ASSEMBLY LINES
Humanoid Robotic Welders to Tackle Shipyard Automation
HOUSTON—Shipyards depend on an army of skilled welders to build aircraft carriers, container ships, ferries, tankers, submarines and other vessels. However, like all industries, they are facing a severe labor shortage.
HD Korea Shipbuilding & Offshore Engineering (HD KSOE) and HD Hyundai Robotics believe that humanoid robots are the answer. In conjunction with Persona AI and Vazil, they are developing bipedal machines specifically designed for shipyard welding tasks.
The goal is to enhance productivity and improve workplace safety in shipyards. The initiative will deliver prototype humanoids by the end of 2026, with field testing and full commercial deployment scheduled to begin in 2027.
Humanoid robots are being developed for use in shipyards and other manufacturing environments. Photo courtesy Schaeffler Group
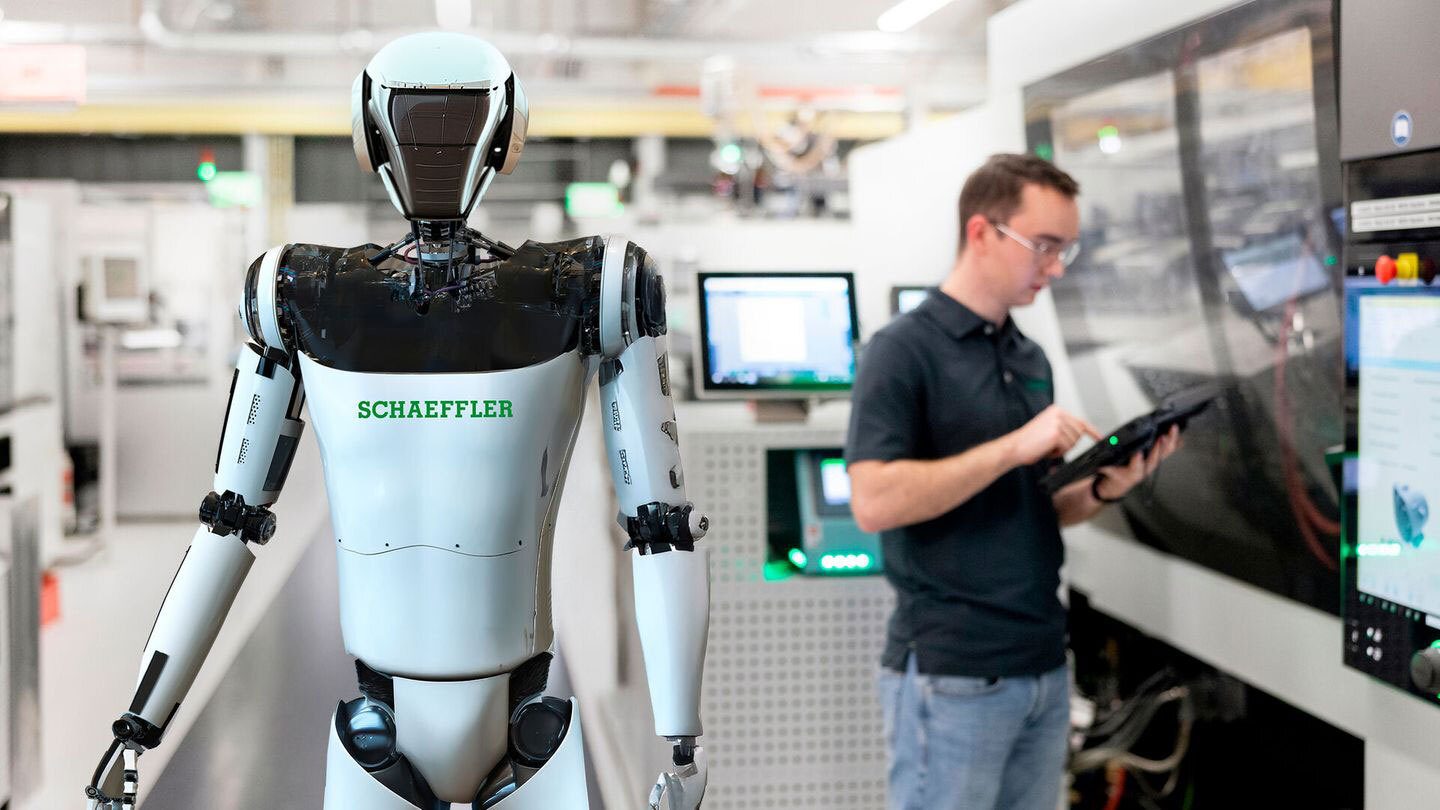
Persona AI will lead the development of humanoid hardware, in addition to AI-based control and learning algorithms. Vazil will develop the welding tools and build the industrial testing environment. HD KSOE will support deployment in live shipyard settings and provide field engineering data. HD Hyundai Robotics will contribute welding-path AI training data and performance validation.
“Welding humanoids will not only boost productivity, but also significantly reduce the burden on workers and greatly enhance safety,” says Dong-ju Lee, senior vice president of HD KSOE. “By developing robots optimized for shipyard tasks, we aim to set a new paradigm in shipbuilding automation. Our goal is a smart shipyard where humans and intelligent robots collaborate seamlessly.”
“As heavy industry faces growing labor constraints—especially in high-risk trades like welding—the need for rugged, autonomous humanoid robots is more urgent than ever,” claims Nicolaus Radford, CEO of Persona AI.
“By developing humanoids capable of precision welding, we will elevate shipyard automation to the next level,” adds Sungwon Kim, chief technology officer at Vazil.
However, despite all the hype and widespread interest in human-machine collaboration, demand for humanoids may not take off as fast as some people think. A recent report by Interact Analysis predicts the market will grow relatively slow, reaching over 40,000 units by 2032 with a revenue of $2 billion.
“The humanoid robot market is currently experiencing substantial hype, fueled by a large addressable market and significant investment activity,” explains Rueben Scriven, research manager at Interact Analysis. “However, despite the potential, our outlook remains cautious due to several key barriers that hinder widespread adoption, including high prices and the gap in the dexterity needed to match human productivity levels.”
According to Scriven, other challenges to widespread adoption of humanoids include regulatory and safety concerns, dexterity limitations, cost and questions over whether humanoid configurations are the optimal form-factor for most AI-enabled robotic tasks and applications.
Although the majority of components used to create humanoid robots have been developed in-house, Scriven predicts there will be a gradual standardization of form-factors as the market matures. “The need for small, lightweight and highly integrated components with very high torque density has necessitated in-house production, but components will slowly shift to being off-the-shelf,” he explains.
Given the relative immaturity of the market at present, Scriven has observed significant diversity in design trends, with small humanoid robots often equipped with planetary drives and wider variation with larger, adult-height robots. There are also regional variations, with many Chinese vendors favoring high-speed motors with harmonic reducers for most joints and more robust, cost efficient high-torque motors with planetary gearboxes for key areas such as hip joints.
At the recent Hannover Messe trade show in Germany, Schaeffler Group displayed a variety of off-the-shelf components that can be used to assemble humanoid robots, such as linear and rotary drives. The Tier One automotive supplier has already developed electric motor and power electronics that can be used to drive humanoid limbs and joints.
For instance, a lightweight and more compact design variant of the XZU bearing has been developed by Schaeffler specifically for the humanoid market. “Thanks to improved friction behavior and high tilting rigidity, these bearings allow the movements of humanoid systems to be controlled more efficiently and precisely,” says David Kehr, president of humanoid robotics at Schaeffler.
“[We are] transferring proven technical solutions to humanoid robots, and in doing so systematically driving their ongoing development,” explains Kehr. “Our goal is to be a strong technology partner to manufacturers of humanoids.”
Virtual Reality Lab Helps Stellantis Engineers Improve Assembly Lines
AUBURN HILLS, MI—Engineers at Stellantis are using virtual reality tools to simulate assembly line workstations before actual production begins. They are using the technology to analyze hundreds of postures to find optimal configurations, tailored for a variety of physical requirements.
The state-of-the-art VR lab allows engineers to optimize plant layouts and refine installation procedures. The goal is to enable operators to assemble vehicles smarter, faster and safer.
The facility is strategically located near the Chrysler Technology Center’s pilot production plant, where early builds of new vehicles are tested and validated. It is equipped with cutting-edge tools such as motion capture, physics-based part simulations and digital twin integration that provide real-time visualization, data accuracy and immersive problem-solving.
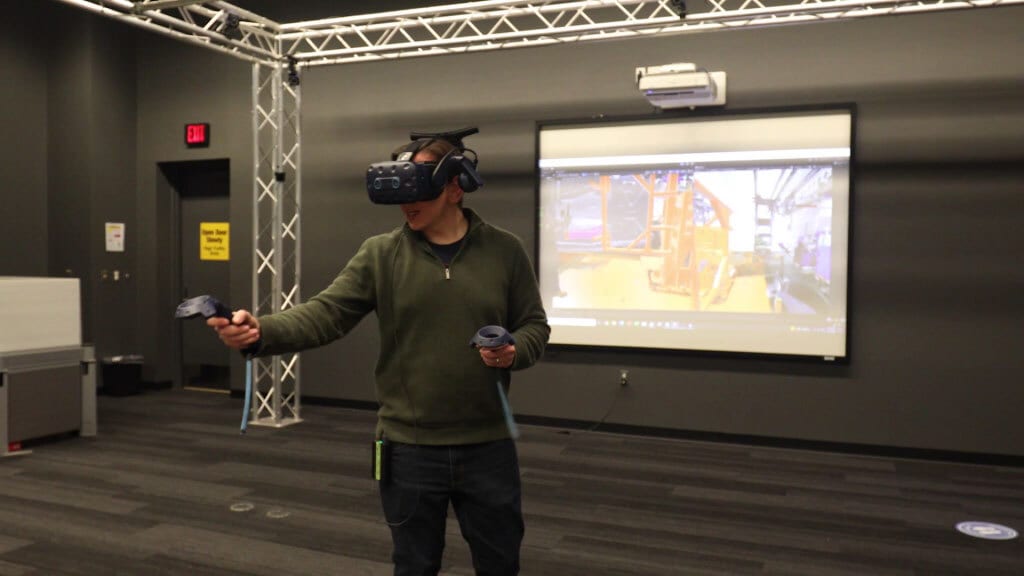
Stellantis engineers are using virtual reality technology to enable operators to assemble vehicles smarter, faster and safer. Photo courtesy Stellantis
“Manufacturing is at the heart of what we do, and advanced technologies like virtual reality allow us to continuously raise the bar,” says Tim Fallon, senior vice president of North America manufacturing at Stellantis. “By identifying issues before production starts, we’re making our facilities safer and better capable of delivering world-class quality to our customers.
“VR is essential for evaluating the postures and movements of hundreds of operators,” explains Fallon. “Deploying this data in a digital environment that mirrors real-life assembly conditions helps ergonomics teams fine-tune platform heights, set ‘golden zones’ for operators’ reach, and refine part-handling techniques for greater safety and efficiency.”
According to Fallon, the VR lab is the centerpiece of Stellantis’ digital engineering efforts, providing a full-scale, immersive platform to “proactively resolve manufacturing challenges and drive operational excellence.”
As a result of deploying VR, Stellantis has identified and resolved hundreds of potential issues on its assembly lines before production begins. For example, the technology was used to help determine the optimal vehicle height for making underbody electrical connections at the Sterling Heights and Warren Truck assembly plants.
By simulating multiple line heights in a virtual environment, engineers ensured that operators would have the proper reach and access to perform these connections safely and efficiently, without ergonomic strain. “Conducting these sessions early in the design process allowed the team to establish accurate conveyor height requirements well before installation, supporting both worker safety and production readiness,” claims Fallon.
“As part of [our] global manufacturing initiative, [we are] scaling VR technology across regions to improve quality, reduce downtime and support [our] long-term vision for smarter, more sustainable production,” says Fallon.
American Auto Factories Boost Investment in Robots
FRANKFURT—Automakers in the United States have invested in more automation to improve productivity and address labor shortages. According to the International Federation of Robotics (IFR), total installations of industrial robots in the auto industry increased by 10.7 percent in 2024, reaching 13,700 units. The machines are primarily used for material handling and machine tending applications in body and paint shops.
“The United States has one of the most automated car industries in the world,” says Takayuki Ito, president of IFR. “The ratio of robots to factory workers ranks fifth, tied with Japan and Germany, and ahead of China.
“This is a great achievement of modernization,” notes Ito, who also serves as chief technical advisor at Fanuc Corp. “However, in other key areas of manufacturing automation, the U.S. lags behind its competitors.”
The U.S. auto industry has invested heavily in robotics technology to improve productivity. Photo courtesy ABB Robotics
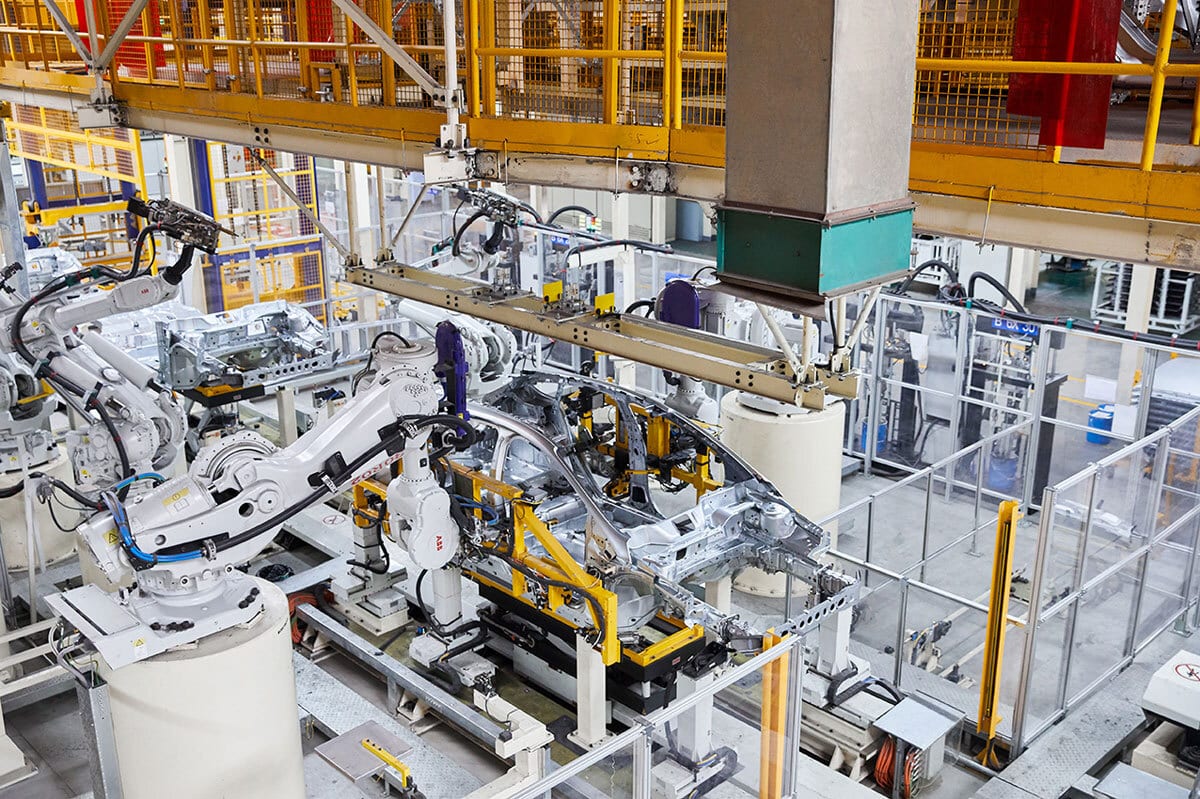
America ranks tenth among the world’s most automated manufacturing countries with a robot density of 295 robots per 10,000 employees. The country’s automation is heavily concentrated in the auto industry. In fact, around 40 percent of all new industrial robot installations in 2024 were in the automotive sector.
This is followed by the metal and machinery industry with 3,800 units representing a market share of 11 percent. Installations in the U.S. electrical and electronics industry has a market share of 9 percent, with 2,900 units.
However, the U.S. lags behind other countries when it comes to robot manufacturing. The majority of machines used domestically are imported from overseas. But, several large companies, such as ABB Robotics and Fanuc America, build some robots in the Detroit area.
Globally, 70 percent of robots are produced by four countries: Japan, China, Germany and South Korea. Within this group, Chinese manufacturers are the most dynamic, with production for their huge domestic market more than tripling over the last five years. That puts China in second place after Japan.
New U.S. Coin Honors the Moving Assembly Line
WASHINGTON—The United States Mint has issued a commemorative $1 coin that honors the moving assembly line. The Michigan American Innovation coin depicts an early 1930s-era factory where a team of auto workers are lowering a body onto a chassis. It’s part of a multi-year series of coins that pay homage to American ingenuity and celebrate the pioneering efforts of individuals or groups from all 50 states.
“The assembly line revolutionized the auto industry and changed the business and manufacturing world," says Kristie McNally, acting director of the Mint. "It also influenced shipbuilding and aircraft production during World War II. We are honored to celebrate this major achievement with this coin.”
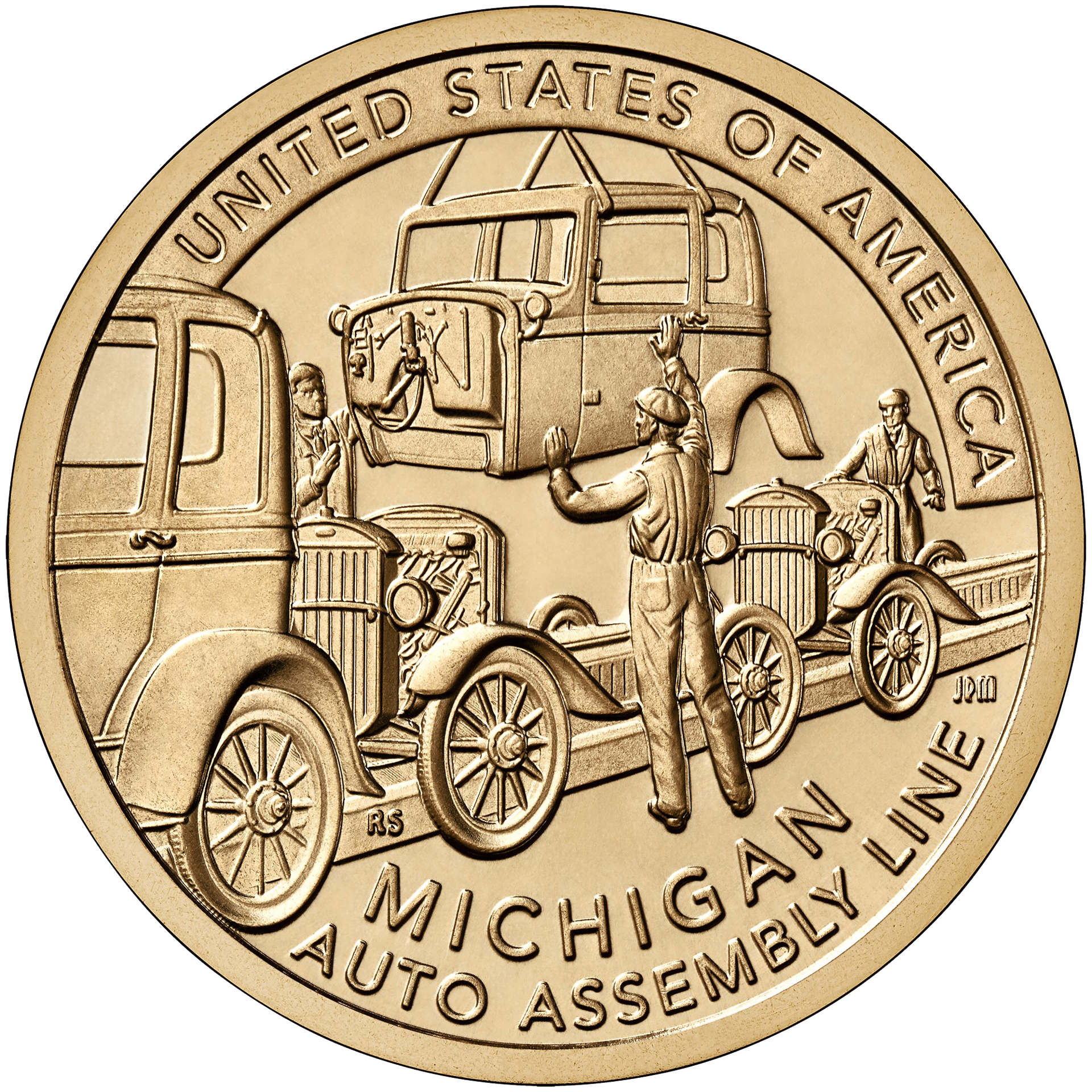
A new commemorative U.S. coin honors the moving assembly line. Photo courtesy United States Mint
“Michigan is the birthplace of innovation and hard workers,” adds Michigan Governor Gretchen Whitmer. “From pioneering the assembly line to being the leader in manufacturing, Michigan has always been a beacon of ingenuity…This coin is a tribute to Michigan’s spirit—a celebration of hard work, creativity and the drive to build something better for generations to come.”
The world’s first moving assembly line was used to produce Model T chassis at Ford Motor Co.’s factory in Highland Park, MI. On Oct. 7, 1913, a group of assemblers stationed along a 150-foot line stood in place as the work came to them, resulting in a dramatic increase in productivity.