ASSEMBLY LINES
Cobots May Ease ‘Baby Boomer Exodus’ in Manufacturing
NEW YORK—As a wave of Baby Boomers reach retirement age during the next five years, collaborative robots will help manufacturers cope with the skills gap. According to ABI Research, demand for cobots will grow 28 percent annually between now and 2030.
“Companies that take a step back will view the demographic shifts as an opportunity to revamp processes and operations,” says Michael Larner, distinguished analyst at ABI Research. “It is not about technology filling former employees’ roles, but how technology augments people’s working lives.
Demand for collaborative robots will grow 28 percent annually between now and 2030. Photo courtesy Universal Robots
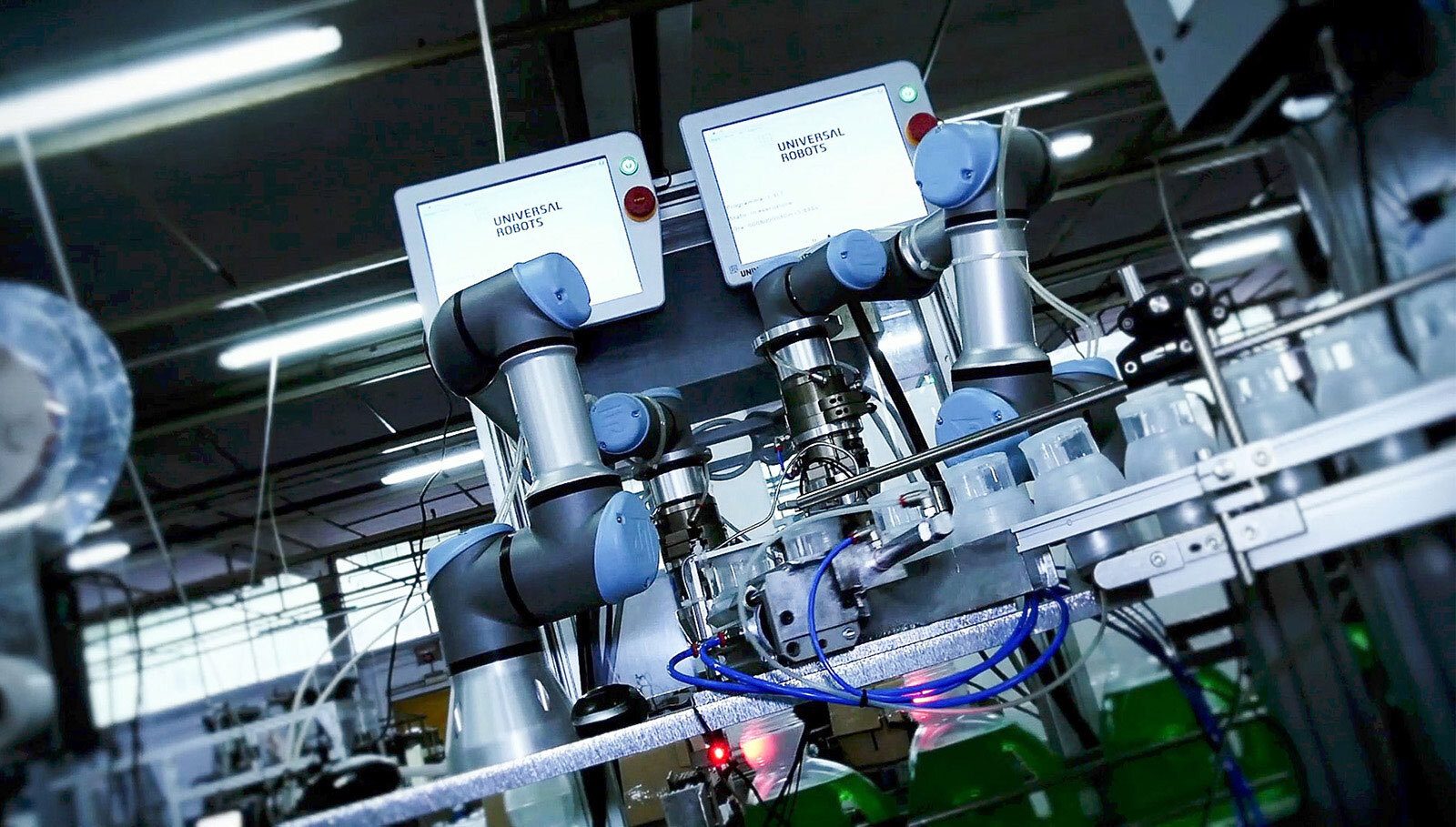
“The nature of manufacturing work will change, with roles for robot programmers and for developing models for machine learning tools coming to the fore,” predicts Larner.
“For manufacturers, one of the biggest concerns with Baby Boomers heading for retirement is the loss of tribal knowledge, such as the detailed knowledge of equipment, processes and customers,” warns Larner, “Manufacturers must capture that tribal knowledge as employees head for retirement as part of a workforce planning strategy.
“Improving mentoring and knowledge sharing processes are just as important as investments in digital technologies for manufacturers to thrive in the coming years,” says Larner.
According to ABI Research, improve safety, lower costs and easier accessibility will drive collaborative robot sales in the near future. In particular, the automotive industry is predicted to pace the market, with cobot shipments growing from 13,000 in 2023 to 115,000 by 2030.
“Cobots are at the forefront of the robotics revolution,” claims George Chowdhury, robotics industry analyst at ABI Research. “They have the potential to democratize automation and bring robots into new markets, working side-by-side with human workers to unlock economic growth.
“Cobots have a synergy with artificial intelligence,” explains Chowdhury. “[Manufacturers] have leveraged the two technologies combined to automate tasks which have, until now, been exclusively reserved for human workers.
"Moreover, the more affordable cost and safety of cobots create an opportunity for small and medium enterprises to adopt robotics, unlocking major productivity advantages for broad sectors of the economy,” Chowdhury points out. “[The machines] can revolutionize industries from medicine to agriculture by augmenting human workers with AI value-adds.”
New Process Automates Electronics Disassembly
MAGDEBURG, Germany—Engineers at the Fraunhofer Institute for Factory Operation and Automation (IFF) here are developing an automated process for electronics recycling. The goal of the Intelligent Disassembly of Electronics for Remanufacturing and Recycling (iDEAR) project is to create a nondestructive robotic method that will invigorate an advanced circular economy that reduces e-waste.
Worldwide annual e-waste generation could rise to as much as 74 million metric tons by 2030. However, only a small fraction of all electronic devices is currently recycled. More than 80 percent of the e-waste generated ends up in landfills or incinerators, including valuable raw materials such as precious metals and rare earths.
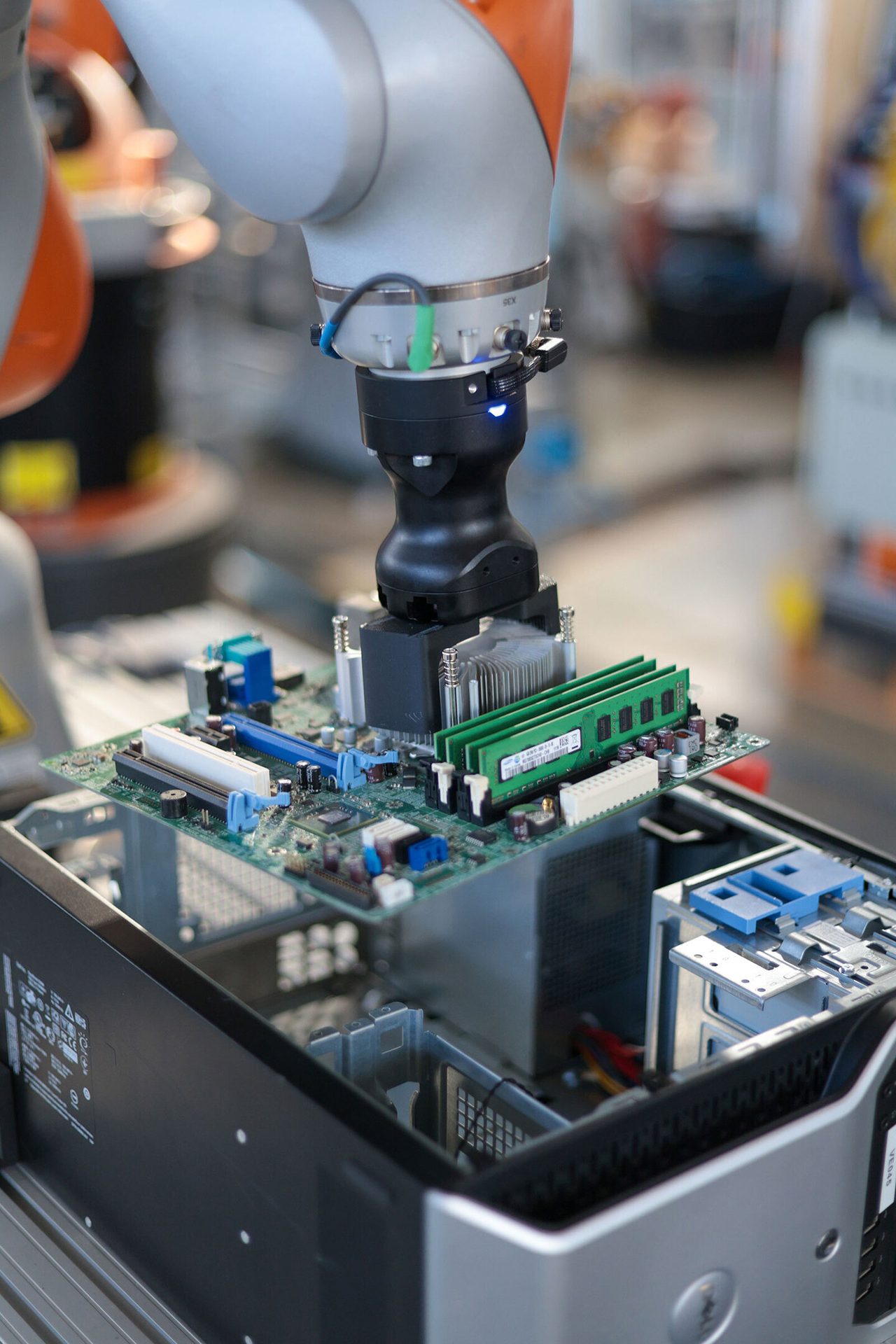
Robots are used to disassemble motherboards and other electronic components used in computers. Photo courtesy Fraunhofer Institute for Factory Operation and Automation
The small percentage of e-waste that undergoes treatment typically gets shredded, while only a limited portion is manually disassembled, cleaned of hazardous substances, broken down mechanically and sorted into different fractions. Manual disassembly entails high costs and is not very effective.
“We intend to revolutionize the disassembly of e waste,” says José Saenz, Ph.D., manager of the assistive, service and industrial robots group at Fraunhofer IFF. “Current solutions require substantial engineering and are limited to a particular product group.
“We are pursuing a data-driven methodology so that a wide variety of products, from computers to home appliances, can be disassembled in real time with little engineering,” explains Saenz.
The engineers are initially focusing on the automated disassembly of computers. However, the system is intended to be upgradeable over time for other types of products, such as dishwashers, microwave ovens and washing machines.
The process of identification and condition analysis uses optical sensor systems and 3D cameras with AI-powered algorithms to detect component types and locations, examine geometries and surfaces, assess the condition of fasteners and detect anomalies.
“Optical metrology helps scan labels and sort different parts, such as screws,” says Saenz. “Previously trained machine learning algorithms and AI interpret the image data, and enable the identification and classification of materials, plastics and components in real time based on sensor and spectral data.”
For instance, AI detects whether a screw is concealed or rusted. All the data is stored in a digital disassembly twin.
In the next step, Saenz and his colleagues define the disassembly sequence so that their software can determine whether to execute a complete disassembly or only focus on the recovery of specific, valuable components.
However, glued or otherwise mated components hinder nondestructive disassembly. Rusty or stripped screws, or deformed components, are not ideal either.
The disassembly process starts based on this high-level information. A robot receives a series of instructions and operations to complete, such as “remove two screws on the left of the housing.”
The skills specified in the disassembly sequences include robot actions, such as screwing, lifting, cutting, extracting, localizing, repositioning, releasing, moving levers, bending, breaking and cutting wires. According to Saenz, the disassembly robot can perform all of those tasks completely autonomously.
“The demonstrator even succeeded in tests to remove a motherboard from a computer—a very complex task that requires a high level of precision,” explains Saenz. “We used AI for that.”
American Manufacturers Face Risk of Severe Labor Shortage
WASHINGTON—According to a recent report from Deloitte and the Manufacturing Institute, almost 2 million U.S. manufacturing jobs could be left unfilled within the next 10 years. The severe shortage caused by a skills gap and tight labor market underscores the dire need for employee-focused strategies to keep up with growth.
Workforce challenges are among the top concerns currently facing American manufacturers in all industries. The report warns that as many as 3.8 million additional employees could be needed in the manufacturing sector between now and 2033.
“Manufacturers recognize that the workforce is evolving,” says Carolyn Lee, executive director of the Manufacturing Institute. “Pandemic-driven shifts have already created hundreds of thousands of new jobs, and now we are seeing increased demand for digital skills that need to be met or risk further widening of the talent gap.
Almost 2 million U.S. manufacturing jobs could be left unfilled within the next 10 years. Photo courtesy GE Vernova
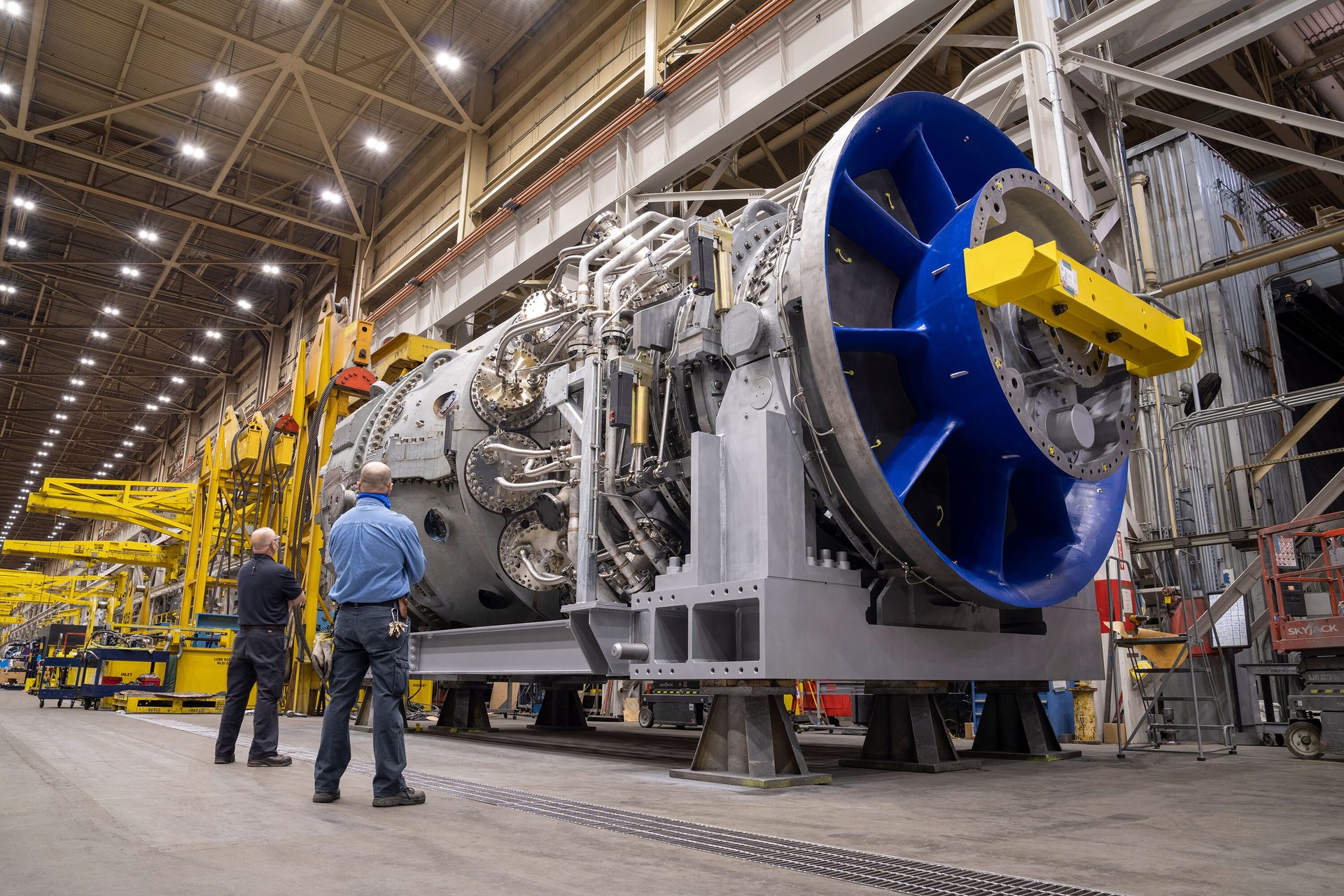
“Companies must prioritize technology, training and talent development, and the investments that are driving growth will also require the industry to build out a talent ecosystem,” explains Lee. “With investments in partnerships, apprenticeships and education, and prioritizing a more diverse and inclusive workforce, a whole host of new talent will be on the factory floor and driving the next wave of growth.”
Lee claims that 1.9 million jobs could remain unfilled if manufacturers are not able to address the skills and applicant gaps. In addition to upskilling the existing workforce through training, technology and policies that meet employee expectations, manufacturers must create strategies to increase existing employee retention.
“As retiring Baby Boomers are replaced by incoming millennials and Gen Z workers, [companies] should invest in strategies aligned with workforce expectations, including more flexibility,” says Lee. “Options include work arrangements such as flexible shifts, shift swapping and split shifts.”
AI and Humanoids Are Top Robotic Trends in 2025
FRANKFURT—According to the International Federation of Robotics, artificial intelligence and humanoid technology are the top two trends affecting the automation industry in 2025.
By leveraging diverse AI technologies, robotics can perform a wide range of tasks more efficiently. For instance, analytical AI enables robots to process and analyze large amounts of data collected by their sensors.
This helps to manage variability and unpredictability in the external environment, in high-mix, low-volume production, as well as in public environments. Robots equipped with vision systems, for example, can analyze past tasks to identify patterns and optimize their operations for greater accuracy and speed.
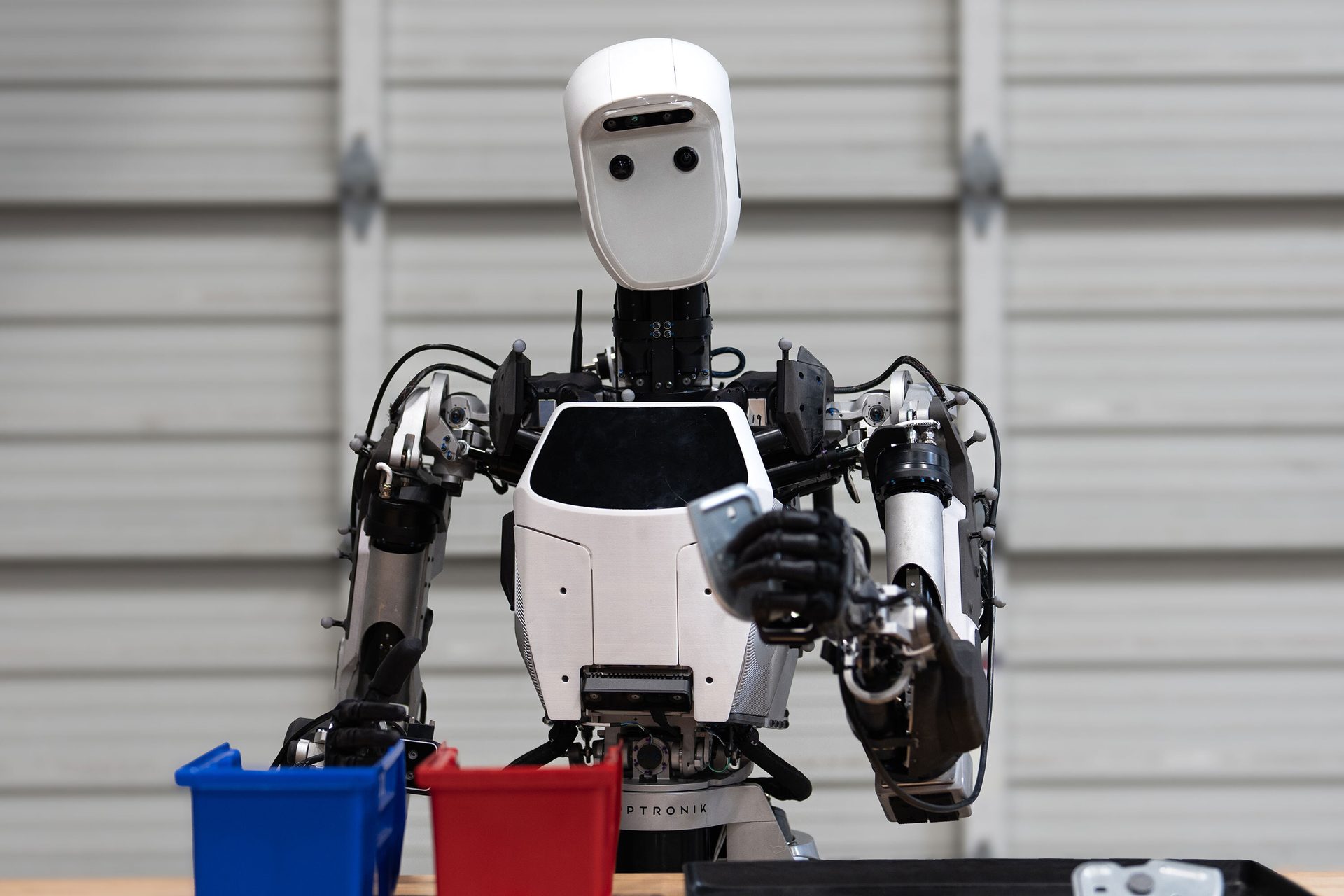
Engineers around the world are focusing their attention on humanoids and other types of general-purpose robots. Photo courtesy Apptronik
Robot and chip manufacturers are investing in the development of dedicated hardware and software that simulate real-world environments. This Physical AI allows robots to train themselves in virtual environments and operate by experience, rather than programming.
These generative AI projects aim to create a “ChatGPT moment” for physical AI. This simulation technology is expected to advance in both traditional industrial robot environments, as well as in service robot applications.
Robots in the shape of human bodies are also receiving a lot of attention. The goal is to create bipedal machines that can perform general-purpose tasks such as loading a dishwasher on their own or working independently on an assembly line.
Many manufacturers are currently focusing on humanoids that only perform single-purpose tasks. Most of these projects are being carried out in the automotive industry and the warehousing sector.
The challenges is to determine if and how humanoid robots can make an economically viable and scalable business case for industrial applications, especially when compared to existing options such as cobots.