ASSEMBLY LINES
Factories Get ‘Smarter,’ But Manufacturers Are Slow to Invest
WASHINGTON—Manufacturing is marching toward a future that is highly automated, intelligent and flexible. Increasingly, “smart factories” are made up of connected machines that generate large amounts of data.
Growing use of artificial intelligence and data analytics technology create new ways for manufacturers to improve production processes, product quality and supply chains. However, realizing the benefits of this Industry 4.0 digital transformation can be difficult for many manufacturers. That’s because not all organizations have the resources, capital or talent required to deploy smart factories.
To discover how companies are progressing on this journey and the challenges they face, the National Association of Manufacturers (NAM) recently conducted a survey under the auspices of its Manufacturing Leadership Council.
Manufacturers are committed to new tools and technology. According to NAM, they are spending at a steady—and in some cases growing—basis. Nearly 69 percent of survey respondents said their investments in 2024 would continue unchanged from last year.
Growing use of artificial intelligence and data analysis technology create new ways for manufacturers to improve production processes, product quality and supply chains. Illustration courtesy National Association of Manufacturers
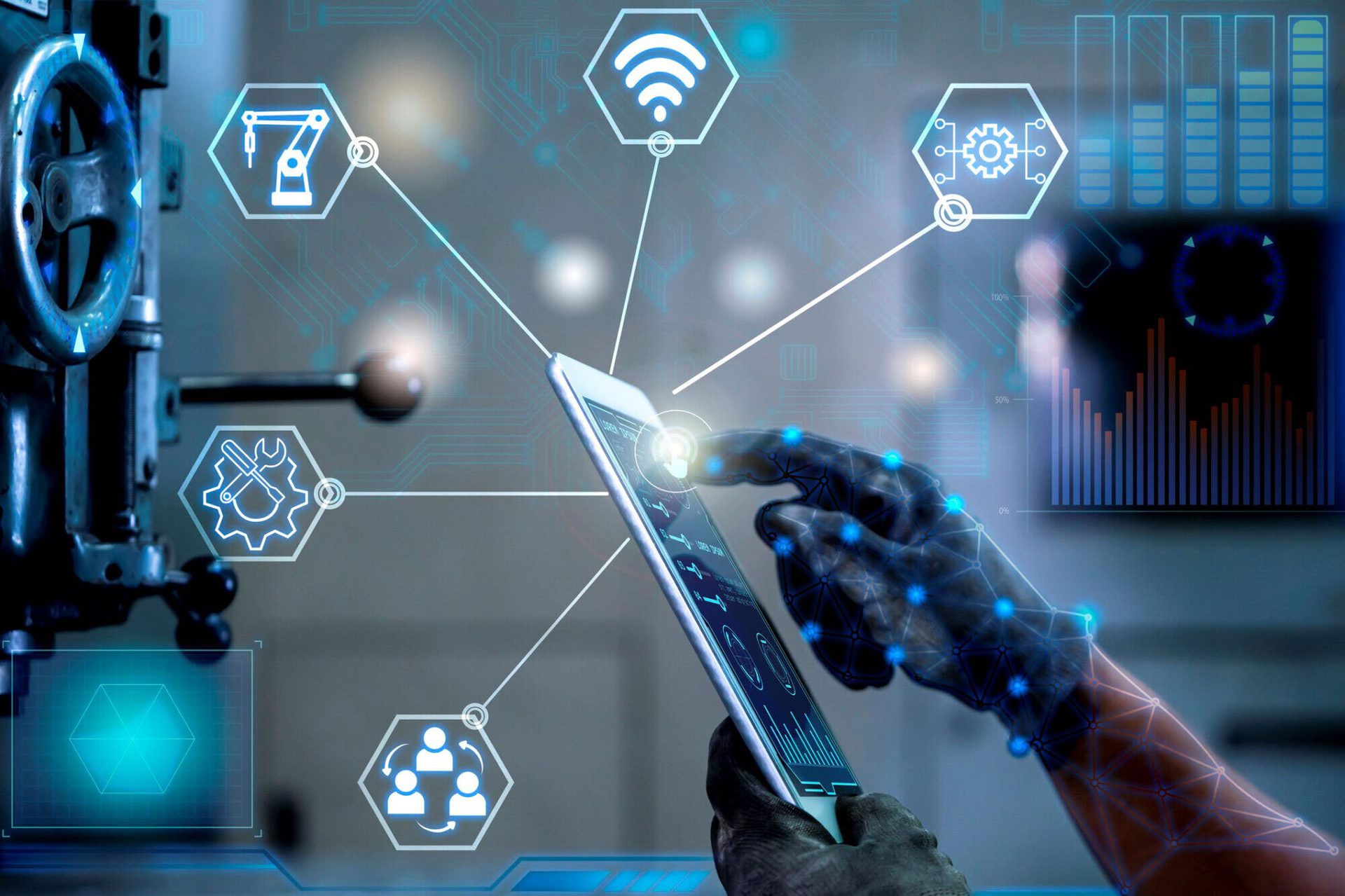
More than one half (58 percent) assessed their company’s digital maturity level in manufacturing operations at three to five on a scale of 10, suggesting the industry has moved beyond the initial stages of Industry 4.0 and has reached an early majority of digital-model adoption.
However, only 7 percent of manufacturers claim they have digitized their factory operations extensively. Approximately 15 percent expect to have their manufacturing operations digitized end-to-end by 2026.
Only 5 percent claim their factories are already “very smart,” while 53 percent believe their facilities are getting smarter, but are still works in progress.
While some manufacturers foresee a future of “lights out” factories, or those that mostly run themselves, most don’t think they will ever reach that state. Indeed, 49 percent of respondents expect fully or partially autonomous factories in the future.
Approximately 56 percent cite organizational resistance to change as the top barrier to implementing a smart factory. But, more than one-third of respondents (40 percent) predict that AI will be either very significant or somewhat significant in the years to come.
Automotive Suppliers Need to Adopt More Automation to Survive
ZURICH—Automation and robotics are crucial to the future of the automotive industry, claims a recent study conducted by ABB Robotics and Automotive Manufacturing Solutions (AMS). New OEMs and start-ups are leading the charge, while suppliers are lagging behind. Many companies are not yet reaping the benefits offered by digitalization.
Almost all respondents (97 percent) believe that automation and robotics will transform the automotive industry over the next five years, with a similar number (96 percent) predicting that software, digitalization and data management will be equally significant.
When asked about the pace of investment, most believe that start-ups were well ahead of the curve, investing “very well” (38 percent), followed by legacy automakers (31 percent).
However, only 7 percent of respondents believe that Tier 2 suppliers are making necessary investments, with Tier 3 suppliers even further behind.
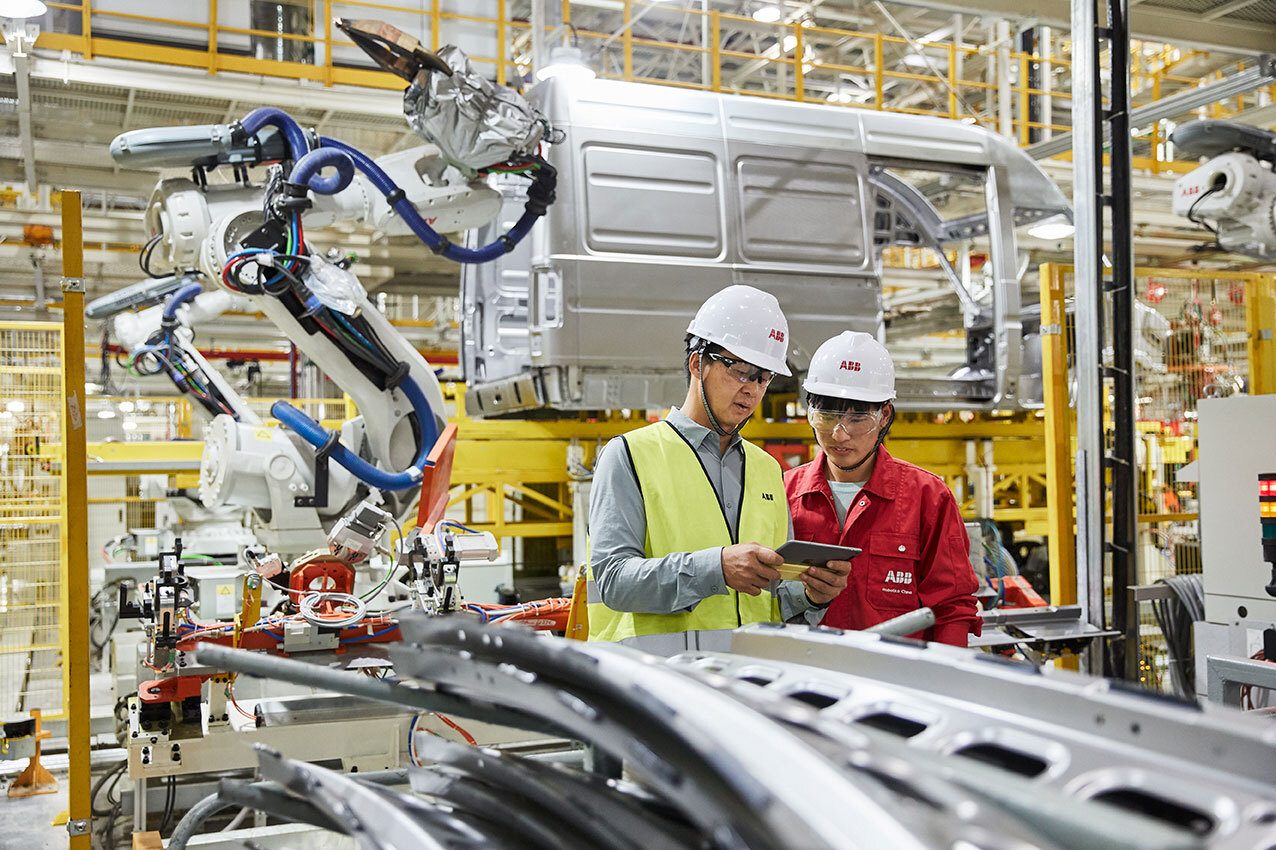
Smaller automotive suppliers need to step up their investments in automation and robotics. Photo courtesy ABB Robotics
“Automation has traditionally been seen as the preserve of only the very largest manufacturers,” says Joerg Reger, managing director of ABB Robotics' Automotive Business Line. “But, the reality is that [robots] can address the challenges faced by even the smallest producers. Automation can make smaller companies more resilient, flexible and efficient.”
“While both new and established manufacturers are making key investments, the essential upstream supply chain supporting them is not moving as quickly,” warns Daniel Harrison, an analyst at AMS. “This could prove problematic in terms of costs, and also the speed new and increasingly complex components for EVs and connected cars are delivered to the factory. Affordable and practical automation and robotics need to be available to the entire industry.”
Generative AI and Digital Twins Will Drive the Future of Manufacturing
TORONTO—Integrating generative artificial intelligence with digital twin technology will transform the manufacturing industry, according to a recent report by Info-Tech Research Group.
“Digital twins have long been recognized for their potential to revolutionize predictive maintenance and streamline processes,” says Shreyas Shukla, principal research director at Info-Tech Research Group. “When combined with generative AI, the possibilities for the manufacturing industry expand exponentially.
“However, many manufacturers worldwide continue to grapple with the challenges of Industry 4.0 and the remnants of pandemic-era supply chain disruptions,” claims Shukla. “The fusion of Gen AI and digital twins promises not only to optimize current manufacturing processes, but also to usher in a new era of design, simulation and real-time predictive analysis."
Integrating generative artificial intelligence with digital twin technology will transform the manufacturing industry. Illustration courtesy Info-Tech Research Group
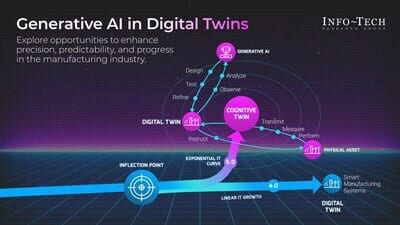
According to Shukla, AI will play a significant role in manufacturing over the next decade, potentially outpacing the impact of automation in the past. He believes that manufacturers prioritizing AI investments now can significantly expand their offerings and capabilities, leading to increased market presence, revenue growth and improved customer satisfaction. This strategic move is seen as crucial for staying competitive.
The transformative potential of integrating Gen AI with digital twins indicates how this combination can propel manufacturers from reactive to proactive modes of operation. “This shift can help organizations achieve greater efficiency, sustainability and resilience in the hyper-competitive and constantly changing global market,” says Shukla.
Info-Tech’s report identifies several obstacles facing the manufacturing sector, including the significant compatibility of integrating new technologies with existing systems. It also reveals there is a lack of skilled professionals who are well-versed in both the manufacturing industry and advanced technologies, including AI.
However, Shukla points out that there’s a pressing need for a comprehensive understanding and ethical use of AI to ensure integrity in decision-making processes within manufacturing operations.
Delta Robot Pioneers Receive Engelberger Award
ANN ARBOR, MI—The two engineers who created the delta robot are the “technology” category recipients of the 2024 Joseph F. Engelberger Robotics Awards sponsored by the Association for Advancing Automation (A3).
Reymond Clavel, Ph.D., professor emeritus of mechanical engineering at Ecole Polytechnique Fédérale Lausanne (the Swiss Federal Institute of Technology) was selected for his pioneering role in the invention of the delta robot concept in the early 1980s. Marc-Olivier Demaurex, Ph.D., president of Demaurex SA, a Swiss packaging company, was cited for his role in bringing the machine to market in the late 1980s.
Delta robots enabled manufacturers to achieve much higher productivity rates than ever before, due to their increased speed and throughput. Each arm of a delta robot is driven by a motor mounted in a stationary base above a large cylindrical work envelope. The arm joints work together to drive a rotary axis connected to an end-effector.
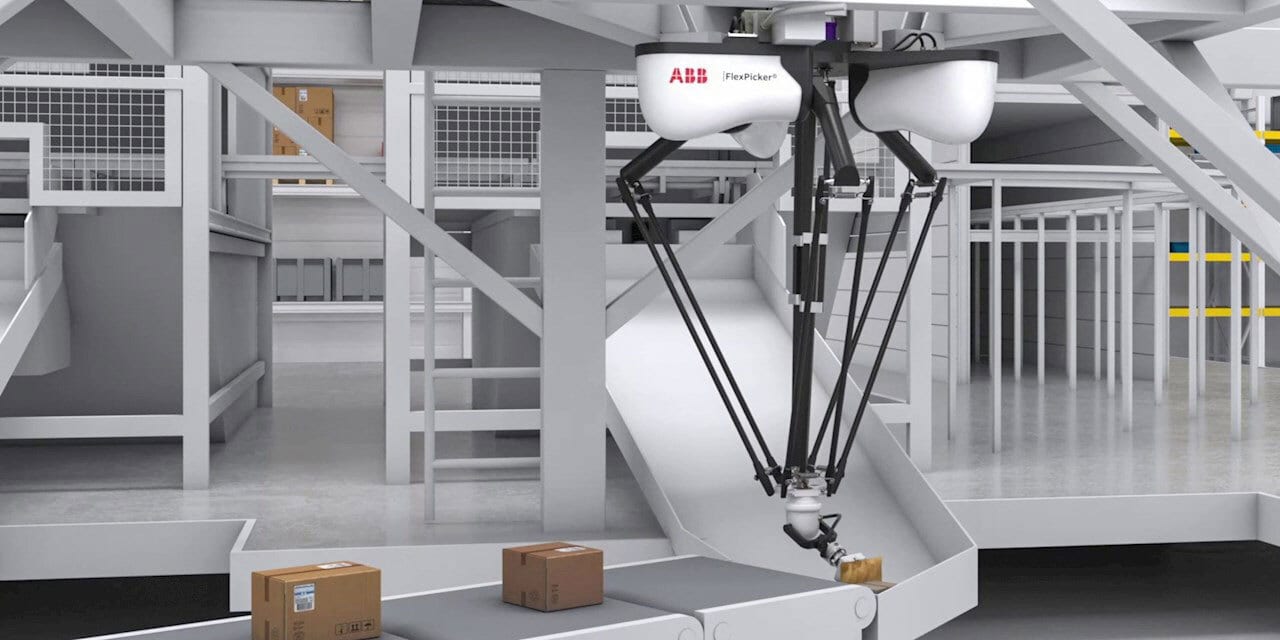
Delta robots enabled manufacturers to achieve much higher productivity rates than ever before, due to their increased speed and throughput. Photo courtesy ABB Robotics
The extremely fast machines were originally designed for low-payload applications, such as food and cosmetics packaging. However, delta robots are also used for some assembly applications today, such as adhesive dispensing, kitting, labeling, parts insertion, pick-and-place, polishing, screwdriving and soldering. They are used to mass-produce batteries, circuit breakers, electronics, medical devices, pens, semiconductors, solar panels and other products.
In the early 1980s, Clavel led the research team that invented the delta robot, which was patented in 1985. In 1987, Demaurex purchased a license for the new design and started to produce delta robots for the packaging industry.
“Who would have thought that a visit to a chocolate factory would result in a robot concept that is not only used worldwide, but is actually studied in universities, and now further recognized with this prestigious Engelberger Award,” says Clavel. “I’m beyond proud that we were able to create a real solution to a problem that so many dealt with as they looked to automate complex piece picking applications and the influence these parallel robots have on today’s robots.”
“Being recognized with an Engelberger Award for my pioneering role in the delta robot concept is definitely a highlight of my career,” adds Demaurex. “We recognized early on that the delta robot…was the solution to problems companies in the packaging industry had long encountered when considering automation. By bringing it to market with early adopters such as Nestlé and Kambly, we created a company—and an industry—that is still going strong today.”