JANUARY 2023
Robotics
Robots Assemble Pressure Sensors
High-speed system produces 4 million pressure sensors annually.
Labor shortages are driving new demand for automation.
Options for Screwfeeding
This robotic assembly line produces a tire pressure sensor every six seconds. Photo courtesy Stäubli Robotics
John Sprovieri // Chief Editor
Today, every car tire is equipped with a wireless pressure sensor that warns drivers of dangerously low pressure levels. Given that there are more than 1.5 billion motor vehicles worldwide, that equates to at least 6 billion pressure sensors.
The only way to meet that kind of production volume is with a high-speed, multistation automated assembly system.
Designing just such a system was the task given recently to systems integrator Modular Molding Systems GmbH (MMS). Based in Berndorf, Austria, MMS specializes in creating complete production lines that combine metalworking, injection molding and assembly processes. The company has built systems for high-volume production of sensors, switches and connectors for cars, appliances and medical devices.
The company’s customer for the automated line was Chinese automotive supplier BH Sens, one of the world’s leading manufacturers of tire pressure sensors. The project would require assembly of 10 components as well as various test and inspection steps. Availability would need to be very high, and cycle times would be short. Four million sensors per year was the target—one sensor produced every six seconds. Flexibility was also required. The system would need to assemble three sensor variants with different base plates.
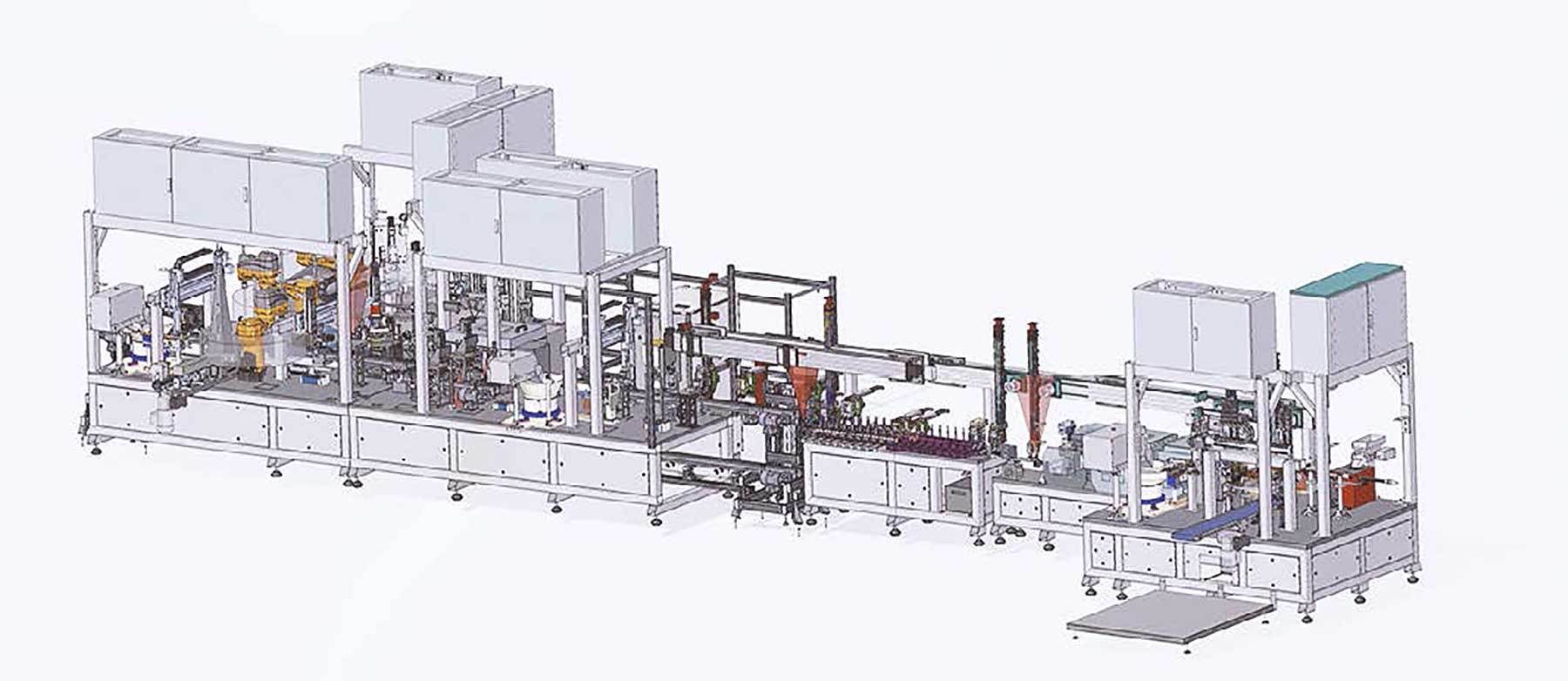
In a compact space, the integrated system combines numerous assembly and testing processes. Photo courtesy Stäubli Robotics
The heart of the system is a rotary indexing table. The components are handled by three Stäubli SCARA robots. The first robot, a large, four-axis TS2-80, removes a blank from a tray and places it in a pallet. The second SCARA robot, a TS2-60, picks up a battery from another tray and places it on the pallet. During this process, the SCARAs must not only work quickly, but also with precision, supported by a vision system.
The next step is three soldering stations on the rotary table, which connect the battery contacts to a circuit board. The assembly is then is placed in a housing. Next, a third Stäubli SCARA, a compact TS2-40, takes over, guided by a vision system, inserting a plastic seal.
Once the seal has been successfully fitted, the printed circuit board is placed on top and positively connected to the housing by hot caulking. Finally, the cover is placed on the housing assembly and welded airtight by a laser. Mounting of the sensor on a valve and installation of screws with an automatic screwdriving system complete the assembly.
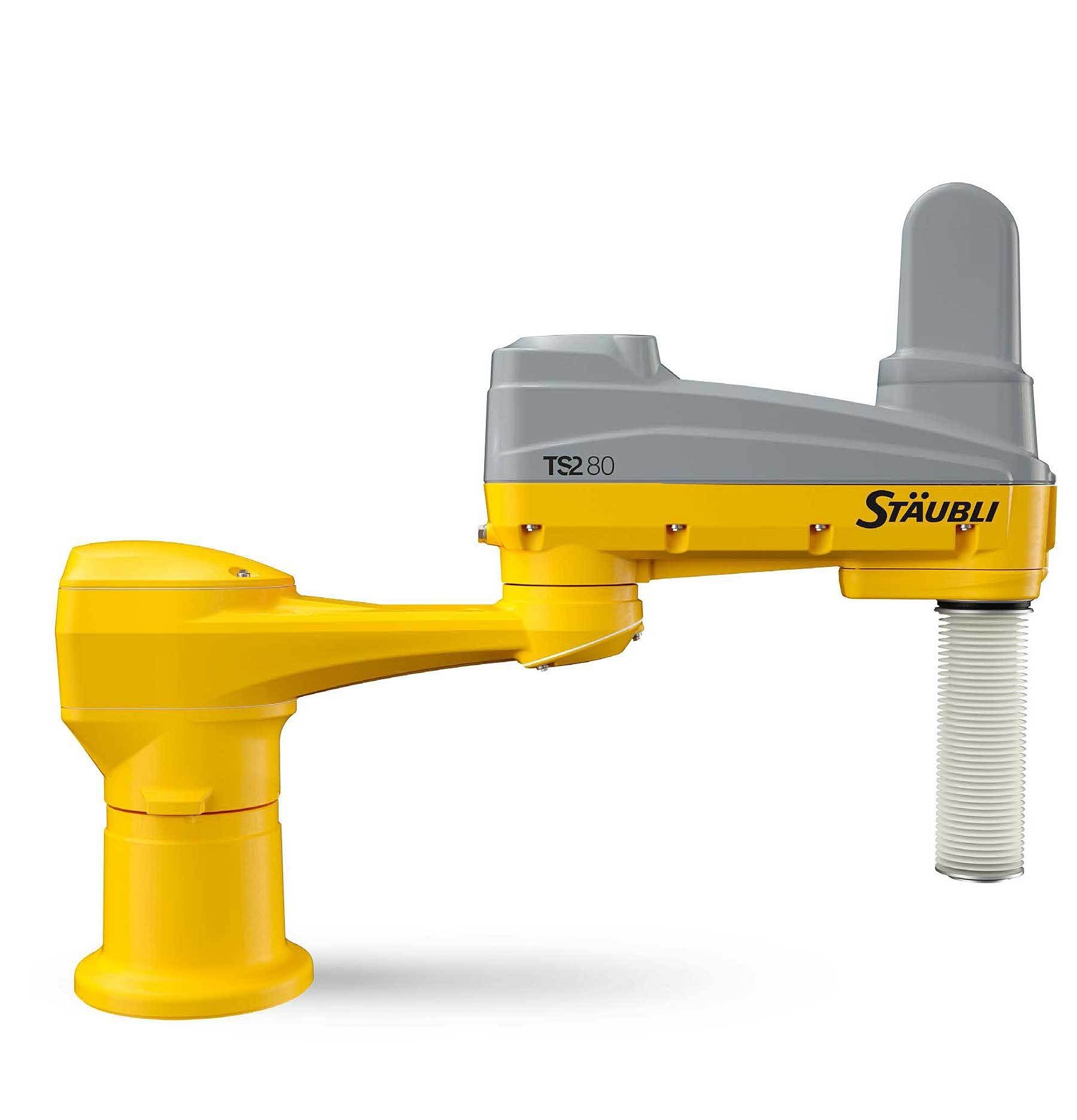

The TS2-80 can carry a maximum payload of 8.4 kilograms and has a maximum reach of 800 millimeters. Photo courtesy Stäubli Robotics
Today, every car tire is equipped with a wireless pressure sensor that warns drivers of dangerously low pressure levels. Photo courtesy BH Sens
Quality checks include a voltage test, a leak test, and a height check of the circuit board.
MMS engineers chose Stäubli’s TS2 SCARAs because of their ability to work with vision systems guidance, as well as their communication with the feeding systems.
The robots’ uniVAL PLC interface paid off when programming the system. It enables simple connection to the higher-level Siemens S7 controller. MMS meets the demand for flexibility by making it possible to change variants without having to modify the hardware.
The assembly system runs around the clock with short cycle times. Because the components are so small, long-term precision of the robots was important.
For more information on assembly robots, visit Stäubli’s website. For more information on automated assembly systems, visit MMS’s website.
ASSEMBLY ONLINE
For more information on robotic assembly, visit www.assemblymag.com to read these articles: