Robotics
Labor shortages are driving new demand for automation.
Options for Screwfeeding
Panorama automated the process of installing screws onto a cover panel of a network antenna. Photo courtesy Vikaso
Automating the screwdriving process increases throughput, improves quality, reduces the risk of repetitive stress injuries.
Cobot
Automates Screwdriving
at Electronics Company
John Sprovieri // Chief Editor
Panorama Antennas has been manufacturing antennas for more than 75 years. The London-based, family-run business got its start making antennas for radio and television, but has since expanded into technology for first-responders, telecommunications and enterprise applications.
These antennas are not merely metal poles with attached wires. They are sophisticated electronic assemblies—and they can require a lot of screws. Installing all those fasteners is a monotonous task. Automating the process with a robot would increase throughput, improve quality, reduce the risk of repetitive stress injuries, and free up skilled labor to perform other tasks.
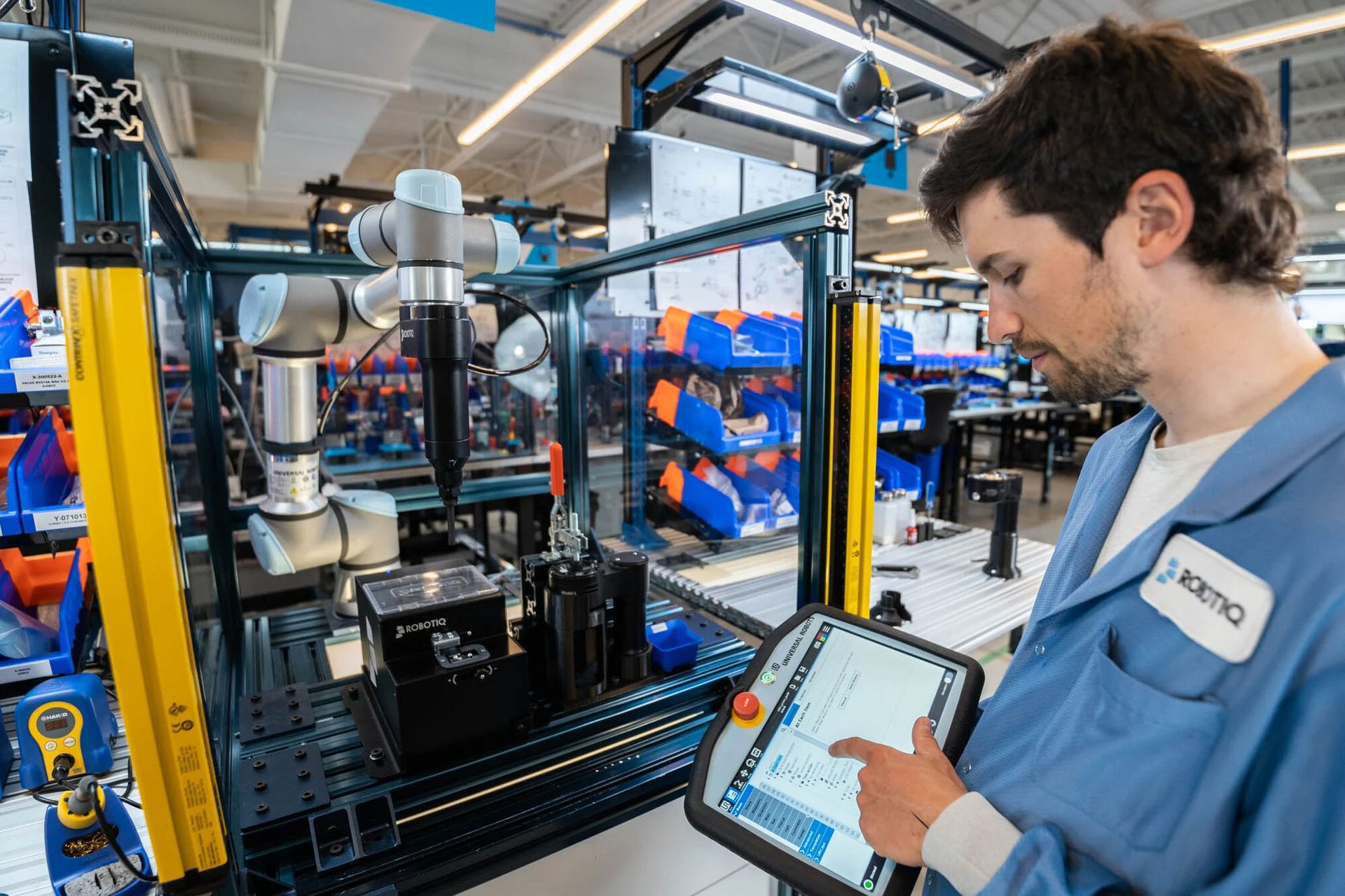
Engineers can program the screwdriver directly with the cobot’s teach pendant. Photo courtesy Robotiq
“The primary reason for integrating a robotic arm into the assembly process was to increase quality through a uniform, repetitive assembly process, whilst at the same time enabling the company to redeploy the assembly operators to higher skilled tasks, such as soldering, connector assembly or RF testing,” explains Mark Jesman, operations and supply director at Panorama Antennas.
Panorama’s first goal was to automate the process of installing screws onto a cover panel of a network antenna. To do that, the company got help from local robotics and automation distributor Raruk Automation in Shefford, England, and systems integrator Vikaso in Quainton, England.
For this application, Panorama chose the UR5e cobot arm from Universal Robots, combined with the Screwdriving Solution from Robotiq. Vikaso also provided its V-CAP URCap software plug-in and V-Eye remote access and monitoring solution, which includes a camera module.
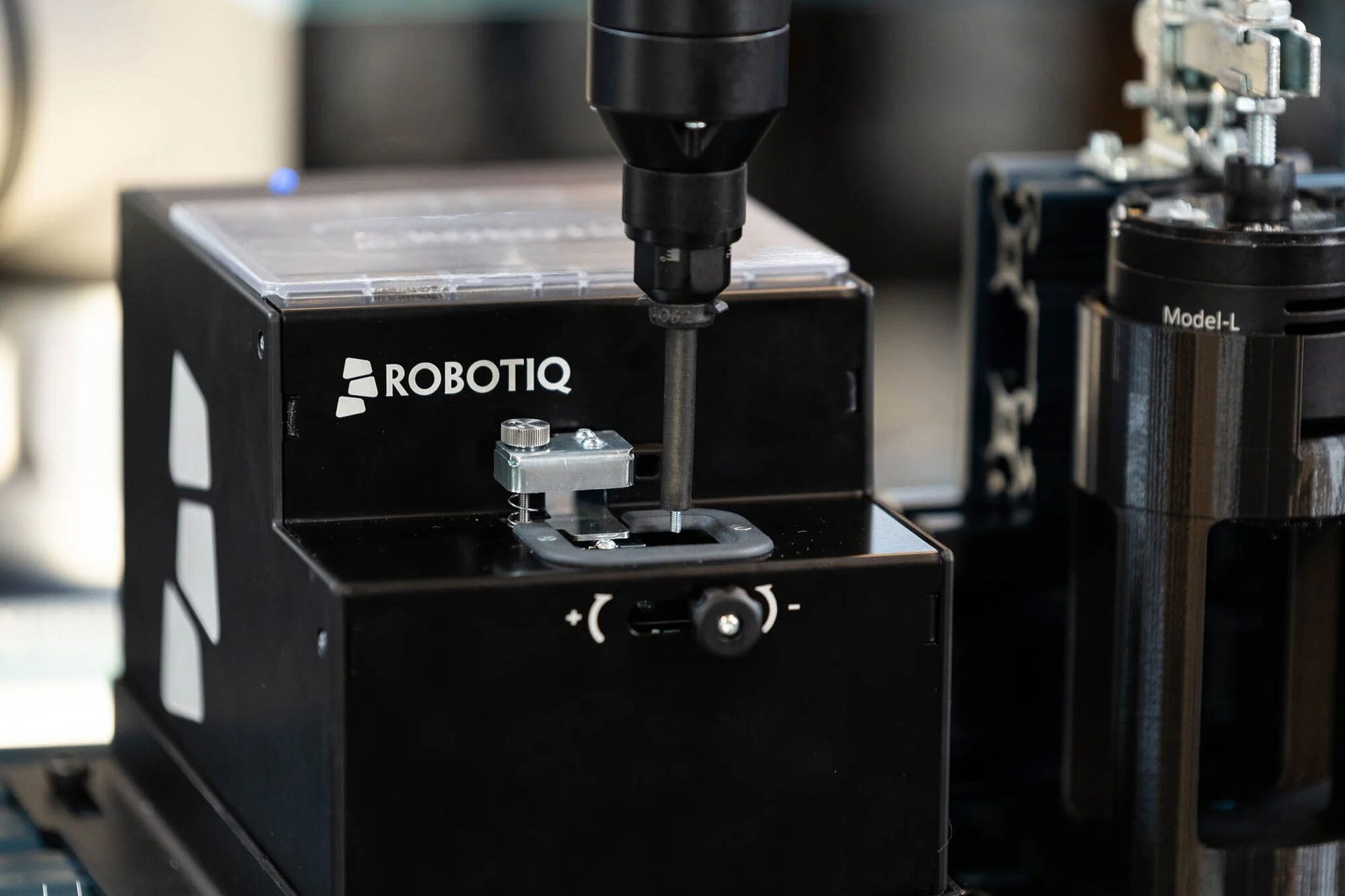
The cobot retrieves a fastener from a screw presenter. A vacuum bit ensure the screw stays put as the robot travels to a fastening location. Photo courtesy Robotiq
The UR5e is the second smallest model in Universal Robots’ portfolio of six-axis cobots. With a payload capacity of 5 kilograms and a maximum reach of 850 millimeters, the UR5e is ideal for low-weight collaborative processes, such as pick-and-place or screwdriving. The robot’s small footprint makes it easy to integrate into existing production setups.
Robotiq offers kits for a range of robotic applications including sanding, palletizing, machine tending and screwdriving. Robotiq’s Screwdriving Solution is a UR+ certified automatic screwdriving system for cobots. The system includes an SD-100 screwdriver, an SF-300 screw feeder, vacuum sleeves, driver bits, Force Copilot software, and screwdriving application software. Changeover from one application to another can be accomplished in 5 minutes. Engineers can program the screwdriver directly with the cobot’s teach pendant. The system provides precision fastening to torques of 1 to 4 newton-meters. It also has error-proofing features for uninterrupted screwdriving, such as screw presence detection, torque control and position monitoring.
“We used the Robotiq Screwdriving Solution for our project. The equipment is very easy to use, and our integration process was quite straightforward,” says Vaibhav Boricha, director of Vikaso.
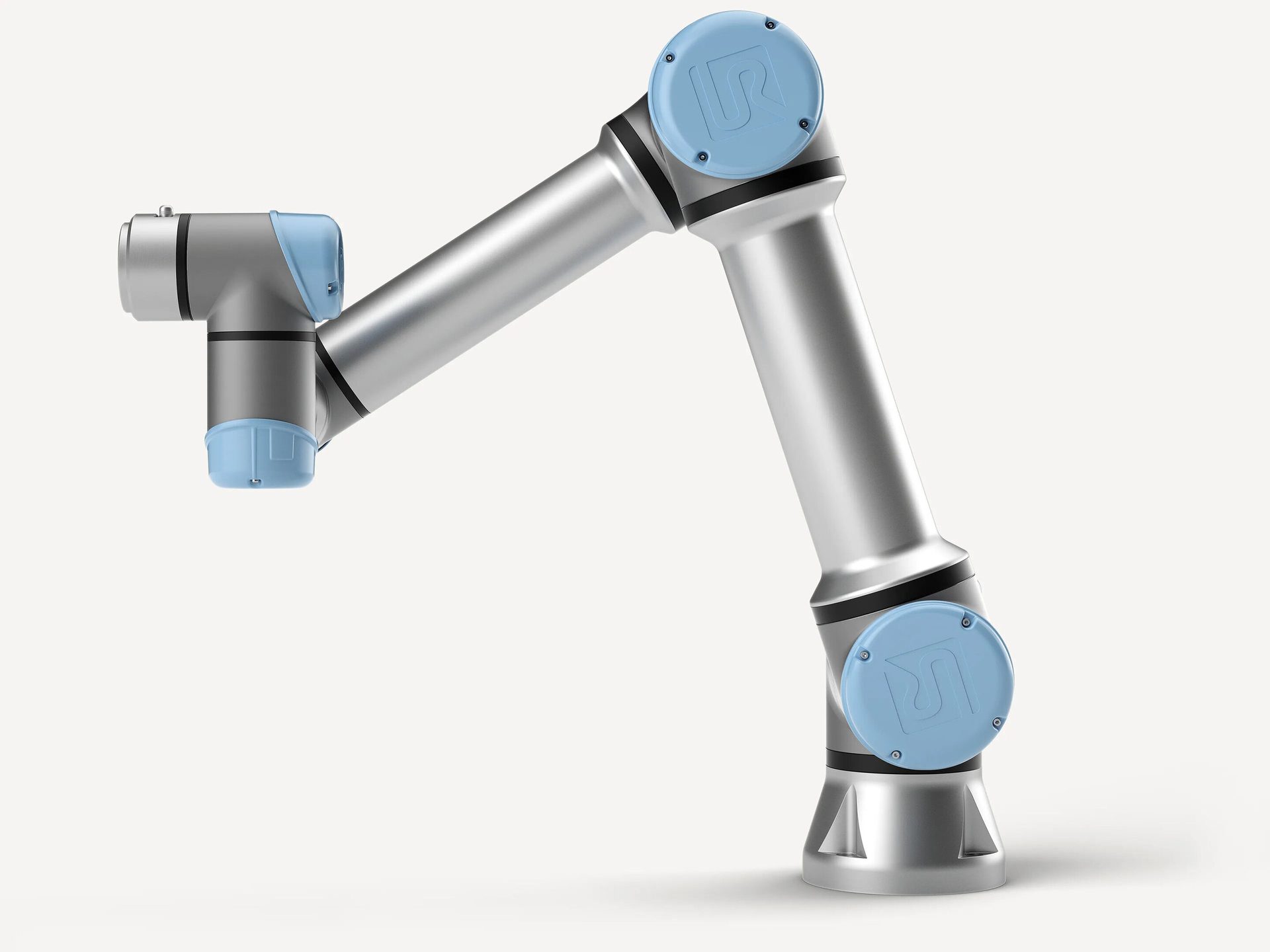
With a payload capacity of 5 kilograms and a maximum reach of 850 millimeters, the UR5e is ideal for low-weight collaborative processes, such as pick-and-place or screwdriving. Photo courtesy Universal Robots
The Automation Process
As Universal Robots’ top global distributor, Raruk Automation provides robots in three ways: just the robot; a complete out-of-the-box system; or by referring the customer to an integrator for additional support. Vikaso is a Universal Robots certified systems integrator and frequent integration partner of Raruk Automation. Panorama Antennas and Vikaso met in the middle for this application.
“Vikaso has taken a very different approach with this project,” explains Boricha. “Our core business is providing turnkey solutions. However, this collaboration with Panorama Antennas only required us to develop the application, while they did the programming and testing.”
“Vikaso has a supportive team that were able to help us build the solution we required and carry out the training, so that we were able to program and operate the equipment with minimum support,” adds Jesman.
The result has been positive for Panorama. The efficient, reliable system ensures consistent product quality. Despite initial hesitation, Panorama’s staff have embraced the change.
“Initially the assembly operators were anxious and apprehensive, because they felt the robotic arm was going to take away their jobs. But, after training and understanding the vision for this equipment, they have embraced it as an asset to their process,” says Jesman.
Automating the screwdriving process has enabled Panorama’s skilled workers to focus on more complex, rewarding assembly tasks. After the successful deployment of the screwdriving cell, Panorama Antennas is looking to implement more robotic automation.
“We are looking to replicate this process at our subsidiary sites, and we also have various other processes that we are looking to automate,” says Jesman.