JANUARY 2023
A highly automated manufacturing process helps first solar compete with cheap imports.
text
First Solar’s Series 6 modules are made using less energy, less water, and less semiconductor material than competing modules. Photo courtesy First Solar Inc.
Labor shortages are driving new demand for automation.
Jennifer Pierce // Multimedia Editor
Every day in more than 45 countries, photovoltaic modules designed and manufactured by First Solar go to work converting sunlight into clean, reliable electricity. First Solar is the only American company ranked among the world’s top 10 solar manufacturers. The company’s headquarters is in Tempe, AZ, but its roots are in Ohio, where it operates the largest solar manufacturing footprint in the Western Hemisphere. More than half of First Solar’s 2,700 U.S. employees are located in Ohio.
What’s more, First Solar’s U.S. manufacturing footprint will soon be getting even bigger. In August 2021, the company begun construction of a new $680 million solar module assembly plant near its existing factory in Perrysburg, OH. That factory—the company’s third—is expected to come on line this year. And, in November 2022, First Solar announced that it will invest more than $1 billion to build a fourth assembly plant in Florence, AL. Expected to create more than 700 jobs, the factory is part of a previously announced plan to increase First Solar’s U.S. manufacturing capacity to more than 10 gigawatts by 2025.
The Alabama project will bring the company’s total investment in U.S. manufacturing to more than $4 billion.
The company also operates factories In Malaysia and, soon, in India.
To get the scoop on all this investment, we sat down with Mike Koralewski, chief manufacturing operations officer for First Solar.
ASSEMBLY: Why is First Solar producing photovoltaic modules here in the U.S.?
Koralewski: First Solar is the only American company among the world’s largest solar manufacturers. We’ve been producing modules in Ohio since we first started manufacturing back in 2002. Our module technology is uniquely American: It was developed in our research and development facilities in Ohio and California.
The U.S. is also our single largest market. In the past several years, the U.S. solar industry has had to contend with amplified political and trade risks as a consequence of the tariffs employed to protect our markets from anti-competitive practices by Chinese solar manufacturers. In addition, challenging conditions in ocean freight over the past several years really impacted the ability to ship modules around the globe.
All that has led to an increase in demand for domestically made modules, and we are aligning our manufacturing capacity to accommodate that.
All the major players in the solar industry are now thinking about the shortcomings of maintaining a single global hub for manufacturing. Locating our supply chain and manufacturing as close to each customer base as possible allows us to mitigate a lot of the negative impacts associated with overreliance on transoceanic shipping. It allows us to be competitive with our pricing and to provide a reliable supply to our customers moving forward.
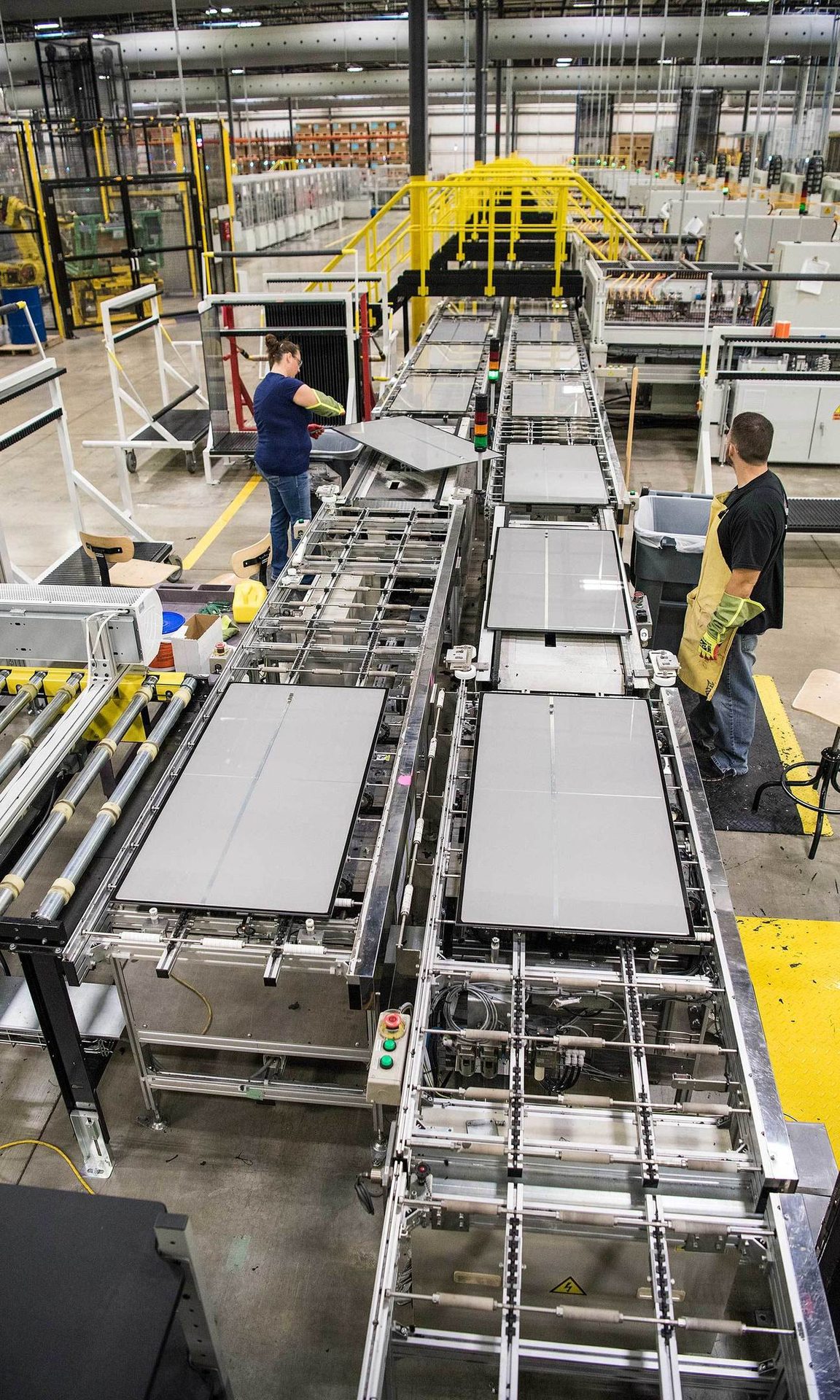
First Solar’s factory in Ohio can turn a sheet of glass into a fully functional photovoltaic module in just four and a half hours, end to end, all under one roof. Photo courtesy First Solar Inc.
ASSEMBLY: First Solar’s factory in Ohio can turn a sheet of glass into a fully functional photovoltaic module in just four and a half hours, end to end, all under one roof. In contrast, competing products can take days to make. How can you produce modules so quickly?
Koralewski: Our factories are among the most advanced in the solar industry, using technology and process optimization that effectively competes against Chinese-made solar panels that are only cheap because they’re heavily subsidized by the government. To compete with the Chinese, we needed to leapfrog their technology with American ingenuity and innovation.
So we really push on cycle time and throughput. The key is our thin-film deposition process, which is completely different than that of our competitors. Our process is actually more similar to making a flat-screen TV than a crystalline silicon solar panel.
We are vertically integrated, which also helps with speed. We go from beginning to end. We don’t have multiple factories producing individual components. We start with that raw sheet of glass and finish with a solar module by using a continuous process vs. a batch process like our competitors.
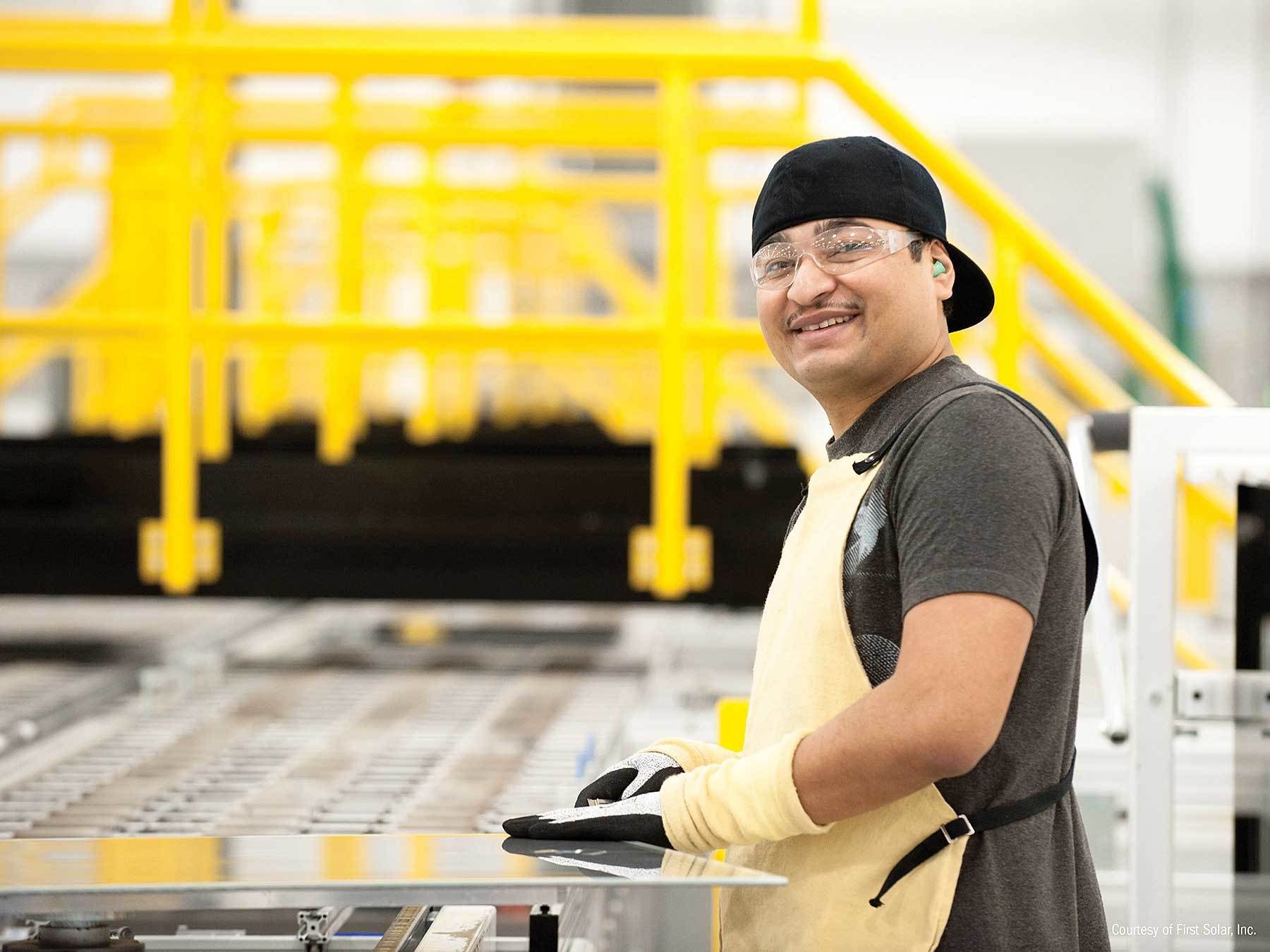
More than half of First Solar’s 2,700 U.S. employees are located in Ohio. Photo courtesy First Solar Inc.
ASSEMBLY: What’s the difference between a continuous process and a batch process?
Koralewski: Let’s say the first step in your manufacturing process is a washing operation. In a batch process, you might wash 100 modules at a time. You would then put those in a container and move that batch to the next operation in the process.
Our manufacturing process is continuous. Think of it like a highway, where one car is always followed by another. All of our assets are interconnected by a conveyor. You go from one process straight to the next one. There’s no batching. You just continuously flow from one process to the next.
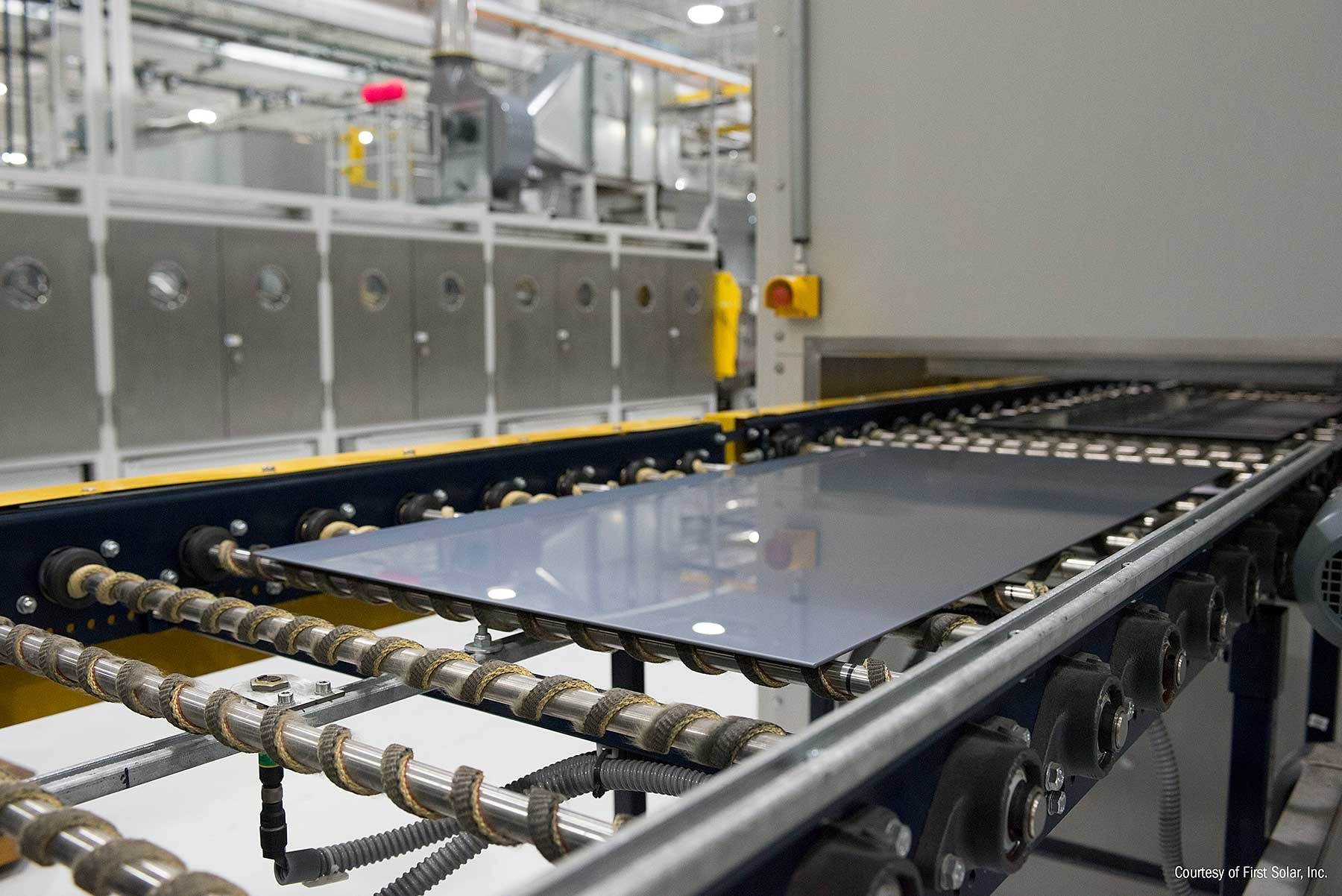
In May 2021, First Solar joined the Responsible Business Alliance, the world’s largest industry coalition dedicated to supporting the rights and well-being of workers and communities in the global supply chain. Photo courtesy First Solar Inc.
ASSEMBLY: What is the most challenging aspect of making a photovoltaic module?
Koralewski: One of the most challenging aspects, at least for U.S. manufacturers, is ensuring a level playing field for our products. Eight of the top 10 solar panel manufacturers are Chinese companies that benefit from unfair subsidies and other forms of government support that contravene World Trade Organization rules on fair trade. For example, many Chinese companies practice unfair trade policies, such as dumping photovoltaic panels at prices that are designed to decimate international competitors. Other manufacturers circumvent trade duties by routing products through Southeast Asia even though they’re actually made in China.
We are building a competitive, responsibly produced, high-quality product, but we spent a tremendous amount of time and resources fighting for fairness.
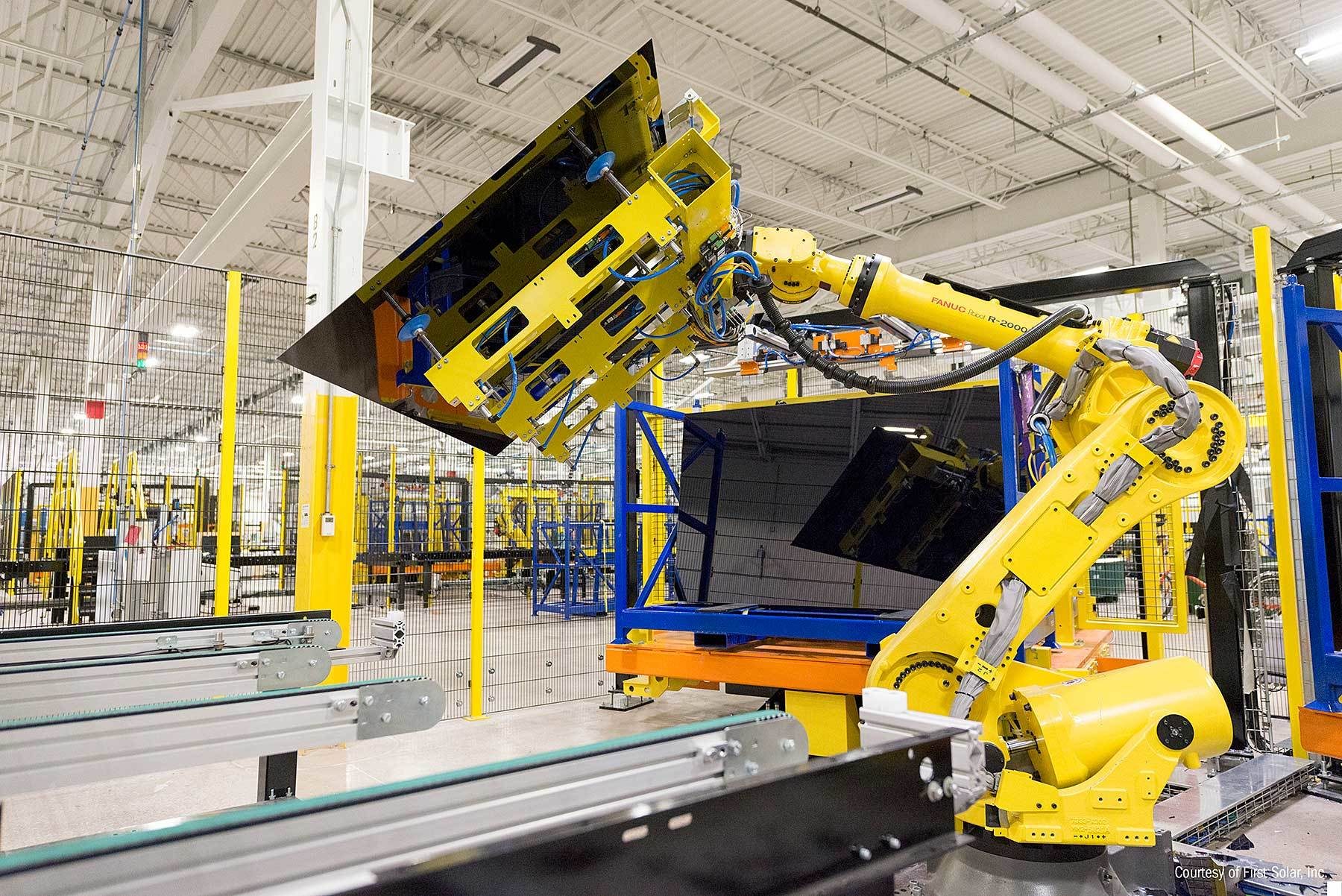
First Solar’s assembly plant in Perrysburg, OH, is highly automated. Photo courtesy First Solar Inc.
ASSEMBLY: First Solar’s Series 6 modules are made using less energy, less water, and less semiconductor material than competing modules. Can you talk more about your company’s commitment to responsible solar?
Koralewski: Our vision of leading the world’s sustainable energy future is important to us. Sustainability has been at the heart of everything that we’ve done since the beginning. It’s not focused on meeting industry standards. It’s set on exceeding them and setting new ones for others to follow. We’re proud to produce solar technology that meaningfully supports the fight against climate change. And, we consider both the social and environmental impact of our operation, and we work hard to make people’s lives healthier now and in the future.
Our thin-film modules have a carbon footprint that is two and a half times lower than crystalline silicon. Our modules are recyclable and actually boast a recovery rate of about 90 percent of its of its value, which includes the semiconductor, the glass, the capsule and several other materials. As a matter of fact, the new modules that we’re making today actually contain about 10 percent recycled semiconductor, which is unique to the photovoltaic industry today.
Our approach to responsible solar continues to be a significant reputational differentiator in the solar manufacturing industry, not only from a sustainability aspect, but in the in the true meaning of responsibility. There are reports of forced labor in the crystalline silicon supply chain in Xinjiang, China. We do not support that.
In May 2021, we joined the Responsible Business Alliance, the world’s largest industry coalition dedicated to supporting the rights and well-being of workers and communities in the global supply chain. We are the first of the world’s 10 largest solar manufacturers to join the alliance. So to us, sustainability not just a tag line; it’s actually the way that we conduct our business in every respect.
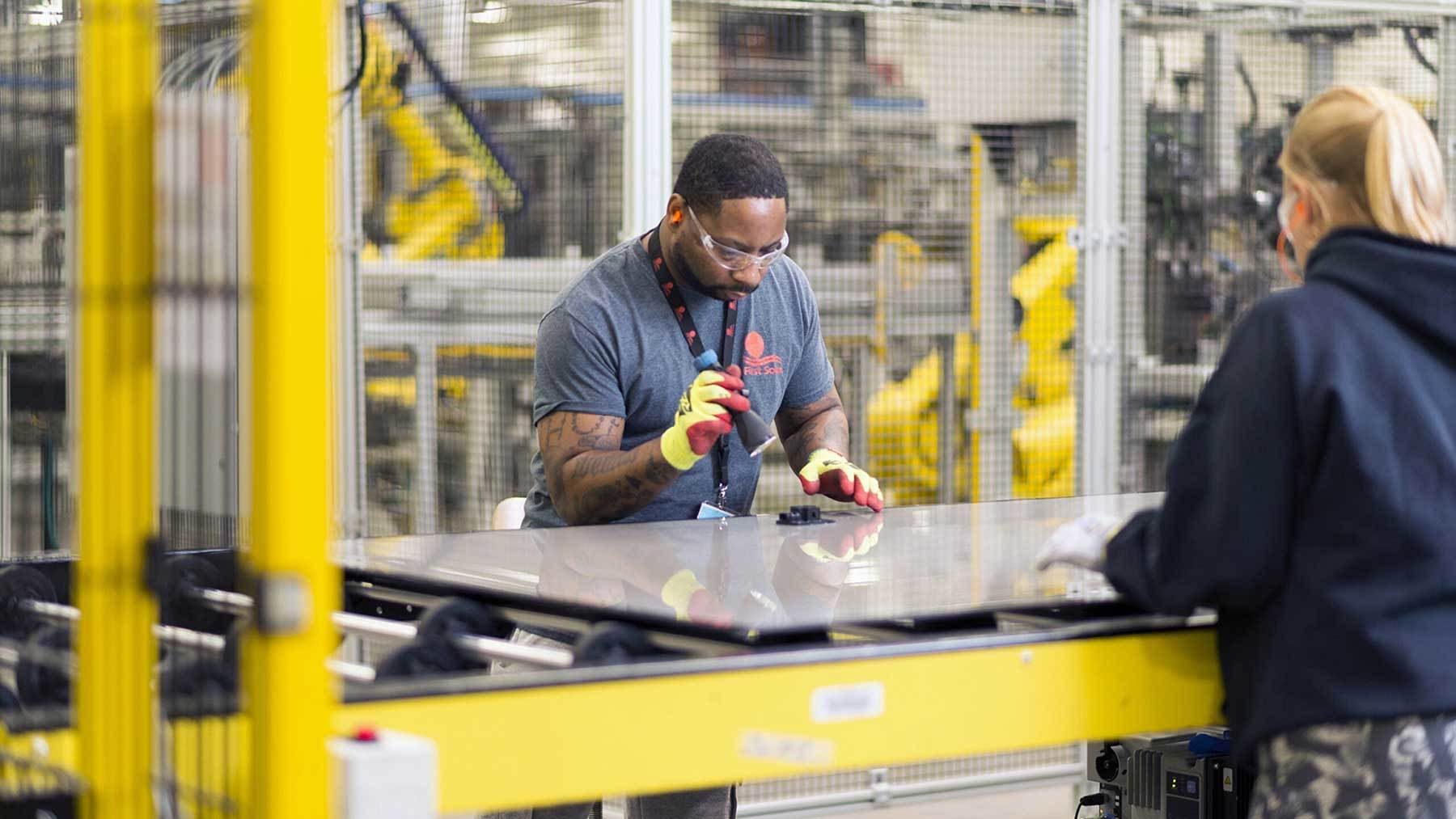
In November 2022, First Solar announced that it will invest more than $1 billion to build its fourth U.S. assembly plant. Located in Florence, AL, the factory is expected to create more than 700 jobs, Photo courtesy First Solar Inc.
ASSEMBLY: Last August, first solar broke ground on its third Ohio factory. Congratulations on that. How is the project going? Will you be doing anything differently with the new facility than you did with the first two?
Koralewski: The factory is right on track. Its walls are up. Roof is installed. Equipment is starting to ship into the facility now. We’ll definitely be ready by the first half of 2023.
This third factory will combine a highly skilled workforce and Industry 4.0 architecture, which includes machine to machine communication. We are eliminating human decisions and having our assets actually talk to each other. Artificial intelligence will control much of the manufacturing process. This will allow us to produce solar panels with a higher degree of automation, precision and continuous improvement.
We’ll have a module coming off the line about every 3 seconds across our northwest Ohio footprint. That’s pretty phenomenal when you think about it. The manufacturing setup in the new factory is a game-changer, and it represents to us a significant evolution in solar manufacturing. For instance, if you go back to 2012, a typical solar factory in First Solar would have employed about 1,200 associates and it produced about 250 megawatts per year. The new factory in Ohio produces 3.3 gigawatts per year with 700 people.
This level of advanced manufacturing is obviously great for the American worker, as well, because it allows us to focus on upskilling our associates. We are creating people who are capable of troubleshooting our process, rather than serving on the line, moving pieces and parts.
ASSEMBLY: What role do people play in First Solar’s production lines?
Koralewski: We believe in upskilling our people. It’s very important to us. We want our people to feel like they work in a high-tech environment that is safe and clean. We offer good wages and benefits, healthcare, tuition reimbursement, internal career progression, and wellness programs.
We also partner with local community colleges, universities and vocational schools to train our people effectively to grow into these roles. As our technology advances, we want our people to advance as well.
Editor’s note:
This article is based on an interview we recorded for ASSEMBLY Audible. This podcast explores the people, processes and technologies for assembling parts into finished products. Whether you make large products in small volumes or small products in large volumes, our goal is to provide insights, ideas and inspiration you can put to work. To hear the latest ASSEMBLY Audible podcast, click here.
ASSEMBLY ONLINE
For more information on solar panel manufacturing, visit www.assemblymag.com to read these articles: