Assembly Presses
Labor shortages are driving new demand for automation.
Options for Screwfeeding
A combined broach and flare process during installation of the bushing ensures consistent mechanical and electrical connections. Photo courtesy PennEngineering
Self-clinching fasteners solve problem of metal oxide layers on copper and aluminum parts.
Contact Bushing Assembles
Aluminum Bus Bars for EVs
John Sprovieri // Chief Editor
Copper has been the industry standard for bus bars in electric vehicles (EVs) due to its superior conductivity and reliability. However, the rising costs and heavier weight of copper make it less attractive as automakers focus on reducing vehicle weight and improving cost efficiency.
Aluminum is emerging as a compelling alternative. Although it has only about half the conductivity of copper, doubling the thickness of aluminum bus bars allows them to perform comparably to copper ones, while still achieving significant weight savings. For instance, even at twice the thickness, aluminum weighs only about half as much as copper and comes at a fraction of the cost.
Moreover, aluminum is widely available and highly recyclable, making it a more sustainable choice as the EV market grows. Besides bus bars, the metal can be used for power distribution units and inverters.
However, using aluminum for bus bars isn’t without its challenges. One of the main issues with aluminum bus bars is the formation of an oxide layer on the surface. This oxide layer is highly resistant to electricity, making it difficult to achieve the same level of conductivity as copper.
To address this challenge, PennEngineering has introduced the ECCB eConnect contact bushing.
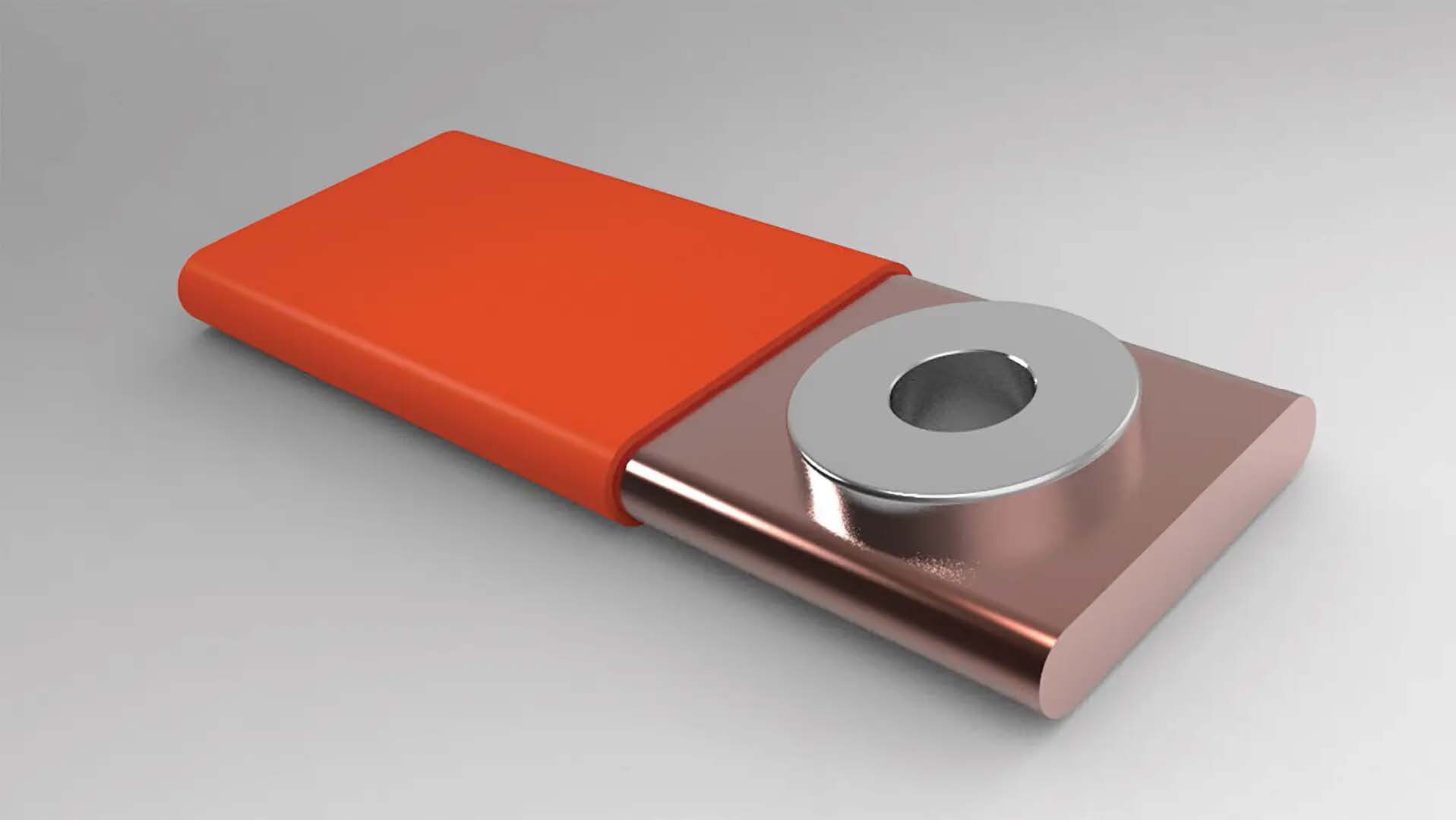
To connect a bus bar to other components, the bushing is intended to work with other fasteners in the eConnect family of products—either a self-clinching nut or a self-clinching stud. Photo courtesy PennEngineering
Defeating the Aluminum Oxide Layer
The aluminum oxide layer that naturally forms on aluminum surfaces acts as an insulator, reducing the efficiency of electrical connections. Over time, this layer can even thicken, further impeding conductivity and compromising the reliability of electrical connections in bus bars. For a component as crucial as a bus bar, maintaining high conductivity is essential for efficient power transfer, especially as EVs rely heavily on optimized energy distribution to extend range and performance
PennEngineering developed the ECCB eConnect contact bushing specifically to address the conductivity issues associated with aluminum oxide. The bushing is designed to deliver ultra-low electrical resistance connections in aluminum bus bars, effectively overcoming the challenges of the oxide layer. Serrations under the head of the bushing break through the oxide layer with any need for surface preparation.
Designed for easy installation, the bushing creates a secure, durable joint that resists loosening or performance degradation over time. This reliability is essential for EVs, where high vibrations and temperature fluctuations can otherwise compromise weaker connections.
The bushing’s unique design disrupts the aluminum oxide layer, allowing for a direct, high-quality metal-to-metal connection. This ensures low electrical resistance.
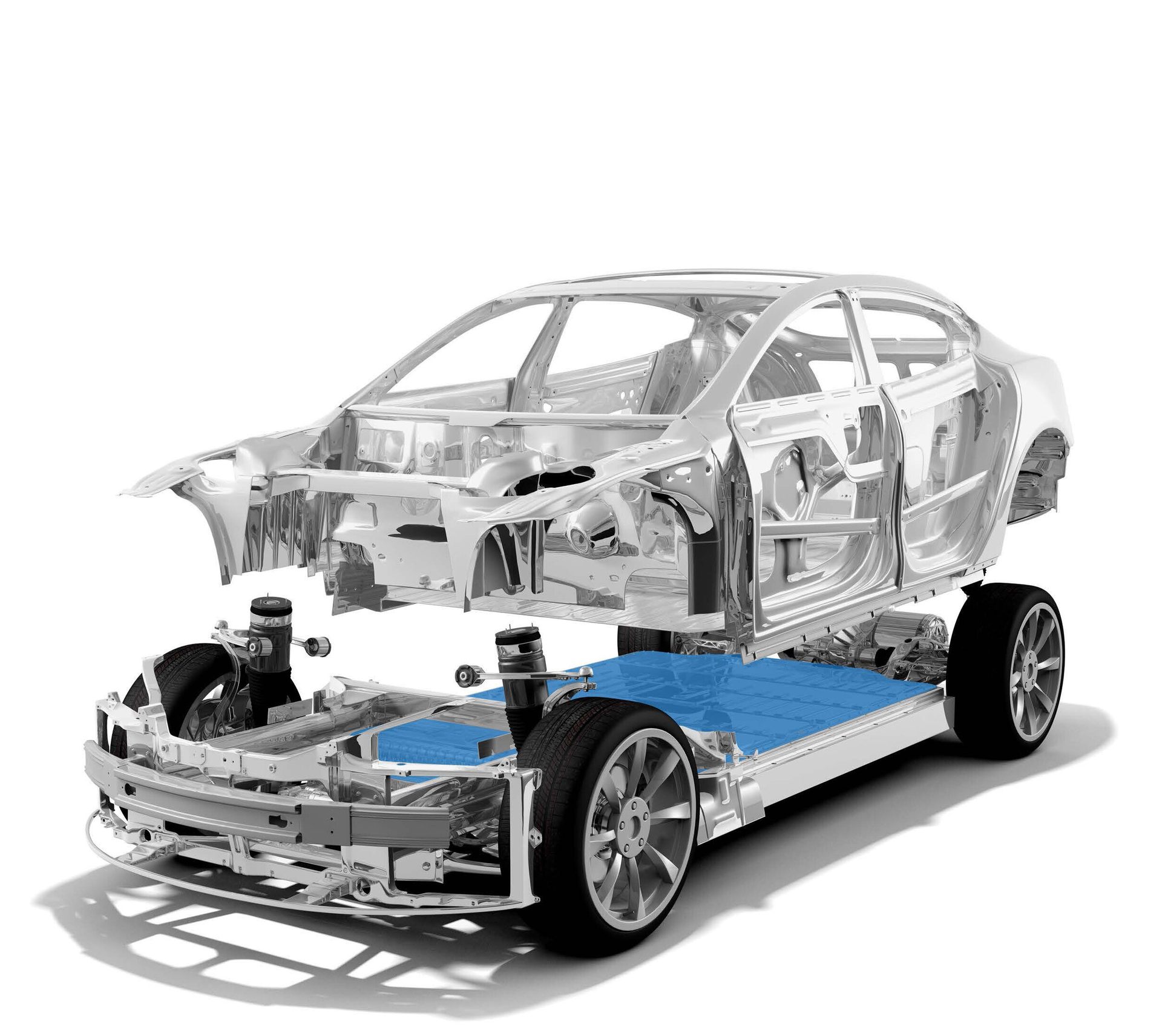
Aluminum is emerging as a compelling alternative for conducting electricity in EVs. Photo courtesy PennEngineering
The bushing is made from high-conductivity copper alloy, which helps reduce resistance and improve overall conductivity. This allows EV manufacturers to leverage the cost and weight benefits of aluminum while achieving copper-like performance.
By incorporating conductive coatings, such as silver, the bushing minimizes resistance at the connection point. Silver is an excellent conductor, enhancing the efficiency of electrical transfer through the bushing, even in challenging environments where the oxide layer might otherwise inhibit current flow.
To connect the bus bar to other components, the bushing is intended to work with other fasteners in the eConnect family of products—either a self-clinching nut or a self-clinching stud.
Self-clinching fasteners are installed not with a power tool, but a press. The fasteners are pressed into thin, soft or otherwise fragile materials to provide strong threads for mating hardware.
Self-clinching fasteners are installed not with a power tool, but a press. The fasteners are pressed into thin, soft or otherwise fragile materials to provide strong threads for mating hardware.
Self-clinching fasteners are installed with a press during fabrication or final assembly. Installation is a two-step process. First, the fastener shank is placed in a mounting hole in one or more thin metal sheets. Then, as the fastener is pressed into place, displaced sheet material cold-flows into the shank recess and locks the fastener in place. When installation is complete, the fastener is flush with the sheet or touching the top of it.
In the case of the bushing, a combined broach and flare process during installation ensures consistent mechanical and electrical connections. The bushing can be installed in metal sheets with a hardness of HRB 50 or less.
ASSEMBLY ONLINE
For more information on self-clinching fasteners, visit www.assemblymag.com to read these articles: