ASSEMBLY LINES
‘Assembly Plant of the Year’ Award Call for Nominations
CHICAGO—ASSEMBLY is seeking nominations for its 2025 Assembly Plant of the Year award. The 22nd annual award will recognize a manufacturing facility in the United States that has applied world-class processes to reduce production costs, increase productivity, shorten time to market and improve product quality.
Entries will be judged by ASSEMBLY’s editorial staff on a broad range of operational performance measures and the use of production tools. The winning facility will receive a crystal award and a commemorative banner. It will also be profiled in the October issue of ASSEMBLY.
The GE Appliances dishwasher factory in Louisville, KY, was the recipient of the 2024 Assembly Plant of the Year award. Photo courtesy GE Appliances
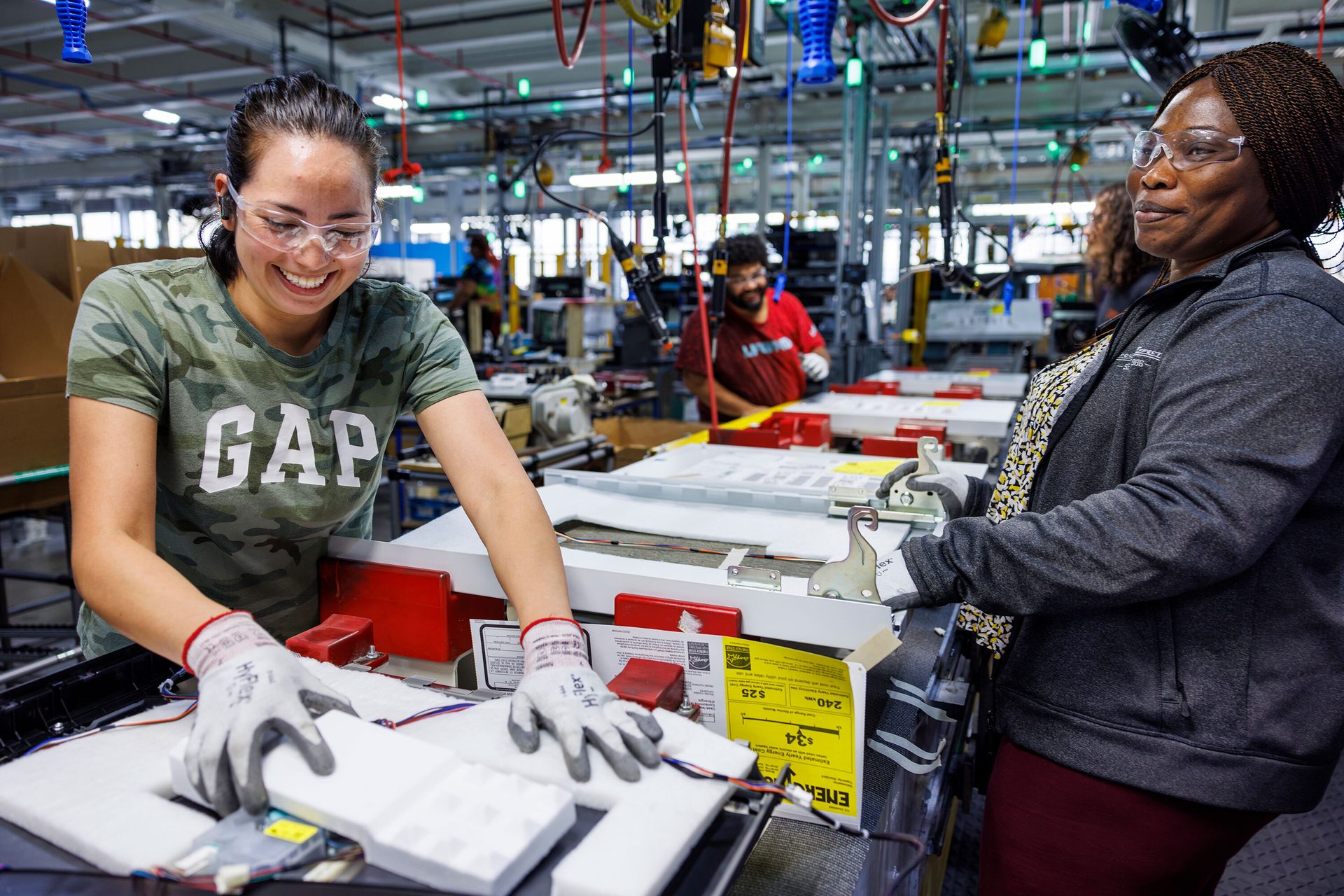
Previous recipients have been GE Appliances, Louisville, KY (2024); Taylor Guitars, El Cajon, CA (2023); Brose Tuscaloosa Inc., Vance, AL (2022); GKN Automotive, Newton, NC (2021); Murakami Manufacturing USA Inc., Campbellsville, KY (2020); GE Appliances, Decatur, AL (2019); Ford Motor Co., Sterling Heights, MI (2018); AGCO Corp., Jackson, MN (2017); Bosch Rexroth Corp., Fountain Inn, SC (2016); Polaris Industries Inc., Spirit Lake, IA (2015); STIHL Inc., Virginia Beach, VA (2014); Northrop Grumman Corp., Palmdale, CA (2013); Ford Motor Co., Wayne, MI (2012); Philips Respironics, New Kensington, PA (2011); Eaton Corp., Lincoln, IL (2010); Batesville Casket Co., Manchester, TN (2009); IBM Corp., Poughkeepsie, NY (2008); Schneider Electric/Square D, Lexington, KY (2007); Lear Corp., Montgomery, AL (2006); Xerox Corp., Webster, NY (2005); and Kenworth Truck Co., Renton, WA (2004).
Companies interested in applying for the 2025 Assembly Plant of the Year award can fill out the online form here. There is no entry fee, and more than one plant may be nominated.
The deadline for submissions is March 28. For more information, contact Austin Weber at webera@bnpmedia.com or 224-202-2340.
Low-Cost System May Improve Wireless Machine Communication
PRINCETON, NJ—Engineers at Brown University, Princeton University and Rice University have developed a low-power, inexpensive way for a large number of devices, such as machines in factories, to share information wirelessly by efficiently using signals at untapped frequencies.
The new tag is the first of its kind that can use backscattering in the subterahertz range, a high frequency portion of the radio spectrum. This range can support high-speed data transmission across broad
bandwidths.
The development means it could be possible to power
signal transmission for dense networks of devices using passive tags, saving significant power and infrastructure compared to conventional wireless systems.
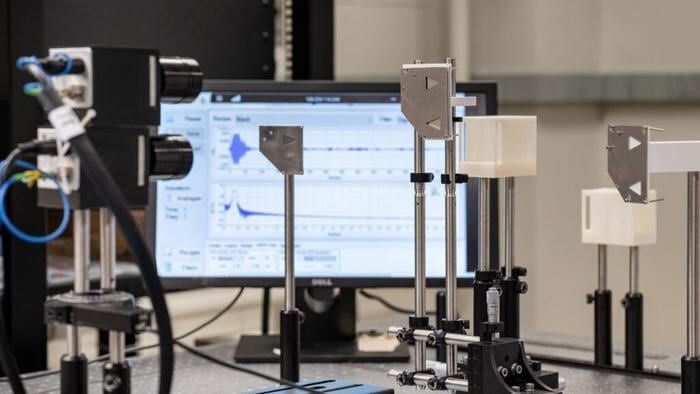
A new communication tag that operates in the subterahertz frequency range can support data transmission for a large network of devices using a technique called backscattering. Photo courtesy Princeton University
“I believe this technology will find applications in many interesting settings,” says Yasaman Ghasempour, Ph.D., assistant professor of electrical and computer engineering at Princeton University. “Despite the conventional wisdom….it is possible to have low-power, scalable communication in the subterahertz range.”
According to Ghasempour, the new technology could enable low-cost, efficient real-time monitoring in industrial settings, such as tracking the condition of robots, by eliminating the need for power-hungry signal transmitters.
Backscattering occurs when a central reader sends a signal to a sensor tag to gather information, and the tag reflects this ambient signal directly back to the reader. It is already used in simple systems like building entry cards, but until now has only been possible at low frequencies.
The low frequency limit poses a problem when many devices try to communicate at the same time, because when more signals are introduced, they are more likely to run into one another and get jumbled up. Traditional backscatter designs also have slow communication speeds, because lower frequency signals have limitations on how much information can travel back and forth at once.
“Using backscattering at higher frequencies is challenging, because the signals are more susceptible to fading as they propagate and must be very precise to travel long distances,” says Ghasempour. “The reader has to form a narrow pencil-shaped beam to shine into the tag’s precise location, and the low-power tag should do the same without consuming any power."
Traditional backscatter tags reflect signals back to their source using simple antennas that typically broadcast the energy in all directions, causing only a portion of the energy to reach back to the reader. While some advanced tags can adjust the direction of their signal, their ability to do so is limited, and they’re restricted to a narrow range of frequencies.
Achieving subterahertz backscattering required Ghasempour and her colleagues to rethink the entire architecture of the tag. They also developed an entirely new antenna structure.
The new antennas allow the direction of the signal to change automatically in response to changes in frequency. By doing this, the tag can “steer” the signal to enable longer range communication and avoid interference from other signals.
New Gripper Moves Multiple Objects at Once
SEOUL—Engineers at the Seoul National University have developed a gripper that can move multiple objects. MOGrip picks up objects one by one and moves them all at once, like a human. The gripper not only transfers multiple objects at once, but also places individual objects at desired locations.
“Unlike humans, conventional gripper designs have predominantly focused on transferring a single object at a time,” says Kyu-Jin Cho, Ph.D., a professor of mechanical engineering and director of the Soft Robotics Research Center. “While grippers for multi-object grasping have been developed, they typically consist of multiple small grippers arranged at the end of a robotic arm, restricting their use to highly structured environments.”
A new multi-object gripper (right) can improve the efficiency of pick-and-place applications. Illustration courtesy Seoul National University/Science Robotics
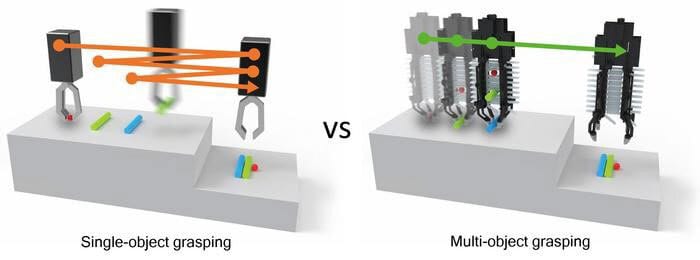
To transfer multiple objects in unstructured environments, humans grasp individual objects with their fingers and translate them to the palm for storage. This action is known as finger-to-palm translation.
MOGrip features fingers that can translate objects and a conveyor palm for storing multiple items simultaneously. The fingers, powered by two motors, grasp objects and transfer them to the palm. Decoupling links in the fingers kinematically separate the grasping and transferring motions, simplifying their control.
The conveyor palm is designed as a pair of belts with elastic hairs embedded on their surfaces. The belts are actuated by a single motor. When the belts rotate, objects are inserted between the hairs, enabling the simultaneous storage and transfer of multiple objects.
During experiments, Cho and his colleagues discovered that eight objects on a shelf could be transferred with just two reciprocating motions. Compared to single-object grasping, this reduced process time by 34 percent and the robotic arm’s travel distance by 71 percent.
“The principles of nature provided inspiration for efficient robotic motion and actuation strategies,” says Cho. “Finger-to-palm translation and palm-to-finger translations are a key component of the multi-object grasping strategy, and [our] gripper is the first example of applying this principle to a robot.”
New Joining Technology Improves Structural Strength
COLLEGE STATION, TX—Engineers at Texas A&M University have developed functional interlocking metasurfaces (ILMs) that provide more structural strength and stability than nuts, bolts or adhesives. The new type of mechanical joints rely on shape memory alloys.
Similar to Legos or Velcro, ILMs enable the joining of two bodies by transmitting force and constraining movement. Until now, this joining method has been passive, requiring force for engagement.
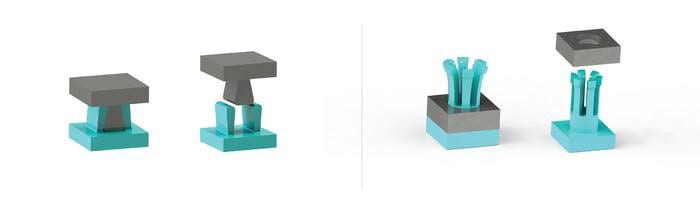
Interlocking metasurfaces could provide more structural strength and stability than traditional mechanical joining methods. Illustration courtesy Texas A&M Engineering
“ILMs are poised to redefine joining technologies across a range of applications, much like Velcro did decades ago,” claims Ibrahim Karaman, Ph.D., head of the Department of Materials Science and Engineering at Texas A&M. According to Karaman, active ILMs “have the potential to revolutionize mechanical joint design in industries requiring precise, repeatable assembly and disassembly.”
Practical applications include designing reconfigurable aerospace engineering components where parts must be assembled and disassembled multiple times. Active ILMs could also provide flexible and adaptable joints for robotics-enhancing functionality.
“In collaboration with Sandia National Laboratories, the original developers of ILMs, we have engineered and fabricated ILMs from shape memory alloys (SMAs),” explains Karaman. “Our research demonstrates that these ILMs can be selectively disengaged and re-engaged on demand while maintaining consistent joint strength and structural integrity.”
Using additive manufacturing technology, Karaman and his colleagues designed and fabricated active ILMs by integrating SMAs, such as nickel-titanium, which can recover their original shape after deformation by changing temperatures.
“Control of joining technology through temperature changes opens new possibilities for smart, adaptive structures without loss in strength or stability, and with increased options for flexibility and functionality,” says Karaman.
“We anticipate that incorporating SMAs into ILMs will unlock numerous future applications, though several challenges remain,” adds Karaman. “Achieving superelasticity in complex 3D-printed ILMs will enable localized control of structural stiffness and facilitate reattachment with high locking forces. Additionally, we expect this technology to address longstanding challenges associated with joining techniques in extreme environments.”