Robotics
Labor shortages are driving new demand for automation.
Options for Screwfeeding
OnRobot engineers recognized that numerous assembly processes involved the repetitive use of screws. One process, in particular, stood out: the mounting of Quick Changers to OnRobot’s various end-of-arm tooling products. The process is common across many OnRobot products. Photo courtesy OnRobot
To increase efficiency and improve safety, OnRobot employs its own automation products on its assembly lines.
for Robots
Robots Assemble Tools…
Kristian Hulgard // General Manager for the Americas // OnRobot. // Irving, TX
OnRobot is the go-to source for a wide array of cutting-edge robotic tools and software tailored for collaborative robot applications. These innovative technologies facilitate the deployment of collaborative automation, regardless of an individual’s prior robotics experience or skill level.
OnRobot’s production setup was predominantly based on manual assembly procedures, posing a significant hurdle to the company’s ambitious expansion plans. Increasing output would require both additional skilled labor and physical space.
If OnRobot was going to increase output without adding headcount, it would have to automate. The goal was to free up skilled workers from simple, but time-consuming tasks, so they could dedicate their time to more complex processes. However, any automation had to fit within the current production layout while also being safe and easy for operators.
Automating Attachment of Quick Changers
When assessing the company’s production line, OnRobot engineers recognized that numerous assembly processes involved the repetitive use of screws. One process, in particular, stood out: the mounting of Quick Changers to OnRobot’s various end-of-arm tooling products. The process is common across many OnRobot products. Regardless of the base product, the process requires the same four screws.
“We knew the solution was to automate, and we looked at what type of screw is utilized the most in our processes,” says Frederik Korsager, supply chain project manager at OnRobot’s headquarters facility in Odense, Denmark. “Since the Quick Changer is part of the majority of our products, it was the obvious task to automate.”
Fortunately, engineers didn’t have to look very far for an automatic screwdriver—the company introduced its own intelligent screwdriving tool for robots in June 2020.
The OnRobot Screwdriver can be mounted to robot arms from a variety of OEMs, including Universal Robots, FANUC, Kuka and Kawasaki. The screwdriver and accompanying screw feeders can handle a range of screw sizes, from M1.6 to M6 and up to 50 millimeters long. Precise torque control ranges from 0.15 to 5 newton-meters. The intelligent tool can detect if the screw has been picked up, if it’s the correct length, and if it’s been properly inserted in the part. Changeovers to a different screw type or size take just minutes. Bit extenders, in lengths of 50 and 100 millimeters, are available to provide extra reach in narrow and tight spaces.
Programming the screwdriver is as easy as entering the screw length and torque value into the user interface, which is integrated into the teach pendant of the robot. The screwdriver automatically calculates the speed and force required for consistent, accurate screwdriving. Another setting enables the tool to install self-tapping screws into predrilled holes.
With the screwdriver’s unique Z axis, screws are retracted inside the tool and driven automatically once the robot arm moves into position, which reduces robot arm movement and additional programming. Screws up to 35 millimeters long are retracted completely inside the tool until the screwdriving process is safely initiated, making it safe for collaborative applications. A safety stop is automatically activated if a screw is exposed to excessive force along its axis, and a signal light illuminates to alert engineers to the issue.
At OnRobot’s factory in Denmark, the initial automated screwdriving application focused on mounting the Quick Changer onto the company’s 2FG7, 3FG15 and VGC10 grippers. Soon, however, the application scope expanded to include the mounting of printed circuit board assemblies on the VGC10 gripper. In the near future, the company’s RG2 and RG6 grippers will be integrated into the automated Quick Changer assembly process, too. Additional subassembly tasks on the horizon.
“We are currently working on having the screwdriver automate the mounting of rails inside the housing of the 2FGP20 palletizing gripper,” says Korsager.
Inspection System
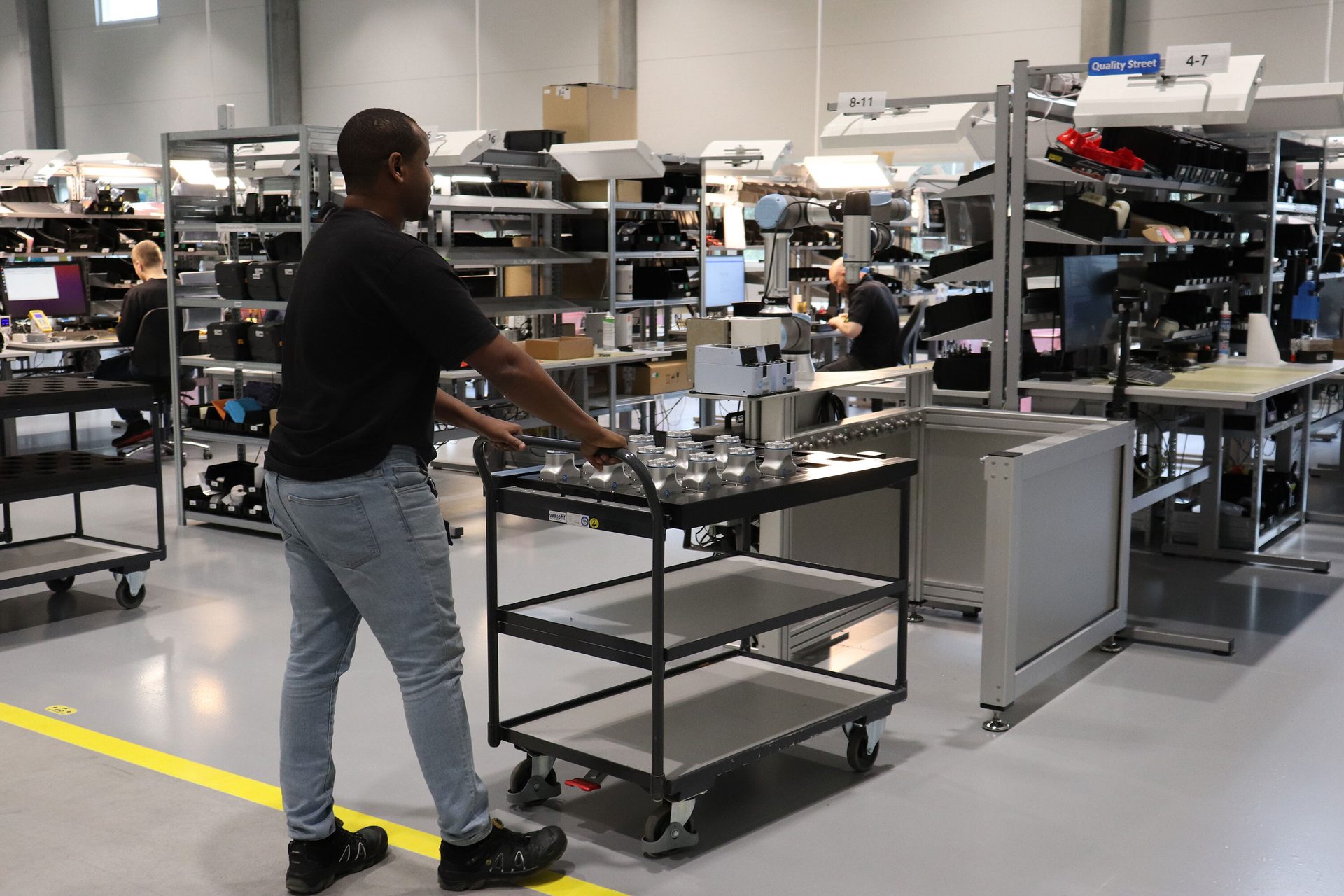
OnRobot incorporated rolling tables into the cell. This allowed the operators to conveniently place products into fixtures and transport them from their workstations to the cobot cell. Photo courtesy OnRobot
The application cell is equipped with an OnRobot screwdriver, two screwfeeders for handling precoated M3 and M6 screws, product fixtures, rolling tables and Universal Robots’ UR5e cobot arm.
Seamlessly integrating this cell into the company’s production line was critical. OnRobot needed a user-friendly cell station that can operate in close proximity to assemblers, ensuring easy and safe interaction. So, OnRobot incorporated rolling tables into the cell, which allowed operators to conveniently place products into fixtures and transport them from their workstations to the cobot cell.
The automation project delivered significant advantages. Notably, it led to a tangible increase in production capacity. By automating repetitive and physically demanding tasks, OnRobot significantly improved the ergonomics of its workplace. Workers were no longer subjected to the physical strains associated with these repetitive tasks, resulting in a safer and more employee-friendly working environment.
“By streamlining our processes and freeing up capacity, we’re not just meeting short delivery times; we’re redefining our commitment to customers, delivering on promises with unmatched efficiency,” says Enrico Krog Iversen, the company’s CEO.
This is an ongoing project, and additional tasks are continually being added to the cell, which improves payback. In addition, OnRobot now has greater flexibility to redeploy its workforce to accommodate additional production without additional costs.