Plastic and Metal Welding
For large areas, maintaining planarity throughout the entire welding cycle is critical. Photo courtesy TECNA USA Inc.
New Technology Improves
Welding
Diffusion
Advancements allow the process to create larger, higher quality welds in less time.
Filippo Cortiglioni // Area Sales Manager // TECNA USA Inc. // Rahway, NJ
Diffusion welding, also known as diffusion bonding or solid-state welding, has long been used in various industries. The process joins layers of material by applying force and heat in specific amounts for a defined period.
Traditionally, diffusion welding relied on autoclaves with lengthy cycles that can stretch over several hours. However, advances in resistance welding technology now offer the potential to perform diffusion welding in a fraction of the time, often within minutes or even seconds, depending on material and part size, making this process suitable for mass production and opening new opportunities for assembly.
In diffusion bonding, axial force is applied to the parts as they are heated to 50 to 75 percent of their melting temperatures. Over time, atoms in each part intersperse, creating a solid-state bond. There is no relative motion between the parts.
This technique relies on atomic diffusion between the pressed surfaces, forming a robust, long-lasting connection over wide areas. The energy applied to the mating surfaces makes the atoms “jump” across the gap. Over time, this forms a solid junction between the surfaces, turning a multilayered pile into a solid block of material.
Unlike traditional welding, diffusion bonding does not melt the materials or require filler metals, making it ideal for complex applications that demand precision and structural integrity. For example, the flexible shunt for a spot-welding system consists of many thin layers of laminated copper. This assembly can get very hot while transmitting electric current. A shunt assembled with diffusion welding will typically operate 30 degrees cooler than shunts assembled with other methods. This means improved performance and electrical efficiency, as well as better safety for the operators.
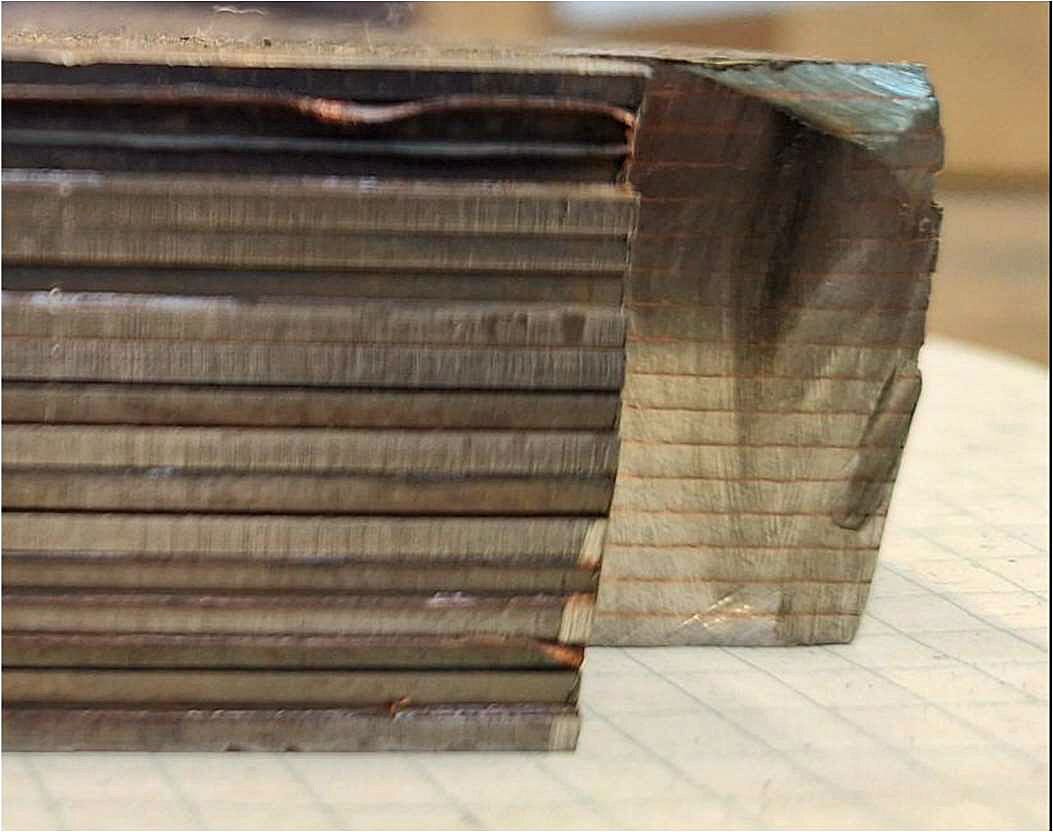
The photo (left) and micrograph (right) show multiple layers of stainless steel and copper welded into a single solid block of material. Photo courtesy TECNA USA Inc.
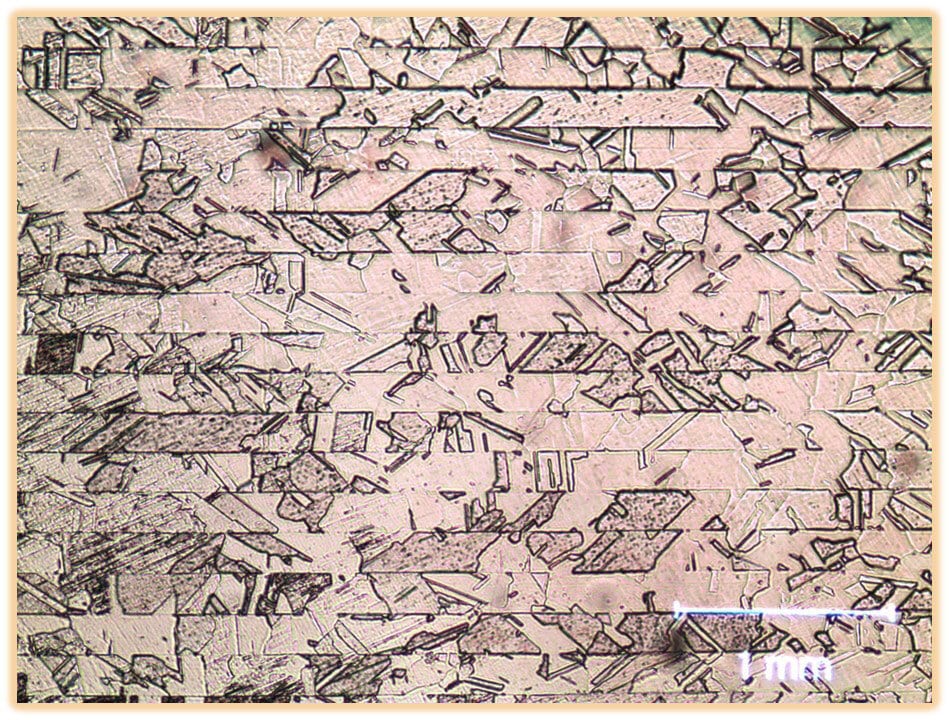
Parameters and Challenges
While highly effective, diffusion bonding has traditionally been limited by challenges related to ensuring uniform pressure across large or irregular surfaces. This limitation has restricted its use to smaller components, where uniform bonding can be more easily achieved.
Modern resistance welding systems, such as C-frame press welders or larger portal frame models, have introduced a new level of efficiency and precision to the process.
The key parameters—heat, force and time—remain at the core of any diffusion welding process. The primary differentiator in diffusion welding systems lies in how these parameters are controlled and combined to produce consistent, high-quality results, especially as the welding area increases in size.
Another critical factor is ensuring perfect planarity across the welding surface, a challenge that becomes exponentially difficult as part size increases. Perfect planarity is essential to guarantee uniform heat distribution, which is vital for achieving consistent diffusion welds.
Let’s explore each of these parameters in detail.
Temperature. In resistance-based diffusion welding, the power source, typically a welding transformer, delivers current to generate heat through the Joule effect. This heat is critical to achieving the correct temperature for diffusion bonding, which must remain below the melting point, but high enough to activate solid-state welding. Accurately controlling this temperature is essential, because deviations can either fail to activate the diffusion process or cause material deformation.
Advanced systems incorporate precise temperature control mechanisms, such as pyrometers (laser thermometers), to monitor heat distribution across the parts. For example, TECNA integrates full pyrometer management directly into its welding controls, eliminating the need for external PLCs. Once the desired temperature is reached, the system automatically modulates the current output to maintain the temperature. This approach shifts the traditional focus of resistance welding from current control to temperature control, revolutionizing how the process is managed. The integration in the weld control minimizes the need for manual adjustments, making diffusion welding more accessible to non-experts.
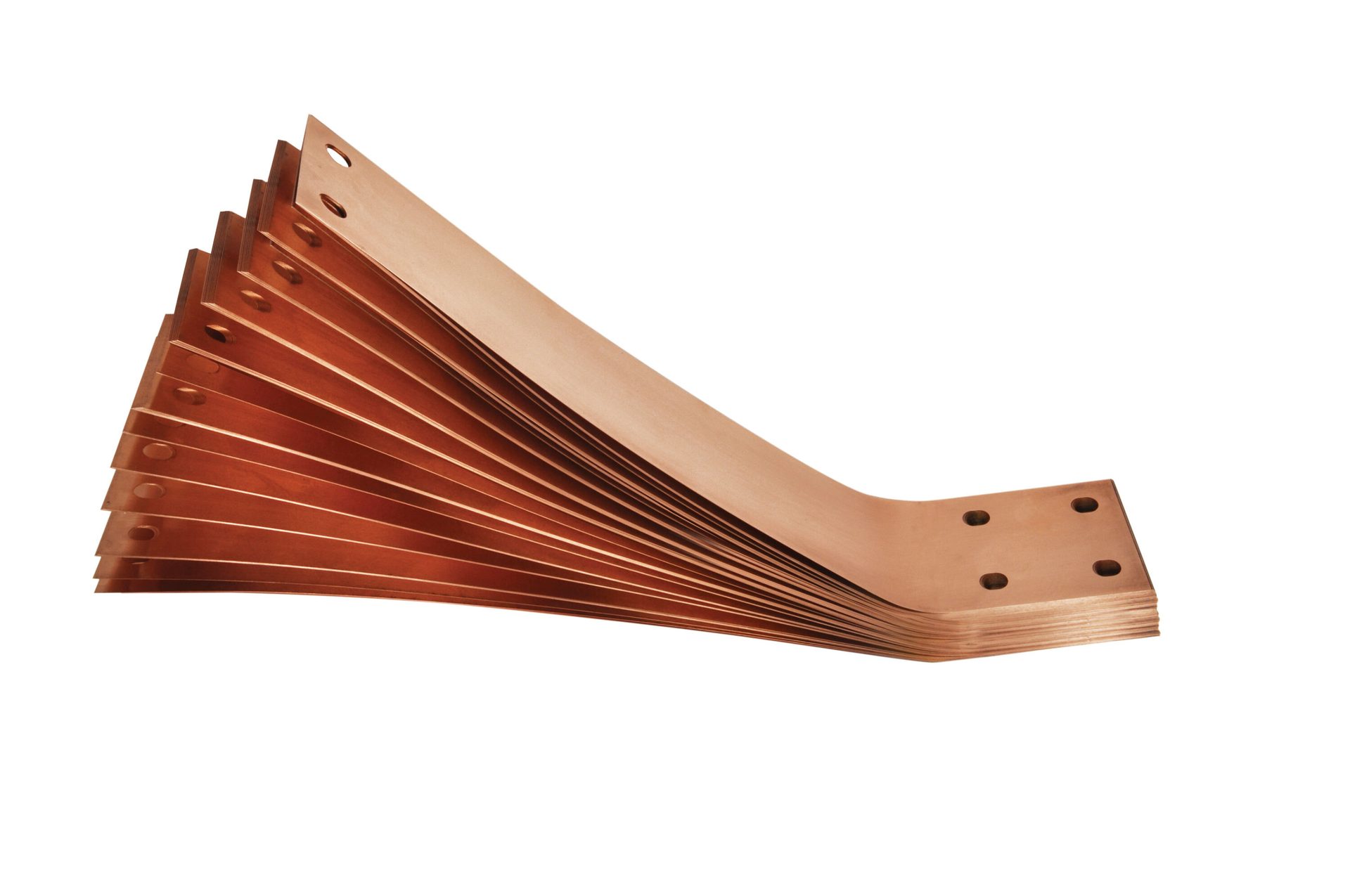
A flexible shunt for a spot-welding system is an ideal application for diffusion welding. Photo courtesy TECNA USA Inc.
Force. While force might seem simpler to manage, it is equally important. For diffusion welding to succeed, the applied force must be uniform and sustained throughout the welding cycle. The amount of force required depends on the area, material thickness, and the number of layers to be welded. For instance, a 2-inch by 2-inch area with 10 layers of 0.04-inch laminations might require up to 6,000 pounds of force.
Advanced welding systems, like TECNA’s large-area portal frame welder, combine hydraulic circuits with servomotors to apply force precisely. These systems can deliver the necessary force—over 80,000 pounds for a 20- by 15-inch welding area—while maintaining rapid positioning and movement.
However, planarity management is crucial when dealing with such large areas, especially to prevent uneven force application, which could lead to partial bonding or defects and rejects.
Time. This is the most straightforward of the three parameters, provided that both temperature and force are stable and well-controlled. Once the target temperature is achieved, a timer will govern the welding cycle according to a predefined recipe.
Optimizing this parameter requires a careful balance. Excessive time can lead to material degradation, while insufficient time can produce weak bonds.
Inspection System
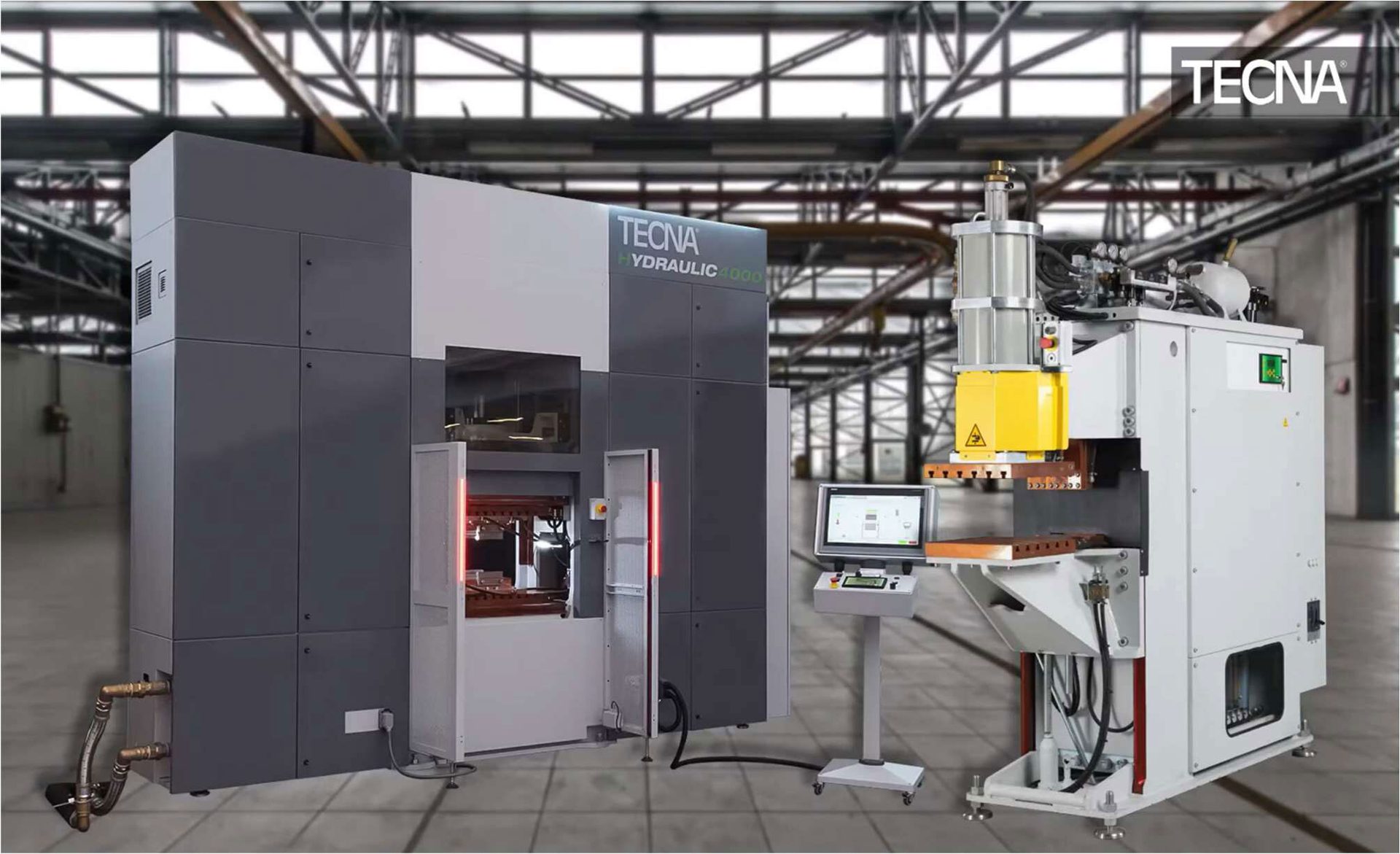
TECNA’s hydrostatic cushion system employs hydraulic compensation cushions to dynamically adjust for pressure imbalances caused by heat expansion during welding. Photo courtesy TECNA USA Inc.
Real-time temperature and force control enables engineers to fine-tune the welding cycle and achieve atomic diffusion in less time. Simulation tools can help engineers create and refine these recipes, ensuring that each weld is performed efficiently and with high repeatability.
Planarity. The final, and arguably most challenging, parameter in diffusion welding is planarity. Achieving perfect planarity across the welding surface ensures uniform heat and force distribution. This becomes increasingly difficult as the size of the part and the welding area grows. Even with finely machined surfaces and precise movement, factors such as material irregularities and thermal expansion can introduce distortions that affect the quality of the weld.
For large areas, maintaining planarity throughout the entire welding cycle is critical. Traditional systems often struggle with this, limiting the use of diffusion welding for large-scale applications.
However, innovations such as TECNA’s patented hydrostatic cushion system have overcome this barrier. This system, derived from press technology, employs hydraulic compensation cushions (hydrostatic planes) to dynamically adjust for pressure imbalances caused by heat expansion during welding.
This adaptive system ensures that the welding area remains flat within a tolerance of 0.02 millimeter, even over extended surfaces. The cushions balance local pressure variations, preventing deformations and ensuring consistent force and temperature distribution. This innovation enables large-area diffusion welding to be performed quickly and accurately, making it possible to weld laminated copper packs up to 20 inches wide in less than 30 seconds. This system is particularly valuable for manufacturing components like bus bars, shunts and heat exchangers.
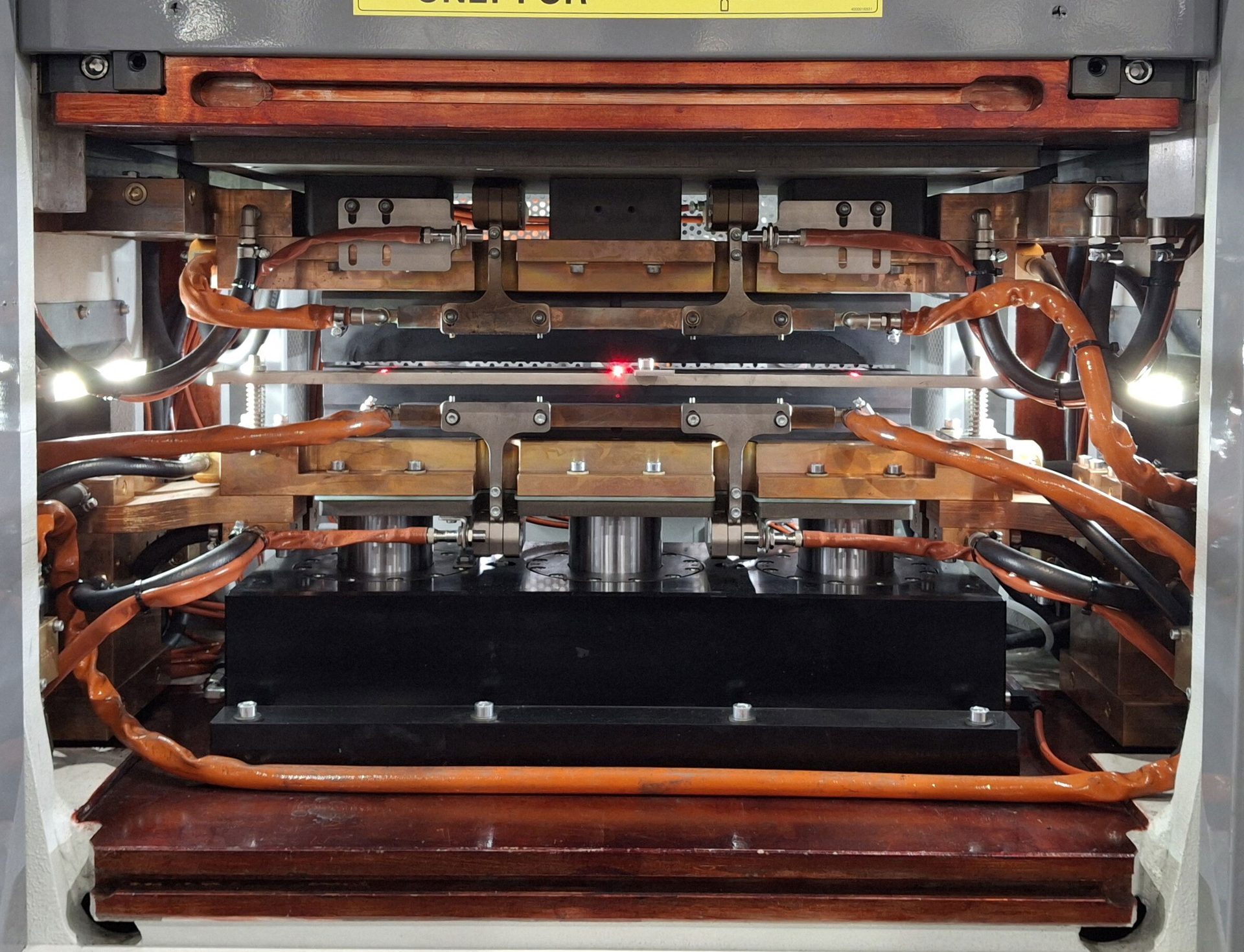
Real-time temperature and force control enables engineers to fine-tune the welding cycle and achieve atomic diffusion in less time. Photo courtesy TECNA USA Inc.
Conclusion
Modern resistance welding technology has transformed diffusion welding, making it faster, more efficient and more accessible. The ability to perform large-area diffusion welding in just seconds opens up vast opportunities for industries that rely on complex, layered materials. The introduction of controlled atmospheres or vacuum chambers could further extend the capabilities of this technology, allowing even more sophisticated material combinations.
TECNA’s advancements, particularly the hydrostatic cushion system and temperature-controlled welding cycle, have addressed some of the most significant challenges in diffusion welding. By ensuring consistent planarity and precise temperature management, these systems provide a robust, repeatable method for welding large areas without manual intervention or complex adjustments. With these innovations, the barriers to large-scale diffusion welding have been broken, opening new doors for industrial applications.
ASSEMBLY ONLINE
For more information on metal welding, visit www.assemblymag.com to read these articles: