Test and Inspection
Labor shortages are driving new demand for automation.
Options for Screwfeeding
ZF Lifetec tests its products under the toughest conditions to ensure the highest possible quality and reliability. Photo courtesy ZF Lifetec
ZF Lifetec employs both physical and virtual testing to ensure reliability and performance of seat belts, air bags and steering wheels.
Product Testing Goes Digital
Knut Zimmer // Press Officer. // ZF Lifetec. // Aschau am Inn, Germany
In 1968, the federal government required all vehicles, except buses, to be fitted with seat belts. Using them, however, was strictly voluntary, and many Americans didn’t want to. In fact, as late as 1983, less than 15 percent of Americans said they used seat belts consistently.
Then, in 1984, New York became the first state to pass a mandatory seat-belt law. Other states soon followed. Despite clear evidence that seat belts saved lives, these measures faced stiff opposition. Some people cut the belts out of their cars. Others challenged seat-belt laws in court.
Today, that sort of mindset is mostly in the rearview mirror. Some 92 percent of Americans now say they wear seatbelts regularly. And why not? Since 1975, seat belts are estimated to have saved approximately 374,276 lives.
One company that is happy about the change is ZF Lifetec. Based in Aschau am Inn, Germany, just east of Munich, ZF Lifetec is one of the world’s largest manufacturers of seat belts, air bags, steering wheel systems and other safety-critical components. The company’s products are found in small, mass-market cars as well as sophisticated luxury vehicles. Employing some 36,000 people, ZF Lifetec has 48 locations across 20 countries.
ZF Lifetec tests its products under the toughest conditions to ensure the highest possible quality and reliability. Such also testing shortens product development cycles and helps engineers design new safety technologies to meet real-life accident scenarios.
Just as automotive safety technology has evolved from seat belts to air bags and advanced driver assistance systems (ADAS), the technology for testing such components has also evolved. Crash tests have been standard practice in the automotive industry since the 1970s, and ZF Lifetec carries out more than 50 dynamic tests per day worldwide. Recently, the company has added digital testing and validation procedures to its product evaluation arsenal.
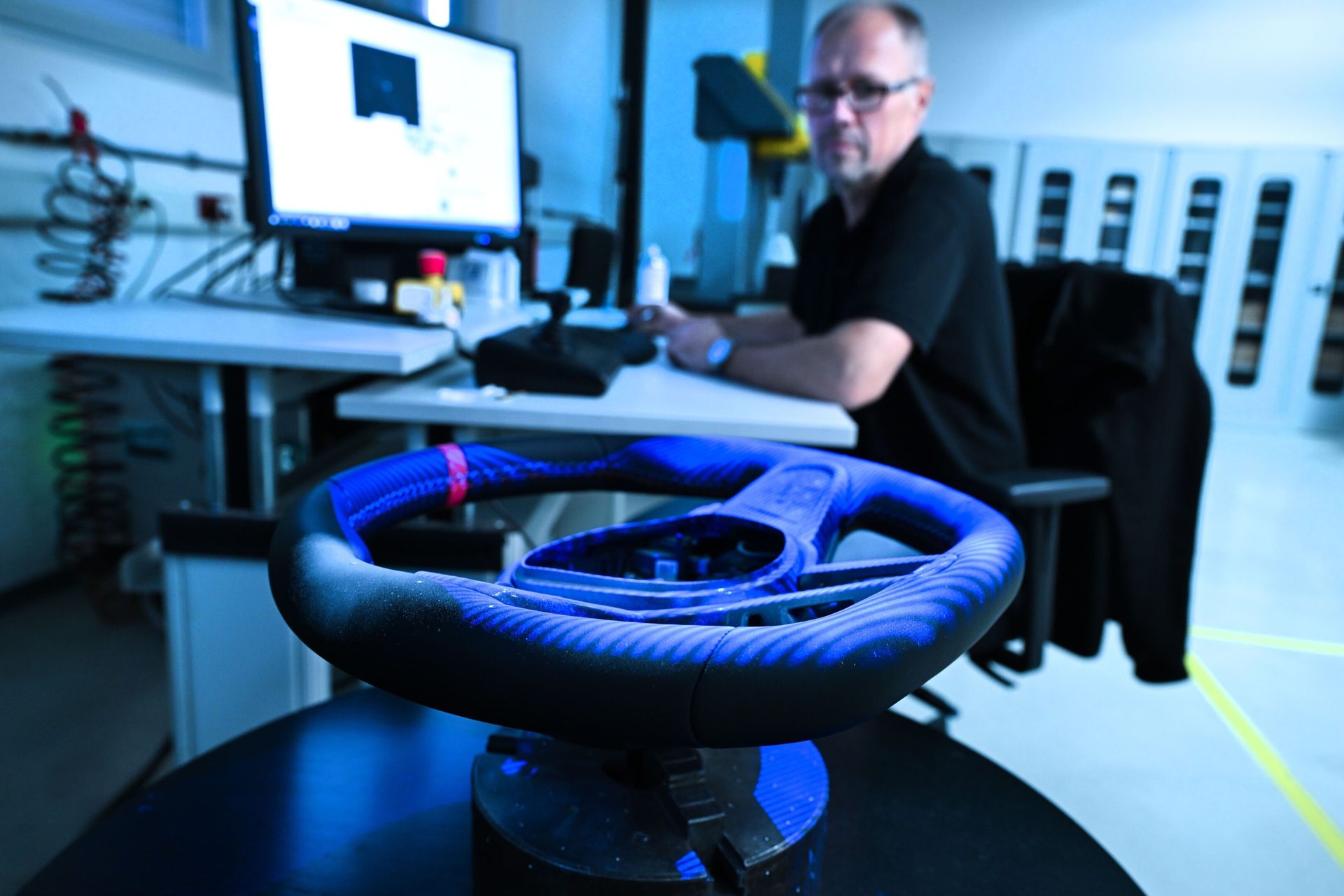
All systems must also be tested for electromagnetic compatibility. In the case of steering wheels, for example, this is important for ensuring that new functions, such as hands-on detection, are fail-safe. Photo courtesy ZF Lifetec
Adaptive Safety
Automotive safety concepts are changing. Today, engineers are increasingly focusing on people as individuals. Engineers are looking to adapt safety technology to the individual stature, gender and age of vehicle occupants. A range of technologies and strategies are available for this adaptive approach, but they can only be developed through a combination of physical testing and virtual validation.
A good example is the crash-test dummy, which was introduced in 1976. Originally, the dummy was developed to simulate an average, middle-aged man. But, of course, no two men or women are the same. Some are tall; some are short. Some are thin; some are fat. Elderly people have more fragile bones than younger people. As a result, a whole family of crash test dummies has since been developed. Now, dummies are available for, say, a “5th percentile woman” or an elementary school child.
“The trend in passive safety systems is towards adaptive systems that can respond more specifically to the actual accident scenario and the actual need for restraint forces,” explains Kai-Ulrich Machens, Ph.D., manager of seat belt systems engineering at ZF Lifetec.
Thanks to novel sensor systems in cars, the control software for restraint systems will have access to significantly more information in the future. What kind of crash is occurring? What is the weight of the person in the driver seat? What is the weight of the occupant in the passenger seat? Is the occupant sitting straight, slouched or leaning forward? This information could be valuable, since a petite person might need a different level of restraint in a frontal crash than a larger person. Adaptive safety means that each passenger receives a level of restraint and protection that fits their situation specifically.
To create adaptive safety systems, engineers will need data from a large number of tests that, for example, place different loads on the components of a seat belt system. To recognize critical dynamic loads in good time and counteract them correctly, all significant dynamic loads on the belt system (force levels, pull-out distance and speed) must be recorded. Even pre-crash dynamics need to be evaluated. This also applies to the entire occupant protection system. Developing this overall picture without the interaction of real and virtual tests would require a great deal of time and resources.
“This is an attractive topic for the future, because the adaptability of restraint systems has been specified by New Car Assessment Programs [NCAP] worldwide as a development goal,” says Harald Lutz, head of development at ZF Lifetec.
The advent of self-driving vehicles is another consideration when developing passive restraint systems. Automated driving will soon change the interior of vehicles, providing seating positions that are significantly different from existing configurations.
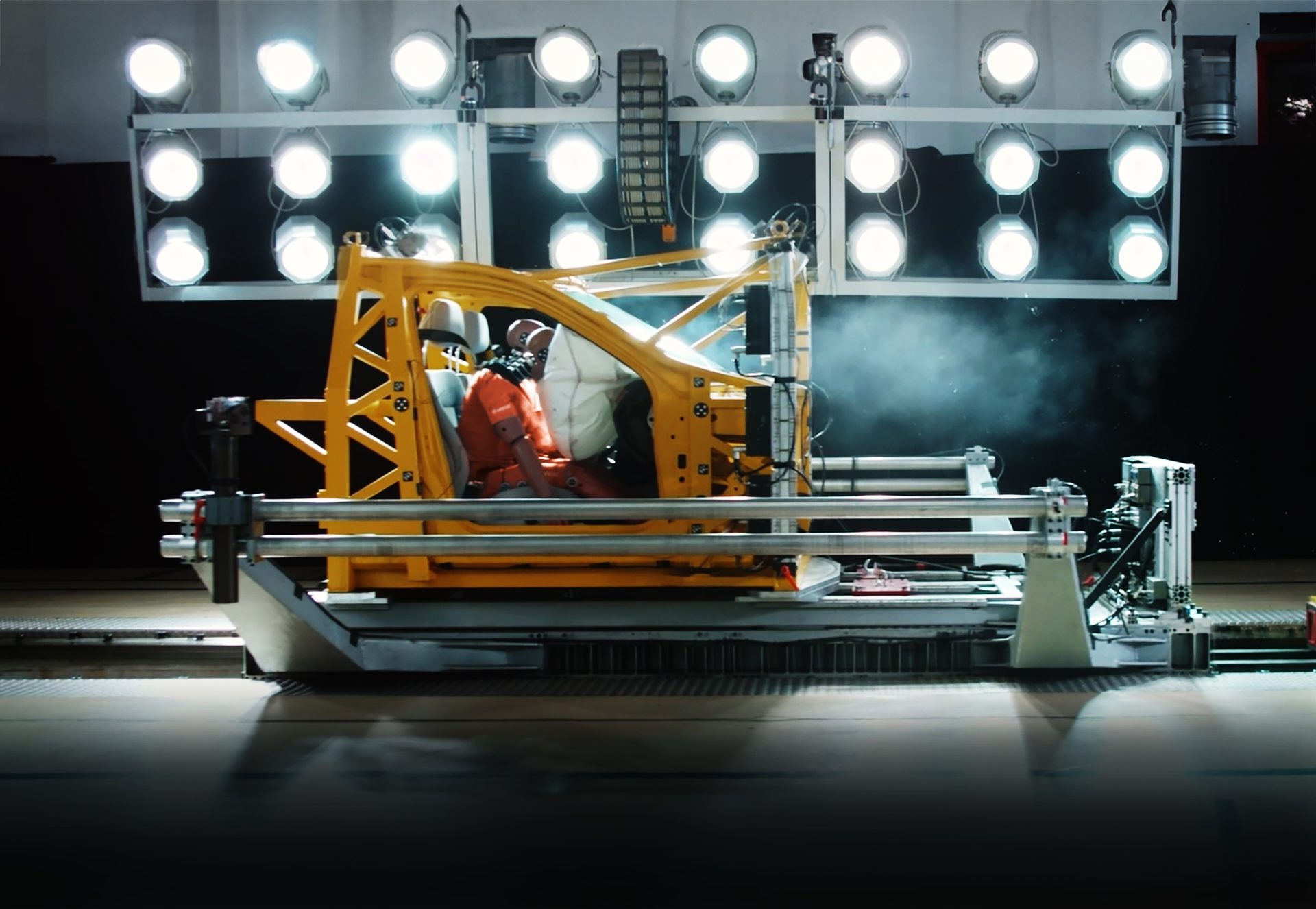
Crash tests have been standard practice in the automotive industry since the 1970s. Photo courtesy ZF Lifetec
Worldwide Dynamic Tests
Dynamic testing assesses how safety components, such as seat belts and air bags, behave both individually and as a complete system during crash simulations. ZF Lifetec has crash-test sleds in five markets (U.S., Japan, Italy, China and Germany). All tests are conducted in accordance with local and global automotive safety standards, such as Euro NCAP, China NCAP, U.S. NCAP, and the Federal Motor Vehicle Safety Standard.
ZF Lifetec is consistently developing and digitizing testing. The company is using its experience and the immense amounts of data from previous tests to virtualize the testing process.
“Simulations will not replace real tests, but a good mix of simulation and real tests will make testing much more efficient in the future,” explains Lutz.
A basic requirement for virtual testing is the validation of the underlying assumptions. This is the only way to ensure that virtual tests match reality. To guarantee this, ZF Lifetec has developed the hyper dynamic response actuator (HyDRA). This test bench, which is unique in the industry, enables a quick and precise comparison with reality. It validates a digital twin that enables significantly shorter development cycles and serves as an enabler for “real-life safety.”
The HyDRA is an electric mini-sled for highly dynamic tests on seat belt systems with velocities up to 144 kilometers per hour and accelerations or decelerations up to 70 g. HyDRA is equipped with precise measurement technologies. For instance, inductive displacement sensors can capture every shift at specific measurement points during the crash sequence up to a thousandth of a millimeter. Integrated load cells precisely record the dynamic load on the seatbelt during the crash phases.
All these sensors generate data to create a digital twin of the simulator that runs in parallel with the physical test from the very beginning. With a digital twin, physical tests (expensive and slow) can be replaced by a multitude of virtual tests or simulations (efficient and fast).
“Usually, during seatbelt development, complex system tests are performed for each model of a vehicle manufacturer,” explains Machens. “With HyDRA, we could generate many of these test results with high accuracy through virtual testing. This enables us to speed up our response time to customer inquiries.”
HyDRA is also helping ZF engineers assess another automotive trend: the advent of ADAS. How are technologies such as automatic emergency braking (AEB) affecting the performance of traditional safety systems, such as seat belts. For example, AEB systems are designed to prevent crashes or reduce the speed of a vehicle at impact. On the other hand, sharp braking may cause vehicle occupants to shift forward, “consuming” some of the seat belt displacement that might otherwise have helped to decelerate vehicle occupants during a crash.
Once the new test system has completed hundreds of tests with standardized and digitized test setups, the data will be used for further analyses, such as comparing different design levels during development or across projects. Artificial intelligence algorithms will be employed to identify patterns and characteristics.
“In this way we will learn even more from the crash tests and further accelerate our development work,” says Machens.
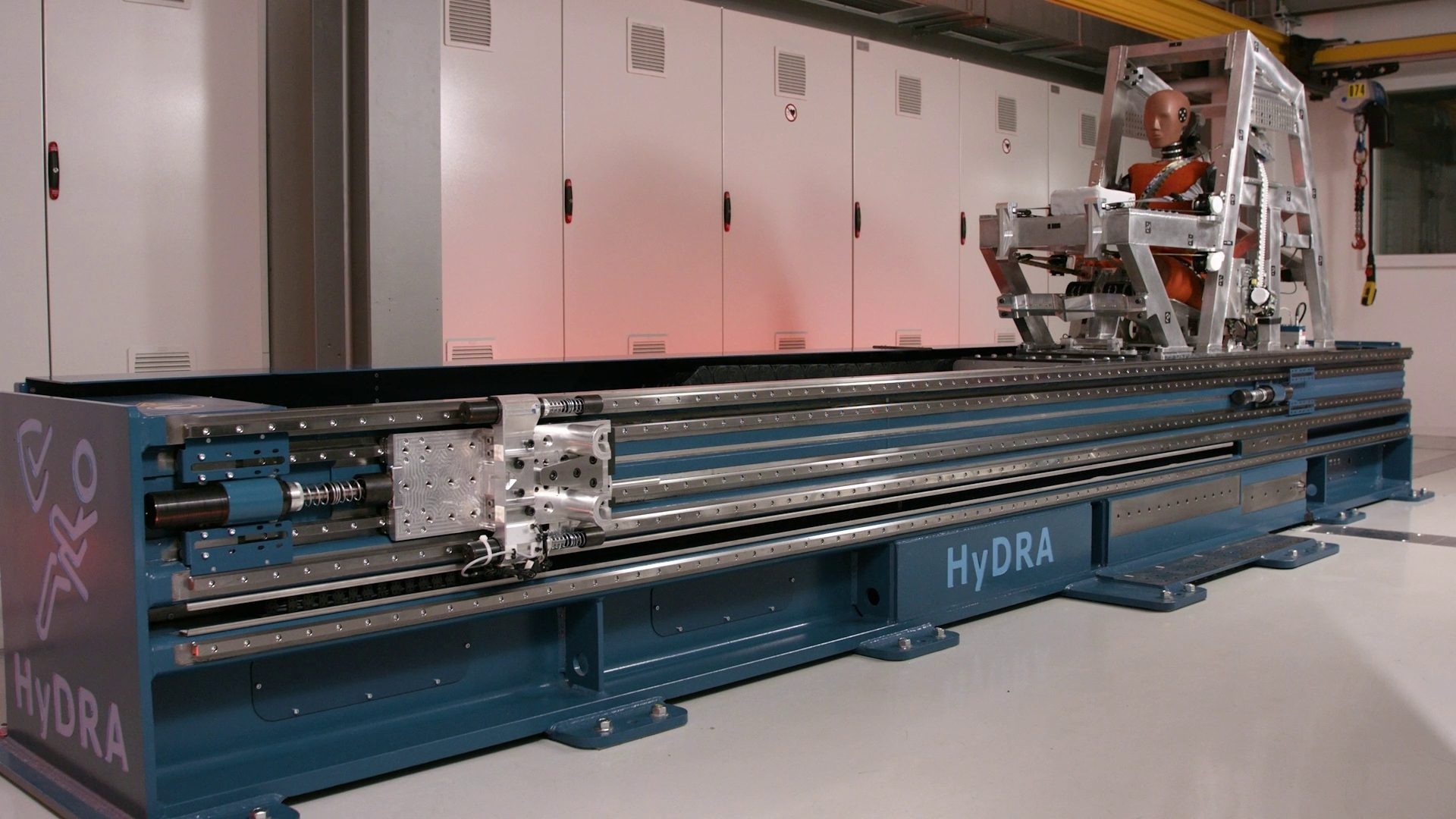
The HyDRA is an electric mini-sled for highly dynamic tests on seat belt systems with velocities up to 144 kilometers per hour and accelerations or decelerations up to 70 g. Photo courtesy ZF Lifetec
Specialist Down to Component Level
Manufacturers of automotive restraint systems must cover a wide range of disciplines, technologies and materials when testing components. Engineers are always experimenting with textiles for seat belts and air bags, plastics and metals for housings and steering wheels, and pyrotechnic propellants for air bags.
Comprehensive material and environmental simulation tests are on the agenda for all components, especially in the prototype phase. Aging and wear processes are simulated and run under realistic conditions, often with the help of custom test benches. Engineers examine the influence of salt water, sunlight, dust, thermal cycling and vibration to rule out impairments to functionality.
All systems must also be tested for electromagnetic compatibility. In the case of steering wheels, for example, this is important for ensuring that new functions, such as hands-on detection, are fail-safe.
Inspection System
ASSEMBLY ONLINE
For more information on product testing visit www.assemblymag.com to read these articles: