FROM THE EDITOR
Factory managers in Asia are bullish that, by 2040, factories will rely almost completely on AI-enabled self-learning machines and robots, overseen and assisted by human workers. Their peers in Europe and the U.S. are more cautious, but agree the future of manufacturing will look quite differently from today.
These are findings from Accenture’s new report, Rethinking the Course to Manufacturing’s Future. Accenture surveyed 552 factory managers in Asia (China, India, Japan), Europe (Austria, Denmark, Finland, France, Germany, Italy and Switzerland) and the U.S. in December 2024. The respondents represent various industries, including automotive OEMs and parts suppliers, aerospace OEMs and parts suppliers, machinery manufacturers, electrical equipment manufacturers, and heavy equipment manufacturers.
According to the report, AI, automation and digital technologies will become increasingly important in manufacturing. Approximately half of the respondents stated that, by 2040, hyper-automated factories will rely on the following elements, which provide more agility and flexibility while enabling a step change in productivity:
• Autonomous operations (53 percent).
• Self-learning machines using generative AI (52 percent).
• Completely automated warehouses (51 percent).
• Smart connected manufacturing cells (49 percent).
• Autonomous mobile robots (49 percent).
• Digitally connected crews (48 percent).
• Digital twins (47 percent).
• Automated guided vehicles (45 percent).
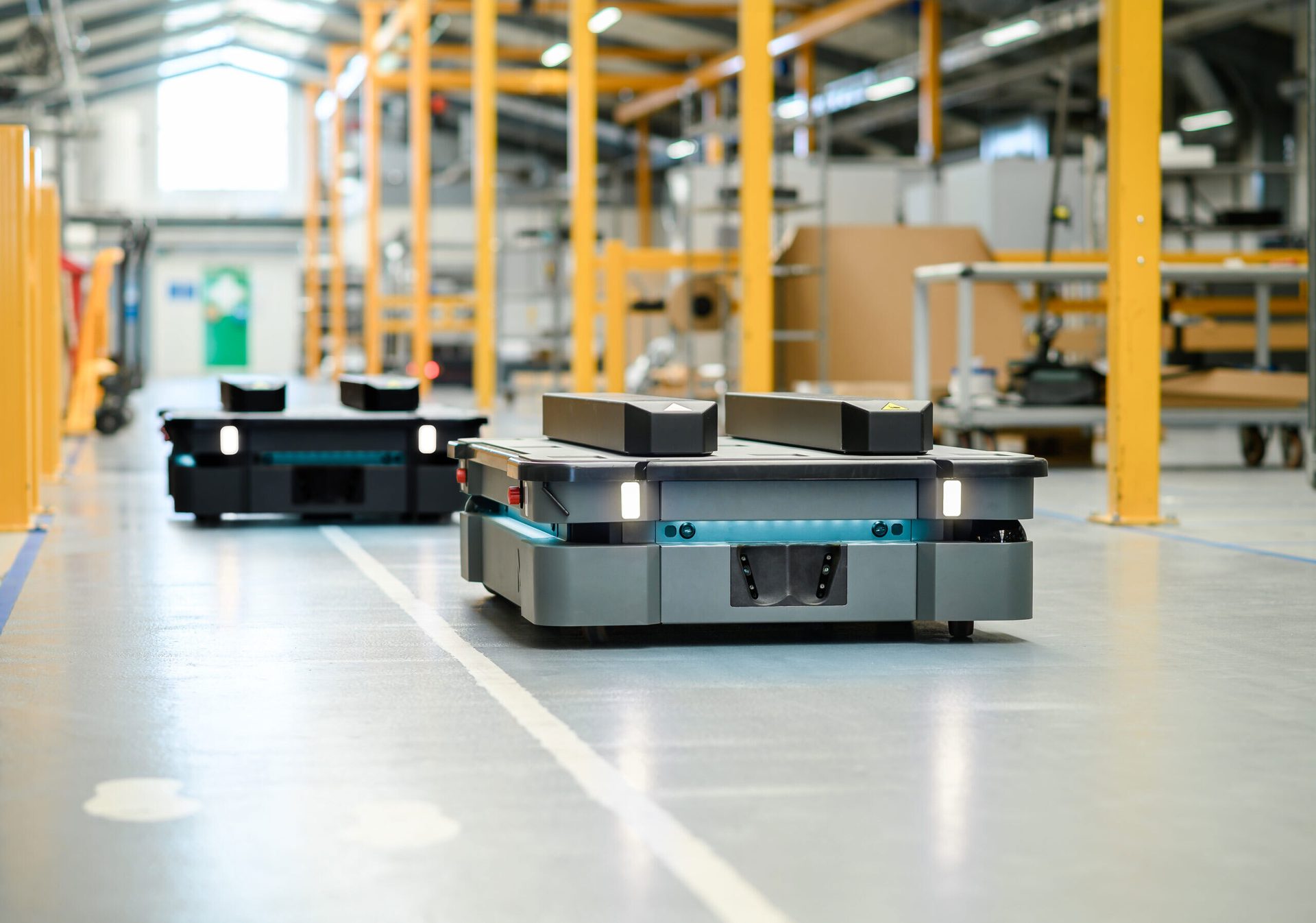
Autonomous mobile robots are among the “hyper-automation” technologies that could someday lead to “lights-out” factories. Photo courtesy Teradyne
“In the factories of the future, AI will govern industrial production in real-time and static production lines will be a thing of the past,” predicts Patrick Vollmer, global industry group lead for industrials at Accenture. “Digital twins will simulate the outcomes of every decision before it is executed, and humanoid robots will work alongside workers. Manufacturers won’t be debating automation, AI or digitalization—those will be the baseline.”
Between 51 percent and 83 percent of the factory managers in China and Japan agreed with these statements—considerably more than in the U.S., where only 31 percent to 50 percent said future factories would feature these technologies and application. In Europe, even fewer respondents (25 percent to 39 percent) believe these technologies and applications will be part of production sites by 2040.
The more futuristic and advanced the concept, the more marked the regional differences:
74 percent of factory managers in Japan stated that, by 2040, their companies will prefer “dark factories” when building new facilities (China: 53 percent, U.S.: 29 percent, Europe: 20 percent).
At the same time, humanoid robots will be standard in their companies’ assembly processes, 72 percent of respondents in Japan claimed (China: 65 percent; U.S.: 35 percent, Europe: 21 percent).
“Manufacturers in Asia are paving the way for hyper-automated manufacturing and will likely benefit sooner from the competitive advantages it brings,” says Vollmer. “Companies in Europe and the U.S. take a more measured approach, in part because they build fewer new sites and existing factories are harder to transform. But this must not keep them from setting the course for hyper-automation today, not least since finding enough qualified workers will get only harder.”
Hyper-automated factories will change how people work, the roles they take on, and the skills they need to be successful in these roles. Accordingly, almost three in four factory managers (70 percent) said “workforce transformation” is a critical enabler of hyper-automated manufacturing, even more than automation (63 percent), AI (62 percent) and digitalization (61 percent).
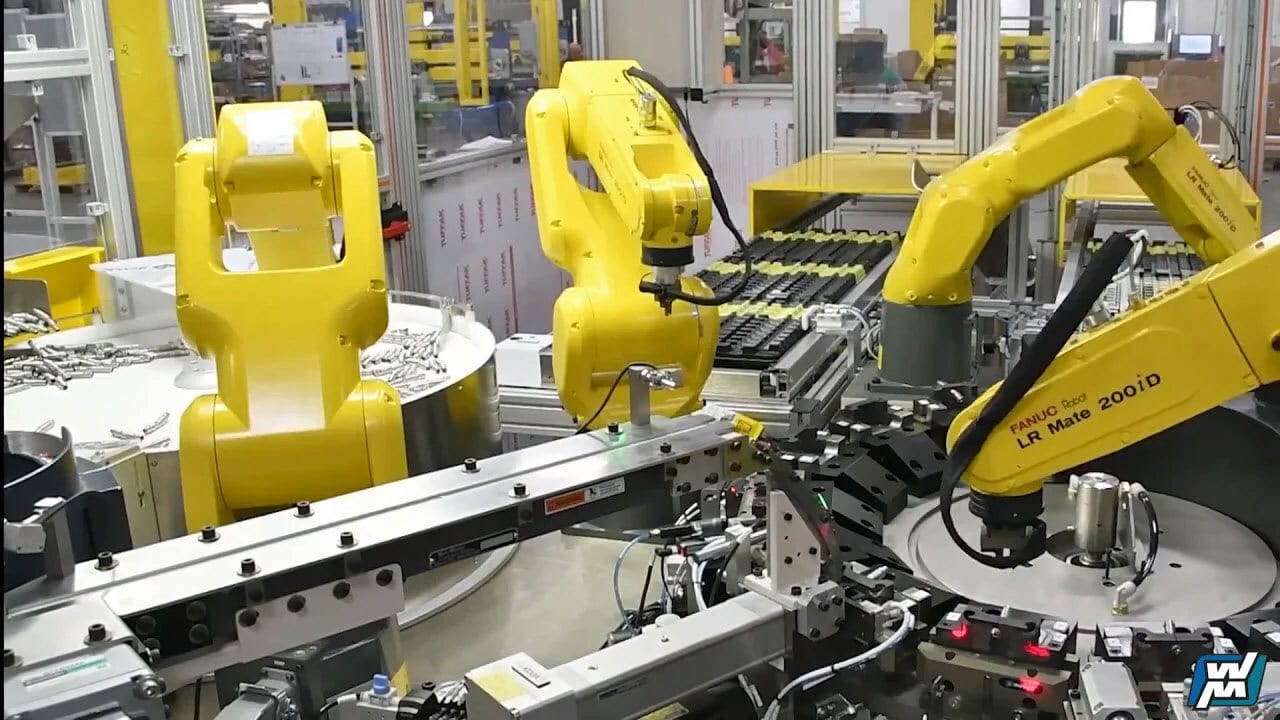
In the factories of the future, AI will govern industrial production in real-time and static production lines will be a thing of the past. Photo courtesy FANUC Corp.
How does the workforce need to change? According to most factory managers, it is in how production knowledge is preserved and shared (74 percent). They also stressed the importance of data-driven decision making (72 percent) and asserted that data analytics must become part of workers’ day-to-day work (73 percent).
Almost half (49 percent) of the respondents said the main barrier to workforce transformation are significant investments in training programs. Other barriers are people’s fear of losing their jobs (46 percent) and workers’ resistance to adapting to expanded roles (38 percent), such as human-robot collaboration manager and autonomous logistics coordinator.
Factory managers also complain about a lack of professionals with AI skills and qualifications (51 percent), which they feel most keenly in India and Japan (67 percent in both cases) and less urgently in China (40 percent).
“By 2040, most workers will no longer work in production, they will work for production,” explains Vollmer. “This means they will have moved from manual labor to process oversight, decision-making and optimization. They will need to be comfortable collaborating with AI and operating autonomous systems. Manufacturers should help their workforce develop the required skills, which are scarce and will likely continue to be.”
Most factory managers are focusing on digitalization measures that should, arguably, already be in place. By far their highest priorities are cyber security measures (77 percent), followed by the implementation of manufacturing execution systems (70 percent) and cloud platforms (67 percent).
Technologies that aren’t among factory managers’ top five priorities include IIoT and digital twins of machines and products, the exception being Japan and China. This is worrisome, according to the study, because these technologies are the digital foundations of the modern factory.
What do you think? Is “lights-out automation” a pipe dream or an achievable goal? Is it even worthwhile? Clearly, Asian manufacturers see a future for the technology. That’s ironic, since neither China nor India necessarily need automation. The two countries have a combined population of 2.8 billion. Manufacturers there can simply continue to “throw bodies” at production.
The hesitancy in the West is more puzzling. Manufacturers here have every incentive to invest in automation and yet a healthy skepticism prevails. Perhaps we’re jaded by technologies that have overpromised and under-delivered. It’s also worth noting that the survey did not include manufacturers of medical devices, consumer products and other high-volume goods.
We urge U.S. manufacturers to keep an open mind about so-called hyper-automation and invest in the technologies where and when they make sense. Our overseas competition is.