JANUARY 2023
ADHESIVES AND DISPENSING
Silicone Adhesives for Medical Device Assembly
Consider these factors when choosing a silicone adhesive for medical device assembly.
Labor shortages are driving new demand for automation.
Options for Screwfeeding
Formulated to quickly cure with the application of heat, HTV silicone adhesives are only available in two-part formulations. Fortunately, however, they are supplied in a convenient two-part dispensing cartridge with an airless mixing nozzle. Photo courtesy NuSil
James Darlucio // Senior Technologist For Biomaterials // Nusil, A Brand Of Avantor // Carpinteria, CA
The innovative medical devices that improve patients’ quality of life require robust materials that meet specific manufacturing and end-use demands. Many medical devices for use in or on the body are assembled from multiple components that need secure and reliable seals. That makes it critical for medical device manufacturers to make the right choice when selecting an adhesive.
From pacemakers to catheters, medical devices are made from a variety of materials such as rubber, plastic, silicone and metal. Silicone adhesives are often used to join and seal these devices.
But, choosing the right silicone can be a challenge because there are numerous functional and technical factors to consider. Medical-grade silicone has long been relied on for its biocompatibility, its purity and the ease with which it can be customized to satisfy the critical requirements of medical device specifications.
Whether a device uses a silicone adhesive as a sole joining element or in conjunction with a physical or mechanical element, like a pin, it’s important to consider the factors that can guide adhesive selection and help ensure efficient and reliable use of silicone adhesives in device assembly. By following these tips, medical device manufacturers can run their assembly operations with greater efficiency and with assurance that their medical devices are fully and reliably joined.
Know Your Silicone Adhesive Options
Many factors, from substrate to surface energy, will determine the best silicone adhesive for specific applications. There are two main types of silicone adhesives: room-temperature vulcanizing (RTV) adhesives and high-temperature vulcanizing (HTV) adhesives.
Traditional RTV silicone adhesives cure when exposed to atmospheric moisture at room temperature. If minimal heat is applied to these formulations, device manufacturers can accelerate the curing process. Silicone manufacturers also offer RTV formulations that do not rely on moisture to cure, offering even more versatility.
There are two types of RTV adhesives to consider: One-part, moisture-cure RTV adhesives and two-part RTV adhesives.
One-part, moisture-cure RTV adhesives are the most common silicones used in medical devices. These formulations can be applied directly without premixing. They are commonly available in self-leveling formulations that flatten or spread out over time. Due to the chemical mechanism of their curing method, they can shrink during cure, typically between 3 to 6 percent of the original volume, which should be taken into consideration when selecting this type of formulation.
One-part, moisture-cure RTV adhesives are available in self-leveling formulations that flatten or spread out over time. Photo courtesy NuSil
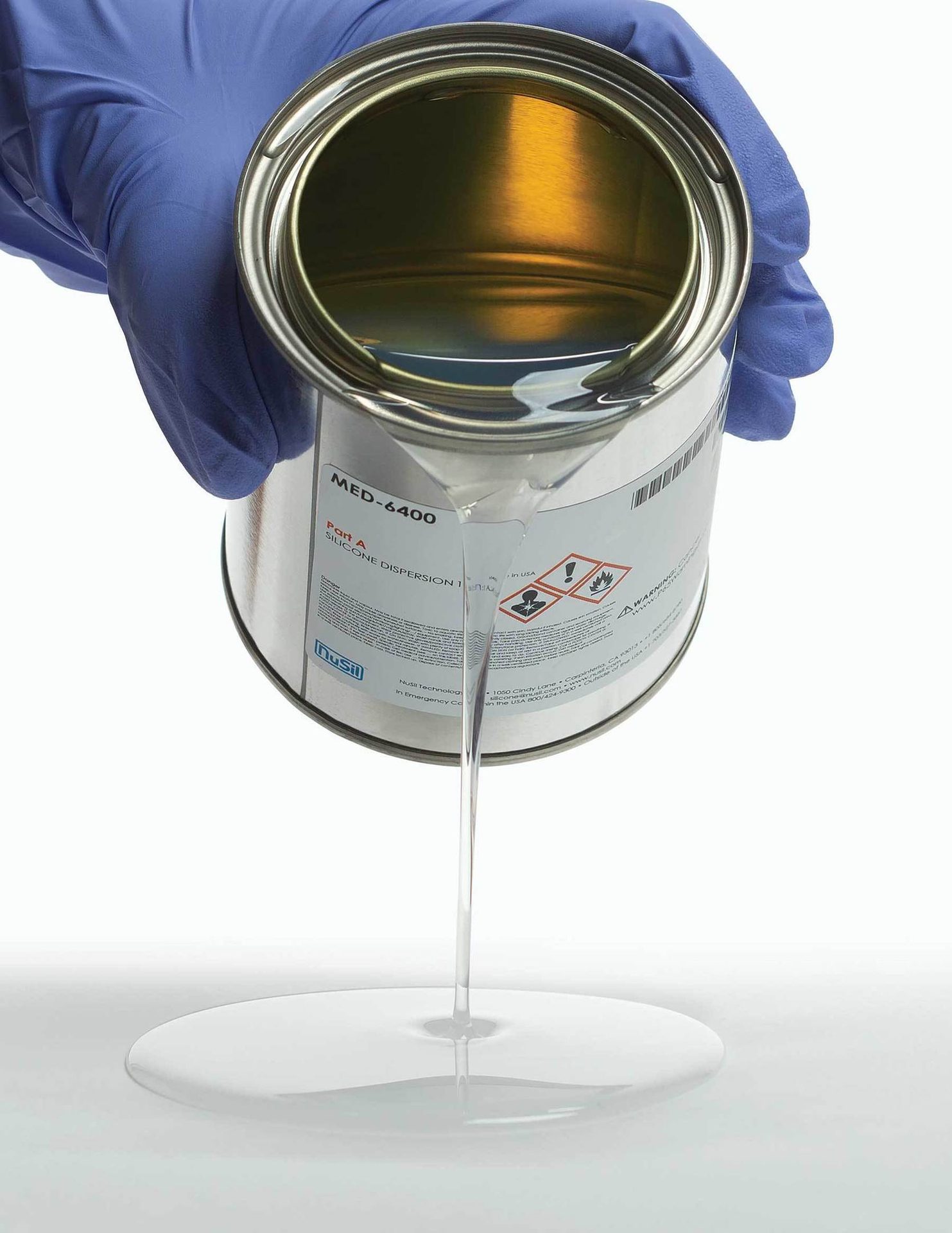
Two-part RTV adhesives are versatile formulations that require much shorter cure times than one-part materials. Because two-part RTV adhesives do not require moisture to cure, they can meet unique assembly requirements, such as forming bonds at interfaces that have little or no access to air. These adhesive formulations are also ideal in applications with temperature-sensitive components and assembly processes where a relatively low temperature must be maintained.
Formulated to quickly cure with the application of heat, HTV silicone adhesives are only available in two-part formulations. Fortunately, however, they are supplied in a convenient two-part dispensing cartridge with an airless mixing nozzle. Consider these adhesives for bonding parts that are not heat-sensitive or when a quick cure is desired to reduce device assembly time.
Understand Surface Energy
Whether a medical device is implanted, inserted or used externally, it is often made of one or more materials, such as silicone, metals (stainless steel and titanium), polyurethane, or plastics like polytetrafluorethylene, polycarbonate, PEEK or polyimide.
Silicone adhesives can be used to seal two pieces of the same substrate, whether plastic, silicone or metal. These formulations can also be used to join and seal two different types of material, such as silicone to metal or silicone to plastic. Depending on the substrates, simply applying the silicone adhesive may not provide the desired level of bonding.
Understanding the surface energy, or wettability, of each substrate being adhered is critical, especially if different substrates are being joined. In general, wettability is the factor that defines how a substrate will accept a coating. For example, a low-energy material like polyethylene does not allow a liquid adhesive to easily spread outward across its surface, creating blank spots on the substrate where the adhesive should be. This situation makes it more likely that adhesion will fail.
Once the surface energy of the substrates is considered, you can better prepare the substrate surface for proper silicone adhesive application.
Understanding the surface energy, or wettability, of each substrate being adhered is critical, especially if different substrates are being joined. Photo courtesy NuSil
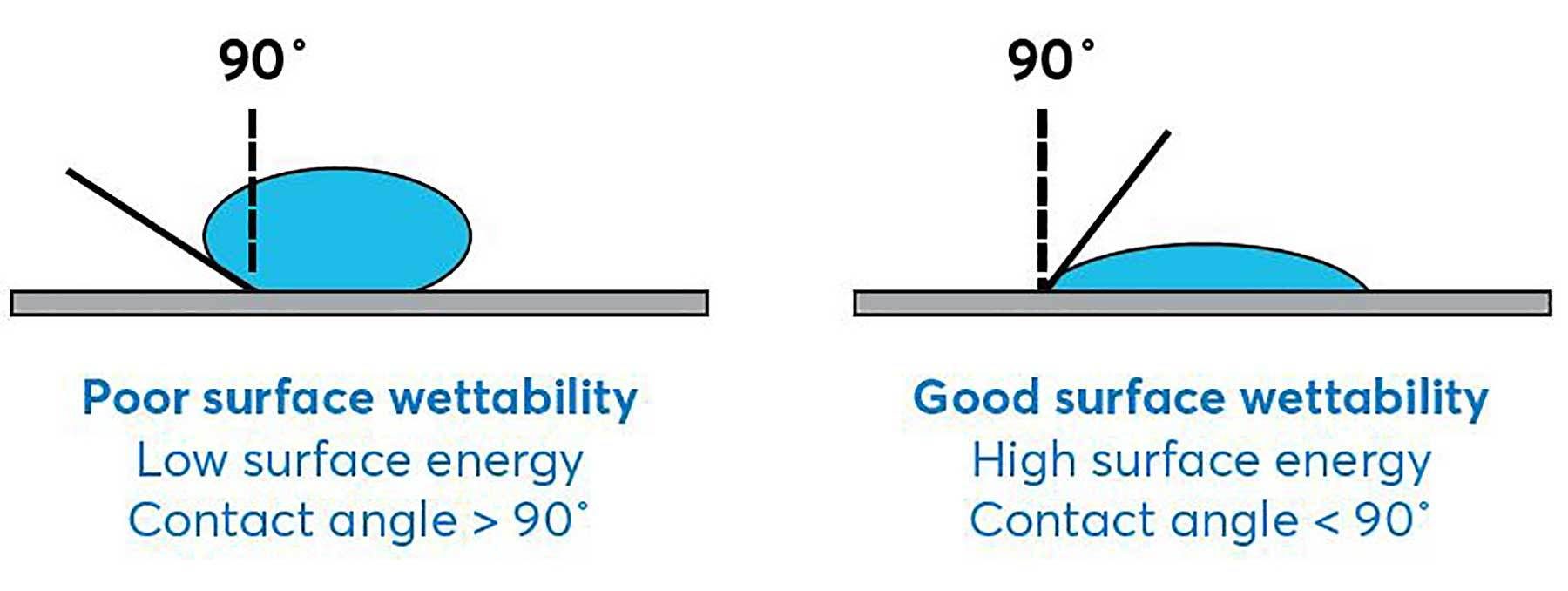
Proper Surface Prep
For substrates with low surface energy, engineers have several options to improve the surface energy and ensure proper adhesive application.
Simply cleaning the substrate may be all that’s required. Finger oils, dust, mold-release agents and machine oils can contaminate the substrate surface. Ensure a better bond by cleaning the surface with an appropriate solvent, such as isopropyl alcohol or heptane, using swabs or lint-free wipes.
Several treatments can also improve a substrate’s surface energy. Two common techniques are corona and plasma treatments. Both expose substrates to electrical charges in air as a way to prepare surfaces for better wettability and adhesion.
A third option is a primer. Primers are ideal for substrates with particularly low surface energy. They act as coupling agents, increasing the covalent bonds between the adhesive and substrate. Adhesive primers also work to increase the silicone adhesive’s ability to wet out on the surface of the substrate.
It’s important to note, however, that that primers are not “one-type-fits-all” solutions. Engineers should pick a primer based on the substrate, adhesive, device manufacturing process, and regulatory requirements.
Proper Surface Prep
The bond can be tested by many different physical, mechanical and chemical forces, which means that determining the acceptable failure point will differ from device to device and manufacturer to manufacturer. Tests based on a variety of real-world conditions can be key to confirming that adhesion is the best choice for the given application.
As you consider silicone adhesive manufacturers, it’s important to choose one with the application expertise and equipment to perform all the tests to qualify adhesion.
Suppliers can often custom-formulate a silicone adhesive to meet specific requirements. Photo courtesy NuSil
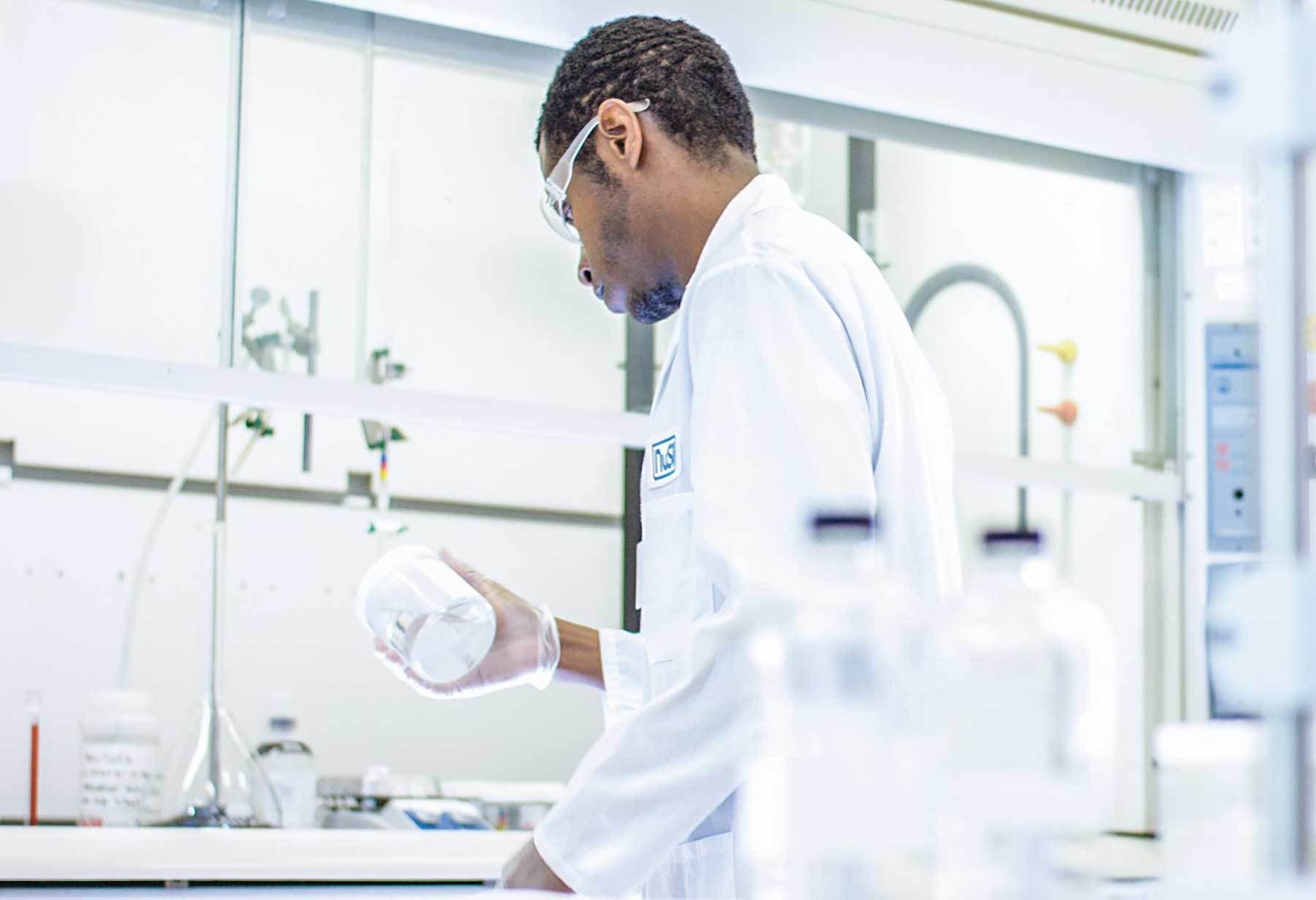
Avoid Cure “Poisons” And Contamination
A critical consideration when designing medical devices is that silicone adhesives in their uncured state may come into contact with solvents, chemicals or substrates that can retard or inhibit the curing process during handling, storing or assembly. Sometimes called cure “poisons,” these inhibitors can create unacceptable variations in the manufacturing process and in the finished product. The presence of inhibitors may cause the silicone to appear “wet” or tacky at the substrate interface after cure is complete.
For platinum-catalyzed silicone systems, watch out for inhibitors that contain sulfur, such as natural rubber, latex or neoprene; nitrogen, such as amines; or organotin, such as condensation-cured silicones. One-part moisture cure RTV silicones are not immune to cure inhibition. The most common inhibitor in moisture-cure RTV or tin-catalyzed silicone systems is the presence of an alcohol, such as isopropyl alcohol, a common cleaning agent in assembly environments.
To prevent inhibition, it’s critical to properly prepare the surface to ensure it is free of contaminants. Testing a small amount of silicone on the surface can help determine if the substrate surfaces have been properly prepared.
Choose A Partner
An adhesives supplier with deep expertise can guide you through the selection process as you consider a variety of adhesives, substrates and manufacturing processes. For example, an experienced silicone partner can provide insight on the appropriate silicone adhesive and primer to use for the specific application. They can also perform a wide range of tests to qualify adhesion requirements specific to your production or end-use needs. This capability should extend to the ability to provide custom silicone formulations if needed.
For medical device design, it’s essential to choose a supplier that can offer manufacturing and purity qualifications, as well as provide support during the regulatory filing process, such as providing device master files to the U.S. Food and Drug Administration.
ASSEMBLY ONLINE
For more information on adhesives and medical device assembly, visit www.assemblymag.com to read these articles: