ASSEMBLY LINES
Manufacturers Must Bridge the ‘Data Gap’
NEW YORK—By the end of this decade, manufacturers worldwide will generate 4.4 zettabytes of data, according to a recent study conducted by ABI Research Inc. That massive data stream will originate from production machinery, Internet of Things sensors, ERP platforms, automated identification readers and MES systems.
It will provide a transformative opportunity for manufacturers to sustain competitiveness, drive innovation and enable AI-driven systems. However, many organizations currently lack the expertise needed to leverage this data fully, resulting in inefficiencies and revenue losses of hundreds of millions of dollars annually.
By the end of this decade, manufacturers worldwide will generate 4.4 zettabytes of data. Illustration courtesy Dploy Solutions
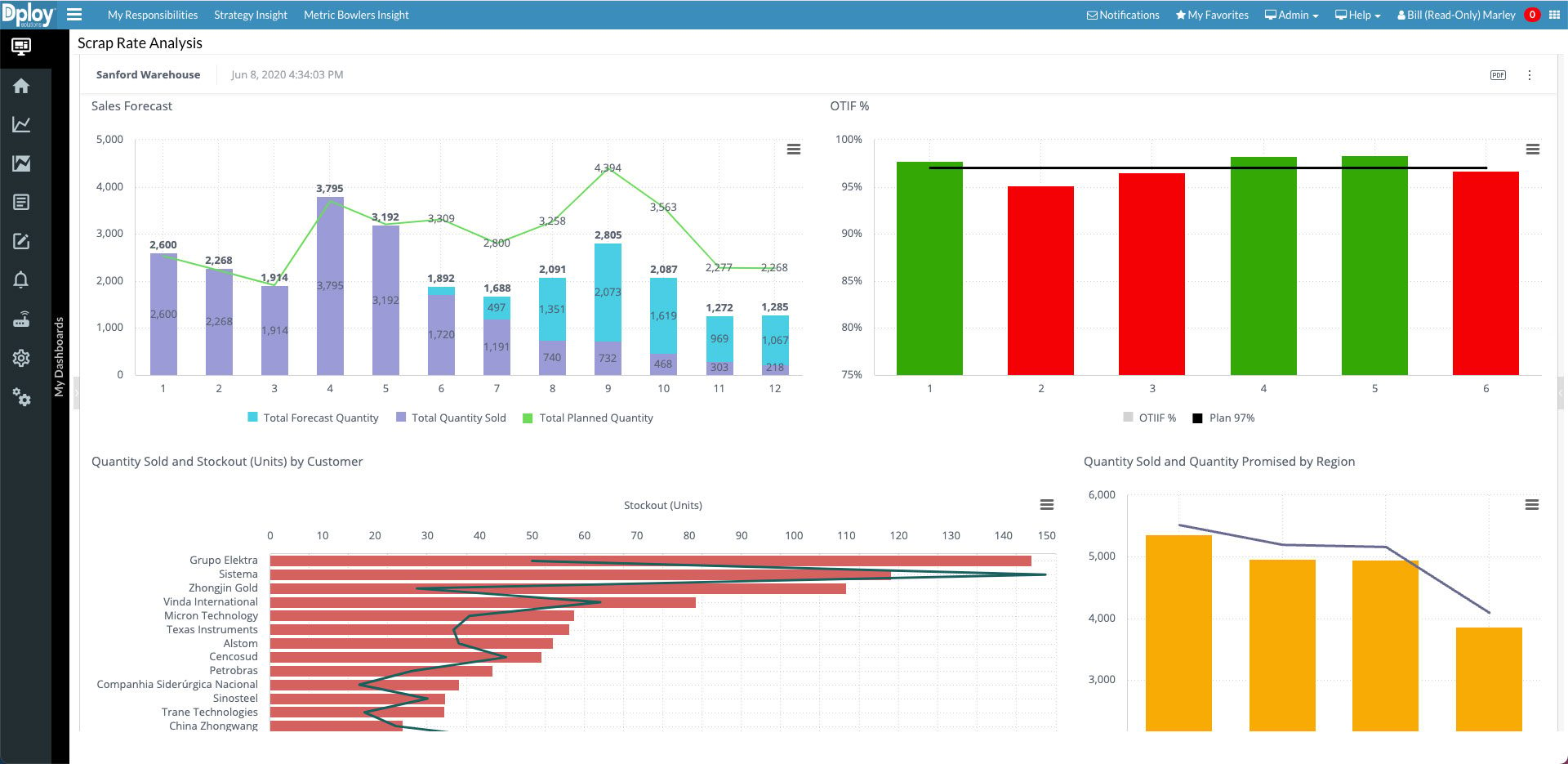
“Generating a lot of data is one thing,” says Leo Gergs, principal analyst at ABI Research. “Being able to analyze and prepare this data for large language models and AI algorithm training is another.
“Data fabrics hold immense promise in transforming operations through seamless integration, enhanced governance and automated data management,” explains Gergs. “To unlock their full potential, it’s imperative to address a spectrum of challenges spanning technology, governance, operations and organizational readiness.”
According to Gergs, integrating legacy systems, on-premise platforms and cloud-native systems into a cohesive data fabric is a major hurdle. “Vendors like Databricks, IBM and NetApp are developing platforms that unify these environments, enabling real-time data processing and seamless compatibility,” he points out.
“The ability to bridge diverse systems is critical to unlocking the true value of data fabrics,” claims Gergs. “Enterprises manage sensitive and regulated data that require strict compliance frameworks.”
Manufacturers need to enforce governance with automated lineage tracking, access control and encryption. However, traditional methods like manual ETL (extract, transform and load) and siloed systems hinder scalability. Several vendors are addressing these bottlenecks by automating workflows, enhancing real-time analytics and streamlining operations.
“[Manufacturers] are looking to data fabrics for faster, smarter and more efficient data handling,” says Gergs. “Balancing customization for unique enterprise needs with scalable solutions is essential. But, in all of this, the right balance between customization and standardization is critical for widespread adoption and long-term success.”
IPC/WHMA Launches Online Wire Harness Design Course
BANNOCKBURN, IL—IPC/WHMA has launched an online instructor-led training course focusing on wire harnesses. “Introduction to Wire Harness Design I” is a two-week program that features both live sessions and on-demand recordings.
Led by Didem Üstün, a seasoned IPC/WHMA-certified expert with more than a decade of industry experience, the course offers participants a deep dive into the complexities of designing, assembling and troubleshooting wire harnesses.
“This program is specifically designed to address the growing demand for skilled wire harness designers who can innovate and excel in an evolving industry,” says Carlos Plaza, senior director of education development at IPC.
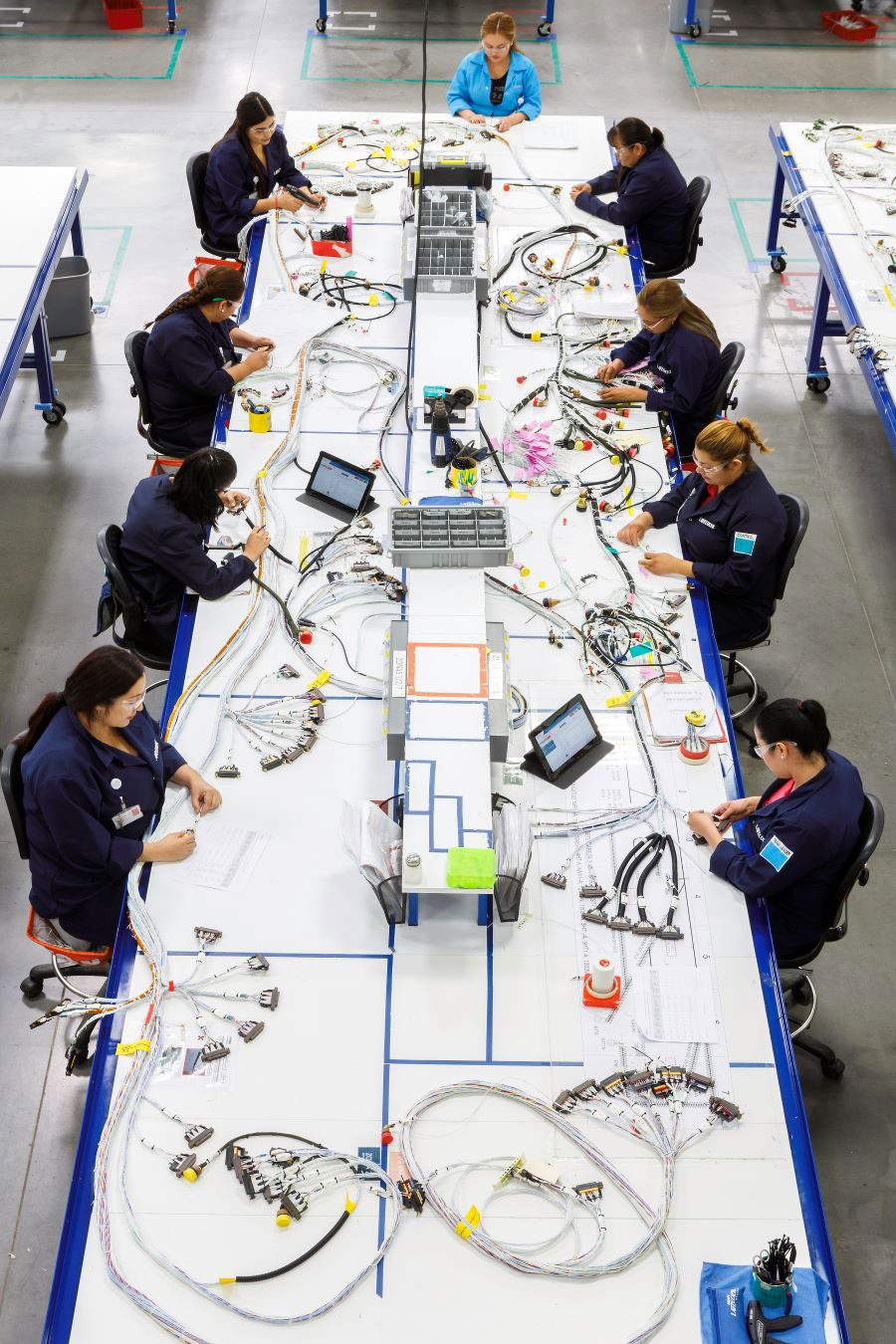
A new online course teaches engineers how to design wiring harnesses. Photo courtesy Latecoere
“Üstün’s expert guidance, combined with a robust curriculum that includes foundational concepts and practical, hands-on techniques, ensures that learners acquire the knowledge and skills they need to excel,” explains Plaza.
Topics covered include materials selection, troubleshooting and the latest wire processing standards, such as IPC/WHMA-A-620. Participants will also gain practical experience through project-based learning that mimics real-world challenges.
To learn more about the online course, click www.whma.org.
Global Robot Density in Factories Has Doubled
FRANKFURT—Robot adoption in factories around the world continues at high speed, according to a new report by the International Federation of Robotics (IFR). Global average robot density reached a record 162 units per 10,000 employees in 2023, more than double the number measured only seven years ago (74 units).
“Robot density serves as a barometer to track the degree of automation adoption in the manufacturing industry around the world,” says Takayuki Ito, president of IFR, who also serves as chief technical advisor at Fanuc Corp. “This year's runner-up is China, which ranks third worldwide behind Korea and Singapore, but right up with Germany and Japan.”
Deployment of industrial robots has doubled over the past seven years. Photo courtesy ABB Robotics
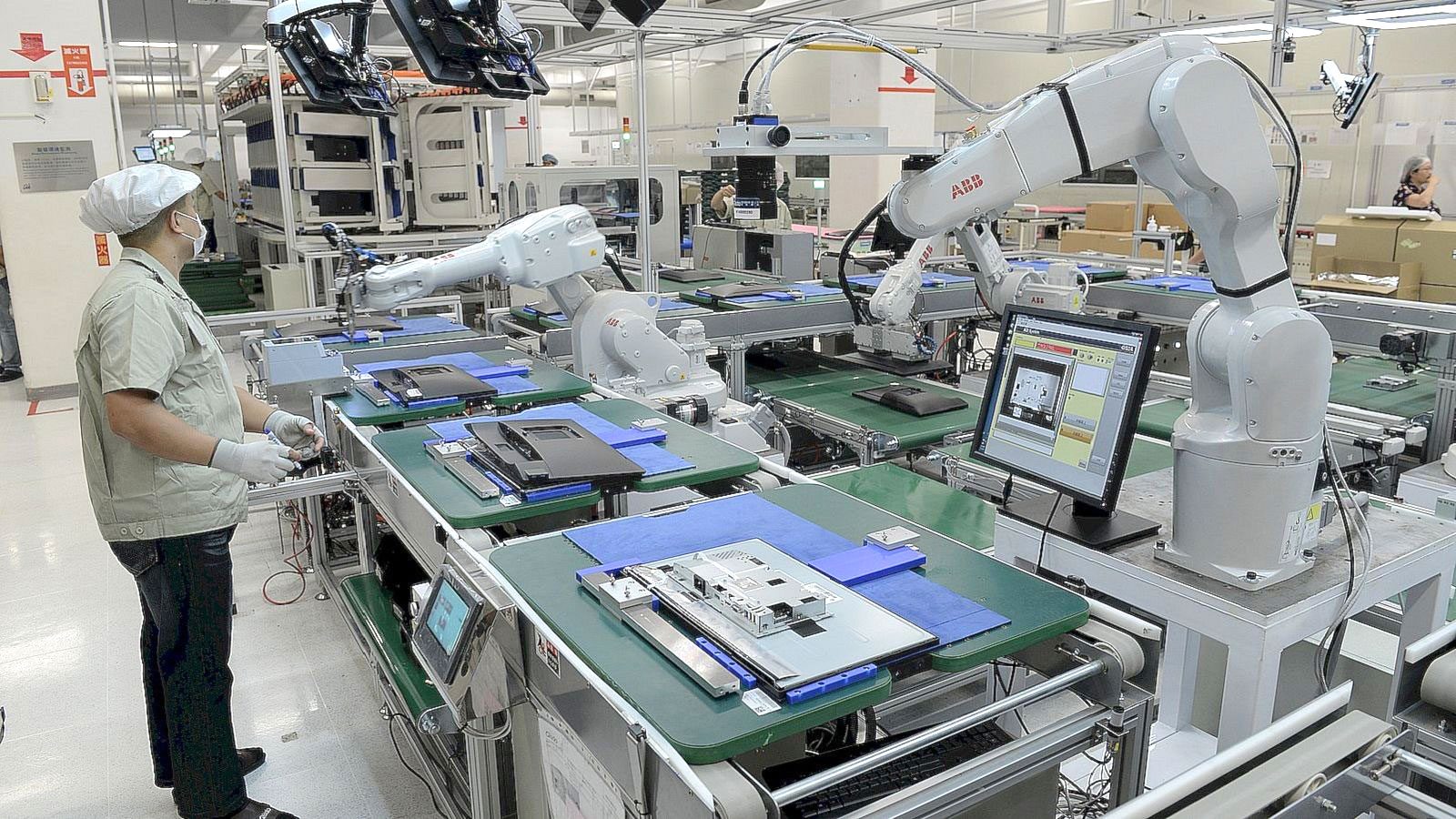
According to Ito, “robot density” refers to the number of operational industrial robots relative to the number of employees. “It can cover the whole manufacturing industry or just specific industrial branches,” he explains. “The number of employees serves as a measure of economic size, so the quotient of operational stock over employees puts the operational stock on a uniform base.”
North America´s robot density is 197 units per 10,000 employees, a 4 percent increase. Robot density in the United States reached 295 units in 2023. The U.S. ranks tenth in the world.
The European Union has a robot density of 219 units per 10,000 employees, an increase of 5 percent. Germany, Sweden, Denmark and Slovenia rank in the top 10.Asia has a robot density of 182 units per 10,000 persons employed in manufacturing, an 8 percent increase.
The Republic of Korea is the world’s No. 1 adopter of industrial robots with 1,012 machines per 10,000 employees. Robot density has increased by 5 percent on average each year since 2018, driven by South Korea’s automotive and electronics industry.
ASME Creates Free Industry 4.0 Courses
NEW YORK—The American Society of Mechanical Engineers (ASME) has launched a series of free courses that delve into various Industry 4.0 topics. It is partnering with Autodesk Inc. on the initiative, which aims to address the manufacturing skills gap.
The first four 30-minute courses cover design for sustainability; introduction to Industry 4.0 and technologies; Industry 4.0 and business; and digital literacy and data skills.
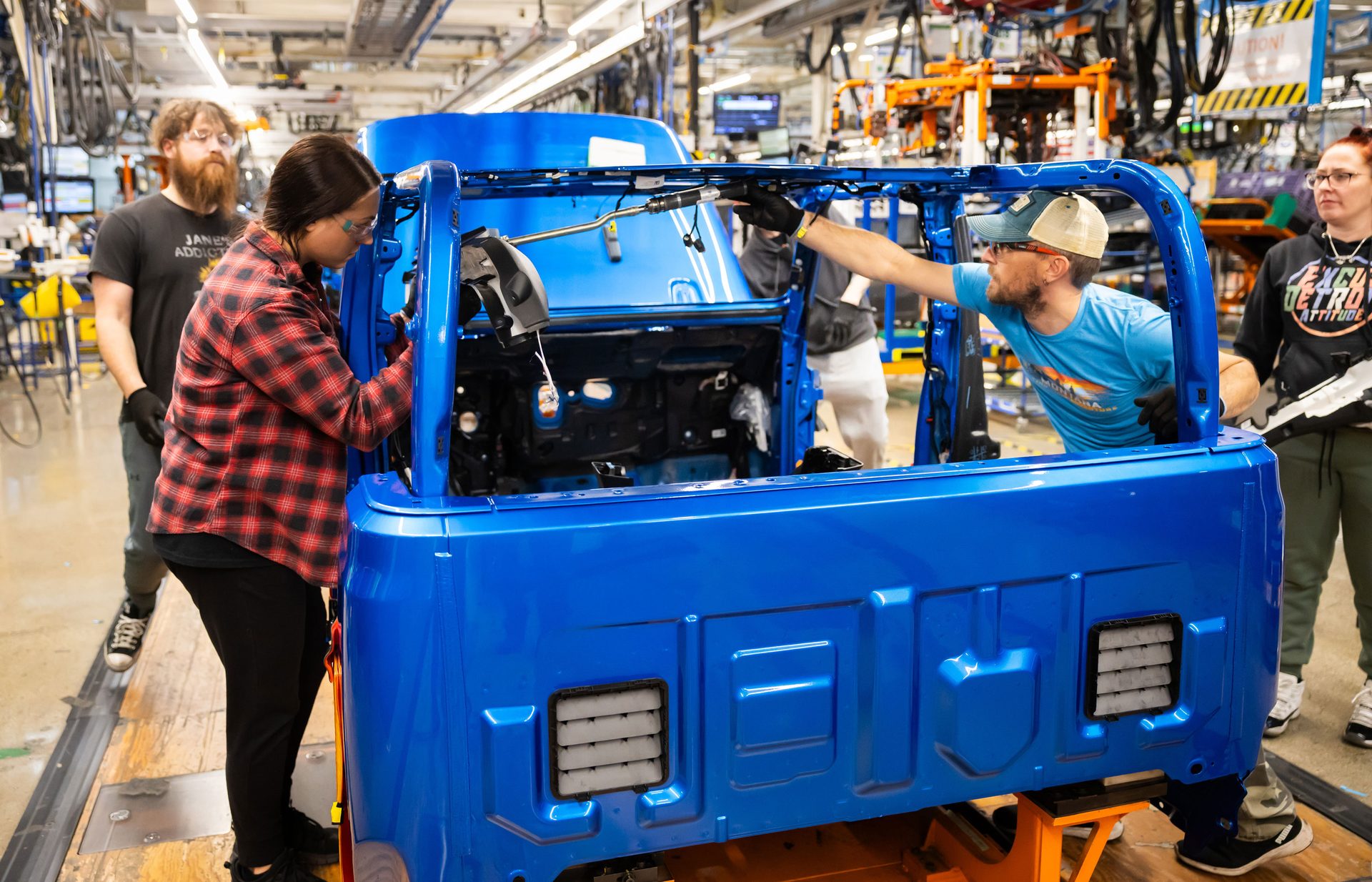
A new series of courses are designed to address the manufacturing skills gap. Photo courtesy Stellantis
“The project-based curriculum uses real-world examples to engage and motivate students and professionals as they develop skills that are in high demand,” says Stephanie Viola, executive director of the ASME Foundation and managing director of programs and philanthropy at ASME. “These courses are the latest chapter in [our] efforts to help engineers and technicians advance their careers, and to support manufacturers as they integrate advanced technologies into their operations.”
“In collaboration with ASME, we’re providing practical, project-based courses that equip students with essential skills for success,” adds Mary Hope McQuiston, vice president of education experiences at Autodesk. “Our curriculum empowers educators to integrate Industry 4.0 technologies and principles into their classrooms, fostering both technical expertise and collaborative skills needed for evolving manufacturing careers.”
To learn more about the Industry 4.0 courses, click www.asme.org.