JANUARY 2023
A special section to ASSEMBLY
What’s New With Harness Testing Technology
xxx
Electric vehicle applications are driving the need for higher test voltages than have historically been required. Illustration courtesy Huber+Suhner
Austin Weber // Senior Editor // webera@bnpmedia.com
A large automotive electrical harness can contain hundreds of wires, dozens of connectors and several electronic components, such as relays and diodes. Despite crimp-force monitoring, pull-force testing and other checks, there’s no guarantee that every crimped connection will be tight, every inch of insulation will be undamaged and every wire will be inserted into its correct destination.
Whether it’s used in a vehicle that rolls, floats or flies, cable and wire harnesses must pass a battery of tests for continuity, functionality and safety. Testing ensures that things don’t go wrong, such as intermittent faults, misconnects, miswires, opens and shorts.
Operators can connect cables and wires to testers using a variety of methods, including plug-in boards, panels and rack-mounted configurations. A standard tester can simultaneously test 1,000 connections between points in 3 seconds.
Despite recent increases in high voltages and testing speeds, continuity testing remains popular. In fact, the basic process has remained relatively unchanged for decades.
The tester is typically located on either a fixture, harness board, test table or standard table. Manufacturers that use a board test harnesses as they’re being built. A test table features a series of connector blocks or tiles that serve as the mating fixture. When testing simple harnesses, it’s economical to use a standard table and standalone tester.
The operator sets the tester to a specified low voltage, such as 5 to 15 volts, and resistance threshold (in ohms), connects it to a mating fixture, and plugs all harness connectors into the mating fixture. The tester runs continuously.
Within fractions of a second, it generates and applies current to all wire test points in a specific sequence. Test results appear on the display panel. If no fault is detected, a pass is displayed, accompanied by a tone. When a fault is detected, the tester stops. It displays the connector and pin numbers, and indicates if the problem is a short or open circuit.
A short circuit occurs when too much current flows through wire. An open occurs when current flow stops due to high resistance.
The display stays on and prevents further testing until the problem is resolved. PC-based testers display this information on a computer monitor, often with pictures of the affected connections.
Low-Voltage vs. High Voltage
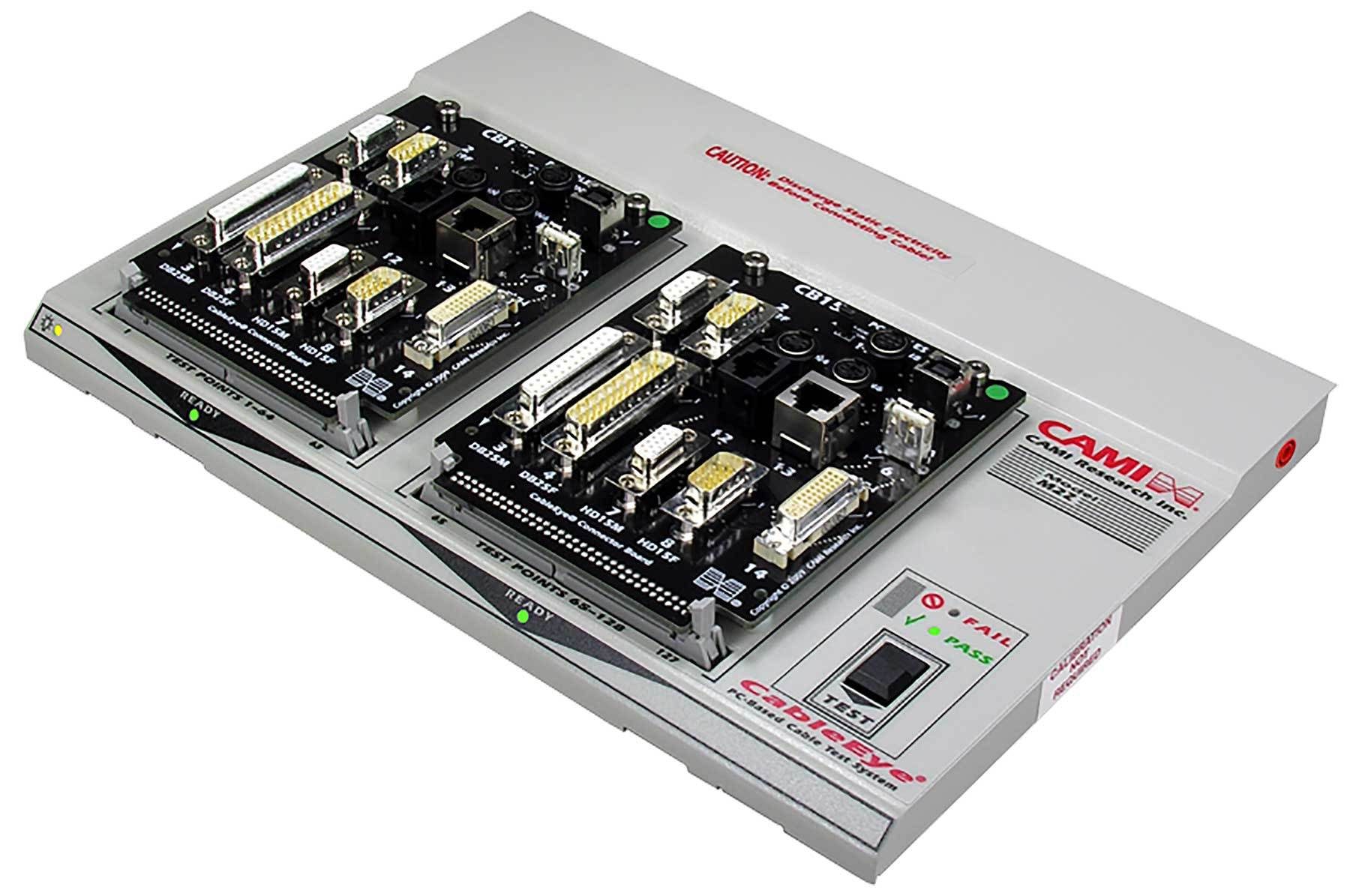
This entry-level tester provides basic continuity measurement in small wire harnesses. Photo courtesy CAMI Research Inc.
The term “high voltage” is subject to debate and often depends on a particular application. For instance, wiring harnesses used in airplanes or railcars typically have larger and more complex assemblies that require more test points and higher voltages than what’s found in household appliances or medical devices.
“Aerospace applications tend to be classified in the 500-, 1,000- and 1,500-volt DC range,” says Brent Stringham, director of sales, marketing and customer service at DIT-MCO International, a company that specializes in test equipment for aerospace, defense and rail applications. “In those industries, anything under 500 volts is deemed to be low voltage.
“Anything above 1,500 volts AC or 2,000 volt DC is considered be extra-high voltage,” Stringham points out. “In the rail industry, we even see some applications that require up to 5,000 or 6,000 volts DC and AC.”
“One of the biggest differences between low-voltage and high-voltage testing has to do with safety requirements,” adds Ryan Balcom, general manager at Electric Continuity and Components (ECC), a company that specializes in continuity fixtures to assist with the building and testing of wire harnesses. It also makes fixtures for functional testing of automotive components such as dashboard assemblies, front and rear fascias, and seat assemblies.
“Low-voltage continuity tests are typically done at a workstation in front of an operator with handheld devices,” explains Balcom. “The operator is there the entire time. High-voltage tests, on the other hand, must often be done in isolation away from people.”
Some low-voltage testers only perform continuity testing. Others have the capability to detect and actuate harness components, including relays, switches, sensors, capacitors, resistors, connectors and diodes.
High-voltage testers are often used for hipot (high potential) and isolation resistance testing. In a hipot test, 1,000 or more volts (direct current) is applied to all test points to see whether or not current flows from one point to another. If no current flows, the test points are properly isolated. Isolation resistance testing checks the quality of wire insulation.
Some benchtop products, such as CAMI Research Inc.’s popular HVX tester, can carry out both low-voltage and high-voltage fully automated testing. It’s one of the company’s CableEye cable and harness test system.
“After checking for opens, shorts, miswires and resistance limits, the HVX system applies a user-selectable voltage to each connection group in the cable from 10 volts to the maximum DC-AC voltage,” says Margaret Bishop, Ph.D., technical marketing manager at CAMI. “Ramp up, ramp down, dwell time (test time), trip current and trip delay (soak time) are adjustable. Leakage current detected during the high-voltage test phase provides a measure of insulation quality.
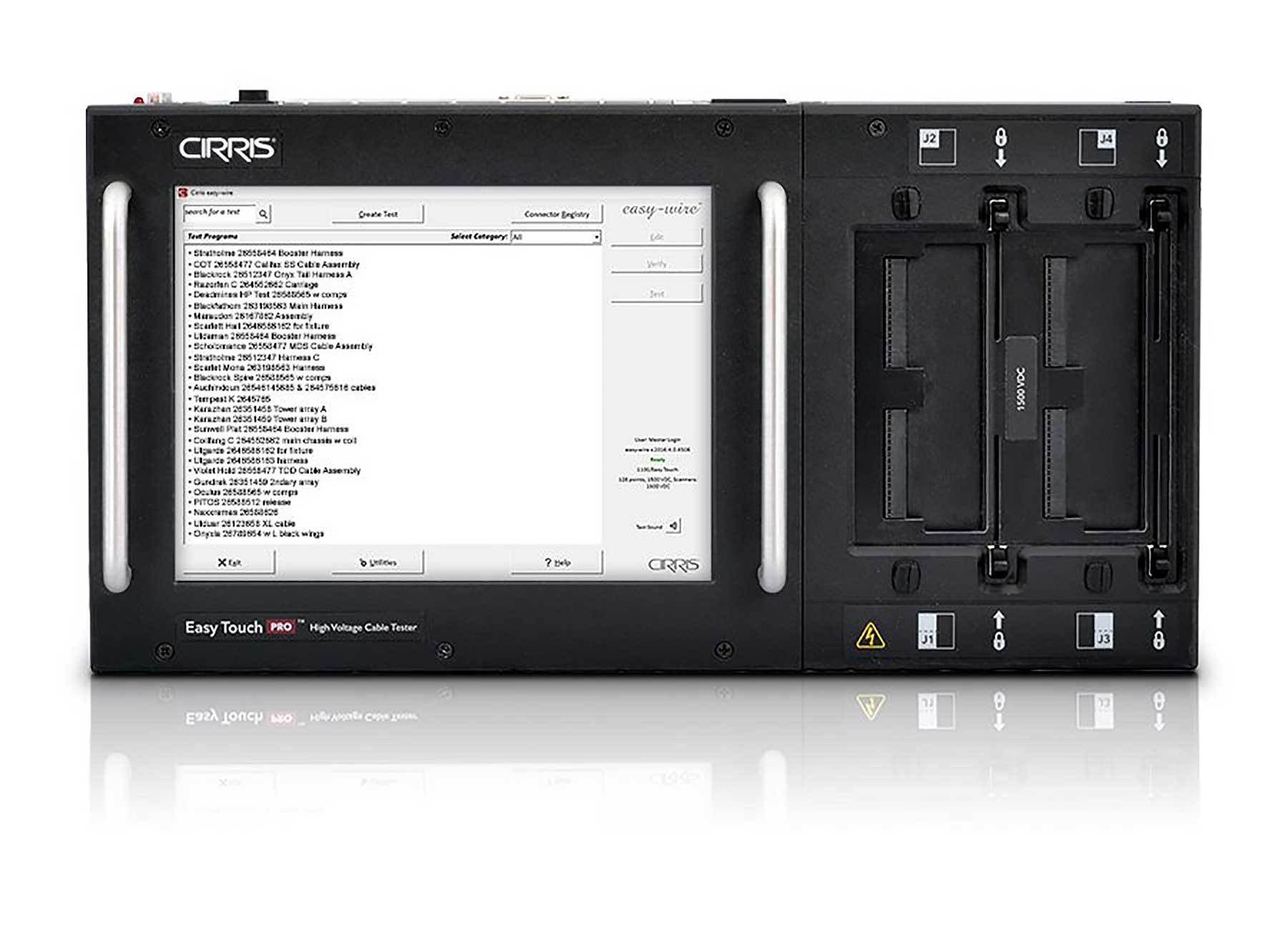
This self-contained high-voltage cable tester is designed for easy integration within production processes. Photo courtesy Cirris Inc.
“Insulation resistance up to 1 or 5 gigaohms may be recorded,” explains Bishop. “Any leakage current exceeding a user preset limit reveals the presence of moisture, flux or other contamination on exposed contacts.”
Containing both low-voltage and high-voltage subsystems, the HVX permits expanded testing for insulation resistance, dielectric breakdown and Zener diode breakdown voltage. An advanced measurements option provides increased two-wire resistance resolution, and enables the measurement of capacitors, wire pair capacitance, twisted pair testing and cable length.
“Our test systems are truly future-ready, allowing for both hardware upgrades and really easy software upgrades via download from our website,” says Bishop. “CableEye systems that were purchased more than 10 years ago are now operating with our most recent software release and using features unavailable when the testers were acquired.
“For example, simply by upgrading their software, a user with an older system will now be able to generate pop-up operator work instructions, a feature that did not exist a few years ago,” Bishop points out. “This degree of future-readiness comes with being a real PC-based system. Other systems with an embedded computer are not this flexible and consequently lag behind in technology advances.
“There is a trend for some specifications to call for unnecessarily high voltages, due to a lack of understanding in what is already capable with current technology,” claims Bishop. “Unfortunately, the harness manufacturer is not usually in a position to push back on those specifications, which consequently promulgate through the supply chain.
“We have seen several instances where we have determined that test objectives could be readily achieved at the lower voltages using systems with greater leakage current sensitivity,” notes Bishop.
Testing Trends
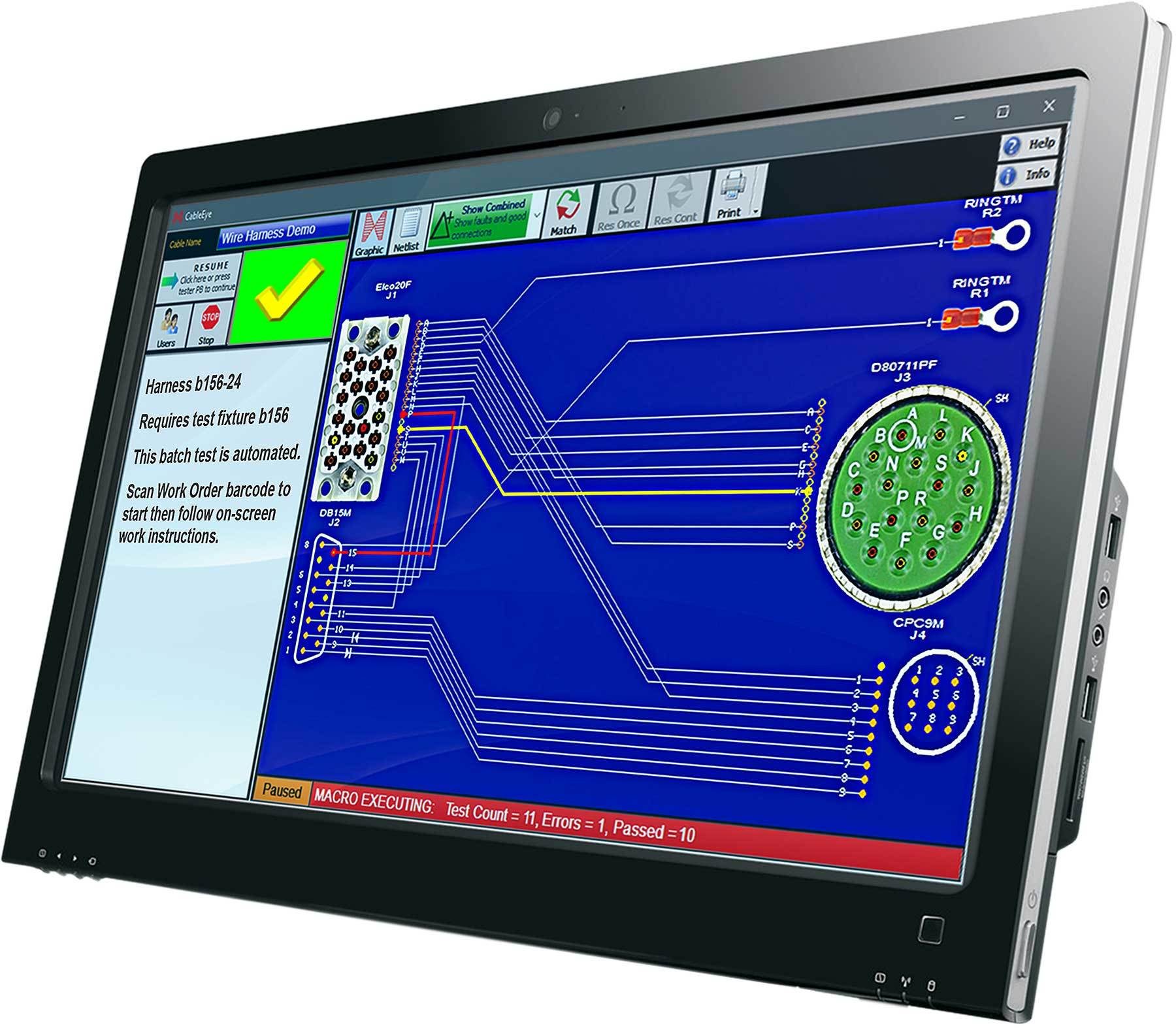
New products now make it easier to test wiring harnesses than in the past. Photo courtesy CAMI Research Inc.
There is a continuous need to streamline the test programming and setup process, particularly at companies that assemble a high mix of products. Providing methods and tools to simplify these processes is key to meeting this need.
“We’re seeing increased interest to integrate our testers with other equipment and to share test data with company information systems,” says Kevin Shelley, product manager at Cirris Inc., a leading supplier of wire harness testing equipment that was recently acquired by the Schleuniger Group.
“Interconnect assemblies are becoming more complex, and with that trend, there’s a need to test more complex assemblies and components,” explains Shelley. “[In addition], the pressure for improved productivity is pushing companies to automate test processes when production quantities justify the investment.
“We’re seeing more demand for test results data, both to document tests and for analysis,” Shelley points out. “We’ve responded to this need with new software and hardware connectivity functionality.
“We are also seeing more demand to test at higher voltages, not just in the automotive market, but for other electric vehicles, plus in-flight and mass transit applications,” says Shelley.
Increasing demand for electric vehicles is driving the need to test high-voltage cable and wire harnesses in the automotive industry, because electrical systems are responsible for a variety of starting, driving, charging and discharging functions.
Cable and wire harnesses are used to connect charging ports to batteries and to connect batteries to traction motors and other drivetrain components. To ensure that only accurate and fully-functional harnesses are installed in vehicles, cables and wires must be tested for continuity, insulation and electrical strength.
“Electric vehicle applications are pushing the need for higher test voltages than have historically been required,” claims Shelley. “There has always been a segment of the market that needs the capability to test at voltages above 2,000 volts DC or 1,000 volts AC, but the EV [trend] has drastically increased this need. These applications require unique, high-volume adapters for testing both physical and electrical characteristics.
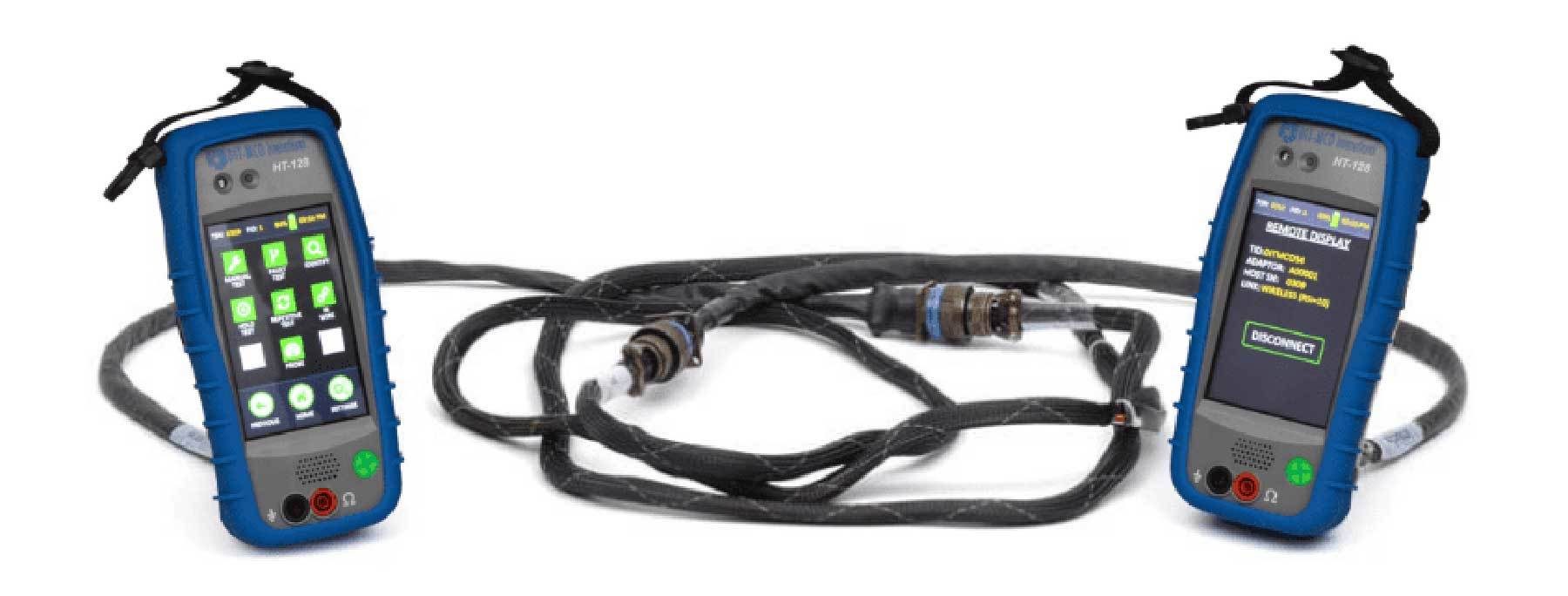
This handheld unit designed for benchtop testing can analyze 128 continuity points. Photo courtesy DIT-MCO International
“As a member of the Komax family of companies, Cirris has been able to leverage the experience and capabilities of our sister companies to produce and support equipment that meets higher voltage requirements and fulfills the need for EV test adapters,” says Shelley. “To support the high production volumes of the automotive industry, we’ve also been able to combine our test capabilities with the wire processing and integration capabilities of our team members.”
According to Shelley and other industry experts, the rapidly evolving EV market is putting new demand on suppliers of wire testing systems.
“We’ve had requests for testing up to 20,000 volts,” says ECC’s Balcom. “Engineers who are writing specs don’t have a good set of standards to go by. So, they’re now specifying voltages that are much higher than what we’ve seen in the past.
“However, those requests are not just in the automotive industry,” explains Balcom. “We are also seeing interest from the alternative energy sector, such as applications related to solar power.
“For EVs, we have some customers testing cable and wire harnesses up to 6,000 volts, but they want it rated for much higher,” Balcom points out. “The lack of standards has forced many engineers to aim much higher to provide wide leeway and build in extra flexibility for down the road.”
Standards such as ISO 6722-1 define a wide range of tests that vehicle cables must pass for certification. However, a new EV standard that’s currently under development may help engineers address additional testing challenges.
IPC-7971 will cover all of the process requirements for assembling high-voltage components. Among other things, it will explain what is “acceptable” and what is considered to be “bad” or “defective.”
The goal is to create a high-voltage wiring harness and cable standard to improve the field reliability of e-mobility and the reliability of manufacturing. Each section will address issues such as assembly and testing, plus material components and equipment requirements. In addition to cars, IPC-7971 will cover buses, motorcycles, tractors, trucks and other types of electric vehicles.
New Products Make Testing Easier
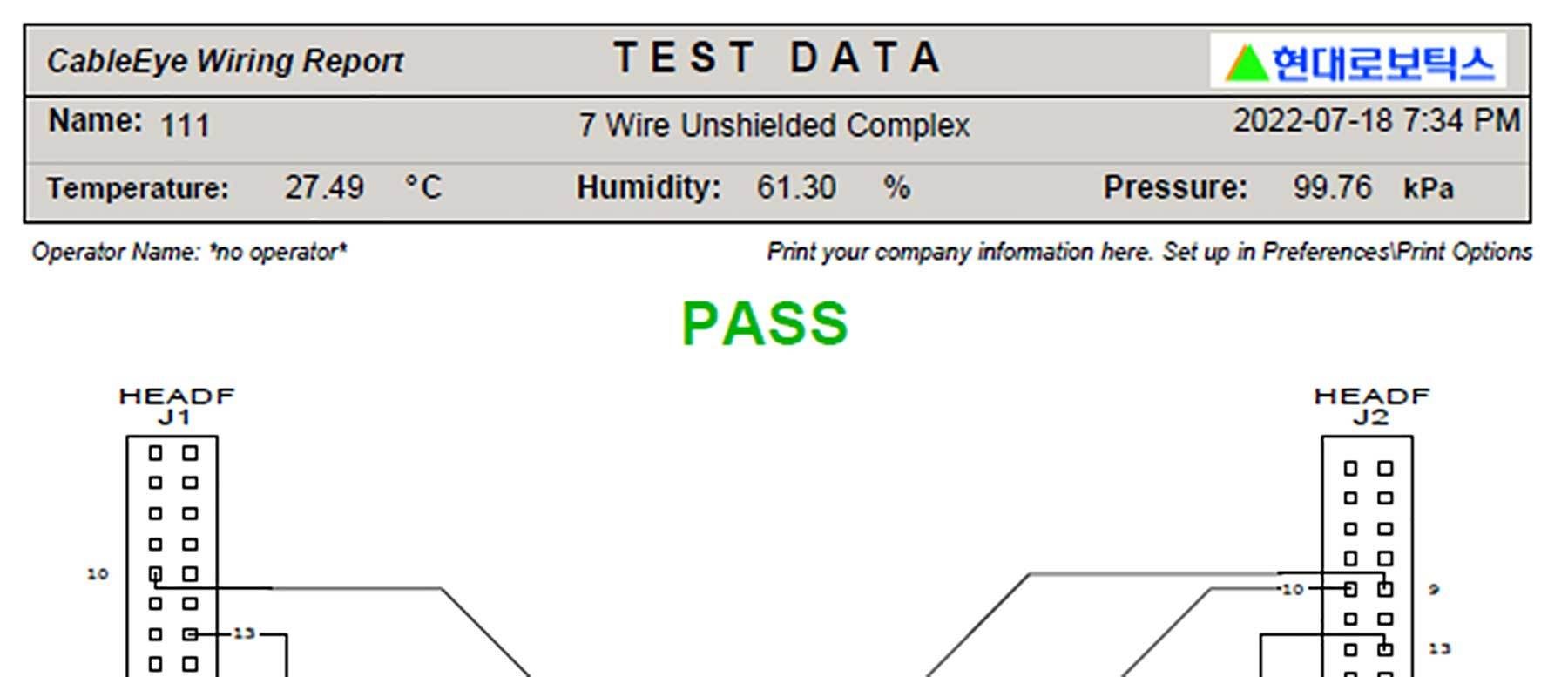
Automatic measurement and reporting of environmental test conditions is provided by this new product. Illustration courtesy CAMI Research Inc.
Engineers can choose a variety of innovative products that now make it easier than ever to test cable and wire harnesses. For instance, CAMI recently released an environmental sensor option incorporating the Dracal PTH200 sensor.
“Of particular interest to medical and defense applications, this option provides automatic measurement and reporting of environmental test conditions (temperature, relative humidity and pressure) alongside electrical function data for the cable, harness or backplane under test,” says Bishop. “This option simplifies test and reporting procedures, especially involving testing with environmental chambers.”
“When prepopulated and preconfigured boards are used, the software automatically displays a graphic of the connectors, in addition to the wiring under test,” explains Bishop. “The tester can be readily programmed to do the same for custom boards and fixtures.”
At the 2022 Electrical Wire Processing Technology Expo in Milwaukee, CAMI unveiled the M2Z low-voltage test system. In addition to checking for opens, shorts and miswires, the entry-level tester checks for intermittent faults and diode orientation. The control module has 128 test points and includes a probe socket with probe.
“The M2Z ships with comprehensive, automation-ready software that allows for tester management, troubleshooting, pass-fail testing, and testing of any product volume and mix from prototyping through to batch testing,” claims Bishop. “It is suitable for cables carrying digital signals or any electronic signaling where small amounts of resistance in the cable or connections will not affect the function of equipment to which the cables are connected.”
DIT-MCO International recently launched the HT-128, a rugged, handheld unit designed for product development, benchtop testing and field support applications. The device can communicate with 128 test points and provide remote analysis.
“It enables end users to test installed cables without shorting plugs or long loop-back adapter cables,” says Stringham. “The HT-128 performs continuity and resistance diagnostics for each wire in a harness. Faults such as opens, shorts, crossed wires or high resistance are reported to the user within seconds.
“The system allows you to connect individual testers to each wire harness branch connector rather than relying on a single, centralized tester and multiple return adapter cables,” explains Stringham. “This distributed approach allows you to use small, battery-operated testers that wirelessly link together to achieve the desired wire harness test coverage.”
Later this year, DIT-MCO plans to unveil a next-generation tester that incorporates both with both low- and high-voltage capability in a modular unit. The company is also working on a new product that uses artificial intelligence to improve wire harness troubleshooting. It hopes to unveil the patent-pending device by 2024.