Screwdriving and Riveting
Labor shortages are driving new demand for automation.
Options for Screwfeeding
Engineers would be wise contact their fastener suppliers well in advance of production and get them involved early in the design phase. Photo courtesy Bossard
A fantastic design can fail if engineers don’t choose the right fastener and assemble it correctly.
Fastening Failures:
The Top Five Mistakes and How to Avoid Them
Jennifer Pierce // Multimedia Editor
Fastening is a critical element in the design and assembly of any product. When there’s an issue with an assembly, many are quick to blame the fastener, resulting in a situation where engineers are faced with defending the parts and, in certain instances, calling on an expert to solve the issue.
One such expert is Doug Jones, applications engineering manager at fastener manufacturer Bossard North America. We connected with Jones to talk about fastening failures and how to avoid them.
The basic premise of bolting things together has existed for a long time. However, there have been a lot of changes in certain areas, such as platings, coatings and finishes. For example, engineers have developed new finishes to increase corrosion protection or to reduce friction during tightening.
A fantastic design can fail if engineers don’t choose the right fastener and assemble it correctly. Engineers must follow sound principles of joint design, but a lack of knowledge about fasteners can lead to joint failures.
Here are Jones’s top five fastening failures and how to avoid them.
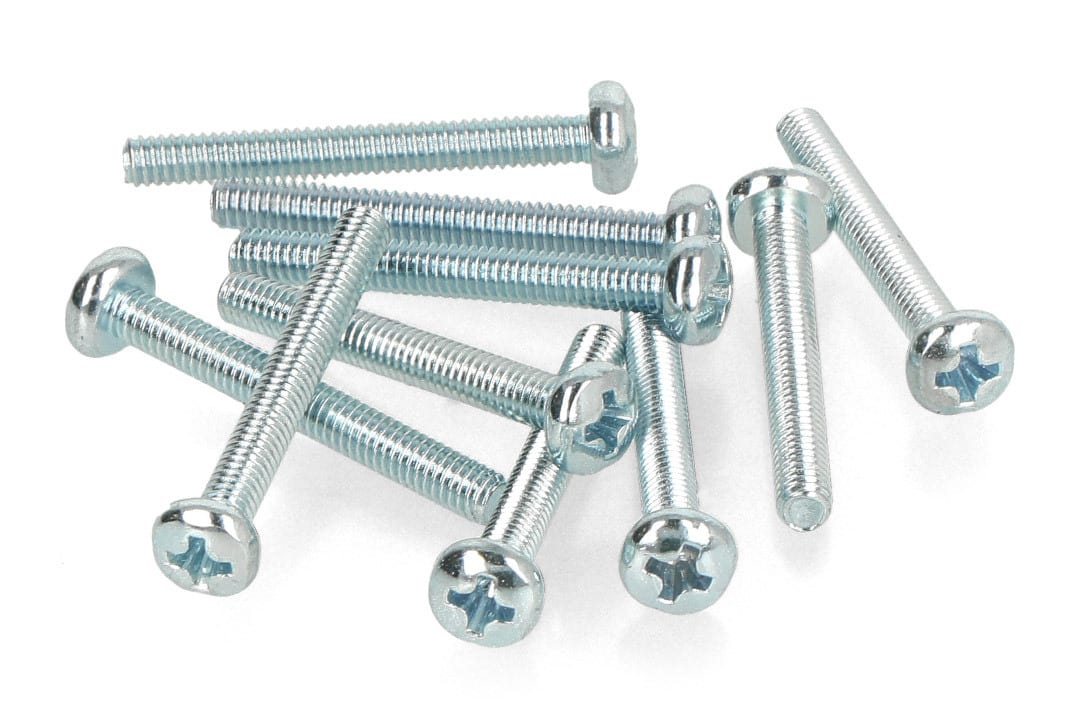
Zinc electroplating is the most common fastener finish. Photo courtesy Bossard
1
Stronger Is Not Always Better
Fasteners need to stretch, especially when assembling critical joints that carry a lot of load. When fasteners break during assembly or in the field, engineers often mistakenly think that they need to make the fastener stronger. They don’t understand the reason for the failure.
Fasteners must be able to stretch, like a rubber band or a spring, since that helps them to maintain clamp load on the joint. When a fastener fails, it’s important to understand why it’s failing and address the problem, rather than just automatically incorporating something stronger. A stronger bolt can actually make the situation worse, because it won’t stretch as much and it can fail more quickly.
2
Not Understanding Zinc Electroplating
Zinc electroplating is the most common fastener finish. The bright silver-colored bolts and nuts are easily identifiable in any hardware store. Many engineers specify zinc-plated fasteners without understanding that there are different levels to the finish.
What is the life expectancy of the part? How much corrosion resistance is needed? Determining those factors will help meet the plating requirements that will give you a longer corrosion life.
It’s important to consider the environment where the part will be used. Will the fasteners be exposed to the elements? Outdoors, conventional zinc plating has low corrosion resistance.
It’s impossible to tell by looking at a fastener what level of corrosion protection it has. The amount of protection has to do with the thickness of the zinc, the thickness of the chromate coating on top of the zinc, and any kind of sealers that might have been applied. Manufacturers often do not to specify anything about the plating on the fastener, outside of indicating “commercial zinc.” That can lead to disappointment when the fastener fails quickly due to corrosion.
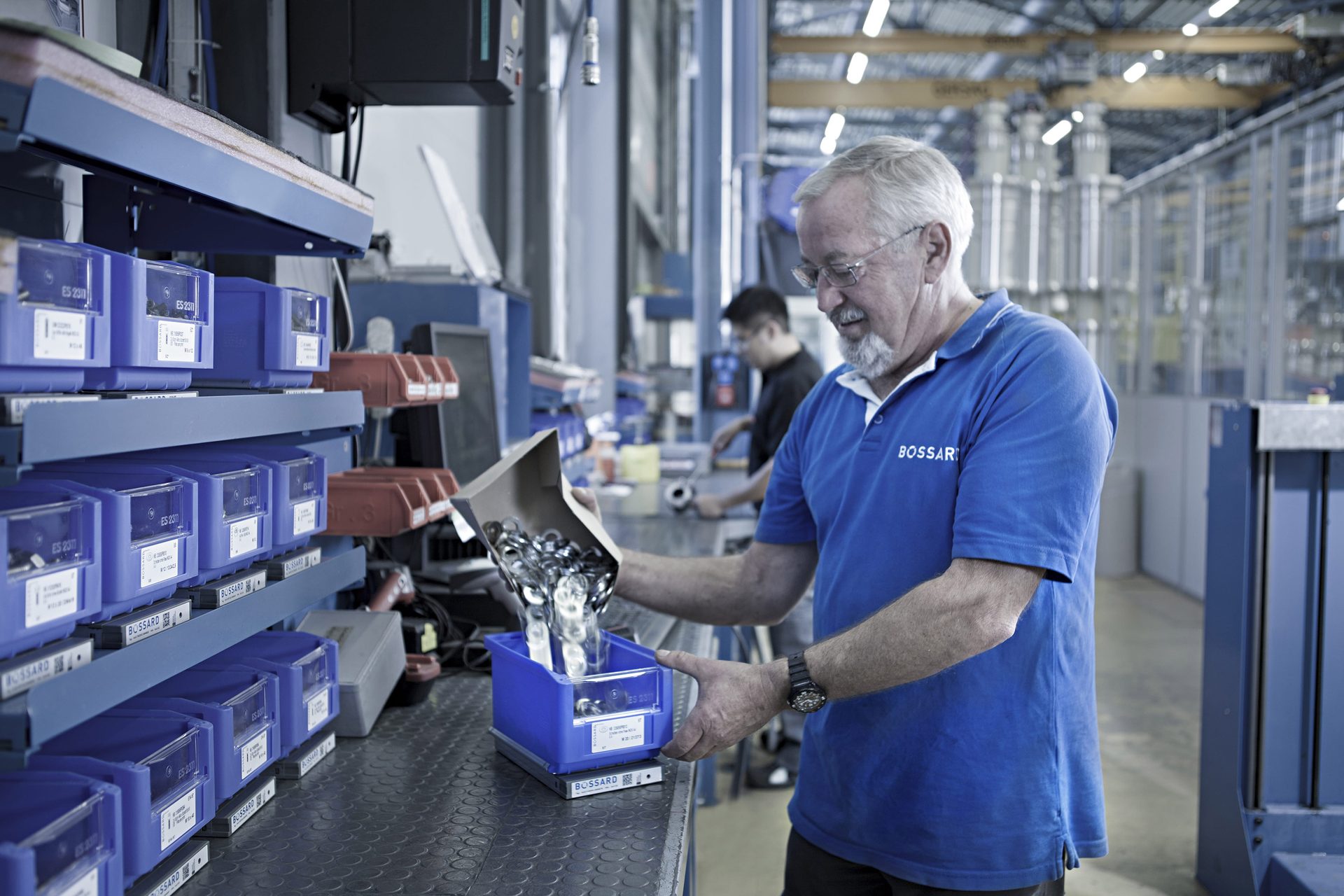
When designing a new product, engineers rarely think about the fasteners. Photo courtesy Bossard
3
Hardware Coming Loose
It’s common to see hardware coming loose when engineers use split lock washers in their designs. Although split lock washers have been around a long time and are commonly used, they really do not provide any locking effect. It’s a common misconception to think that adding a lock washer to a joint will prevent it from loosening.
In fact, washers often create more problems than they solve. Many times, omitting the washer will make for a better joint.
4
Nonstandard Fasteners Increase Costs Significantly
Everyone wants to reduce costs. Fasteners are genuinely the cheapest component of an assembly. However, if the design calls for a lot of fasteners, costs can really add up in a high-volume operation.
Engineers should specify standard fasteners in their designs whenever possible. Don’t specify special heads, points or thread lengths if you don’t have to. Products become much more expensive if they require a fastener that you can’t get off the shelf.
Engineers are well-advised to become familiar with the advantages and limitations of the standard fasteners available today. It will save you a lot of money.
5
Waiting Until the Last Minute to Select Fasteners
When designing a new product, engineers rarely think about the fasteners. All too often, engineers consider the fastener six or even three weeks in advance of production. Only then do they realize that they may be unable to get the specific fasteners they want, especially if they’re not standard. Lead times may be longer than originally anticipated.
Engineers would be wise contact their fastener suppliers well in advance and get them involved early in the design phase. Engineers should choose fastener suppliers with whom they have a good relationship. Work with them on the design and selection of the fasteners.
Partner with them to help design your products. Working with fastener experts early in the design phase will avoid problems down the road.
For more information on fasteners, visit www.bossard.com.