
FACTORY OF THE FUTURE
Jon Sprovieri // Chief Editor
Highly automated smart factories are no longer a pie in the sky concept.
Smart Factories:
Here and Now
Photo courtesy Traitov, iStock / Getty Images Plus

Rotor blades, guide vanes and other components for jet engines are made from costly materials and machined to precise tolerances. Such components are typically made in batches, due to the time involved in setting up machine centers. The process also requires a fair number of people to tend the machines and assist in changeover.
However, new technology is changing that scenario. At its assembly plant in Munich, Germany, MTU Aero Engines has developed an automated production process that can operate autonomously for 66 hours.
At the start of the process, a six-axis robot places a blank in the clamping device, secures it with screws, and loads it into one of the five machining centers. The machines drill and mill, grind and gauge—everything is fully automated. And it’s efficient: While the machines are hard at work, the robot is already attending to the preparation and post-processing of the next parts and tools.
“With the new system, we have proven that Industry 4.0 can even meet the extremely sophisticated requirements for production of engine parts,” says Christiane Müller, head of high-pressure turbine guide vanes at MTU. “And, it takes up just a third of the space needed for conventional production.”
MTU’s flexible manufacturing system (FMS) marks the company’s first step in creating an overall smart factory. Assisted by a control system, the facility’s machining centers manufacture components in parallel, working flexibly and autonomously for days at a time without human intervention.
In fact, the production line can work autonomously for 66 hours without human intervention. “This is the exact amount of time it takes to comfortably bridge a whole weekend,” says Marc Weiß, FMS project manager.
The machine’s built-in autonomous correction function and preventive maintenance system ensure process stability. This sets the stage for even more efficiency gains in the future.
At its assembly plant in Munich, Germany, MTU Aero Engines has developed an automated production process that can operate autonomously for 66 hours. Photo courtesy MTU Aero Engines
Employees still have to mount and remove grinding wheels and other tools by hand—95 percent of the work steps required to manufacture turbine blades involve grinding. But drill bits and milling cutters are automatically switched out and gauged by the machining centers.
This system has also made order processing more efficient and flexible—a welcome development, given the industry trend of having to produce in increasingly smaller batch sizes and needing to tailor customer orders. Orders are usually placed for batches of 70 to 120 pieces. With the new system, these batch sizes can be reduced without incurring high retooling costs.
A double structure is in place to minimize downtime. For example, one milling cutter is used in the tool machine while another is being prepared for the next step. The same goes for the robot cells: a new blank is clamped in place on one fixture while a processed component is removed from another.
“This means we can plan orders more flexibly, and we don’t have to worry so much about retooling times—on balance, our production is more efficient in several respects,” Müller says.
Continental is investing $4.9 million to build a new highly automated production line for industrial hoses at its factory in Korbach, Germany. Photo courtesy Continental AG
While conventional production lines had previously needed seven to eight hours for retooling, the new system is ready to go in just 15 minutes.
It took a lot of time and effort to reach this stage of flexible manufacturing: “But by the same token, we’ve benefited from a successful, if steep, learning curve,” Weiß says. Continuing to run the old system while setting up the new one proved to be challenging logistically. But, by July 2021, the new FMS was fully operational.
“This has essentially become a lighthouse project, not just for MTU but also for the wider industry. We’ve never seen an automated production system like it anywhere in the world, especially not for this type of component or extremely sensitive manufacturing situation,” Weiß says.
A high level of in-house knowledge was critical to developing the line. MTU programmed the machining centers itself. Even the clamping station, with its robot-operated screw-fitting, was developed by MTU engineers. The company’s work on the tool changing cell was also groundbreaking. Together with its partners, MTU developed technology that did not yet exist.
Müller emphasizes the importance of the expertise offered by the company’s employees, who drew on their experience with conventional systems. “Incorporating this knowledge into the new system means that it represents a balanced partnership between humans and machines,” he says.
With the FMS fully operational, MTU will continue to automate. MTU plans to build another, more extensive production line at the Munich factory in the future. “The FMS has created a blueprint for other systems, which will emerge over the next few years on a much larger scale and take up an entire hall,” Weiß says.
The next step will be to take those efforts companywide. “In the future, MTU will connect the many individual initiatives we have relating to smart systems in assembly or production and link them to an overall digital system—transforming island solutions into a truly smart factory,” predicts Fabian Lindermer, head of digitization at MTU.
FLEXIBLE HOSE PRODUCTION
To improve competitiveness, sustainability and health, electronics assembler Flex implemented a variety of Industry 4.0 initiatives, such as a supply chain control tower and IIoT-enabled recycling of electronic waste. Photo courtesy Flex Ltd.
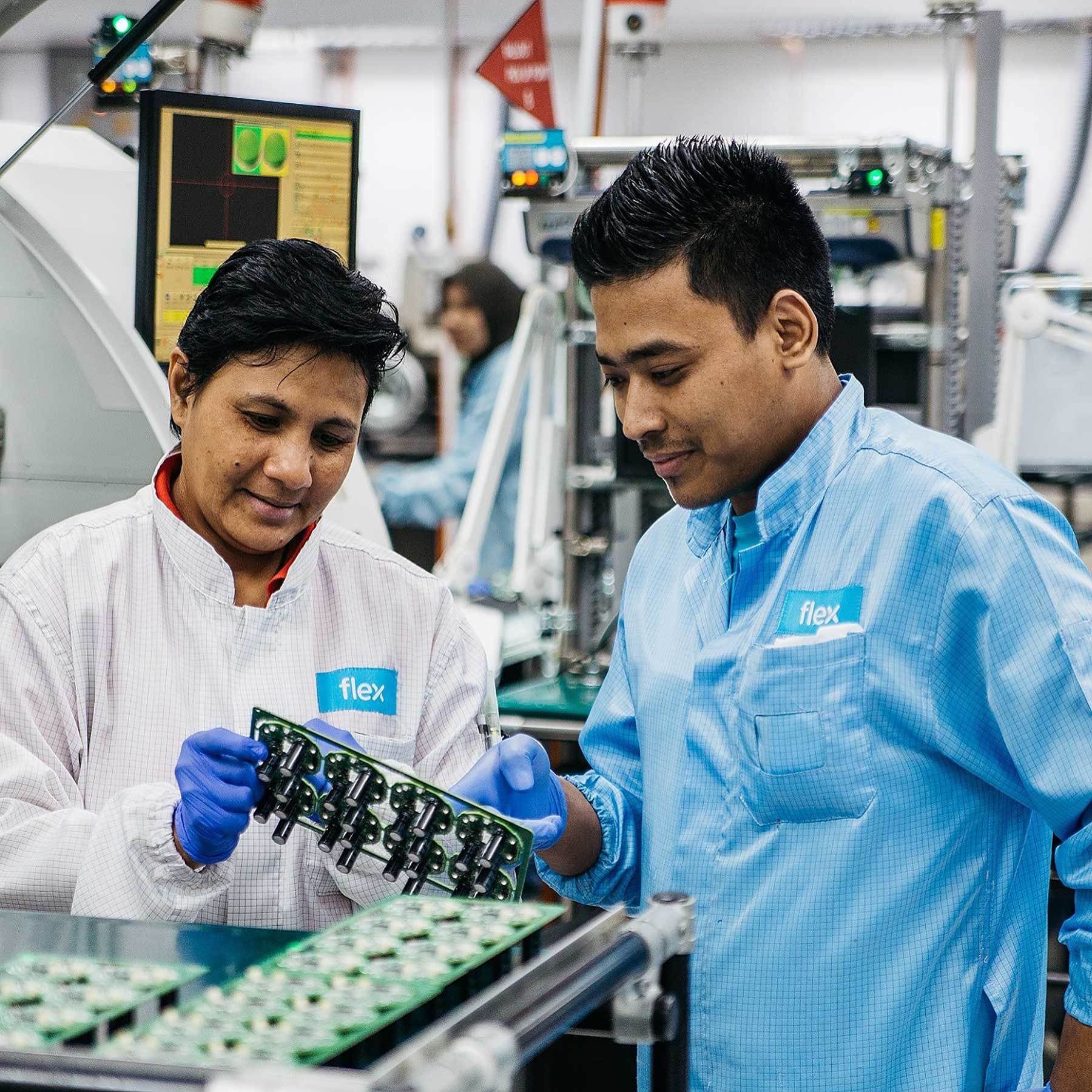
MTU’s lights-out production line in Munich is one example of how manufacturers worldwide are applying state-of-the-art technology to solve problems and improve processes.
Some 327 miles north of Munich, a similar project is underway at Continental AG’s factory in Korbach, Germany. In May, Continental said it would invest $4.9 million in a new highly automated production line for industrial hoses at the factory. The line, which will operate 24/7, is scheduled to start up at the end of 2023. It’s the company’s largest investment in Korbach in more than 10 years.
With the new line, the technology company can manufacture existing products more efficiently, while also expanding its portfolio and increasing its competitiveness. The new line will enable Continental to pursue new markets, particularly in the industrial sector.
“The new line will improve our manufacturing process enormously. We are producing more sustainably, more flexibly, more safely and more ergonomically,” emphasizes Torsten Dietmann, head of the hose plant in Korbach. “Networked and automated plant elements based on a smart factory approach guarantee energy-efficient production and ideal value creation in the process.”
With a capacity of around 5 million meters of hose per year, the new line will be able to manufacture hoses with an inside diameter of up to 38 millimeters. The hoses can be used to carry food, water, fuels, coolants and other fluids.
A major plus of the new line will be its flexibility: It will be able to produce hoses using different techniques, with inner layers of either rubber or plastic.
“This gives us tremendous flexibility. On the new plant, we will continue to manufacture standard products, but will also add new applications. This will enable us to better adapt to rapidly changing market needs and expand our product portfolio in a focused manner,” says Dietmann.
Continental’s investment is about more than just increased flexibility and competitiveness. It will also help the automotive supplier meet sustainability goals. Thanks to new recycling options and the ability to process additional materials, the Korbach site is taking a step toward climate-neutral production in line with a companywide strategy.
AMGEN BETS BIG ON SMART FACTORY
Amgen is building a $365 million smart factory in New Albany, OH. Photo courtesy Amgen Inc.
The pharmaceutical industry is also investing in automation and digital transformation. Last summer, Amgen Inc. unveiled plans to invest $365 million to build a smart factory in New Albany, OH. Set to feature the company’s most advanced assembly and packaging processes, the plant will assemble, label and package autoinjectors, syringes and vials for a plethora of Amgen medications.
Construction of the 270,000-square-foot plant began last fall. The facility will eventually employ 400 people with an expected annual payroll of about $40 million. The site is expected to come online in early 2024.
The goal is to make the assembly and packaging site Amgen’s “most digitally advanced facility,” says Arleen Paulino, senior vice president of manufacturing at Amgen. By leveraging the latest manufacturing technologies, the company also hopes to get ahead of anticipated growth in demand for its drugs.
The smart facility will rely on a host of digital technologies, including artificial intelligence (AI), across three areas: advanced automation and robotics; automated inspection, testing and real-time release of manufactured batches; and data analytics to monitor and manage process and operational performance.
The site will employ highly automated storage and retrieval systems, automated guided vehicles to ferry materials, and collaborative robots, says Paulino.
LIGHTHOUSES LEAD THE WAY
Powered by 100 percent green electricity, Arçelik’s appliance assembly plant in Ulmi, Romania, has deployed a variety of technologies to address sustainability. Photo courtesy Arçelik
In October, the World Economic Forum (WEF) added 11 new factories and industrial sites to its Global Lighthouse Network, a community of more than 100 manufacturers that are showing leadership in applying Industry 4.0 technologies to improve productivity, workforce engagement, sustainability and supply chain resilience.
Amid warnings of a global recession, energy price hikes and disrupted supply chains, lighthouse factories offer business leaders and policymakers examples of how the manufacturing sector can stay competitive and continue to create jobs.
“The new factories of the Global Lighthouse Network show how manufacturers can meet business goals while having a positive impact on economies, peoples’ livelihoods and the environment,” says Francisco Betti, head of advanced manufacturing and value chains at the World Economic Forum. “The challenge for companies and policymakers is how much they can scale-up these innovations across whole production networks and value chains.”
While supply chain issues and other problems held back most manufacturers in 2022, other companies proved that digital transformation could be scaled across global enterprises. In the new cohort of lighthouses, many companies, such as Cipla, Danone and Sany Heavy Industry, are deploying large digital transformation programs at scale across 20 to 40 factories in parallel, over time spans of just 18 to 24 months.
“The newly designated lighthouses show that scaling can be done, with three must-haves,” says Enno de Boer, global lead of digital manufacturing at McKinsey & Co., which partners with the WEF on the lighthouse project. “First, clear strategy. Without that, you get stuck in pilot purgatory, never seeing which technologies matter for your business. Second, workforce capabilities. Without enough of the right skills, your transformation runs out of steam. Third, strong governance. Without a real execution engine, you won’t capture impact or keep improving.”
After deploying AI, IIoT and flexible automation, CATL’s battery assembly plant increased line speed by 17 percent and reduced yield loss by 14 percent. Photo courtesy Contemporary Amperex Technology Co. Ltd.
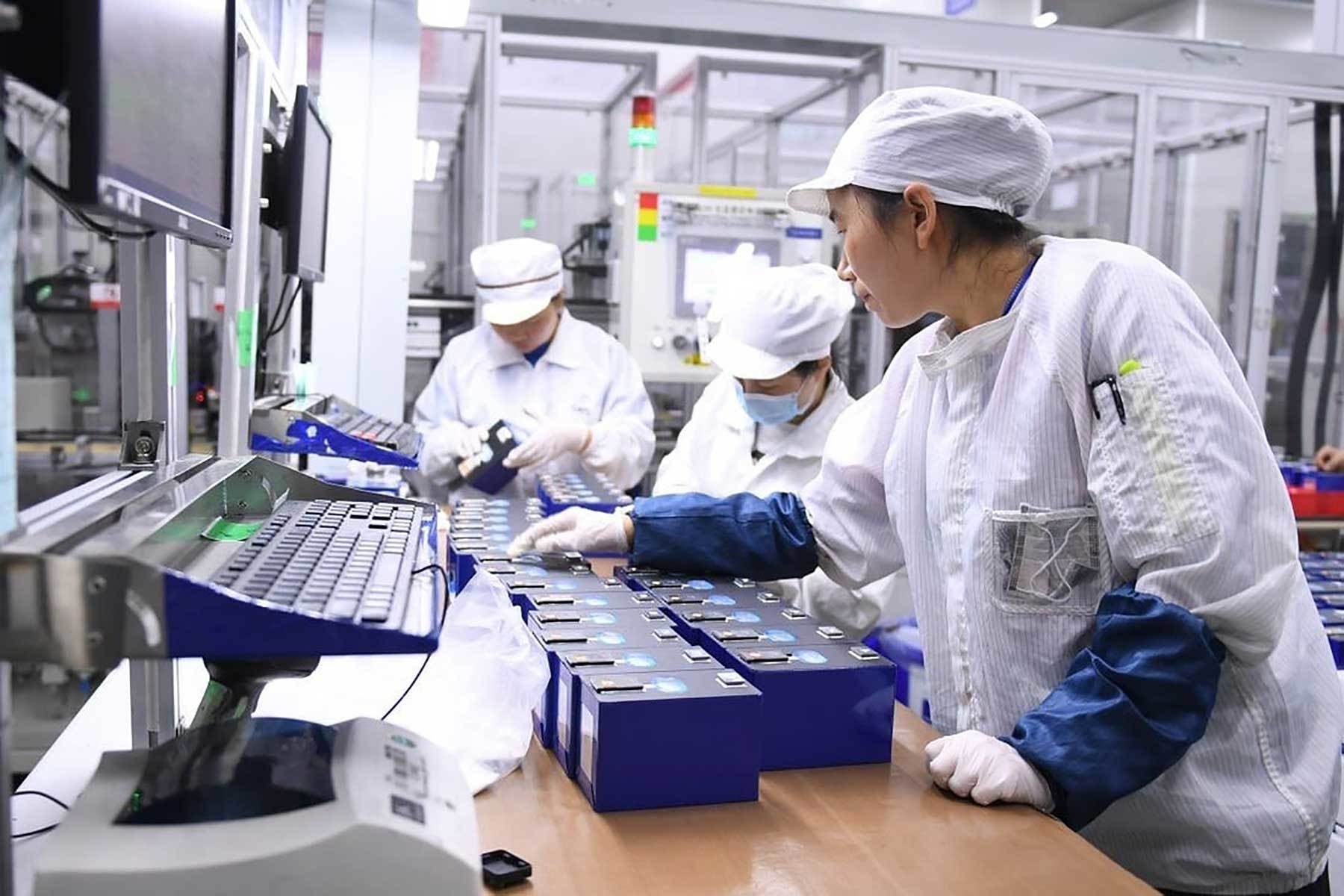
The new lighthouses are:
Agilent Technologies in Singapore. With the ambition to simplify manufacturing of low-volume, high-complexity instruments to meet rising demand, Agilent deployed IIoT, digital twin, AI and robotic technology to achieve sustainable growth, overcoming bottlenecks from specialized manpower and transforming the workforce into Industry 4.0 generalists. This improved output by 80 percent, productivity by 60 percent, cycle time by 30 percent, and quality cost by 20 percent.
Contemporary Amperex Technology Co. Ltd. (CATL) in Yibin, China. To catch up with significant business growth, the manufacturer of lithium-ion batteries for electric vehicles and energy storage systems built a large greenfield assembly plant in Yibin. After deploying AI, IIoT and flexible automation, the plant increased line speed by 17 percent and reduced yield loss by 14 percent. It also reduced carbon emissions to zero.
Cipla in Indore, India. Facing an increase in material and labor costs, Cipla deployed automation and data analytics technology at 22 factories in India in parallel. The company’s Oral Solid Dosage facility in Indore led this journey by implementing 30 Industry 4.0 use-cases. It improved total cost by 26 percent, enhanced quality by 300 percent, and reduced greenhouse gas (GHG) emissions by 28 percent.
Danone in Opole, Poland. To address increasing complexity in its product portfolio, food manufacturer Danone engaged its whole workforce across functions and levels in a digital transformation journey. The goal was to implement AI and automation and create a connected shop floor. The company improved costs by 19 percent and efficiency by 12 percent. It also reduced GHG emissions by close to 50 percent. It is now a leader for Danone 39 other plants in Europe.
Dr. Reddy’s Laboratories in Hyderabad, India. Faced with severe price erosion, the pharmaceuticals company embarked on a large-scale digitalization project. The site deployed more than 40 Industry 4.0 use cases by operating in an agile way, leveraging IIoT technology, and implementing data analytics. As a result, it improved manufacturing cost by 43 percent and reduced energy consumption by 41 percent.
Flex in Sorocaba, Brazil. To improve competitiveness, sustainability and health, electronics assembler Flex implemented a variety of Industry 4.0 initiatives, such as a supply chain control tower and IIoT-enabled recycling of electronic waste. The efforts resulted in a 50 percent improvement in labor costs, an 81 percent reduction in material loss, and an 18 percent increase in customer satisfaction.
Haier in Qingdao, China. Facing growing demand for customized design, fast delivery and high quality, the appliance assembly plant leveraged big data, digital twin and advanced visual inspection technology to accelerate R&D, upgrade manufacturing processes and improve logistics scheduling. As a result, lead time has been shortened by 35 percent, production efficiency has been increased by 35 percent, and quality performance has been improved by 36 percent.
Midea in Shunde, China. To meet demand for high-quality products and shorter lead times, appliance assembler Midea deployed AI, digital twin and other Industry 4.0 technologies. It has achieved 24 percent lower unit production costs, 41 percent shorter lead times, 30 percent shorter R&D lead times, and 51 percent less defect rate.
Mondelēz in Sri City, India. With a goal of increasing production volume, reducing costs and increasing supply chain resilience, the snack food manufacturer deployed end-to-end digitalization, predictive analytics, AI and advanced automation. The company increased labor productivity by 89 percent and reduced manufacturing costs by 38 percent.
Sany Heavy Industry in Changsha, China. To address market cycle fluctuations and product complexity, Sany leveraged flexible automation, AI and IIoT at scale to build a digital and flexible manufacturing system for its heavy equipment. As a result, the site expanded capacity by 123 percent, improved labor productivity by 98 percent, and reduced unit manufacturing cost by 29 percent.
Western Digital in Shanghai, China. To address workforce challenges, a 250 percent annual growth rate, and a technology transition pace of 18 months, the semiconductor manufacturer implemented a variety of Industry 4.0 technologies, such as an automated product design system, wafer testing based on machine learning, and an intelligent planning system. The site reduced time to market by 40 percent and product cost by 62 percent. It also improved productivity by 221 percent.
Haier’s appliance assembly plant in Qingdao, China, has leveraged big data, digital twin and advanced visual inspection technology to accelerate R&D, upgrade manufacturing processes and improve logistics scheduling. Photo courtesy Haier Home Appliance
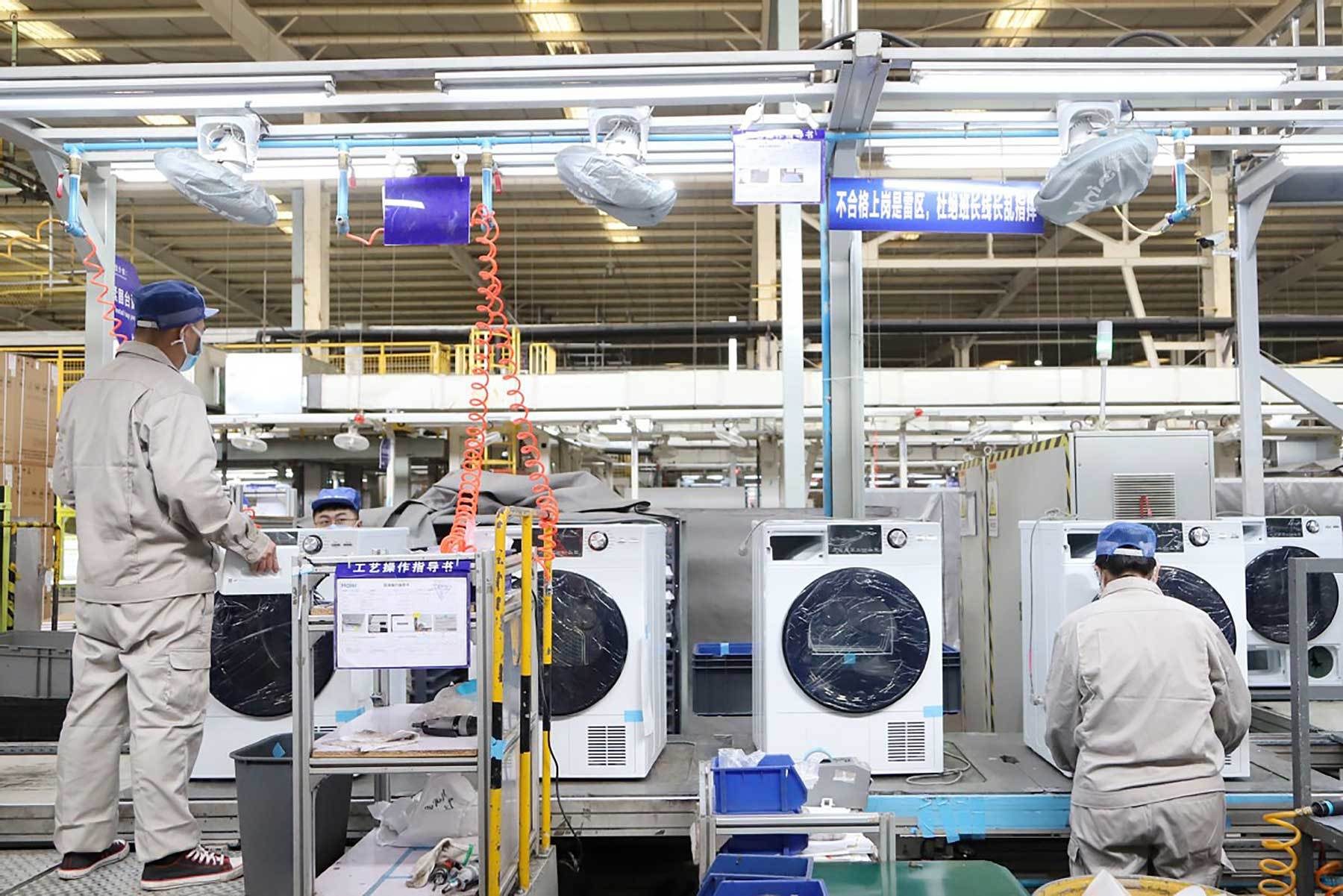
Four existing lighthouse facilities with outstanding environmental records gained the additional designation of sustainability lighthouses. They are:
Arçelik in Ulmi, Romania. Powered by 100 percent green electricity, Arçelik’s appliance assembly plant has deployed a variety of technologies to address sustainability, including a digital twin for energy management and a closed-loop water management system integrated with an advanced water treatment plant. In an environment suffering from water stress, the factory has reduced water consumption by 25 percent, energy consumption by 17 percent, and GHG emissions by 22 percent per unit manufactured.p
Micron in Singapore. With growing demand for memory chips, Micron needed to expand production while reducing its environmental footprint. From 2018 to 2021, Micron increased output by 270 percent and simultaneously reduced resources used per gigabyte produced by 45 percent. The company optimized materials consumption and implemented environmental footprint tracking.
Unilever in Dapada, India. Faced with corporate mandates to reduce emissions and water consumption, the company found 14 use-cases for sustainability technology. These included applying machine learning to optimize energy consumption and employing digital twin technology to accelerate development of eco-friendly formulations. As a result, Dapada has reduced emissions by 54 percent and its water consumption by 36 percent.
Western Digital in Shanghai, China. Between 2017 and 2021, Western Digital doubled the site’s output of memory chips while reducing its environmental footprint. This result was enabled by multiple Industry 4.0 use-cases, such as machine learning to dynamically optimize the performance of the water recycling plant. These measures reduced water consumption by 62 percent and energy consumption by 51 percent per petabyte of memory produced.
ASSEMBLY ONLINE
For more information on smart factories, visit www.assemblymag.com to read these articles:
Data Analytics and the Smart Factory
Inside Schneider Electric’s Smart Factory
Industry 4.0: Myths vs. Reality
FACTORY OF THE FUTURE NOVEMBER 2022
