Robotics
Labor shortages are driving new demand for automation.
Options for Screwfeeding
Both SCARA and six-axis robots automate assembly of air bag sensors. Photo courtesy Stäubli
The new automated assembly line was running 24 hours a day, six days a week, within its first seven months.
Robots Automate Assembly of
Air Bag Sensors
John Sprovieri // Chief Editor
There’s no doubt that automotive air bags have saved lives. Especially when used in conjunction with seatbelts, air bags have significantly reduced automotive fatalities.
The National Highway Traffic Safety Administration estimates that frontal air bags have saved more than 50,000 lives in the U.S. alone between 1987 and 2016. Frontal air bags reduce driver deaths by 29 percent in frontal crashes and fatalities of front-seat passengers aged 13 and older by 32 percent. The combination of airbags and seatbelts reduces the risk of death in frontal crashes by 61 percent. Side air bags, particularly those protecting the head, further reduce the risk of death in driver-side crashes.
Not surprisingly, then, demand for the technology is growing. Consulting firm Fortune Business Insights valued the global market for automotive air bags at $16.3 billion in 2024. Moreover, the market is projected to grow 7.2 percent annually during the next seven years, from $17.1 billion in 2025 to $27.74 billion in 2032.
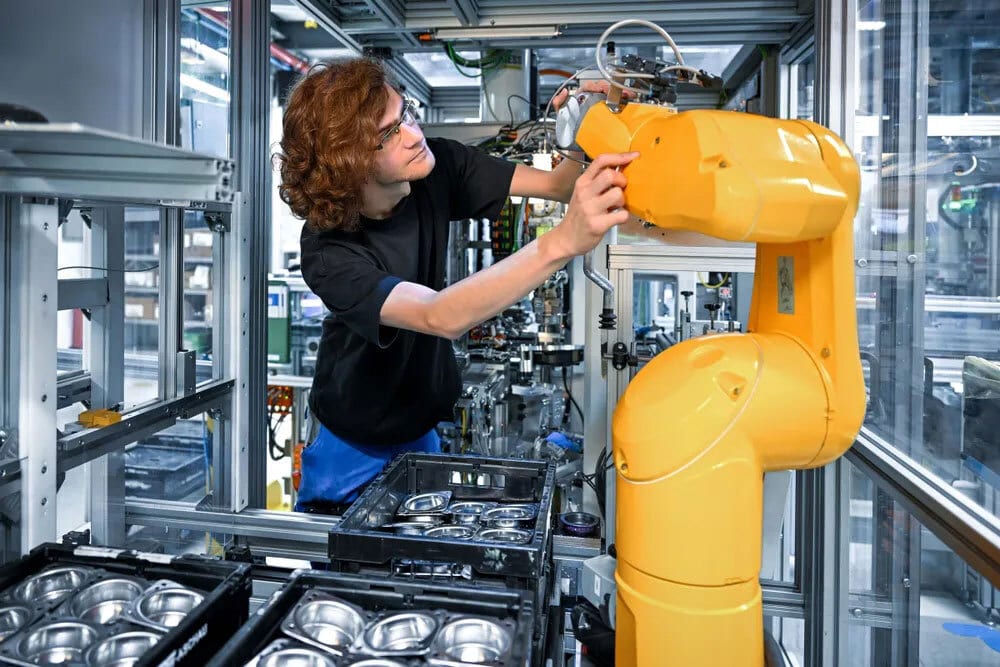
ZF employs Stäubli robots throughout its worldwide network of assembly plants. This six-axis robot assembles air bags at a factory in Germany. Photo courtesy ZF Friedrichshafen AG
ZF Friedrichshafen AG is one of the world’s largest automotive suppliers, with a strong presence in the air bag market. The company manufactures frontal, side and knee air bag systems, and this year, it introduced a new air bag to help protect the lower legs.
ZF makes more than just the air bags; it also makes the sensors that trigger the air bags to deploy. During a crash, these sensors provide crucial information to a dedicated electronic control unit (ECU), including collision type, angle and severity of impact. Using this data, the ECU determines if the crash meets the criteria for deployment and triggers various firing circuits to deploy one or more air bag modules within the vehicle.
ZF manufactures these sensors and ECUs at its assembly plant in Peterlee in the United Kingdom. Until recently, the production of air bag modules at the plant relied to a large extent on manual labor. Rising demand and a desire to bring more of the supply chain in-house generated the need for new investment in a dedicated assembly line.
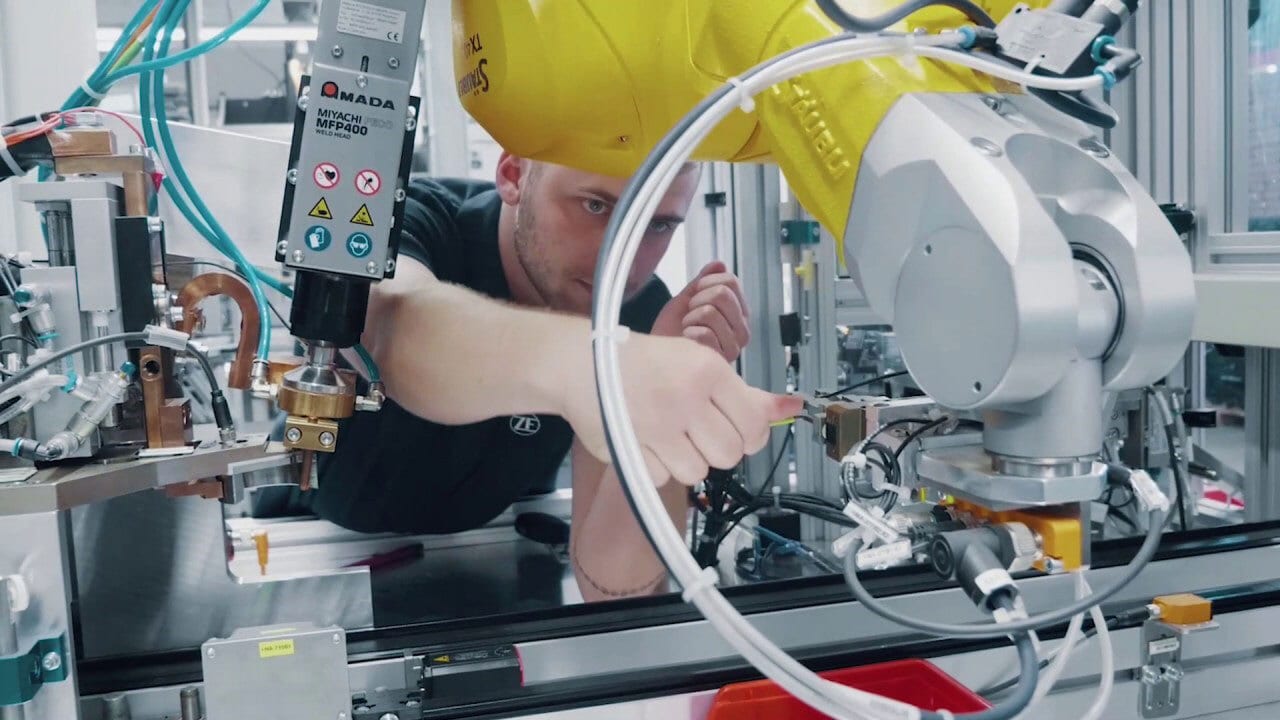
ZF engineers and assemblers quickly got up to speed on managing the new line, which was running 24 hours a day, six days a week, within its first seven months. Photo courtesy ZF Friedrichshafen AG
Robots Automate Assembly
To design and build the line, ZF brought in German system integrators Grohmann Engineering and IPTE Factory Automation. A preliminary analysis revealed that simply expanding or duplicating the existing manual assembly line would not be able to compete with a fully automated line in terms of either output or cost benefit. As a result, ZF opted for a new, fully automated assembly line based on four-axis and six-axis robots supplied by Stäubli Robotics.
The new assembly line consists of several cells connected in series, all of which are equipped with Stäubli robots. In the first step, two Stäubli TS60 SCARAs insert a metal contact into a printed circuit board. This is followed by the soldering of electrical contacts on the board. During the subsequent quality inspection, another SCARA TS60 manipulates the components.
The next stage is the over-molding of the PCB. This is carried out by two six-axis RX160 robots, which were chosen for their range and dynamics.
After over-molding, the robots transfer the module to the final quality assurance station, where it is tested for correct triggering in case of an accident. To pass the test, the response time for the air bag signal must not exceed 19 milliseconds.
The failure rate in these tests has been drastically reduced by the new assembly line and now stands at under 0.1 percent—a remarkable improvement on the manual system, which used a higher proportion of outsourced components.
At the last station on the line, the product is marked and labeled to ensure 100 percent traceability.
ZF engineers and assemblers quickly got up to speed on managing the new line, which was running 24 hours a day, six days a week, within its first seven months.
Due to the flexibility of the line, different variants of the air bag module can be produced. Shortly after the line went into operation, ZF already had 12 models in production. Compared to the manual system, the automated line gets by with 12 fewer people.
For more information on robots, click www.staubli.com.
Inspection System
ASSEMBLY ONLINE
For more information on assembly robots, visit www.assemblymag.com to read these articles: