Wire Harness Benches Increase Production.
Tolerances have to be consistently tight when you’re assembling wire harnesses for a jet fighter – 1/8 of an inch over 32 feet to be exact. Workbenches that can’t accommodate such tolerances would be, well, intolerable.
That’s the problem that a jet manufacturer faced when they determined that they needed to upgrade their facility. They were using pieces of plywood on A-frames for the assembly. This not only affected tolerance levels but also led to stress, strain and fatigue.
The jet fighter manufacturer found a company that could deliver what they were looking for in Proline. A leader in ergonomic workbenches. A company renowned not just for its rugged, technologically advanced workbenches, but also for its ability to “think on the fly” and produce, application-specific solutions, Proline met all of the jet manufacturer’s specs.
Thanks to the range of easy vertical movement provided by the Pro-Line benches, along with tilt, all sections of the wire harness are always within easy reach. Since this initial installation, this jet plane manufacturer is currently in the process of expanding its operation with additional Pro-Line workbenches. Clearly they are more than satisfied that they have harnessed such precise, ergonomically sound and productivity-enhancing workbench solutions.
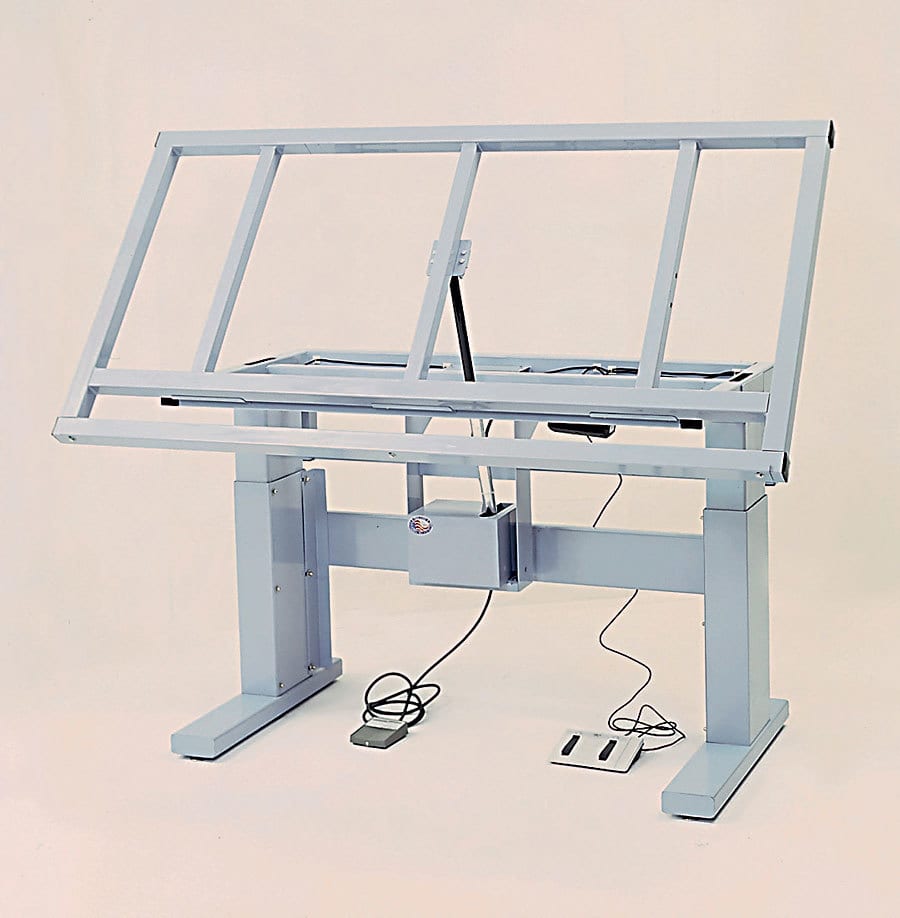
EMH Crane Lifts Animal Care
Prior to the EMH Crane installation at Zoo Atlanta, when large animals such as an elephant needed emergency care, the Zoo had few options. One option was using a fixed hoist. Unfortunately, that only worked when the elephant was situated close to an exact spot under the hoist where the elephant could be easily accessed.
During construction of Zoo Atlanta’s Zambezi Elephant Center, the decision was made to install an overhead EMH 7.5-ton overhead crane system with the new EG Series Hoist. The EMH crane covers the entire facility with a span of 70 ft. and a runway length of 128 ft. A hoist hook height of 25 ft. was considered perfect for emergency elephant lifting. The EMH Crane was also provided with NEMA 4 enclosures for water spray considerations, and a radio remote control that allows zoo personnel to operate inside or outside the elephant enclosures. According to Zoo Atlanta’s Lead Elephant Keeper, “Since African Elephants are tree-top grazers in their natural habitat, the EMH Crane installation also provides an important side benefit. With push-button and radio control, we can move the food around, engaging the elephants to enjoy a better experience while providing them with a little exercise.”
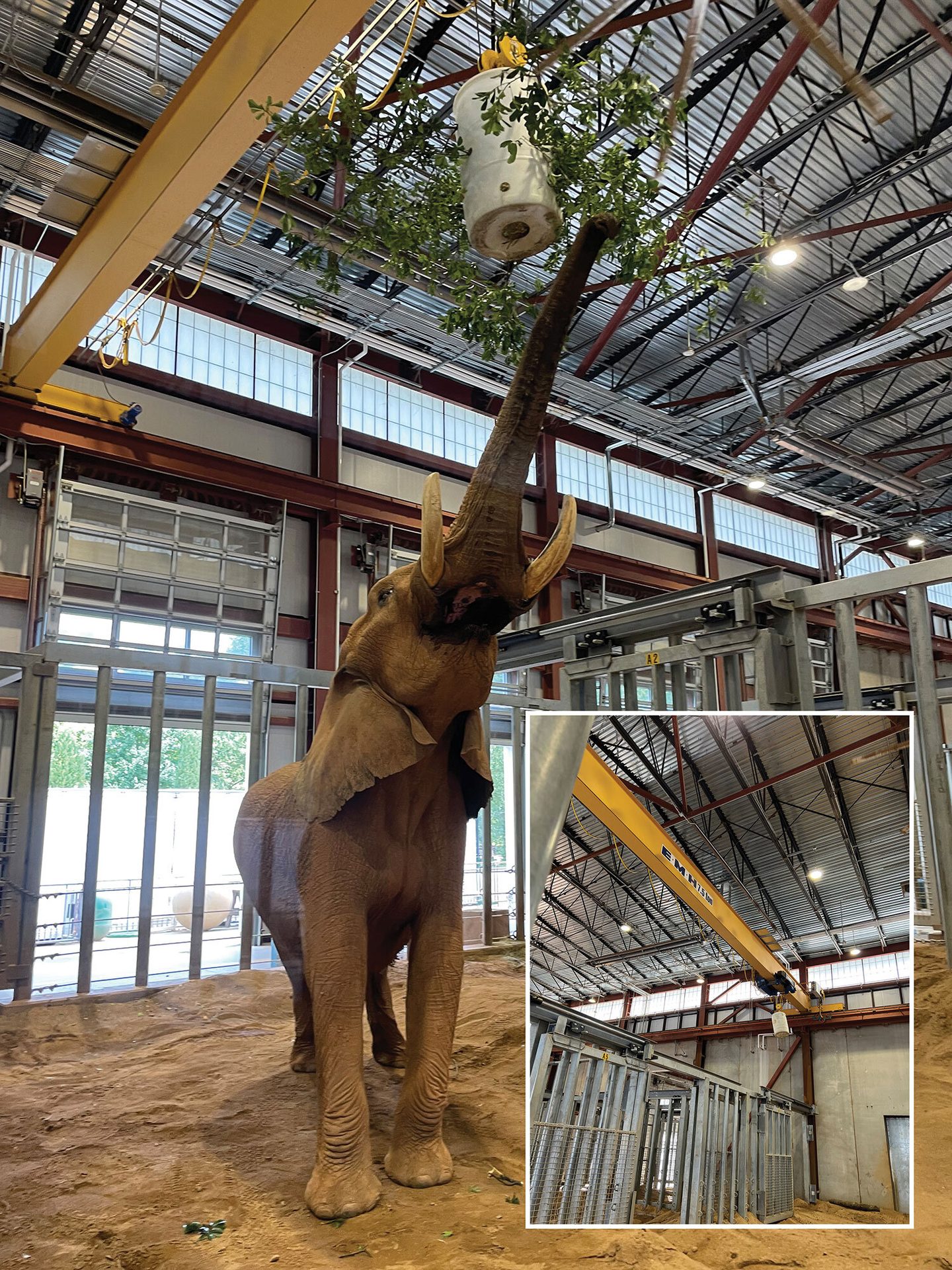
Meeting Market Deadlines with Scalable Automation
A leading medical device manufacturer faced a critical challenge: their initial automation supplier was falling behind schedule, jeopardizing a key product launch. Delays threatened substantial market share and revenue losses. Turning to Arthur G. Russell Co. (AGR) for a solution, the manufacturer required swift, effective action.
AGR responded with unparalleled speed and precision, delivering a 30 PPM (parts per minute) machine in under four months. This rapid solution ensured the product launched on time, safeguarding the manufacturer’s market position. Following this success, the customer quickly commissioned a second 30 PPM machine to meet growing demand.
AGR’s strategic approach also minimized risk. By validating automation concepts on the first two lines, AGR set the foundation for future high-volume production with proven technology and processes.
“Our unprecedented collaboration showcased the true power of teamwork and innovation,” said Jason Ensminger, President of AGR.
AGR’s scalable solutions not only addressed immediate challenges but positioned the customer for long-term success. With expertise spanning proof of principle to full-scale automation, AGR ensures timely market entry and the flexibility to scale efficiently as demand grows, making them a trusted partner in the competitive medical device industry.
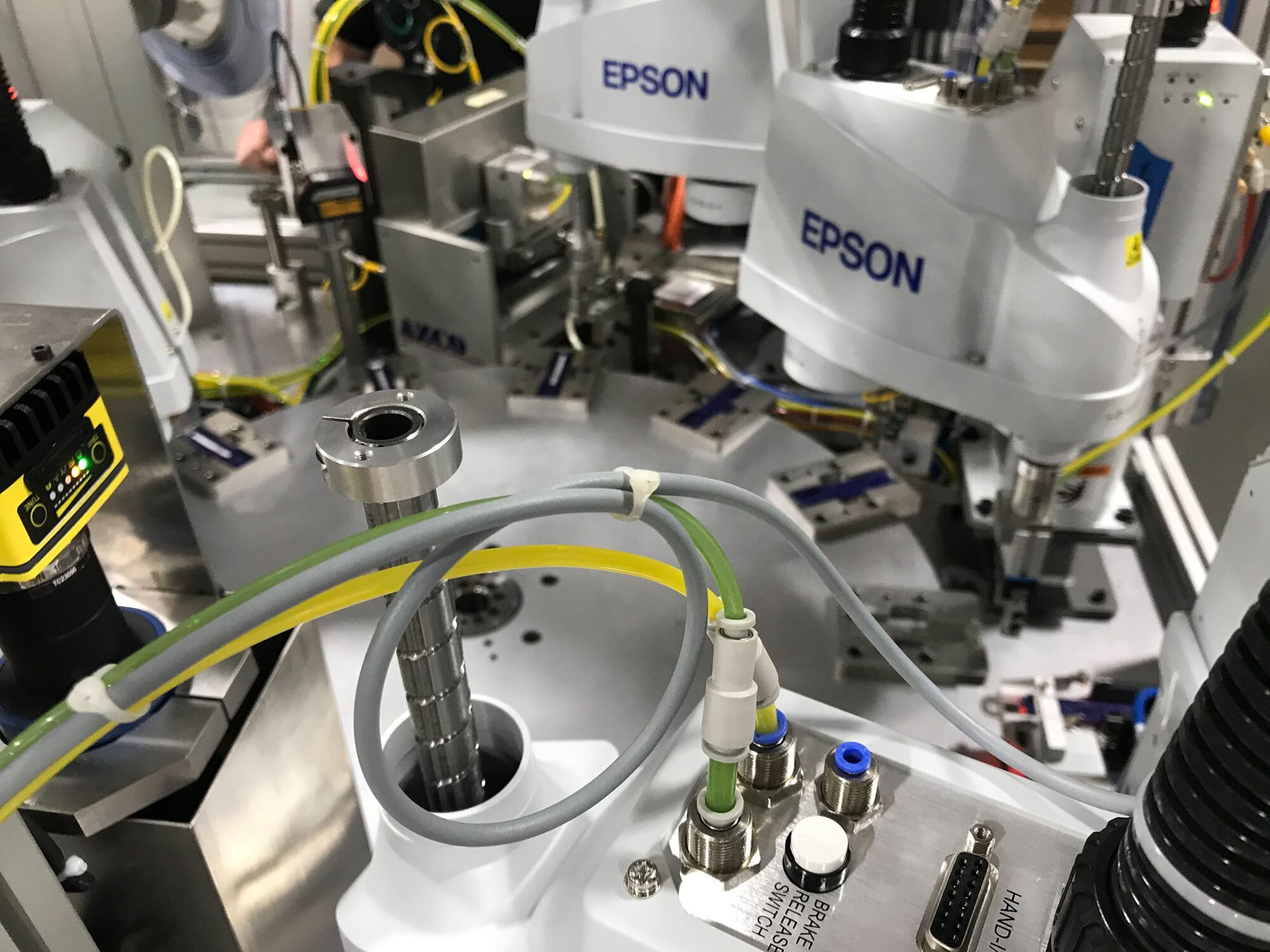
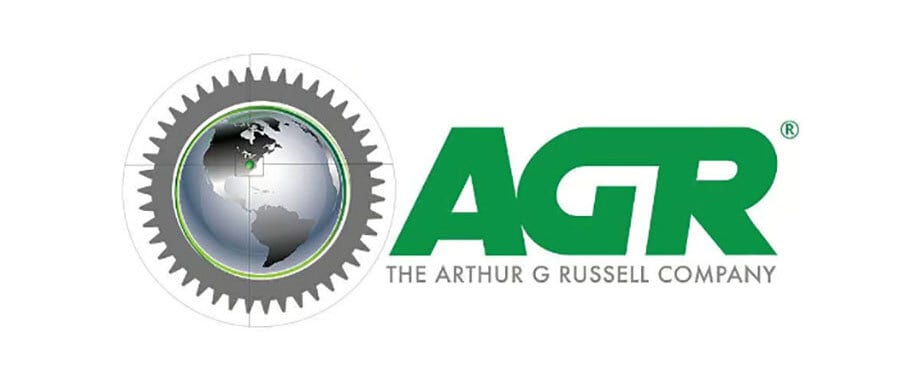
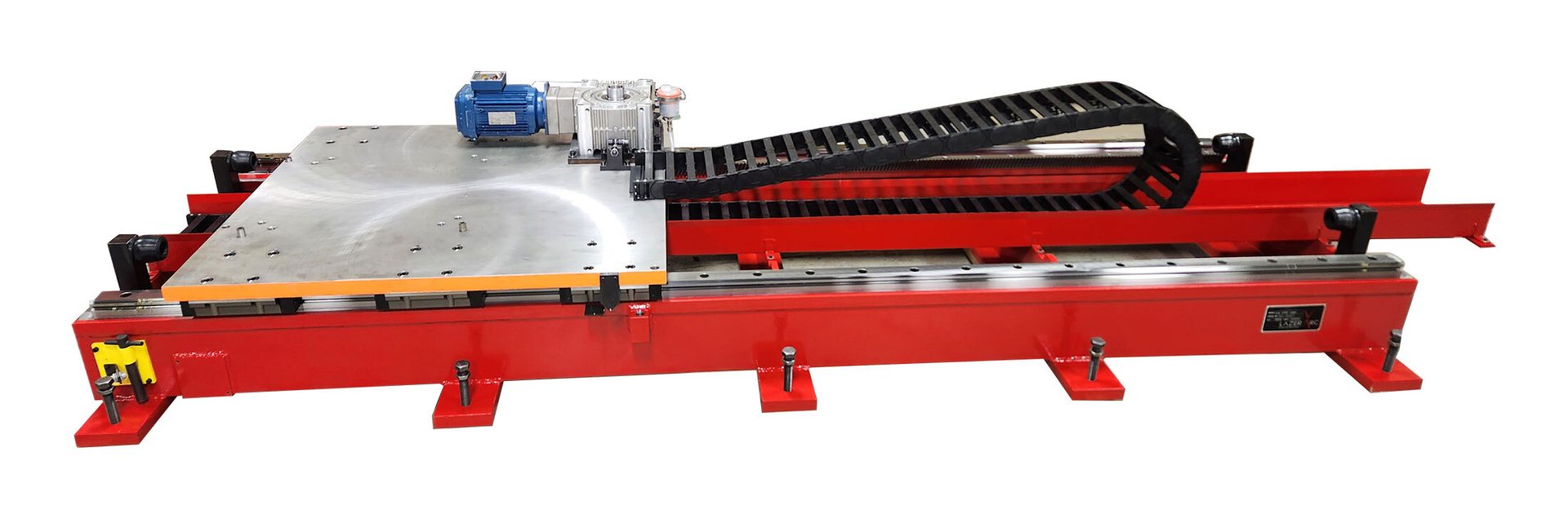
Linear Transfer Systems for Automotive Manufacturing
Our precise linear robot integrated solutions come in a heavy-duty design and custom lengths such as the Robot Transfer Unit. It is used to shift tooling or parts linearly with a standard accuracy - DIN 6 on gear rack +/-0.0003”/ft. Motion Index Drives’ Robot Transfer Units are manufactured with high-precision helical rack & pinions handling the high dynamic loads and required accuracy. To extend the reach of the robotic arm on the Robot Transfer System, it is placed on a support carriage on a seventh axis slide and rack & pinions were chosen to drive the axis. Multiple robotic arms can be placed on the same slide for additional productivity and flexibility.
This compact 10-foot Robot Transfer Unit is expertly designed for handling automotive parts with ease. Capable of managing 5500 lbs of moving load across its axis, it's built to accommodate a Fanuc Robot and ready to accept any robot brand motor. Featuring an automatic lubrication system and a scraper, it ensures zero maintenance on the linear guide rails. It comes equipped with hard stops and overtravel switches at each transfer's end for added safety.
Mixed Model, Labor Saving Cell
Worksmarts’ Fleximate® Transport System, consisting of modular ergonomic workstations joined together by a unique conveyor, enabled this assembly team to create a frictionless, mixed production flow while trimming labor. The synergy of transporting the WIP on Worksmarts’ Fleximate® carts, point of use subassembly presentation, and quick change fixturing with rotation, resulted in reductions of assembly time and wasteful handling.
The modular design and one tool requirement provided the means for the production management to further dial in enhanced work methods and continuous improvements. Other key features included mobile parts racks with gravity flow, integration of online test, and end of line product lifting and packaging.
The net results were increased throughput : seamless, mixed model production change overs and a dramatic, 35% reduction in labor . An additional dividend was a very quick ROI.Find out how Worksmart Systems’ Fleximate® Transport can easily provide the methods for your team’s transition to simplified, frictionless, mixed model, single piece, flow.
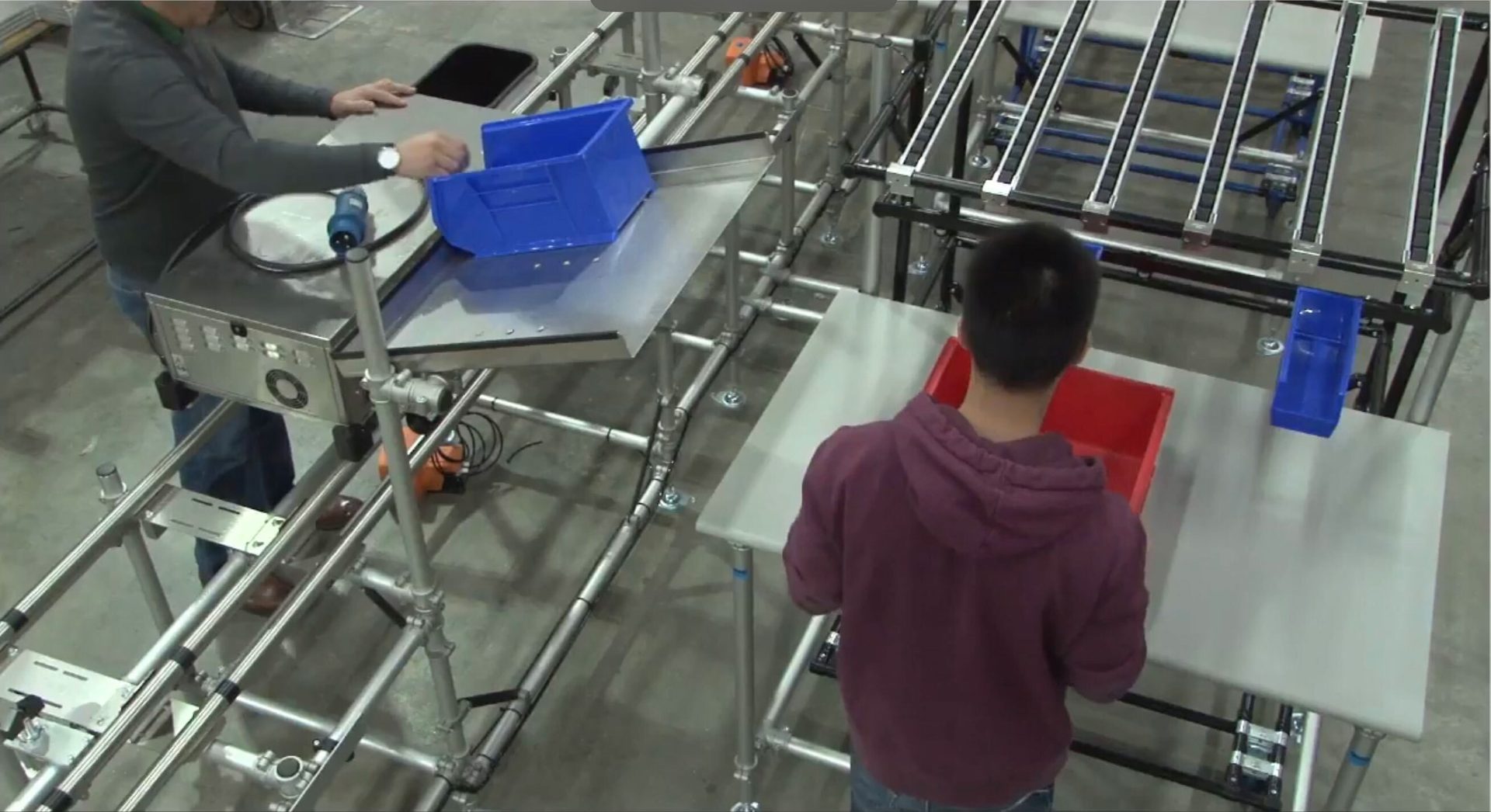
WEISS North America, Inc.
888-WEISSNA (888-934-7762)
info.us@weiss-world.com
Multipurpose Flexibility from WEISS
A consumer goods manufacturer recently decided to standardize on multipurpose assembly chassis with a flexible tool plate. Twenty chassis will be purchased as this customer standardizes and updates their assembly cells. Together with the customer’s in-house build team, WEISS provided custom-designed chassis with two tool plate variations.
Each chassis features a two-station TC120 indexer, a welded base, aluminum base plate, and aluminum tool plate with clear anodized finish, leveling plates with casters, aluminum side panels and lockable, hinged door, an aluminum indexer mount plate and extruded aluminum guarding with hinges and latches from Industrial Profile Systems, a wholly owned subsidiary of WEISS North America.
Initially contacted to provide the 2-station TC120 rotary indexers while the customer sourced other suppliers for the chassis, guarding, hardware, and other components of the design, WEISS proposed a single-source solution designed around proven and reliable WEISS automation components and value-added services. This provided the customer a simplified vendor sourcing/vetting process, proven platforms and components, faster time to completion, reduced lead time and overall cost savings due to economies of scale.
To learn more about WEISS, please visit www.weiss-world.com or call one of our automation pros today at 888-934-7762.
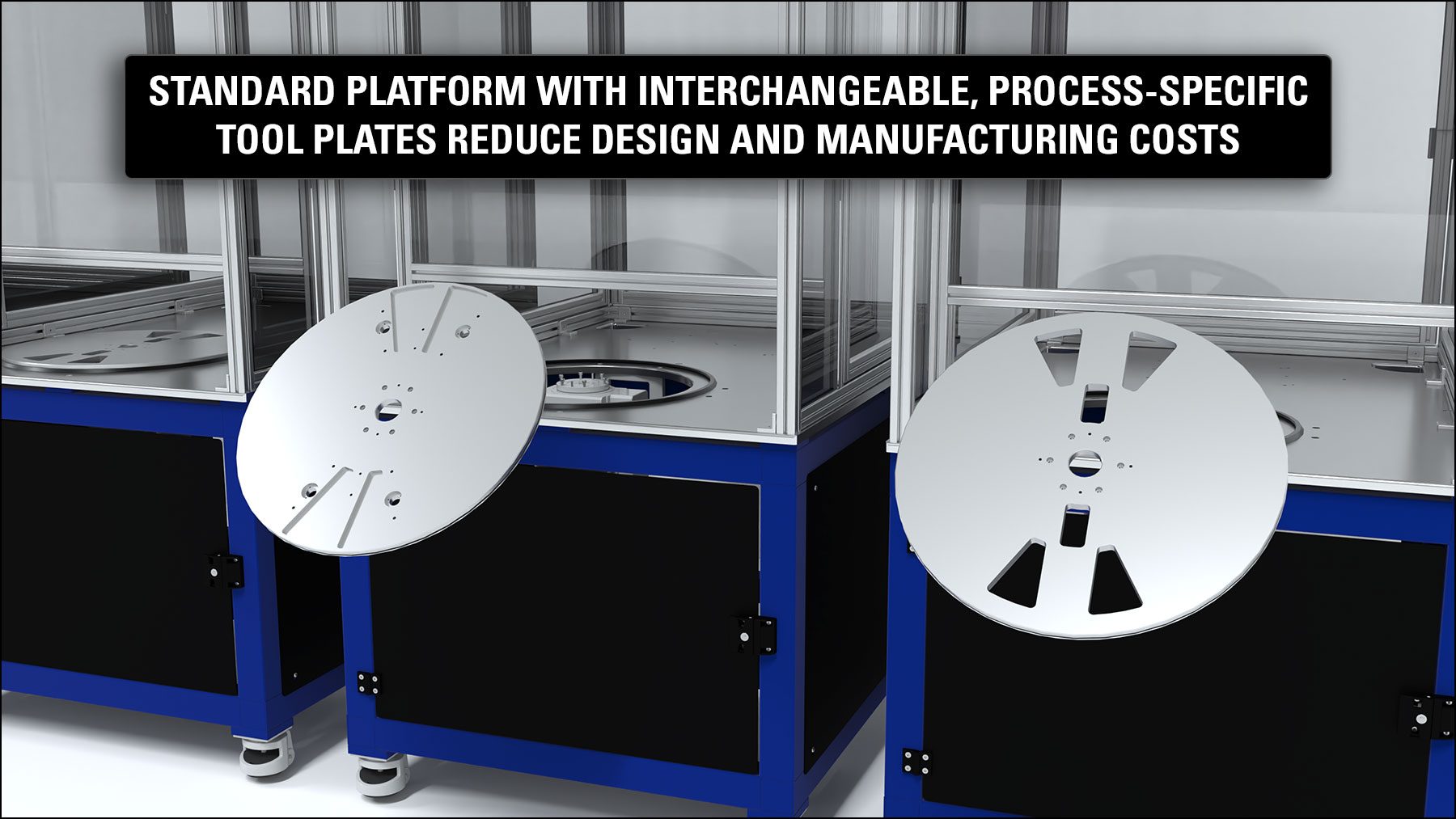
Promess Inc.
810-229-9334
promess@promessinc.com
Tailored Electric Press Work Stations
The Promess Electric Press Work Station is a stand-alone unit with an integrated Promess Electro Mechanical Assembly Press (EMAP). The EMAP is a programmable motion-controlled ball screw press with integrated motion control and monitoring. Promess offers 33 press sizes with capacities ranging from less than an ounce to over 200,000 pounds. The Work Station is designed to meet your specific application needs, and Promess offers various standard floor and table top stations to fit your needs.
The Work Station provides a mobile and readily accessible foundation for assembly, test, and lab applications. Being fully electric and energy-efficient, it also contributes to a cleaner work environment, which is not possible with traditional workstations.
To find the perfect Work Station configuration for your application, schedule a visit to the Promess facility or send in your parts for assessment. There is a range of Work Station configurations available on-site for viewing, and the Promess Process Development Center can help validate your process. Contact Promess today for more information on the Electric Press Work Station.
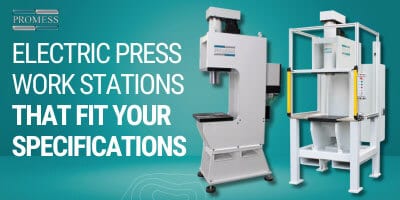
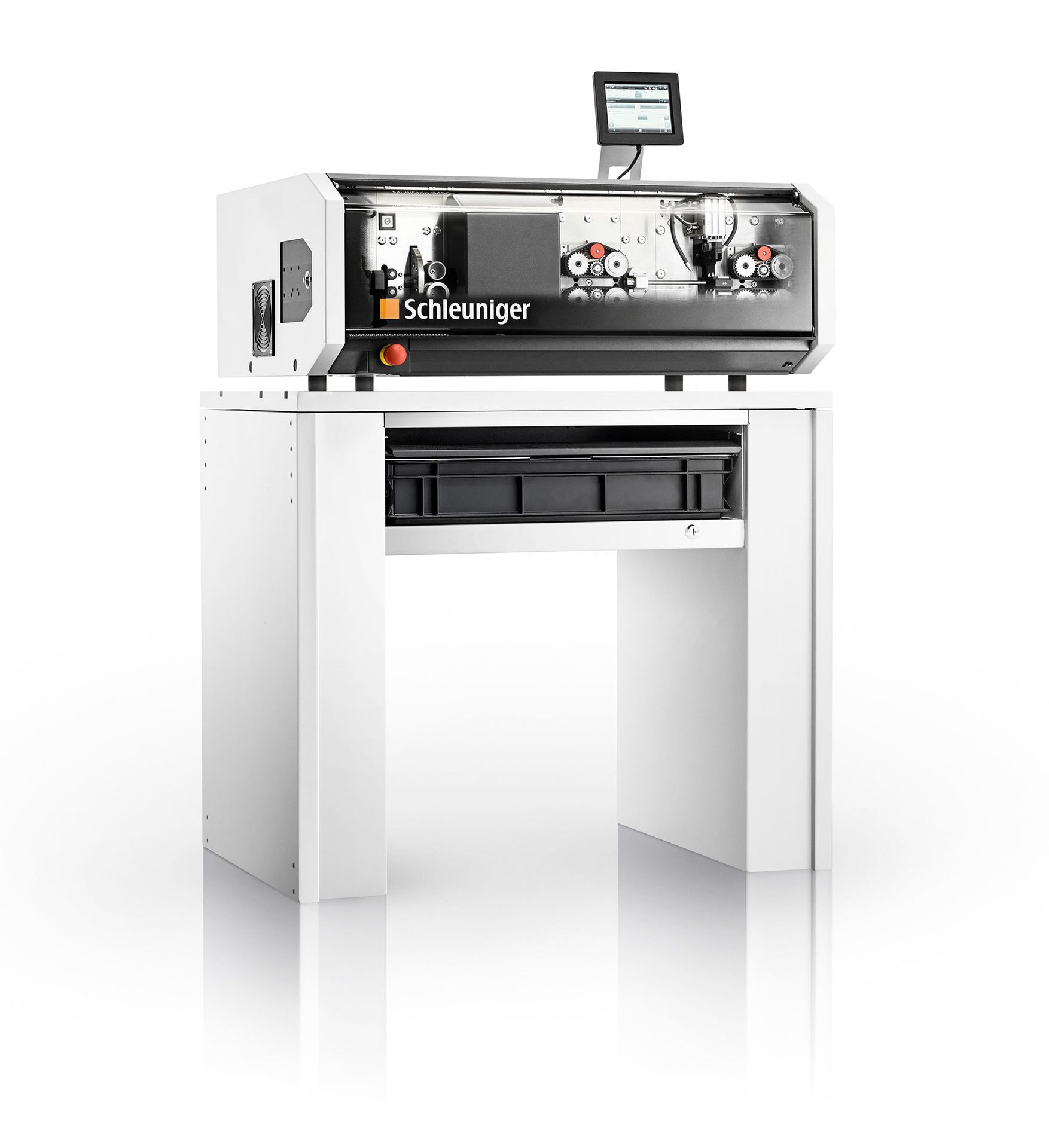
Buckeye Electrical Streamlines Production with Schleuniger
Buckeye Electrical is a family-owned custom wire harness and cable assembly manufacturer located in Botkins, OH. The company strives to offer its customers high-quality products and recognizes the value of efficient, reliable equipment.
After President Kevin Platfoot noticed that outdated machinery and manual processes were hindering precision, efficiency, and turnaround, he took decisive action to research and invest in new equipment.
With assistance from Schleuniger Sales Representative Bruce Moore, Platfoot determined the MultiStrip 9480 and PowerStrip 9580 would help streamline the processing of Buckeye's primary range of cables, including 8–18 gauge hook-up wire and coax multiconductor, and battery cable.
Since modernizing, Platfoot reported, "We [now] process around 12,000,000 feet of wire per year using three cut and strip machines, which would have been unfathomable before.” He also commended Cayman, Schleuniger's cut and strip software, for its seamless usability and file sharing.
Another noted improvement is the Multistrip 9480 and Inket printer integration, which increased marked wire output by 50%.
Overall, restructuring has been game-changing, and Platfoot shared he is looking to purchase additional Schleuniger machines to help with company expansion. For small manufacturers considering equipment upgrades, he shared, “it will be crucial to continue to pursue automation to remain competitive.”
Schleuniger, Inc.
603-668-8117
Toll Free Technical Support: 877-902-1470