MARCH 2023
MANUFACTURING SOFTWARE
Mobile Computers Boost Efficiency at Magna
Tablets and smartwatches enable managers and maintenance staff respond quickly to issues on the assembly line.
Labor shortages are driving new demand for automation.
Options for Screwfeeding
Tablet computers equipped with cameras can be invaluable for remote troubleshooting. Photo courtesy Samsung Electronics
John Sprovieri // Chief Editor
Magna International Inc. is one of the world’s largest auto parts companies, supplying OEMs in 28 countries and four continents. Its Dortec Industries plant in Newmarket, Ontario, Canada, produces 21 million door latches per year.
Competition from China and other low-cost labor regions has put pressure on the plant, which has been operating since 1985. However, the factory continues to defy the odds, offering encouragement that Canadian manufacturers can compete in the global marketplace.
A critical component of its ability to remain competitive has been the plant’s focus on being efficient and striving for continuous improvement and growth. In a facility with 40 assembly lines, issues are bound to arise. To gain a competitive advantage, Magna engineers wanted to move from a reactive approach to addressing these issues to a more proactive one, in which issues could be handled immediately. The ability to gather intelligence on key performance indicators, such as factory waste and mean time to repair, was also a high priority.
Given the size and scope of their factory, Magna engineers thought mobile computers—tablets, smartphones and wearables—could help. One significant efficiency challenge engineers wanted to resolve with wearables was improving employee communication. When a line goes down, there are usually only one or two people in a given facility who can resolve the issue and restart the line. Finding those individuals by phone, radio or physical search inside an enormous and loud factory can be difficult and time-consuming.
See us at The Assembly Show South, Booth 625
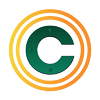
“We were trying to create a system that could self-generate and be more intuitive than our current reactive setting,” says Darren Charbonneau, the director of lean manufacturing at Magna International.
Engineers also wanted to use wearables to collect intelligence that would make waste more visible than in the past. Specifically, engineers wanted data to do the following:
- Minimize transportation.
- Reduce downtime.
- Make rework visible.
- Better utilize workforce skills.
Finally, with a long-term goal of becoming a smart factory, the company wanted to find a partner who could work with them to develop a baseline for a smart factory concept. Because Magna is a global company, it also needed a partner with a similar global reach and the expertise to show management how to leverage and develop technology that would meet the company’s needs.
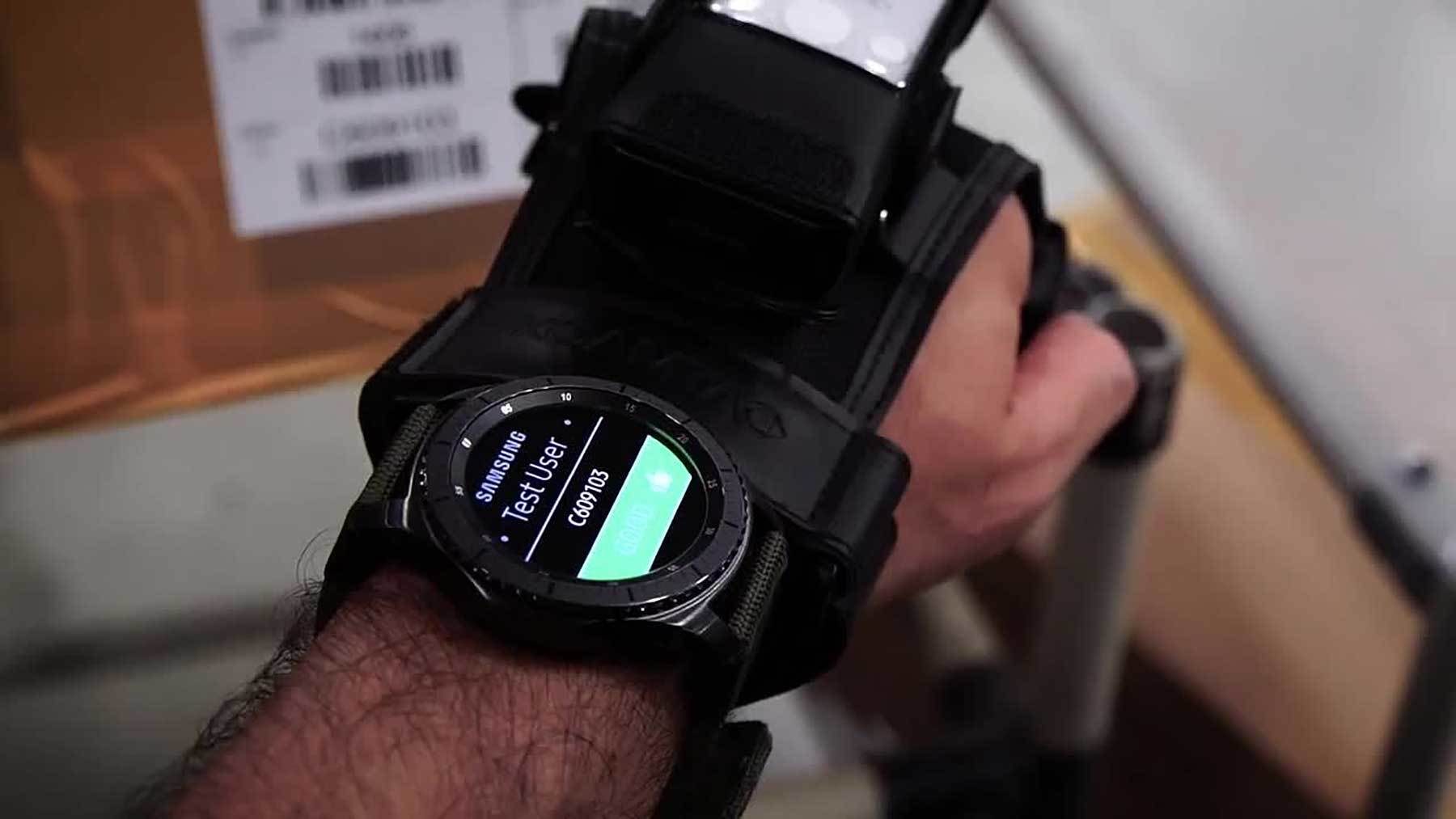
Smartwatches quickly alert maintenance personnel whenever a problem arises on the assembly line. Photo courtesy Samsung Electronics
Wearables Boost Productivity
When Magna began searching for a partner to help with wearable technology, Samsung Electronics quickly emerged as the right choice. Among the leading factors was that Samsung could offer an end-to-end system, including both hardware and software.
“We were able to utilize Samsung’s enterprise solutions as a package set where we would have [otherwise] required multiple vendors to supply us,” says Charbonneau.
Samsung worked closely with the Magna’s engineers to create a comprehensive system that would provide real-time information about their factory environment, as well as enable them to take the first step toward becoming a smart factory. The system uses Samsung Gear S3 smartwatches, tablets and 55-inch televisions around the facility. When issues arise, the tablets are used to send alerts to maintenance personnel wearing smartwatches. The televisions display analytics on critical factory metrics, such as mean time to repair. With improved factory intelligence from wearables in manufacturing, Magna can more easily identify areas of waste and react faster to issues.
Everything is connected. Tablets and smartwatches can communicate with each other around the plant. To ensure security, the entire system is managed by Samsung Knox, a defense-grade security system built into Samsung mobile devices from the chip up, according to Kristin Abbinante, a senior mobile enterprise business manager at Samsung who worked with Magna on the project.
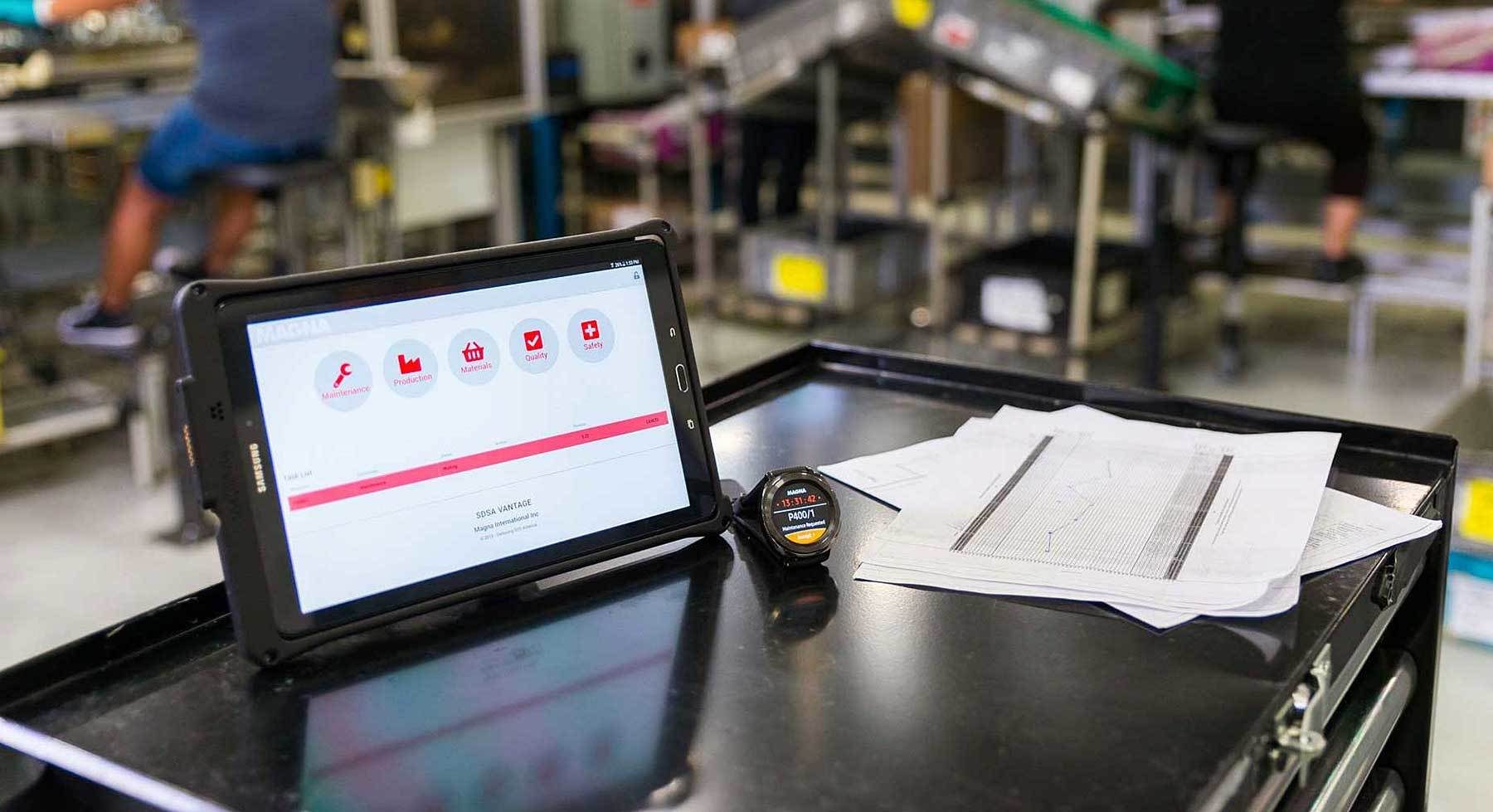
Tablets display key performance indicators from Magna’s assembly lines. Photo courtesy Samsung Electronics
With the use of wearables and tablets on the shop floor, Magna engineers can now envision how to achieve the next steps in their improvement plan, including:
- Going paperless.
- Using analytics in a paperless environment via touch screens.
- Creating more intuitive analytics to guide operations.
- Speeding up the continuous improvement curve over time.
- Achieving more innovation.
The company also notes that the partnership with Samsung was about more than just its products. “We needed the expertise and real-world experience of Samsung’s business solutions and the integration of the technologies it has to create a new level of improvement,” says Kyle Robinson, continuous improvement supervisor at Magna. “This is a key part of this partnership.”
Samsung has provided support to educate plant management on what technology is available and how they can leverage Samsung services to the company’s advantage. “Samsung showed us several use cases outside our industry to start the creative cycle and see if we could change or adapt those to our needs,” Robinson says.
Before implementing the technology, Magna engineers visited Samsung’s product experience centers in the United States and Canada so they could see the technology in use. They were even able to visit Samsung’s Korea-Gumi plant, which operates as a smart factory, to see the potential future state they could achieve.
Samsung technologies, including the Gear S3 smartwatch, have allowed Magna to reap the benefits of wearable technology by improving maintenance personnel response times and gaining plant intelligence that wasn’t previously available. The plant can now further reduce downtime and improve their manufacturing waste through smart factory projects. Additionally, the technology is helping the plant speed up its continuous improvement curve.
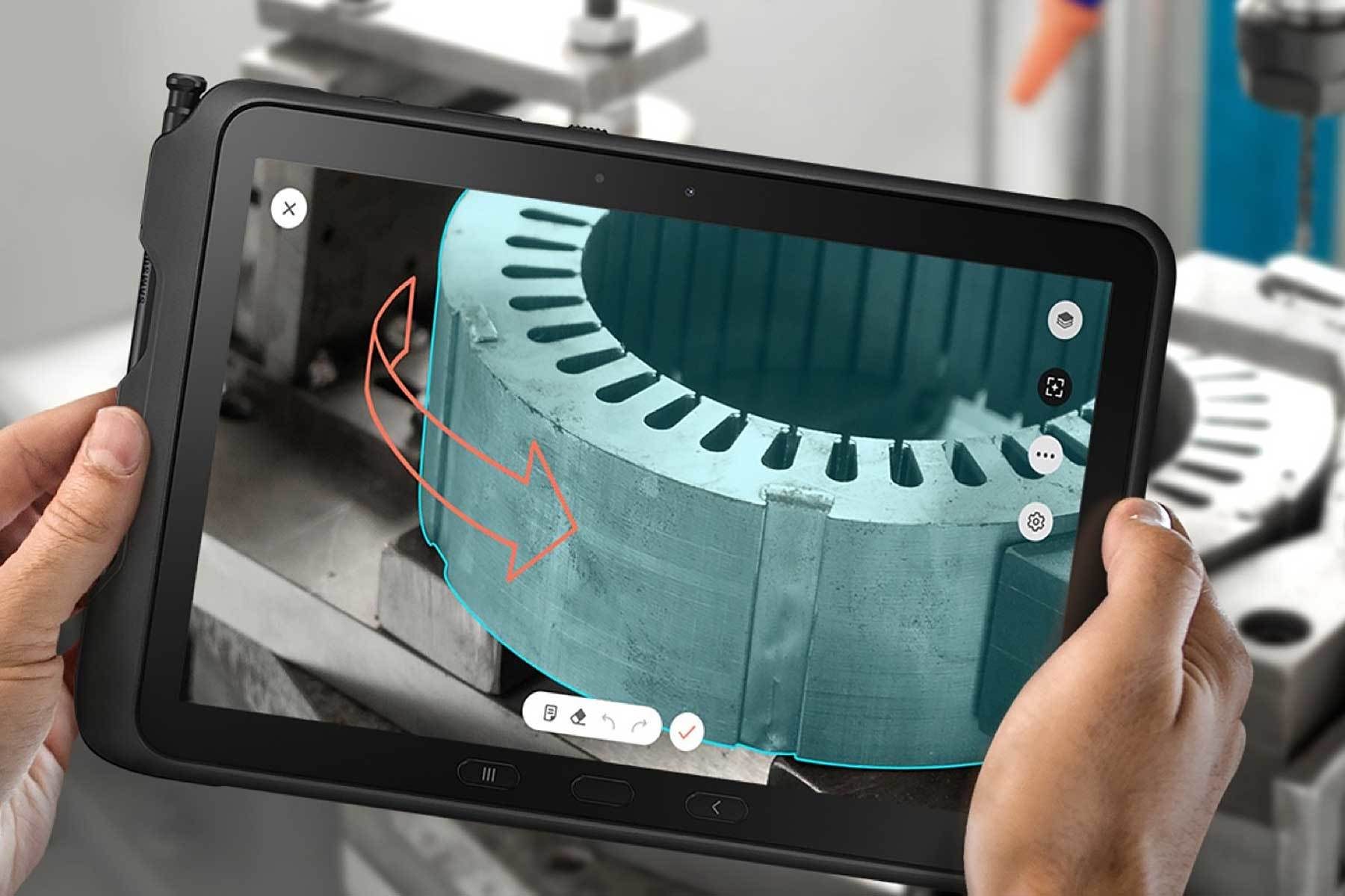
Tablet computers have enabled Magna to create a paperless factory. Photo courtesy Samsung Electronics
Greater Competitive Advantage
To determine the value of improving employee communication, Magna engineers began by calculating the return on investment (ROI) of reducing systemic downtime. According to their calculations, a 15 percent improvement in downtime would save them over $250,000 annually, with a full ROI in less than a year.
Magna also reaped several other benefits, including:
- Faster reaction times to issues. With more data and intelligence coming in via wearables, as well as being more visible by using television screens to display reports and analytics, managers can make better decisions faster. “Going into a paperless environment, you can get all that data, trend it, chart it, understand it and make better reactions and actions coming out of it,” says Charbonneau.
- Continuous improvement and cost savings. The system allows more technology and monitoring on the production floor, which in turn is reducing waste. With better intelligence on the floor, Magna can continuously reduce costs as time goes on.
- Software is deployable across the company. The software being used at the plant can easily be transferred to other Magna divisions and groups. The only cost for implementation would be the capital required to purchase the hardware.
- Baseline for a smart factory. The infrastructure implemented with this system provides the base technology for other smart factory improvement projects and phased improvements.
- Future implementation of emerging technologies. With the success of this project, the company is now launching a virtual reality (VR) application for divisional benchmarking as well as using VR in other areas, such as training and remote troubleshooting. Charbonneau notes that their experience so far with the Samsung technology has allowed the plant “to be more confident in pursuing emerging technology like VR and augmented reality that can be leveraged in many ways.”
Another future project that the plant is working on with Samsung is using facial recognition for their training process. The plan is to use a tablet with facial recognition that will be able to identify and authenticate the operation staff coming to a specific station. “This will allow the company to validate that the right product at the right time is being made with quality in mind,” says Charbonneau.
For more information on mobile computing technology for assembly plants, click here.
ASSEMBLY ONLINE
For more information on ergonomic equipment, visit www.assemblymag.com to read these articles: