ASSEMBLY LINES
Robotic Swarms Will Assemble Large Aerospace Structures
SANTA BARBARA, CA—Using automation in aerospace manufacturing applications has traditionally been difficult. But, a start-up company believes it has found an answer. H2 Clipper Inc. plans to deploy autonomous and semi-autonomous robotic swarms to assemble its rigid airship.
The 1,000-foot-long hydrogen-powered vehicle will be capable of economically transporting heavy payloads up to 340,000 pounds over long distances. The company claims that its airship will be 70 percent less expensive than traditional air freight.
The airship has an aerodynamic shape that gives it a top speed of 175 mph and a range of 6,000 miles. Electric motors will drive five propellers. A triangular-shaped exoskeleton hull made of lightweight carbon fiber composite materials gives the 150-foot diameter airship a rigid shape and eliminates the need for bulky internal braces and supports.
Robotic swarms will be deployed to assemble a large airship for cargo transport applications. Illustration courtesy H2 Clipper Inc.
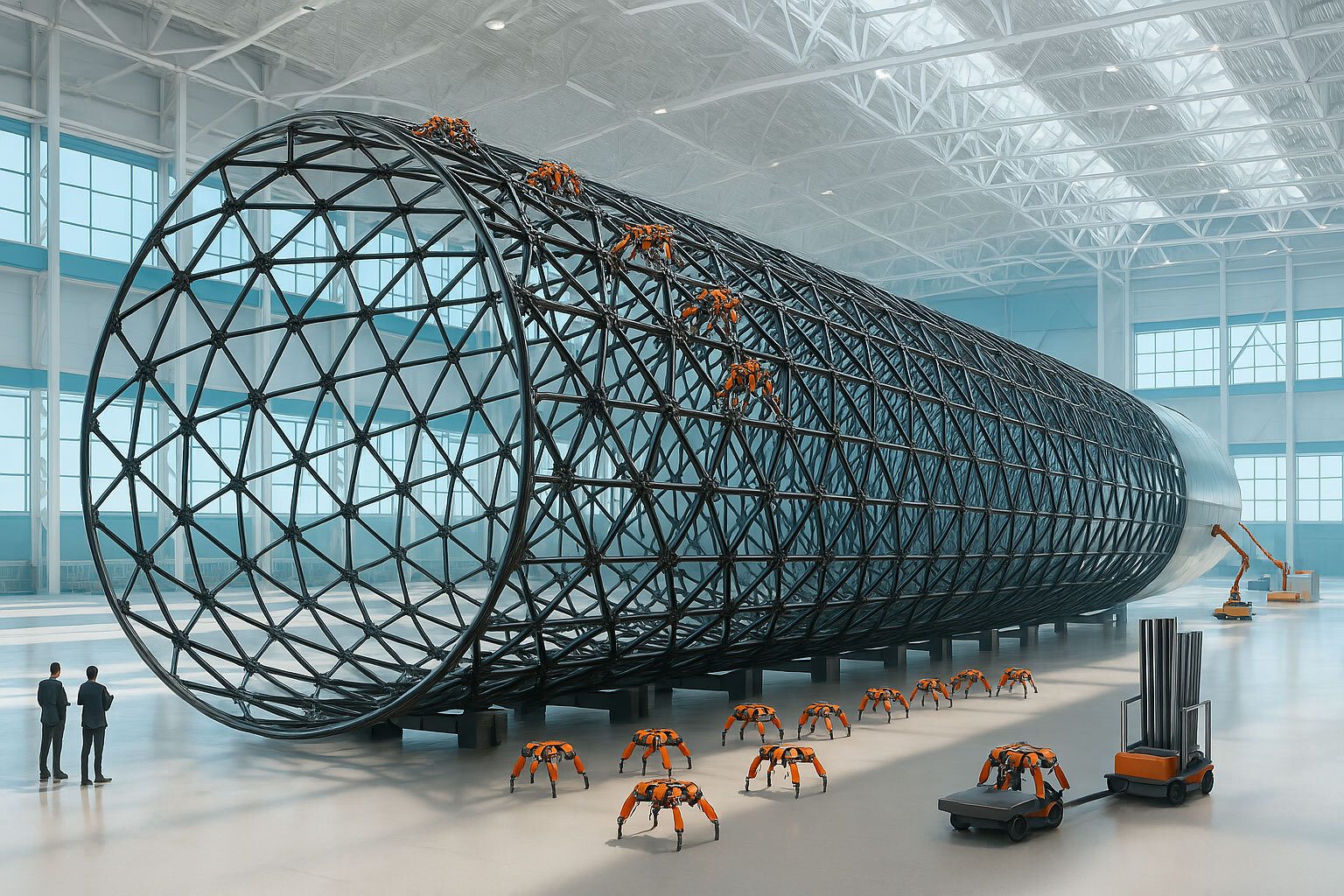
," Separately fabricated nose and tail cones will attach to the exoskeleton. The airship’s external skin will be made from a fire-resistant and flame-retardant material.
H2 Clipper recently received a U.S. patent for the use of swarm robotics in large-scale aerospace manufacturing “to assist in assembling the frame, attaching the skin and performing other tasks in manufacturing an airship, and constructing other structures that are otherwise challenging, inefficient or unsuitable for humans to perform, or that traditionally require significant investments in capital intensive manufacturing facilities.”
“The issuance of this patent marks a pivotal moment in the evolution of aerospace and aviation manufacturing,” claims Rinaldo Brutoco, CEO of H2 Clipper. “By replacing traditional assembly lines with robotic swarms, this breakthrough enables aircraft and large aerospace assets to be built faster, at a significantly lower cost, and with far greater precision.
“Conservative estimates based on current aerospace production benchmarks suggest this approach can reduce total manufacturing costs by 40 percent or more, and cut production time by up to 60 percent, while simultaneously improving quality,” says Brutoco.
According to Brutoco, the innovation enables “unparalleled precision and continuous round-the-clock autonomous production.” He says it offers numerous benefits, including:
• Automated manufacturing. Robots work in a coordinated swarm to assemble airframes, attach the exterior skin, install structural and internal components, perform bonding and fastening operations, conduct in-process quality inspections, and carry-out other complex, high-precision assembly tasks.
• AI-driven optimization. Machine learning and generative AI guide the robotic swarm to self-correct, improve manufacturing precision, reduce errors and optimize construction timelines.
• Scalability and safety. The system uses built-in sensors and AI-driven oversight to safely manage all operations, assuring collision-free operation and eliminating the need for people to operate at dangerous heights. With no fixed assembly line or gantries required, manufacturing can be supervised remotely and scaled across multiple locations.
• Heavy-lift robotics integration. The technology enables large-scale structures to be constructed entirely in place—horizontally or vertically—using autonomous robots capable of repositioning and aligning major components. This flexibility supports multiple assembly approaches, while reducing infrastructure requirements and improving safety.
“Whereas traditionally, aircraft must be moved through multiple stages, requiring massive facilities, complex scheduling and high logistical overhead, [our airships will be] built in place, eliminating costly movement, saving time, and reducing the need for assembly line infrastructure," says Brutoco.
Brutoco believes that swarm robotics could be used to build other types of aerospace structures, such as aircraft fuselages. He plans to assemble a team of manufacturing experts to develop a technology roadmap that would support potential licensing to various OEMs.
“This patent represents a game-changing moment for aerospace manufacturing—a shift as significant as the invention of the assembly line itself,” claims Brutoco. “Swarm robotics gives OEMs the ability to build aircraft and spacecraft smarter, faster and more affordably than ever before, opening the door to a new era in aviation and the future of flight.”
Mercedes-Benz Deploys Humanoids at Berlin Assembly Plant
BERLIN—Mercedes-Benz’s oldest factory, which was built in the late 1800s, has deployed some of the most advanced manufacturing technology in the world, including artificial intelligence and humanoid robots. The Marienfelde plant produces power train components, such as EV traction motors.
“Mercedes-Benz Berlin-Marienfelde remains at the cutting edge of automotive production and keeps Germany on the map as a global center for innovation,” says Jörg Burzer, member of the board of management responsible for production, quality and supply chain management at Mercedes-Benz Group AG. “Artificial intelligence and humanoid robots open up an exciting new frontier which make automotive production more sustainable, efficient and more intelligent.”
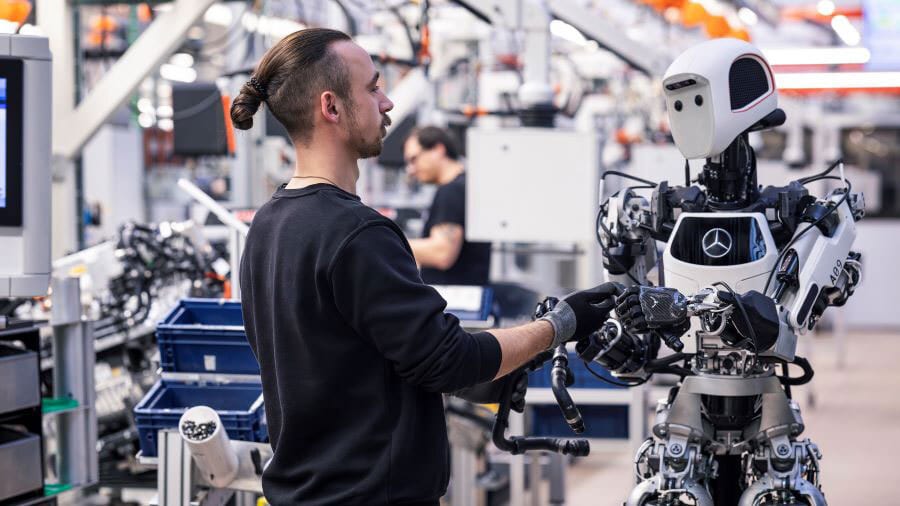
Mercedes-Benz has deployed humanoid robots at its Berlin power train assembly plant. Photo courtesy Mercedes-Benz AG
According to Burzer, Mercedes-Benz is currently using Apptronik Inc.’s Apollo robot for material handling applications. The humanoid performs “repetitive tasks within intralogistics…to transport components or modules to the production line for [human operators] to assemble, and to carry out initial quality checks of components.”
Apollo robots have been collecting data in a production environment to train for specific use cases within MO360 (Mercedes-Benz Cars Operations 360 digital production ecosystem), which contains all the important software applications and data of the automaker’s global production network.
“Mercedes-Benz employees with real-life production know-how have transferred their knowledge to Apollo using teleoperation processes and augmented reality,” explains Burzer. “[We are] now taking the next decisive development step at the Digital Factory Campus Berlin, enabling Apollo robots to perform autonomous operations, a technological milestone on the way to a flexible, intelligent assistance system for production.”
Mercedes-Benz has also invested in Apptronik. “[We are] relentlessly focused on pushing the boundaries of what’s possible in automotive innovation—not only in the cars we design, but in how we build them,” says Burzer. “Our work with Apptronik has given us a front-row seat to the incredible pace of progress in humanoid robotics and AI, and the transformative potential these technologies hold for modern manufacturing.
“We are proud to support Apptronik as they pioneer new ways to bring intelligent, adaptable robots onto the factory floor—helping us set new benchmarks for efficiency, safety and collaboration between people and machines,” adds Burzer.
A3 Calls for a National Robotics Strategy
WASHINGTON— The Association for Advancing Automation (A3) has issued a national robotics strategy that would enable the United States to maintain its leadership role in robotics and automation. It outlined key policy priorities, including establishing a central robotics office and robotics commission, to strengthen U.S. competitiveness in robotics, drive innovation and support workforce development.
The strategy aims to foster economic growth, enhance national security and ensure that the U.S. remains a leader in robotics-driven innovation.
“The United States is at a critical moment in shaping the future of automation,” says Jeff Burnstein, president of A3. “While AI is a major focus, we cannot afford to fall behind in robotics. Our vision for a national strategy provides a roadmap for strengthening U.S. competitiveness, innovation and workforce readiness.”
Burnstein’s organization recommends six key policy priorities to drive U.S. leadership in robotics:
A national robotics strategy would enable the United States to maintain its leadership role in advanced automation. Photo courtesy ABB Robotics
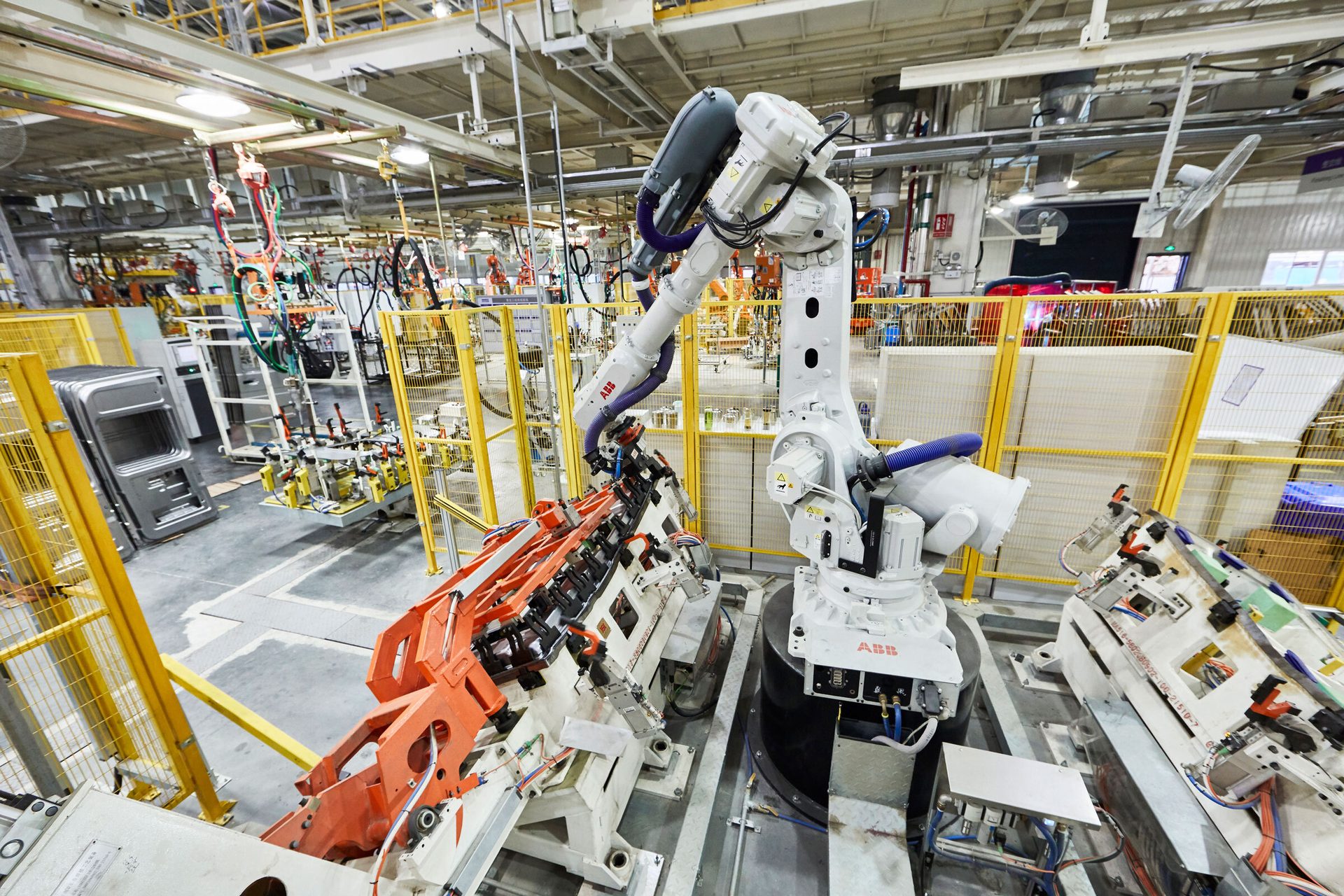
• Establish a central government robotics office and a robotics commission. The dedicated federal organization would coordinate robotics policy, innovation and industry collaboration, along with a commission of appointed industry and academic leaders to formulate policy recommendations to assert U.S. leadership in robotics, and bolster economic and national security.
• Implement tax incentives to drive adoption. Tax credits and incentives would accelerate robotics investment and innovation.
• Government as a leading adopter. Federal agencies would be encouraged to integrate robotics into their operations, setting an example for industry.
• Expand workforce training programs. Investing in STEM education and upskilling programs would prepare American workers for automation-driven industries.
• Fund academic research and commercial innovation. Strengthening public-private partnerships would drive automation technology breakthrough and robotic advancements.
• Develop new industry standards. Modernizing standards would support safe and effective AI-powered robotics deployment.
“With recent advances, including the rapid integration of AI functionality, robots are becoming increasingly capable and essential in industries that will face worker shortages due to demographics,” says Brendan Schulman, chairman of the A3 advocacy committee and vice president of policy and government relations at Boston Dynamics Inc. “It is urgent for government leaders to launch a national robotics strategy….”
Quantum Computing Streamlines Auto Assembly Line
PALO ALTO, CA—Quantum computing promises to be the next big leap in technology, enabling next-generation applications in artificial intelligence, smart manufacturing and supercomputers. It can manage calculations too complicated for traditional machines.
Ford Otosan, a joint-venture between Ford Motor Co. and Koç Holding, recently deployed quantum computing at its assembly plant in Gölcük, Turkey, to streamline vehicle sequencing operations.
The technology was supplied by D-Wave Quantum Systems Inc. It has improved production of Ford Transit vans, which have more than 1,500 variants. This model variability presents manufacturing efficiency challenges, because producing identical products consecutively is significantly more productive than frequently adjusting for custom specifications. Sequencing requires maximizing throughput and adhering to physical and workforce constraints of the body shop, paint shop and final assembly line.
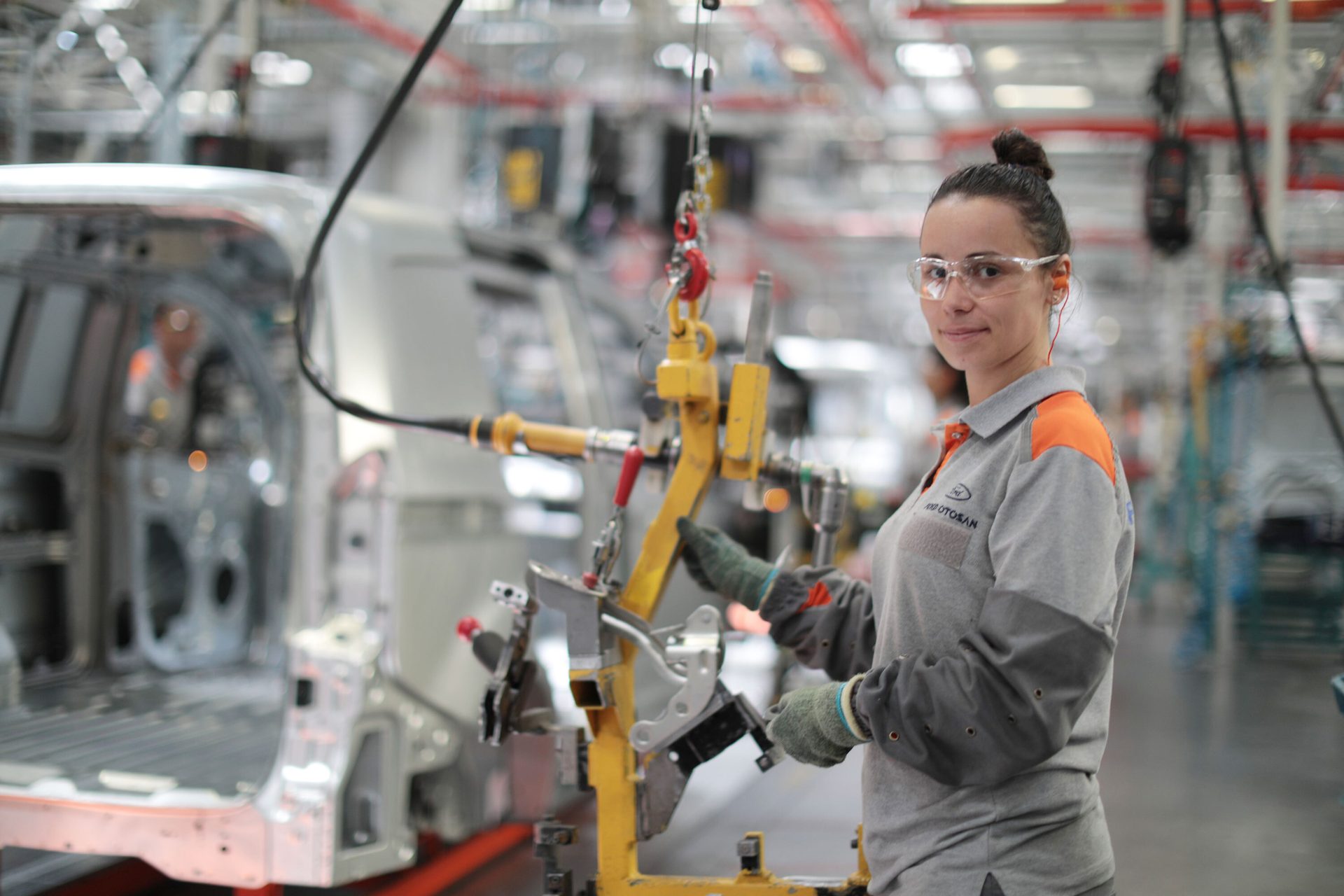
Ford Otosan has deployed quantum computing to streamline vehicle sequencing operations. Photo courtesy Ford Otosan
Ford Otosan reduced the scheduling time of 1,000 vehicles per run from 30 minutes to less than five. The technology also provided more flexibility to adapt to changes in demand or auto part availability, maintaining productivity without disruption.
“It is imperative that [we] maintain the highest standards of production processes and efficiencies to meet customer demand,” says Ziya Dalkılıç, a data scientist at Ford Otosan. “Working with D-Wave’s technology, we’ve deployed a quantum optimization application that goes beyond what we were able to achieve with a purely classical computing approach.”
“Production scheduling demands meticulous planning and agile responses, and classical computing methods can often struggle to keep up with the manufacturing industry’s growing scale and complexity,” adds Alan Baratz, Ph.D., CEO of D-Wave. “For manufacturers on the leading-edge of innovation, such as Ford Otosan, quantum computing technology has proven capable of finding better solutions to complex, real-world problems than classical computing alone. We’re thrilled to see this application move into production and help Ford Otosan realize the powerful benefits of quantum.”
By reducing workload imbalances, Ford Otosan aims to minimize the frequency of unplanned maintenance, ensuring a more stable production process. Optimizing longer schedules can also help mitigate supplier uncertainties and reduce delays.