AUTOMOTIVE ASSEMBLY
CONTACT
Austin
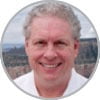
Lightweight battery-powered aircraft are ready for take-off.
Sustainable Interiors Tap Plant-Based Materials
Austin Weber // Senior Editor // webera@bnpmedia.com
Bioplastics and natural fibers help automakers address recyclability and lightweighting.
Automakers and suppliers are starting to use more sustainable interiors. Photo courtesy Mercedes-Benz AG
AUTOMOTIVE ASSEMBLY PRODUCTS
Agave, bamboo, flax, kenaf and seaweed aren’t things that most people associate with automotive interiors. But, that isn’t stopping engineers from using them as ingredients in a new class of eco-friendly materials, such as bio-based foams and trim coverings for center consoles, door panels, floor mats, headliners, instrument panels, seats and other cockpit components.
Automakers and suppliers are scrambling to create sustainable interiors for luxury sedans and electric vehicles. The goal is to create an earth-friendly alternative to traditional interior coverings (synthetic or traditional animal leather), while reducing the use of chemicals and water consumption.
“The biggest benefit of using eco-friendly materials for automotive interiors is that you’re able to recycle the materials, so they don’t end up in landfills,” says Ryan Bailey, head of R&D for the Americas at Continental AG, a leading supplier of surface materials for passenger car interiors. “We can close the loop to ensure we’re doing our part for the Earth.
“That’s the huge ‘why’ of using these types of materials,” explains Bailey. “One surprising benefit is that a lot of these materials create exciting new textures or designs that we wouldn’t have otherwise thought of. An example of this is the thermoplastic polyurethane monomaterial artificial leather that incorporates post-industrial polyurethane waste into the film, which creates a speckled surface appearance not possible with standard materials.”
Features
• Open frame designs allows access all around
• Tensioned with chordal compensating cam to reduce vibration
• Link pins use needle roller bearings for increased longevity
• Multiple drive options
Performance
• Zero-backlash in all directions
• High load capacity
• Long-term accuracy
• Fast and flexible indexing
Sankyo Automation
937-498-4901
beilert@sankyoautomation.com
www.sankyoautomation.com
IC80 Inline Chassis
Continental has developed a variety of products that feature recycled or eco-friendly raw materials. Some applications include cut and sewn interior parts, such as instrument panels, trim parts, seating and bolsters. It has also developed thermoformable materials for door panels, seat back panels and instrument panels.
“[We are] working with customers to develop eco-friendly surface materials for most applications in each of the product lines,” says Bailey. “The guiding principle behind the development is the reduction of the product carbon footprint (PCF), which is a measure of the carbon dioxide (CO2) associated with the life of the product from raw material creation to end of life.
“Our Benova polyurethane artificial leather product family has a new member, EcoProtect, which has nearly a 25 percent reduction in PCF,” claims Bailey. “Acella polyvinyl chloride artificial leather, an eco-friendly material already in serial production, has a reduction of 30 percent.
“With Xpreshn polyolefin thermoformable materials, a foam laminate construction is already available that has a PCF of almost zero,” adds Bailey. “That’s the first target for all materials where there is no negative carbon dioxide impact.
Makita’s cordless tools are the perfect solution for the high demands required of today’s automotive assembly factory. To meet these challenges, Makita offers precision torque you can trust, documented energy savings, proven ergonomic/safety benefits, and wireless communication that can document good and bad fastenings. To see how Makita’s complete lineup can benefit your factory, contact us today!
Makita USA, Inc.
Contact Sue Stenhaug
800-867-8265 ext 3121
sstenhaug@makitausa.com
www.makitaassemblytools.com
The Leader in Cordless Precision Fastening!
“As an example, our Xpreshn monomaterial textile consists of a polyolefin film that is laminated to an olefin-based textile carrier,” says Bailey. “Since both layers of the construction are polyolefin based, they are compatible and create a well-bonded composite. However, the similar chemistry allows for simple end-of-life thermomechanical recycling without separation of layers.”
This new vehicle uses a non-petroleum-based leather for its interior. Photo courtesy BMW AG
Seat of Sustainability
Magna International Inc. is another Tier One supplier that’s bullish on sustainable automotive interiors. The company has been focusing its R&D efforts on seats and door carriers.
“Part of our goal is to make a better world of mobility, and do it cleaner and responsibly,” says Carrie Young, chief engineer for seating innovation at Magna. “There are certain components in our seat systems that contain many different materials within those assemblies that are difficult to recycle and create a circular economy.
“There’s a big push in the auto industry today to lower CO2 emissions,” explains Young. “It’s all about recyclability and bio content. We want to ensure that not only are we creating these sustainable solutions, but we’re doing it while maintaining the same performance that the current products have.
“We see bio content being used for a variety of trim surfaces, including seats,” notes Young. “Many different subassembly components go into a trim cover assembly or a foam pad assembly. Just the amount of dissimilar materials in those components makes them very difficult to recycle at a vehicle’s end of life. So, unfortunately they end up as waste in landfills.”
To address those issues, Magna engineers recently developed a new line of products called EcoSphere that combine sustainability with performance. They feature monomaterial polyethylene terephthalate with 100 percent melt recyclable foam.
“You can take those components off and turn them over to a recycler that can mechanically grind it up, melt it down and create new polyester fibers,” says Young. “That creates a circular economy that can be used over and over again. Currently, it’s too difficult to disassemble a seat at a vehicle’s end of life.
“The EcoSphere product line focuses on the trim cover assembly, the trim foundation, the base pad assembly and structures,” Young points out. “This enables our seating materials to be repurposed and reused in the creation of new polyester products, contributing to a circular economy approach. Our technology offers automakers a game-changing opportunity to enhance sustainability without compromising comfort, quality or performance.”
The Omega 740 S wire assembly machine produces complex wire harnesses with terminal housings on one or both ends. Equipped with up to six modules and a carousel feeding system, it ensures optimal results, shorter lead times, and continuous, operator-independent quality for wire cross-sections from 0.13 to 1.5mm² (26–16 AWG).
Komax
800-521-3320
Fully Automatic Wire Harness Production
Aside from cost, one challenge faced by Magna’s engineers was ensuring that the performance of these products meets or exceeds automotive-grade specifications. To address that issue, they looked beyond material specifications and ran products through complete seat testing to make sure that all functional objectives were still being met, such as comfort, durability and safety.
“Typically, seats are assembled with clips, hook-and-loop fasteners, or hog rings to tie trim covers down to the foam pad assembly,” says Young. “We developed a way to continue using that same exact process, but do it in a sustainable way. With EcoSphere, we still keep those components attached and don’t have to worry about disassembling them. Because everything is monomaterial, it can all get recycled as a single assembly component.“
EcoSphere is not currently in any production vehicles, but we are working with several OEMs to get it launched,” explains Young. “It will be available within the next year or two. We’re also trying to determine where else this technology can be used in other automotive applications.”
European Influence
European automakers are leading the charge to sustainable interiors, due to strict environmental rules, such as end-of-life recyclability legislation. That’s why brands ranging from Audi to Volvo are unveiling green alternatives.
Let Fusion help streamline your brazing or soldering process! We transform manual processes into turnkey automation systems, providing years of cost-efficient production. Cut labor costs, increase production, and optimize output. Ready to learn more? Visit our website or contact us for a free consultation!
Fusion Incorporated
440-946-3300 / 800-626-9501
Automated Brazing and Soldering Machines
“There is significant interest from automakers from all regions,” says Continental’s Bailey. “However, the European market currently has a higher implementation rate for eco-friendly interior material.
“In North America, it is more challenging to find eco-friendly raw materials,” Bailey points out. “Because the raw materials can be so limited, they’re still considered a specialty product, with increased prices over the standard.
“Some people will pay more for a product that they know is [sustainable], so we are always juggling with how much the market will absorb,” says Bailey. “The availability of raw materials and the prices that limited availability creates are the two biggest challenges.”
Eco-friendly car seats are an alternative to traditional animal leather and synthetic skins. Photo courtesy Magna International Inc.
According to Bailey, newer automakers are more likely to adopt eco-friendly interiors compared to legacy companies. They see it as a way to differentiate their products and appeal to upscale consumers.
Electric vehicles are also a natural fit for sustainable interiors. That’s why EV start-ups such as Tesla offer things like bamboo-based vegan leather alternatives.
“The customer base targeted by EVs are excited about opportunities to do their part in good stewardship of the world for future generations,” explains Bailey. “This group of customers also generally are willing to pay the cost associated with leading the way on vehicles containing eco-friendly materials.”
“There is a growing global demand for integrating bio-based materials as automotive OEMs respond to consumer expectations and regulatory pressures to decarbonize vehicles and embrace circular consumption models,” adds Per Mårtensson, Ph.D., chief revenue officer at Bcomp Ltd., a Swiss company that specializes in lightweight materials made with flax fiber.
“Natural materials are extremely efficient when used and applied in the right way,” claims Mårtensson. "Flax is an easy-to-care-for and highly robust plant that has been used as a raw material for linen in the textile industry for millennia.”
Today, 75 percent of the world's scutched flax fiber is cultivated in western Europe. BComp’s natural fiber materials are already used in Cupra, Polestar and Volvo vehicles. In 2023, the Volvo EX30 compact electric SUV became the first production vehicle to use BComp’s ampliTex fiber composites for its dashboard and doors. The Polestar 3 is an electric SUV that also uses the robust flax-based material for various interior trimmings, such as seat backs.
Creating custom parts feeding solutions for 50 years, Performance Feeders continues to develop our comprehensive parts feeding product line, supporting the production of electric and autonomous automotive products. We design custom conveyors, vibratory, centrifugal, step and flex feeding systems and offer a variety of peripheral automation components to advance sustainable vehicle production.
Performance Feeders, Inc.
813-855-2685
Custom Solutions for Automotive Assembly
“Compared to conventional plastic trim, this can save more than half of the petroleum-based raw materials,” says Mårtensson. “Additionally, the material shines with its unique lightness and enables reduced vibrations."
“However, the issue of consumers’ general unwillingness to pay a premium for vehicles containing less plastic and more bio-based or recycled materials is compounded by the fact that plastics benefit from highly optimized and cost-effective supply chains rooted in linear consumption,” adds Christian Fischer, CEO of BComp. “[That is] without factoring in the environmental costs of landfilling at the end of a vehicle’s life.
“[Our products] address this gap by offering added value, such as lightweight design, high-performance and customization, enhancing the demand for bio-based materials, despite cost pressures,” notes Fischer.
“In [our] experience, this growing trend is most pronounced in Europe, where bio-composites are helping OEMs meet increasingly stringent regulatory standards aimed at reducing carbon footprints, improving recyclability and adhering to end-of-life vehicle directives,” says Fischer. “While the trend toward sustainability has been evident for years in Europe, it is now gaining traction worldwide, with increasing interest in the United States and Asia.”
- PW Series – Cordless Shut-Off Hydraulic Pulse
- TDIS Series – Pneumatic Shut-Off Hydraulic Pulse
- SCEP Series – Cordless Shut-Off Clutch
- IWT Series – Cordless Shut-Off Impact
- TDCS-D Series – Pneumatic Shut-Off Clutch
TORQTEC
919-561-5536
info@torqtec.net
www.torqtec.net
Featuring our DuPas Brand offering an operating range of 1 to 450 NM in the following Models:
Green Alternatives
The European Union’s proposed end-of-life vehicle regulation is still under study. However, it mandates that 25 percent of the plastic used in vehicles must be recycled from vehicles at their end of life.
“This regulatory approach will force some financial responsibility on OEMs for the full lifecycle of the vehicles they produce, from production through to the waste generated at the vehicle’s end of life,” predicts Mårtensson.
Bcomp’s range of flax-based technical fabrics are optimized for lightweight reinforcement with exceptional performance and quality. They meet automotive standards and are suitable for both interior and exterior applications.
The Volvo EX30 uses natural fiber materials for its interior. Photo courtesy BComp Ltd.
“What sets ampliTex apart is its ability to combine customizable, attractive surface designs—achieved through various weaves, fiber color and tinted resins—with high quality mechanical properties such as vibration damping, UV resistance and radio transparency,” explains Mårtensson. “This is all delivered with a low environmental impact.
“It is highly versatile and designed for large-scale automotive production,” claims Mårtensson. “And, it can be used in both structural and visual applications, such as interior trims and panels.
“For interior applications, ampliTex thermoplastic prepregs are a drop-in solution, as they are compatible with standard manufacturing processes like injection molding and compression molding, delivering both structural and visual features in one manufacturing step,” says Mårtensson. “This adaptability ensures seamless integration into diverse production methods, while delivering both functional strength and visual appeal.”
BComp also produces powerRibs, a lightweight, high-performance natural fiber reinforcement grid. With a design inspired by the veins of a leaf, they add maximal stiffness at minimal weight for interior car components, providing up to triple the flexural bending stiffness of thin shell components, while decreasing both material use and weight and improving vibration damping.
Automotive engineers are developing eco-friendly interiors that address new sustainability and recyclability initiatives. Photo courtesy BMW AG
“The powerRibs create a 3D structure on one side of a thin shell element, using less base material to decrease weight, as well as consumables and production costs, to achieve optimal performance,” explains Mårtensson. “They are ideal for reinforcing almost any thermoplastic composite shell structures made through compression molding.
“When combined with ampliTex technology and a layer of natural fiber polypropylene, powerRibs enable the efficient creation of recyclable, ultra-light, yet stiff components,” claims Mårtensson. “The grid further enhances stiffness and reduces weight, making it a versatile solution for high-performance, sustainable interior applications.”
Earth-friendly materials enable automotive parts to be recycled. Photo courtesy Continental AG
Cutting-Edge Applications
BComp has been working with engineers at BMW AG to develop applications for ampliTex and powerRibs. They recently created a lightweight seatback that features a natural fiber layup. The award-winning design took circularity and recyclability into account right from the start.
“We are already using existing technologies and materials to provide an outlook on the possibilities for reducing emissions and conserving resources in the future,” says Falco Hollmann, innovation manager for lightweight construction and sustainability at BMW. “This is not just about the substitution of materials, but above all about the topic of design for circularity.
“By combining the structural and aesthetically pleasing visual properties of the material in one manufacturing step, production is both more efficient and dematerialized,” explains Hollmann. He says less complex assemblies and materials that can be separated by type will enable the recyclability of the seat at the end of its life.
“Flax fiber composites are CO2 neutral from cradle to grave and can reduce manufacturing-related emissions of high-performance composite parts by up to 85 percent [vs. traditional] carbon fiber,” claims Hollmann. “Compared to current large-scale automotive plastic parts, flax fiber materials can reduce component weight by up to 50 percent, due to their low density and high stiffness.”
When BMW’s next-generation Neue Klasse vehicles begin rolling off the assembly line in Debrecen, Hungary, later this year, they will feature a number of innovations. Besides boasting 30 percent more range, 30 percent faster charging and 25 percent more efficiency, the EVs will sport new eco-friendly interiors that reduce their carbon footprint.
This vehicle’s interior features parts made from plant-based materials. Photo courtesy BComp Ltd.
A completely plant-based, mineral-based and petroleum-free surface material called Verdana was developed for interior applications. The Neue Klasse X sport utility vehicle will use the material for its center console and lower portion of door paneling.
“Maritime plastics are also being utilized for the first time for injection-molded parts,” says Adrian van Hooydonk, head of design at BMW Group. “In selected components, this secondary raw material, which is obtained, for example, from discarded fishing nets, already accounts for 30 percent. The choice of materials and construction method enable easier disassembly of components and improved recyclability.”
BMW is also working with an American start-up company called Natural Fiber Welding Inc. (NFW). It relies on a process developed by engineers at the U.S. Air Force Research Laboratory that has been successfully used with plant-based materials such as cotton, flax, hemp, jute and sisal.
Natural fiber welding is a process in which individual fibers are swollen by an ionic liquid-based solvent to form a congealed network. It is controlled by the composition of the solvent, which includes a liquid solvent plus additives such as methanol and water. Conditions, such as the amount and placement of solvent, and process variables, such as time, temperature and pressure, control the extent to which fibers are fused.
NFW recently developed a non-petroleum-based leather alternative for car interiors. Mirum is made from natural rubber, natural fibers, plant oils, natural pigments and minerals. It provides superior durability and quality that can replace traditional animal-based or synthetic leather products without the use of any polyurethane or other coatings.
“A company with Ford’s scale can really influence the supply chain and business practices across our entire industry,” adds Sue Slaughter, purchasing director at Ford Motor Co. “It is so important that we not only think about how [we] can use our purchasing power to fuel our business needs, but also to advance sustainability.”
Because the automotive supply chain is extremely complex, the Guiding Principles contain expectations about business ethics, working conditions, human rights, health and safety, environmental leadership and supply chain due diligence for suppliers at all tiers. All suppliers are expected to uphold these standards and enforce them throughout their supply chain.
The Guiding Principles are based on fundamental elements of social, environmental and governance responsibility that are consistent with applicable laws and international standards created by organizations such as the United Nations.
Topics covered under the revised guidelines include the following:
Business ethics, including counterfeit parts and data protection.
Environmental issues, such as air quality, carbon neutrality, chemical management, circularity and water management.
Health and safety issues, such as personal protective equipment and workspace.
Human rights and working conditions, such as benefits, wages and working hours.
Responsible supply chain management, such as ethical sourcing of raw materials.
The BMW Group has implemented several projects in its packaging logistics unit to help the environment and conserve resources. The goal of the initiative is to work closely with suppliers to reduce carbon emissions and adhere to the principles of a circular economy.
BMW’s European assembly plants are using more recycled material in their packaging. For newly awarded contracts, the proportion of recycled material in reusable packaging for logistics purposes will almost double this year from around 20 percent to over 35 percent.
Using alternative sustainable materials, reducing single-use packaging, introducing lightweight packaging in certain areas and reducing transport volumes will also help cut carbon emissions.
BMW is monitoring the impact of individual measures via a CO2 calculator for packaging. The automaker’s overall aim is to reduce CO2 emissions in the supply chain by 20 percent per vehicle compared to 2019.
“Our re:think, re:duce, re:use, re:cycle approach is being implemented consistently in packaging logistics,” says Michael Nikolaides, head of production network and logistics at BMW Group. “We’re using innovative strategies to consistently reduce the volume of resources we use, thus reducing our carbon footprint.
“We are also doing our part to get the BMW iFACTORY up and running, with a particular focus on the ‘green’ side of things…with an emphasis on flexibility and efficiency, sustainability and digitalization,” explains Nikolaides. “It provides an answer to the challenges involved in the transformation to e-mobility and [leverages] the latest technologies to create a production process that uses minimal resources.”
According to Nikolaides, BMW is using more recycled material, such as expanded polypropylene (EPP) packaging. “Our newly developed EPP packaging already contains 25 percent recycled material,” he points out. “EPP is used in special containers, as its shape can be adapted to the components being packaged, allowing them to be transported safely.
“Around 360,000 of these containers are needed each year,” claims Nikolaides. “Using 25 percent recycled material allows us to save almost 280 tons of CO2 annually. There are plans to increase this proportion of recycled material even further, with the first pilot schemes with 100 percent recycled material currently underway. If these tests are successful, this configuration will become standard for new contracts from 2024.
“An additional 680 tons of carbon emissions savings can be made every year by using covers and so-called small load carriers with 50 percent recycled contents,” says Nikolaides. “As things stand, these measures are focused within the European markets due to the current waste management situation and available recycling infrastructure. But, we are working toward expanding to our locations in China, Mexico and the United States.”
BMW also plans to use folding large load carriers in place of traditional pallet cages made of steel. The plastic alternatives will be made from over 90 percent recycled material. They work in a similar way to the collapsible shopping crates that most people are familiar with.
When they’re empty, the carriers can be folded up, making them easier to transport. Nikolaides claims that using 15,000 of these new containers will reduce CO2 by around 3,000 tons per year.
“When it comes to packaging, the sky’s the limit,” says Nikolaides. “We’re launching pilot projects using bio-based materials to replace oil-based substances such as polyethylene and polypropylene.
“We are also investigating whether and in what ways we can use materials from recycled household appliances in our packaging,” explains Nikolaides. “In the long term, our aim is to use alternatives to raw materials across the board.”
BMW Initiative Targets Sustainable Packaging
BMW is using sustainable packaging in its assembly plants. Photo courtesy BMW Group
ASSEMBLY ONLINE
For more information on sustainable automotive materials, visit www.assemblymag.com to read these articles: