Screwdriving and Riveting
Labor shortages are driving new demand for automation.
Options for Screwfeeding
Kubota assembles around 12,500 excavators and 2,500 wheel loaders per year in Zweibrücken. Photo courtesy Desoutter Industrial Tools
Desoutter technology helps Kubota increase quality and streamline assembly processes.
Controlled Tools
Boost Output at Tractor Manufacturer
Thomas Preuss // Contributing Writer
A bolted joint in a tractor may not seem like a thing of beauty to most people, but not Jens Weber, production engineer at Kubota Baumaschinen GmbH in Zweibrücken, Germany.
“The most beautiful screwdriving point in our factory is the slewing ring screw connection,” says Weber. “This joint is used to connect the undercarriage and upper carriage.”
An electronically controlled screwdriver from Desoutter Industrial Tools is used to fasten this joint. The tool is attached to a cantilever arm with a radius of more than 3 meters. An assembler installs 20 screws on the slewing ring at a torque of around 300 newton-meters. The “zero-gravity” arm carries the weight of the tool and absorbs the high reaction torque that occurs during screwdriving. The tool is fixed in a holding device and can be easily moved in space despite the large moving masses. The assembler only needs to position the tool at each screwdriving point and press the start switch. The screw connections are ergonomic, safe, reliable and traceable.
Kubota assembles around 12,500 excavators and 2,500 wheel loaders per year in Zweibrücken. It is the only factory in Europe for mini and compact excavators. The factory produces machines in the weight class of 1.6 to 2.7 tons; larger devices are manufactured in Japan. There are two models of wheel loaders: a variant for Europe and one for the U.S., Canadian and Australian markets. Europe, Australia and North America are supplied from Germany, while the rest of the world is served from the Japanese factory. Around 700 employees work in Zweibrücken, of which just over 500 work in production.
Retrofitting Assembly Lines
“We have significantly more orders than we can process,” says Weber. “That’s one of the reasons why we started converting the assembly lines here from compressed air to electric tools years ago.”
This would streamline the screwdriving processes. Now, instead of using two tools—pre-tightening with a pneumatic screwdriver and final tightening with a torque wrench—only one would be needed at various screwdriving points. Above all, the switch to controlled electric screwdrivers offers more options for monitoring and documenting the fastening process than are available with compressed air tools. That’s important, because product liability laws require manufacturers to prove that assembly was carried out according to the “state of the art.”
At Kubota, fastening data is stored as according to the VDI/VDE 2862 standard, which is best implemented with controlled electric screwdrivers.
Kubota relies on screwdrivers from Desoutter, including ERP pistol-grip screwdrivers, EABC cordless angle screwdrivers, and Q-Shield electronic torque wrenches. They all automatically control the screwdriving process during assembly and communicate via WLAN or, for some high-torque screwdrivers, via a wired network connection. In addition, the manufacturer also benefits from higher security, better ergonomics, lower energy consumption, and the possibility of IT connection.
Critical Screwdriving Cases
The screwdriving applications in Zweibrücken are classified by Kubota’s Japanese design department, and the nomenclature corresponds to the VDI/VDE guidelines. Safety-critical screw connections, which fall into risk class A in the standard, are denoted internally at Kubota by the letter S. Kubota has assigned the abbreviation A to function-critical screw connections, which are risk class B in the VDI guidelines. And the noncritical class C screw connections according to the VDI, are classified at Kubota in Class B.
“We have significantly more of these noncritical screw points on the excavators than on the wheel loaders,” explains Weber.
Depending on the model and equipment, there are around 24 monitored screwdriving applications on the wheel loaders, which is more than on the excavators with 12. All these joints are critical and therefore monitored electronically.
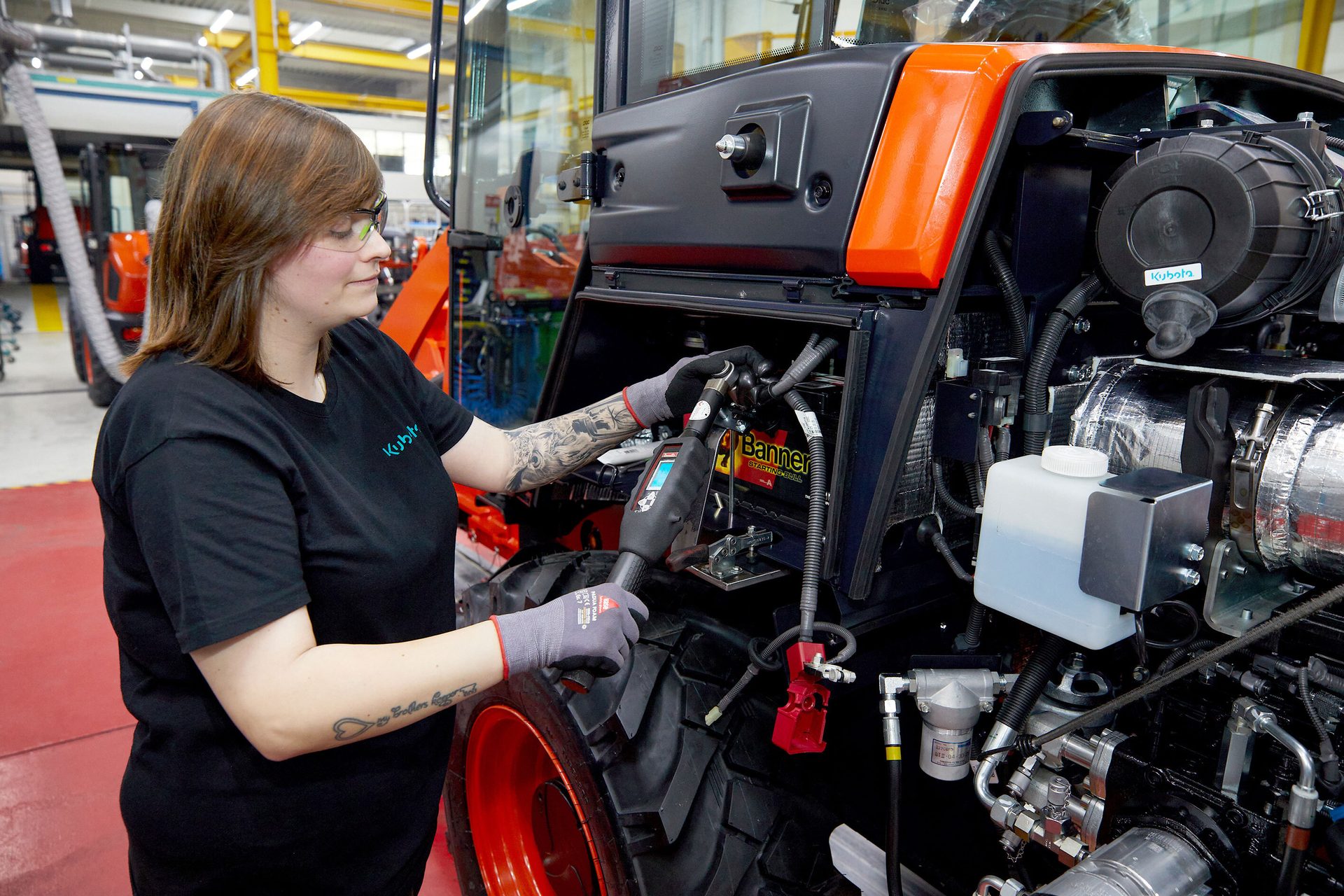
The ground screw on the engine main switch is tightened with a digital torque wrench. Here, the screw must be tightened to 8.8 to 11.8 newton-meters. Photo courtesy Desoutter Industrial Tools
Converting to VDI Nomenclature
In the long term, Kubota wants to standardize on the VDI when it comes to the design and testing of the tools and joint measurements. This is happening in parallel with the conversion of compressed air and impulse screwdrivers to controlled screwdriving technology.
“We have already converted all S-Class screw connections,” says Weber.
The A screw cases are currently undergoing transformation, and all B screw cases will be addressed in the near future.
“We decided to switch the screwdriving case classes to the nomenclature of the VDI guideline, and the tools to higher-quality technology because we want to meet a certain standard for our customers,” the production engineer continues.
The initial requirement for the new tools and systems was that they must work reliably and be capable of documentation, which many manufacturers meet. “The most important requirement was that the technology had to communicate well with the internal IT system,” emphasizes Weber.
Kubota wanted to record all the data and make the workstations as clear and as error-proof as possible. This is where the wheat was separated from the chaff. Desoutter has been at the forefront of the competition, because of the flexible communication possible via Open Protocol.
Error Rate Reduced
“At the assembly stations where we have already replaced the pneumatic and impulse screwdrivers with controlled systems from Desoutter, the error rate has decreased significantly,” emphasizes Weber.
Screws are no longer forgotten. Problems with overtightened or undertightened screws are now a thing of the past. The tolerance ranges specified in the design are well maintained.
“Most importantly, we can now analyze the screwdriving data,” says Weber. “Of course, that wasn’t possible at the stations where we used to work with bending wrenches or pneumatic screwdrivers.”
The implementation into the existing system was very positive. “The workers know the system, the software is connected excellently,” adds Weber.
The processes were found to be convenient by everyone. The collaboration between the Desoutter control and Kubota IT works perfectly.
Inspection System
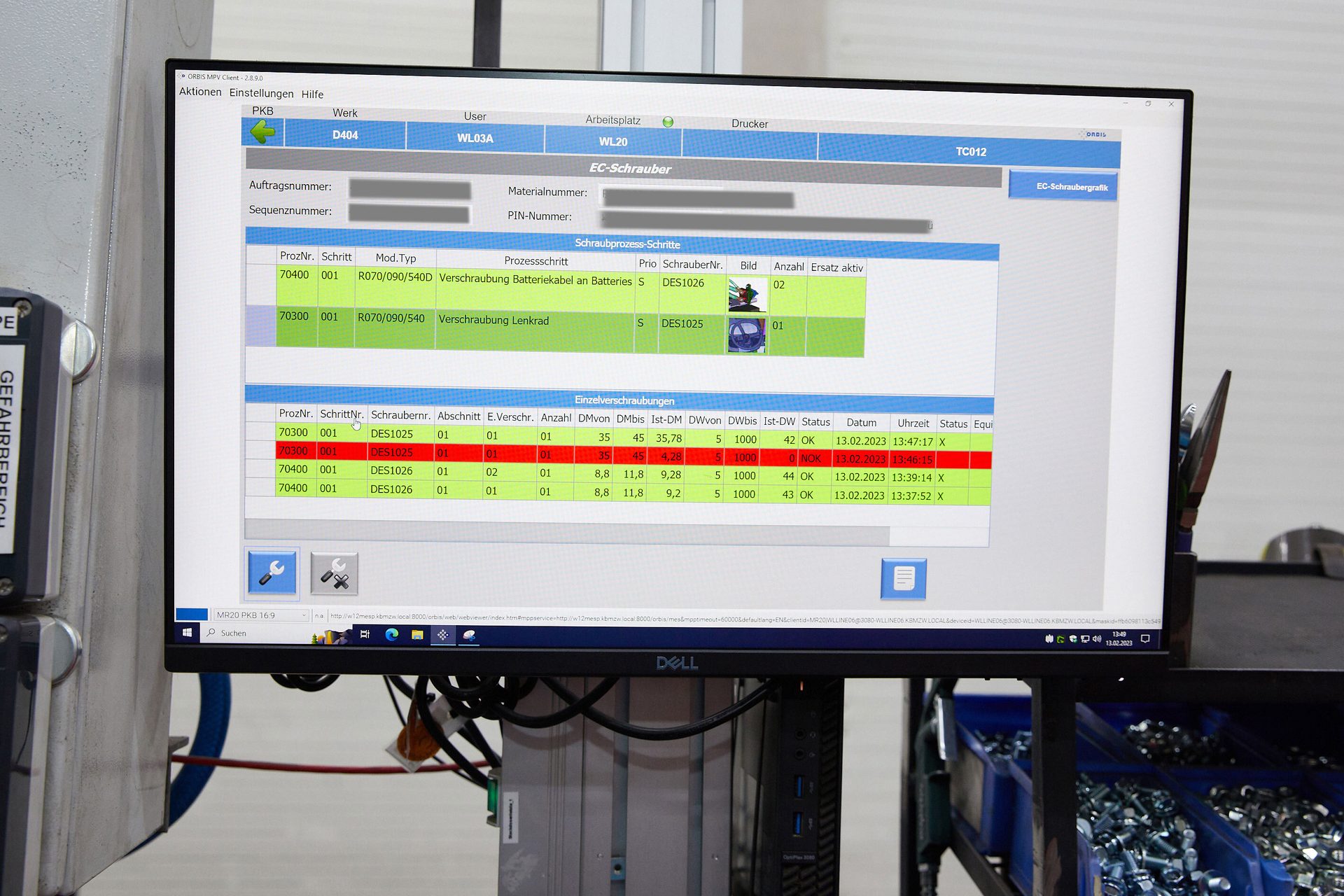
The quality control screen shows employees in real time whether a screw connection was OK (green background) or not (red background). The software immediately detects many errors, such as forgotten or incorrectly placed screws, so that the worker can correct them during the process. If this is not possible, a quality assurance employee is called out to solve the problem. Photo courtesy Desoutter Industrial Tools
SAP Software Tailored to Kubota’s Needs
Communication between the systems looks like this: At all stations where controlled electric or cordless screwdrivers or torque wrenches are used, the MES client from SAP consulting firm Orbis SE is used. More than two dozen Desoutter tools are included in the system.
The interface and functions were defined by Kubota and programmed by Orbis. Assemblers on the line see a stripped-down MES surface. For each component or task, they scan a bar code on the routing card that comes with the machine. The scanning process triggers a message to the MES system, whose software, in turn, addresses the screwdriver control. It also reports the target values to the screwdriver via Open Protocol and plays the data back to the MES after screwdriving.
The MES software monitors the number of screw connections required for the task. Torque, angle and various tolerance ranges are monitored by the Desoutter controller. All values are displayed on the MES interface of the monitor. The worker receives feedback firstly through the vibration of the Q-Shield torque wrench, secondly via the monitor above his workstation, and thirdly on the key’s display. If everything is OK, a line on the monitor will be highlighted in green. In the event of errors, a red warning message indicates that corrections need to be made.
Only if the screw connection is “OK” will the task be logged off from the MES system. If it wasn’t OK, the employee must call in someone from quality assurance who can initiate a restart or solve the problem in another way.
“We save all screwdriving results in our MES system and document them at machine level in the SAP system,” explains Weber. “Here, they are permanently assigned to the respective screwdriving locations as well as to the individual wheel loaders and excavators.”
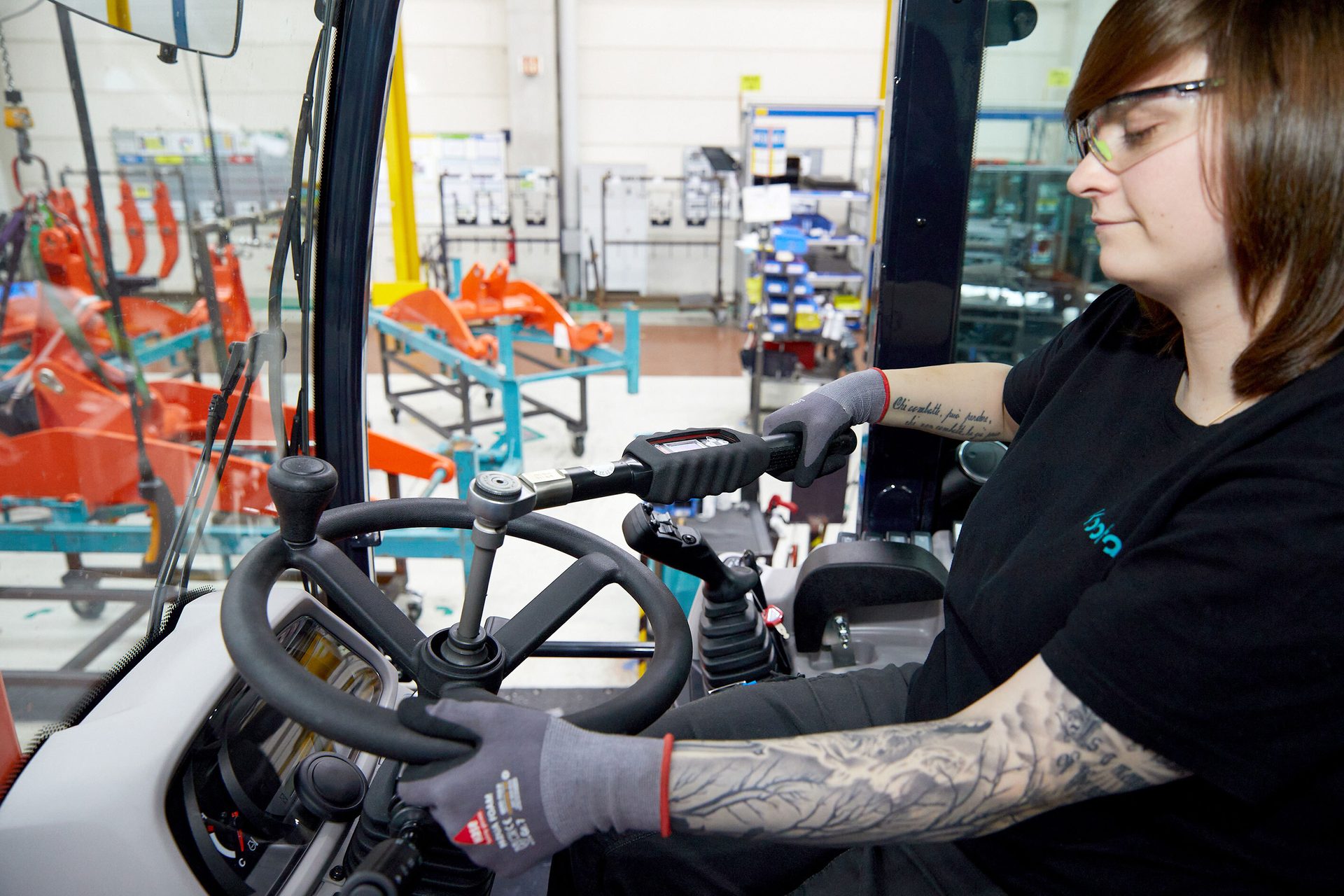
An assembler installs the steering wheel on a wheel loader. Photo courtesy Desoutter Industrial Tools
Final Tightening of Large Screws
All screw locations are hard joints—screw connections of metal on metal or metal in metal, in which the torque increases suddenly after head of the screw contacts the part. The specified tightening torque is achieved within a maximum rotation angle of 30 degrees. The programming provides for torque and angle as control variables for all screw connections, the most common screwdriving strategy in such cases. The torques are between 10 and 500 newton-meters, although some of the Desoutter torque wrenches used at Kubota can reach up to 800 newton-meters.
The highest torques in excavator and wheel loader assembly are on the screws with which the rear weight is attached to the excavator (a maximum of 431.5 newton-meters), and the screws for attaching the wheels to the wheel loader (a maximum 525 newton-meters). A 1.5-meter-long torque wrench from Desoutter is used on these joints.
Another interesting screw connection is the steering wheel nut on the wheel loader. This is tightened to 40 newton-meters (± 5 newton-meters) using a shorter Q-Shield torque wrench. The ground screw connection on the engine main switch, with which the battery can be disconnected, is also made with the torque wrench. Here, the screw must be tightened from 8.8 to 11.8 newton-meters. Both screw connections are safety-relevant, just like numerous hydraulic screw connections on construction machines.
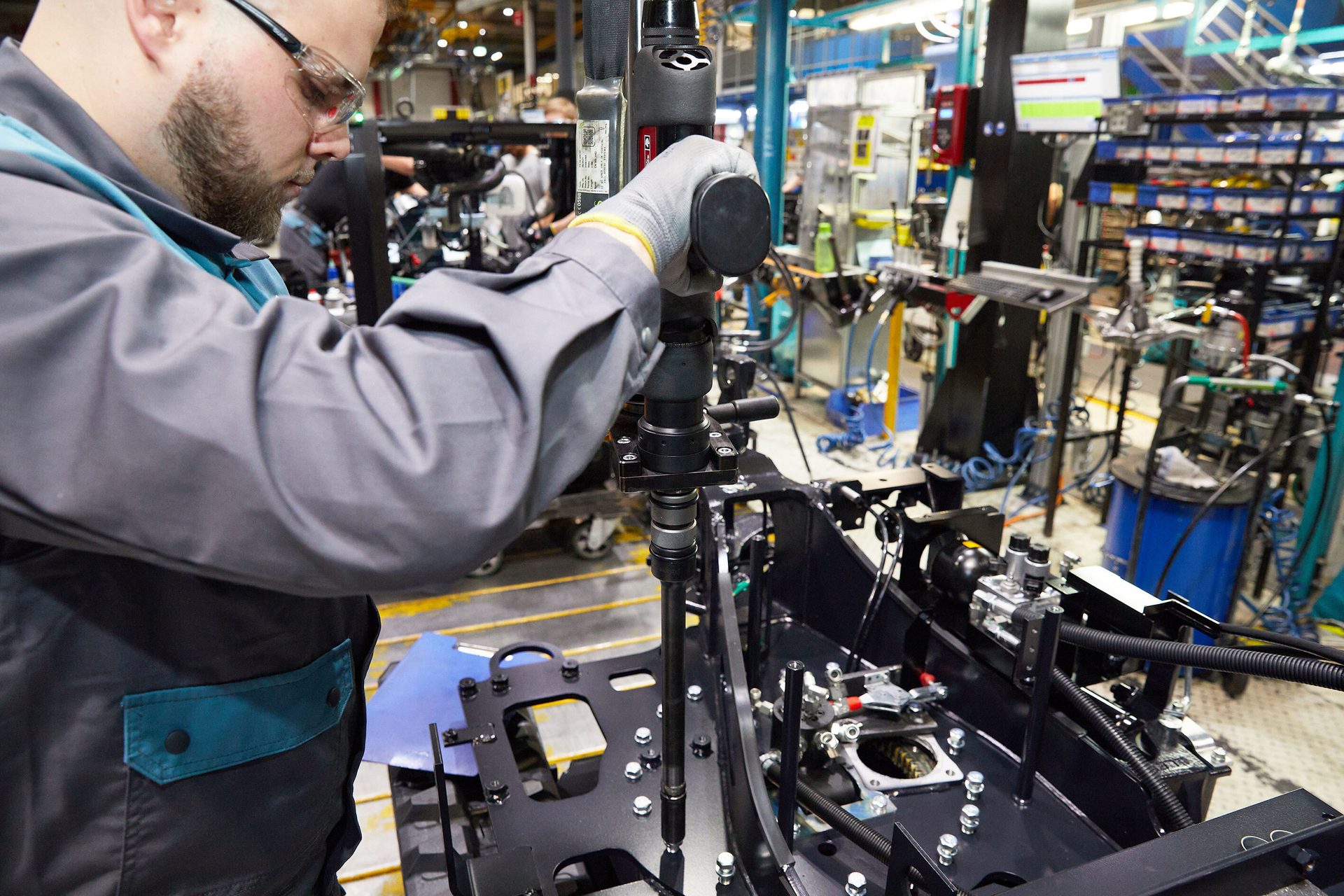
The screws on an excavator’s slewing ring are tightened to a torque of 300 newton-meters. Photo courtesy Desoutter Industrial Tools
Communications Center Organizes Data Flow
Various electric angle and pistol screwdrivers are in use in Zweibrücken. Most of these tools work wirelessly. They are powered by batteries and controlled via WLAN.
In addition, Kubota has four high-torque corded wrenches in operation. They are used to work on the slewing ring and on the underside of the vehicle. The torques at these screw points are between 100 and 300 newton-meters. All tools are electronically controlled. The corded tools exchange their data with the CVI3 control from Desoutter, while the battery-powered tools are connected to a Connect. This small control unit acts as a communication center for the entire data flow and is deliberately located a little further away from the line. No separate screwdriver controls are necessary at the workstations for the wireless tools. Several screwdrivers can be connected to one Connect. However, almost every assembly workstation has a PC with a screen that is also used for other processes.
The employees are satisfied with both the wired electric and cordless battery-powered tools as well as the electronic Q-Shield torque wrenches from Desoutter, especially when they provide physical relief.
“In many cases, workers previously had to use heavier compressed air tools,” explains Weber.
Visual, audible and tactile feedback from the tool is also viewed as positive. Both the driven tools and the torque wrenches are robust and hard to break, says Weber.
He is also impressed by the many operating functions that can be carried out on the PC: “You no longer have to adjust anything on the tools,” he says. “I can easily set up or change everything on the PC using Desoutter’s CVI Config software. We no longer have to visit the line if there are small problems with the tools. We can solve them from the office.
“The entire technology and communication between the different systems works wonderfully,” continues Weber. “The software is overall very easy to use.”
Adjustments during operation are also possible without any problems—for example if rotation angle monitoring should be changed to other parameters “on the fly.”
For more information, click https://us.desouttertools.com or visit the company’s booth at The ASSEMBLY Show South, which will be held April 30-May 2 at the Music City Center in Nashville, TN.
ASSEMBLY ONLINE
For more information on fastening tools, visit www.assemblymag.com to read these articles: