Screwdriving and Riveting
Window manufacturers should take a proactive approach to environmental health and safety. Photo by Anatoliy Cherkas, courtesy Getty Images
Software Analyzes Fastening Data
CNH Industrial uses data-driven software to solve problems on the assembly line before they occur.
John Sprovieri // Chief Editor
In 1840, Jerome Increase Case started a small business in Rochester, WI, threshing his neighbors’ crops with horse-powered machines. Over time, Case tinkered with the equipment to improve its performance. Two years later, he came up with a new and improved threshing system powered by water, rather than horses, and he founded a company in nearby Racine to supply the machines nationwide.
From those humble beginnings arose CNH Industrial, one of the world’s largest manufacturers of agricultural machinery and construction equipment. The C in CNH stands for Case, and Case tractors are still produced in Racine. In 2024, CNH tallied sales of $19.8 billion, and the company has a commercial presence in some 170 countries. CNH operates 40 assembly plants worldwide, and it employs more than 35,000 people.
One of those plants is located in St. Valentin, Austria, about 100 miles east of Vienna. Since it opened in 1947, the plant has produced a variety of tractor models, ranging from 100 to 300 hp, under both the Case and Steyr brands. Each tractor takes approximately 40 hours to build, and a finished machine leaves the assembly line every 10 minutes. With 6,400 different specifications, it is rare that any two tractors are the same.
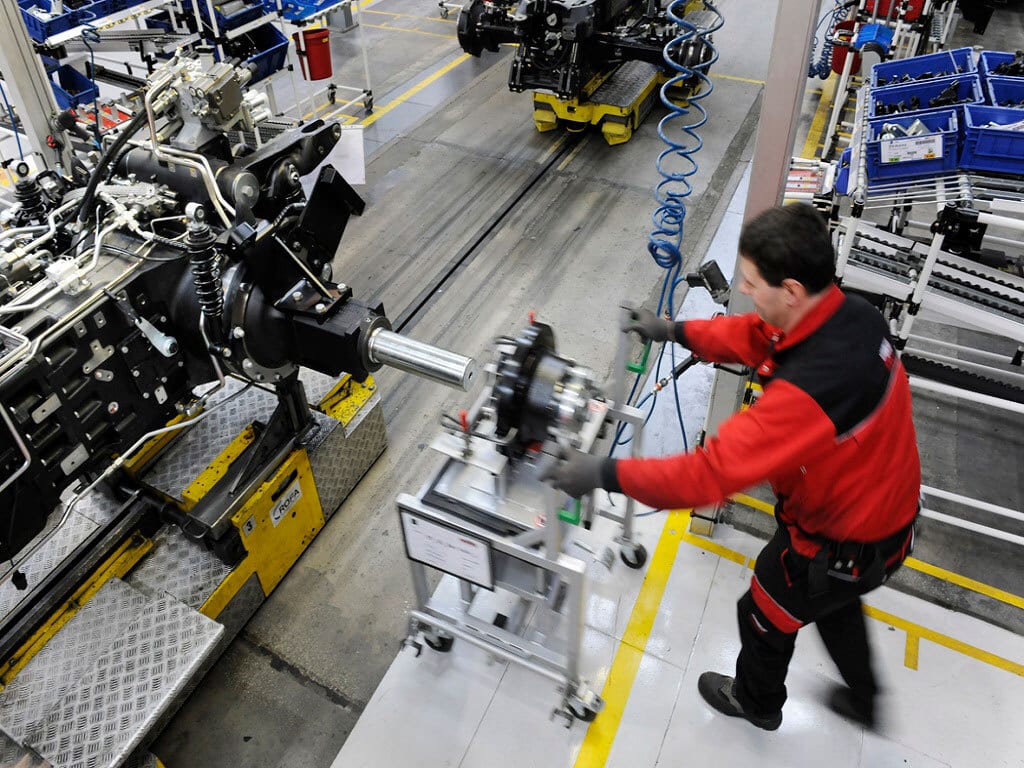
The software detects anomalies in the fastening data and determines if they are the beginning of a trend or just one-off occurrences. Photo courtesy CNH Industrial
Keeping Track of Fastening
Since each tractor contains thousands of threaded fasteners, CNH engineers must ensure that every screwdriver and nutrunner in the plant is performing perfectly.
In the past, the evaluation of tightening data was done manually, which was time-consuming and error-prone. To live up to the plant’s motto “solve problems before they arise,” engineers wanted to adopt a proactive approach to the assembly process. The goal was to detect anomalies and negative trends in the tightening data automatically, in real time, and thereby prevent defects from occurring.
The factory had been using Atlas Copco fastening tools for many years, so it was the first company CNH engineers turned to when they wanted help with data analysis. Atlas Copco recommended its Alture software.
Alture enables CNH to capture and analyze all tightening data. The software monitors all the technical parameters set on the tool controllers, including torque and angle of rotation. Engineers determine a standard range for each parameter, and these ranges serve as the basis for analysis of assembly quality. Algorithms in the software detect anomalies in the data and determine if they are the beginning of a trend or just one-off occurrences. The software even goes one step further and formulates potential causes for the trends in real time. Accordingly, the user is provided with several recommendations to take action, so that corrections can be made early on.
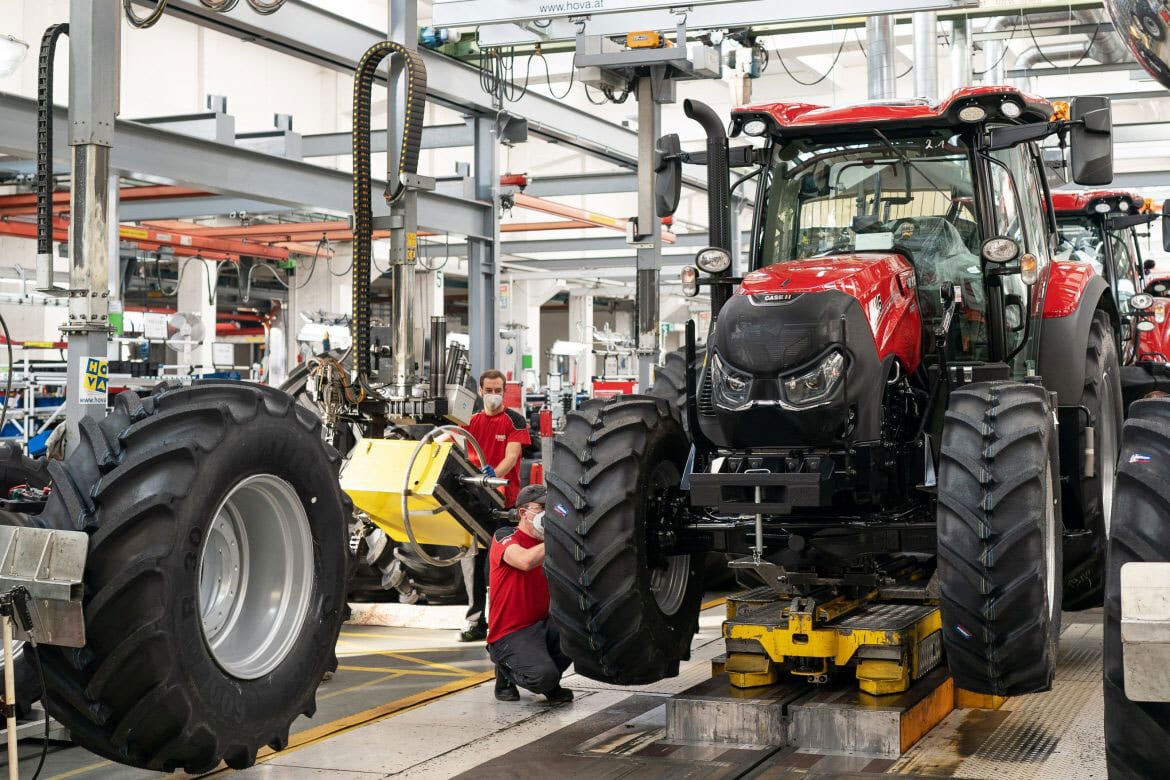
Software informs the assembly team immediately when predefined fastening parameters are exceeded or not met. Photo courtesy CNH Industrial
Thanks to Alture, CNH is now harnessing the full potential of data analysis on the assembly line. Now, the assembly team is informed immediately when the predefined parameters are exceeded or not met. If there are too many deviations in the values, the software communicates precise recommendations to the user. For example, it might advise engineers to inspect the coating on parts or to check the screw threads for lubricant.
Thanks to these sorts of suggestions, the assembly team detected new components with modified materials that would have affected the parameters of the fastened joint. By adjusting the technical parameters in good time, it was possible to avoid faulty assembly and the reworking of numerous tractors.
Thanks to the sensitivity of Alture to deviations in the tightening data, CNH can intervene in the assembly process at an early stage. For the first time, CNH can be proactive instead of merely reacting to situations. This has improved initial production quality, increased productivity, and reduced scrap.
“ALTURE allows us to work in a more proactive and even preventive way in the final assembly,” says Niklas Doschko, electrical system engineer at CNH.
Inspection System
No More Manual Analyses
Manual analyses of tightening data are now history. So are long waiting times for personal feedback within the assembly team. Thanks to Alture, tightening data is automatically analyzed, deviations from technical parameters are detected early, and proactive measures against production errors can be initiated immediately. Even damaged hardware can be quickly identified and reported. The response time on the assembly line has decreased immensely.
“When ALTURE detects an issue in the assembly line, it sends me clear notifications and recommendations on how to fix the issue,” says Doschko. “I also have Alture on my Apple watch, so I receive a notification directly on my wrist.”
The proactive approach at the St. Valentin plant is attracting interest from CNH’s other assembly plants, and the tractor manufacturer now plans to implement the software at its facilities worldwide.
ASSEMBLY ONLINE
For more information on fastening tools, visit www.assemblymag.com to read these articles: