JUNE 2023
SCREWDRIVING AND RIVETING
What’s New With Conveyors
Conveyors remain essential for getting parts to the right spot at the right time. Here’s a look at the state of the art.
What’s New With Riveting
Here’s a look at some of the latest riveting technologies.
John Sprovieri // Chief Editor
Threaded fasteners are the most common method of product assembly. The primary advantage of threaded fasteners is that they permit disassembly of the parts for repair or recycling.
If, however, the parts need not or should not be taken apart, then rivets are a more cost-effective way to go. Rivets install faster than screws, and there’s no need to tap threads in the parts. With threaded fasteners, engineers rely on one variable, torque, as an indirect measure of what they really want to know, which is the clamp load on the joint. That’s not the case with riveted assemblies. With rivets, engineers can specify exactly how much force will be applied by the fasteners.
The following is a look at some of the latest products for forming or installing rivets.
400 Clinches On One Charge
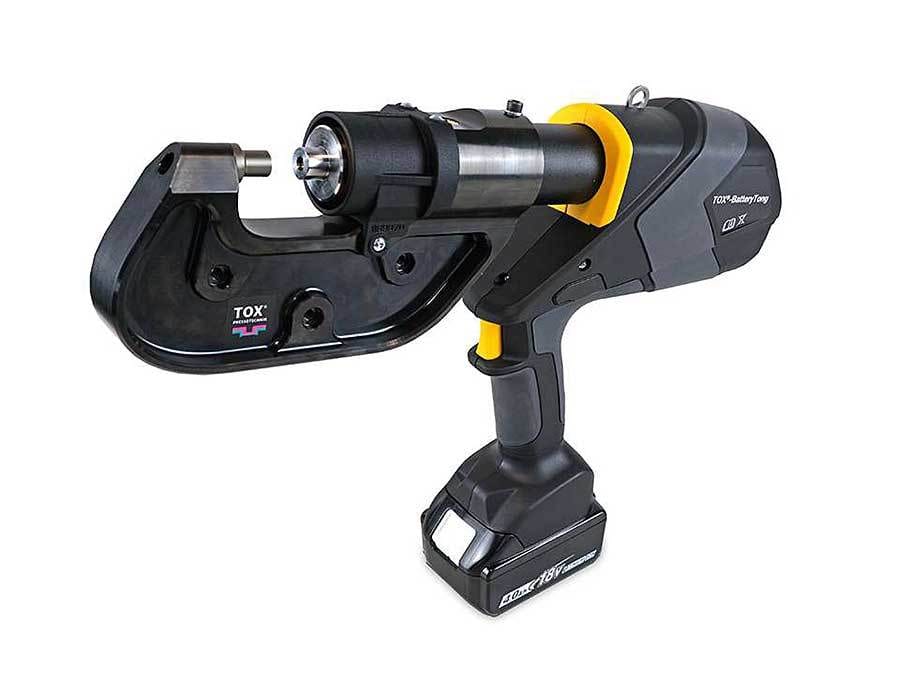
The TOX-BatteryTong MBT-C 050 is a handheld, battery-powered clinching tool. This easy-to-operate tool weighs less than a comparable hydropneumatic tool and can be used anywhere, thanks to the rechargeable battery. Including the lithium-ion battery, it weighs only 7 kilograms and generates a pressing force of 10 to 50 kilonewtons. Force is adjustable in 1 kilonewton increments. This makes it powerful enough to permanently join different materials and metal thicknesses.
Available with either a 30- or 60-millimeter wide C frame, the tool can set up to 400 clinch points with one battery charge. Cycle time is six seconds. The tool can export fastening data via a Bluetooth interface.
The tool is supplied in a case and includes clinching tools, battery and charger. Options include an extra battery and a dimensional gauge for checking the thickness of the clinch point.
See this product at The ASSEMBLY Show, booth 442.
TOX Pressotechnik
CNC Riveting Machine
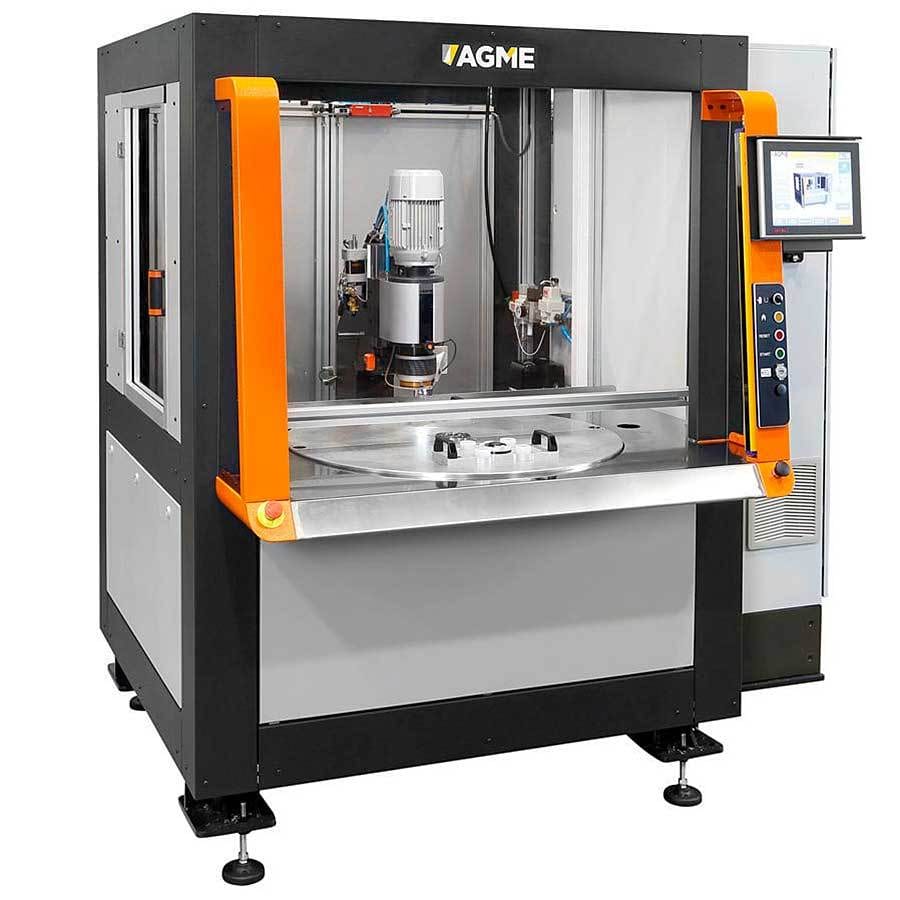
Available with two or three servo-controlled axes, the RA-NCD CNC-controlled riveting machine can automatically head multiple rivet points, in sequence, at various heights and locations.
Flexible, robust, ergonomic and easy to program, the machine is equipped with AGME’s fourth-generation RA-UC series riveting head. The enclosure has removable panels for better accessibility for maintenance. The electrical cabinet is narrower and more accessible than previous models, and the keypad and control screen are closer and more accessible to the operator.
The tactile HMI is intuitive to operate. Users can create, copy, edit and delete riveting programs without having specific programming knowledge. Control is carried out by a standard Siemens PLC, which manages programs and machine signals and tells the servomotors the exact location of each riveting operation.
See this product at The ASSEMBLY Show, booth 1717.
AGME
Auto-Feed Riveting Tool
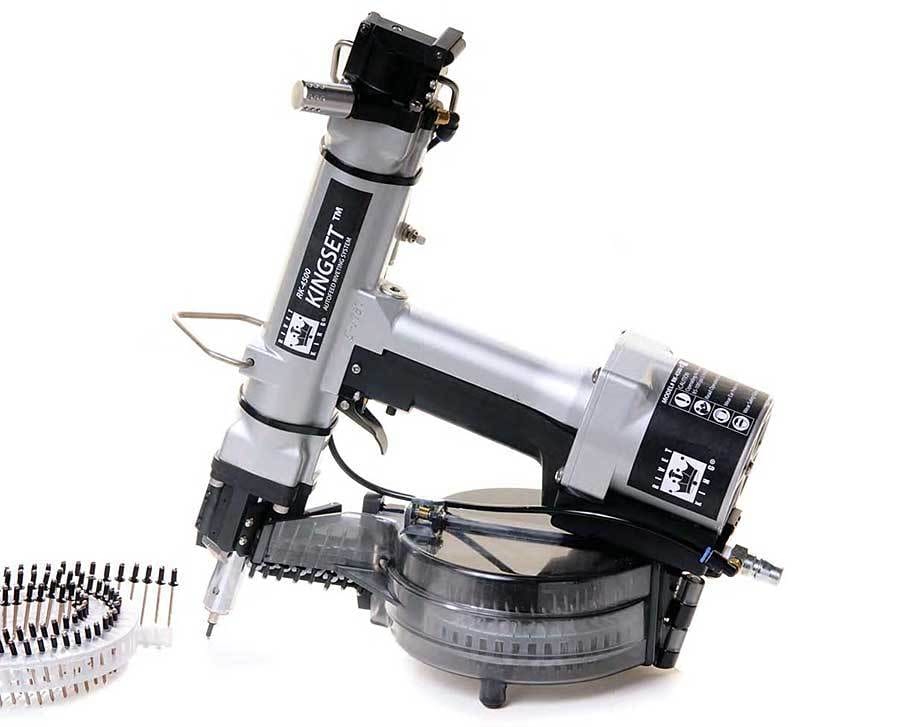
The KingSet is a handheld autofeed tool for installing break-stem rivets. Automatic feeding enables the operator to align workpiece holes with one hand while riveting with the other, which saves time. This portable tool can be suspended horizontally or vertically.
The tool can apply rivets of many sizes with minimal changeover time. It can set most 1/8- and 5/32-inch rivets in any material, as well as certain 3/16-inch blind rivets. The tool can even install rivets in a downward position for 360-degree flexibility.
It takes two seconds to install a rivet and feed the next fastener on the strip automatically. The tool accommodates up to 100 rivets per coil, and only eight seconds are needed to changeover between strips.
The tool is more economical than bowl fed, blow feed or pick-and-place systems, since it has fewer parts and needs less air to operate.
The tool’s ergonomically balanced design and one-touch operation allows users to set rivets automatically. Operators don’t need to focus on picking, placing and keeping the rivet in the nose of the gun. For even greater efficiency, an adjustable vacuum system minimizes air consumption based specifically on the size of the rivet being set. A built-in mandrel collection system vacuums up all disposed nails.
See this product at The ASSEMBLY Show, booth 1139.
Industrial Rivet & Fastener Co.
Tool Installs Lockbolts

The Feed-n-Swage is a semiautomatic tool for installing LPG lockbolts. The operator presents the nose to the pintail, and a feeder dispenses a collar on the pin. The feeder pivots, exposing the nose for installation, while picking up next collar. Next, the feeder automatically returns to its original position for the next lockbolt installation. A feeder bowl automatically reloads the collar feeding tube in less than 1 minute.
See this product at The ASSEMBLY Show, booth 351.
Gage Bilt Inc.
Benchtop Radial Riveter
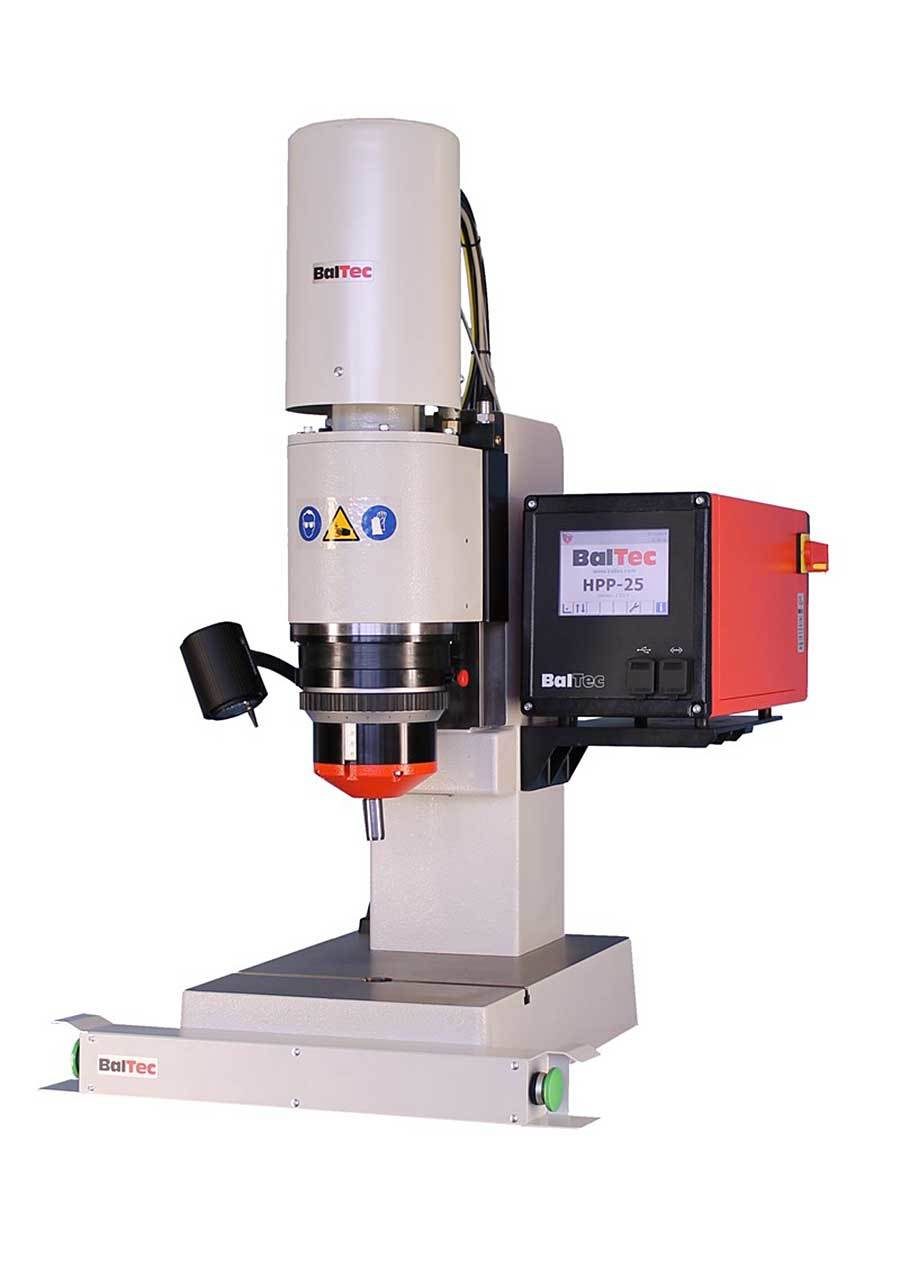
Model RN281-RC3 is an electropneumatic benchtop radial riveting machine. Riveting force ranges from 5.67 to 17 kilonewtons, and stroke length ranges from 5 to 40 millimeters. It can form rivets up to 12 millimeters in diameter.
It has two-hand control switch, a time-based control, and an adjustable task light. Options include a sensor for detecting when the spindle is in work position; a workpiece detection device; a probe arm and probe; and an automatic spindle lubrication system with lubricant level monitor.
See this product at The ASSEMBLY Show, booth 1223.
Baltec Corp.
To use a welder equipped with dynamic mode, the engineer selects the single-parameter weld mode that provides the best application results. Then, the engineer enters two application-specific “scores,” which act as limits for dynamic mode activity. The first is a material density score that characterizes the hardness or resistance of the material to be welded. A low density score equates to a harder, more resistant material. The second is a weld reactivity score, which fine-tunes the reaction time the welder needs to achieve the desired density setting. In operation, dynamic mode monitors each weld cycle, using the density and reactivity limits to optimize the cycle in response to specific part-to-part variabilities throughout production.
Dynamic mode ultrasonic welding can outperform single-parameter weld modes when:
- assembling electronic components that are sensitive to pressure, vibration or heat damage.
- close-tolerance assemblies containing sensitive components require hermetic seals.
- part structures rely on consistent performance of flexible or elastomeric components.
- elements must be staked or inserted into substrates that vary in hardness or structural consistency.
For example, consider the need to weld a form-fitting, watertight plastic cover onto the shell of a small electronic device. The cover is closely contoured to fit around the electronic components. The cover must be bonded gap-free and watertight, but the weld process and cover structure cannot be allowed to contact or compress the electronics directly beneath. Due to ordinary part variability, reliance on a single-parameter weld mode, such as collapse distance, could exert excessive pressure on the cover and damage the electronics. With the help of material density and reactivity scores, the dynamic welding mode can optimize the collapse distance in each weld cycle to ensure a tight seal without compressing the electronic components.
Dynamic mode is also useful for bonding plastic assemblies that contain compressible materials. Consider, for example, an elastomer-filled, two-way pin connector. The outer shell of the connector consists of a molded plastic cup and lid that contain holes through which metal connecting pins protrude. Inside, the pins are embedded in a compressible core of elastomeric plastic, topped by a weld-on lid that compresses the elastomer radially around the pins. Despite the fact that the elastomeric cores vary in height, sealing of the plastic lid requires a flat fit.
In dynamic weld mode, the density score enables weld-by-weld adjustment that compensates for the varied consistency and height of each plug’s elastomer core. It ensures that the weld actuator travels the required depth and that it “feels” the specified amount of resistance before welding the lid.
Emerson
Cordless Tool Installs Rivet-Nuts
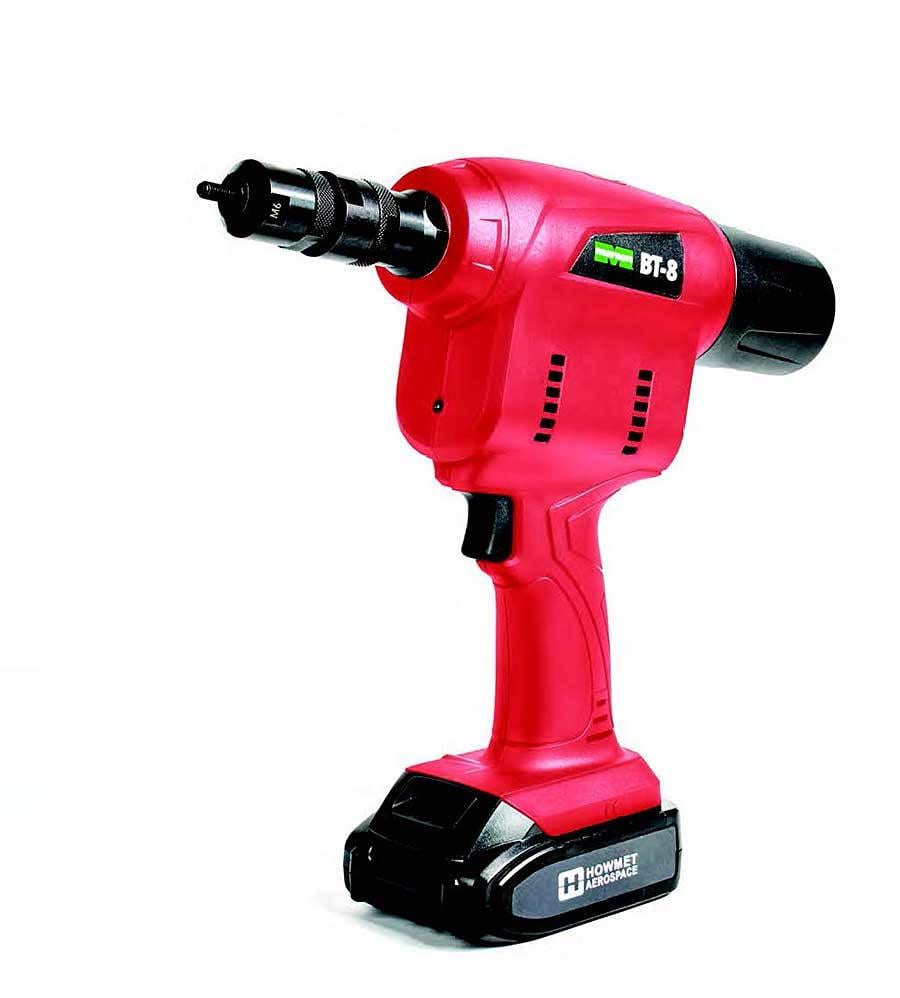
The Marson BT-8 is a battery-powered rivet-nut installation tool designed to deliver reliable pull-force for high-volume assembly applications. This versatile, lightweight tool has good balance, an ergonomic grip, and an LED work light. It can install rivet-nuts ranging from M4 to M12.
Maximum stroke length is 6 millimeters and maximum pulling force is 15,290 newtons. With the lithium-ion battery pack, the tool weighs just 5 pounds. Recharge time is approximately 45 minutes.
Howmet Aerospace