July 2023
ROBOTIC ASSEMBLY
Robots Star at Automate
The latest robotic technology was on display at the automate show in May.
Robots Star at Automate
The latest robotic technology was on display at the Automate show in May.
John Sprovieri // Chief Editor
Automate, the largest robotics and automation trade show in North America, was held May 22-25 in Detroit. More than 30,000 people from around the world registered to attend the show, which featured 757 exhibitors.
“I want…to thank all the sponsors, speakers, exhibitors and attendees who contributed to making Automate 2023 such a tremendous success,” says Jeff Burnstein, president of the Association for Advancing Automation (A3), the organizer of the event. “As this show demonstrated, demand for robotics and automation technologies is accelerating as companies in every industry seek automation solutions to improve their competitiveness.”
Here’s a look at some of the products on display at the show.
High-Payload Cobots
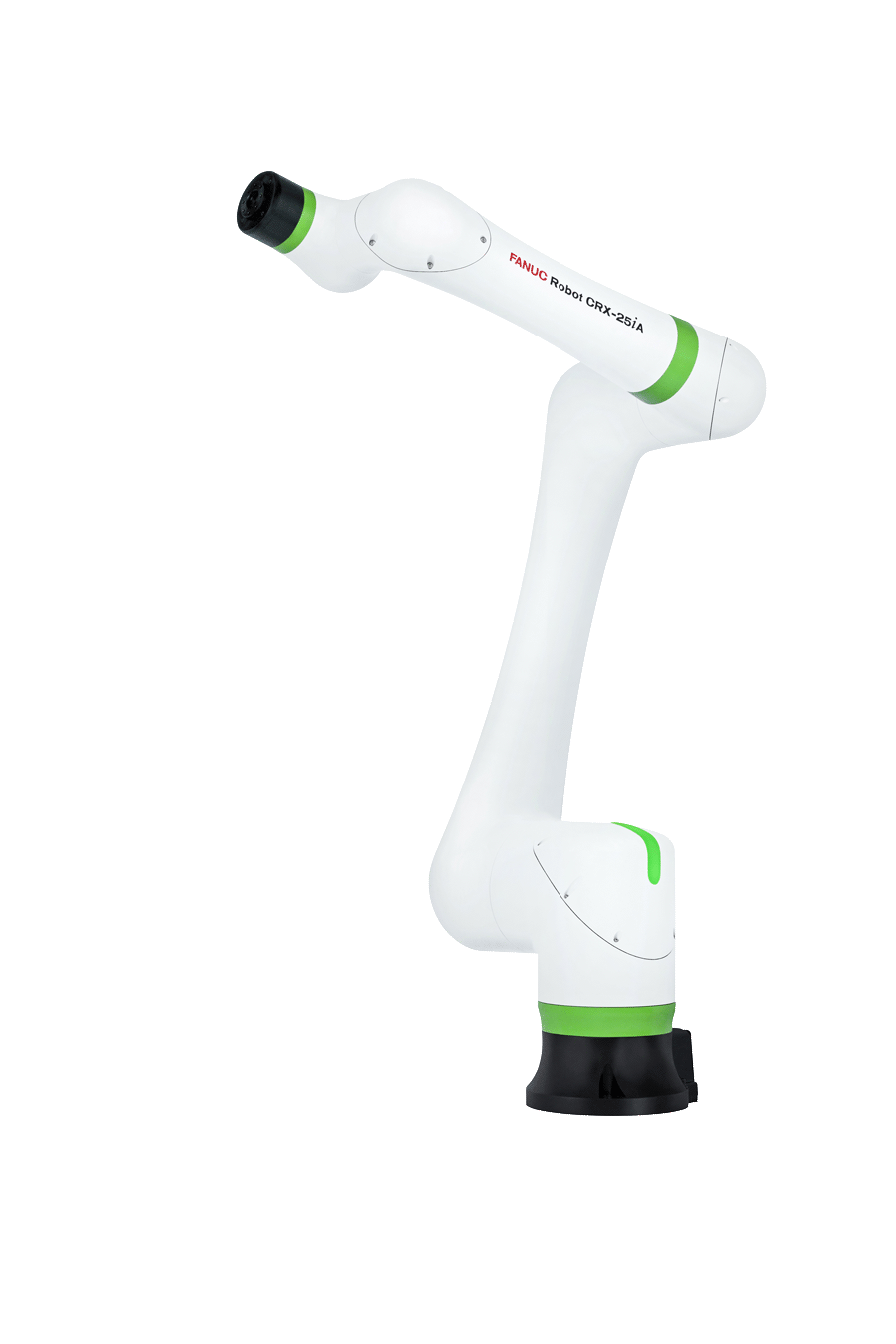
FANUC has increased the payload capacity of two of its collaborative robots. The CRX-25iA cobot now has a maximum capacity of 30 kilograms, while the CR-35iB cobot can now handle 50 kilograms.
At Automate, the CRX-25iA cobot demonstrated its new capability by handling a 30-kilogram kettle bell with full wrist articulation. A second CRX-25iA, equipped with the FANUC Servo Torch, showcased the cobot’s 1,889-millimeter reach in a hands-on welding demonstration. Easy-to-use interactive programming allows operators to teach points using hand guidance or a teach pendant with drag-and-drop icons.
The CR-35iB is the industry’s strongest collaborative robot featuring a large work envelope and a small installation footprint. A streamlined and lighter mechanical unit includes FANUC’s latest sensor technology for safety.
At Automate, a CR-35iB equipped with 3DV iRVision, located and picked castings on a pallet and placed them on a shelf to represent a flexible automated storage and retrieval system. The cobot then returned the parts back to the pallet. The demonstration showed the cobot’s ability to adjust when the pallet location shifts.
FANUC America Corp.
Flexible Gripper For Small Components
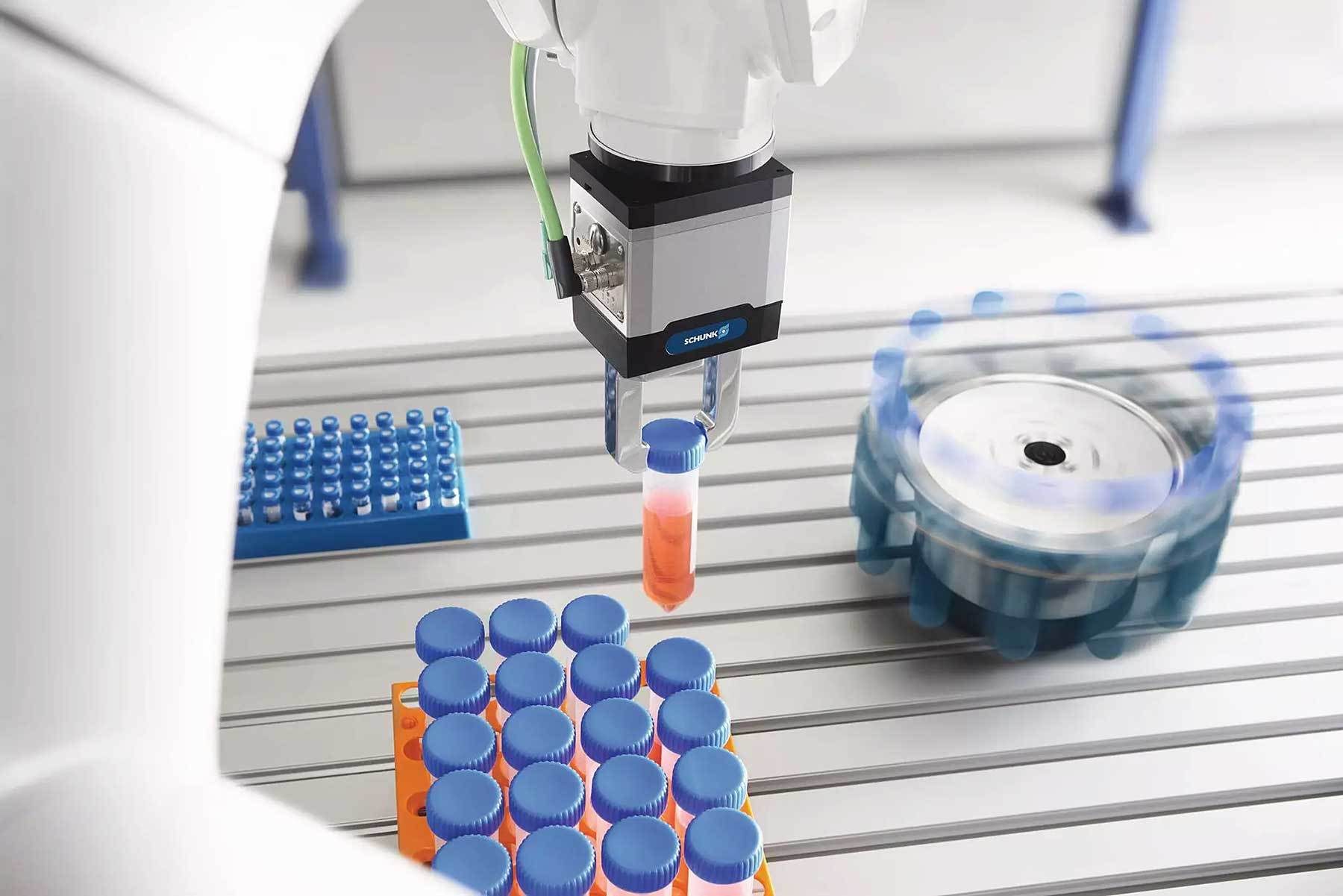
The EGK is an intelligent, versatile gripper for handling small, fragile components, such as glass vials or circuit boards.
The electric gripper has a spur gear and rack-and-pinion to ensure constant gripping force over the entire finger length and allow permanent re-gripping. Since no startup distance or force impulse is required for power generation, the gripper delivers 100 percent of its performance right from the start. The integrated gripping force maintenance avoids the loss of workpieces and holds the finger position even in the event of an emergency stop.
A high-resolution, integrated absolute encoder offers additional process transparency. It permanently captures the base jaw’s position. Therefore, the gripping process can be continued after power failure or reboot without new referencing.
Depending on the gripper size, the highly flexible component range enables various workpieces to be handled with the same gripper due to its long, freely programmable jaw stroke and continuously adjustable gripping force of 20 to 300 newtons. For sensitive gripping of particularly fragile workpieces, SCHUNK has equipped the EGK with a special “SoftGrip” mode, in which almost no impulse forces are acting.
The gripper is certified for use in clean rooms. It is lubricated with food-compliant H1-grease, and it is equipped with a sophisticated three-stage sealing concept that protects gears and electronic components effectively while minimizing wear. Its control and power electronics are also fully integrated and sealed according to protection class IP 67.
Available in three sizes, with and without a brake, the gripper has a variety of interfaces and can be integrated into the following networks: Profinet, EtherCat, EtherNet/IP, IO-Link and Modbus RTU. Robot plug-ins and PLC function modules reduce programming effort during commissioning.
SCHUNK
All-In-One Scaras
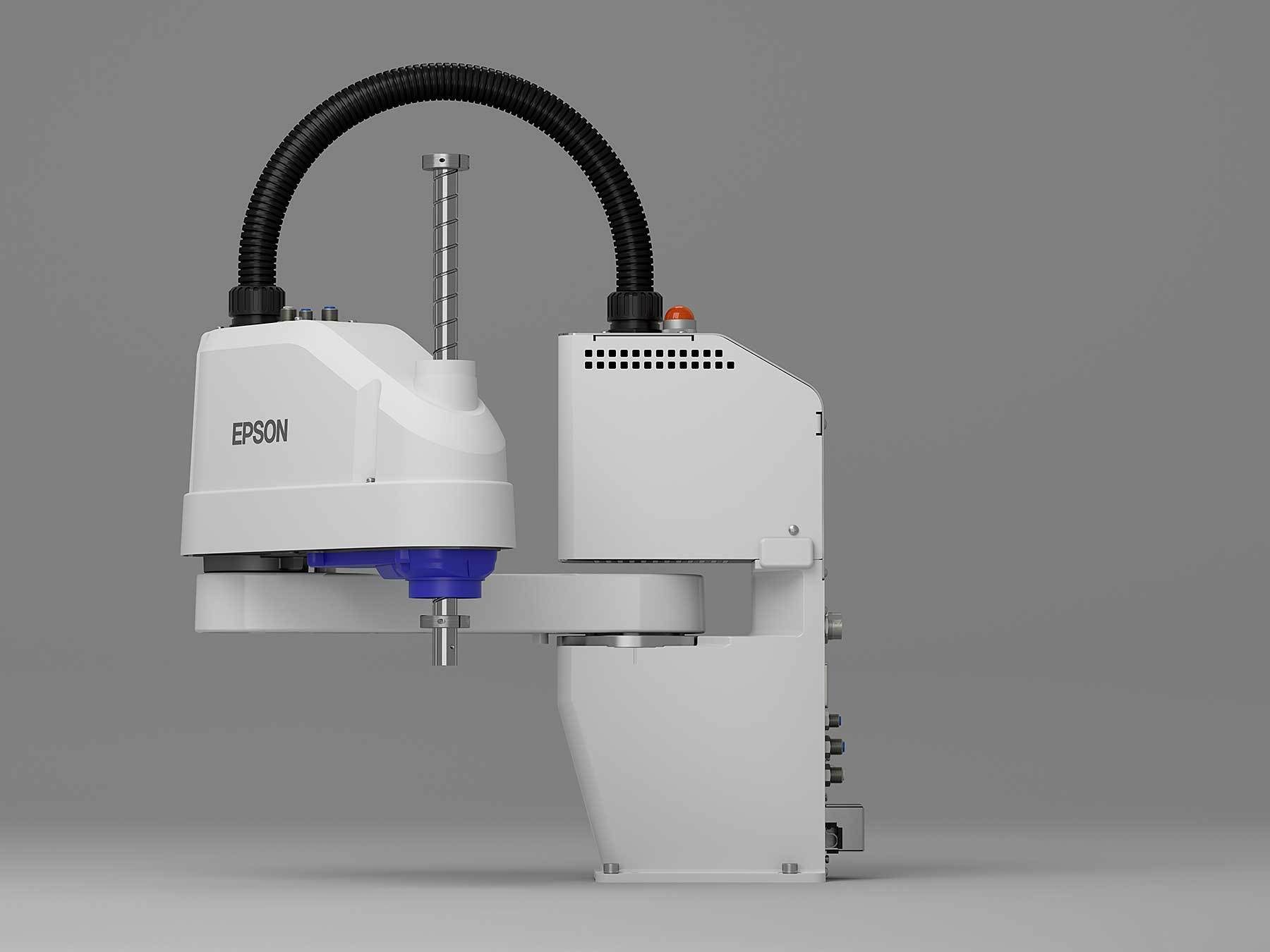
The T3-B and T6-B all-in-one SCARA robots offer high-quality and high-performance at an exceptional value to simplify both complex and simple automation applications, such as packaging, pick and place, dispensing, and inspection. These robots include the same intuitive software, features and reliability found in Epson’s high-end robots, while keeping total cost of ownership low.
The robots have a space-saving design that includes a built-in controller housed in the robot’s base with power for end-of-arm tooling. The T3-B and T6-B are compatible with Epson’s suite of integrated options, including vision guidance, IntelliFlex parts feeding, teach pendants, and fieldbus master and slave interface boards. Additional updates include an improved form factor design and updated motion control for smoother, faster cycle times.
Designed for ease of use, the T3-B and T6-B come equipped with Epson RC+ and no-code Epson RC+ Express industrial automation development software. Ideal for novice and advanced users, Epson RC+ is an easy-to-learn programming language that offers a powerful set of tools for automation. An intuitive, visual-based teaching environment, Epson RC+ Express is designed for users with little-to-no programming experience to easily and efficiently develop simple, powerful robotic programs.
The robots run on standard 110- and 220-volt power; no special panel or plug is required. No battery is required for the robot’s encoder, which minimizes downtime and reduces overall cost of ownership.
Epson Robots
Flexible Robotic Cell
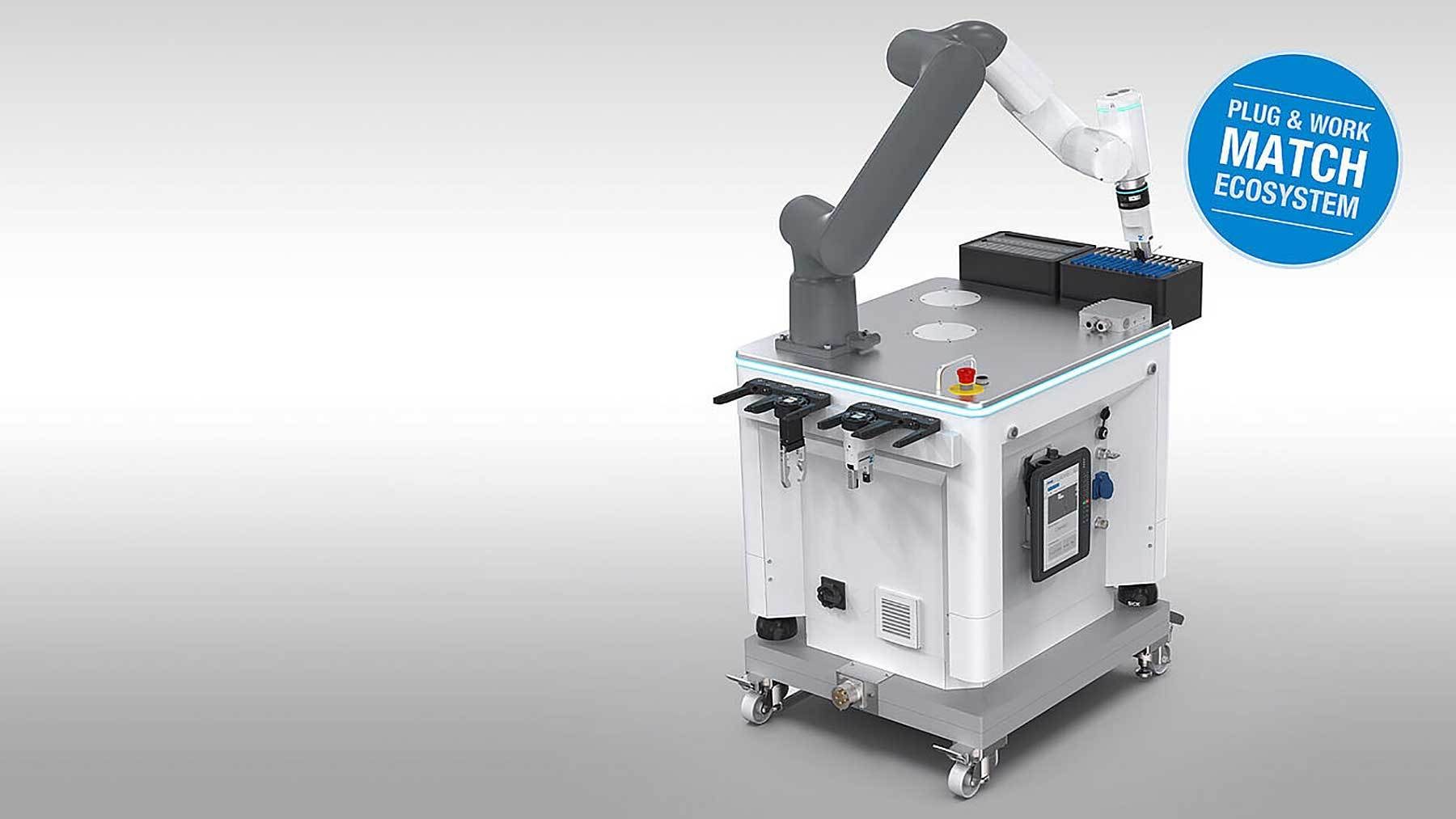
ZiMo is a simple, inexpensive, mobile robot workstation for automating small- and medium-sized batch production in high-mix operations. Its compact size enables engineers to position the robot in any production situation. Commissioning and operation is easy via a robot-neutral human machine interface. No programming knowledge is necessary. Engineers can choose from a wide portfolio of accessories, individually tailored to specific requirements.
Zimmer Group
Multi-Axis Motion For Universal Robots
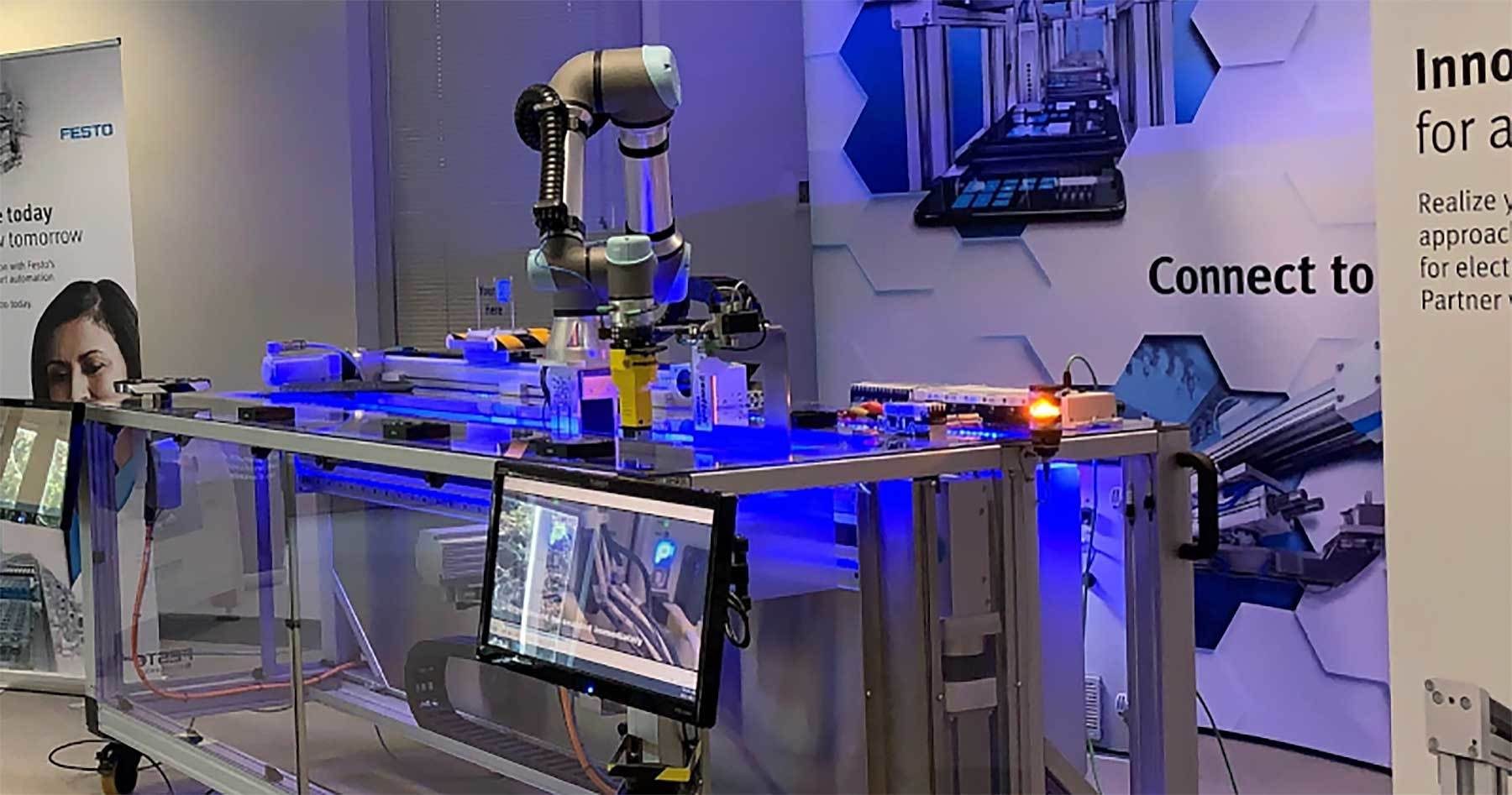
The Festo Motion Control Package (FMCP-UR) is a complete motion control panel for up to four axes motion to complement the operation of a six-axis collaborative robot from Universal Robots (UR). The FMCP is fully integrated with UR’s cobot control panel and HMI and features an enhanced safety I/O handshake and communications interface.
The FMCP-UR can control turntables, gantry systems, conveyors, transfer tables, and any combination of linear and rotary servo axes up to the 10th axis.
Streamlined axis configuration allows for less engineering, integration and troubleshooting during setup and can be easily done through the UR HMI. The Multi-Axis Drive controller is a URCap software that allows engineers to set position, peed, and acceleration on the HMI or use the toolbar to jog the axes in manual mode to configure motion.
Festo Corp.
To use a welder equipped with dynamic mode, the engineer selects the single-parameter weld mode that provides the best application results. Then, the engineer enters two application-specific “scores,” which act as limits for dynamic mode activity. The first is a material density score that characterizes the hardness or resistance of the material to be welded. A low density score equates to a harder, more resistant material. The second is a weld reactivity score, which fine-tunes the reaction time the welder needs to achieve the desired density setting. In operation, dynamic mode monitors each weld cycle, using the density and reactivity limits to optimize the cycle in response to specific part-to-part variabilities throughout production.
Dynamic mode ultrasonic welding can outperform single-parameter weld modes when:
- assembling electronic components that are sensitive to pressure, vibration or heat damage.
- close-tolerance assemblies containing sensitive components require hermetic seals.
- part structures rely on consistent performance of flexible or elastomeric components.
- elements must be staked or inserted into substrates that vary in hardness or structural consistency.
For example, consider the need to weld a form-fitting, watertight plastic cover onto the shell of a small electronic device. The cover is closely contoured to fit around the electronic components. The cover must be bonded gap-free and watertight, but the weld process and cover structure cannot be allowed to contact or compress the electronics directly beneath. Due to ordinary part variability, reliance on a single-parameter weld mode, such as collapse distance, could exert excessive pressure on the cover and damage the electronics. With the help of material density and reactivity scores, the dynamic welding mode can optimize the collapse distance in each weld cycle to ensure a tight seal without compressing the electronic components.
Dynamic mode is also useful for bonding plastic assemblies that contain compressible materials. Consider, for example, an elastomer-filled, two-way pin connector. The outer shell of the connector consists of a molded plastic cup and lid that contain holes through which metal connecting pins protrude. Inside, the pins are embedded in a compressible core of elastomeric plastic, topped by a weld-on lid that compresses the elastomer radially around the pins. Despite the fact that the elastomeric cores vary in height, sealing of the plastic lid requires a flat fit.
In dynamic weld mode, the density score enables weld-by-weld adjustment that compensates for the varied consistency and height of each plug’s elastomer core. It ensures that the weld actuator travels the required depth and that it “feels” the specified amount of resistance before welding the lid.
Emerson
Heavy-Duty Tool Changer
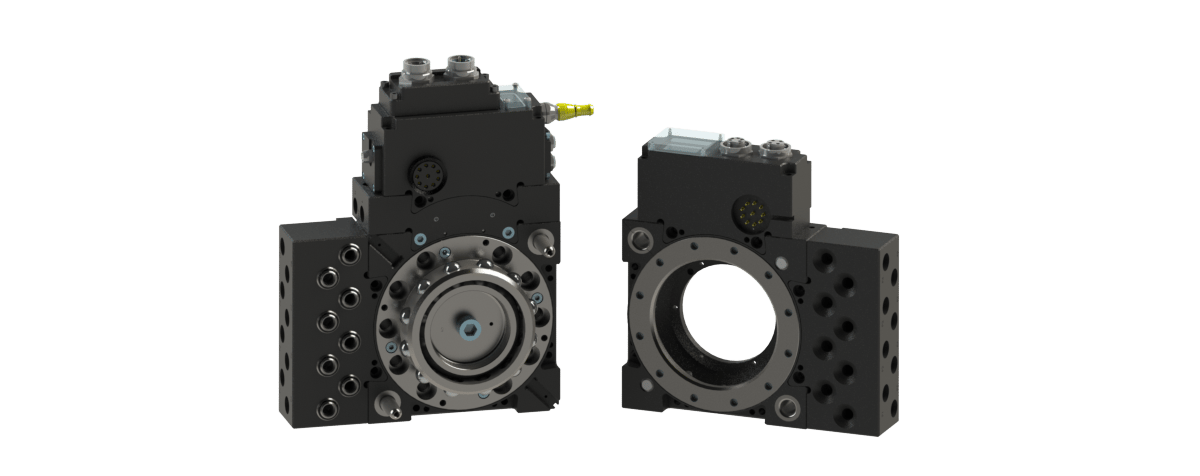
In a large cell, ATI demonstrated how its heavy-duty tool changers are used to automatically switch large end-effectors. A FANUC R-1000iA/80F robot, equipped with a ATI QC-210 tool changer, simulated the joining of automotive B-pillar assemblies by changing between an Atlas Copco K-Flow flow-drill fastening tool and an Atlas Copco SCA dispensing tool.
The QC-210 features modular construction. High power, coolant, servo, DeviceNet, and discrete signal capabilities are built into separate modules making maintenance easy. Internally routed cabling supports integrated valve and DeviceNet options, making it easy to add and remove the valve and DeviceNet module. The modules are designed to place electrical, pneumatic and water ports in-line. Modules can be rearranged to accommodate dress needs.
The tool changer has a maximum payload of 660 pounds, a static moment capacity in the X and Y axes of 24,000 inch-pounds and a static moment capacity in the Z axis of 20,000 inch-pounds. At a pressure of 80 psi, it provides a locking force of 7,000 pounds.
ATI Industrial Automation
Modular Tooling
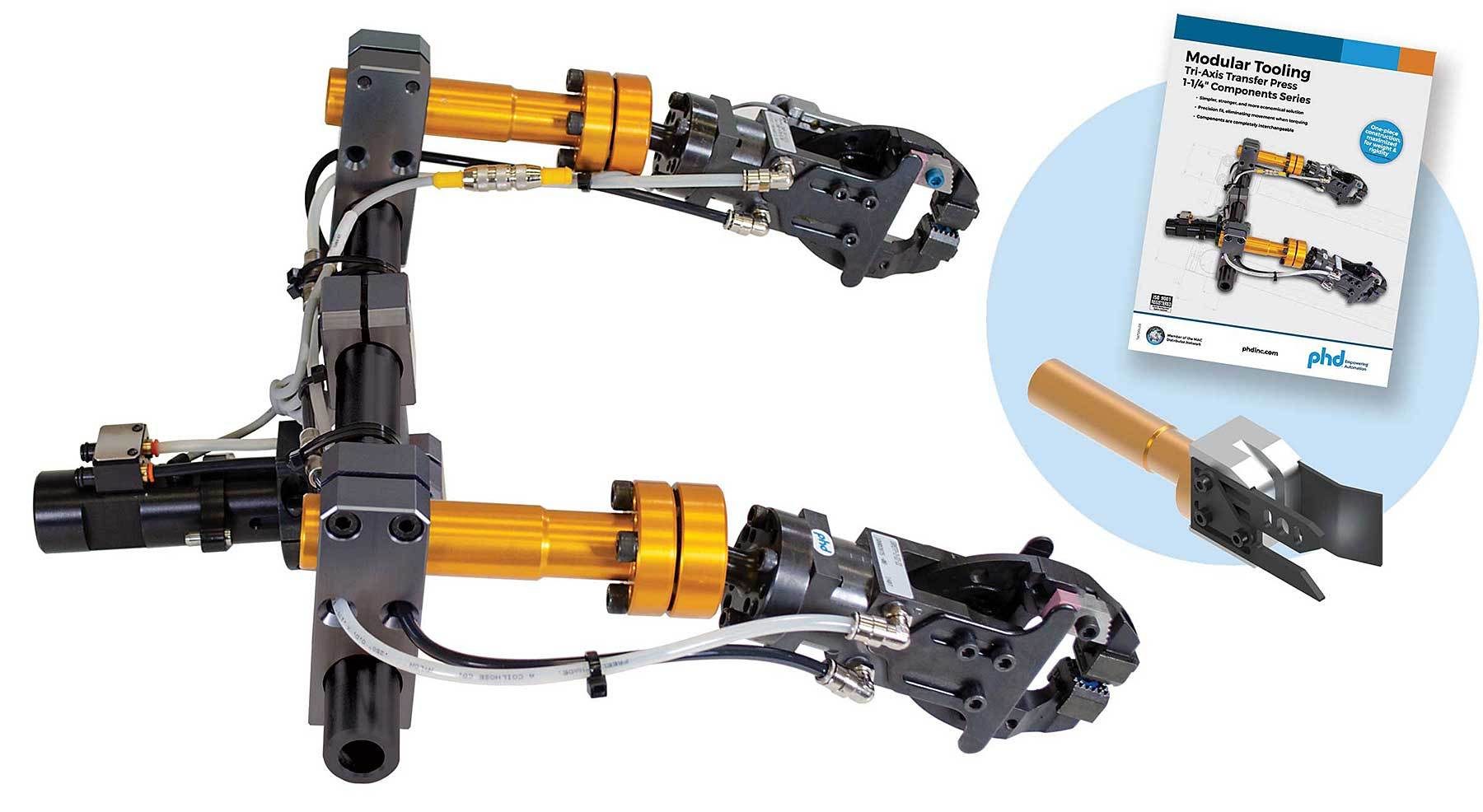
Tri-Axis modular tooling components for transfer press systems are strong, lightweight and versatile. These components are one-piece construction, completely interchangeable, and have been maximized for light weight and rigidity. When combined with the GRM Series of automated sheet-metal handling clamps, these components optimize the performance of high-speed tri-axis transfer presses.
Recent additions to the tooling components lineup include Receiver Adapters and Modular Shovels. Receiver Adapters plug into the rail receiver (docking device) and, when securely latched, create a pneumatic and electrical connection for the transfer finger assembly to the press feed bar. Modular Shovels are used in conjunction with GRM clamps. Their flexible design makes it easy to create a shovel that delivers optimum support and control of the panel through the transfer press. These modular components can be rebuilt and repurposed for future applications.
PHD Inc.
Modular Multi-Stage Vacuum Pump
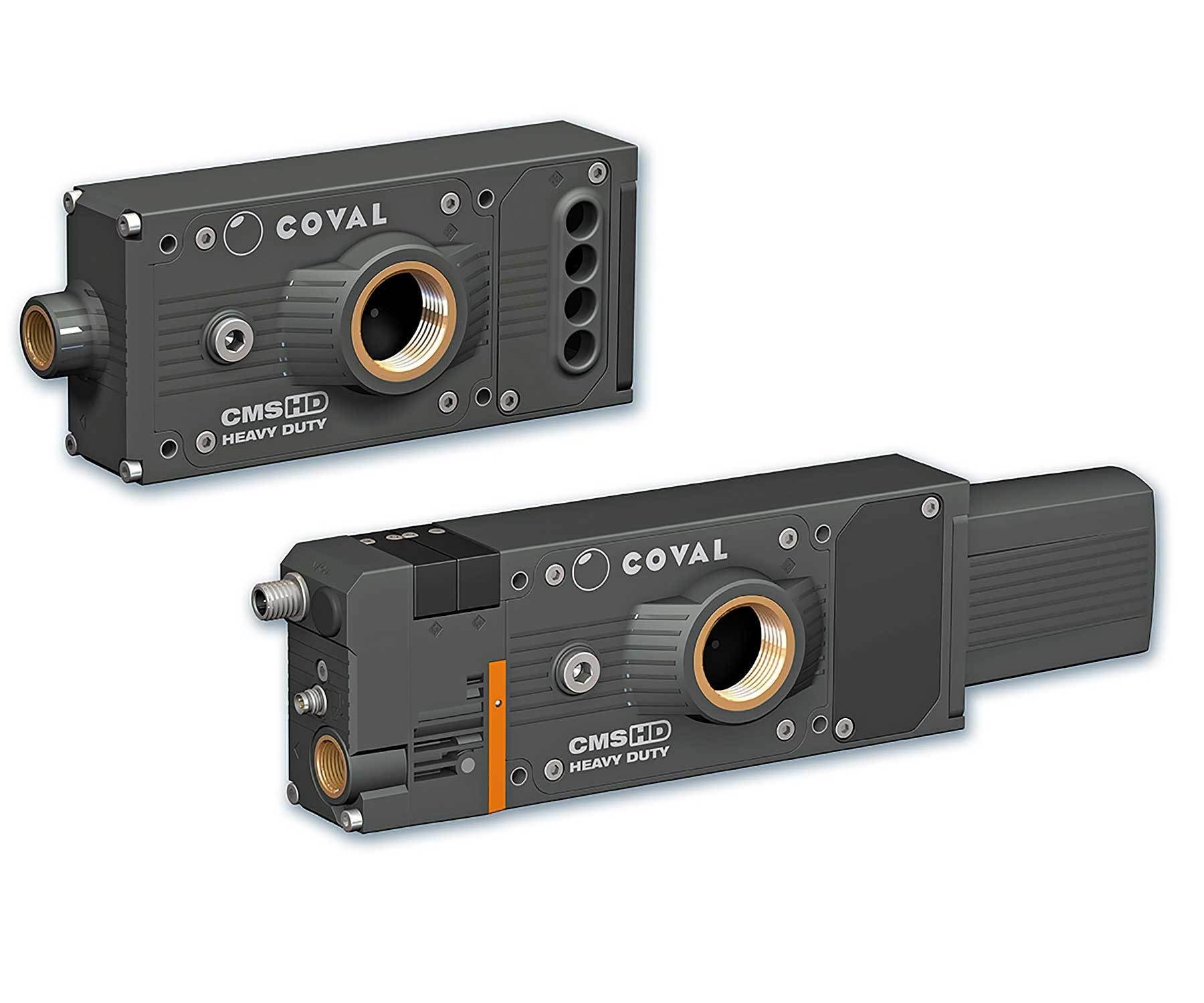
The CMS HD series of modular multi-stage vacuum pumps are for high-suction flow rate vacuum handling of a wide variety of objects. The pumps are ideally suited for pick-up and transfer operations in applications such as handling of porous parts or emptying large-volume tanks.
The new pumps improve on the performance of previous models in three areas: power, robustness and modularity. The pumps are specified to handle flow rates up to 1,300 normal air liters per minute. These heavy-duty pumps withstand harsh environments. The IP65-rated pumps are designed for a service life of 50 million cycles. With their modular design, the pumps can be configured with a selectable flow rate, with or without piloting, and with three configurable exhaust methods, depending on the application. The modularity allows each of its subassemblies to be accessed individually for servicing, which also improves the reparability rate.
Some models offer a fully integrated control system, making them easy to install, even where space is limited.
Coval
ASSEMBLY ONLINE
For more information on robotic assembly, visit www.assemblymag.com to read these articles: