Manufacturing History
Labor shortages are driving new demand for automation.
Options for Screwfeeding
Caterpillar embarked on a lean manufacturing and Six Sigma initiative in 2001 to strengthen operating efficiency, improve quality and reduce waste. Photo courtesy RedViking
Competitive market pressures forced Cat to adopt new technology and implement lean manufacturing processes.
Caterpillar —
A Bold New Era
Austin Weber // Senior Editor // webera@bnpmedia.com
The 1970s was a time of change for Caterpillar Tractor Co. and other big American manufacturers. In addition to bell bottoms, disco, gas rationing and sideburns, the era was defined by new laws and government regulations, increased globalization and foreign competition, and new types of automation ranging from computers to robots.
For most of the 20th century, Caterpillar faced competition from companies such as Allis-Chalmers, General Motors (Euclid), International Harvester, LeTourneau-Westinghouse and White Motor Co. (Cletrac). However, as those firms succumbed to market pressures and industry consolidation, Cat enjoyed a near monopoly in the global construction equipment sector.
By 1973, Caterpillar was the fourth largest exporter of manufactured goods in the United States, exceeded only by General Motors, Ford Motor Co. and General Electric. It dominated the “yellow iron” industry and produced a broader line of products than anyone else.
“For decades, Peoria, IL-based Caterpillar was as invincible as the mammoth yellow earthmoving machines it produced,” noted an article in the Dec. 19, 1988, issue of Fortune magazine. “Like a D10 tractor…Cat could push, crush or roll over just about anything that got in its way. Competitors were too weak to be taken seriously.
“Customers were willing to pay fat premiums for Caterpillar quality and service. And workers, though periodically restive, could always be bought off with higher wages. With 50 consecutive years of profits and returns on shareholders’ equity as high as 27 percent, Caterpillar was king of the mountain.”
Caterpillar’s assembly lines were well-oiled machines that hummed with efficiency. “Unlike Detroit, we don’t have to stop our production lines to make a change,” Manufacturing Vice President William Naumann told Forbes magazine. “Even when we phase out an old model, the new one goes right in behind it because of the close relationship of our products.
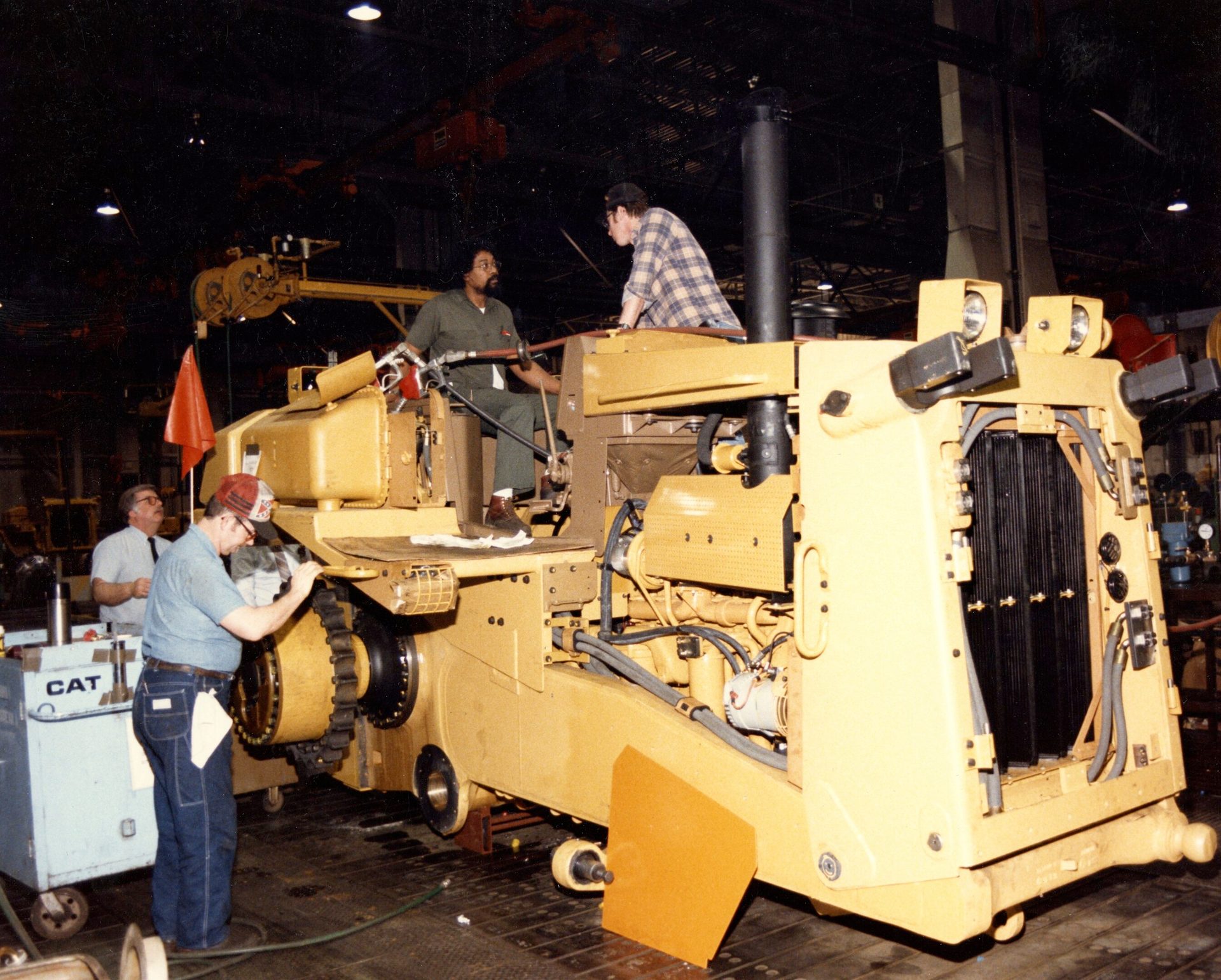
Assemblers work on a tractor at Caterpillar’s East Peoria plant in 1998. Photo courtesy Caterpillar Inc.
“The interrelation of our parts also makes it possible for us to assemble several different machines—a tractor, a scraper, a loader—one behind the other on the same production line. As they move along, machines are fitted with any attachments specified by the customer’s orders.”
During the 1970s, Caterpillar was not content to sit on its laurels and continued to pour money into R&D. Those investments paid off with two major product launches. One was a new line of hydraulic excavators in 1972. The other occurred six years later when elevated drive sprocket technology debuted on the D10 tractor.
Hydraulic excavators were developed in Europe and Japan in the 1950s and 1960s, but were slow to catch on with American manufacturers. In fact, Caterpillar was “badly behind the curve in excavator technology until it launched the 200-Series,” says William Haycraft, a retired Caterpillar marketing executive and author of Yellow Steel: The Story of the Earthmoving Equipment Industry.
Caterpillar’s other big innovation, the hi-drive system, raised the drive sprocket on crawler tractors and added a rear idler, which enabled the track to move around three points instead of two. It improved serviceability, in addition to ground contact and performance.
“It was a gutsy move for Caterpillar, considering that its conventional machines already dominated the large tractor business,” claims Haycraft. “It was a costly development program…that entailed some risks, but the longer-term effect was to strengthen its position in track-type tractors, particularly in the larger sizes.”
Despite a major economic recession, Caterpillar set new sales and profit records in 1975. A big chunk of that demand was driven by OPEC orders in the Middle East.
“Manufacturing space increased by one-third, from 32 million square feet in 1975 to more than 42 million square feet in 1981,” explains Haycraft. “The company was pulling out all the stops in an effort to provide facilities to meet its long-range sales forecasts.”
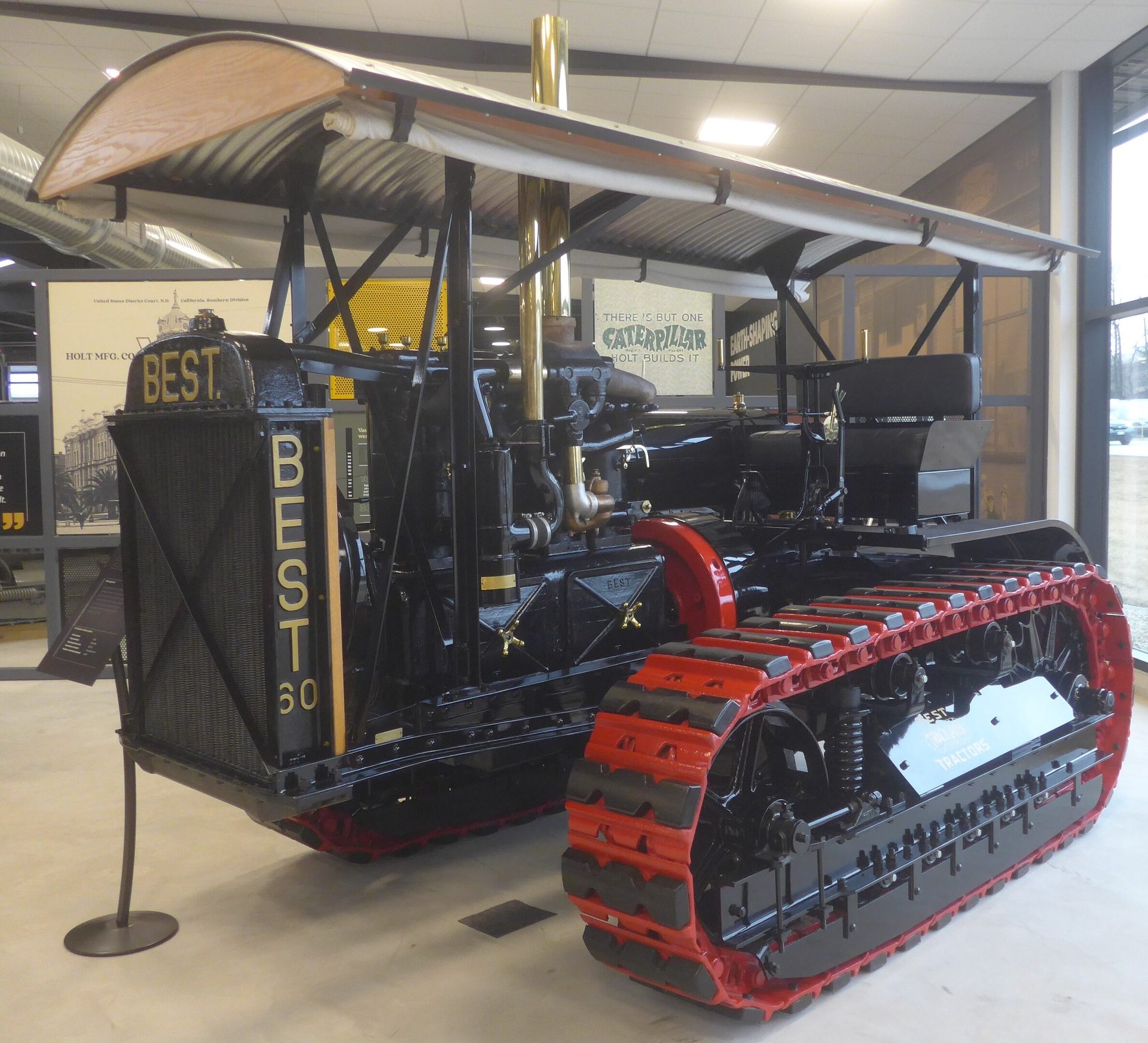
The DNA of every modern Caterpillar tractor can be traced back to this Best 60 Tracklayer from the mid-1920s. Photo by Austin Weber
Factory Updates
Two federal agencies had a profound effect on Caterpillar and other manufacturers in the 1970s: the Occupational Safety and Health Administration (OSHA) and the U.S. Environmental Protection Agency (EPA). Both were both created in 1970 and forced companies to absorb increased compliance costs and address extra regulatory burdens. But, factories in many industries were updated to improve working conditions.
The cover story in the August-September 1970 issue of Caterpillar World, an employee magazine, proclaimed that “in Caterpillar plants around the world, work is safer and a little more pleasant as factory areas become better ventilated, better lighted, less noisy….
“Improving working conditions for Caterpillar men and women is a never-ending process. And it’s one aspect of environmental control that has probably undergone more change than any other….
“The muffler on an air hoist, for example, isn’t impressive. It looks like a beer can. Yet the muffler on a large piston type hoist can reduce noise from 105 decibels to 88. Thousands of them have been installed—more than 3,000 at East Peoria Plant alone. It is just one of several steps Caterpillar is taking to reduce noise—a major problem in heavy manufacture.
“To improve air circulation in factory areas, a major conversion to low-level ventilation is underway. This system has become a feature of new facilities and is being installed in older ones. It is expected to be effective in helping make factory areas more comfortable in the summer.
“And, experimentation is also underway to develop equipment that will draw off welding smoke. At East Peoria and at other major welding plants, welders are trying experimental extractor welding guns that suck up smoke at the source.”
Caterpillar engineers worked with Hobart Brothers Co. to develop a new welding gun that could extract up to 80 percent of the smoke produced at the arc. “The extractor gun will make the work of 3,000 welders more pleasant as it replaces conventional models at Caterpillar plants worldwide this year,” explained an article in the September-October 1972 issue of Caterpillar World.
“A vacuum in the gun’s nozzle removes smoke which used to billow about welders’ heads. The smoke goes through a cellulose filter element which takes out all particles before they can enter the shop air.
“The smoke extractor welding gun is just one example of how we’re advancing technology to the benefit of the men and women who work here…. As a result of the smoke studies, Caterpillar is possibly the first company in the world to set limits for the amount of particulat matter emitted by electrodes….”
The new welding system was tested at Caterpillar’s factories in Aurora and East Peoria, IL. Nearly 5,000 pounds of electrode were melted in proving the unit could meet the rigors of production. Several units, working all three shifts during the six-week program, burned 13,000 pounds of electrode.
“If you used the new type for a while, you’d never want to go back to the old one,” a welder at the Aurora assembly plant told Caterpillar World. “Besides less smoke, the big advantage is the coolness of the gun. If you accidentally touch it, you don’t have to worry about being burned, and you can clean weld spatter off the nozzle soon after you shut off the gun.”
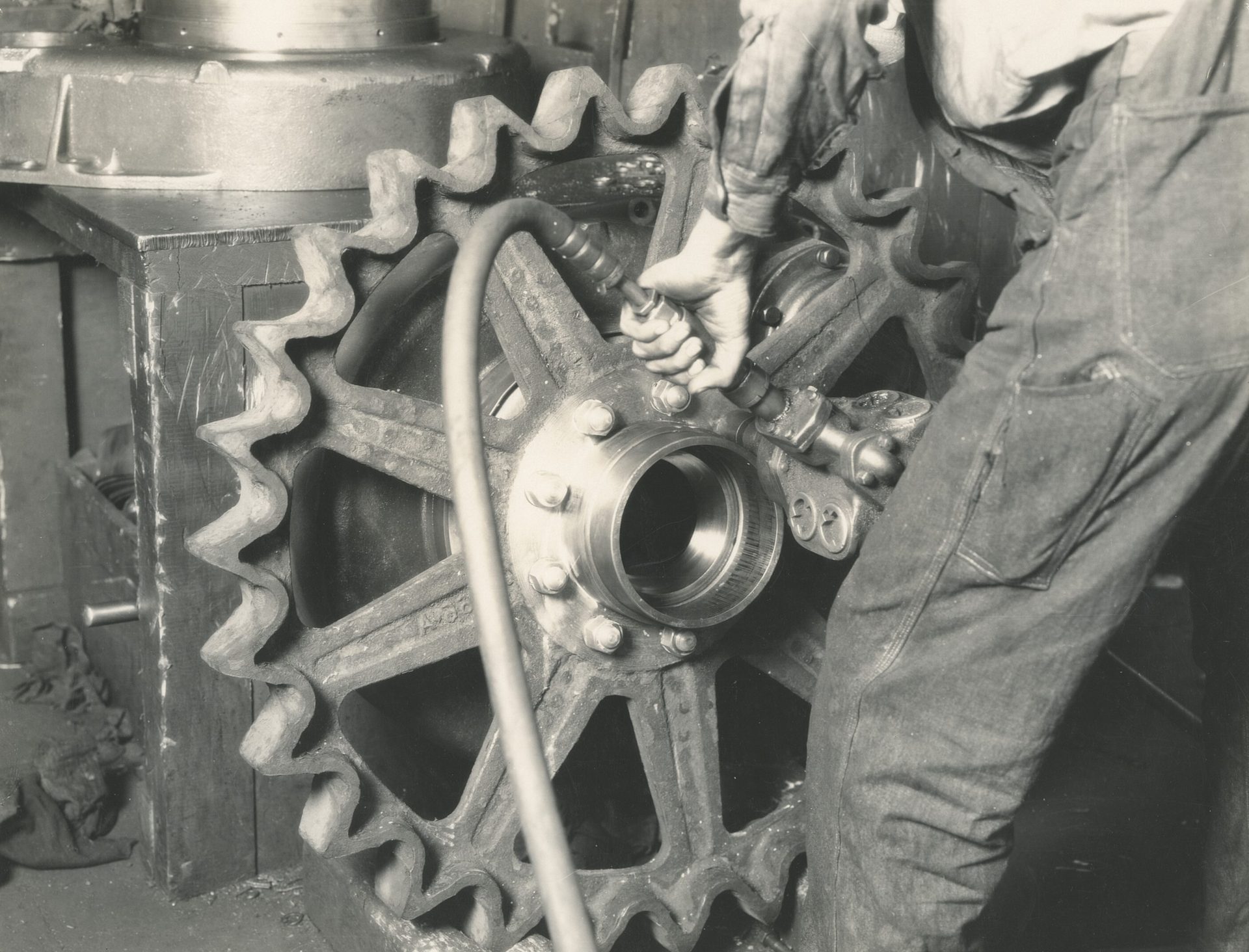
An assembler uses a pneumatic air gun to tighten nuts on the final drive sprocket of an early Caterpillar tractor. Photo courtesy HBS Archives, Baker Library/Harvard Business School
Assembly Line Innovation
The Aurora plant also pioneered a new type of conveyor system that was used to assemble the Model 225 hydraulic excavator, the first of a four-model line. Air pallets, lifted by cushions of air, helped move machines down the assembly line.
“Moving units between assembly stations is a new experience for Aurora excavator builders,” noted an article in the December 1972 issue of Caterpillar World. “Where other machines inch along on conventional assembly lines, the 225 is lifted and moved by a floating pallet.
“Teams of two assemblers and an inspector follow excavators from beginning to end on the assembly line….Although subassemblies such as transmission packages have previously been used on many Caterpillar-built products, the excavator is the first machine to be virtually ‘constructed’ of subassemblies. The units are built from individual parts by assemblers working near the line."
“We chose the air pallet system because of a weight distribution problem,” explained an engineer who came up with the innovative idea. “When subassemblies are added, the center of gravity changes. Conventional dollies would have to be so large to accommodate these changes, they’d be impractical.
“We also wanted an assembly line that could be easily expanded—we need latitude that a drag chain or conveyor line doesn’t have.
“Only a slight hiss is heard as a pallet rises about an inch off the floor and moves to the next assembly station. A programmed clock controls when and how far the pallet moves and how long it stays at each station before moving on.
“The system will be an advantage when we begin building other excavator models. Since all the machines won’t stop at the same assembly stations, they can be programmed to pass stations where there’s no required work.”
In addition, the Aurora plant was equipped with a computerized end-of-line test and inspection system. It was an offshoot of a project from the mid-1960s when Caterpillar worked with IBM and American Rockwell to create the world’s first computer database management system.
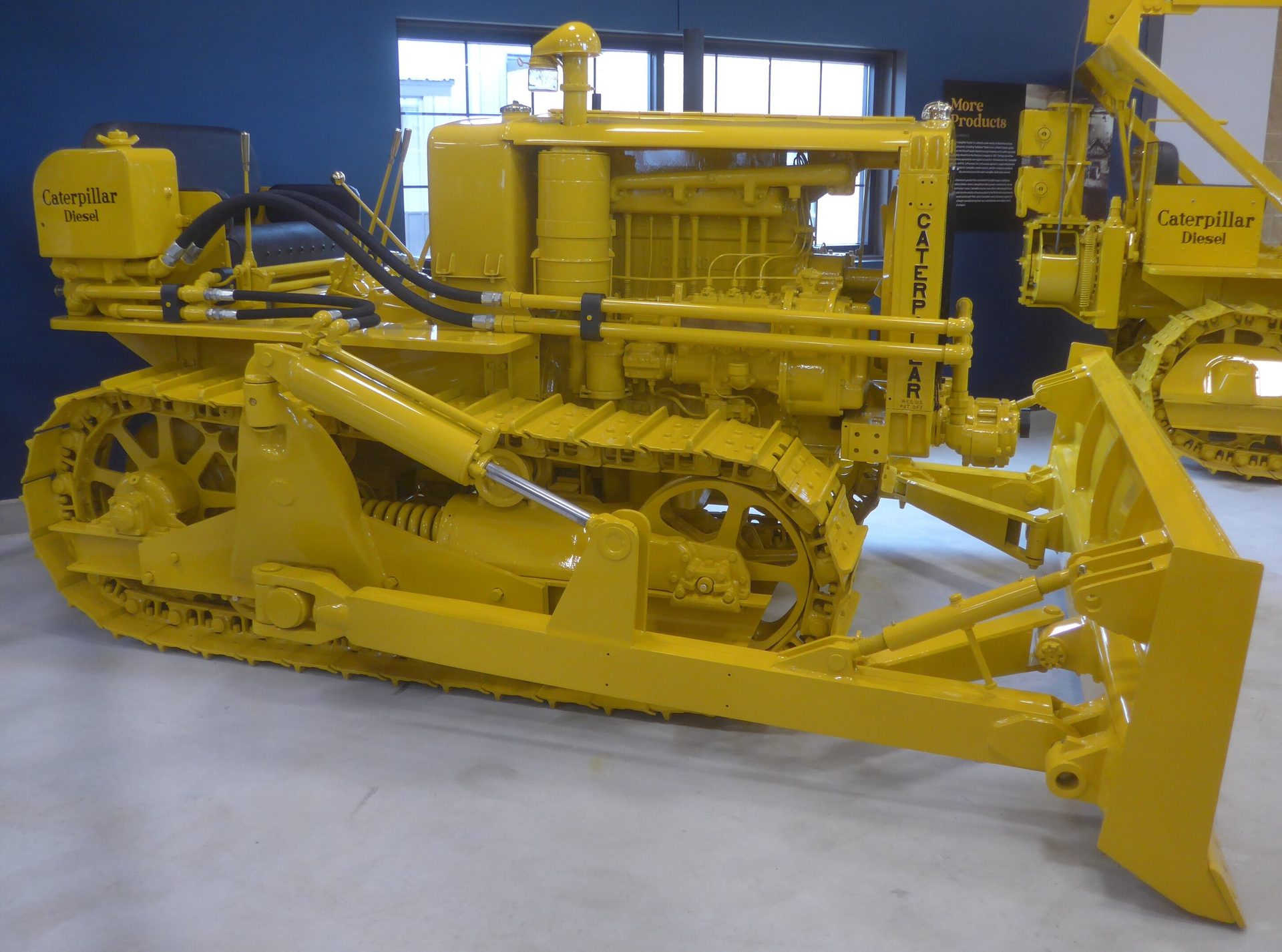
In the 1940s, Caterpillar engineers developed hydraulic systems to control dozer blades. Photo by Austin Weber
“At line’s end, an electronic flush and fill machine counts and removes particles that might damage the 225’s hydraulic system,” explained the Caterpillar World article. “Then, a computer tells assembly teams what tests to perform on the system and how the results compare to predetermined standards. Both testing devices were specially designed for the excavator program….
“An electronic counter gives assemblers and inspectors an instant reading of the number of particles in the system. After contaminants are filtered to a safe level, assemblers flush the hydraulic system and put in fresh oil. Then they move the excavator a few feet to a computerized test cell.
“Quality control people have programmed the computer to give operators step-by-step instructions for testing the 225’s hydraulic functions. Instructions, appearing simultaneously on a printout machine and two TV screens, are abbreviated and to the point….”
Because of OSHA, the 1970s also ushered in a new era of industrial ergonomics. Some of those efforts were on display at Caterpillar’s new facility in Mossville, IL, which the company claimed was the “most modern engine factory in the world” when it opened in 1974. For instance, automatic multiple-spindle torque wrenches were installed on the industrial division’s 3208 diesel truck engine assembly line.
“Engine assemblers can now tighten as many as 18 bolts simultaneously,” explained an article in the March 19, 1976, edition of Caterpillar Folks, an employee newspaper. “Previously, each bolt was torqued with a manual wrench. Three of the new wrenches are now in the plant….
“Assemblers’ jobs have been made easier and torque accuracy has increased since the new device went into use… Bolt torque accuracy has increased 39 percent since we began using these wrenches. They also decrease assembly time. The 18-spindle wrench saves five minutes per engine and the five-spindle wrenches save 2.5 minutes per engine."
“It’s a lot better than pulling a torque wrench all day,” quipped an assembler.
“The multiple-spindle torque wrenches are specially designed to operate with the moving 3208 assembly line. Each unit is air-powered and electronically controlled. They’re attached to four-way bridge cranes which allow the assembler to maneuver the wrenches around the engine with little effort.
“Assemblers set the [control panel] dials at acceptable high and low bolt torque levels. If the wrench misses a bolt or fails to torque within the specified range, a horn sounds. Lights corresponding to the particular spindle blink red if the bolt is too tight or amber if it’s too loose.
Inspection System
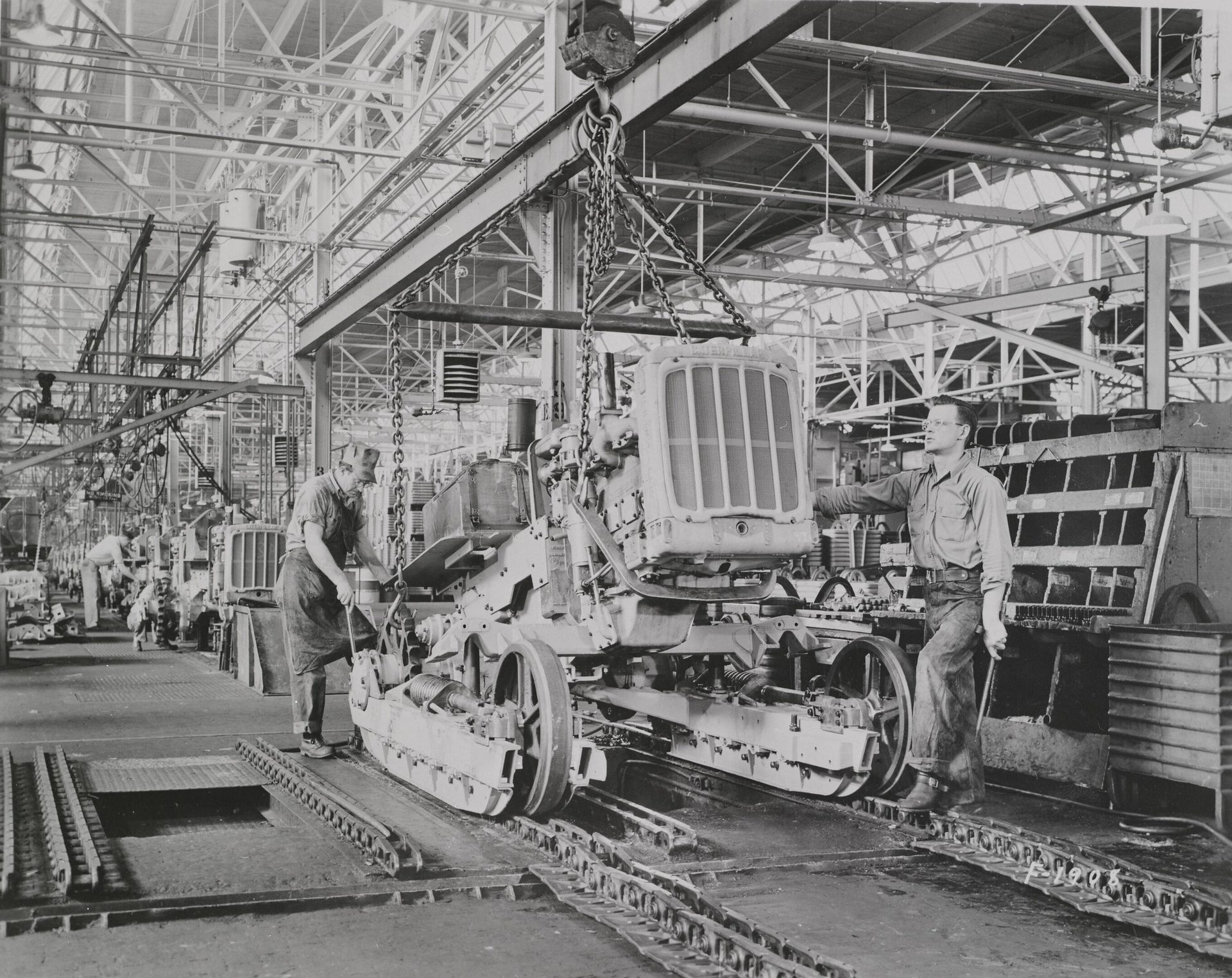
When this photo was taken in 1948, Caterpillar was struggling to keep up with unprecedented demand for crawler tractors. Photo courtesy Caterpillar Inc.
“By dialing the spindle selector, an assembler can get a readout of the exact torque of the incorrect spindle. He then torques the bolt by hand with a preset torque wrench.”
As part of its effort to improve working conditions in the early 1970s, Caterpillar also embarked on an initiative to brighten its factories. It implemented a color-coded paint system to improve visibility. The goal was to eliminate eye fatigue, improve morale and reduce accidents.
“A few years ago, interiors of Caterpillar’s manufacturing plants around the world had one thing much in common: their appearance,” said an article in the April-May 1972 issue of Caterpillar World. “But some refreshing changes have taken place, the result of a color-conditioning program…. Color selection and application are based on building layout, light sources, area size, operating condition and appearance of equipment, and type of manufacturing or assembly operation…. Several plants have undergone this kind of color conditioning and others are considering it.”
Ironically, issues related to color and safety came full circle later in the decade when Caterpillar was forced to change the iconic color of its machines due to environmental concerns.
“The traditional hi-way yellow had been closely identified with Caterpillar for almost 50 years, but because of the paint’s high lead content, OSHA ruled that hi-way yellow could no longer be used without an extensive revamp of factory painting facilities,” says Haycraft.
“In a manufacturing-driven decision, the company chose to switch to Caterpillar Yellow,” he explains. “That drab, brownish-yellow resulted in such a marked deterioration in the appearance of the machines that some dealers at their own expense routinely repainted the machines when received from the factory.”
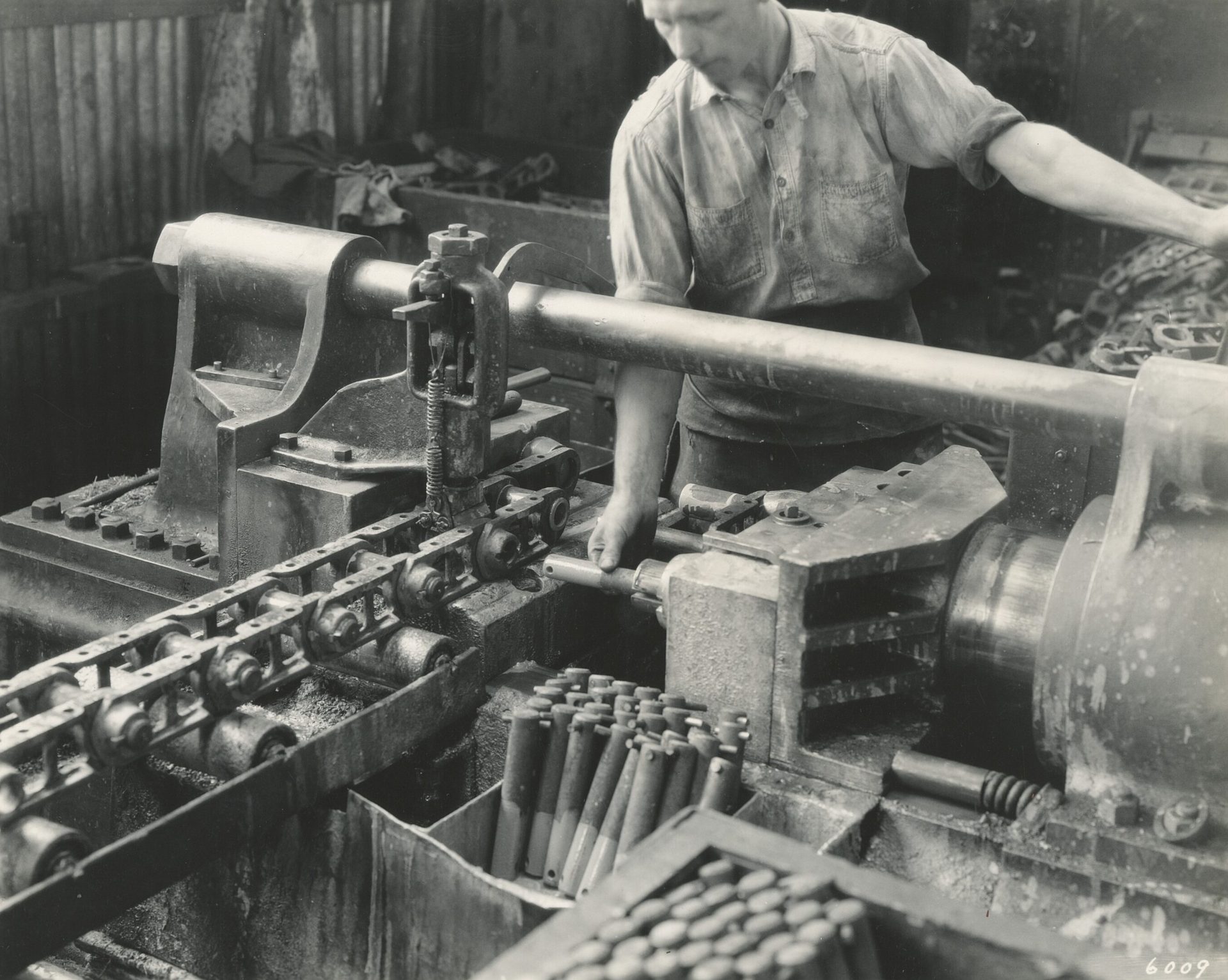
A Caterpillar assembler uses a press to insert pins and bushings into track links in the late 1920s. Photo courtesy HBS Archives, Baker Library/Harvard Business School
Quality Crusade
Caterpillar’s 1967 annual report explained how the company was investing in new tools “to increase productivity of older plants and equip new plants with [the] latest manufacturing and material handling techniques…. New techniques and equipment are helping maintain Caterpillar’s high quality standards.
“For manufacture of critical parts like hydraulic controls, new facilities automatically regulate air temperature, humidity and cleanliness. New test equipment such as air gauges and special liquids that reveal defects under ultraviolet light aid and improve inspection. Stationary load testing of tractors and scrapers uncovers leaks, overheating and other defects in a fraction of the time needed to make such tests on a test track.”
Caterpillar’s 2-million-square-foot factory in Decatur, IL, was ground zero for a major quality initiative. The facility mass-produced numerous models of large off-highway dump trucks, motor graders and wheel tractor scrapers. The linear assembly line was the company’s longest—almost a quarter of a mile—and one of its busiest.
“Into this line flow thousands of parts and components,” explained an article in the February-March 1971 issue of Caterpillar World. “Racks, rails, circles, frames, housings and other parts designed, heat treated, machine, welded at Decatur…..
“If everyone does his job right before these materials reach the line, and as they are put together, a virtually defect-free motor grader should come off the conveyor ready for finish paint. But…people can make mistakes. Those mistakes must be discovered before machines go out the back door to customers.”
To address the issue, Caterpillar engineers combined manual defect cards with state-of-the-art data processing technology to determine the number and type of mistakes made on the assembly line. The improved online detection and reporting system, dubbed Defect Control, started at the Decatur plant in 1969.
“As a motor grader goes down the assembly line, it must pass five quality reporting stations, each manned by an inspector and one or more assemblers,” reported Caterpillar World. “At each location, the inspector carefully goes over the partially assembled machine, recording each defect he finds on an IBM card.
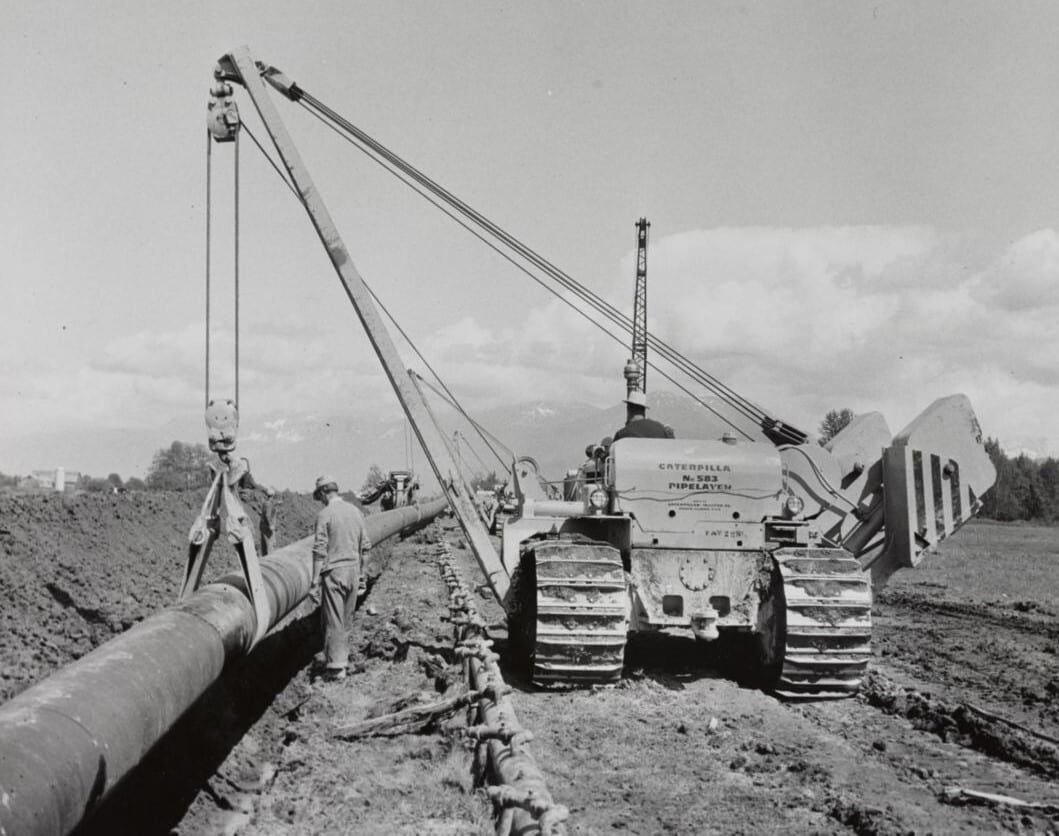
When it was unveiled in 1955, the No. 583 pipelayer met a burgeoning need for oil, gas and water pipelines around the world. Photo courtesy Caterpillar Inc.
“He gives a carbon copy of the card to the assembler, who corrects the defect. If the assembler can’t correct it at his station, the card stays with the machine until the correction is made. The machine also goes through two on-line adjustment stations before it reaches the adjustment floor.
“At the end of the shift, all the cards from the assembly line go to data processing. There they are punched and the information fed into a computer which performs the necessary arithmetic. A printer then types out the printout sheet reporting performance for the day. The report contains the kinds of defects found, their number, the number corrected and at what station.
“[Foremen receive copies and] go over the report with inspectors, assemblers and adjusters to determine what they must do—or what other departments must do—to reduce the number of defects."
“With the improved system, we can pin down defects a lot faster,” noted an engineer working on the project. “We soon learn where most of our trouble is….Defect Control is the answer to reducing the number of assembly and other defects without the need for expensive last-minute rework.
“Defect control stations right on the line make it easier—and less expensive—to catch errors in early stages of assembly. For example, it’s a lot easier to correct a defect when it’s discovered on the assembly line than when it gets to the adjustment floor….
“Before the improved defect control system, most of the job of finding errors fell to the adjustment floor and customer acceptance test men. Now, these men can do what they’re supposed to do—adjust, not repair.
“Defects may involve several departments…so [the plant has] a defect control meeting once a month….Changes have been made in design and manufacture as the result of such meetings….[For instance], engineering redesigned some parts to reduce rework and cost of assembly….
“Complaints from customers about their motor graders are declining. Looks like Decatur’s on the right track.”
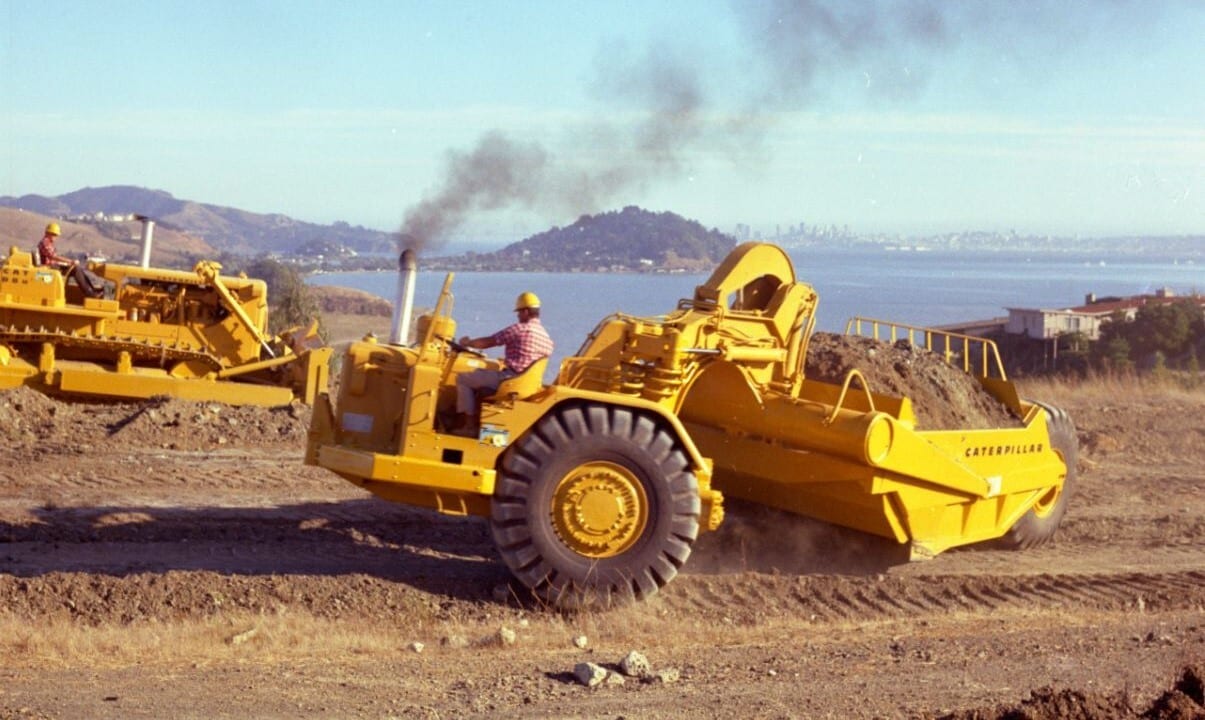
Caterpillar bulldozers and motor graders revolutionized the earthmoving industry. Photo courtesy Caterpillar Inc.
Challenging Decade
Caterpillar dominated the construction equipment market for decades. Although it faced domestic competitors, such as Allis-Chalmers, Case, Deere and International Harvester, Cat remained the No. 1 brand and even managed to gain market share against its rivals.
However, all of that changed dramatically in the mid-1980s. Foreign competition, lengthy labor disputes and the sharp rise of the U.S. dollar against other currencies forced Caterpillar executives to make some painful decisions about the company's manufacturing footprint and production philosophy.
Komatsu Ltd. took advantage of Reagan-era economic policies and outmoded foreign exchange rates. It aggressively entered the U.S. market, focusing on total quality control programs and new product development.
Labor strife also put added pressure on Caterpillar’s manufacturing strategy. The company had developed a contentious relationship with labor unions over the years that resulted in numerous strikes. Most of those problems started after World War II.
“Caterpillar’s postwar labor relations were both simplified and complicated by its position as essentially a one-plant manufacturer,” says Haycraft. “That resulted in one large bargaining unit: Peoria Local 105 of the United Farm Equipment and Machine Workers of America Union.”
Things came to a head with a 28-day strike in 1946. Then, two years later, the East Peoria plant came under the auspices of the United Auto Workers (UAW) Union. However, many of its future contract negotiations were marred by unrest.
In 1958, Caterpillar suffered a seven-week UAW strike at the plant, plus other shorter strikes in the 1960s. Progressively longer strikes occurred in 1979 (80 days), 1982-83 (205 days) and 1994-95 (18 months).
Just months after it recorded its highest sales and profits in history in the early 1980s, Caterpillar was hit by a sharp drop in demand, due to a recession and a strike. Komatsu took advantage of the situation and nipped away at the company. It began underselling equipment by as much as 40 percent.
Komatsu also opened a factory in Chattanooga, TN. And, through a joint venture with Dresser Industries, it even acquired a factory in Caterpillar’s hometown of Peoria, IL (the facility is still in operation today, producing large mining trucks that compete with Cat vehicles made in Decatur).
In 1979, Caterpillar accounted for 36 percent of the world market. By the mid-1980s, that number dropped to 28 percent. In North America, the company’s market share dropped 11 points between 1981 and 1986.
To survive, Caterpillar was forced to fight back. After losing nearly $1 billion during the previous three years, in 1985 the company began to shrink its historic manufacturing footprint in the Midwest.
The first cuts occurred when the company announced plans to close plants in Burlington, IA; Edgerton, WI; and Mentor, OH. The historic 900,000-square-foot San Leandro, CA, factory that dated back to Caterpillar’s birth was also shuttered in 1985.
In 1987, Caterpillar announced that it would close its 2-million-square-foot factory in Davenport, IA. Its assembly plant in Uddingston, Scotland, near Glasgow, closed that same year.
Caterpillar also embarked on a controversial initiative in 1985 called Plant With a Future. “Unlike previous lavish capital spending, the program focused on cost reduction and proved to be the wisest capital investment the company ever made,” says Haycraft. “Indeed, it may well have been the salvation of Caterpillar.”
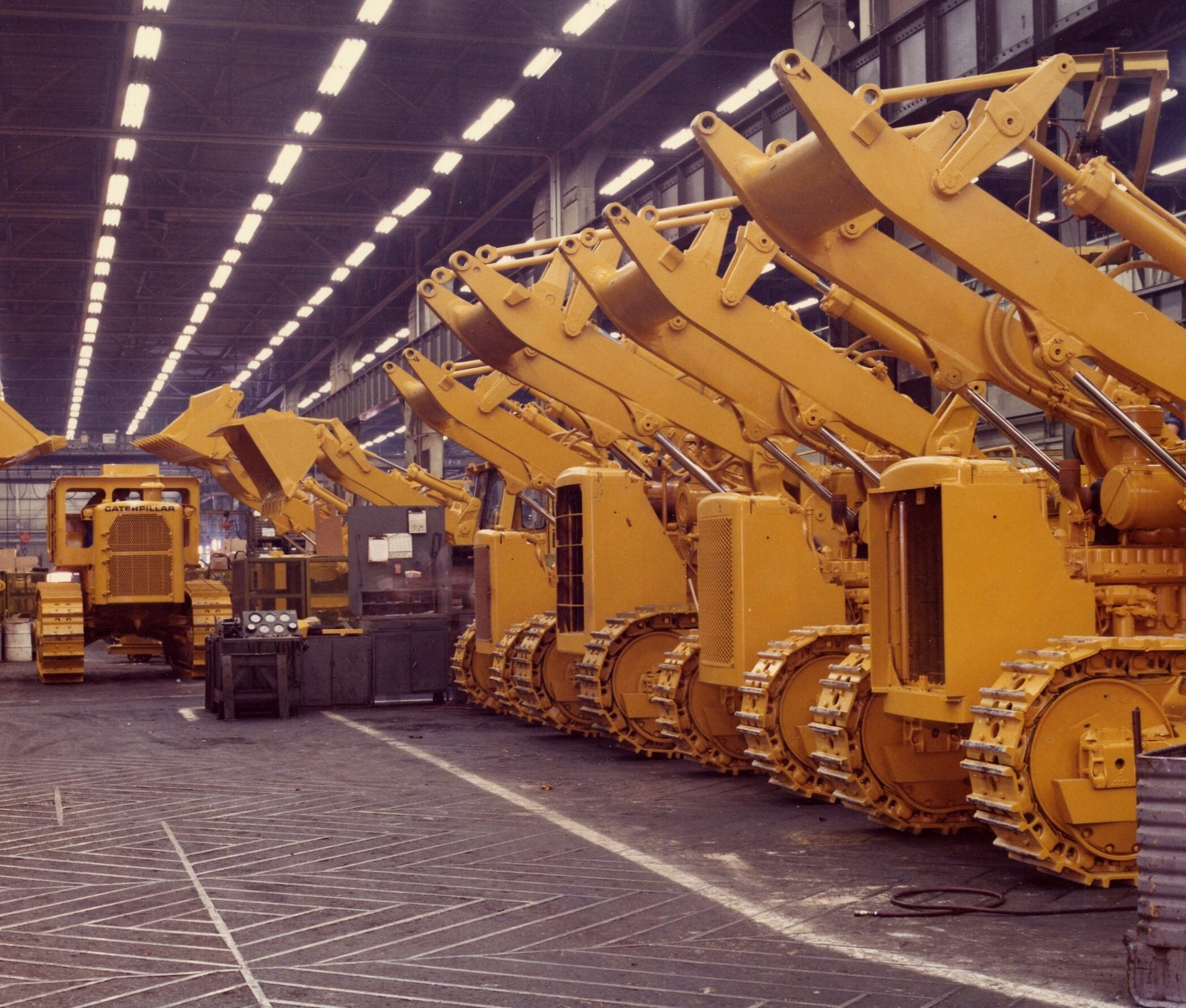
A fresh batch of front-end loaders are waiting for buckets to be attached at the East Peoria plant in 1959. Photo courtesy Caterpillar Inc.
Plant With a Future
Before the early 1980s recession, Caterpillar had invested billions of dollars in factory expansion, pouring resources into additional floor space and production equipment to increase manufacturing capacity. However, factory modernization was not occurring.
“Little attention was paid to material flow, in-process inventories, just-in-time supplier deliveries and other areas where the potential for cost reductions was relatively untapped,” says Haycraft. “After more than 35 years of uninterrupted expansion of manufacturing facilities, the pivotal year of 1982 marked the point at which Caterpillar was forced to retrench for the first time in its history.
“Between 1983 and 1985, it closed about 20 percent of its manufacturing space and stopped construction on additional space,” explains Haycraft. “But, with the 1985 birth of Plant With a Future (PWAF), the company embarked on a new course that would pay huge dividends.
“Management came to realize that it could lower costs and operate with much reduced manufacturing space provided that operations were radically modernized to use facilities more efficiently,” Haycraft points out. “PWAF involved new tooling and a massive rearrangement of factories within existing space, and was to be carried out over six years at a cost of around $2.1 billion.”
The factory modernization program was the brainchild of Pierre Guerindon, a Frenchman who headed Caterpillar’s manufacturing operation in Europe. However, the new vice president for manufacturing and planning was not universally welcomed, especially at the company's old-school Midwestern plants.
“Guerindon looked at the flow of parts through a Caterpillar factory and saw a tangle of spaghetti,” explained an article in the Sept. 7, 1992, edition of the Chicago Tribune. “In untangling it, he began to alienate the manufacturing fraternity at Caterpillar. Caterpillar had its way of doing things, and Guerindon was changing that….
“Guerindon’s vision was undeniably sweeping. His plans gutted factories, eliminating hundreds of hand-operated, labor-intensive machine tools in favor of automatic ones. He tore down walls. And he spent money….
“To those who feared automation meant jobs for robots, not people, PWAF came to stand for ‘Peoria Without a Factory.’ The project made some workers bristle. They complained that machines broke down, and that some were nothing more than fancy gadgets that made no real improvement.”
Despite those concerns, PWAF worked and proved popular with industry analysts, who saw the project as key to Caterpillar’s long-term survival.
“Before PWAF, it took three weeks to assemble a wheel loader,” explained the Tribune article. “Now, it takes two to three days to put together some models in Cat’s Aurora factory. And the time it takes to process an average part from start to finish...was cut from 25 days to 10 days. Through just-in-time shipping techniques, inventory was cut in half.
“But, with every change, the need for workers was reduced. Between 1979 and 1992, the company`s Peoria-area hourly work force [was] cut by almost two-thirds, from 23,000 to 8,600.”
New Plant Layouts
To reduce inventories, speed up assembly time and improve quality, Guerindon believed that it was necessary to change the entire layout of some plants. An article in the Dec. 19, 1988, issue of Fortune magazine described some of the changes occurring at Caterpillar’s flagship factory in East Peoria, IL:
“Transmission assembly formerly performed in five different buildings will be consolidated under its roof. It will take five years and $200 million to turn the 40-year-old red-brick facility into a ‘plant with a future.’ Nearly every one of the 500 machine tools will be moved or replaced. Caterpillar intends to accomplish all this without once slowing down the production lines. So far, it has succeeded…."
“Efficiency has been rising even amid the uproar,” claimed the plant’s PWAF project manager. “By installing a computerized inventory control system, [we] have drastically compressed the time it takes to run components through the plant. The parts for a clutch housing used to hang around in various stages of assembly for 20 days before they were packed up and shipped out. They are now in and out in just four hours.
“It used to take 11 workers to machine, burr, balance and wash planet carriers (the guts of a transmission). Now, two workers do the job, running a manufacturing cell consisting of just six machines.
“Cellular manufacturing is nothing new, but making it work requires a radical reorientation of old attitudes. Workers must be trained to handle multiple tasks, work in teams, and take responsibility for the quality of the parts they produce. Such changes do not come naturally to Cat’s hard-boiled workers and managers.
“For all their shared pride in the big yellow machines they built, the shop-floor style was classically confrontational and hierarchical. Middle managers still worry about losing their authority, and longtime screwdriver jockeys sometimes sour on the idea of running not just one, but several, newfangled machines….
“But the new ways are catching on. Many employees, particularly younger ones, appreciate getting a bigger share of the action. Blue-collar workers are now encouraged—and expected—to pipe up on issues like product engineering, workplace layout and quality improvement."
“‘Five years ago, the foreman wouldn’t even listen to you, never mind the general foreman or the plant supervisor,’” explained a veteran assembler. “‘Now, everyone will listen.’
“Caterpillar has enlisted the shop-floor experts in shaping up its suppliers. Machinists, for example, may visit suppliers’ factories to help the teams that evaluate and certify production quality….
“The certified companies get preferential treatment in exchange for meticulous attention to quality. The reject rate for parts they furnish is 0.6 percent vs. 2.8 percent for noncertified suppliers.”
Several years after he retired, Guerindon wrote a book entitled Continuous Flow Manufacturing. “Between 1986 and 1992, Caterpillar converted 18 factories in nine countries to continuous flow manufacturing,” he explained. “I am grateful to have served as the architect of this effort.
“[Companies] such as Caterpillar choose to transport in-process assemblies by automated guided vehicle, but remove the assemblies at workstations. The AGVs run in a continuous loop, picking up and dropping off assemblies at the appropriate work areas. In Caterpillar’s Decatur, IL, plant, the world’s largest AGV carries off-highway trucks and construction equipment to stations along the ‘assembly highway.’
“Because the plant is designed for stall building, each workstation has been customized for the operation performed there. Work areas are equipped with the right tools and feature hydraulically powered lifting devices that elevate the product, giving the assembler better access to the underside. This arrangement has generated a quantum jump in quality and productivity compared to what was achieved in a moving assembly line where workers had to climb on the product to do their jobs.
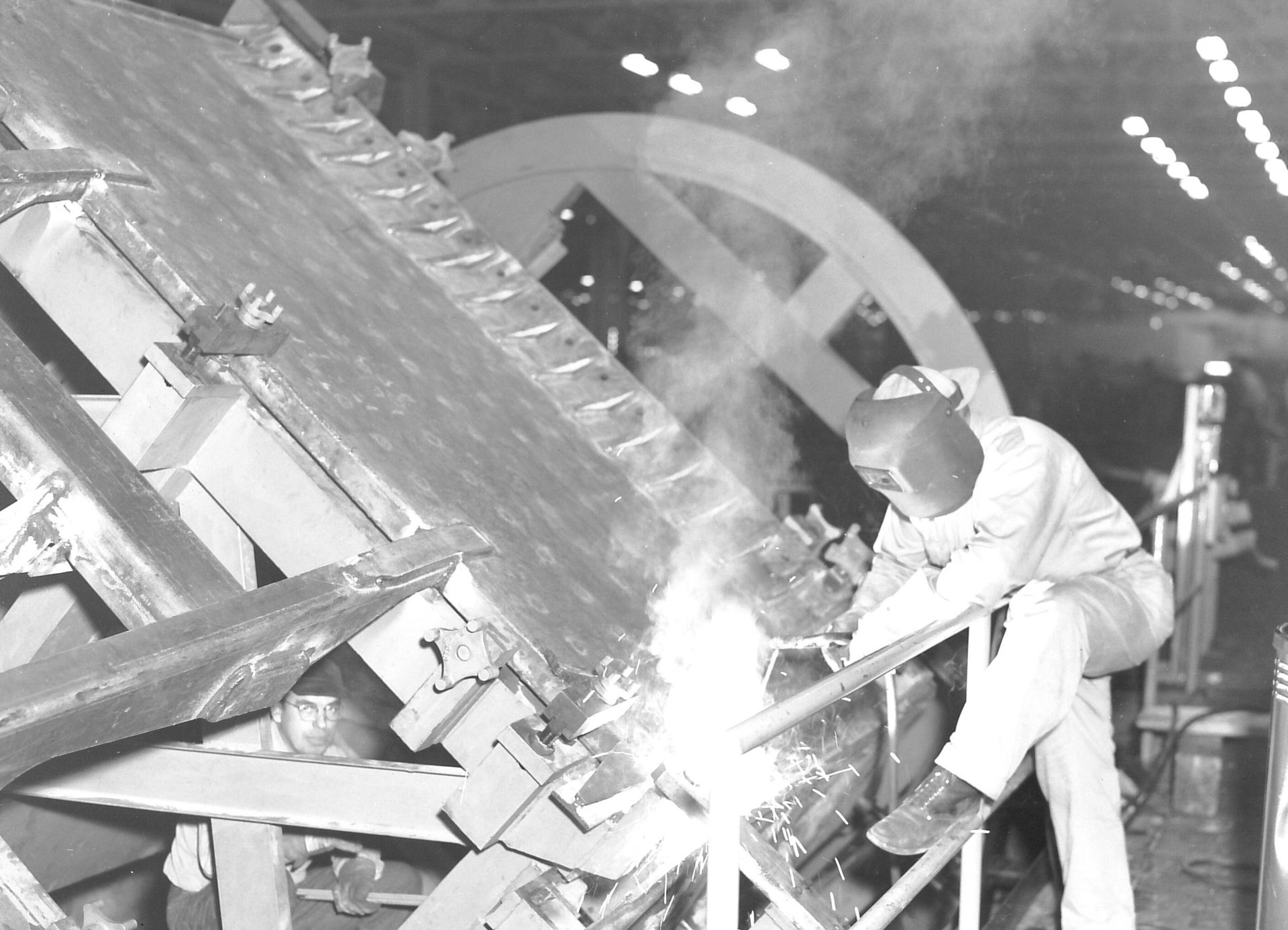
A large piece of earthmoving equipment is manually welded at Caterpillar’s assembly plant in Joliet, IL, in the 1960s. Photo courtesy Joliet Area Historical Museum
“Experience at Caterpillar’s Grenoble, France, plant has shown that given comparable production levels, a flexible assembly system reduces direct and indirect labor content by 50 percent over a traditional assembly operation.”
Caterpillar’s 1988 annual report touted how its plants were evolving with state-of-the-art technology and a fresh approach to operational excellence: “Walk through any Caterpillar manufacturing plant, and you’ll see change. We’re removing old machine tools, tearing down walls, digging pits, pouring concrete and installing new equipment. Cat employees are implementing a comprehensive factory modernization strategy to improve response time to customers, reduce costs and extend our quality advantage.
“More than 80 major modernization projects have been approved in facilities around the world….We’ve reduced manufacturing space by 21 percent. Further consolidation within existing facilities will result in an additional 7 percent reduction. While we consolidate, we’re also rearranging factory layouts.
“To date, we’ve rearranged 47 percent of the worldwide manufacturing base. That will let us make more product in less space and in less time, because work flow is streamlined….Cells process entire families of parts from start to finish and supply the assembly line just-in-time. Cell manufacturing allows higher quality production at lower costs.”
The annual report provided two examples of how Caterpillar was “building for tomorrow” and eliminating waste in its Decatur and Aurora factories, respectively: “Under the old manufacturing process, motor grader front axle parts moved through four different buildings before assembly was complete. Now, we’re doing the entire job—machining, welding and assembly—in one cell. Costs have been reduced by 35 percent….
“Excavator booms are manufactured on a flexible machining system. Welding is done in the same area. Caterpillar has a patent on the welding process, which features an electronic vision system. Using a form of artificial intelligence, the welding automatically adapts to the shape of the joint.”
The tumultuous 1980s ended with one final transition: the name of the business itself. Caterpillar Tractor Co. was rebranded as Caterpillar Inc. According to the company, the word “tractor” no longer accurately described its product line, which had expanded into a diversified portfolio of machinery.
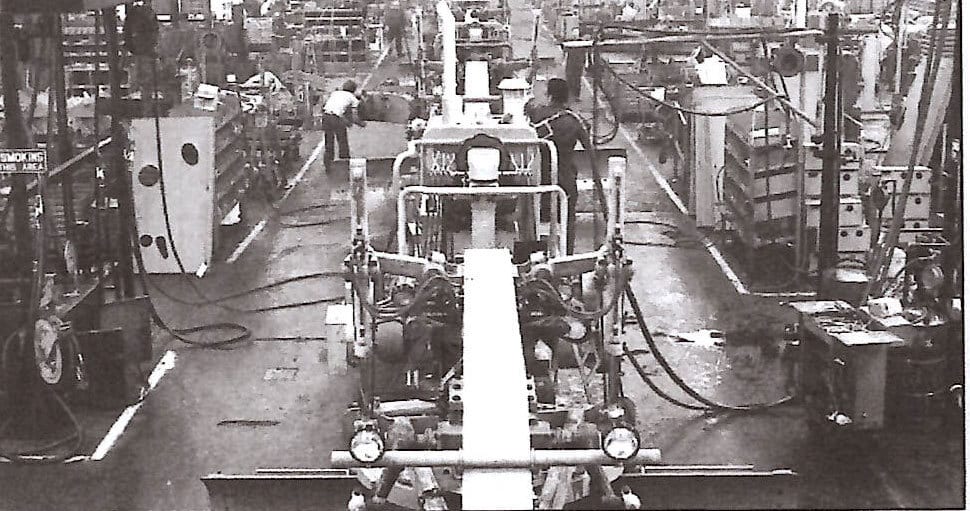
The motor grader assembly line in Decatur, IL, was Caterpillar’s longest. Photo courtesy Decatur Public Library Herald and Review Archives
Robotic Transformation
By the mid-1990s, Caterpillar had fully rebounded and was flying high once again, with profits topping $2 billion.
“The increasingly aggressive product program between 1986 and 1995 left Caterpillar at the end of 1995 with a formidable, state-of-the-art product line across the board,” says Haycraft. “Between 1990 and the end of 1995, Caterpillar was transformed.
“There was no doubt that Caterpillar had made fundamental changes in the way that it operated: drastic downsizing from the 1983 peak of 45.7 million to about 33 million square feet; the plant modernization program; a total reorganization of the company; rigid control of employment; judicious outsourcing; and transfer of some operations to lower cost locations.”
In 1994, after achieving record-setting sales, profits and market share gains in each quarter, Caterpillar chairman and CEO Donald Fites told financial analysts that the strategies were paying off: “The company has achieved its efficiencies over the years, primarily through the seven-year factory modernization program that today is showing a return of more than 20 percent. The modernization effort, of which the company continues to reap benefits, has improved Caterpillar’s competitive position.”
One big change at Caterpillar during this period was a strategic investment in robotic technology. It started dabbling in the devices a decade earlier to improve the efficiency, speed and precision needed to mass-produce fuel systems and other critical components.
According to an article in the April 2000 issue of Welding Journal, “Caterpillar was in on the ground floor when robots were first introduced to arc welding…almost 20 years ago…. There was a huge amount of research into robotic arc welding at the Caterpillar Manufacturing Development Center in East Peoria, IL, and developments in advanced robotic systems continue today at the Tech Center in Mossville, IL.
“The original spadework has paid off to the extent the company now has several hundred robots in operation throughout its plants worldwide, specifically engaged in arc welding. Why all this effort? What was the goal? Quality, productivity and environmental impact.
“There was a time not too many years ago when welders wielding semiautomatic guns performed most of the welding operations in a typical Caterpillar manufacturing plant. Most of the welds were made with flux-cored wire. Today, most of the welders have become robot operators or have moved to other jobs.
“Robotic arc welding systems now make the welds the welders produced in the past. Nowadays, the welds are made mostly by solid, not flux-cored, wire. Things are quiet. The plant area is clean.
“To continue the way they had been doing things, Caterpillar would have needed a huge number of qualified welders. Not enough welders were available to do what had to be done. Automatic welding, especially robotic welding, seemed the logical answer.
“Over the years, Caterpillar has played an important role in advancing robotic technology from its simple single-axis beginning to the point where the designers of the equipment and the designers of the manufacturing process work together to optimize the process before the first arc is ever struck….
“Generally, Caterpillar is moving away from flux-cored arc welding, a technology the company played a major role in developing years ago, and toward small-diameter sold wire welding…. Early robots were used in production mostly for making fillet welds and some small groove welds…. At first, the applications were mostly small parts, such as brackets. These were all low-volume applications…. Electric robots started to replace hydraulic robots in 1983.
“The most advanced production systems in heavy fabrication can be found in Caterpillar’s East Peoria plant, [which has] 56 robots…and close to 35 vision systems operating today….There are 17 robotic systems at the Decatur plant—all of them big.”
“Robotic welding gets more of our employees out from under the hood and gives them a chance to focus on other critical areas in our manufacturing process,” explained a fabrication process engineer at the Decatur plant. “Our manufacturing environment is much more high-tech than in years past. Gone is the perception that working in a factory is dirty, unpleasant work…. The welder of today needs to understand high-tech robotic welding systems and how these systems interact with other manufacturing systems elsewhere in the plant.”
By the turn of the last century, Caterpillar engineers were busy exploring other types of new joining technology, such as laser welding.
“Traditionally, Caterpillar has been a major user of arc welding technology,” explained Jerry Palmer, vice president of the company’s wheel loaders and excavators division, in an article that appeared in the January 2004 issue of ASSEMBLY magazine. "However, the company has been investing heavily in laser welding.
“We’re looking at new welding technology that allows us to improve the weld deposition process to increase strength,” added Palmer. “We hope to decrease the weight of structures 20 percent to 30 percent with the same-strength weld.”
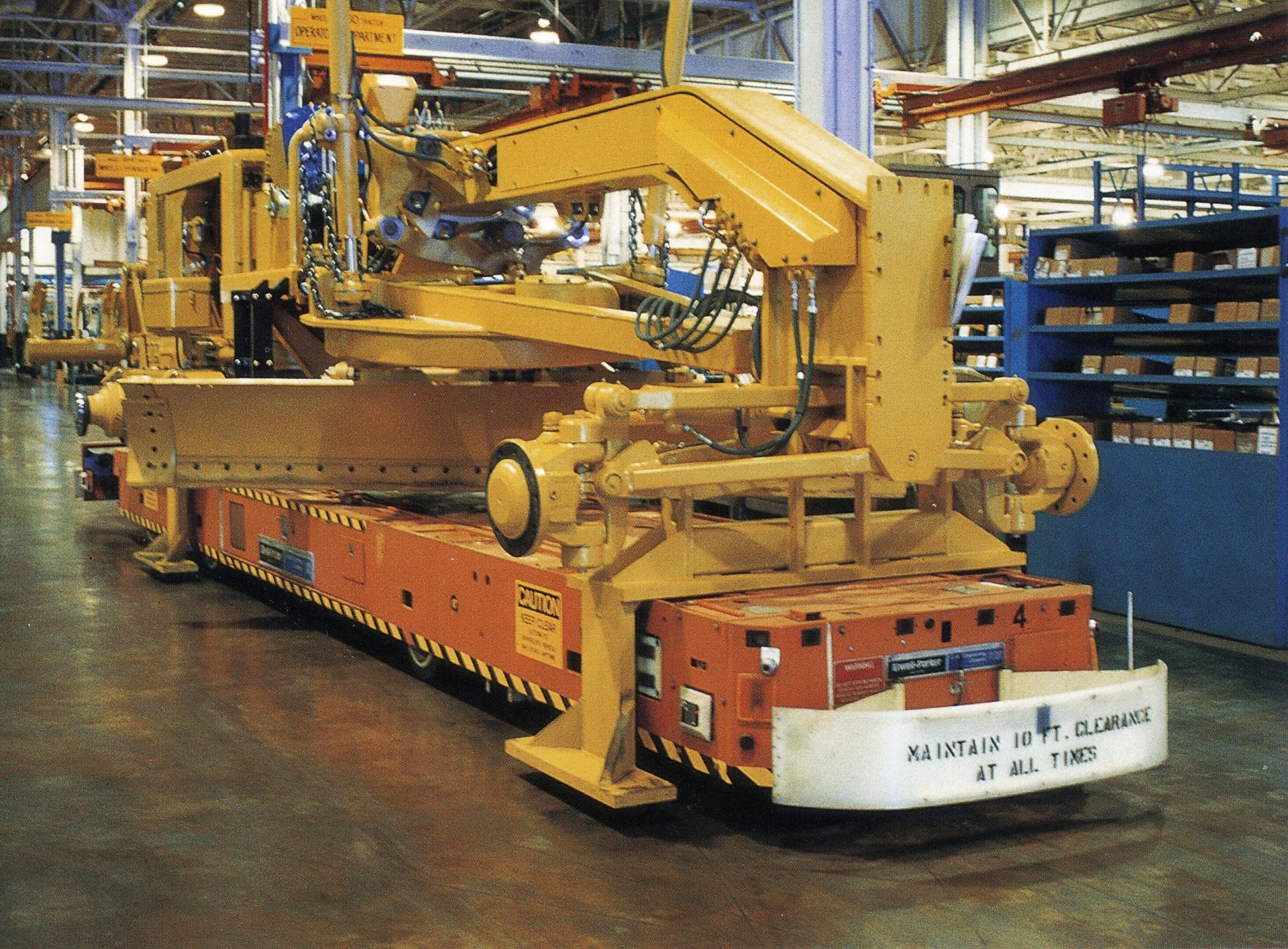
This photo from 1980 shows an early automated guided vehicle in operation at Caterpillar’s assembly plant in Decatur, IL. Photo courtesy Decatur Public Library Herald and Review Archives
Continuous Improvement
In the same ASSEMBLY article, Palmer outlined Caterpillar’s lean manufacturing and Six Sigma initiative, which it implemented in 2001. The goal was to strengthen operating efficiency, improve quality and reduce waste.
“Caterpillar is pursuing Six Sigma because it has the power to provide us with an energetic new direction and raise our business success to unprecedented levels, further solidifying our leadership position in the industries we serve, and providing greater satisfaction to employees, customers and shareholders,” Palmer pointed out.
The company was using a set of strategies, statistics and methods to improve product design and manufacturing. “By applying the rigorous practices of Six Sigma, we can achieve breakthroughs in financial and quality performance that would otherwise be unattainable,” claimed Palmer.
“Since we adopted Six Sigma [in January 2001], it has transformed how people work, what they work on and how they perform their work,” noted Palmer. “It has made people ask the right questions…rather than shooting from the hip.”
At the time, Caterpillar boasted 40 product lines and more than 280 different models. During the last 10 years, the number of models had more than doubled. Engine sizes ranged from 5 hp to 8,000 hp.
“We’ve expanded horizontally into a number of different product lines,” explained Palmer. “For instance, 10 years ago, we didn’t have products such as skid-steer loaders and compact construction equipment.”
Palmer’s 46-year-old plant in Aurora, IL, was assembling eight product lines and more than 25 different models of wheel loaders and tracked excavators. Because customers specified numerous options, such as unique axle and power train configurations, each machine moving down the assembly line was different than the next.
Caterpillar’s executive team first addressed Six Sigma during its strategic planning meeting in August 2000. It appointed a full-time team committed to Six Sigma and the first employee training session was held in December.
Although Six Sigma was still a relatively new concept at the company, it had already achieved some impressive results by late 2004. For instance, Palmer pointed to a six-year-old plant in Sanford, NC, that assembled small skid-steer loaders. Because of Six Sigma, the facility was able to increase production by 26 percent and decrease assembly cost per unit by 25 percent.
In 2005, the Caterpillar Production System (CPS) was launched. The goal was to “implement a common enterprise-wide order-to-delivery process to improve safety, quality and velocity, add capacity, and improve cost management. The principles followed with Six Sigma and the alignment process for closing gaps in achieving goals are all leveraged in the execution of CPS processes.”
CPS focused on eliminating waste—defined as “any activity that consumes resources but creates no value for the customer”—in Cat’s production processes from order to delivery.
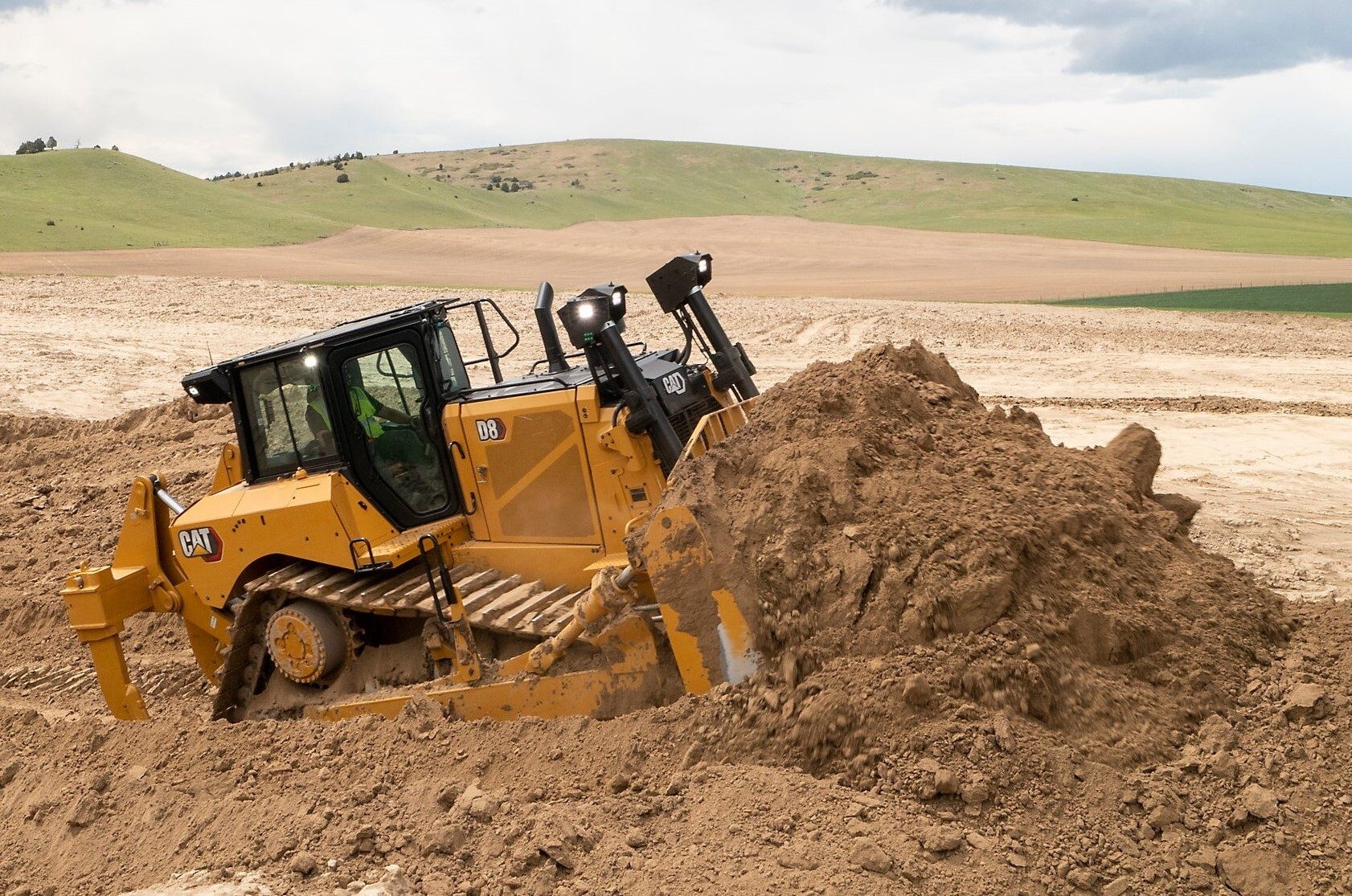
Caterpillar engineers developed elevated drive sprocket technology in the 1970s. Photo courtesy Caterpillar Inc.
According to Caterpillar’s 2006 annual report, “CPS is a mechanism for integrating our operations, culture and management system to pursue radical improvements in safety, quality, velocity, cost and other key performance measures.
“CPS made significant progress in its first full year of development and implementation. We put much of the framework and many key methodologies in place worldwide, which already has resulted in more than $125 million in benefits.
“Our Mossville Engine Center played a groundbreaking role in implementing CPS in 2006. Value stream transformation processes created a safe and team-based environment that enabled employees at all levels to make a significant impact on continuous improvement of people, quality, velocity and cost metrics.”
Beginning in 2010, Caterpillar began building new plants in non-union southern states such as Arkansas, Georgia, North Carolina and Texas. A few years later, the company closed two large assembly plants near Chicago.
In 2017, Caterpillar announced plans to close its 4-million-square-foot Aurora factory, transitioning medium wheel loader production to a newer facility in North Little Rock, AR.
After 68 years in operation, Caterpillar also closed its factory in Joliet, IL, and began shifting jobs to a facility in Monterrey, Mexico. At one time, the former plant had employed up to 7,000 people.
But, through all those transitions, Caterpillar has continued to invest in state-of-the-art production tools and technology, such as additive manufacturing, collaborative welding robots, DC electric fastening tools and RFID-based real-time locating systems.
In its 2023 annual report, Caterpillar outlined its current manufacturing strategy and devotion to operational excellence: “The most important thing we do is ensure employees go home safely every day. Through continuous improvement efforts over the past two decades, we have established an industry-leading safety culture. Today, we are working toward a 2030 goal to deliver a 50 percent reduction in recordable injury frequency from our 2018 performance.
“We continue to modernize our global parts distribution network through lean principles, automation and robotics. This agile and autonomous ecosystem—now in operation at seven facilities worldwide—enhances safety, improves quality and increases efficiency, ensuring our network operates effectively at the lowest cost.”
NOTE: Part 1 of this article, which focused on manufacturing at Caterpillar before 1970, appeared in the April 2025 issue of ASSEMBLY Magazine.
ASSEMBLY ONLINE
For more information on construction equipment manufacturing, visit www.assemblymag.com to read these articles: