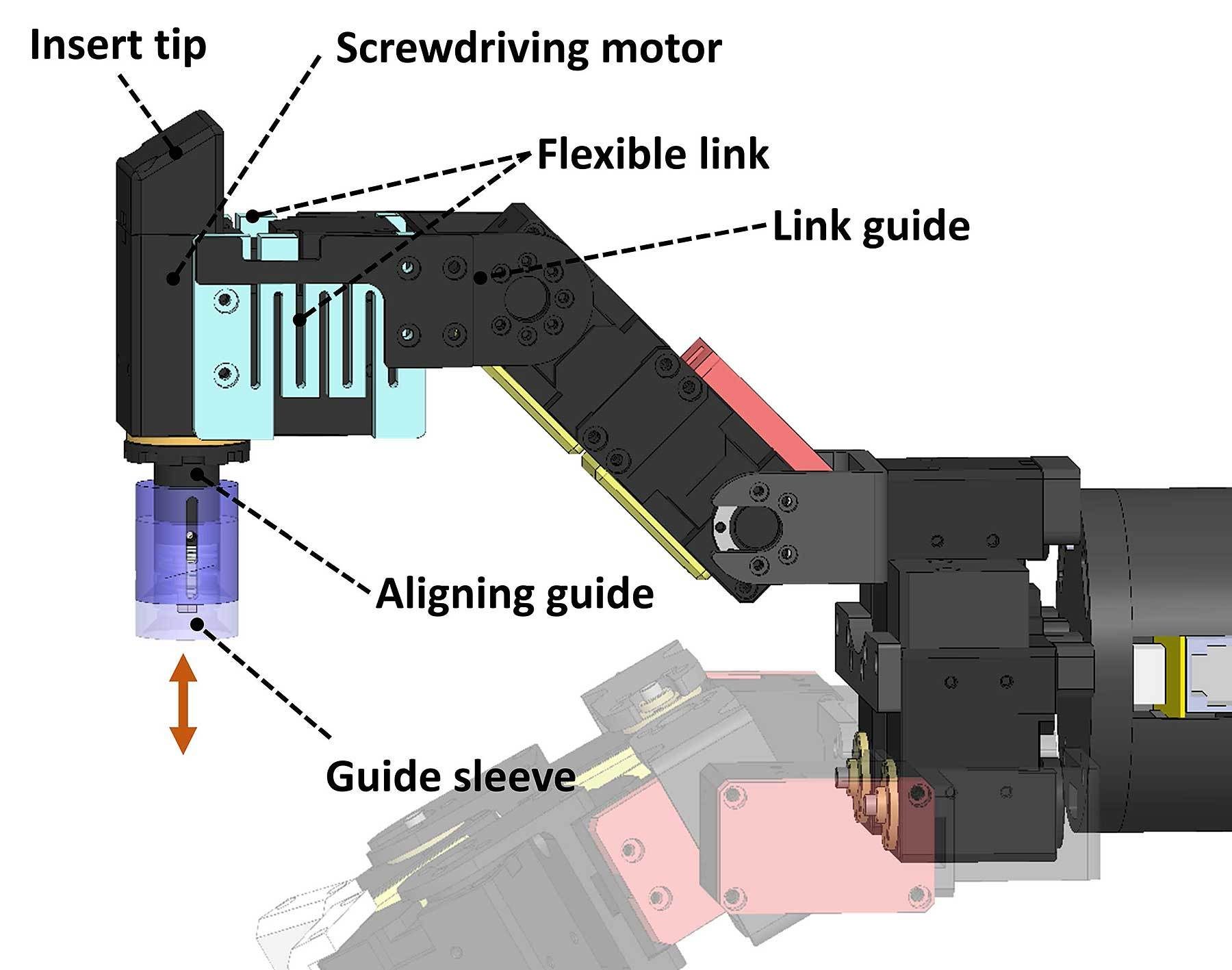
The screwdriving finger is located at the top of the gripper and consists of a roll-pitch-pitch joint configuration with three degrees of freedom. Two of the links are rigid. The last link, connected to the screwdriving motor, is flexible. The roll joint prevents the screw from being stuck by rotating left and right. It also rotates the screwdriving finger by 180 degrees to enable the use of the insert tip.
The screwdriving motor can equipped with a bit for driving screws or an insertion tip for installing wooden pegs. An alignment guide attached to the outside of the bit makes it easy to connect with the screw.
A flexible link is mounted on both sides of the screwdriving finger, together with a link guide. The guide prevents the flexible link from swinging left and right. It also provides up and down motion. The flexible link consists of several W shapes. It has a protruding structure in contact with the link guide. This continuous W shape makes it a compliant element. The flexible link allows the driver to maintain contact force without a precise force controller. It also prevents the screw and assembly from being stuck while driving the screw by providing passive compliance.
To test their robotic screwdriving end-effector, the researchers devised a robotic cell to assemble a wooden chair. The cell is equipped with three cobots. Two cobots, equipped with standard grippers, hold parts of the chair in place while the third cobot, equipped with the screwdriving end-effector, installs screws. Photo courtesy Korea Institute of Industrial Technology
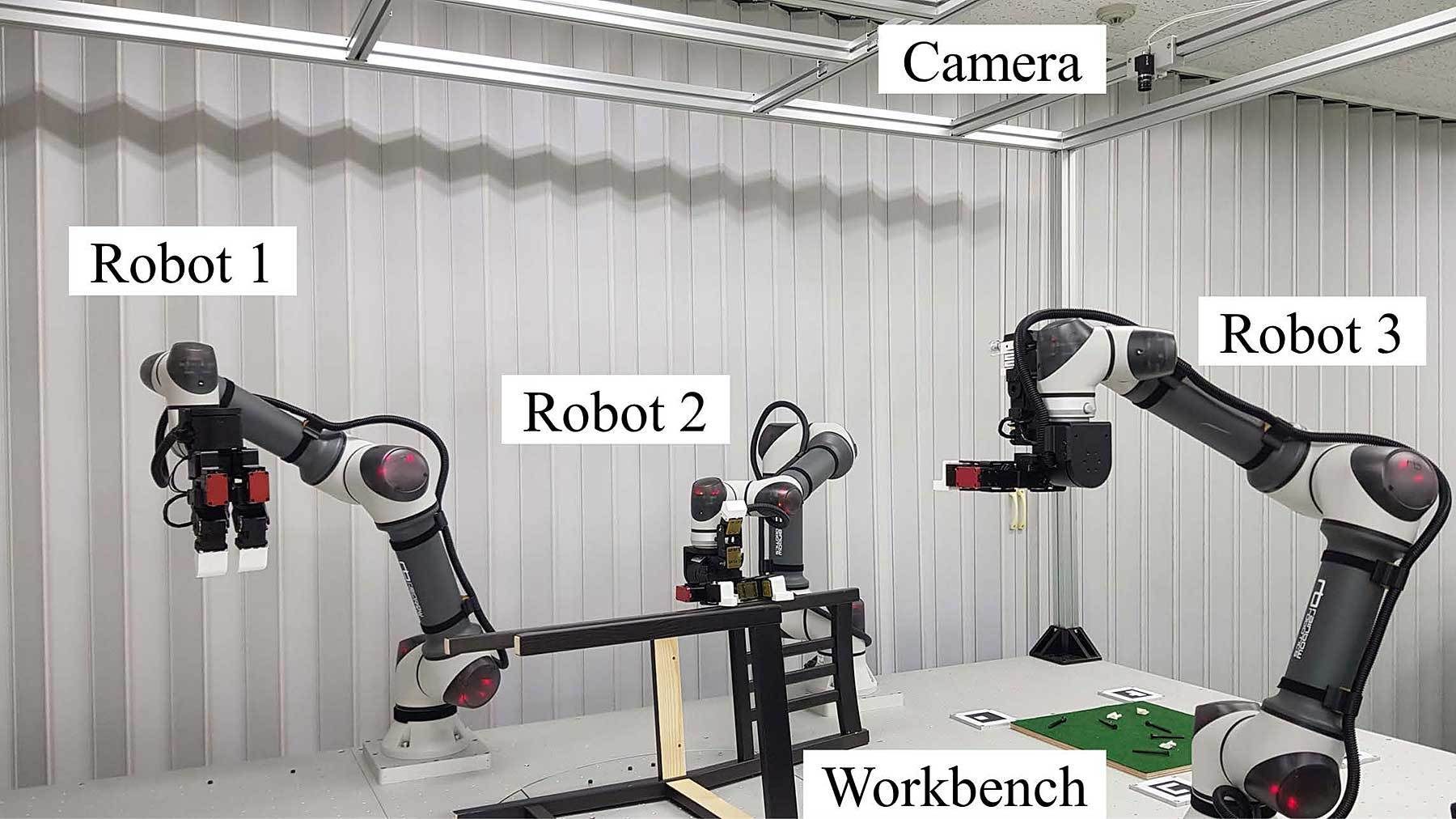
When a force is applied in the direction opposite to that of gravity, the flexible link bends in response. When the force is applied in the direction of gravity, the link guide supports the protruded structure of the flexible link, which remains horizontal. Thus, compliance can be changed according to the direction of operation. During screwdriving, the force acts in the direction opposite to that of gravity, and the flexible link is bent. However, for installing pegs, force can be stably transmitted to the peg because the insert tip is fixed.
The alignment guide mounted on the screwdriver comprises a guide and a sleeve connected by a spring-slide link. During screwdriving, the sleeve is inserted into the alignment guide and it protrudes again when the screwdriving task is completed. The inside of the guide sleeve has an oblique shape, which helps align the screw with the alignment guide when the grasping finger inserts the screw into the screwdriving finger without precise position control.
The insert tip is attached to the back of the screwdriving actuator. It presses down on the peg to insert in the hole. The insert tip is oblique, so that the peg and insert tip surfaces are at right angles.
Both the grasping part and the screwdriving part of the end-effector are powered with standard commercial servomotors with built-in sensors. Only four wires are needed to control the motors and supply them with power. Each motor and the main controller communicate via RS485.
All joints are serially connected. As a result, the end-effector can be modularized at the joint level. The modular joint structure is easy to maintain, and the joint configuration of the finger can be changed easily.
The screwdriving part of our end-effector measures 25.7 centimeters long, 22.7 centimeters wide, and 16.9 centimeters tall. It weighs approximately 1.5 kilograms. The sleeve of the alignment guide is made of transparent acrylic. The flexible link between the screwdriver and fingertip material is ABS. It was made with a 3D printer.
ASSEMBLY WITH THE END-EFFECTOR
Insertion is a five-step process: determine the position and size of the screw or dowel using machine vision; grip the part; align the part with the driver bit or the insertion tip; align the part with the hole; and drive the screw or push in the dowel. Photo courtesy Korea Institute of Industrial Technology
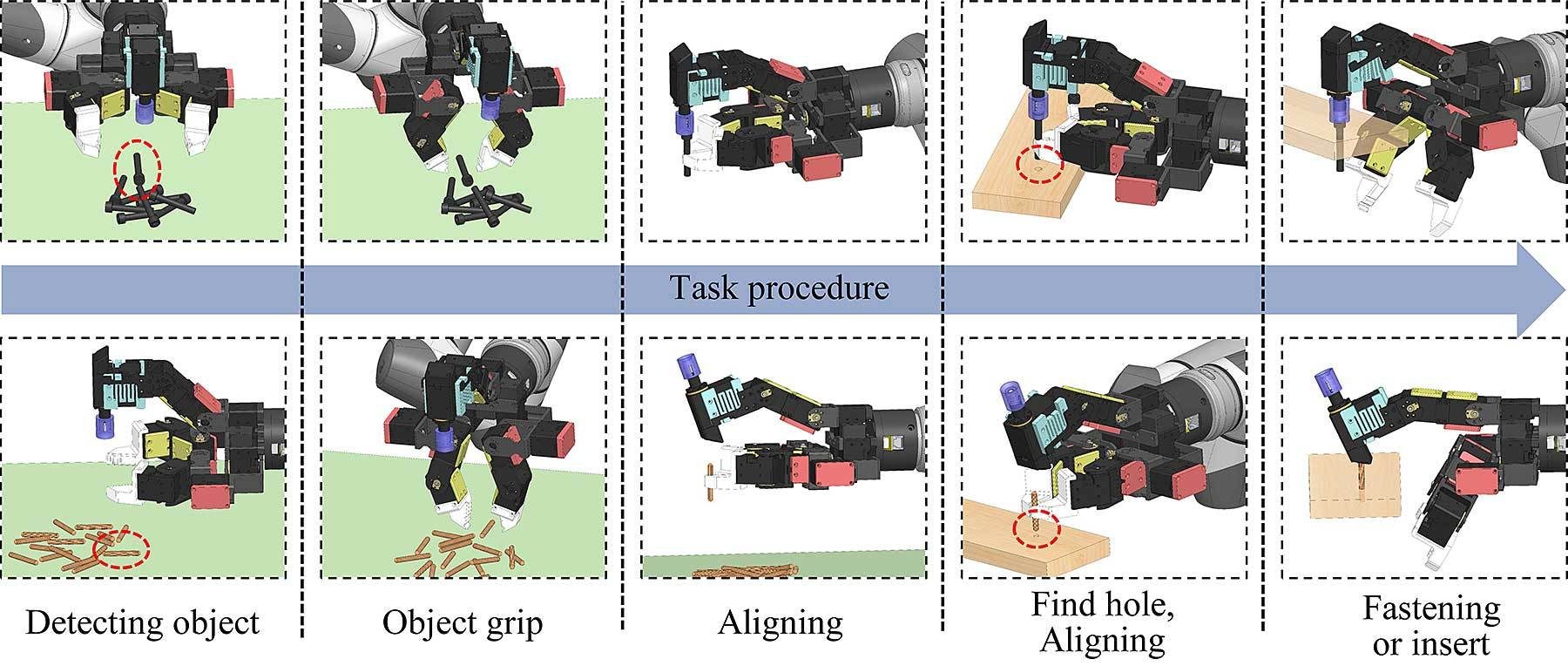
To assemble parts with our end-effector, position information is acquired using a vision system installed above the workbench. The vision system locates randomly scattered objects, such as screws and dowels. It also determines the location of holes in the parts. The robot uses a spiral search method to insert a peg or screw into the hole. This enables the robot to insert the part without force feedback or passive compliance, and it can overcome the inevitable positional uncertainty of the parts.
Insertion is a five-step process:
Step 1. Determine the position and size of the screw or dowel using machine vision.
Step 2. Grip the part.
Step 3. Align the part with the driver bit or the insertion tip.
Step 4. Align the part with the hole.
Step 5. Drive the screw or push in the dowel.
The screwdriving process is monitored by a sensor built into the motor. An external torque sensor was not used. Before driving the screw, the motor rotates back and forth to ensure bit engagement. Then the motor drives the screw at a constant velocity. The motor shuts off when the sensor detects a dramatic change in motor velocity, which would indicate that the screw has been fully seated.
TESTING THE CONCEPT
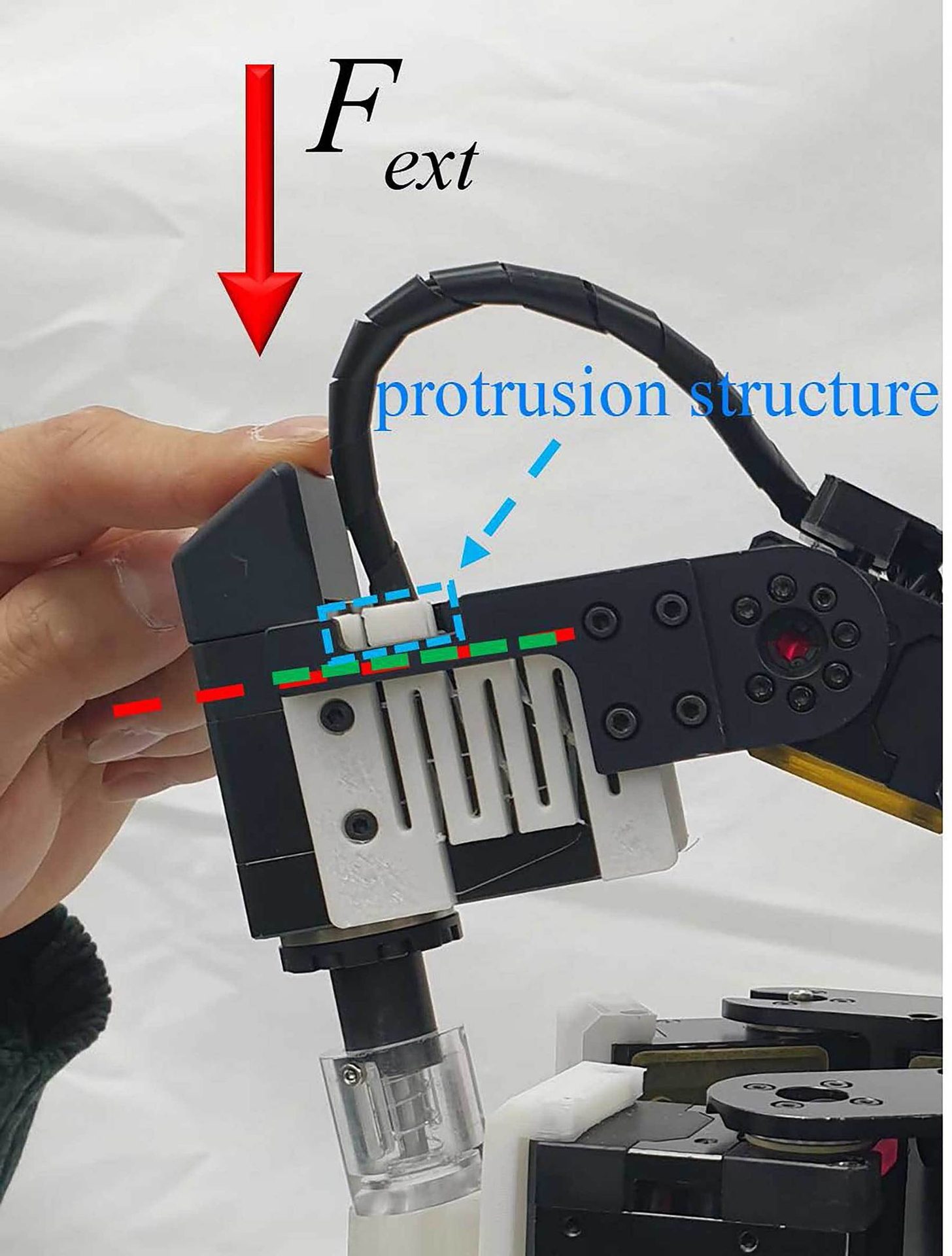
To test our robotic screwdriving end-effector, we devised a robotic cell to assemble a wooden chair. Our cell is equipped with three six-axis collaborative robots from Rainbow Robotics. Two cobots are equipped with standard multifinger grippers. These cobots hold parts of the chair in place while the third cobot, equipped with our screwdriving end-effector, installs screws. A vision system is mounted above the workbench to locate the parts. The screws are randomly placed on a green plate for ease of recognition.
Our results indicate that it is possible for a team of robots to assemble a wooden chair. Our screwdriving end-effector was able to reliably pick up screws from the plate and install them.
A flexible link is mounted on both sides of the screwdriving finger. Its shape makes it a compliant element. The flexible link allows the driver to maintain contact force without a precise force controller. Photo courtesy Korea Institute of Industrial Technology
ASSEMBLY ONLINE
For more information on robotics and screwdriving, visit www.assemblymag.com to read these articles:
New Tech for Robotic Fastening
Five Things: Automatic Screwdriving
Robotic Screwdriving Mistakes to Avoid
FACTORY OF THE FUTURE NOVEMBER 2022
