AUTOMATION REVIEW
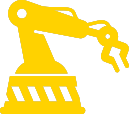
CONTACT
Austin
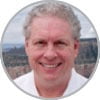
Lightweight battery-powered aircraft are ready for take-off.
Nissan Plant Hosts Assembly South Attendees
Austin Weber // Senior Editor // webera@bnpmedia.com
The 42-year-old facility in Smyrna, TN, is home to the Murano, Pathfinder and Rogue.
Nissan’s state-of-the-art assembly plant in Smyrna, TN, is one of the largest auto factories in the world. Photo courtesy Nissan Motor Co.
Nissan Motor Co.’s state-of-the-art assembly plant in Smyrna, TN, is one of the largest auto factories in the world. The 42-year-old facility boasts more than 6-million-square-feet of production space, including a body shop, a paint shop, a final assembly line and a two-mile-long test track.
The plant recently hosted a group of Assembly South attendees before the third annual show began in Nashville. During the “field trip,” 60 participants toured various parts of the massive complex. The guided trip aboard a tram provided an up-close look at the vehicle production process.
The Smyrna factory specializes in mass-producing sport utility vehicles. It is home to popular SUVs such as the Murano, Pathfinder and Rogue.
Nissan’s flagship factory was in the news during the visit in mid-April due to the threat of tariffs. Because it is particularly vulnerable to the effects of a prolonged trade war, the automaker announced that it would reverse course on a recent decision to cut back on U.S. manufacturing activity. That plan originally called for a reduction at Smyrna from two shifts a day to only one.
Instead, Nissan revealed plans to shift assembly activity from facilities in Japan and Mexico to “max out” production at the underutilized Smyrna plant, which has a capacity to produce 640,000 vehicles annually. The top-selling Rogue, for instance, is also made at a Nissan factory in Kyushu, Japan.
AUTOMATION ASSEMBLY PRODUCTS
The AGV provides 50-course 128-command control, programming. The AGV is a model HA-A50060 single-direction AGV drive unit with 90° and 180° spin/turn capability. The unit can travel with speeds up to 164 fpm (50 M)/min and can carry a load capacity of up to 1320 lb.
Creform Corporation
800.839.8823
SCsales@creform.com
www.creform.com
AGV system with powered conveyor help increase productivity.
Nissan, which is in the midst of a corporate restructuring, generated 30 percent of its revenue in the United States in 2024. It sold 924,000 vehicles here, with 45 percent of them imported from Japan and Mexico. In a dramatic shift, the automaker now plans to produce at least 80 percent of its vehicles in America, with the Smyrna plant playing a key role.
Proud History
Nissan traces its roots to the Kwaishinsha Motor Car Works, which started building vehicles in Tokyo in 1914. The company changed its name to Nissan 20 years later and opened Japan’s first large auto factory in 1935. An integrated production system developed at its main plant in Yokohama enabled the company to create that country’s first mass-produced car, the Datsun Model 14.
Nissan sold its first automobile in the U.S., a Datsun 210, in 1958. Eight years later, through a joint-venture operation in Jiutepec, Mexico, it opened its first overseas assembly plant.
In 1977, Nissan engineers developed the world’s first multiarm robot. A joint R&D project with Tokyo Shibaura Electric Co. (Toshiba Corp.) resulted in a machine that could perform the work of four conventional robots, with simultaneous multi-spot-welding capabilities.
Let Fusion help streamline your brazing or soldering process! We transform manual processes into turnkey automation systems, providing years of cost-efficient production. Cut labor costs, increase production, and optimize output. Ready to learn more? Visit our website or contact us for a free consultation!
Fusion Incorporated
440-946-3300 / 800-626-9501
Automated Brazing and Soldering Machines
Nissan Motor Manufacturing Corp. USA (NMMC) was established in July 1980. Soon after, the company made headlines when it announced plans to build a large factory 23 miles southeast of Nashville.
Smyrna was selected as the location for the new plant because of Tennessee’s antiunion reputation. The town is strategically located near I-24 and along the main line of the CSX railroad between Nashville and Atlanta. The state of Tennessee also agreed to build an interstate connector road and to provide extensive training for employees.
Marvin Runyon, formerly vice president of body and assembly operations at Ford Motor Co., was named president and CEO of NMMC. He played a key role in the construction and ramp up of the Smyrna factory. Runyon later went on to become chairman of the Tennessee Valley Authority and served as U.S. postmaster general in the 1990s.
Ground was broken in February 1981 on a 778-acre site that was once rural farmland. At the time, Japanese manufacturers and lean manufacturing practices were still a novelty in the United States.
Nissan spent $63 million training employees and adopting the latest robotic techniques. It implemented just-in-time assembly processes using more than 2,000 parts supplied by third-party suppliers.
With their innovative design, COVAL's CVGC carbon vacuum grippers correspond perfectly to the demands of collaborative robot applications. The CVGC series stands out with a compact, light, strong carbon structure, collaborative safety measures, a choice of gripping interfaces, with or without an integrated vacuum generator. It is easily incorporated on your robot guaranteeing a fast setup.
COVAL Vacuum Technology, Inc.
919-233-4855
New Generation Collaborative CVGC Carbon Vacuum Gripper
Originally, many of those parts, such as axles, chassis components, engines and transmissions, were imported from Japan. But, eventually, almost all were produced within a 100-miles radius of Smyrna using just-in-time delivery.
“Along with importing such practices as morning exercises and company uniforms, [Nissan] is also applying many of the more substantive features of the Japanese way,” explained an article about the new assembly plant in the April 4, 1983, edition of The New York Times. “These include special relationships with suppliers, bonus payments for all employees, cross-training for workers in several jobs and a leaner management structure.
“The $660 million plant—the largest direct investment in the United States ever made by a Japanese company—will begin operations next month, although the main opening is scheduled for October and full-scale production will not be reached until well into 1984. By then, the plant is scheduled to be producing 13,000 light trucks a month, and the payroll will include more than 2,000 workers. About 1,000 workers have been hired so far.
“Nissan executives believe they will meet with little resistance in transplanting Japanese-style work methods to the United States. For one thing, they say, the company is starting with a fresh work force that is not steeped in American car-making and labor-management traditions. For another, Nissan has had the luxury of being able to be fussy—more than 80,000 people have applied for the 2,000 available jobs.
“One of the main considerations in selecting workers for the Tennessee operation has been the applicants’ willingness to go along with ‘the participative management that [will be used] at the operation.’ So far, the company has spent several million dollars bringing more than 375 American employees, including 128 hourly workers, to observe and work alongside their Japanese counterparts at Nissan factories in Japan.
A large integrator of equipment for a global leader in automobile manufacturing, Ford Motor Co, came to us in need of a specialized index drive, capable of handling extremely high loads, but also maintain specific load height and dimensions, due to tooling design and operator ergonomics. The integrator required us to not only supply the indexing device, but also the complete base plate and frame to meet their needs.
Motion Index Drives
248-743-9999
Tooling Frames for Automotive Manufacturing
“One Japanese manufacturing practice put in place at Smyrna has already had an effect outside the plant gates. Japanese auto companies are known for their unusually close relations with suppliers and for demanding delivery of small batches of parts or components every few hours. The practice, known as kanban, or ‘just-in-time’ inventory control, reduces manufacturing costs by eliminating expensive stockpiles of parts.
“As one example of how the practice is affecting potential Nissan suppliers, Hoover Universal, a Michigan-based company, agreed to build a factory in Murfreesboro, TN, to win a contract to supply Nissan with seats for its small trucks. The seats will be delivered to Nissan’s plant every hour. In contrast, American parts suppliers are accustomed to shipping freight-car lots every week or so to customers who may be hundreds of miles away.
“‘We have only one supplier for seats, and we don’t plan to have a second,' Runyon said, noting that American manufacturers traditionally have wanted two suppliers for the same part.
“‘We are going to be very dependent on our suppliers and they on us,’ Runyon added. “‘There has to be close cooperation and trust between us for both parties to stay in business.’
Designed for optical inspection and robotic part selection, Performance Feeders’ Flexible Feeding solutions enhance the efficiency of automated product assembly processes. From the simple, economical conveyor matrix to the FlexiBowl® turntable model, our Flex Feeders handle a wide variety of part materials, shapes and sizes and are easily reconfigured to accommodate part changes. Take a closer look
Performance Feeders, Inc.
813-855-2685
“In its attempt to build a cooperative spirit between workers and management, Nissan is making every effort to minimize the usual trappings of rank and corporate status. All employees, for example, will eat at one of two company cafeterias and ‘there’s no separate dining room for executives,’ Runyon said.
“In another break with the traditions of American-style auto manufacturing, there are no ‘line workers’ in the vernacular of the Smyrna plant—only ‘production operators’ and ‘technicians.’”
On June 16, 1983, the first Nissan manufactured in the U.S.—a white 720 pickup truck—rolled off the Smyrna assembly line. Since the trendsetting factory opened 42 years ago, other automakers have opened facilities in Tennessee, including General Motors (Spring Hill) and Volkswagen (Chattanooga).
Ford Motor Co. is currently in the process of building Blue Oval City in Stanton, TN. A who’s who of Tier One suppliers also operate assembly plants in the Volunteer State, including Denso, Hitachi, Mahle, Marelli and ThyssenKrupp.
Nissan has since opened several other facilities in the U.S., including an engine assembly plant in Decherd, TN, (59 miles southeast of Smyrna) and a factory in Canton, MS, that produces the Altima sedan and the Frontier pickup truck. Nissan North America Inc.’s corporate headquarters are located in Franklin, TN. It also operates a technical center in Farmington Hills, MI, and a design center in San Diego.
RACO International provides customized, precise products that enhance efficiency and reliability in industrial operations. Our global expertise and commitment to quality offer innovative solutions tailored to business needs, boosting productivity and competitiveness in the industrial sector.
RACO International, L.P.
412-835-5744
We are Linear Motion People
Productive Plant
Nissan’s Smyrna plant has always been known for being highly productive and committed to quality. In 1985, it began assembling passenger cars such as the award-winning Sentra sedan. A third line was added in 1991 for the Altima sedan. At the end of the decade, the plant ramped up production of a new SUV called the XTerra.
Smyrna made headlines again in January 2013, when it became the first U.S. factory to mass-produce lithium-ion batteries and electric vehicles at the same location. Nissan opened the state-of-the-art battery plant a month before. The 1.3-million-square-foot integrated facility could produce both cells and modules, with a capacity to make up to 200,000 battery packs annually.
“Though Leaf is a revolutionary vehicle, its assembly requirements are much more similar to those of its traditional siblings like the Altima and Maxima, with which it shares a manufacturing line,” explained Susan Brennan, vice president of manufacturing at Nissan. “Adding the electric vehicle to the Smyrna manufacturing environment required only a few process changes, such as the addition of quality confirmation specifically for electric vehicles and special training for technicians.
Ready or not, your industry is changing. Discover how to stay in the lead with this must-read white paper. You’ll gain clarity on the data-connected systems and automated motion control technologies reshaping workflows for critical agility and uncompromising precision.
GET THE INSIGHTS
IMI Norgren
Mike Parzych
720-283-5263
Four industrial shifts you can't ignore
“Process efficiency is a never-ending activity for us,” claimed Brennan. “We strive to create new internal benchmarks in efficiency with each new model. By assembling the Leaf on our current Altima and Maxima line, we are able to reduce costs by using existing equipment.
The Smyrna factory specializes in mass-producing sport utility vehicles. Photo courtesy Nissan Motor Co.
“For example, while gas-powered vehicles receive fuel tanks and internal combustion engines when they come down the line, the Leaf gets a lithium-ion battery pack made at our battery plant next door and an electric motor produced at the Nissan power train plant in Decherd. We truly have localized U.S. manufacturing of the Leaf’s major components across the board.”
Nissan Smyrna began assembling the Rogue in September 2020, during the midst of the Covid pandemic. “Our U.S. manufacturing team rallied together like never before to overcome unprecedented challenges that could have impacted this moment,” said Steve Marsh, senior vice president of manufacturing, supply chain management and purchasing at Nissan North America.
Nissan engineers used virtual reality tools to ensure a smooth ramp up and to troubleshoot issues before moving to the production floor.
“The technology not only helped to identify manufacturability concerns before the first steel was cut for production tools, but also shaped the design of process equipment through early, virtual feedback from production technicians, helping to prevent production delays,” explained Marsh.
Boulware Equipment, LLC is 100% committed to repurposing industrial wood waste. We convert industrial wood trash into a valuable product and have a nationwide network of wood fiber buyers who rely on our systems supply of predictable quality.
We deliver our clients a reliable “Turn-Key” wood waste solution for almost any pallet / crate & industrial wood waste problem in manufacturing and assembly industries. We offer our systems nationwide.
Boulware Equipment, LLC
704-651-6061
Boulware Systems Keep Wood Trash Out of Landfills
Engines are made at a nearby factory in Decherd, TN. Photo courtesy Nissan Motor Co.
Those efforts paid off when Nissan Smyrna was honored for the quality of its products in 2021. It received the coveted Gold Plant Quality Award from J.D. Power. And, that same year, the Murano assembly line ranked first in quality performance among North American manufacturers.
“The Smyrna team is incredibly focused on building exceptional vehicles that are driven on roads across the country—and all over the world,” remarked Jeff Younginer, vice president of manufacturing at Nissan. “This recognition is a testament to their ‘one team’ spirit and pride in delivering products with great quality and reliability.”
Current Operations
Sport utility vehicles play a key role in Nissan’s U.S. strategy. Four models—Frontier, Murano, Pathfinder and Rogue—accounted for 48 percent of its U.S. sales in 2024. The latter three products are made at the Smyrna plant, which has a capacity to produce up to 2,000 SUVs a day. Vehicles are exported to a variety of countries, including Norway, South Korea and the United Arab Emirates.
Nissan has invested more than $6 billion in the facility over the last 44 years. In 2024, the plant won the inaugural “Coolest Thing Made in Tennessee” competition sponsored by the Tennessee Manufacturers Association. It also celebrated the production of its 15 millionth vehicle, but the plant shows no signs of slowing down.
Although Leaf production in the U.S. ended in December, Nissan has plans to produce other EVs in the near future. The automaker is currently in the process of installing three new stamping machines in the Smyrna body shop, in addition to a $13 million investment in plastic injection molding equipment to produce interior and exterior trim components. The facility is also unique among auto plants because it produces front- and rear-end fascias in-house.
ACE Controls delivers precision motion control solutions that enhance automation system performance. Our shock absorbers and gas springs ensure smoother, faster, and more reliable machine operation. Trusted across industries, our products help reduce downtime and increase productivity, making them an essential component in today’s high-performance automated assemblies.
ACE Controls
(248) 476-0213
ACE Controls Streamlines Automation Efficiency
Nissan Smyrna is home to popular SUVs such as the Pathfinder. Photo courtesy Nissan Motor Co.
Nissan Smyrna has also invested heavily in automation, with 36 miles of conveyors. Automated guided vehicles and smart carts are used for line-side parts delivery. And, an army of 1,500 six-axis robots in the body shop perform 95 percent of all welding tasks.
The recent tour during the Assembly South show focused on the factory’s chassis, trim and final assembly lines. At one point, the guide slowed down the tram and proudly pointed out the collaborative robots in use at the window installation workstation.
Nissan claims that it has deployed more cobots on the Rogue assembly line than it has with any other previous model launch. The technology enables humans and machines to work in close proximity.
Collaborative robots enable operators to focus on value-added assembly tasks. Photo courtesy Nissan Motor Co.
Cobots ensure that repetitive tasks are done the same way every time, while reducing ergonomic risks and improving safety. This frees up operators to focus on value-added assembly and enables them to produce even higher quality vehicles.
Nissan Smyrna also is a leader in energy management. In 2012, it became the first passenger vehicle manufacturing facility to attain ISO 50001 and Superior Energy Performance certifications. In addition, the plant is ISO 14000 certified and has received an Energy Star distinction every year since 2006. And, it’s currently in the process of becoming a landfill-free facility.
“A company with Ford’s scale can really influence the supply chain and business practices across our entire industry,” adds Sue Slaughter, purchasing director at Ford Motor Co. “It is so important that we not only think about how [we] can use our purchasing power to fuel our business needs, but also to advance sustainability.”
Because the automotive supply chain is extremely complex, the Guiding Principles contain expectations about business ethics, working conditions, human rights, health and safety, environmental leadership and supply chain due diligence for suppliers at all tiers. All suppliers are expected to uphold these standards and enforce them throughout their supply chain.
The Guiding Principles are based on fundamental elements of social, environmental and governance responsibility that are consistent with applicable laws and international standards created by organizations such as the United Nations.
Topics covered under the revised guidelines include the following:
Business ethics, including counterfeit parts and data protection.
Environmental issues, such as air quality, carbon neutrality, chemical management, circularity and water management.
Health and safety issues, such as personal protective equipment and workspace.
Human rights and working conditions, such as benefits, wages and working hours.
Responsible supply chain management, such as ethical sourcing of raw materials.
The BMW Group has implemented several projects in its packaging logistics unit to help the environment and conserve resources. The goal of the initiative is to work closely with suppliers to reduce carbon emissions and adhere to the principles of a circular economy.
BMW’s European assembly plants are using more recycled material in their packaging. For newly awarded contracts, the proportion of recycled material in reusable packaging for logistics purposes will almost double this year from around 20 percent to over 35 percent.
Using alternative sustainable materials, reducing single-use packaging, introducing lightweight packaging in certain areas and reducing transport volumes will also help cut carbon emissions.
BMW is monitoring the impact of individual measures via a CO2 calculator for packaging. The automaker’s overall aim is to reduce CO2 emissions in the supply chain by 20 percent per vehicle compared to 2019.
“Our re:think, re:duce, re:use, re:cycle approach is being implemented consistently in packaging logistics,” says Michael Nikolaides, head of production network and logistics at BMW Group. “We’re using innovative strategies to consistently reduce the volume of resources we use, thus reducing our carbon footprint.
“We are also doing our part to get the BMW iFACTORY up and running, with a particular focus on the ‘green’ side of things…with an emphasis on flexibility and efficiency, sustainability and digitalization,” explains Nikolaides. “It provides an answer to the challenges involved in the transformation to e-mobility and [leverages] the latest technologies to create a production process that uses minimal resources.”
According to Nikolaides, BMW is using more recycled material, such as expanded polypropylene (EPP) packaging. “Our newly developed EPP packaging already contains 25 percent recycled material,” he points out. “EPP is used in special containers, as its shape can be adapted to the components being packaged, allowing them to be transported safely.
“Around 360,000 of these containers are needed each year,” claims Nikolaides. “Using 25 percent recycled material allows us to save almost 280 tons of CO2 annually. There are plans to increase this proportion of recycled material even further, with the first pilot schemes with 100 percent recycled material currently underway. If these tests are successful, this configuration will become standard for new contracts from 2024.
“An additional 680 tons of carbon emissions savings can be made every year by using covers and so-called small load carriers with 50 percent recycled contents,” says Nikolaides. “As things stand, these measures are focused within the European markets due to the current waste management situation and available recycling infrastructure. But, we are working toward expanding to our locations in China, Mexico and the United States.”
BMW also plans to use folding large load carriers in place of traditional pallet cages made of steel. The plastic alternatives will be made from over 90 percent recycled material. They work in a similar way to the collapsible shopping crates that most people are familiar with.
When they’re empty, the carriers can be folded up, making them easier to transport. Nikolaides claims that using 15,000 of these new containers will reduce CO2 by around 3,000 tons per year.
“When it comes to packaging, the sky’s the limit,” says Nikolaides. “We’re launching pilot projects using bio-based materials to replace oil-based substances such as polyethylene and polypropylene.
“We are also investigating whether and in what ways we can use materials from recycled household appliances in our packaging,” explains Nikolaides. “In the long term, our aim is to use alternatives to raw materials across the board.”
BMW Initiative Targets Sustainable Packaging
BMW is using sustainable packaging in its assembly plants. Photo courtesy BMW Group
ASSEMBLY ONLINE
For more information on automotive assembly, visit www.assemblymag.com to read these articles: